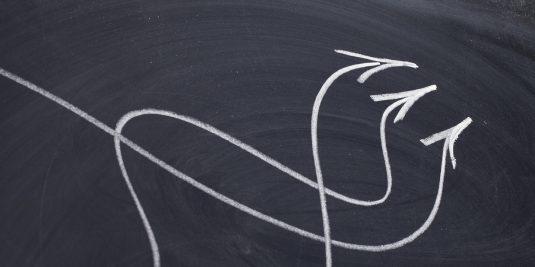
12 minute read
Polarisation helps to reveal often hidden details; Ethernet communication for Ex areas
OT/IT CONVERGENCE
WHERE TECHNOLOGY CONVERGENCE LEADS ORGANISATIONS MUST FOLLOW
Advertisement
There appears to be agreement among automation vendors that Operational Technology (OT) and Information Technology (IT) convergence is now becoming a reality across all industrial sectors. Suzanne Gill finds out more about the impact that this will have on the role of the control engineer.
It would appear that not only is OT/IT convergence becoming a reality, but that it is a process that has been underway for some time, led by technology convergence – albeit it is happening at varying rates, depending on the way in which a company is addressing the digital transformation of its business and how far along the Industry 4.0 journey it is.
Mike Loughran, chief technology officer at Rockwell Automation, is certain that OT/IT convergence is happening across industry because
Rockwell is seeing many more companies with advanced connected enterprise approaches who are starting to unlock the benefits of Industry 4.0. “This is happening as a result of either increased cooperation between OT/IT, or due to the rise of the hybrid OT/IT workforce. Whichever way we look at things, the definition and function of both roles in the industrial setting is becoming looser as the lifeblood of industry 4.0 – data – needs to move more easily through the business and plant levels to enable efficiency and productivity gains.”
Loughran says that the OT/IT convergence journey will be different for each company, depending on their existing plant, resources and desired outcomes. But he says that support is available for all – training and benchmarking such as the Cisco Certified Network Associated (CCNA) designation – to build organisational competency and to improve workforce readiness as this convergence advances. “In a way, this shows that IT-style certification is becoming an important marker for OT personnel in the converged world of the connected enterprise – an interesting proof point that the two worlds are indeed coming together,” he said.
Rapid learning curves
Matthew Wells, vice president of Digital Product Management at GE Digital,
OT/IT CONVERGENCE
believes that OT and IT departments have been on a rapid learning curve and that both have already come a long way. “IT has learned about what real time actually means and how that translates to the needs of the plant floor, while OT has learned how to leverage the latest IT technology to improve security and data integrity and meet the needs of the plant floor while adhering to enterprise IT policies and standards. The bottom line is that plant floor systems need to be connected, secure, and provide high reliability and performance,” he said.
The reality that we are facing today is that most factories contain multiple generations of systems where both ageing and new equipment need to be part of the digitisation journey and both IT and OT capabilities are needed to bring the expertise to make this happen.
Wells believes that the traditional role of the control engineer has changed already. He said: “Not only are control engineers providing more value to organisations, but this expansion of the role provides new and interesting challenges. The opportunity to leverage technologies such as analytics can help engineers make substantial optimisation improvements to their plants.”
Wells goes on to point out that control engineers also need to enhance their collaboration skills – not only with IT teams but also with operators. Elaborating on this point, he said: “In an IoT world there is a closed loop of information. Data comes from the systems and then, through a solution involving data analytics and execution orders, it is fed back to the operators. Control engineers need to work with operators to train them on ways to optimise processes leveraging new tools. There is also a need to include operators at the front end of development. Operators will support control engineers with their own domain expertise for leveraging tools and adjust faster with deeper collaboration.”
A clear understanding
Greg Hookings, head of business development – digitalisation at Stratus Technologies, said: “IT professionals now need a clear understanding of the operational constraints and priorities of the plant floor, including the requirements for IT resilience and the need for reduced downtime. The same can be said for OT professionals, who are gaining a better appreciation of the need for connectivity and the importance of data to operational improvements.”
Hookings believes that the reality of the continued OT/IT convergence is the emergence of a ‘hybrid’ professional – someone who perhaps started their career as a traditional control engineer – the hybrid professional has a deep understanding of the technology needs that drive decisions on the production floor and can see the value of data collected at the network edge. Their role will be to use data and make strategic business decisions while simultaneously understanding the functionality of the manufacturing plant. Explaining further, he said: “Control engineers do not need to be data analysts, but with the coming wave of technologies and approaches that digital transformation is bringing, they will need to be digitally competent and prepared to extend their digital skillset, bringing their OT knowledge and perspective to their company’s digitally enabled future. Collecting data, aiding the understanding and further bridging the gap between the two disciplines is edge computing, which comes in many shapes and sizes. The right deployment of this can provide insightful data that many traditional OT engineers might not have thought possible with a simple deployment.”
Overcoming barriers
The converging worlds of OT and IT could present a barrier to smart factory initiatives across Europe, according to a recent study undertaken by teknowlogy Group on behalf of Stratus Technologies. This showed that 40% of those surveyed – IT and OT decision-makers from 204 european manufacturing companies – cited OT/IT convergence as a significant challenge to their smart factory initiatives. Failure to integrate these two skillsets could hold industry back from reaching the next level of smart technology.
Continuing on the subject of barriers to successful convergence, Wells pointed out that another obstacle hinges around the different technology maturity levels. He said: “Technology maturity spans the personnel as well as the processes within a plant. What kind of technology do you need to bridge functional siloes? Can you identify the heterogeneous data sources? More than likely there are multiple control systems including PLCs, RTUs and CNCs. The best way to address this is to look for solutions that can be deployed seamlessly on top of the existing infrastructure. Layer HMI/SCADA and MES seamlessly on top, using a structured model.” Wells believes that industry standard protocols, such as OPC UA, will enable interoperability. “These protocols allow systems to speak the same language. They are trusted, secure-by-design and can facilitate turning data into knowledge which is a common need across both OT and IT,” he said.
Loughran highlighted another barrier to successful OT/IT convergence as being a culture difference. He said: “Historically, and for good reason, IT and OT have been somewhat siloed. An amount of understanding of IT has been required on the plant floor for some time – networks at the control level are common. Similarly IT professionals in industry have required an understanding of OT requirements in order to support plant level IT.
“What has changed is the era of IIoT, whereby many more ‘things’ are enabled to share data and offer insights and potential previously hidden from view. What hasn’t changed for the IT professional is the need for security from outside threat, and what hasn’t changed for the OT professional is a requirement for the highest possible
OT/IT CONVERGENCE

uptime and a level of resilience that is less common at the IT level. The cultural barrier might be summarised as saying that we need to bring IT levels of security without compromising OT levels of reliability. In a sense, neither IT nor OT should compromise, but rather, they must work together to make it possible. The benefits for those who do makes this convergence inevitable. The real winners will be those companies who understand the strategic importance and support their personnel to help take them forwards quickly.”
Connecting the dots
While industrial companies all vary in their approach to organisational alignment of IT and OT, it is clear that technology evolution is now inexorably linking them. According to Jason Urso, vice president and chief technology officer of Honeywell Process Solutions, this journey actually started over 20 years ago, when previously proprietary OT technology began to utilise open system capabilities – including Microsoft-based PCs, servers and EtherNet networks. These technologies served to reduce cost, but also allowed interoperability between systems and applications through open standards like HART, OPC, EtherNet/IP and PROFINET. Over this period, new benefits were achieved by linking OT automation systems with numerous software applications. This integration enabled improvements in throughput, yield, reliability, safety, security and personnel efficiency. Companies are operating process plants better and safer than ever before thanks to the pace of innovation enabled by the pervasive use of open systems and open standards technology.
“As manufacturing has increasingly adopted open systems, plant and IT personnel are expanding the application of new technologies to cross the digital divide between IT and OT forming a new digital intersection,” said Urso. “Doing this offers instant access to plant and asset information and ultimately laying the foundation for IIoT. By harnessing the power of electronic data available across a corporation, we are in the midst of creating a new generation of operational benefits that spans an entire enterprise. Yet, we have only just scratched the surface of what is possible. With new data mining and analytics techniques coupled with collaboration across subject matter experts and suppliers, we will see a manufacturing and automation renaissance by augmenting human intelligence with technology – providing better insight into operations and more precise actions that are driven by best practices. Doing so will deliver another step change in industrial performance, reliability, security and safety.”
With the recent Covid-19 pandemic, the vital need for IT and OT collaboration and what it can accomplish has been brought sharply into focus for many. “Process plants that were mandated to reduce staffing or sites that have quarantined individuals needed to instantly find new ways to operate and maintain business continuity,” continued Urso. “By establishing remote operation capabilities IT/OT professionals across process industries are able to securely extend control room operations to remote locations. Even engineering support personnel working from their homes are able to provide operations assistance as if they were standing with the process operator in the control room.”
Conclusion
While for some users OT and IT may not yet have achieved organisational convergence, from a technology perspective it has already happened and this is offering industry a wealth of new opportunities. In time, remote collaboration, coupled with new analytics methods and intelligent wearables are expected to transform industries and this means that the current trajectory of OT/IT collaboration will continue allowing the two disciplines to apply their unique strengths by pushing technology to limits in ways that will deliver substantial new benefits and creating another step change in business performance well beyond what has been seen in the past.
sponsored article
SPE SYSTEM ALLIANCE
Cross-industry and cross-application alliance for Single Pair Ethernet technology
The technology partnership between Phoenix Contact, Weidmüller, Reichle & DeMassari (R&M), Fluke Networks, and Telegärtner for the Single Pair Ethernet (SPE) has progressed to create the SPE System Alliance. Find out more about this collaboration.
The newly formed SPE System Alliance consists of leading technology companies from various industries and fields of application who have come together to bundle their respective SPE expertise and ensure the target-oriented exchange of this knowledge. The partners in this group are pursuing the goal of driving the development of SPE further forward for the Industrial Internet of Things (IIoT) and may branch out to other areas as well.
The System Alliance has most recently been joined by Datwyler, Kyland, Microchip Technology, Rosenberger, SICK, O-Ring, Draka/Prysmian Group, and University 4 Industry.
Synergies in the SPE System Alliance
The network aims to collaborate on the technological challenges faced when implementing SPE in IIoT applications. The goal of the companies is to accelerate their own development of expertise in SPE technology and to allow it to be implemented faster and more reliably in their products.
Through this orientation toward a cross-industry and cross-application exchange platform, companies from all future SPE ecosystems are coming together. The focus is not, however, on individual aspects such as connection technology. Instead, the focus is on questions and challenges that continue to exist with many market participants in connection with SPE. Rule exchange formats and collaborative project activities provide the freedom for close cooperation. The members are already working together in the first subcommunities, in the fields of connection technology, standardisation, SPE usecase reports, and even for cable solutions, among others.
Commenting on the alliance, Torsten Janwlecke, President Business Area Device Connectors at Phoenix Contact, said: “SPE is one of the mega trends in industrial data processing for end-toend IP-based networking from the sensor to the cloud. The Single Pair Ethernet technology therefore not only includes all infrastructure components of industrial network technology, such as connectors, cables, PHYs, sensors, switches and other devices, but will find its application in many different areas. This is exactly where the SPE System Alliance comes in. The exchange of members takes place across industries and applications and is not limited to one aspect, such as connection technology. All participating companies can contribute their expertise in the various working groups and thus also benefit from the exchange. The contribution of Phoenix Contact in the Alliance refers in particular to the part of connection technology and infrastructure components, such as switches. Here, we contribute, among other things, findings on the newly developed M8 SPE connector, which is highly relevant for the connection of sensors and thus for the implementation of IIoT and SPE.”
Thanks to its broad lineup, the SPE System Alliance already covers a large range of applications and fields of application: For example, within the automotive industry Ethernet systems are increasingly being employed within vehicles. Meanwhile, for the passive industrial cabling field of connectivity SPE can provide consistent IP communication from the field level right through to the corporate level, and therefore from the sensor through to the cloud.
Further, in sensor technology, in addition to their use in classic automation technology, sensors are increasingly being integrated as intelligent data suppliers into IIoT applications via Ethernet networks. Due to the miniaturisation of the connection technology that has become possible with SPE, smaller sensors can also be connected to Ethernet networks. Combining SPE with the power supply over the data line means that additional plug connections to the voltage supply are no longer needed. Moreover, the use of SPE as the standard interface allows device manufacturers to provide an optimised range of devices with fewer versions.
The SPE System Alliance is an open platform for companies that want to further advance SPE technology on the market. Details and options for contacting the System Alliance are available on the website
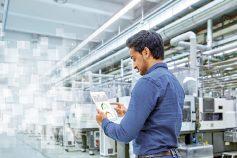