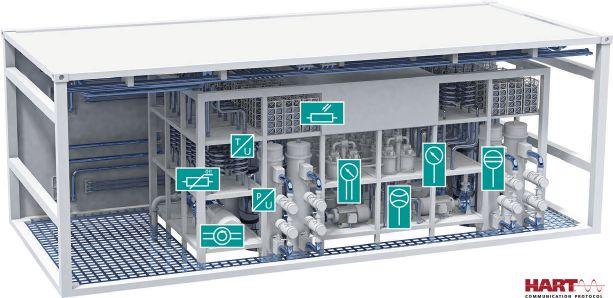
5 minute read
HART increasingly used for quick diagnostics
Pluggable disconnect terminals for process engineering control systems
By Alan Sappe’ and Torsten Schloo
Advertisement
Figure 1: In the chemical and process industries, the cost of technology is rising, especially given tighter process schedules — pluggable test disconnect terminals simplify servicing and maintenance. All graphics courtesy: Phoenix Contact
“M ore complex, more compact, more efficient” – is the credo for control system engineers in the oil & gas, chemical, and process industries. This view also accelerates efforts to squeeze production into tighter and tighter process schedules.
Over the last few years, engineers in the petrochemical and process industries have tested many new ways to make production quicker, cheaper, and more flexible — quite successfully in some cases. These advances help the industry recover relatively quickly from cyclical downturns. Modularization, industrial automation, retrofitting, and system expansion all contribute to industry success.
These tendencies have also facilitated the increased use of Highway Addressable Remote Transducer (HART) communication protocolcapable sensors and control valves. This protocol uses traditional 4-20 mA current loop as a transmission medium for a modulated data transmission signal in accordance with the Bell 202 FSK standard, where communication is conducted with signal sequences of varying frequencies alternating between command and response on simple twisted-pair cables. This keeps implementation costs down, without affecting the actual analog measurement signal. It allows the system
to transmit multiple pieces of information and makes it possible to diagnose problems or configure devices remotely.
Over the past 25 years, countless HART devices have been installed in applications related to flow, pressure, temperature, and fill-level measurement. In many cases, only the 4 - 20 mA signal is permanently connected, while HART data is only accessed during start-up or troubleshooting.
What are disconnect terminals?
HART is used with several sensors for measuring temperatures, pressures, vacuums, filling levels, distances, conductivities, densities, and pH values. Valves, servomotors, inputs and outputs of all varieties, and analog values are also controlled using HART. This can be done in three ways: 1. Readjustment and calibration of measurement values 2. Troubleshooting in complex systems 3. Parameterization or querying of device configurations using a computer.
It is often necessary to connect measuring or diagnostic devices to a current loop — to measure the parameters that the sensors receive and to evaluate the switching states or system parameters. In conventional control systems that do not use a current loop for data communication, a short signal interruption does not necessarily cause any problems. But if the current loop is also the transmission medium, interruption causes a break in communication with the HART modem and a system error message is sent. That explains the indispensable value of interruptionfree connection for HART-controlled systems.
Innovative and rugged disconnect terminals have test sockets on each side of the disconnect point where a measuring device is inserted before the disconnect knife or switch is opened. This action must be completed before the measurement. Test disconnects make that action easier for technicians because the disconnect zone is
designed as a contact spring. The contact spring is automatically disconnected when a suitable test adapter or probe is inserted. The plug’s disconnect pin ensures that capacitive contact is made with the test socket. This facilitates safe, interruptionfree connections so that HART communication is not impaired during the measurement process.
Reduce downtime
Advantages of a pluggable disconnect terminal include ease of operation, troubleshooting efficacy and space savings. Any signal conducted through such a terminal can be easily evaluated by quickly plugging in the test probe. This is particularly convenient during troubleshooting. When technicians are working with conventional disconnect terminals, they must ensure that the test lines are secured and do not slip. Testing lines also often impair the opening and closing of the disconnect knife blade. Special disconnect terminals, with widths as narrow as 6.2 mm, can be installed and operated in compact spaces within the control system.
It is also important to avoid errors due to interruption of the HART protocol. Such errors would consume a great deal of time and require unnecessary space in error message logs. Finally, responses can be conveniently tested at the disconnect terminal with analysis and diagnostic devices.
Eliminate errors, calibrate readings
Despite simple bus topology, system faults may still require repeated service calls. During such calls, technicians need quick, easy access to the signals by means of multimeters, diagnostic tools, and current loop profile calibrators. Common causes of faults include: • Substandard connections or corrosion at the connection point in the complex system structure, resulting in inaccurate measurement values • Overloaded 24 V voltage supplies, leading to an undefined sensor or actuator signal state • Incorrectly interpreted input and output signals that disrupt the process • Noisy measurement signals from the signal transmitters that make it difficult to adhere to process schedules.
Pluggable disconnect terminals provide welltested electronic component technology. The clamping sleeve’s Reakdyn design ensures a self-locking screw connection, and nickel-plated clamping sleeves and silver-plated contact springs ensure stable, low transition resistances. The spring’s base material is a hard copper alloy — the surface is passivated and greased to better protect against corrosion. These disconnect terminals are shock- and vibration-tested according to DIN EN 61373, with a Category 1B certification. The terminal withstands salt spray atmospheres, according to industry standards DIN EN 60068-2- 11, with a test duration of 144 hours, as well as atmospheres containing sulfur dioxide, according to DIN EN 50018.
Defined switching behavior
To address switching applications of a disconnect terminal, some manufacturers offer three test disconnect adapters available in multiple colors. This allows either capacitive (red) or delayed (green) disconnection based on the differences in the disconnect pins. For a simple disconnect procedure, there are service disconnection plugs, which do not provide power pick-off terminals (gray).
Building a bank of multiple blocks and using simple wire jumpers make it possible to construct suitable circuits for use with current and capacitor voltage transformers. This allows current transformers to be capacitively short-circuited. With current ratings of up to 10 A/300 V per UL 508A and 1059 standards, and a maximum of 6 mm² clamping capacity, test disconnect terminals cover a large portion of process engineering requirements. For currents up to 30 A, more powerful products that feature inline test disconnectors can be used.
In addition to disconnect terminals, a comprehensive HART solution typically includes components such as signal isolators, surge protection devices, multiplexers, and USB modems. By providing a cost-effective, permanent connection to HART data, process engineers can optimize maintenance and system operating times. OG
Alan Sappe’is product marketing manager at Phoenix Contact USA, with more than 20 years’ experience in industrial connectivity and control systems.
Torsten Schloo is product marketing manager at Phoenix Contact headquarters in Blomberg, Germany, with 10 years of experience in planning and maintenance of robot-assisted manufacturing systems and another 20 years in industrial connection technology.