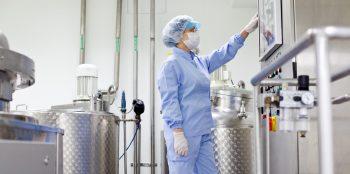
5 minute read
Jan Zhang reports that COVID-19 is forcing manufacturers to rely more on automation and digitalisation for long-term operations to reduce the financial impact
FINAL WORD
Will Coronavirus force manufacturers to enhance automation and digitalisation?
Advertisement
Jan Zhang reports that COVID-19 is forcing manufacturers to rely more on automation and digitalisation for long-term operations to reduce the financial impact from epidemics and other potential economic challenges.
The COVID-19 outbreak is becoming a global stress test. As the outbreak subsides in China, there are some major short- and long-term effects the Chinese manufacturing industry is feeling, which will carry over to other countries.
For many of the infected regions, the economy will fall sharply in the short term, and then rebound after the epidemic is over, but COVID-19 is unlikely to have a huge long-term impact. Epidemic prevention and control measures from local governments will be a key factor.
In February 2020, China’s manufacturing purchasing manager index (PMI) was 35.7%, down 14.3 percentage points from the previous month. Meanwhile, the Production Index was 27.8%, down by 23.5 percentage points from the previous month, indicating that manufacturing production activity had slowed down radically. As outbreaks continue to unfold around the world, external demand will falter, further hampering recovery.
According to analysis of data segments such as power generation, population migration, and transportation; the work resumption rate in China is about 65% (except for students). Although the overall recovery of enterprises is better, it is more difficult for small and medium-sized enterprises and lifestyleservice industries to return to work. It is expected that production and operation will get back to normal completely by May.
COVID-19 may have a far-reaching impact on the capacity layout and supply chain network of many enterprises. Multinational enterprises in particular will further improve their disaster emergency mechanisms and supply chain management.
Many enterprises will now be thinking about relocating manufacturing. During the 2011 earthquake in Japan, even companies who were hardly hit by supply chain issues decided to relocate. However, cross-border relocation of production capacity is not an easy decision to make, and many factors need to be taken into account, such as local market capacity, time and investment required, local government policies, infrastructure and logistics, labour costs, and skill levels.
Exposing problems
For manufacturing enterprises, the epidemic has exposed problems and risks that already existed. As such, it might force industry to undertake much needed reforms to automation, digitalisation and logistics processes and systems.
For manufacturing enterprises, the short-term impact of the epidemic is a decline in revenue and profits. For example, under China’s stringent prevention and control measures, a large number of manufacturing enterprises were completely suspended, and the loss of production capacity is expected to be 1 to 3 months in total. Production recovery cannot be achieved overnight, and the resumption of work may also face difficulties in the form of recruitment problems, an insufficient supply of raw materials, and other issues such as logistics and cash flow. Operating costs will also clearly remain high during this period, further eroding profit.
Small and medium-sized enterprises, and those with insufficient cash flow, will feel the pressure most. For enterprises with good operation and high capacity utilisation, the focus must be to restore production as soon as possible.
The COVID-19 epidemic has brought unexpected difficulties and challenges to governments, industries and enterprises around the world. But it is a shortterm effect and it will eventually pass. In the long run, COVID-19 is a chance for industries to make much-needed operational improvements.
Jan Zhang is a research director at market analyst firm Interact Analysis.
PRODUCT FORUM •
www.controlengeurope.com to read the full story
Alarm systems management
Creating a successful control environment
Complex industrial systems require complex control systems – but carefully thought out alarms systems
Know what you want, plan what you’ll get, check that you’ve got it!
EEMUA is the acknowledged leader in the field, with EEMUA 191, ‘Alarm systems - a guide to design, management and procurement’, being regarded as the benchmark in alarm systems management.
The EEMUA Alarm Systems e-learning module provides an introduction to EEMUA 191 and is positioned at the awareness level. It offers simple and practical guidance to managers, designers, supervisors and operators on how to recognise and deal with typical human-factor problems involving alarm systems. Its scope covers many sectors, including the energy, process and utilities industries. The e-learning is recommended for both discipline and project-focused engineers from a variety of backgrounds who want to gain an introduction to the fundamental principles for design, management and procurement of alarm systems. The course is also relevant to engineers and managers from operating companies as well as specialist contractors and equipment suppliers. Visit the EEMUA website for further details.
www.eemua.org
The EEMUA Control Rooms e-learning module provides guidance to engineers and the wider teams involved in the design of control rooms, control desks and consoles. It will help during newbuild and modification projects, as well as evaluating existing set ups where people operate industrial processes and activities on facilities such as chemical plants, power stations and oil refineries.
The e-learning will benefit anyone with an interest in process plant control rooms and control desks using Human Machine Interfaces.
It is especially relevant to control engineers, control room console (and HMI) designers and vendors, control room operators, engineering consultants, engineering contractors, engineering managers, facilities managers, graduate engineers, plant operations managers, process safety managers, SCADA engineers and systems support managers. The e-learning is positioned at the awareness/introductory level and is an optional precursor to working through EEMUA 201, ‘Control rooms: A guide to their specification, design, commissioning and operation’. Visit the EEMUA website for further details.
www.eemua.org
TO BE FEATURED IN THE CEE PRODUCT FORUM
Contact Adam Yates on +44 (0)7900 936909 or email Adam.Yates@imlgroup.co.uk
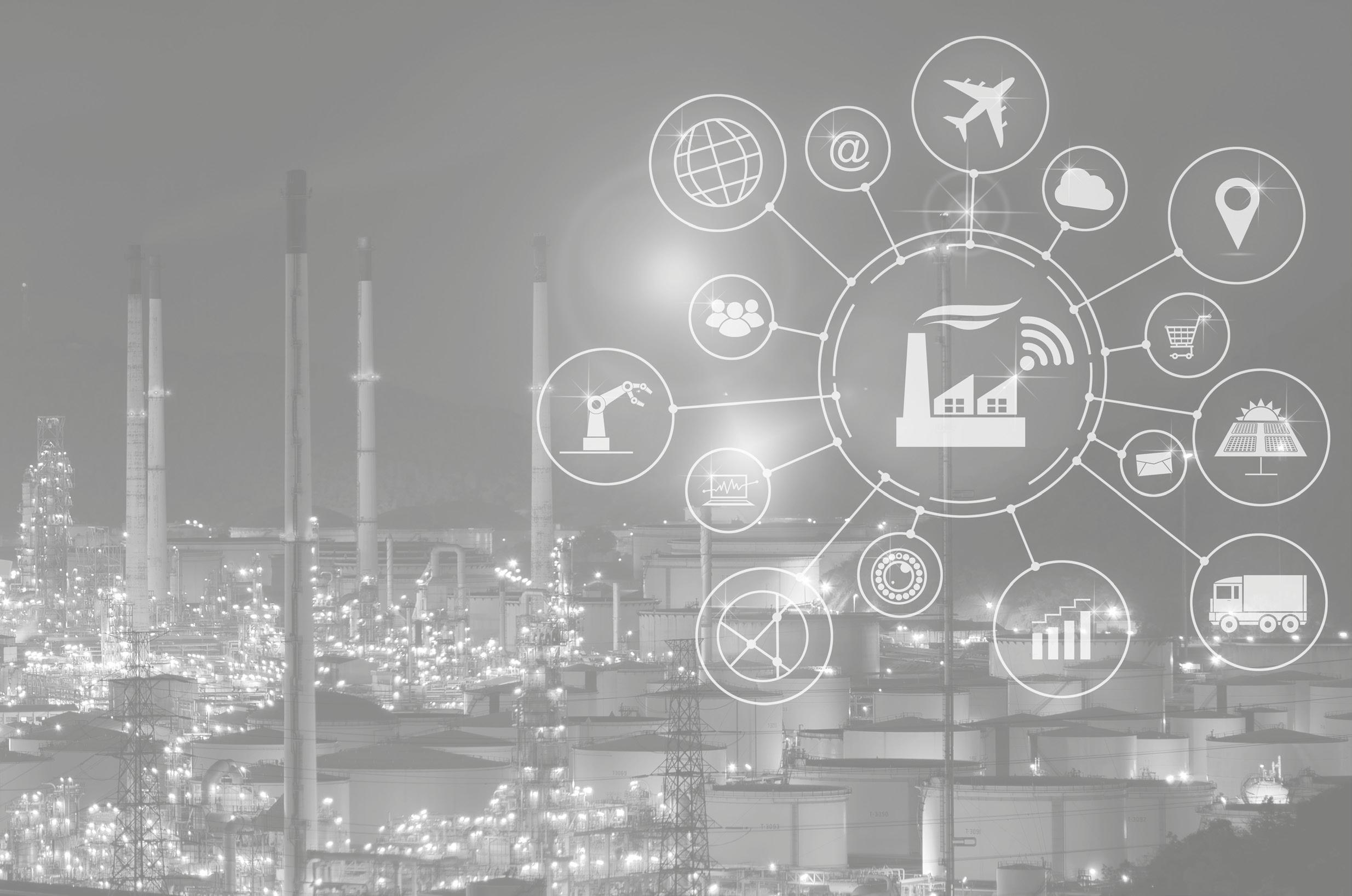
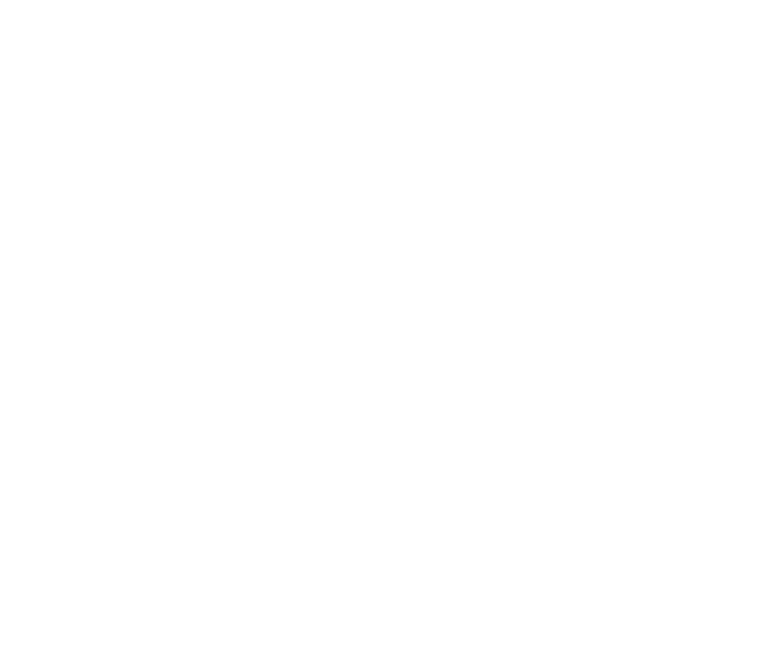
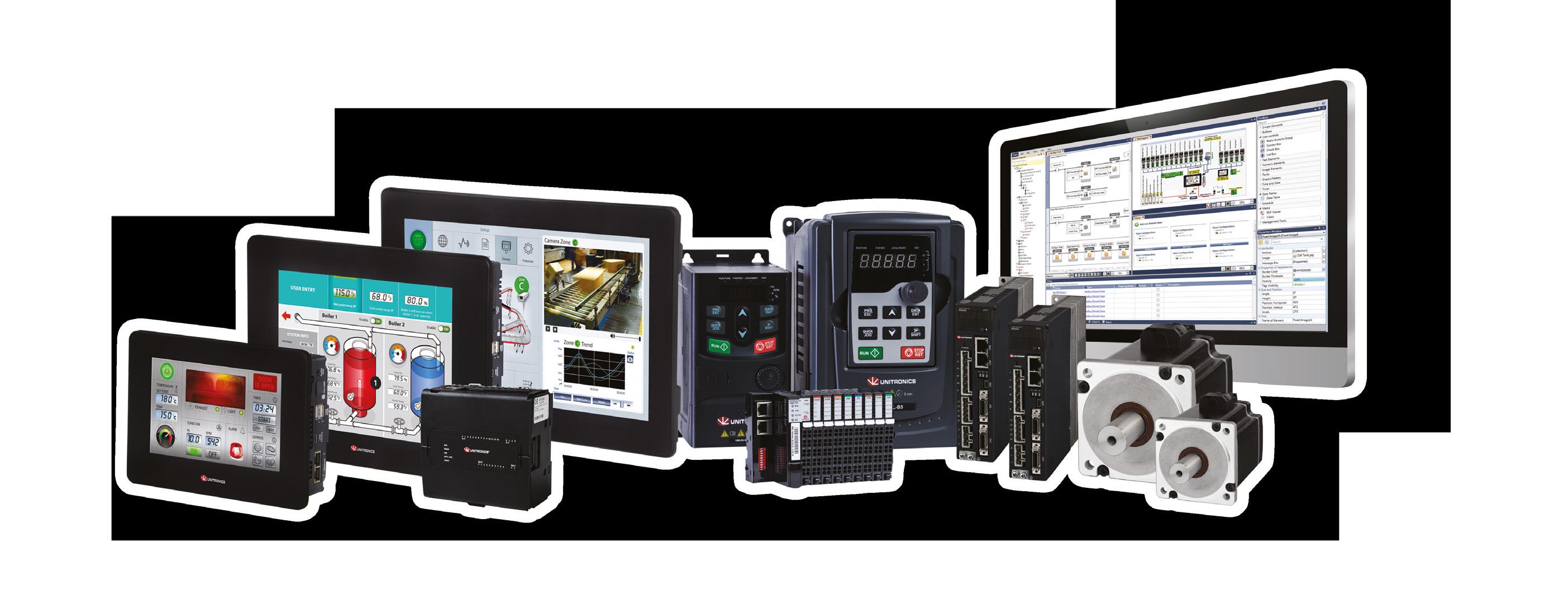
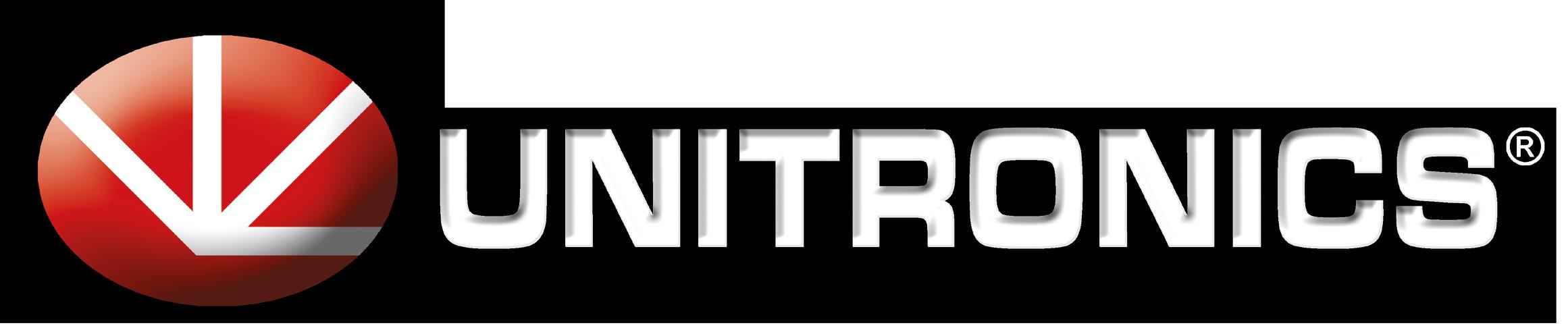