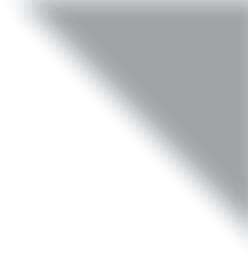
3 minute read
How to communicate an automation project
from PE_21_01_02
by Modiconlv
INSIGHTS
PROJECT MANAGEMENT
Advertisement
By Claudia Jarrett
How to communicate an automation project
Staff support is essential for the integration process; tips on how to get employees on board with a new automation project
Abook, “Teamwork makes the dream work,” by John Maxwell, was written with the idea that by working in a team, you will fulfil your dreams. This concept can be applied to all manufacturing practices, as by realizing one’s dreams and communicating them well, manufacturers can remove concern and create understanding among staff.
Manufacturers are increasingly investing in robotics to automate tasks such as welding, packing, dispensing, cutting and handling. Developments in robotics, industrial vision and cobots are opening new opportunities for companies to apply automation to mass production processes. Businesses operating high-mix, low-volume production environments looking to incorporate Lean manufacturing principles can see a powerful business case for automation.
While the benefits of automation to a business’ bottom line are clear, the benefits to employees may be more shrouded in doubt. Though an increase in automation means that job roles are changing, rather than lost, concerns around job security could potentially threaten employee support for an automation project.
In the 2019 Annual Manufacturing Report, Cara Haffey, industrial manufacturing and automotive leader at PWC, highlighted the need for clear and strong leadership in automation. Manufacturing managers are leading the charge toward automation and as part of this, must remember to minimize the risk of miscommunication about the impact of automation on their employees.
Be ready to answer
An important factor of leadership is not only communication itself but ensuring the right message has been delivered in the right way. With new projects, staff might want to ask questions and receive reassurance that they will be safe working around the robots.
Clearly defining and sharing your health and safety policy, explaining the safety features of equipment and being clear about how staff will be working alongside automation equipment can help to address this concern effectively. Staff might also have concerns about maintaining the equipment and the risk of downtime, which manufacturers can address by partnering with a reliable automation equipment supplier and communicating this clearly with employees.
Explain your reasoning
Once all employee concerns have been addressed, manufacturing managers must also explain to their workforce what is happening with the automation project. A clear vision must be communicated honestly and early to avoid misconceptions. Because people may be fearful of automation’s impact on job security, an early line of communication can go a long way to reassuring the workforce.
Once you have decided on what automation you are going to implement, delivering presentations to employees is an important process. The presentation should clearly outline why you are investing in robotics before discussing how the company will proceed. The scope of automation also must be explained — are you adding a new robotic cell or building an entirely new line?
During your presentation, you also can explain the timescale for the project and detail the employees’ involvement in the integration of the new equipment, as well as if and how their roles might change long term. Being able to understand the how and why behind automation is essential if the process is to gain the necessary traction.
If your company is to build the support it needs for a new automation project, managers must think carefully about internal communication. By taking advice from John Maxwell, manufacturers can get their staff behind their new automation project and make the dream work. PE
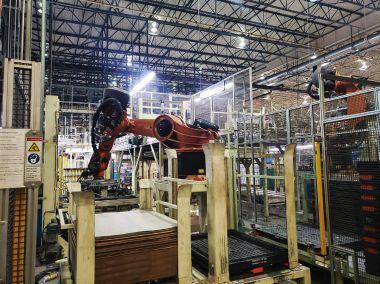
Claudia Jarrett is the U.S. country manager at automation parts supplier EU Automation.