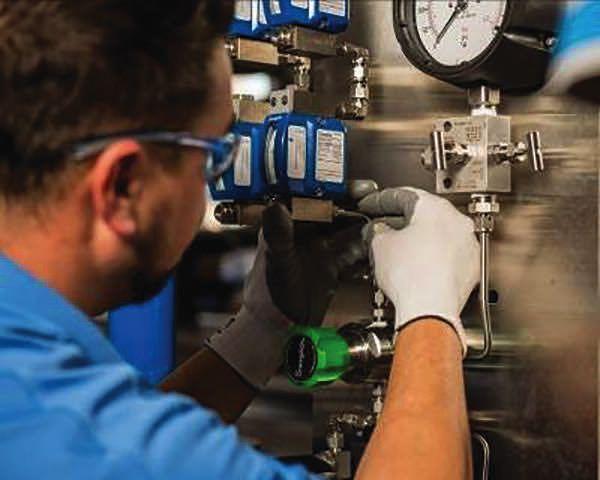
8 minute read
Execute an effective plant turnaround in seven easy steps
from PE_21_01_02
by Modiconlv
SOLUTIONS
ENTERPRISE ASSET MANAGEMENT
Advertisement
By Lawrence Crynes
Execute an effective plant turnaround in seven easy steps
Follow these tips to make a plant turnaround run smoothly and ef ciently
Refineries and chemical plants do not undertake plant turnarounds lightly due to their inherent complexity. A turnaround can often entail the use of hundreds of technicians from multiple vendors, all aiming to finish important maintenance, revamping and renewal projects either on specific systems or across entire plants at once.
In addition, plant turnarounds often require facilities to halt production. Owners and operators have a vested interest to make sure a turnaround goes smoothly. The longer turnarounds take, the longer contractors are on site, which increases costs and risks for the plant’s management. Sometimes, particularly in larger plants, a turnaround can involve years of planning and constitute a major investment by the owner. In fact, it is not unusual for turnarounds to be a significant part of the plant’s annual maintenance budget. As a result, a poorly managed turnaround can be costly for plant managers.
Taking all that into account, the following seven tips will help owners and operators ensure effective turnaround management, enabling them to save significant time and money — not to mention headaches.
No. 1. Engage early with trusted suppliers
Given the complexity of many plant turnarounds, it can sometimes take years of planning before the work ever starts. It is important for owners and operators to prepare as much as possible to minimize potential project challenges.
Part of being adequately prepared for a turnaround is the willingness of an operator to enlist the help of critical parts and service suppliers as early in the process as possible. The complexity of major fluid systems means specialized parts and components constructed from specific alloys will be needed for various processes. Such parts typically require longer lead times, so early engagement of authorized vendors will help to ensure these highly engineered parts will be available when needed. By talking with your suppliers early in the process, those timelines can be synched.
No. 2. Identify areas of new opportunity
When turnarounds are planned, owners’ minimal expectations are that systems will be returned to their original working condition. However, turnarounds also offer another key opportunity: a chance for plants to upgrade and improve their systems, which can mean higher reliability and performance.
Improving systems does not happen by chance. Owners must sign off on system adjustments well before a turnaround event. Plants that have already reached out to their vendors ahead of time – see tip No. 1 — are at an advantage and can enhance their outcomes by engaging their vendors for expert recommendations on system improvements.
Replacing traditional grab sampling elements in a system with pre-engineered and assembled grab sampling panels is just one example of a potential system improvement. This practical option does not require the plant to retool its design. Rather, the vendor will customize the panels to the plant’s specifications and optimize the components inside for accuracy and safety, simplifying future maintenance and repair needs while also enhancing the ability of owners to draw proper samples more easily (see Figure 1).
Figure 1: Replacing traditional grab sampling elements in a system with pre-engineered and preassembled grab sampling panels can enable efficiencies from the system design stage to installation to maintenance. Image courtesy: Swagelok Co.
Figure 2: Using standardized mechanical seal support systems can streamline installations, servicing, and replacements, while improving mechanical seal longevity. Image courtesy: Swagelok Co.
Figure 3: A fully documented, prefabricated fast-loop system like this enables consistent, simplified installations during plant turnarounds to enhance efficiencies. Image courtesy: Swagelok Co.
No. 3. Be prepared for the unexpected
As with any major project, variables and contingencies are inevitable, so anticipating them is another way owners can improve overall turnaround effectiveness.
Thanks to the large and complex nature of fluid systems in chemical plants and refineries, it is difficult to know the precise number and nature of the components that will be needed during a typical turnaround. As a result, it helps to have a variety of hoses, valves and adapters on hand before the project begins. It will save time and money to have basic parts on site at the plant instead of having to order them once the project has already commenced. Sometimes waiting for a single part can cause significant progress delays.
The trick is balancing the need for basic parts while avoiding the pitfall of unused inventory. Project managers should try to negotiate terms with suppliers that would let plants stock temporary or consignment inventory, so the proper parts are always available. That way, plant operators will only be charged for the actual parts used for the project.
No. 4. Ensure the availability of local support
No matter how well you plan, there will be unforeseen issues that arise — and they may require you to order parts to solve the challenges. That is why it is critical to use vendors that can offer localized support near your project so they can deliver the necessary parts in a timely fashion. Quick-turnaround deliveries are often a necessity to maintain overall progress, and a local supplier may be able to provide a part within a day or less after being ordered.
No. 5. Installation training Is critical
Turnarounds often involve hundreds of workers from different companies, making it difficult to maintain consistent levels of installation knowledge. But inconsistency can doom a turnaround project and cost owners’ money.
What can you do to standardize installations and ensure proper practices are used across the variety of contractors working on the turnaround? Attempt to incorporate training and certification levels in your specifications. That way, anyone working on the turnaround will be required to have the same baseline knowledge and will be cognizant of sound installation best practices. Internal plant personnel who will be involved in turnaround projects can also benefit from a training refresher, so consider partnering with a supplier to review a variety of installation basics. For example, training on fluid system installations may include a review of basics such as how to properly prepare and bend tubing, as well as best practices for tightening and inspecting fittings.
No. 6. Seek out prefabricated assemblies
Fluid systems in chemical plants and refineries are often complex, but if plant managers specify prefabricated, preassembled and pretested systems before the turnaround begins, contractors will have a much easier time installing them.
With prefabricated assemblies, the concerns about inconsistent knowledge and installation practices
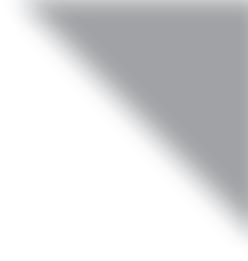

SOLUTIONS
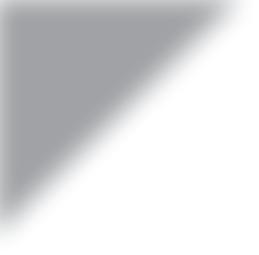
ENTERPRISE ASSET MANAGEMENT
between vendor groups can be partially relieved and free up workers for other tasks. As noted above, prefabricated grab sampling assemblies and panels enable easy plug-andplay installations, helping to accelerate new implementations and replacements, while ensuring all components are built to specifications, tested, and verified prior to installation.
Standardized mechanical seal support systems are another option. Such kits and assemblies comply with approved American Petroleum Institute (API) 682 designs and consider such aspects as convenient locations for vents and drains, proper flow and circulation paths for fluids, and safety mechanisms. Their standardized nature enables easy replacements, while their overall design can help improve the longevity of mechanical seals, saving plants money and downtime (see Figure 2).
Finally, fast loops, field stations, calibration and switching modules, sample probes and fluid distribution headers can also be simplified and bring consistency to your operations. Suppliers can provide fully
documented fluid sampling and control systems that eliminate the need to otherwise acquire and assemble multiple parts (see Figure 3).
No. 7. Maintain tight quality control
Quality control over parts and equipment is essential to executing a successful turnaround. If specifications offer too much flexibility, contractors might use less expensive — but lower-quality — parts. With inconsistent part quality comes inconsistent performance, unnecessary maintenance requirements, and/or downFigure 4: Engaging early with trusted suppliers time. Tight, up-to-date specifications lead to highercan lead to the implementation of best quality components being used in your fluid systems, practices that save time and money, including which makes turnarounds more effective and efficient. heading off potential delays for critical, highly Consistent specifications will reduce the intermixing engineered parts and systems. Image courtesy: of parts from different suppliers, making the job of Swagelok Co. keeping the systems in working order much easier in the future.
Keys to efficient turnarounds
A plant turnaround will nearly always be major endeavor, but it does not have to be a major headache — especially when you plan ahead. Remember to get trusted suppliers on board early to not only be prepared to deliver timely supplies and support, but also to help you plan logistics and potential contingencies to ensure efficient turnarounds. Using these best practices as your guide can help your plant turnarounds go much faster and more efficiently, while also enabling the potential to upgrade the long-term dependability and performance of your fluid systems. PE

Figure 5: Vendors that offer localized support can often deliver parts in a timelier manner — sometimes within a day or less — to help keep turnarounds on schedule. Image courtesy: Swagelok Co. Lawrence Crynes, Ph.D., is market manager, oil & gas, for Swagelok Co.
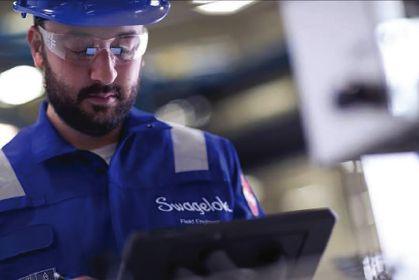
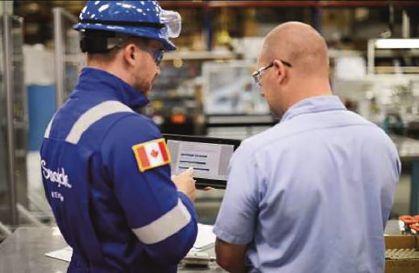
Figure 6: Supportive suppliers can help plant owners and operators be prepared for the unexpected by anticipating supply needs and offering the stocking of temporary or consignment inventory. Image courtesy: Swagelok Co.