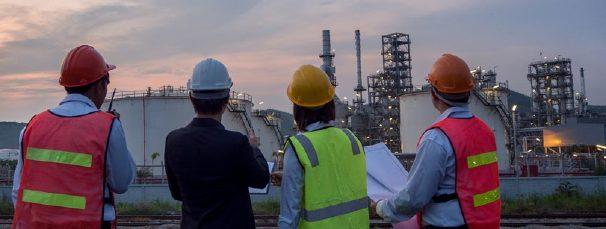
9 minute read
The role of poor shift handover in oil and gas incidents
In the oil and gas industry, hazards are inevitable and if they are not identified properly, they may lead to incidents. When it comes to continuous processes, engineers are required to be available 24/7 to carry out operations or maintenance. Workers are therefore frequently rotated on a routine basis within a cycle of shifts and conduct a handover between teams at the end of each shift. A shift handover is defined as transferring responsibilities and tasks from one individual or team to another and it is the best-known type of safety critical communication. The goal of a shift handover is to communicate “accurate, reliable, task relevant information across shift changes, thereby ensuring continuity of safe and effective working.”
This article describes the key challenges in shift handovers and illustrates how poor handovers contributed to some of the oil and gas industry’s worst disasters, before offering some recommendations on how to implement robust and effective shift handover management.
Advertisement
A shift handover is a critical activity with a direct influence on production and safety. Poor shift handover is known to cause operational problems such as plant upsets, unplanned shutdowns and product reworks, all of which can result in considerable revenue loss. Research has revealed that whilst start-ups, shutdowns, and changeover periods account for less than 5% of engineers’ time, 40% of plant incidents occur during these instances.
Role of shift handovers in major incidents
The importance of shift handovers has been highlighted by major oil and gas incidents such as Piper Alpha, Texas City, Buncefield, and Deepwater Horizon. The Cullen report published following the Piper Alpha disaster clearly mentioned, as one of many factors, that the failure of transferring information during shift handover contributed to the incident. Specifically, information about a pressure safety valve which had been removed and replaced by a blind flange was not communicated between shifts. In addition to that, there was no written procedure for shift handover and information that was written in the shift handover logbook was left to the lead operator’s discretion.
Elsewhere, the Buncefield oil storage depot explosion and fire in 2005 was also partially caused by poor shift handover. The incident investigation team revealed that effective arrangements for shift handover were not in place and there was confusion between supervisors about which tank was being filled. The shift logbook was also only used to capture information about one pipeline and only had information about the plant’s situation during the end of a shift and not about events which occurred during a shift. Finally, it was also revealed that there was an insufficient amount of time allocated for the handover between supervisors.
The BP Texas City Refinery explosion in 2005 is another example of the total failure of shift handover management. The explosion occurred when a flammable vapour cloud was created by liquid overflow from a blowdown stack. The investigation team found that there was no procedure to follow when conducting a shift handover. The absence of a lead operator during handover, miscommunication, unclear information and a lack of detail in the logbook were all evident. Operators were working in shift patterns for 30 consecutive days at a time which led to excessive fatigue among personnel and demonstrated an ineffective policy for shift work. Even though shift handover management issues and the general lessons learned from BP’s Grangemouth refinery incident in 2000 were available, the BP Texas City management did not appear to learn from the Grangemouth incident.
Communication matter
The UK Health and Safety Executive (HSE) guidance document HSG48 clearly states that reliable communication is highly critical to safety. Effective communication during a shift handover provides a strong layer of protection against major incidents. People tend to underestimate the complexity of the communication process, and consequently
overestimate their ability to communicate effectively. Good communication between management, supervisors and workers at an informal level, is a feature of low incident plants.
All communication is prone to error and misunderstandings are an inevitable feature of human communication. In complex processes, the occurrence of errors is more likely, so it is critical to check that information has been received and understood correctly. Unreliable communication can stem from issues including: - Missing information - Unnecessary information - Inaccurate information - Poor quality of information - Misunderstandings

Barriers to effective communication in shift handover
Shift handover is effectively the transfer of knowledge from the outgoing staff to incoming staff. A handover is typically thought to be a unidirectional process in which the outgoing operator decides which information is of importance and needs to be communicated. However, when operators write shift handover reports, they assume that all staff members have a shared thought process and common understanding in line with their personal ‘mental model’. Herein lies the problem – this assumption leads to miscommunication and a lack of common understanding which can lead to potential incidents. When an outgoing operator writes anything that they feel is relevant to the incoming shift, it will mostly be written in an unstructured manner and based on their own personal judgment and individual mental model.
Lack of structure, poor legibility, and insufficient information in shift logbooks are common issues. Literature reviews have indicated that 80% of oil and gas production facility logbooks are in an unstructured style and don’t capture key information. Sometimes, they include unnecessary information while key information is buried in the content.
High risk shift handovers
It is important to give special attention to handovers during certain circumstances, such as maintenance or abnormal plant conditions. Miscommunication of maintenance issues when maintenance is runnning over a shift change can have serious safety implications unless a clear picture of activities is given. If activities are miscommunicated, all the actions done by the incoming shift will be based on poor and incomplete information. Further high-risk situations include shift handovers between experienced and inexperienced staff, changing crews when the incoming staff have been absent for a long period of time, or when a safety system has been overridden. When possible, maintenance work should always be completed within one shift in order to eliminate the risk of miscommunication between operators and crews.
Buncefield oil depot fire – Image: Stuart Axe / Flickr
Regulatory requirements
Following major incidents, regulators look closely at shift handover management and the defined requirements for handovers. When the UK HSE examined 16 companies operating offshore on the UK Continental Self, it noted the following issues in relation to shift handovers: - Did not clearly define responsibilities and information requirements - Did not provide written guidance - Did not mention it in their safety case - Lacked risk awareness among their operators - Provided little or no training - Did little monitoring or auditing - Had accidents that involved miscommunication at shift handover, e.g. maintenance or plant status There are several reasons why making improvements to shift handover management can be difficult, but the above are areas that can be improved to reduce risk.
An organisation’s set-up and culture both play a critical role in improving the shift handover process. In many cases there is no guidance or procedure provided by a company or it is unclear how a shift handover should be conducted. Management teams should ensure they control all aspects of communication in handovers. If information is not being received, understood or acted upon, the organisation should investigate and remove any barriers preventing clear communication.
Shift handover logbook
Efforts should be taken to prevent the use of a blank logbook during a handover because this means the content is left to the discretion of the out-going shift personnel. It is good practice to involve any related personnel in the structuring of the logbook. Research conducted by Honeywell on improving shift handovers showed that structuring a logbook and informing workers what information needs to be reported helps reduce the risk of miscommunicating critical information. A structured logbook also helps individuals recall specific information and acts as a record of what was communicated prior to any potential incidents. Structured logbooks also help further by providing information regarding minor incidents, near misses, and human error which personnel can learn from.
Time management
The most important person in a shift handover is the person who is finishing their shift. The effectiveness of a shift handover heavily depends on the quality of information this person provides and their communication skills. However, at the end of a shift, even the most conscientious person is eager to go home. A typical 12-hour shift handover may last up to 30 minutes; however, it is crucial that the length of a handover is not impacted by time pressures. A handover should be allowed to take longer if there are unusual operational circumstances to report or if a handover report is left unwritten until the end of a shift and the operator needs to remember several fine details that occurred up to 6-12 hours prior.
Preventing any interruptions during a shift handover is also critical. An organisation should make plans to prevent any interruptions and remove devices such as phones that may interrupt safety critical communications. Oil and gas facilities are also noisy, so it is essential to find an appropriate, quiet place to conduct a handover.
Improving communication skills
In many organisations, learning about how to conduct a shift handover is done informally through trial, error and observation. It is fundamental that a company ensures its employees are aware of the shift handover procedure and what is expected of them. It is also essential that an organisation looks to improve certain attributes in their workers’ communication skills so that handovers can be conducted in a clearer and more structured way. These attributes include but are not limited to, providing unambiguous information, choosing the correct method of communication, selecting the right tone, nonverbal cues, being assertive where necessary, confirmation of understanding messages etc.
It is not good enough to just leave a logbook for the incoming shift to read because there is no opportunity for feedback. When possible, handovers should be conducted face-to-face with relevant information, such as a logbook and computer screen, easily accessible. Both parties should participate in two-way dialogue which includes questioning, clarification and explanation. In recent years, digital handover systems have been used in some organisations, however face-to-face communication is the best way to conduct a complete and accurate shift handover.
Conclusion
Poor shift handover has contributed to some of the world’s worst oil and gas disasters. Organisations must promote a positive safety culture and improve their approach to communication at all levels so that effective shift handovers are conducted, and incidents are prevented. Handovers are a critical activity and should be regarded as high priority for any organisation active in hazardous industries. Shift handover improvements require a systemic approach, including procedure, training, assessment, monitoring and auditing. Face-to-face shift handovers are essential and using more than one communication medium (written and verbal) increases the efficiency of handovers and clarifies any misunderstandings. High-risk shift handovers, such as maintenance activities across shift changes or deviations from normal working modes at a plant, need to be given particular attention. Allocating more time for handovers between experienced and inexperienced staff, and implementing a structured logbook are also vital in helping to reduce the level of risk in a handover.
About the author
Shahram Vatanparast MSc CFIOSH is a Chartered Safety and Health Practitioner and Human Factors Engineer. Over the last 20 years, he has worked on various oil and gas projects throughout Middle East and South East Asia.
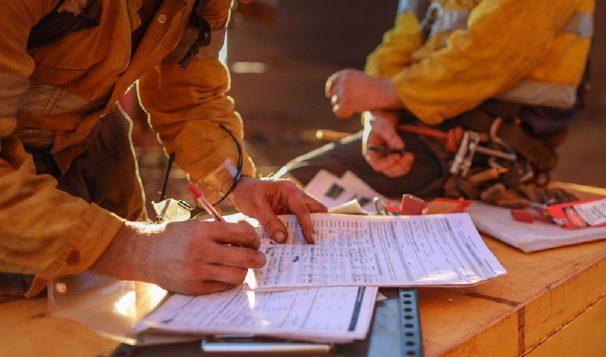