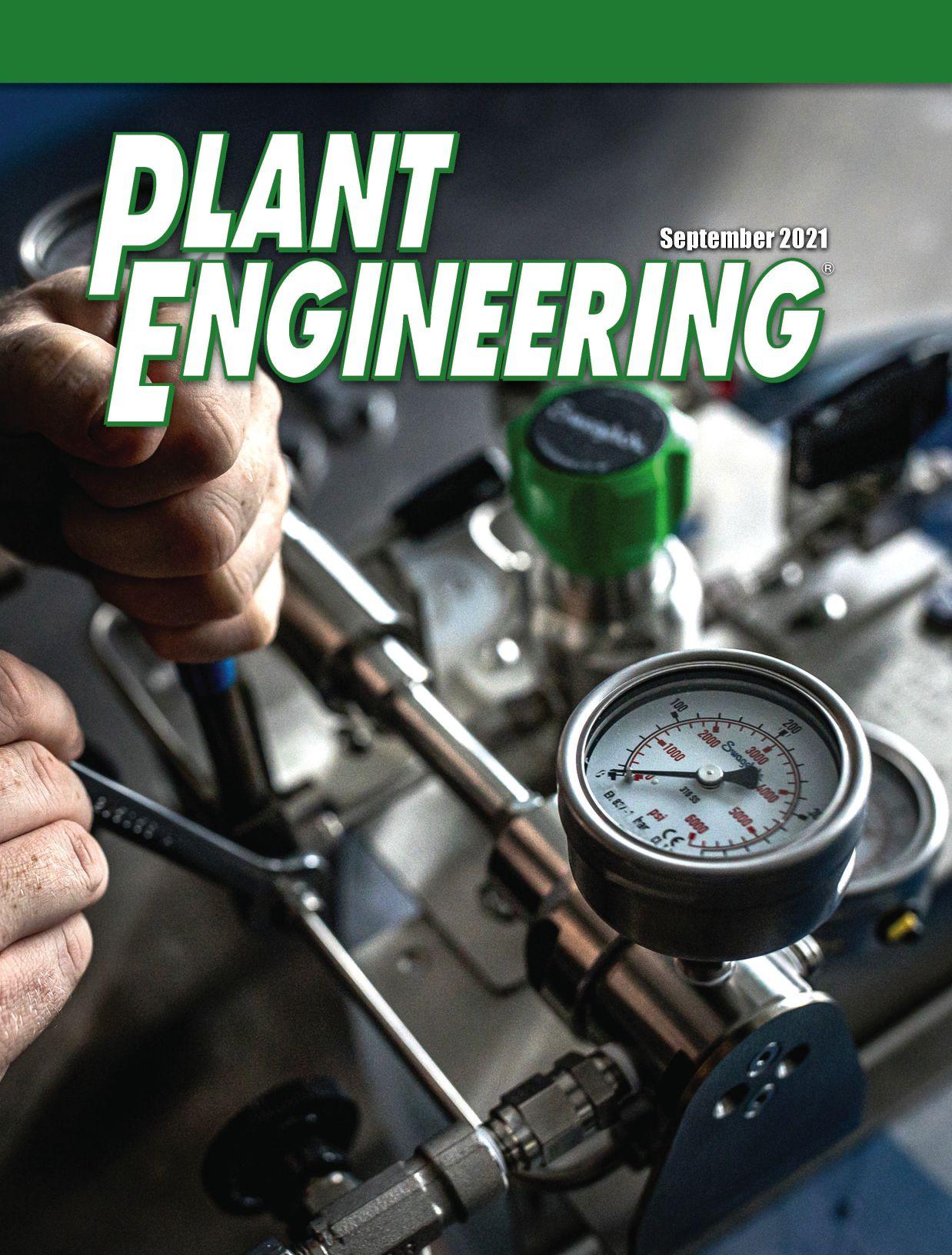

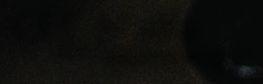
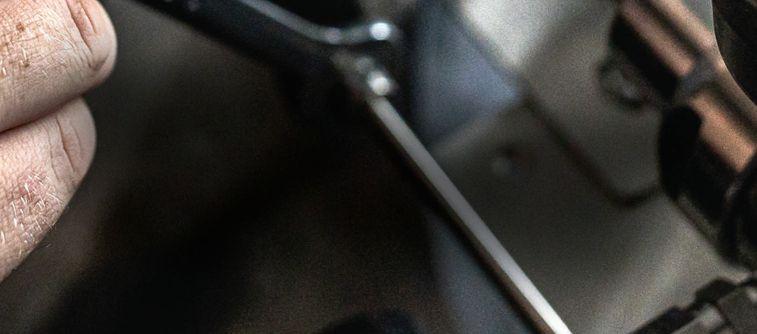

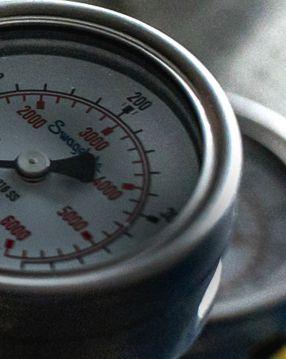
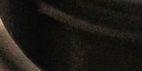



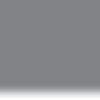

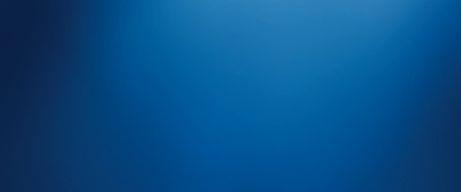
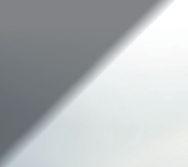

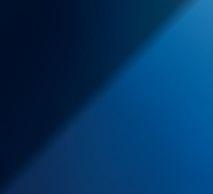
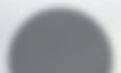
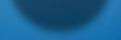





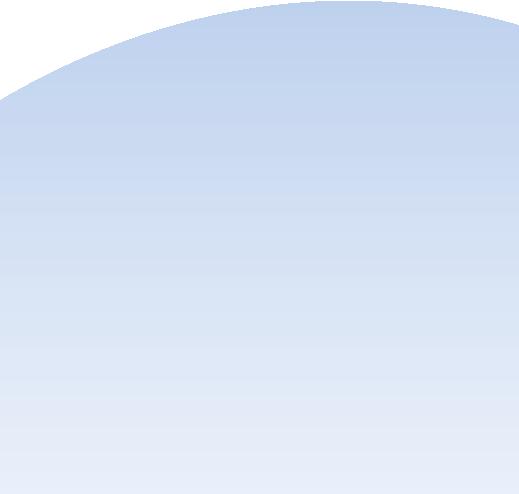

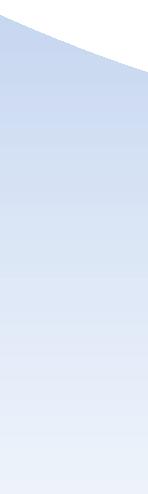

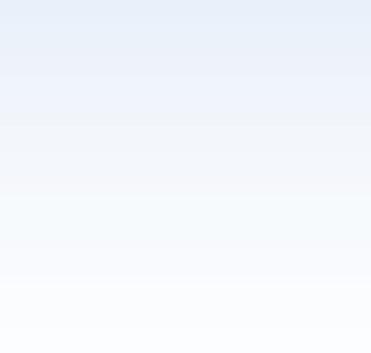




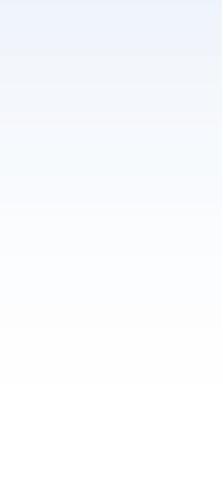

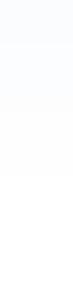
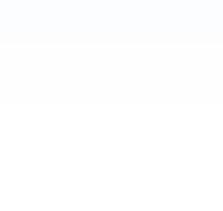
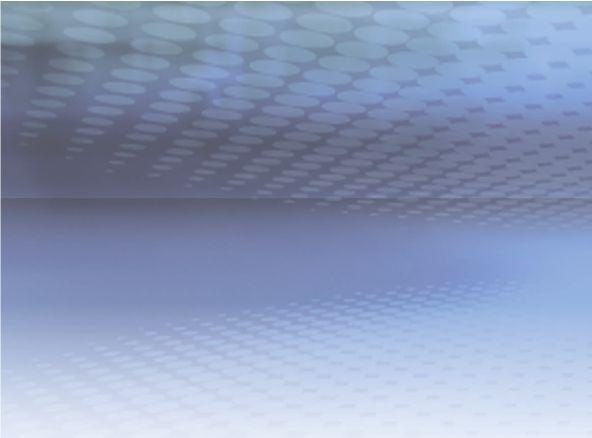
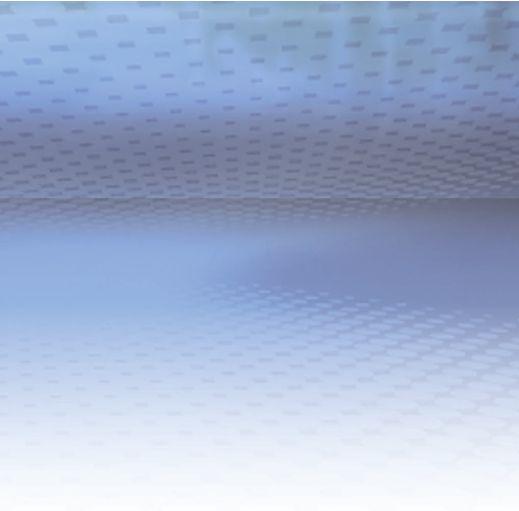
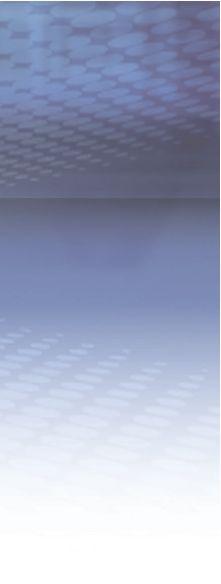
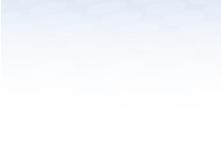
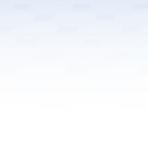
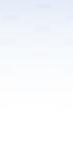

















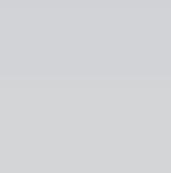
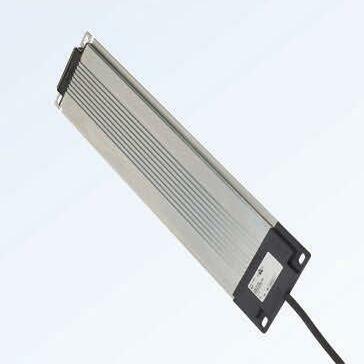
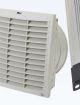
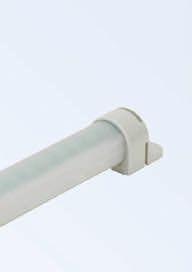
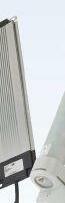
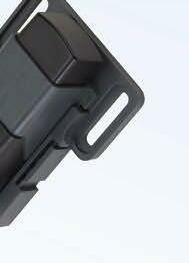
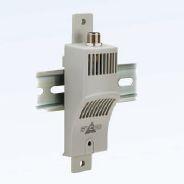
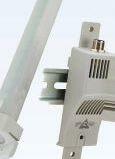

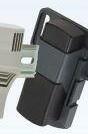

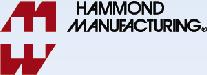
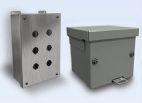
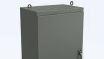
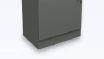
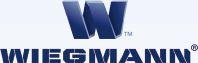
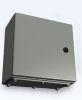

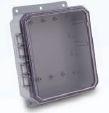
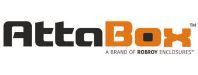
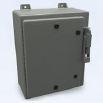
















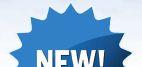

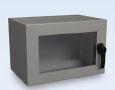
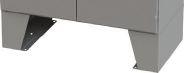
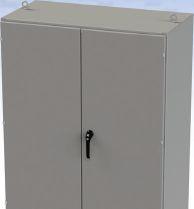
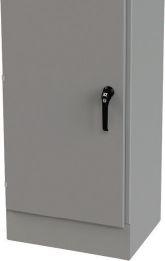
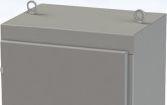
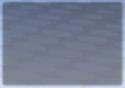
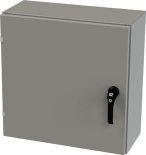
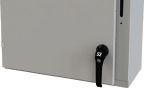
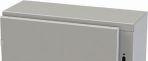
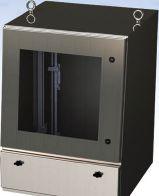



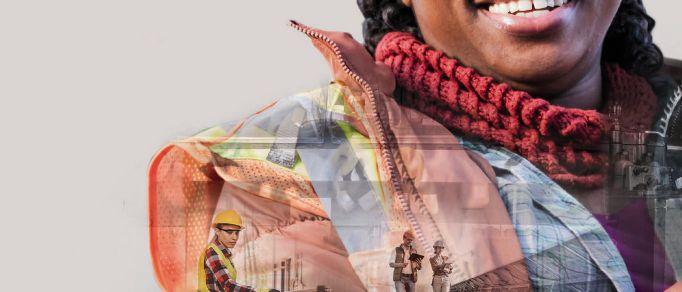
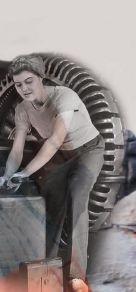
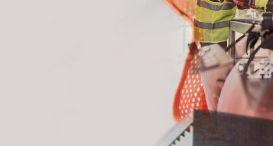
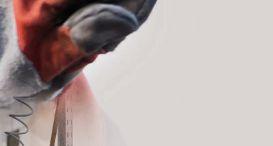
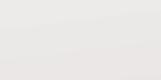

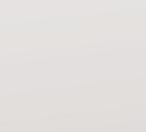
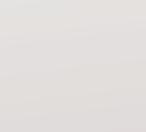
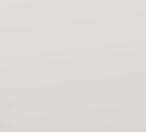
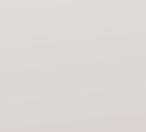

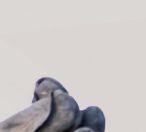
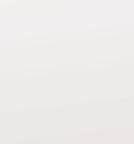

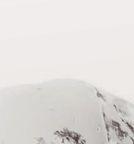
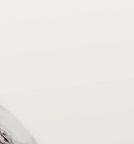
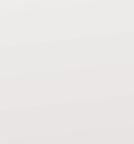
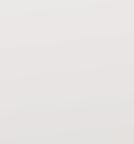
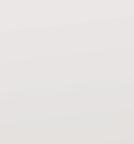
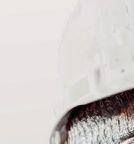

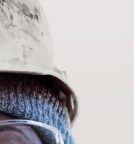
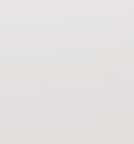
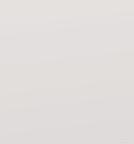
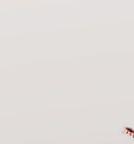
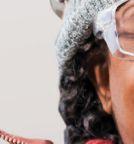



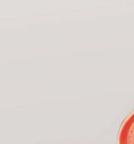
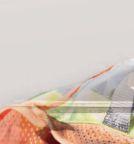
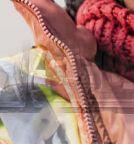
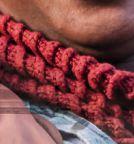
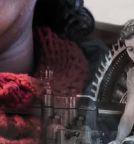

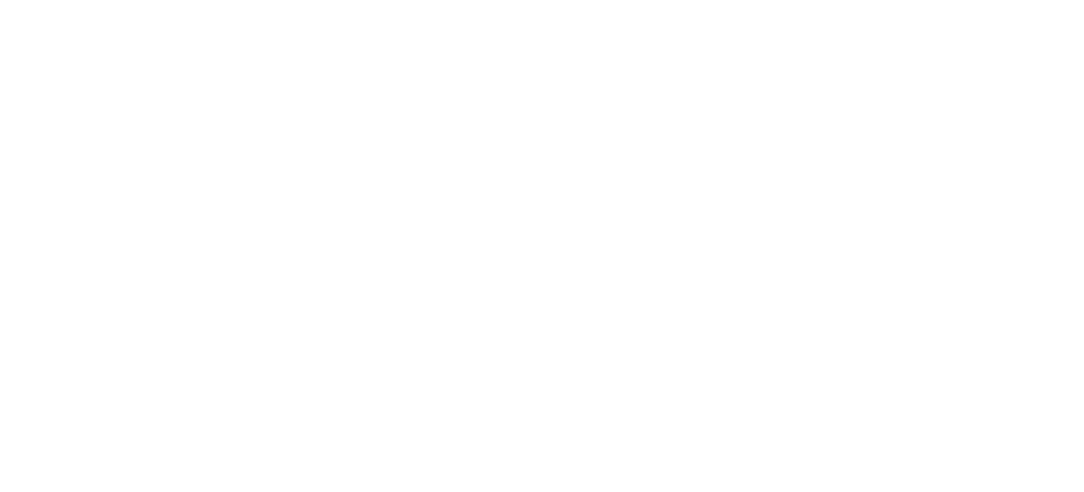






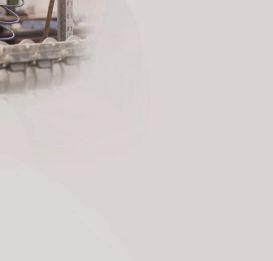
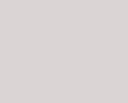
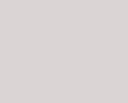
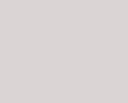
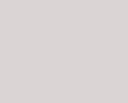
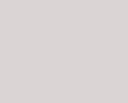
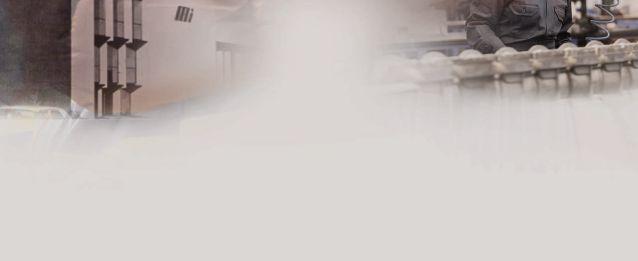
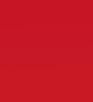


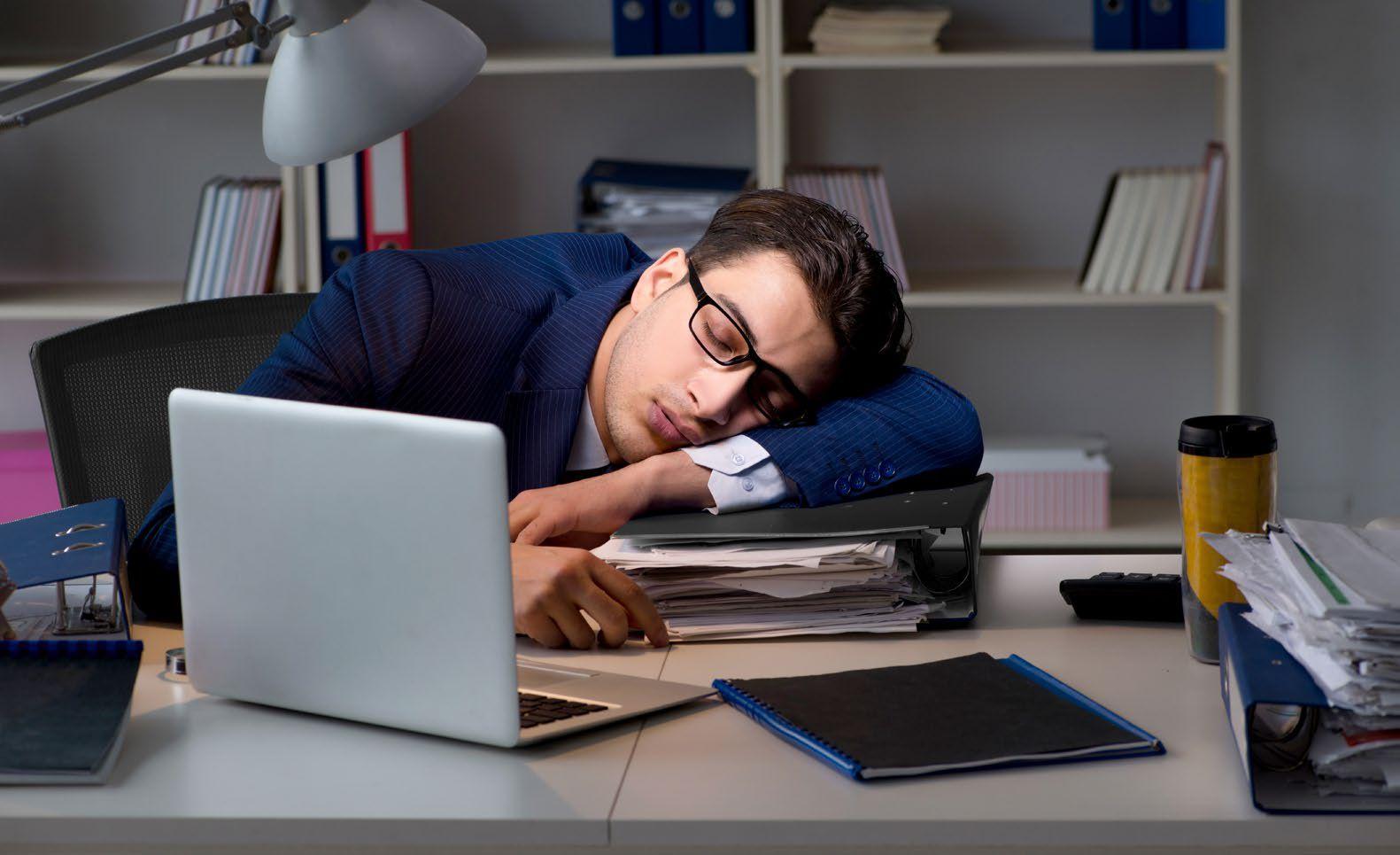

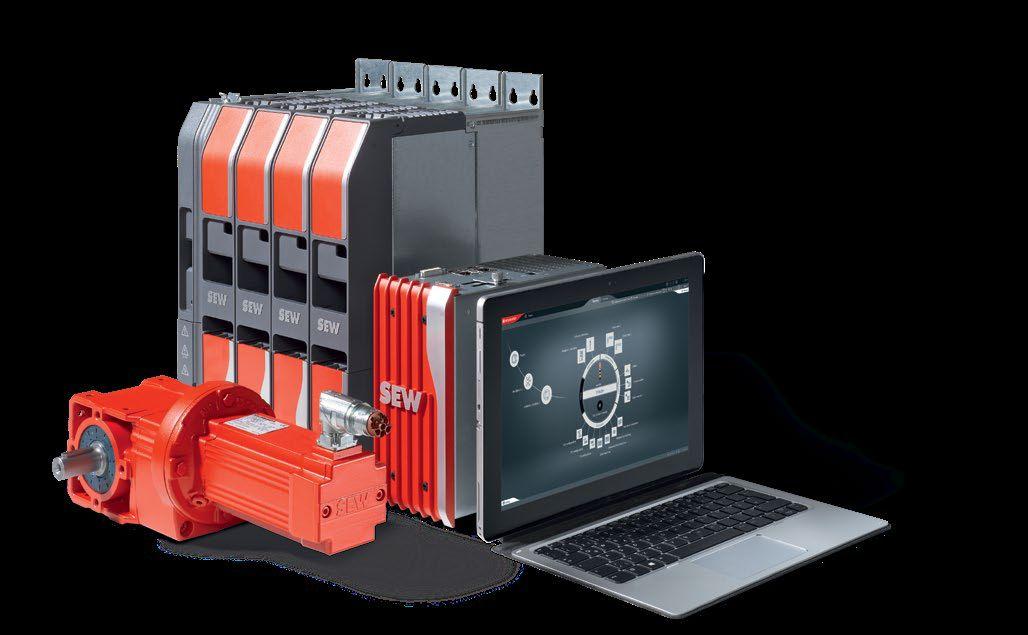
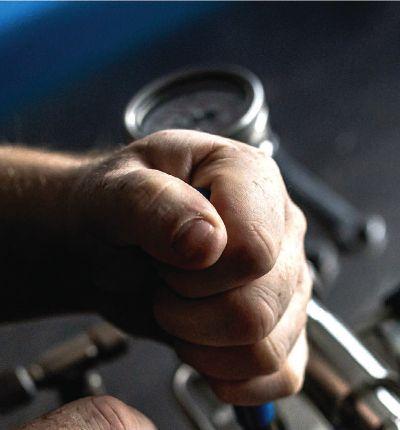
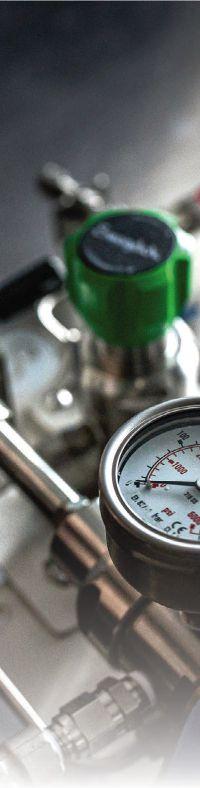
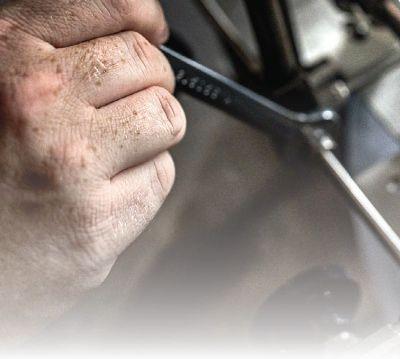
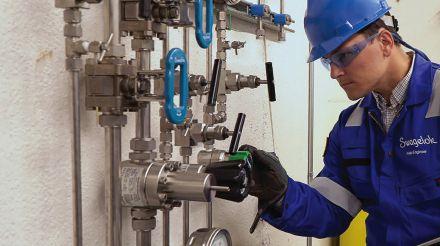
|
Using this process creates better batch accuracy and less maintenance
Preventative leak detection measures play a vital role in the sustainability in manufacturing environments
33 | Gain additional value from inspections
Inspection is changing but a traditional mindset is preventing further evolution
35 |
Advances in automated data processing and machine learning algorithms enhance the value of models and simulation
SEPTEMBER 8, 2021:
Fearlessly implement cybersecurity at the edge
SEPTEMBER 16, 2021: Arc flash mitigation design
SEPTEMBER 22, 2021:
Overcoming the limitations of human-machine interfaces
To view all upcoming webcasts for Plant Engineering visit WWW.PLANTENGINEERING.COM/WEBCASTS
38 |
Process engineers enabled with advanced analytics can have better operational control
|
Meet the engineers who are exceeding expectationsand improving operations
48 | Exploring industrial wireless best practices: more answers
Learn more on industrial wireless, including wireless sensors, wireless reliability
A1 |
Asset management, intelligent workflows and automation play critical role in operationalefficiency
|
Who will win gold in 2021? Oil & Gas Engineering announces the finalists for the 5th annual Product of the Year competition, and readers will have the final word.
|
Advanced temperature measurement technology leads to cleaner, safer and more profitable downstream operations
|
Compressor stations often employ automated valves activated using pressurized natural gas, requiring improved actuator designs to eliminate emissions
3010 Highland Parkway Suite 325 Downers Grove, IL 60515
Ph. 630-571-4070, Fax 630-214-4504
CONTENT SPECIALISTS/EDITORIAL
KEVIN PARKER, Editor KParker@CFEMedia.com
JACK SMITH, Managing Editor JSmith@CFEMedia.com
AMANDA PELLICCIONE, Director of Research 860-432-4767, APelliccione@CFEMedia.com
KATIE SPAIN NAREL, Art Director KSpain@CFEMedia.com
SUSIE BAK, Production Coordinator SBak@CFEMedia.com
H. LANDIS “LANNY” FLOYD, IEEE Life Fellow H.Landis.Floyd@gmail.com
JOHN GLENSKI, President, Automation Plus jglenski@processplus.com
SHON ISENHOUR, Partner, Eruditio LLC sisenhour@EruditioLLC.com
DR. SHI-WAN LIN, CEO and co-founder,Thingswise, LLC Industrial Internet Consortium (IIC) board member shiwanlin@thingswise.com
JOHN MALINOWSKI, Senior manager of industry affairs (retired), Baldor Electric Company
DAVID SKELTON, Vice president and general manager Phoenix Contact Development and Manufacturing dskelton@phoenixcontact.com
BILLY RAY TAYLOR, Director of commercial and off-highway manufacturing The Goodyear Tire & Rubber Billytaylor@goodyear.com
LARRY TURNER, President and CEO, Hannover Fairs USA lturner@hfusa.com
MARK WATSON, Senior director, manufacturing technology, IHS Markit Mark.watson@ihsmarkit.com
Content For Engineers. That’s what CFE Media stands for, and what CFE Media is all about—engineers sharing with their peers. We welcome content submissions for all interested parties in engineering. We will use those materials online, on our Website, in print and in newsletters to keep engineers informed about the products, solutions, and industry trends.
* www.plantengineering.com/contribute explains how to submit press releases, products, images and graphics, bylined feature articles, case studies, white papers, and other media.
* Content should focus on helping engineers solve problems. Articles that are commercial in nature or that are critical of other products or organizations will be rejected. (Technology discussions and comparative tables may be accepted if non-promotional and if contributor corroborates information with sources cited.)
* If the content meets criteria noted in guidelines, expect to see it first on our websites. Content for our enewsletters comes from content already available on our Websites. All content for print also will be online. All content that appears in our print magazines will appear as space permits, and we will indicate in print if more content from that article is available online.
* Deadlines for feature articles intended for the print magazines are at least two months in advance of the publication date. Again, it is best to discuss all feature articles with the content manager prior to submission. Learn more at: www.plantengineering.com/contribute
The Offshore Technology Conference (OTC)
2021 was held August 16 -19 at NRG Park in Houston. If the Delta variant of Covid-19 hadn’t come along it’s likely that the exhibition’s foot traffic would have been considerably more than was evidenced at the event.
Caterpillar Inc. had a large presence at OTC, befitting its increased footprint in the industry. In February, the company completed its acquisition of the Oil & Gas Division of the Weir Group PLC, a Scotland-based global engineering business. Headquartered near Fort Worth, Texas, SPM Oil & Gas will continue to produce a full line of pumps, flow iron, consumable parts, wellhead and pressure control products offered via a global network of service centers.
“Combining Weir Oil & Gas’ pressure pumping and pressure control portfolio with Cat engines and transmissions provides additional value for our customers,” said Joe Creed, Caterpillar Group President.
The transaction includes more than 40 global service centers and approximately 2,000 employees. “We are uniquely positioned to provide end-toend solutions from the engine to the wellhead. As one of the only companies with natural gas or electric-powered 5,000 HP pumps operating in the field, we provide technologies that reduce emissions while promoting efficiency gains for positive operations and bottom-line impact,” said Paul Coppinger, president of SPM Oil & Gas.
Stress Engineering Services Inc. said it will be working with Lincoln Electric, the maker of welding products and equipment, to introduce oil & gas service companies to the virtues of additive manufacturing.
Additive manufacturing, also known as 3-D printing, is the computer-
controlled sequential layering of materials to create three-dimensional shapes. One good use of additive manufacturing is the provision ondemand of replacement parts needed in production environments, including for the U.S. Airforce.
In late 2020, The United States Airforce Rapid Sustainment Office said a team consisting of Stress Engineering Services, Origin, and nTopology was awarded first place in the F-1 Approval Sprint Challenge.
The goal of the challenge was to identify innovative strategies for rapid design, qualification, and deployment of solutions that leverage new manufacturing materials, processes, and components.
Requirements for the challenge were complex and looked at dimensional accuracy, stresses and loads, flammability compliance, temperature ratings (low and high), jet fuel exposure, vibration tolerance, hydraulic fluid exposure and engine oil exposure.
The part submitted by the team was designed on nTopology software, uses Loctite 3955, a flame-retardant chemically resistant material from Henkel, is manufactured on the Origin One 3D printer, and validated by Stress Engineering Services using an advanced rapid digital qualification process.
Finally, HYTORC, a maker of industrial bolting systems, received a Spotlight on New Technology Small Business Award at OTC 2021. The company won the award for its HYTORC J-Washer.
The J-Washer is suitable for use in applications with dynamic loads and high vibrations where bolt loosening is a concern. These applications include joints with cyclic transverse loads that can overcome the frictional forces of the preloaded joint. PE
As the role of a supplier continues to evolve, it’s no longer just about product support and understanding the customer’s needs. You really should be a trusted advisor and a local expert.
Paul HumphreysI spoke to a recent graduate student who has joined Atlas Copco, and his career path was leading him to become a financial planner — he’s now a high-performing service sales manager inside Atlas Copco. When asking the reason for his career change, he looked a bit puzzled. He expressed that it’s not a career change in many ways but instead a continued focus on stocks and capital investment. “I am advising customers how to manage assets and use all the tools to ensure that their compressed air system improves their contribution to the bottom line — I’m a financial compressed air planner!”
A big part of this trusted advisor status is understanding what energy rebates are available for compressed air equipment. Here’s a real life example from a packaging supplier in the U.S.
kWh Annual Savings: 933,791
Annual Electricity Cost Saving: $84,298.96
Annual Reduction in 600 metric tons (equivalent to annual CO2 Emissions: electricity usage of 112 average homes)
Project Cost: $312,243.49
Energy Incentive: $140,068.65
NET Project Cost: $172,174.84
Payback Period: 2 Years
Let’s state that again. The new compressor was so energy efficient that the local energy company wrote them a check for $140,068.65. Across the United States, trusted advisors are helping their customers achieve amazing things at the best possible cost. There are plenty of other incentives out there too, such as the Section 179 tax deduction program.
VP Communications and Branding, Atlas Copco Compressors.The bottom line is important, but so is the top line.
When we talk about the top line, we like to focus on CO2 emissions. The recent climate change report published in August from the IPCC was labeled ‘Code Red for Humanity.’ The one compressor change on the previous page reduced annual CO2 emissions by 600 metric tons. That’s a massive saving!
We all have a role to play in climate change, and the compressor business can make a real difference —it’s win-win. Energy efficiency saves money and saves the planet.
It’s not a new trend, but as compressed air has always been discussed as the “fourth utility” inside a plant — more customers are considering purchasing air like gas, electricity, or water. So, in essence, buying air and not the actual compressor. For the right customer, this has several advantages, including not needing a significant capital expenditure at the start of the project and having no maintenance responsibility for the equipment, as that’s taken care of by the manufacturer. We have seen many customers where the monthly cost of the air compressor is way less than the monthly energy saving, resulting in money to the bottom line from day one and CO2 savings for the top line.
24/7 connectivity is offered with just about all new compressors. This is not about being ‘tied’ to your compressor but instead giving you peace of mind to ensure you can always be in control – no matter where you are working. You can also think of remote monitoring as an ongoing audit that happens 24/7, offering the capability to identify any potential issues before they can become serious problems.
The term “total-solutions provider” when it comes to our business is outdated. At Atlas Copco, we innovate in areas where we can add value and offer an outstanding payback. With this in mind, innovation means that we can provide compressors, blowers, vacuum pumps, dryers, chillers, and nitrogen and oxygen generators, and much more!
The benefits are enormous when it comes to harmonized central connectivity, remote monitoring, service contracts, and operator familiarity. Imagine if all these pieces of equipment can be controlled in a uniform way? This is genuinely game-changing.
It’s a fact that modern compressors do not make a lot of noise, and there should not be a pool of oil or water surrounding them. With that in mind, and a lack of available space a genuine concern, we have seen more and more compressors fitted at the heart of the production facility. When you see this it’s a real sign that the compressor is low-noise, innovative and saving the company money.
Every plant manager across the country knows the cost of downtime. Building a system that removes the “all or nothing” approach is vital to success. Adding a second compressor or running two smaller ones instead of one large unit can often be the optimal solution.
The pandemic has also highlighted how the supply chain can be affected quite quickly — from the manufacturing of goods to the ability of shipping companies to deliver based on capacity issues. This means that manufacturers cannot afford to ignore contingency planning for all scenarios.
And one last thing, never neglect service and the need for preventative maintenance – it will catch up with you eventually!
When the COVID-19 pandemic hit in early 2020, many companies slowed or shut down operations with the expectation that normalcy would resume within a matter of weeks. However, as the months wore on, it became painfully obvious that it would be a long time before things returned to normal.
As COVID-19 capacity constraints and social distancing requirements entered the manufacturing arena, talk of manufacturers transitioning to lights-out automation renewed with vigor. Factors often cited as reasons for transitioning to lights-out manufacturing include lighting, heating and cooling savings, with the argument being that robotics and other machines can run in the dark and under a wide range of temperatures. But, given the cost of transitioning, a lights-out program will not pay for itself in less than a couple of years. The return on investment is just not there, except over a long period of time.
Another argument for the introduction of lightsout automation is improved capacity, for example, saving space with auto-retrieval. To date, most automated retrieval systems have remained prohibitively expensive and have proven to be problematic unless used under highly predictable and repetitive operations — and still requiring skilled human operators and other workers to fulfill the kinds of tasks that require adjustments and on-the-fly thinking. Given that people will be part of the manufacturing process for the foreseeable future, reducing space, at this time, is counter to COVID-19 compliance and physical distancing requirements.
In general, a large-scale lights-out automation strategy can make sense for large manufacturers, but for smallto-medium-businesses (SMBs), which make up the bulk of manufacturing in the U.S., it is far too costly. There are three specific scenarios, however, where it makes sense to implement lights-out automation for the SMB manufacturer:
According to the World Economic Forum, 2020 was the year that automation sgained additional impetus in the market place. This is due to the ongoing and widening skilled labor shortage in manufacturing. This is one of the biggest factors in deciding to automate, to address the need for truly advanced automation that can fill highly specialized, if still repetitive, tasks.
Scenarios where production volumes are so high that a human workforce could not achieve the quota require automation. This could be the case when millions of the same or a few parts are required or in which many thousands of tests are required. Robotic work cells are an example of a hybrid lights-out automation model relegated to a specific area or plant process, and some manufacturers are looking at a shift-model, where the night shift is automated with a robot workforce to supplement the human workforce that arrives in the morning.
Scenarios where automation has already been in place for years include the manufacture of films, semiconductors and pharmaceuticals, among others. These all are areas where high quality and even lights-out conditions are required to minimize the introduction of various types of contaminants and/or where production environments use hazardous materials that introduce risks to human safety.
The key drivers for lights-out automation are the need for skilled labor, support for high-volume production and quality or contamination prevention. One manufacturer of engineered-to-order lab automation equipment is a good example of why and when lights-out automation makes sense for an SMB manufacturer. Its automated testing lab, powered by a robust enterprise resources planning (ERP) system, is being put to critical use in COVID-
The interactive manual is a digital repository where you can retrieve all the information related to an industrial plant.
Within the information that we have compiled for the interactive training manuals, you will find the following:
• Information about the plant and its equipment.
• Standard operating procedures and fundamental processes allow the user to have an objective response and knowledge to operational contingencies.
• How critical variables are controlled, and the impact of out-of-range variations on processes would cause.
• Procedures, interlocks, alarms, the cause of failure, and the appropriate corrective action.
• Abnormal operating scenarios and frequently occurring fault conditions, and how to resolve them.
With the Interactive Manual, prepare your team for any operational process in your plant.
19 research and testing. The company developed highly flexible, modular COVID-19 research and testing robotic solutions that allow scientists to scale production.
Manufacturers should move now, as lockdowns are lifted, to put in place technology-enabled strategies, such as implementing social distancing and related work safety practices. This strategy, combined with virtual inspections and operations meetings where someone on site provides a virtual tour from the conference room and across the production floor, has enabled some production to move forward. A virtual operations tour also has the added benefit of being recordable for playback and extended reviews.
Longer term, introducing automation can pay dividends, and it starts with accurate data, which is enabled via ERP solutions. From remote monitoring capabilities that enable access to real-time data, to
maintenance, as well as identifying the reasons for machine downtime, automation augmented with ERP is a winning solution that provides value to both large and small manufacturers.
Manufacturers are returning to work with saferat-work policies that are likely to be part of new normal operations, which can go a long way to prepare the industry for potential new shutdowns and future pandemics. Now is the time to start long-term planning. Strategic manufacturers will move forward with automation and effectively using ERP, machine learning and related technologies to succeed in the post-COVID manufacturing era. PE
Paul Denmark is a senior consultant at Ultra Consultants with specific industry expertise in medical device, aerospace and defense, oil and gas, and consumer electronics, as well as pressure sensitive adhesive industries. He has extensive experience offering end-to-end supply chain reengineering with crossfunctional integration among supply chain planning,
CALTRAN C50 Insulating
provide exceptional insulating properties and low temperature fluidity which are ideally suited for the Canadian climate.
Readily available for your next oil fill or top-up!
Your Northeast Cat® Dealers maintain the region’s largest fleet of high quality, low hour power rental solutions. They offer a rental product line specifically designed to meet the needs of commercial, industrial, institutional, and manufacturing facilities. Our line encompasses the most critical systems to your operations, including temperature control, compressed air, and of course, electric power products. We have the largest, most modern fleet of equipment in the Northeast, so you can be sure that you will have the right equipment to meet your needs wherever you jobsite is located.
Learn more today by visiting www.necatdealers.com/standby
Lubriplate’s line of ultra high-performance, 100% synthetic compressor fluids has been formulated to provide a wide range of benefits including: extended fluid change intervals, cooler operating temperatures, reduced friction and reduced downtime. Available products include...
SYN LUBE SERIES 22 - 100
Extended life, PAO-based, fully compatible OEM replacement fluids.
SYNXTREME AC SERIES
ECO-Friendly, biodegradable POE-based compressor fluids.
SYNAC SERIES
High-performance, diester-based compressor fluids.
SYNCOOL
ECO-Friendly, Biodegradeable polyglycolester-based fluids.
SYNCOOL FG
NSF H1 Registered, Food Grade - polyglycolester-based fluids.
SFGO ULTRA SERIES 22 - 68
NSF H1 Registered, Food Grade - PAO-based fluids.
Most readers of Plant Engineering magazine are familiar with electric motors made to National Electrical Manufacturers Association (NEMA) standards as commonly used in the U.S., Canada, Mexico, some parts of South America and Saudi Arabia. But nearly 70% of the industrial motors sold worldwide are made to International Electrotechnical Commission (IEC) standards. Motor standards for these motors are MG 1 for NEMA and the 60034 series and 60071 for IEC that define mechanical, electrical, and performance specifications.
Many people do not fully understand the differences between these electric motors. Not only are there mechanical mounting and dimensional differences, but usual features and electrical designs are different as well. Users must recognize and adjust for these variations as they manage projects around the world. It is becoming increasingly commonplace to import machinery using IEC motors and many original equipment manufacturers (OEMs) to use IEC motors on products for export outside of North America.
Figure 1: NEMA motors offer a wide range of enclosures such as open-drip proof (ODP) motors used in many compressor and fan applications. NEMA motors are defined in inch units and are made with the finned cast frames and rolled steel frame housings. Courtesy: ABB Motors and Mechanical
In the past, NEMA manufacturers were usually independent companies based in the U.S. Today, many large motor companies in North America are part of large multi-national companies that make both NEMA and IEC motors. The same engine components may show up in both.
This article focuses on 3-phase NEMA low-voltage motors
(less than 600 V) in the 1 to 350 hp (0.746 to 261 kW) range and their IEC equivalents most used in industry.
The most obvious mechanical difference is that NEMA motors are defined in inch units and IEC are defined in metric units. Beyond that, NEMA motors offer a wider range of motor enclosures not common in the IEC designs such as open-drip proof motors used in many compressor and fan applications (see Figure 1).
IEC motors are commonly made with either finned cast aluminum or iron frames, while NEMA motors are made with the finned cast frames and rolled steel frame housings (see Figure 2). There are only slight differences in frame sizes based on shaft height (see Table 1). The shaft diameters and lengths are different between NEMA and IEC as are the mounting base dimensions and mounting hole spacing.
An especially important difference is that NEMA motors commonly use a polyurea-based grease where most IEC motors use lithium grease. These greases are not compatible and should not be mixed. If a plant’s motor population is mixed between NEMA and IEC, care must be taken when someone is sent to regrease motors.
Typically, NEMA motors are made with a sidemounted conduit box (F1 position) with leads for connections. Most IEC motors have the conduit box at 12-o’clock (F3) with a terminal block for connections.
NEMA motors usually do not have a shaft seal except for some severe duty designs such as those made for IEEE-841 compliance where a noncontact rotating shaft seal is used. In some custom designs, a lip seal may be used on the shaft to prevent ingress of liquids. Many IEC motors are supplied with a standard lip seal.
NEMA motors often have a “weep hole” at the lowest point of each end plate to allow condensation to exit. On severe duty motors, this hole is changed to a breather drain. This practice is not common on IEC motors.
Over the past few years, NEMA has started to adopt IEC standards as part of MG 1. The levels of ingress protection (IP) for motors and for cooling (IC) are
NEMA and IEC motors are similar but have different usual practices; take care when managing a facility with a mixed population
±5% of rated and a frequency within ±2% of rated. IEC also recognizes zone B, which allows a voltage variation of ±10% and a frequency variation of +3%, -5%.
Most NEMA motors have a continuous duty cycle. NEMA also defines intermittent duty motors for some applications with 15-minute, 30-minute and 1-hour duty cycles. This means the length of time for the motor to operate at full load before reaching maximum safe operating temperature, then the motor must cool to ambient before it is operated again. IEC has a more elaborate duty cycle rating system that also includes cyclic loads, but the S1 is the normal continuous duty cycle on most motor designs. IEC 60034-1 goes into more detail on the definitions of these duty cycles with illustrative charts.
shown in the MG 1 standard. Recently, the vibration standards have been harmonized.
Some usual mechanical configurations used in North America are not common in the IEC world. Pump motors (JM and JP) with provisions for axial shaft load are not used on IEC motors because the pumps take the axial load from the impeller instead of the motor.
NEMA motors are generally designed with NEMA Design B torque/current characteristics per Part 12 of the MG 1 standard. Those with higher inrush current are Design A. IEC motors in these sizes are IEC Design N and NE, typically having somewhat higher inrush currents than a NEMA Design B motor. High starting torque motors are NEMA Design C, like IEC Design H and HE. High slip motors used in punch presses and oil beam pumps are NEMA Design D; there is not an IEC equivalent.
The 3-phase 60 Hz motors used in North America are usually 230/460 V with a 9-lead 1-wye/2-wye connection. An IEC motor at 4 kW and larger have wye/delta connections for 230/400 volts where they start in a wye/ delta manner, not direct across the line (see Table 2).
The difference between NEMA and IEC is not the voltage/frequency combinations, but the tolerance each standard places on these parameters. The maximum voltage variation allowed by NEMA is ±10% at rated frequency, while the maximum allowable frequency variation is ±5% at rated voltage. IEC separates motors into operating zones where a zone A motor shall be capable of performing its primary function with a voltage within
S6
operating periodic
S7 Continuous operating periodic with electric braking
S8
Continuous operating with related load/speed changes
S9 Duty with non-periodic load and speed variations
S10
Duty with discrete constant loads and speeds
Most NEMA motors are designed with a service factor of 1.15. In section 1.42 of NEMA MG 1, service factor (SF) is defined as “a multiplier, which, when applied to the rated horsepower, indicates a permissible horsepower loading, which may be carried under the conditions specified for the service factor.” IEC motors do not recognize a service factor, so they would be equivalent to 1.0. In the U.S., some compressor manufacturers use the service factor when sizing their motors. If an IEC motor is used on a compressor sized in this manner, a motor of a higher power rating may be needed.
Both NEMA and IEC motors are rated for a standard 40°C (104°F) ambient with a minimum temperature of -15°C (5°F). The insulation classes between motors are the same for Class B, F and H. NEMA motors are rated for 3,300 feet (1,000 meters) above sea level altitude, the same as in IEC standards.
NEMA motor efficiencies are defined in MG 1 and have two levels defined as “Energy Efficient” as shown
Sometimes it makes sense to replace your electric motors. Other times, repair is the best option. EASA members can help you make that decision. They understand motors can be repaired or rewound without reducing efficiency or reliability if the work is performed to the industry standard.
ANSI/EASA AR100-2020: Recommended Practice for the Repair of Rotating Electrical Apparatus is the standard for maintaining (or sometimes even improving) AC electric motor efficiency and reliability.
Does
More than 145 service centers have earned EASA Accreditation. These companies demonstrated via third-party, independent audit that they follow the prescribed practices of ANSI/EASA AR100 to consistently deliver quality repairs that maintain or sometimes improve AC electric motor efficiency and reliability.
Count on an EASA Accredited Service Center for your electric motor repair/service needs!
See a full list of these service centers at easa.com/accreditation.
in table 12-11 of the standard and “Premium Efficient” as in table 12-12 of the standard. NEMA Premium is trademarked and the term should only be used by manufacturers who are part of NEMA’s premium motor program. IEC 60034-30-1 defines the efficiency classes for motors. IEC IE2 is equivalent to energy efficient and IE3 is mostly equivalent to premium efficiency.
The usual test methods for these motors are IEEE 1122017 Method B and CSA 390:10 (R2019). In the past, the IEC test method was different because it did not measure all losses, some losses were assumed. In the past few years,
IEC 60034-2-1 Method B1 is the current test method equivalent to the IEEE and CSA methods.
Since 1992, the U.S. Dept. of Energy (DOE) has mandated efficiency levels for motors sold for use in the U.S. This includes motors imported as part of a machine as well. The present level for integral horsepower motors is premium efficiency (IE3) and includes both NEMA and IEC motor designs. Canada has followed the U.S. on these regulations and Mexico regulates motors sold through distribution only. The EU requires IE3 motors but currently allows use of IE2 motors if combined with an adjustable speed drive.
Where the U.S. and Canada recognize fire pump motors as a separate class of motors and allow the efficiency at the energy efficient level of NEMA table 12-11 (IE2) because of their infrequent use and lower inrush current, the EU makes no such differentiation. Fire pump motors in EU are general purpose motors and must be IE3 efficiency.
NEMA and IEC motors are similar but have different usual practices. When trying to manage a facility with a mixed population, one must take care to cater to the differences in these motors. PE
Whether you’re deciding on purchasing our products or learning our products after you buy, why jump through hoops or even pay for the information you need?
We have exhaustive documentation all freely available online, including overviews, technical specifications, manuals and 2D and 3D CAD drawings.
We have over 1,000 videos online to get you up to speed quickly. We even provide FREE online PLC training to anyone interested in learning about industrial controls.
http://go2adc.com/videos
http://go2adc.com/training
For over two decades, we’ve been offering a controls by running our direct business efficiently on to you. No complex pricing structures or penalty low everyday prices on everything from fuses Programming software for controller products can be costly, so we help you out by offering downloadable software for all our latest PLC lies and C-more HMIs. No license or upgrade deal with!
http://go2adc.com/why
You don’t want to wait for your We have fast shipping, and it’s FREE if your order is over $49.*
AutomationDirect has always maintained a huge us to ship over 97% of orders complete within one (Certain items may have early order deadlines, see by part).
*Order over $49, and get free shipping with delivery in 2 business the U.S. (Certain delivery time or shipping cost exceptions may Conditions online for complete details. http://go2adc.com/terms
AutomationDirect is a non-traditional industrial controls ideas from the consumer world to serve your automation quality products fast for much less than traditional suppliers, every step of the way. See below . . . FREET
You insist on getting better service and you want it FREE. Our technical support has been voted best in service for 15 years in a row. And it won’t cost you a cent!
Before, during, and after any sale, contact us with questions and we’re glad to help, http://go2adc.com/support
For over 25 years, our primary focus has been customer service. Practical products, great prices, fast delivery, and helpful assistance. But the intangible value of customer service is something that cannot be faked, automated or glossed over. Our team members here at AutomationDirect.com approach every day with one goal in mind - serve the customer. If the answer to any decision is “Yes, this is good for our customers”, then we do it, whether personally or via self-serve features on our site.
Donald in STUDIO CITY, CA: “Automation Direct is now my one stop shop for all pneumatic components. They have the biggest selection of parts, and the shipping is prompt. No more searching the internet for this part and that part. Highly recommended!”
Gary in ORANGE BEACH, AL: “Not only are the products high quality, numerous and easy to choose on the website, THE PRICES ARE REALLY GREAT! Example, we looked at VFD (Variable Frequency Drive) from several suppliers, Automation Direct was about 1/2 the price, and we see no reduction in features, reliability, and setup. Really, why buy anybody else’s VFDs?”
Murph in Chicago, IL: “Love this product, I specify materials for breweries and distilleries and all of the panels I design are exclusively AD. Love the fact that we can get replacements sent to anywhere in the US in 2 days. Tech support has been consistently excellent.”
David in HOMERVILLE, OH: “AutomationDirect has great customer service and support. When I get stumped...they always quickly help out and get me going. They know their products. Very friendly staff, make me feel like I am their number one customer.”
Brian in GARDNER, MA: “I have been a customer since Automation direct was PLC Direct. All the products that I use hold up to industry standards. I have always been pleased with Automation Direct. Their web site is by far the best on the web. And as far as tech support goes questions are answered quickly and precisely without having to jump through service contract hoops.“
We’ve shopped around to bring you the most practical industrial control products that are in-stock, ready to ship and at the right prices!
If you’re a plant facility manager tasked with reducing energy costs and minimizing the facility’s carbon footprint, the compressed air system likely offers the greatest opportunity to address both tasks. Does your compressed air system consist partially or entirely of centrifugal air compressors? Then implementing a load sharing control system may substantially reduce energy use and carbon footprint.
To maximize potential Return on Investment (ROI) of a load sharing control system, it is critical to address both the supply side and demand side of the compressed air system. You’ll want to begin with an air system audit. The project manager should compile a list of audit objectives and expectations to share with an independent auditor that specializes in compressed air systems. There are many firms that offer energy audits for an entire facility. While these firms may do an acceptable job on the supply side of the system, a compressed air audit specialist typically provides more in-depth demand side analysis and also likely knows about the latest advances in supply side controls. These additional insights matter because controls are the most critical part of the plan in terms of performance and energy savings.
This article outlines and explains the steps necessary to implement an intelligent load sharing system controller applicable to facilities with multiple centrifugal compressors.
1. Set objectives and expectations for compressed air system audit.
a. Collect data and provide in Excel format with final report for internal review. Data readings should be collected at least every 15 seconds, averaged into one-minute intervals.
b. For larger systems, particularly with multiple centrifugal compressors, the use of insertion-type flow meters in the air piping and power meters on the compressor is recommended.
c. Request histograms showing percentage of time at flow and at power, with at least one full week of data.
d. Focus on clean-up of equipment, including pressure drops across dryers and filters. If desiccant dryers are in use, confirm purge pressure is set at factory recommendation. If purge pressure is not at factory recommendation, confirm purge pressure. Verify desired operating pressure dewpoint is achieved, either from the dryer control panel or with a portable dewpoint monitor installed immediately downstream of the dryer.
e. Another supply side focus is pneumatic equipment that creates dynamic pressure drop in the system, such as fast acting solenoid valves. Point of use pressure transmitters can log data showing the impacts of these production components on the system.
f. Identify opportunities to increase system performance by installing storage tanks, whether they are in the compressor room or in the facility on the demand side.
4. Evaluate load sharing designs for multiple centrifugal installations or systems with a mix of centrifugal units and rotary screw compressors.
a. Pressure bumping strategies – Individual centrifugal compressor set points are bumped in order to keep them operating in turndown range. Bump intervals are usually below 1 psig, typically in the 0.25 to 0.50 psig range. This control design keeps all units operating in turndown before any compressors begin to blowoff.
g. Test for leaks facility wide, showing location and volume of leaks. Estimate ROI based on cost of repairs vs potential savings.
h. Identify applications where compressed air is misused. For example, blowing with full pressure compressed air is a common misuse. Using low pressure nozzles with amplifiers and low-pressure blowers are more efficient solutions.
2. Become familiar with the various types of compressor controls.
a. Start with the compressors currently operating in the plant.
b. In many cases, audit report recommendations may include a new compressor or compressors, so take time to understand control methods that differ from what you have experience with.
c. Request data on unloaded power for rotary screw compressors and blowoff points for centrifugal units. Control curves for various concepts show best case power vs load.
3. Understand flow gaps. This requires knowledge of existing or future compressor controls and how they will impact opportunities to reduce or eliminate wasted energy based on flow profile (histogram time at flow).
b. Inlet guide vane (IGV) and blowoff valve (BOV) control – A local compressor controller operates both valves keeping the compressor in turndown range, again turning down all units before any units go into blowoff. Some companies offering this design require that their compressor controller be installed on the units. Other suppliers may provide a separate, wall-mounted interface box, integrating all compressor operations together.
c. Load shaping – Large volumes of storage and, in many cases, boosting pressure in one or more of the tanks, provides significantly higher pressure than plant operating pressure. The design scheme includes small horsepower boosters and flow control valves to reduce pressure out of the high pressure tanks. Typically there is a trim compressor (or compressors). The control logic is to bump centrifugal operating pressures to keep them operating in turndown range when necessary.
5. Properly size the header pipe to minimize pressure drop.
6. Consider installing permanent flow and power monitoring equipment after completion of the audit.
7. Plan for the future. Is system demand expected to increase or decrease in the foreseeable future?
Centrifugal compressors utilize dynamic compression, converting kinetic energy to pressure energy. Ambient conditions, as well as cooling water temperature, impact flow and power performance. If the final audit report recommendations include performance curves, always request that the curves reflect performance in standard cubic feet per minute (scfm), which is 14.7-psia, 60°F and Dry Air (0% RH). This is important when looking for control gaps.
Eliminating blowoff is critical to maximize centrifugal compressor system performance. Often it is the single greatest opportunity to reduce power costs.
Figure 1 depicts a standard performance curve with pressure line, surge line, requested flow, maximum flow,
Inlet Guide Vane (IGV) positions and turndown. Pressure line is the operating pressure, requested flow is anticipated required flow, maximum flow is peak compressor output at operating pressure and surge line is the natural surge of the unit at operating pressure. Natural surge – the point on the curve where the surge line crosses the pressure line – is to be avoided, as it is the point where flow reverses, possibly damaging the compressor. The curved colored lines show IGV positions by angle, with 90° being fully shut, 45° being half open, and 0° fully open. Minimum flow is the point where the natural surge line crosses the pressure line, in this case 2,500 scfm @ 120 psig.
During commissioning, a control line will be set up to protect the compressor from natural surge. The IGV will throttle shut as pressure rises (flow drops). Once the compressor reaches maximum turndown, the blowoff valve will begin to open in order to prevent the compressor from surging.
In Figure 2, the point where the red dotted line (control line, just below the natural surge line) crosses the pressure line illustrates the new, site-adjusted blowoff point. It’s common to set the control line 5-8% below the natural surge line. Job site turndown percentage and blowoff flow point will be less than what is shown on a standard performance curve. Jobsite blowoff point is now approximately 2,650-scfm @ 120-psig.
Lubricated rotary screw air compressors offer four types of control: inlet modulation, geometry (also known as variable displacement), load/no load and VFD (variable frequency drive, aka variable speed drive or VSD). Oil-free rotary screw compressors offer load/ no load or VFD (VSD). Note that the VSD curve is based on utilizing a variable frequency drive motor (in lieu of induction motor with VFD drive).
Figure 3 shows the various controls in percent load (horizontal axis) versus percent power (vertical axis) under ideal conditions.
Every air system has unique performance characteristics, therefore the curve data shown above may not reflect actual, real world control performance. System design characteristics influence compressor performance. Factors such as storage tank volume, header volume, operating pressure band, number of compressors and flow events suddenly reducing system pressure can all affect system efficiency. The VSD curve shows a linear relationship between percent load and percent power, which is based on the unit shutting off and remaining in standby at loads below maximum turndown/minimum flow rating of the compressor.
Control gaps exist in nearly all compressed air systems. A control gap is a flow window where demand is too low for the trim compressor to run without blowing off, but too high for it to unload and shut down. Eliminating control gaps from your system can be difficult. It’s important to understand where they exist, and why. Understanding control gaps will enable plant personnel to choose replacement equipment and system improvements that may eliminate gaps.
Control gaps for centrifugal compressors are sometimes more difficult to eliminate than they are in rotary screw systems, especially when all the compressors are rated for similar flows. Utilizing compressors of various capacities and operating pressures can reduce or eliminate gaps.
Fully understanding the plant flow and pressure profile is key to unlocking solutions. Figure 4 shows flow gaps in a system with three centrifugal compressors. One unit is new with an inlet valve utilizing IGV’s, and two are older units using butterfly-style inlet valves. The turndown range of a centrifugal compressor utilizing IGV’s on the inlet is considerably wider than on a unit with a butterfly inlet. A and B show the flow gap where #3 Turbo would be running in blowoff, and the tank volume required to store the flow gap cfm for one minute. Pressure band
Figure 5: Histogram Showing Percentage of Time in Various Flow Ranges.
Courtesy: Atlas Copco Compressors Figure 6: Compressor Control Gaps with Two Centrifugal Compressors & 1 Load/No Load Screw.
Courtesy: Atlas Copco Compressors
be somewhat misleading. The screw compressor could have a high cycle interval or be running in unloaded condition. The histogram in Figure 5 will help determine if the fixed-speed screw is the right choice for the system.
Courtesy: Atlas Copco Compressors
width on turbo compressors is typically low, therefore the storage volume required to cover a flow gap for only one minute is generally large, as illustrated.
Figure 5 is a histogram illustrating the system demand profile as percentage of time in various flow windows. Histograms are useful for identifying flow gaps, where system compressors and local controllers are not capable of efficiently meeting system demand. This can waste a tremendous amount of energy. Thorough analysis of the flow profile allows for correctly sizing new or replacement compressors. Figure 5 shows minimum through maximum flow, in 300 cfm windows.
Figure 5 illustrates how often the equipment listed in Figure 4 is in blowoff (red bars). In flow gap A, #2 turbo is blowing off 12.8% of the time. In flow gap B, #3 turbo is blowing off 30.3% of the time. This system, as currently configured, is blowing off and wasting energy 43.1% of the time.
Courtesy: Atlas Copco Compressors
Figure 6 displays control range in the same system with two centrifugal compressors and one load/no load rotary screw. The graph shows no flow gaps, however that can
Figure 7 shows control range in the same system with two centrifugal compressors and one VSD screw. The graph shows no flow gaps, but that also can be misleading. The VSD screw compressor could be running in start/stop if trim demand is below minimum flow (speed). Compressor control design could impact performance near the minimum flow range of the compressor. Some VSD screws operate in load/ no load below minimum flow, therefore providing a wider range of capacity resulting in increased efficiency. Again, using the histogram showing time at flow will help determine which type of VSD screw is the right choice for the system.
System flow profile has a significant influence in selecting the correct equipment to reduce or even eliminate control gaps.
Storage tanks are often the most economical performance investment to make in a compressed air system. Header size and length can be misleading with respect to volume in gallons. For example, 500’ of 8” header may sound like a lot of storage, but it is only 1,305 gallons by volume. Every air system is unique, so no rules of thumb consistently apply here. Figure 8 shows equivalent gallons of storage versus 1,000’ of various pipe sizes. From a value standpoint, tanks provide a much better performance value improvement compared to designing a system that relies solely on header capacity for storage.
Implementing a load sharing control system can drastically improve operational efficiency and reliability in a multiple compressor system. Permanent metering equipment with data logging capabilities will assist in assessing system performance as plant conditions change. Setting an efficiency metric will allow for investigating negative changes in efficiency. With experience, operators will be able to target supply side or demand side inefficiencies.
The realized return on investment is in the hands of the project manager or project team. Developing an action list, plus a list of requirements for implementation, will allow for setting realistic expectations. A well thought out plan will eliminate guessing and give the manager needed data to make the best investment for the facility. PE
Ensuring a safe, continuous supply of primary and specialty gases to support critical processes is important to many laboratories, test centers and industrial sites. Responsibility for making sure gas distribution systems are functioning at peak performance often falls to lab and reliability managers, engineers and operations staff. Unfortunately, many operations face limited internal resources and inefficiencies that can make it difficult to properly maintain these systems.
Figure 1: Undetected leaks and inefficient gas bottle usage can lead to extra spending if these issues go unresolved.
Courtesy Swagelok
If gas bottles are used inefficiently or leaks remain undetected, for example, facilities can accumulate unnecessary costs (see Figure 1). Some facilities also do not have accurate line drawings of the systems, which can make it difficult to diagnose problems. Finally, untimely setbacks and costly delays can occur if tests must be repeated or the results are deemed inaccurate.
To improve evaluations of gas distribution systems and identify any problems, facilities can hire experienced outside consultants to look at the systems with an unbiased eye and locate areas for improvement. Having this fresh perspective will often lead to the discovery of trouble spots that otherwise might be overlooked. The practice provides an opportunity to
establishes a connection between the highpressure gas source and the distribution system and ensures that gas can be safely fed into the primary gas pressure control or automatic changeover. Courtesy Swagelok
eliminate all previous assumptions and evaluate how a system has been built from the ground up.
Design inefficiencies, malfunctioning components or other factors can prevent a system from operating properly. For example, improper regulators can have an enormously negative effect on system performance. Choosing the right regulators is a specialized skill that not all facilities might have onsite, so it can be helpful
Figure 3: As the primary gas pressure control, the gas panel completes the first pressure reduction of the source gas and ensures it is delivered at the correct flow rate to the next stage of the system.
Courtesy: Swagelok
to work with a supplier to ensure these components are right the first time.
Since systems are complex, it is often difficult and time-consuming to address all of the issues facing gas distribution systems. Plant managers may be addressing other, more obvious challenges that need immediate attention, or they may not be aware of the issues the systems are facing altogether. This can lead to lingering
issues that can cost facilities money in the short and long term. To keep that from happening, an experienced outside field engineer can help build the system properly by specifying the best components and alerting plant managers to inefficiencies that may be present.
Most gas distribution systems focus on regulating the pressure of the gases they transport and usually are made up of four subsystems: a source inlet connection, a primary gas pressure control, an automatic changeover and a point-of-use control.
The source inlet (See Figure 2) connects the highpressure gas source to the gas distribution system. Importantly, the inlet must be built with appropriate cylinder connections, hoses, tubing, filters, vent, purge and relief functions. Some gas panels may not include a standard source inlet. Always verify componentry and that panels will use the correct cylinder connector. Some high-pressure and/or hazardous gases (including oxygen) also require the use of special construction materials.
The primary gas pressure control (see Figure 3) completes the first pressure reduction and ensures the source gas is delivered at the correct flow rate to the next stage of the system. Reduction is accomplished with either a single pressure regulator or through a dual pressure regulator arrangement. Pinpointing correct inlet and delivery pressures is challenging. It is important, for example, to consider the differences between media, such as ammonia that is bottled around 116 psi (8 bar) and nitrogen that can be bottled at 4351 psi (300 bar). Meanwhile, many bottles that use a two-stage pressure regulator may not, in fact, require one. This can be a cost-saving opportunity.
The automatic changeover (See Figure 4) seamlessly switches from one gas source to another to ensure an uninterrupted supply. This is performed through staggered set points of two pressure regulators, allowing the system to continue to operate as the primary gas source is changed. It is advisable to look for a solution that allows for varying changeover pressures to get the most use from gas bottles.
The point-of-use (see Figure 5) provides the critical last stage of control. Typically having a pressure regulator, gauge and isolation valve, these subsystems give operators a convenient and accurate method for adjusting pressure. Where varying line pressure between
Figure 4: The automatic changeover system seamlessly switches from one gas source to another to ensure an uninterrupted supply and helps to reduce wasted gas left in cylinders.
Courtesy: Swagelok
the primary gas pressure control and point-of-use is acceptable, a single-stage pressure regulator might be used to reduce cost and complexity.
Choosing quality components for gas distribution systems is critical to their operational success. If systems are constructed from high-quality components, the cost of maintenance-related labor will decrease, thereby increasing a facility’s overall profitability.
Gas distribution systems should also be designed so they can be serviced more easily. To reduce the amount of time it takes to access components for repair or replacement, facility managers should use compression fittings in place of threaded fittings. Not only do these fittings allow the flexibility to change components instead of replacing entire panels, they provide technicians with the ability to work more efficiently while also reducing the possibility of doing accidental damage to components as the repairs are being done.
In addition, facilities should emphasize the need for high-quality regulators because they are such critical parts of gas distribution systems. The best quality regulators have been tested and rated for millions of cycles and can last as long as the system is in operation. Installing proper regulators can eliminate the need to replace them at all, lowering labor costs and potential downtime while simultaneously improving the performance and safety profiles of the systems.
When in doubt, it may make sense to bring in professional pressure control advisors to evaluate the system for upgrade opportunities, provide guidance on proper regulator sizing and selection, and oversee the design and assembly of engineered solutions. Advisors who have familiarity with the particular challenges of gas delivery can offer:
• Suggestions for how existing systems can be modified to meet new requirements (often, old panels are disposed of unnecessarily – be sure to ask about solutions designed to last)
• Options for easy procurement of gas panels built and tested by experienced installers working in suitable facilities (potentially reducing time, cost and risk as opposed to panels assembled onsite by less-practiced installers)
• An unbiased recommendation that puts the needs of the business first (an advisor having no prior owner-
ship stake in the system or its operation can offer impartial advice)
Advisors can also help prevent the leakage of toxic and flammable gases, as well as make sure the panels are clearly labeled and the instructions are clear. Finally, they can offer guidance on how to design systems properly, so they are easy to operate and troubleshoot (See figure 6).
No matter what needs to be accomplished with a facility’s gas distribution system – whether it is a complete replacement or just trying to understand why the facility is replacing gas bottles before they are empty – external pressure control specialists can help diagnose problems and suggest cost-effective solutions. These contributions will help facilities maximize their investments in gas distribution systems and protect their bottom line. PE
identify system upgrades, inform regulator sizing and selection, and guide the design and assembly of engineered solutions.
Arace is underway to find the best ways to extract factory data and connect it with cloud computing services. The finish line may be a little hard to discern, but end users and OEMs alike want to collect this data, and then use third-party apps or their own self-developed analytics to gain value by improving their operations.
Connecting all sorts of operations technology (OT) systems up to on-site and cloud-based information technology (IT) resources is the foundation of industrial internet of things (IIoT) and Industry 4.0 projects. These connections are also necessary for performing data logging, product tracking, analytics and visualization. While some new field-located equipment will arrive with native cloud connectivity, most users will have many legacy systems they would like to tap into for data access.
However, stitching together a complete field-tocloud data connectivity solution is not a good option for most applications. It is complex to determine the
best hardware, software and networking elements to deliver reliable and secure performance. Instead, these users need a dependable off-the-shelf solution so they can focus on the field and cloud endpoints.
This article discusses what users should look for when selecting a cloud platform to support their IIoT projects.
Industrial manufacturing operations need data to fully take stock of their equipment assets, raw materials, output and production efficiencies. There is a lot of different data originating from a variety of sources, and it can be difficult to know where to start. An IIoT maturity model can help users understand their current state and where they can make improvements (see Figure 1).
Many companies are well under way with using programmable logic controllers (PLCs) and PCs to perform local automation and computerization of their equipment and systems. They may also have established good network connectivity on-site.
But the next steps into Industry 4.0 call for connecting source data to more elaborate — and typically cloud-based — resources for analyzing, predicting and adapting operations. At the very least users will want capable visualization of their operations, but they will quickly find it important to develop their own cloud-based analytics and learning systems in a way that carefully protects their intellectual property.
Some users might build their own computing solutions from the ground up, but most are far more likely to integrate with and leverage widely used systems like:
• Microsoft Power BI and Azure
• Tableau business intelligence and analytics platform
• Ultimo asset management
End users and OEMs are more interested in getting to the valuable end results of data storage and analysis than they are in building a solution to transport this data. This is why they need a flexible and secure data handling solution which can be set up quickly and maintained easily.
There are many connectivity, security and reliability requirements for an IIoT data connectivity solution. Among the most important is an open platform without a vendor lock to provide the most flexibility moving forward. Other key requirements are:
• Intelligent routers for connecting to many PLCs and human-machine interfaces (HMI)
• Support for the most common OT communication protocols
• Simplified cloud logging (real-time and historical) for PLC data sources
• Multiple IT integration methods, such as an API and web hooks
• Flexible licensing and management services
• Comprehensive security support, certified to ISO 27001
• Connection reliability
A primary goal is to convey data into the cloud, while a secondary need is making that data accessible to the users and applications that need it.
Remote connectivity and monitoring solutions for industrial IIoT projects must include hardware and software elements to connect with all OT data at a site and transport it to the cloud. One of the best architectures for this involves an intelligent router on site, connected seamlessly to a cloud platform via the internet (see Figure 2).
Not only must the router support all standard OT communication protocols, but users should be able to configure and download router settings from the cloud without visiting the site or adjusting the target PLC programs. A connectivity solution of this type can be added to any installation without impacting the underlying and existing automation systems, and it can be optimized for logging both real-time and historical data to the cloud (see Figure 3).
Access to this data can be accomplished in many ways. A mobile app will provide basic data visibility to any authorized users. Web hooks can tie to external applications to provide more advanced functionality, such as generating text/email alarms upon problem conditions so service teams can respond rapidly. The most capable method is usually an application programming interface (API) as it enables cloud computing services to dynamically access any data needed from the cloud database.
Licensing associated with any cloud solution should be flexible, simple and affordable. Users need the capability to easily add and remove tags without
getting bogged down with complex tag-count schemes or other issues. From a system management standpoint, cloud solutions should incorporate centralized monitoring and logging to detect performance anomalies.
Figure 2: An AutomationDirect StrideLinx router can seamlessly connect with PLCs and HMIs on-site, providing a cloudcapable remote connectivity and monitoring solution. Courtesy AutomationDirect
A natural concern when implementing any data access project surrounds its cybersecurity aspects. This is a complex subject, which requires specialized expertise and significant IT know-how if a user is building their own custom solution. The best way to address security is to select an off-the-shelf solution that uses coordinated routers and cloud services certified to ISO 27001 requirements. Routers should incorporate firewalls, reject outside traffic, use secure protocols over outgoing ports, provide comprehensive user access restrictions and include two-factor authentication. Third-party scanning and auditing should be employed on a continual basis by the hosted VPN service provider to detect any vulnerabilities in the network.
Reliability is created by removing single points of failure. Routers should be capable of failing-over from a primary/preferred network to a secondary/fallback network, whether the connection is Wi-Fi, 4G, or Ethernet. If a connection is lost, the router must include significant on-board memory to log data until the connection is back online and the data can be transmitted. Cloud services should be networked throughout dozens of servers at geographically diverse data centers worldwide to provide responsive operation and redundant storage and processing.
Once an end user or OEM has chosen an IIoT connectivity solution addressing the details indicated above, how might they use it?
A majority of users are relying on these solutions strictly for the data handling capability, while a growing number are also incorporating visualization capabilities to effectively create a remote/mobile HMI experience.
Many users are OEMs who deploy machines to many locations and need a consistent way to access them, while carefully segregating clients from each other. Increasingly, end users—or their designated systems integrators (SIs)—are rolling out IIoT projects using cloud solutions.
OEM Access
OEMs are not only interested in the performance and throughput of machines on a case-by-case basis. Many find it extremely valuable to consolidate data from
Figure 3:
VPN routers are optimized to work on-site and access PLC data, and then transmit it efficiently and securely over the internet to the StrideLinx cloud platform. Courtesy AutomationDirect
a fleet of deployed equipment, so they can perform deeper analysis, leading to better ways of optimizing operation or avoiding problems. This can include condition monitoring data like equipment temperature and vibration. Some cloud IIoT solutions can be ‘white labelled,’ so the OEM can offer these hardware and software services as a value-added feature with their own branding.
End users can employ a cloud IIoT solution that is scalable from one machine, up to an entire site or across many sites, to gather the data they need in a consistent manner. As with OEMs, sometimes this production, availability and energy usage data is needed for more advanced operational analysis. In other cases, end users need to track usage of raw mate-
rials through the production process, monitor on-site inventories of products or perform other tasks.
Creating a field-to-cloud IIoT solution from scratch is not feasible for most end users and OEMs because it requires detailed implementation and support for the required connectivity, security and reliability. Off-the-shelf solutions are available to address each of these aspects, making it easy to add IIoT capability to any existing on-site system, and to connect these systems to cloud resources for advanced processing. An end-to-end solution using intelligent routers and associated cloud services helps users of all types quickly establish a trustworthy IIoT system so they can begin realizing value and improve their operations. PE
Bill Dehner has spent the majority of his fifteen-year engineering career designing and installing industrial control systems for the oil and gas, power, and package handling industries. He holds a bachelor’s degree in electrical engineering with an associate’s in Avionics from the USAF. At AutomationDirect, Bill is a technical marketing engineer.
Lincoln, California — Gladding, McBean is a leading manufacturer of terra cotta products. Founded in 1875, the company mines clay from its own reserves and combines traditional methods with modern technology to create roof tiles, floor and paving tiles, clay pipe, ornamental pieces and architectural elements for buildings.
To streamline batching and mixing of clay blends for different products, the company installed five bulk bag dischargers and five pairs of flexible screw conveyors from Flexicon to automatically deliver weighments of bulk ingredients for blending of clay compounds. The system cut dispensing and weighing time for each batch by half and reduced out-of-spec material and scrap by 95%.
Clay is a natural material that varies in composition, so the company must determine the ideal ratio of ingredients for
various products. “We have to ensure that what we create in the lab will translate to the final material. The only way to accomplish that is to maintain precise control of production,” says Joe Parker, operations manager.
The clay is sourced from the company’s nearby mine, classified and loaded into bulk bags at the plant. Crushed, recycled ceramic material called grog is the other major component used in the manufacturing of terra cotta.
To prepare a batch, operators previously retrieved clays and grogs from bins, weighed them on a scale and transferred them to the mixer using an open trough conveyor.
The new batching system, supplied by Flexicon Corp., integrates bulk bag dischargers, flexible screw conveyors and a central weigh hopper, all of which are actuated by programmable controls, also from the supplier. The system enables Gladding, McBean to vary bulk bag discharging, conveying, weighing and mixing on a batch-by-batch basis according to recipes developed in the lab. A Human Machine Interface (HMI) includes options for automatic or
conveyor's feed rate to dribble before stopping it once the precise batch weight has been gained. The system weighs up to 30 batches per day, with improved accuracy and reduced labor.
Five, forklift-loaded Bulk-Out BFF model bulk bag dischargers stand side by side. An operator attaches a bulk bag to the steel lifting frame by sliding the bag straps into four Z-Clip strap holders. A forklift raises the lifting frame with the 2,000 lb (909 kg) bag of clay or grog intact into four self-centering cradles atop the discharger frame.
With the bag in place, the operator opens a 12 inch (305 mm) diameter iris valve, pulls the bag spout through it, and closes the valve before untying the spout. The operator can then open the iris valve gradually to prevent bursts of material into the hopper, and displaced dust from escaping the enclosed system.
hand-mode operation, as well as setpoints, adjustments, status, start/stop, completion and other parameters.
Once the recipe is programmed for a batch, each ingredient is conveyed by a flexible screw conveyor from a bulk bag discharger to a central weigh hopper. Load cells supporting the hopper transmit weight gain amounts to the controller, which steps down the
Flow-Flexer massaging devices on each discharger promote flow by raising and lowering opposite edges of the bag at timed intervals. To impart additional flow promotion, each floor hopper is equipped with a pneumatic turbine vibrator.
The clay or grog is transferred to the 40 cu ft (1,133 l) capacity central weigh hopper by flexible screw conveyors in two stages to accommodate the plant’s limited floor area and headroom. Each conveyor extends either 15 or 20 ft (4.6 or 6.1 m), depending on the position of the discharger and the need to route the conveyors under the roof trusses or between the truss components.
Each conveyor consists of a polymer tube with an inner flexible screw, which is driven above the discharge point, avoiding material contact with seals.
Material moves through the transition discharge adapter of the lower conveyor into the inlet of the upper conveyor. Custom-engineered masts support the top end of the first conveyor and the bottom end of the upper conveyor.
The upper conveyor gravity discharges into the weigh hopper, which is 4 ft (1.2 m) in diameter and suspended 19 ft (5.7 m) above the floor.
Most batches of clay mix weigh 1,000 lb (454 kg) or 750 lb (341 kg), Parker says, with a typical loading/ blending cycle requiring 10 to 15 minutes. After blending with water, the batch is delivered to the appropriate process elsewhere in the plant.
“The system allows us to blend up to five different types of clays or grogs,” Parker says. For example, the dischargers might handle bulk bags of two kinds of clay and three grogs, delivering the correct amount of each for a given batch.
“The versatility of the system makes it cost efficient,” says Egidio Modolo, plant manager. “It’s a simple, straightforward process, and an efficient way to measure and transfer clay to the blender.”
He notes that no maintenance was required in the six months since installation, and that throughout discharging, conveying and mixing the enclosed system prevents dusting.
“We can make a small or large batch, and alter the recipe and raw materials,” says Parker, adding, “Currently we have two different clays and three different grogs. We can change that any time.”
“It gives us the ability to be accurate in spite of clay’s unpredictability,” Parker says. “Now we have a tool for our team in the lab to create a mix that will allow us to be very precise with our final product specifications.”
Microscopically, clay is very abrasive, Parker says. “It will destroy just about any equipment you use, over time. One of the reasons we chose this system was for simplicity of maintenance due to few moving parts, which should minimize downtime."
Having the system in place, Parker says, “opens-up possibilities for other types of products and materials that need the same type of batching accuracy.” PE
Figure illustrates how microphones impact the ability to 'see' problems.
Courtesy: Teledyne
Compressed air is one of the most expensive and essential utilities to many industries. Often, it costs more than does many of the uses of electricity, natural gas or water in maintaining and operating a plant. Yet up to a third of that compressed air is lost annually due to leaks and inefficiencies. Ultimately, finding and fixing leaks is vital to lowering costs, operating efficiently and reducing the organization’s carbon footprint while potentially improving key stakeholder and investor relations.
Leaks are a large source of wasted energy for compressed air systems, and according to the Office of Energy Efficiency & Renewable Energy, those leaks approximate 20-30% of the total air compressor output within a
facility. Further, leaks contribute to system operation problems such as fluctuating system pressure, which can cause air tools or air-operated equipment to function less efficiently and possibly affect production. Unknown leaks may also require excess compressor capacity, potentially requiring additional compressors that may otherwise be uneeded, resulting in higherthan-necessary costs. They can also lead to decreased service life while increasing maintenance needs due to unnecessary cycling and increased run time.
Alongside energy and resource preservation, costs can be lowered significantly through proactive leak detection. The Office of Energy Efficiency & Renewable Energy conducted a study at a chemical plant that undertook a leak-prevention program following a compressed air audit, proving how plant costs can be lowered significantly through remediation efforts. By remediating just the 10 largest leaks found at the plant, operators could generate 70% of the overall potential cost savings.
To improve energy standards, reduce excess waste and align with regulatory, tax and investor expectations. Many industrial organizations are also looking to align with ISO 50001 energy management standards. Like other ISO management system standards, ISO 50001 certification isn’t mandatory, but it does require organizations to develop policy for more efficient energy use. This includes fixing targets and objectives to meet the policy; using data to better understand and make decisions about energy use; measuring the results; reviewing how well the policy works and continually improving energy management. When organization leaders decide to implement these standards it empowers them to understand the organization’s respective carbon footprint and show external parties and investors that the business has implemented an effective energy management system.
Whether an organization plans to implement ISO
50001 or simply wants to improve plant efficiency for cost savings, identifying compressed air leaks is vital, but they can be particularly tricky to identify in a noisy manufacturing environment. Therefore, identifying the most appropriate methods or tools for the situation is crucial to a successful program.
The traditional leak detection tool is a specialty soap solution, which entails saturating a suspected leak area with an approved soap solution. Simply stated, if a leak is present the soap will begin to bubble. This method works if the leak site is known and the system is well pressurized. However, in cases where the leak site is unknown, this can be a cumbersome process where operators may need to apply the solution to the entire suspected piece of equipment in hopes of pinpointing the leak. Therefore, soap bubble tests can become time consuming and messy without necessarily providing sufficient data to confirm accurate leak sizes and flow rates.
Ultrasonic (acoustic) leak detectors offer a solution that can detect leaks using a single microphone system operating around 40 kilohertz (kHz). This method relies on "heterodyning" to enable the operator to distinguish between noise generated by the leak and background noise. Heterodyning converts high frequency noise to lower, audible frequencies, which the operator must be trained to recognize based on the sound characteristics. The microphone is scanned back and forth over the process piping being inspected until a suspected leak is found and measured. False alarms on non-existent leaks and missing actual leaks can be common for inexperienced inspectors. Furthermore, manually moving the microphone around equipment to locate leaks can be time consuming and may put the operator in harm’s way. In addition, this system requires significant training time to master.
High definition (HD) acoustic imaging devices that rely on a series of specialized integrated microphones can be up to 10 times faster at detecting leaks compared to traditional methods, such as the soap bubble and single-microphone ultrasonic options. Generally, the higher number of microphones, the better the acoustic performance. The optimal choice in this case would be MEMS (microelectron mechanical systems) microphones, which are small, consume less power and provide better performance and stability than other systems.
HD acoustic imaging provides precise acoustic images that visually display ultrasonic information, even in loud environments. Images are transposed in real time on top of a digital camera picture, which allows
for pinpoint accuracy of the sound source. Depending on the tool, it can be equipped with networking capabilities that automatically save images to the cloud for post-inspection review and processing. This allows for easy access to stored files and easier separation of sound sources for a deeper analysis and classification of the problem back at the office. When paired with a regular maintenance routine, acoustic imaging can help facilities save money on utility bills and delay the potentially large capital expense required to replace compressors and other related equipment.
Some handheld devices only require one hand to operate along with the ability to conduct accurate assessments more than 100 meters away for safe problem detection and analysis, further improving safety and convenience. Operators can conduct a quick scan of large areas from a safe distance without the need to physically touch machinery or shut down the production line.
Noisy plants and manufacturing environments can make it nearly impossible to detect a leak with the human ear, so frequency range is crucial to leak detection technology. The most effective frequency range for detecting compressed air leaks is between 20 and 30 kHz, as that range aids in distinguishing compressed air leaks from the background noise in a plant environment. The amplitude of machinery noise typically peaks below 10 kHz and trends down to zero at 60 kHz, and since there is a greater difference between air leak noises and background noises between 20-30 kHz compared to higher frequencies, it’s easier to detect the air leak in this range.
Nevertheless, background noise interference can still be an issue. In this case, devices must be able to differentiate sound sources that resemble a leak from other interfering sounds. The majority of acoustic cameras on the market require the user to manually filter out interfering noises using sliders to change the frequency range, but the ideal device can automatically detect sound patterns that resemble those of air leaks and remove interfering noises for both single and multiple sound sources using advanced on-camera, AI-based filters. In essence, these
Air leak noise versus background noise compared to find the optimal frequency in a noisy environment.
devices can recognize whether the sound resembles an air leak or background noise, without manual user intervention, much the same way people are able to distinguish the same note played by two different instruments.
Microphone quantity also plays a large role in leak detection – specifically with very high frequency sound sources. To accurately hear these sounds, acoustic cameras must have a multitude of microphones, preferably
close to each other, otherwise issues of spatial aliasing will occur, leading to erroneous results and sound sources displayed at improper locations.
Beyond cost savings, HD acoustic imaging provides organizations with an effective tool to mitigate inefficiencies, reduce the overall carbon footprint of plant operations and improve the safety of personnel who operate and test air compression equipment.
Ultimately, preventative leak detection measures can play a vital and strategic role in the sustainable future of manufacturing environments. Compressed air leak repair and mitigation can be a fast way for organizations to reduce energy consumption and enjoy the requisite cost and safety improvements. With energy being one of the largest controllable operating expenses for organizations using industrial compressed air systems – resources, time, money and key stakeholder relationships can all be safeguarded. PE
Rob Milner is the global business development manager - condition monitoring at Teledyne FLIR.
The SIMATIC S7-1200 offers an efficient and precise automation solution for complex control tasks. With its flexible and modular design and integrated communication and technology functions, the S7-1200 proves to be the ideal choice for endless applications.
Extensive communication versatility including PROFINET, PROFIBUS, IO-Link, and industrial ETHERNET
Up to 14 DI, 10 DO, and 2 AI/AO without expansion modules
Further digital and analog expansion available with IO modules and signal boards
OPC UA data access enables horizontal and vertical communication
Fully integrated into the TIA Portal
At Automation24 we offer all the components needed to complete your S7-1200 control system at the best prices!
automation24.com/s7-1200
Need it fast? We've got you covered!
All items shown in stock on our webshop ship the same day you place your order!
CPUs
Precision solution for basic control applications
Compact and modular for easy commissioning
Comprehensive offering with a variety of I/O configurations
Ethernet and PROFINET ready
Digital modules available up to 16 DIO
Analog modules available up to 8 AI and 4 AO
TC and RTD modules for accurate temperature measurement
Compact signal boards can be front mounted on the CPU
Communication processors
Communicate to HMIs, controllers, drives, and more
PROFIBUS, IO-Link, LAN, and LTE networks
Standard modules and compact devices available Serial (RS232, RS422/485) communication also supported
STEP 7 Basic and Professional V16 versions available
Floating licenses included
Ladder, Structured text, and many other languages supported
Integrated library of drag and drop engineering functions
We can help! You can reach our support team Monday through Friday from 8 am – 6 pm EST.
Awhole market exists to serve the inspection needs of the oil and gas industry, ready to catch defects and failures before they impede safety and operations. Yet inspection can be costly, time consuming and in many cases, inefficient.
What do we mean by inefficient? Let’s take pitting as an example. When inspecting a pipe for pitting, based on material science, fluid service and a host of other factors, pitting is more likely to occur in certain areas. Target inspections proceed accordingly. However, if the inspection returns a clean bill of health, can someone really be confident that this result is reflective of the pipe’s overall condition and that risk has been managed effectively?
Without 100% coverage, a lack of defects and failures in inspection regimes success could come down to luck. However, while complete 100% inspection will likely deliver ultimate confidence, it’s a time consuming and expensive approach that few operators are able to undertake for every single threat. But, it is no longer the only option.
While risk-based inspection (RBI) methods go some way to focus inspection efforts, as digitalization takes hold, more intelligent and efficient approaches are becoming available, which is changing the way value is derived from inspection.
With traditional methods, asset and integrity managers only gain value from inspections when they identify a defect or failure; therefore, many inspections return no value. With a data-driven approach to asset integrity management, all inspection outcomes provide a return.
Most operators are familiar with the benefit of running statistical analysis on traditional inspection data to inform their asset integrity plan. The latest iteration of this approach takes it a step further; collating leading real-time (or near real time) data from existing operational sources such as process conditions (temperature, pressure and other parameters) to create a degradation model of an operator’s assets.
The predictive integrity management plan produced is based on event-driven inspection whereby inspections are primarily motivated by changing process or environmental conditions, for example, scenarios which may indicate accelerated corrosion, wall thickness loss, degradation or fatigue issues.
Every inspection carried out helps to validate the model’s assumptions about the degradation of each asset and fills in data gaps, thus building a more robust model and methodology by which inspection and integrity activities are enacted.
Operators can confidently focus their resources on areas where changing conditions require real-life validation to ensure risks remain understood, and that every inspection effort made provides value to the asset team. While using a data model will see most operators expend a similar amount of inspection effort, the model continuously validates the need for those inspections while significantly improving their return on investment too. Even with assets nearing end-of-life there are benefits. Anecdotally, operators using IMRANDD’s data model AIDA see a typical return on investment in less than a year and cost savings in a matter of weeks or months.
The are many immediate benefits of this new style of integrity management. Leveraging real-time data means that engineers no longer need to wait until an asset is beginning to degrade to assess condition. This change in strategy can have a significant impact on profitability as well as lengthening an asset’s lifespan. And, it can also help operators better achieve overarching business goals such as their commitment to operating sustainably and responsibly; for example, by reducing flights, optimizing resources and/or reducing fugitive emissions.
What’s more, most operators will have data readily available, which simply needs to be extracted and analyzed in a different way to enable the integrity team to be more planned and effective in managing plant maintenance.
Despite the obvious benefits, it can be quite difficult for asset and integrity managers to move away from the traditional mindset – not least because of the way
industry sees safety and standards as one and the same. This gives little room or incentive for teams to innovate more efficient ways of managing integrity.
The point of these standards is to reduce the risk of operation to as low as is reasonably practical (ALARP). However, if operators aren’t using readily available digital technologies that can further reduce risk – is ALARP being achieved? It seems that a shift in perception is still required for industry to recognize the inefficiency of relying on only historic data and lagging indicators.
Inspection results are only truly valid on the day they are taken. Yet some reports are not processed for weeks or even months – putting the operator at risk of making decisions based on outdated information. On the other hand, using real-time data enables asset and integrity managers to react quickly to potential issues before they occur, in much the same way that rotating equipment is treated. An operator would never wait to see if a turbine has developed a crack because by then it would be too late. Instead, the model is constantly assessing the data to generate early warning signs so that timely interventions can ensure safety.
In the spirit of regulation, to be responsible as an industry, people should constantly strive to go above and beyond the existing standards. With all the data that is available, that spirit is now digital. IMRANDD’s predictive modelling and machine learning solutions are a prime example of data analytics tools that push the industry to achieve more.
With the ability to gain insights that enable operators to rapidly react to changing operating conditions, asset and integrity managers can at the same time have the opportunity to manage static assets more proactively, leading to reduced failure and reduced impact. It is not an incremental improvement. It’s an order of magnitude better than the traditional approach that’s been employed for the past 20 to 30 years. It’s redefining what it means to be reasonably practical. PE
Ronald Cartwright is head of operations for IMRANDD. IMRANDD combines engineering expertise and tactical implementation with commercial understanding for its clients in the oil & gas industry.
Modern manufacturing processes produce a vast volume of data, and as sensors become more numerous on industrial shop floors with the spin-up of the IIoT, even more data is now available.
In the past, data was typically used in a very conservative manner—primarily to let users know, in retrospect, what happened on the shop floor. The data could then be used in regulatory reports, and in some cases, to discover trends and identify issues.
However, as artificial intelligence (AI) and machine learning (ML) gain prominence, the sky is the limit for what can be accomplished using shop floor data, most notably identifying patterns, and then using this information to speed time to market and optimize production.
Figure 1: The ideal Model 1 trendline is seldom realized because, left unmitigated, a model’s accuracy diminishes over time, like the Model 2 and Model 3 trendlines.
Courtesy: Siemens
Experts once believed computers could only compute algorithms understood by humans. They also assumed there was no way to teach software how to exercise intuition—such as identifying whether a picture was of an adult or a young child, a cat or a dog—but data scientists now know this is no longer true.
With ML, humans have succeeded in teaching computers to do intuitive tasks, without being able to explicitly explain the tasks to the computer. Simply by feeding the machine enough different examples— such as pictures of dogs and cats, and then identifying each accordingly—the machine can learn to determine the subject of new pictures by identifying patterns within the examples. Similarly, computers can now tackle industrial issues once considered unsolvable by using ML, without complex coding.
Devices on a plant floor can feed massive amounts of production process data into a computer’s ML algorithm. For example, in quality assurance for a printing process, the ML algorithm can detect use of an incorrect paint color, inaccurate position, missing details and other defects. The machine can learn to test for these and other qualities over time without the need for a programmer to predefine all test parameters. The analyzed details of the final printed product determine whether the subject passes or fails an overall quality test.
As a computer becomes more familiar with production procedures, it can associate manufacturing process data prior to the end results of quality testing. This information can be used to predetermine, in near real-time, whether a particular production batch will pass quality tests. Oftentimes, process adjustments can be made to save a batch otherwise heading for quality test failure. By identifying main contributors to quality within the collected dataset, the computer can quickly identify patterns humans cannot automatically adjust processes or alert operators so they can act.
Unfortunately, ML implementation is not simply plugand-play. Like a student, a machine requires proper instruction to execute its tasks with excellence.
Collecting high-quality data is the greatest initial challenge to the ML implementation process, and this step is
sensors, such as cameras, microphones, thermometers and others. After importing and preprocessing, the ML model analyzes the data and infers a model output (see Figure 2).
critical because a machine cannot learn from corrupted, noisy, distorted or misclassified data. Proper collection includes recording data in a standardized format, sometimes requiring translation from its raw format.
Following data collection, an ML model requires a labeled dataset for learning. This dataset is categorized by class—such as OK or not OK, pass or fail—but many organizations do not have experts and resources available to identify and label these ML patterns.
ML models often rely on static historical extracts of generally dynamic data for training. However, production data may change rapidly in an unknown and undetected manner after models are implemented because of variable process conditions, dynamic human intervention and other causes. This typically leads to the decrease of a model’s predictive performance and reliability over time (see Figure 1).
When a model misclassifies properties or presents results with low confidence, it is necessary to retrain it with a new or additional labeled dataset.
A typical ML application receives data input from
For example, in a quality prediction use case, the model output is often a score related to product quality, or the probability of producing an acceptable versus a faulty part or batch. The ML application provides this quality prediction to various consumers, like a manufacturing execution system capable of adjusting process parameters for optimization, or simply for operator visualization.
To prevent model accuracy slip over time, the ML application must compare its predicted output to the actual results, adjusting future modeling in accordance with the model’s deviation from reality. This deviation provides actionable insights to the next iteration of the model for incident handling and bug tracking. Through this act of refining, the model can learn to recognize new patterns in data streams.
When sensors and other field equipment send signals to on-site computers and servers—and to the cloud in many cases—they help create an inventory of a facility’s current state. This helps inform operators, and the information can be used to improve productivity, ensure safety and adjust to new requirements.
A digital twin facilitates the process of continuous optimization like no other tool, and data collected from sensors on the shop floor can enrich efficiency dramatically.
This type of tool not only reveals a defined product created from specific materials or ingredients with a known weight, produced on a certain date with a specific quality—but can also reveal the humidity, temperature and many other factors impacting the final product, and then correlate these environmental factors with the product’s outcome quality. This complete dataset enables creation of a digital twin of the process and product, which is a complete virtual representation of the product and how it was produced.
In cases where real data to train a model is difficult to generate, an engineer can create a digital twin, running simulations to create the necessary product dataset to train an ML model. Digital twins enable better and quicker product development because simulation technology accelerates design and testing long before any physical prototypes are produced. Digital twins also boost design efficiency because they enable developers to try out and compare more configurations than possible with physical models (see Figure 3).
For example, a digital twin can be used to increase the energy efficiency of a new building prior to
construction.In addition to incorporating visualizations of the building’s geometric elements, the digital twin can include project schedules and budgets, plus data regarding the building’s energy supply, lighting, fire protection and operations. As a result, engineers can optimize the building’s future climatic impact before even breaking ground.
Additionally, a digital twin continues collecting data throughout its lifecycle. This can include information about physical stresses, components that have failed or how an object—such as a milling machine, an aircraft or a building—is operating. Such information supports optimization during operations, and it aids designers, architects and engineers in preparing the next generation of a product.
To create accurate digital twins of real technical systems, developers must understand the system’s material values, design data, functional workflows and surrounding laws of nature. The digital twin must also record discrepancies between modelled and real performance values of the system to maintain accuracy over time.
Using ML and a computer’s inherent fast processing of large datasets, the model can reveal highly complex connections a human could not determine, and the computer can invoke the ‘ant method’ to efficiently optimize the model.
In nature, colonies of ants use a scent to mark their path on their way to a food source. Because ants taking the shortest path cross it more often, marking it more frequently than those on longer paths, the shortest route becomes more strongly scented than all others over time.
Similarly, ML-based modelling utilizes this method to optimize production processes over time because simulating all conceivable procedures and comparing them against each other all at once would exhaust computer processing resources. Instead, the machine adjusts the production procedure bit by bit as correlations are drawn between operational methods and quality test results. This methodology enables an ML model to determine the most efficient way of performing operations.
A leading manufacturer of gasoline, diesel and electric automotive powertrains began using Siemens SimCenter Amesim software and services to develop and couple virtual sensors with AI. The simulation software enabled them to create virtual models (see Figure 4) of their powertrain to determine ideal design parameters prior to production, reducing time and costs due to failed physical prototypes.
In addition to hardware design, the manufacturer used the virtual model to optimize control strategies.
By also translating the model to a format for deployment to the powertrains’ onboard electronic control units, they equipped the controllers with AI-based ML capabilities. This provided powertrains the ability to automatically adapt their output based on current driving cycle and application.
Over time and with properly labeled datasets, ML algorithms are improving, and digital twins are becoming standard in the development of products, plants and other automated systems. As a result, these technologies are increasingly accepted for certifications, such as compliance with security and environmental regulations.
As digital twins become more commonplace, they will be coupled with the delivery of physical systems and products, empowering users to hypothesize and test the results of modifications to their designs and processes prior to production.
With insightful ML and pattern recognition, simulated data from digital twins and actual data from field sensors can be processed to create accurate and timetested production models. These models accelerate process and machine optimization, increasing productivity and time to market, while reducing maintenance costs and downtime. PE
Alessandra Da Silva is the head of artificial intelligence and edge deployment for Siemens Digital Industries, Factory Automation. She has twenty years of experience in industrial and building automation, working in roles in software development, solution design, project management, and portfolio/marketing management.
Alessandra is an electronic engineer with a degree from the University of São Paulo, Brazil, specializing in IT systems, artificial intelligence, and edge computing.
Amesim software is used to create AI-equipped virtual models for simulating and optimizing mechanical system components, speeding up physical production and testing. Courtesy: Siemens
The speed at which vaccines for COVID-19 became available – from development to clinical trials to production is something the world has never seen. In a way, we were lucky to have had this happen in a time with so many scientific and digital advancements because having a vaccination for a global pandemic in less than a year is something that could not have been possible without digital technologies.
Many pharmaceutical companies have had to contend with complex process challenges while mass producing an effective and safe vaccine at a record pace. So now, when time is of the essence, vaccine producers can’t afford minor incidents along the production line, bad quality batches or unscheduled downtime due to failing equipment. Luckily, the rapid adoption of IIoT-enabled solutions like automated operations, process simulations and advanced data analytics have helped organizations become safer, more efficient and cost-effective. And when it comes to the production of something as critical as a vaccine, self-service advanced analytics in particular is a production and quality control gamechanger.
When the pandemic hit, self-service analytics had to take center stage to help pharmaceutical companies ensure that the high quality standards for the COVID vaccine were maintained. Quality for pharmaceutical manufacturers relates to the quality and performance attributes of the raw material used in the production process in addition to production line performance. Principal ingredients in producing COVID-19 vaccines comprise of water, adjuvants, preservatives/stabilizers and the active ingredient (antigens)2, which contains residual inactive ingredients necessary to the actual production process. Equipment health, storage and shipment conditions, packaging and handling are other key factors that could impact product quality.
During pharmaceutical production, it is good manufacturing practice to utilize a process control system (PCS) to maintain consistent levels of quality, cost and capacity while also ensuring worker safety. Another important component to ensuring product quality is the use of self-service analytics that can fully leverage process time-series data. Using data captured from sensors throughout the production line, self-service analytics can analyze time-series data to give experts process insights to improve operational performance and control product quality. Additionally, self-service analytics allows for the integration of crucial batch information, which can be assessed and tracked for quality control purposes.
Quality assurance (QA) delivers confidence that quality standards are being upheld. Certain activities and actions can be performed to prevent quality problems by using systematic measurement, comparisons with known standards, monitoring the production processes and variables and establishing an associated feedback loop. The pH, temperature and cycle time are key variables that should be monitored because they can affect quality. Sensor-generated time-series data of these variables should also be monitored. (See Figure 1)
Data scientists have been using sensor-generated timeseries data, which could include data from other sources as well, to create process monitoring and prediction models used to resolve complicated process challenges. This problem solving approach is a time consuming, analytically demanding and requires experts in the field, so only the most critical process problems can feasibly be addressed.
However, process and subject matter experts (SMEs) are already conducting some data analytics on a daily basis through the studying, troubleshooting and optimizing of their processes. Importing data from sensors and integrating contextual information from other sources often involves filtering out irrelevant periods and performing mathematical manipulations as well as calculating correlations. All of which is an iterative process.
Similar to the approaches that data scientists take, traditional approaches in process analyses tend to be extremely time consuming. A thorough exploration that would take days, sometime even weeks, is typically reserved only for the most critical problems. A more practical, effective approach is to allow SMEs to do more advanced analytics themselves, so they can leverage their process knowledge and time-series data to monitor, analyze and predict industrial processes. An example of this approach is when SMEs used selfservice advanced analytics to optimize COVID vaccine production.
SMEs were able to rapidly interpret the time-series data to uncover meaningful information regarding production processes at any given time. Data was easily visualized and patterns easily recognized. In addition, the machine learning capabilities of the self-service analytics supported users allowing them to more quickly troubleshoot problems and optimize operations.
Advanced analytics further contributes to product and quality control by enabling SMEs to contextualize their data. During the production process, various events such as maintenance stops, process anomalies, asset health information, external events and production losses can affect product quality and impact operational performance. Usually though, this information is stored in different data silos within different teams thus prohibiting data transparency. Now with self-service analytics, information for these events can be collected and recorded within the platform to provide one data source for all personnel and teams to gain additional insights into quality control and operational performance. Thus, data silos are eliminated.
Fully leveraging context data can be instrumental. As seen with vaccine production, for example, every batch is comprised of its own metadata including the batch number, cycle time, compliance data, etc. – all of which can be extended to include the lab test data. Such information enables a more meaningful and quicker assessment of the best production runs. Process experts can then create a “golden batch fingerprint,” or a “good batch” benchmark that can be used for assessing future batches. The data of underperforming batches can be more readily determined and can serve as a reliable starting point for conducting an investigative analysis, which we will detail in the following use case.
While COVID-19 vaccine production was underway, a pharmaceutical company’s team of process experts recognized an issue with the vaccine’s quality. It was evident they needed to drill down into the data as quickly and effectively as possible to determine the problem. They used a self-service analytics tool that delivered many capabilities to view all details of production trends and other context process information. The analytics tool guided them through the vital steps within their investigative phases in order to fully understand what factors were affecting their batches in order to know what actions to take to resolve the quality issues in their vaccine production.
The investigation phases they conducted were as follows:
The team first ran a query to check out the batch data trends. The self-service analytics tool they used has the capability of providing a dashboard which contains tiles that are visual representations of important process data points. By reviewing the box-plot tile on the dashboard, the team saw that the cycle time of a
determine the cause of the lower quality batches. Since pH is a key driving factor in determining the final quality numbers, the team began with investigating this parameter. The team used the “Recommendation Engine,” a valued feature of the self-service analytics tool that uses machine learning to produce recommended solutions as well as answers to process questions. They uncovered that a drop in temperature caused a drop in pH. Therefore, they believed it was plausible that the temperature drop was likely the reason for the lower quality product.
By comparing the failed batch against a set of previously approved batches (saved as a “golden fingerprints”), they were able to pinpoint where the process deviated. They discovered that the first the temperature dropped out of threshold, which was then followed by a pH drop out of threshold. All these findings supported their hypothesis of the cause of the batch failures. (See Figure 3)
recent batch was much longer than normal. They were also able to determine that some of the process phases had a higher variation than others.
Next, they checked the “current value” tiles within the dashboard and determined their overall process had been behaving within the expected control parameters. Lastly, looking for any inconsistency in the quality of the material, they drilled down into a tile’s data that contained contextual process information to view specific events and to search for batch inconsistencies. Even though there were different events occurring throughout the process, they were only interested in investigating the "Failed Batch" events, which represented the discrepancy in quality. (See Figure 2)
This phase constituted a root cause analysis in which process experts assessed the “Failed Batch” events to
To prevent future deviations and keep their batches within the ideal thresholds, the team set up a monitor that could work in conjunction with the golden batch fingerprint. Thus, when any process deviation is detected, the self-service analytics tool will automatically send an email alert to personnel to notify them about the potential problem. This alert gives the team enough time to address the process issue and to prevent a bad batch from occurring. (See Figure 4)
The ingenuity of IIoT-enabled technology can deliver deeper insights into operations like never before. Thanks to self-service advanced analytics, critical pharmaceutical processes like COVID-19 vaccine production and other lifesaving medicines can now benefit from data-driven quality control and optimized production processing. It also means pharmaceutical companies can reduce production losses and costly setbacks due to production anomalies. This is just one example of how self-service analytics really delivers on its worth and drives process optimization. COVID-19 vaccinations are helping to save lives and to return life to normal. Without the help of self-service analytics, vaccination production could never meet the targets needed to protect and save lives and get society back on track. PE
Under 40 program recognizes manufacturing professionals under the age of 40 who are making significant contributions to their company’s success and to the control engineering and/or plant engineering professions. The Class of 2021 includes 46 well sought-after individuals with high ethical standards who prefer to go above and beyond to ensure success for their customers. These advanced strategists enjoy getting down and dirty with designs in an effort to avoid unnec-
essary downtime, keep production booming and strengthen their own reputations, as well as that of the companies they work for.
View the Engineering Leaders Under 40, Class of 2021, in the following section and read about their industry contributions online at www.controleng.com. CFE Media and Technology aims to honor these individuals at the annual Engineering Awards in Manufacturing dinner in spring 2022 in downtown Chicago. Congratulations to the Class of 2021!
• For information on how to nominate for 2022, visit: www.controleng.com/EngineeringLeaders.
Liberty, SC, United States
BS Electrical Engineering, Clemson University
—Jeff has designed more than 60 industrial computer systems for leaders in defense, energy, public safety and transportation; his favorite being the “extreme rugged” designs and those that focus on functional density.
Milwaukee, WI, United States
BS Electrical Engineering, University of Wisconsin-Platteville
—As a system integrator and consultant, Nicholas has traveled to various sites across the U.S. to assist in replacing aging controls systems and is a co-creator of a one-on-one PLC training/mentoring program.
Sealevel Systems
Liberty, SC, United States
AS Science, Trident Technical College
BS Electrical Engineering, Clemson University
—Cameron led the development of an industrial SuperSpeed USB 3.1 hub, taking it upon himself to become immersed in a comprehensive understanding of USB specifications and protocols as he set out to create the best-inindustry hub.
Seattle, WA, United States
BS Chemical Engineering, Purdue University
MBA, Louisiana State University
Syscon Automation
Sandy, UT, United States
AS Electrical Automation & Robotic Technology, Utah Valley University
—Jake is a leading controls engineer for battery handling machines that support the EV industry, a task for which he has developed several programming standards that have contributed to Syscon’s re-use code library.
Hargrove Controls + Automation
Baton Rouge, LA, United States
BS Computer Engineering, Louisiana State University
—John is a licensed Professional Engineer and TÜV Rheinland-certified Functional Safety Engineer who embraces the highest ethical standards while fulfilling the spirit of his client’s needs, rather than just the required task.
Maverick Technologies
Webster, TX, United States
BS Chemical Engineering, Louisiana State University
—Josh has worked his way from process control engineer to project manager and now business manager; he recently moved to the Houston office to take over a struggling project portfolio for a critical customer, strengthening the relationship and profiting the company.
Panacea Technologies
Montgomeryville, PA, United States
BS Chemical Engineering, University of Pittsburgh
—In her current role, Allison is shaping the go-to-market strategy, developing account-based expansion strategy, guiding the product development roadmap and growing new and existing chemical industry business at Seeq.
account-based expan-
—Anthony led the effort to design strategies and educate a pharmaceutical company’s engineering team on how to comply with data integrity standards; he worked to educate them and give them the tools to perform the work on their own.
Avalon International Aluminum
Tualatin, OR, United States
BS Nuclear Engineering, MS Nuclear & Radiological Engineering, Georgia Institute of Technology
—Baron developed and patented a new product that has revolutionized the interior glazing process in the interior aluminum door frame industry; the product allows Avalon to solve glazing issues with non-standard walls.
Malisko Engineering
Denver, CO, United States
BS Chemical & Biological Engineering, Colorado State University
—As Senior Project Leader, Briana was a key contributor on the design and build out on a project for Colorado State University that featured a brewery on campus in support of the science and fermentation program.
Maverick Technologies
Baton Rouge, LA, United States
BS Chemical Engineering, Louisiana State University
—While leading successful migrations as lead on projects for Honeywell and Triconex, Dominique developed an HMI [human-machine interface] Best Practice Wiki for Maverick, a guide that has helped others successfully plan and execute graphic migrations.
Technologies
Maumee, OH, United States
BS Electronics Engineering Technology, University of Toledo
MBA, Bowling Green State University
Wunderlich-Malec Engineering
Houston, TX, United States
BS Electrical Engineering, University of Texas at San Antonio
—Nayeli has developed her technical, people and management skills by traveling internationally and working in several industries, while also successfully managing a growing team, multiple projects and clients for Wunderlich-Malec.
Maverick Technologies
Pensacola, FL, United States
AS Science, Pensacola Junior College
BS Electrical Engineering, University of West Florida
—Jonathan leads and continues to grow a team of engineers, project managers and subject matter experts, supporting them in execution of controls and systems integration projects, while driving business growth in targeted areas.
Mechanical
Yuba Water Agency
Dobbins, CA, United States
BS Mechanical Engineering & Sustainable Manufacturing, California State University, Chico
experts,
—Aaron takes pride in mentoring and successfully advocated for Yuba Water Agency’s internship program in 2020, providing on-the-job engineering training for several interns during an otherwise dark year for many college students.
Kyle Finkbeinier, 39
Sr. Electrical Engineer
Dart Container Corp.
Mason, MI, United States
BS Electrical Engineering, Michigan State University
—Matt recently oversaw the automation development and assisted with the execution for a project that doubled a customer’s capacity to produce household cleaning products during the worldwide COVID-19 pandemic.
execution for a
—Kyle has completed several projects, including upgrading the obsolete controls package on different machine with modern controls; such projects improved machine safety, quality of the product produced and machine throughput.
and Triconex, Domi- matterCincinnati, Ohio, United States
BS Electrical Engineering, University of Cincinnati
—Bob was instrumental in the upgrade of an automotive production-critical machine, including safety upgrades and an all-new design for mechanical clamps; he developed a phased plan to install all upgrades during the nonproduction time.
Maverick Technologies
Webster, TX, United States
BS Chemical Engineering, Louisiana State University
—Chris is a trusted advisor to his clients, particularly for high-performance graphic development and implementation; he has selflessly delivered results and is often sought out by clients who would “pay 10% more to have him on the project.”
Assembly
Manufacturing and Maintenance, Nissan North America
Powertrain Plant
Decherd, TN, United States
MS Industrial Engineering & Engineering Management, University of Tennessee at Knoxville
—Kaleigh manages over 300 personnel and is responsible for three assembly lines that produce nearly 500,000 engines and electric motors per year on a multiple-shift operation.
Orion Charter Township, MI, United States
BS Mechanical Engineering, Ohio Northern University
—Michael developed a standard controls package for PLC, HMI and robots for palletizing applications, as well as a custom AOI for Rockwell Automation PowerFlex drives; his biggest contribution has been in the development of other employees through mentorship.
Malisko Engineering
St. Louis, MO, United States
BS Industrial & Manufacturing Systems Engineering, University of Missouri (Columbia)
—Due to successful project execution since 2010, Tim was recently requested by name for project work at a specific client; with many interfacing systems to consider when installing a process line, Tim is careful to view every angle and address inconsistencies early.
Robert Harman, 38 Senior Control System
Engineer/Project Engineer
Plus Group
Cincinnati, Ohio, United States
BS Chemical & Biomolecular Engineering, Ohio State
—Robert helped design the Automation Plus Metrix365 data collection platform written in .NET Core, which operates within the ISA95 security model and features agnostic edge agents, key performance indicator (KPI) analytics and integration to enterprise systems.
Maverick Technologies
Tinley Park, Illinois, United States
BS Chemical Engineering, Auburn University
—As part of a leadership development team at Maverick, Alex took on a yearlong project with a goal of improving company efficiency; he spent time learning from various business units to provide experience beyond the level of an individual contributor.
San Francisco, CA, United States
BS Music Education, University of Vermont; MS Music Education, Teachers College of Columbia University; MBA, Quantic School of Business and Technology; EdD, Teachers College of Columbia University
—Jess manages the Telegraf project at InfluxData, which has produced over 300 plugins that makes real-time access to OT data easy; she also teaches management courses.
The Woodlands, Texas, United States
BS Electrical Engineering, Louisiana Tech
—Hannah is involved in developing remotely controlled stations that are involved in the safe movement and monitoring of hydrocarbons across Texas; she holds a patent from when she developed offshore control systems early in her career.
Montgomeryville, PA, United States
BS Chemical Engineering, University of Delaware
—Mike led a company effort to evaluate IIoT platforms and edge devices using MQTT and other communication protocols. His efforts led to Panacea adopting a new philosophy and nudged them towards cutting edge deployment methodologies.
Honeywell Aerospace
Phoenix, AZ, United States
BS Aerospace Engineering, Arizona State University
MS Aerospace Engineering, Arizona State University
—Mike oversees automatic flight and thrust control functions as part of the Integrated Flight Systems team at Honeywell Aerospace; he has been a part of developing new and novel aerospace technology in addition to cutting-edge designs.
Denver, CO, United States
BS Chemical & Biological Engineering, Colorado State University
—Ben has led the effort on the Ramskeller project, a unique and highly automated brewing system at Colorado State University; the system provides students an example of controls, electrical, chemical and mechanical engineering design.
Bridge Gap Engineering
Northampton, PA, United States
BS Mechanical Engineering, Pennsylvania State University
—In his current role, Jeffrey is responsible for all engineering and execution activities throughout BGE’s global office network; he has regularly contributed to IEEE/PCA conference as a presenter of industry relevant topics
Taunton, MA, United States
BS Mechanical Engineering, Worcester Polytechnic Institute
execution activities
—Kevin is a go-to for out-of-the-box and unusual projects at ACE due to his ability to learn and figure out new and old technologies; he enjoys leading by example and mentoring young engineers on technical and people skills.
Yokogawa
Newnan, GA, United States
BS Biomolecular & Chemical Engineering, Georgia Institute of Technology
—Ryan is a certified Product Manager, an engineer-in-training and an expert in the field of laser analytical gas measurement with the ability to communicate a complex subject with a wide range of coworkers and clients.
Tesco Controls
Sacramento, CA, United States
BS Electrical & Electronics Engineering, California State University Sacramento
—As a manager of two departments at Tesco, Raju leads a team of 30 PLC engineers working on critical infrastructure projects as well as a team to develop devices specifically designed for the water/wastewater industry.
Maverick Technologies
Pensacola, FL, United States
BS Chemical Engineering, Auburn University
—Jason was the technical lead for a greenfield automation project beginning with functional development through commissioning for the scale up of a pilot plant for a customer’s cutting-edge precursor material.
Interstates
West Chester, OH, United States
BS Computer Science, Iowa State University
MS Information Assurance, University of Dallas
—When customers began asking about cybersecurity, Alan took it upon himself to expand his expertise into understanding standards from NIST and ISA and developed training programs to help customers meet compliance requirements.
Bayer U.S.
Creve Coeur, MO, United States
MS Chemical Engineering, Illinois Institute of Technology
—Deepak manages a multimilliondollar infrastructure project supporting Bayer’s production of the SARS-COV-2 vaccine; his implementation will enable timely delivery of vaccines that will save lives.
Anaheim, CA, United States
BS Mechanical Engineering, Cal State Fullerton
—Ryan oversaw the design and improvement of pharmaceutical conveyor belts via RFID technology such that blood samples are more readily processed and errors are minimized; patients are able to get results and proper care faster as a result.
Patti Engineering
Indianapolis, IN, United States
BS Electrical Engineering Technology, Indiana University–Purdue University
Indianapolis
—Dan has developed expertise with UHF RFID for manufacturing and asset tracking applications and has implemented RFID systems in multiple industries; he also has participated and spearheaded UHF RFID application engineering studies.
Allentown, PA, United States
BS Systems Engineering, University of Pennsylvania
—As lead for Grantek’s Smart Manufacturing Practice, Sam is responsible for identifying and developing solutions for customers by working cross functionally across all departments; in two years Sam has doubled this initiative’s revenue.
Masimo
Irvine, CA, United States
BS Electronics & Communication Engineering, National Institute of Technology, Nagpur;
MS Electrical & Computer Engineering, Rutgers University
—Understanding machine safety, industrial communications and controls, Pratul has led integration of collaborative robots into a manual assembly line and current materials flow.
Hargrove Controls + Automation
Mobile, AL, United States
BS Electrical Engineering, Auburn University
—As Leader of Projects, Doug uses his project management skills to lead other project managers on profitable and successful projects; his unique skill to communicate his vision while remaining focus on individual needs benefits his teams.
with functional devel- SARS-COV-2 vaccine; hisCertainTeed
Buchanan, New York, United States
MS Science, Arizona State
—Ankita led a project to reduce dryer jams resulting in more than $116,000 in annual savings; she was also key support for Burn/Wet/Peel and Cupping projects that accounted another $500,000 in combined savings.
Schlumberger
Houston, TX, United States
MS Oil, Gas & Petrochemicals, Universitat Guillermo Marconi
—Jeniffer has made important contributions to the remote control and monitoring of oil and gas well production using electro-submersible pumps; she has also been involved in the development of software that has greatly improved the remote control of wells in production.
Houston, TX, United States
BS Electrical Engineering, Lamar University
—Mike shows an eagerness to dive into projects and master them by understanding the problem and developing solutions that are robust and well executed; he actively listens and seeks solutions that go beyond the obvious to anticipate and prepare for eventualities not presented in the problem description.
Schneider Electric
Andover, MA, United States
BS Electrical Engineering, Zhejiang University, China; MS Electrical Engineering, University of Minnesota
—Having worked closely with customers in different functions, Kaishi has been leading a team to define the next generation of automation platform; his dedication to bringing innovative products to the market is recognized by customers, partners and peers.
Maverick Technologies
Houston, TX, United States
BS Chemical Engineering, Texas A&M University
—Janika is a dependable leader who is strongly oriented towards supporting and mentoring her direct reports. As a working/functional team leader, she seeks solutions to problems and looks for opportunities to increase efficiencies.
Oak Ridge National Laboratory
Oak Ridge, TN, United States
BS Mechanical Engineering, University of Dayton
MS Mechanical Engineering, University of Dayton
and mentoring her
—Under Thomas’ leadership, the U.S. Dept. of Energy Better Plants program has grown to more than 250 industrial partners, generating over $8.2 billion and 1.7 QBtu in cumulative energy savings.
Know someone who qualifies as an Engineering Leader Under 40? Help give them the recognition they deserve.
The Engineering Leaders Under 40 program recognizes manufacturing professionals under the age of 40 who are making a significant contribution to their plant’s success, and to the control engineering and/or plant engineering professions. Our research shows that finding, training and retaining workers is the biggest issue facing manufacturing today. The goal of the Engineering Leaders Under 40 program is to call attention to these successful young engineers in manufacturing and to show how manufacturers are recruiting and developing the next generation of manufacturing professionals.
someone at: professionals.
Nominate someone at: https://www.plantengineering.com/ events-and-awards/engineering-leaders-under-40/
Also
leaders online at the page above,
Also see past leaders online at the page above, going back to 2010.
Dept. of Energy Bet-More industrial wireless best practices were provided by speakers from a Control Engineering webcast, “Exploring industrial wireless best practices.” Laurie Cavanaugh, business development manager, E Technologies, and Dean Fransen, Applied Intelligence, Wood, answered more industrial wireless audience questions below that were submitted but not answered in the one-hour July 8 webcast. Answers below include information on wireless sensors, wireless reliability and wireless technology selection.
Question: If wireless is the industrial communication choice, how do you help clients decide among technologies? What are criteria used?
Cavanaugh: The very first thing is to determine what problem you’re trying to solve. And what is the perception that wireless will be the answer? Answer will definitely include these criteria: Range, speed/performance, reliability, cybersecurity, cost to implement, cost to support and maintain, compatibility with existing systems, lifecycle?
Fransen: Additional criteria to ask yourself, what am I using wireless for? Data collection? Streaming? Discrete data? Location/mobile? Time sensitivity/latency. The answers to these questions will help provide some answers.
Q: Are wireless communications more likely to require updates in hardware or protocols than wired industrial communications?
Cavanaugh: Wired devices in a control infrastructure have always communicated across multiple firmware levels, so updates are not required, and having the ability to put in a new controller and talk to a 20-year-old controller on the same wired network is doable. This was driven by certain industries that required validated systems so applying firmware updates, SCADA or other application updates, and even adding a wireless option requires significant planning and is expensive to modify after the initial installation due to the need to revalidate those systems.
Fransen: This depends on the wireless infrastructure. For example, an Internet of Thing (IoT) solution using 2G cellular may be impacted by carriers migrating to 4G/5G only.
Q: Is the wireless lifecycle generally longer or shorter than industrial-wired applications?
Industrial Internet of Things (IIoT) sensors and wireless mesh network can notify maintenance there is a problem. Courtesy: Control Engineering webcast on “Exploring industrial wireless best practices.”
Industrial Internet of (IIoT) and wireless mesh network
Cavanaugh: Wired communication, when installed well and with environmental factors taken into consideration, can be stable, reliable and last a long time – and even provides a path for replace-
ment of equipment on either end without changing wireless infrastructure. It is easier to secure. Wired does involve multiple players for implementation and maintenance – a direct correlation with the harshness or complexity of the environment.
Q: Is wireless reliability a concern compared to wired communications?
Cavanaugh: Wireless reliability is the key factor; that’s why you have to understand the application. There are also issues with interference, ensuring you’re on the right license bandwidth, etc. There are have been advancements to reduce environmental impact to strength and reliability, but it’s still a consideration during design and planning.
Q: Are retrofits more often from wired to wireless or older wireless to newer wireless?
Cavanaugh: From what I see, there is not so much a replacement as an augmentation or adaptation. If new equipment has wireless sensors, but also a wired controller, there will be an opportunity for creating a hybrid wireless and wired communication and information sharing network. Fortunately, the ability to use an existing Wi-Fi network, add an Edge Industrial Internet of Things (IIoT) device to collect wireless sensor data, wire in the new controller to an existing control network, and add a switch into the new panel to connect to the network allows for that evolution into the adaptation into a hybrid wireless architecture. It’s an evolution, not a revolution.
Q: Does a customer ever start with one wireless technology in mind, then change because the application needs something else?
Cavanaugh: This is absolutely a real possibility, and for that reason, we start with a pilot project to prove what is unknown and can’t be determined during a design phase. Design only gets you so far. And everyone may think they’re solving the root cause problem at first, but the pilot project should flush out the real root cause.
Q: Does industrial wireless advice differ from a couple years ago?
Cavanaugh: It is critical to evaluate wireless within the organization to determine whether (a) wireless has or will be part of a long-term information exchange direction for the overall organization or (b) is more of an opportunistic and case-based solution consideration. If it is (a) then I’d propose a corporate wireless strategy needs to be developed and maintained as part of the overall information technology / operational technology (IT/OT) Strategy. If (b) then having an identified “Task Force” as part of the IT/OT group would be sufficient to plug
into the discussion on how/where wireless would be used as part of a specific project initiative.
Q: Are there industries that should be using more industrial wireless, but aren’t? Why?
Cavanaugh: The process industries: Life sciences, food and beverage, and consumer packaged goods. Due to their heavy reliability on equipment, they can really start to build analytics based on the higher volume of real-time data.
Q: What’s next for industrial wireless?
Cavanaugh: The evolution because of the volume of data collected would be closed-loop decision making to correct or adjust equipment without operator intervention. In addition, as less operator and worker involvement drives using machine learning and AI models, the integrity of that machine learning would be driven by models for compliance safety and quality. Machines need calibration, not motivation.
Fransen: With greater access to broadband, industrial wireless will go beyond traditional controls and data collection. Add connected operators and maintenance with augmented reality (AR) to support manufacturing processes. Think about real-time access to data for trouble shooting, drawings, visualization of assembly processes.
Q: How do you recommend we advance our industrial wireless maturity level?
Cavanaugh: Understand your organization’s “real” maturity level. Take some of the learnings here to do a little more self-education so that you can ask deeper questions in the organization and identify where wireless may be in use. Knowing what “smart questions” to ask will help to quickly determine opportunities to advance using wireless solutions. Depending on what you learn, you may reevaluate where you are on the maturity spectrum. Once you’ve assessed your current state, and learned about what is possible and how to help the organization operationally and financially, you’ll be in a better position to propose use cases and determine if there is traction to evolve.
Q: Any industrial wireless lifecycle advice?
Cavanaugh: I think the advice would be that wireless lifecycle or end of life announcements aren’t necessarily as scary as they may have been several years back, because there are technologies being developed to bridge that gap and provide a middleware translation. There are solutions out there to bridge that gap so that you can put together
‘
With greater broadband access, industrial wireless will go beyond data and controls. Augmented reality will support manufacturing.
KEYWORDS: Industrial wireless, system integration
Industrial wireless webcast included audience questions, with more answers here.
Wireless sensors, wireless reliability and wireless technology selection are among topics.
E Technologies and Wood provide system integration services, including industrial wireless communications.
CONSIDER THIS
Are you questioning where to add wireless industrial communications?
ONLINE
www.controleng.com/ networking-and-security/ wireless
a more tactical strategy to address aging technology over time.
Q: Are there vulnerabilities of cellular networks vs private?
Cavanaugh: Yes. Cybersecurity or wireless security is not a given, so there has to be a well thought-out security strategy for wireless integration. That will be called out in corporate IT standards. That’s why there’s either a task force or strategy already developed. That strategy has to be maintained against current threats.
Q: Have you seen 5G and AI applications?
Cavanaugh: The adaptation of AI into the manufacturing space has been slow. I’ve seen it in other distributed industries like water/ wastewater, where there are multiple locations.
Q: What about wireless cybersecurity?
Fransen: How will your solution manage protecting access to the network? Can you restrict access once on the network? Is the data
FIELD TO CLOUD CONNECTION
moving across the network encrypted? Hiding the service set identifier (SSID) of the wireless network are a few considerations.
Q: Can you discuss virtual private networks (VPNs) over carrier-based networks?
Fransen: Wireless connected devices using VPN for connectivity to corporate domain is commonplace for employees using laptops and tablets. A similar strategy can be used to IoT devices if direct connection to corporate networks is required.
Q: What are pros/cons of IEEE 802.11 Wi-Fi grid vs. Zigbee mesh network?
Fransen: Zigbee is a short range, small data, low power, mesh network. Each node can connect to the network directly or via another node (passthrough). This helps extend range and adds some reliability as nodes have multiple paths to connect to the network. Wi-Fi has longer range, large amounts of data, much higher power consumption. ce
Edited by Mark T. Hoske, content manager, Control Engineering, CFE Media, mhoske@cfemedia.com.• IIoT-ready with Sparkplug, native MQTT and TLS encryption
• Built-in VPN and Firewall for increased network security
• Run Docker Containers in parallel with PLC logic
• Interface with existing controls via onboard fieldbus gateways
www.wago.us/IIoT
Request more information about products and advertisers in this issue by using the http://plantengineering.hotims.com link and reader service number located near each. If you’re reading the digital edition, the link will be live. When you contact a company directly, please let them know you read about them in Plant Engineering.
PlantEngineering.com
3010 Highland Parkway, Suite 325 Downers Grove, IL 60515 Ph. 630-571-4070, Fax 630-214-4504
KEVIN PARKER, Editor KParker@CFEMedia.com
JACK SMITH, Managing Editor JSmith@CFEMedia.com
KATIE SPAIN NAREL, Art Director KSpain@CFEMedia.com
AMANDA PELLICCIONE, Director of Research 860-432-4767, APelliccione@CFEMedia.com
CHRIS VAVRA, Production Editor CVavra@CFEMedia.com
SUSIE BAK, Production Coordinator SBak@CFEMedia.com
JIM LANGHENRY, Co-Founder & Publisher JLanghenry@CFEMedia.com
STEVE ROURKE, Co-Founder SRourke@CFEMedia.com
KATIE SPAIN NAREL, Art Director KSpain@CFEMedia.com
PAUL BROUCH, Director of Operations PBrouch@CFEMedia.com
COURTNEY MURPHY, Marketing Services Director CMurphy@CFEMedia.com
MCKENZIE BURNS, Marketing and Events Manager MBurns@CFEMedia.com
MICHAEL ROTZ, Print Production Manager 717-766-0211, Fax: 717-506-7238 mike.rotz@frycomm.com
MARIA BARTELL, Account Director, Infogroup Targeting Solutions 847-378-2275, maria.bartell@infogroup.com
RICK ELLIS, Audience Management Director 303-246-1250, REllis@CFEMedia.com
LETTERS TO THE EDITOR
Please e-mail your opinions to KParker@CFEMedia.com
INFORMATION
For a Media Kit or Editorial Calendar, e-mail Susie Bak at SBak@CFEMedia.com
CUSTOMER SERVICE OR SUBSCRIPTION INQUIRIES (800) 217-7972
e-mail Plant Engineering at PE@omeda.com
REPRINTS
For custom reprints or electronic usage, contact: Shelby Pelton, Wright’s Media 281-419-5725 x138, cfemedia@wrightsmedia.com
Robert Levinger, Midwest RLevinger@CFETechnology.com 3010 Highland Parkway #325 Tel. 516-209-8587 Downers Grove, IL 60139
Karen Cira, Southeast KCira@CFEMedia.com 879 Autumn Rain Ln. Tel. 704-523-5466
Charlotte, NC 28209 Fax 630-214-4504
Diane Houghton, AL, FL DHoughton@CFEMedia.com
38 Charles River Drive, Tel. 508-298-9021 Franklin, MA 02038
Dodge® Raptor tire coupling was created with industrial users in mind. The innovative elastomeric element has higher bond strength, more resistance to fatigue, and longer life than competitive urethane designs. The split element leads to simpler maintenance, and the slotted clamp ring holes result in easier installation. The Raptor was designed for a broad range of industrial applications and is available for hazardous and extreme environments.
Easier installation. Increased reliability. Longer life. Dodge Raptor couplings
479.646.4711
baldor.abb.com