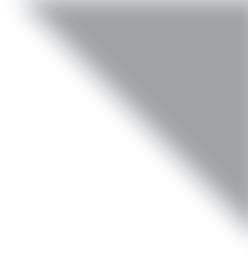
10 minute read
E-House OEM delivers higher asset utilization
PlantEngineering.com
3010 Highland Parkway Suite 325 Downers Grove, IL 60515 Ph. 630-571-4070, Fax 630-214-4504
Advertisement
CONTENT SPECIALISTS/EDITORIAL
KEVIN PARKER, Editor KParker@CFEMedia.com
JACK SMITH, Managing Editor JSmith@CFEMedia.com AMANDA PELLICCIONE, Director of Research 860-432-4767, APelliccione@CFEMedia.com KATIE SPAIN NAREL, Art Director KSpain@CFEMedia.com SUSIE BAK, Production Coordinator SBak@CFEMedia.com
EDITORIAL ADVISORY BOARD
H. LANDIS “LANNY” FLOYD, IEEE Life Fellow H.Landis.Floyd@gmail.com JOHN GLENSKI, President, Automation Plus jglenski@processplus.com SHON ISENHOUR, Partner, Eruditio LLC sisenhour@EruditioLLC.com
DR. SHI-WAN LIN, CEO and co-founder,Thingswise, LLC Industrial Internet Consortium (IIC) board member shiwanlin@thingswise.com JOHN MALINOWSKI, Senior manager of industry affairs (retired), Baldor Electric Company DAVID SKELTON, Vice president and general manager Phoenix Contact Development and Manufacturing dskelton@phoenixcontact.com
BILLY RAY TAYLOR,
Director of commercial and off-highway manufacturing The Goodyear Tire & Rubber Billytaylor@goodyear.com LARRY TURNER, President and CEO, Hannover Fairs USA lturner@hfusa.com
MARK WATSON, Senior director, manufacturing technology, IHS Markit Mark.watson@ihsmarkit.com
CFE MEDIA CONTRIBUTOR GUIDELINES OVERVIEW
Content For Engineers. That’s what CFE Media stands for, and what CFE Media is all about—engineers sharing with their peers. We welcome content submissions for all interested parties in engineering. We will use those materials online, on our Website, in print and in newsletters to keep engineers informed about the products, solutions, and industry trends. * www.plantengineering.com/contribute explains how to submit press releases, products, images and graphics, bylined feature articles, case studies, white papers, and other media. * Content should focus on helping engineers solve problems. Articles that are commercial in nature or that are critical of other products or organizations will be rejected. (Technology discussions and comparative tables may be accepted if non-promotional and if contributor corroborates information with sources cited.) * If the content meets criteria noted in guidelines, expect to see it first on our websites. Content for our enewsletters comes from content already available on our Websites. All content for print also will be online. All content that appears in our print magazines will appear as space permits, and we will indicate in print if more content from that article is available online. * Deadlines for feature articles intended for the print magazines are at least two months in advance of the publication date. Again, it is best to discuss all feature articles with the content manager prior to submission.
Learn more at: www.plantengineering.com/contribute
INSIGHTS
By Kevin Parker, Editor
Address strategic flow control concerns
How will U.S. industry restructure to support the reshoring of productive capacity from overseas? One challenge will be finding the skilled workers to fill those repatriated positions.
While automation and the growing scope and scale of software applications may eliminate repetitive, unsafe or manual work, computerization itself calls for a skilled workforce. Moreover, when it comes to things like data science and analytics, manufacturing has to compete with the financial, medical and oil & gas industries for gifted personnel.
In the recently published 2020 Plant Engineering salary survey (Jan/Feb 2021), 43% of respondents said that lack of skilled staff was one reason why their facilities outsourced select functions to 3rd parties.
One way to make best use of scarce resources is to station them centrally while connecting them as managed service providers across a wide range of production resources.
Industrial fluid motion
To date, most managed services providers are purveyors of information technologies. It’s also proved effective for things like the compressors used in the upstream and midstream oil & gas industries.
Dallas-based Flowserve’s introduction of its RedRaven IoT services platform is a good example of the managed services concept extending into other areas, in this case flow control.
Flowserve’s IoT service suite helps production facilities monitor assets remotely, predict equipment failures before they happen and take preventive measures to avoid business disruptions.
The platform supports any flow control equipment regardless of manufacturer, opening the door for companies to realize IIoT and predictive analytics benefits without major infrastructure changes. Use of predictive maintenance is growing, made possible by IIoT technology for sensing and connectivity, while analytics are applied to the gathered data. “We’re betting big on IoT to help companies avoid costly downtime, which is not allowable in today’s world,” said Scott Rowe, Flowserve president and chief executive officer. “The COVID-19 pandemic illustrated the critical importance of digitalization in production facilities.”
RedRaven includes sensors for placement on industrial equipment and gateways to collect asset data that is securely transmitted to the cloud. Companies access critical equipment performance data via a portal dashboard.
The remote monitoring facility doesn’t just identify problems, it addresses issues. RedRaven is suited for the oil & gas, water, chemical, power, food & beverage and mining industries, among others. The name RedRaven comes from the bird known for its intelligence and insight.
Let’s talk it over
On April 9th, Flowserve will sponsor a CFE Media webcast on how IIoT and remote services enable major changes in industrial flow control.
Join us that day, as we discuss application of IIoT, analytics and managed engineering services to industrial fluidmotion processes with Flowserve’s Vice President of Global IoT, Aric Zurek.
Topics will include current challenges in industrial flow operations under COVID-19 business restrictions; how IIoT is being applied in industrial flow environments; why managed services use is growing; and the application of analytics in industrial environments. For more information, visit the Plant Engineering website under the “online training” tab. PE
INSIGHTS
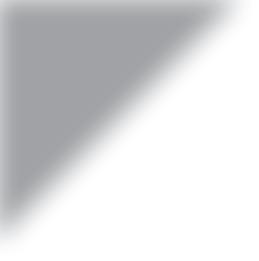
THE GLOBAL SUPPLY CHAIN THE GLOBAL SUPPLY CHAIN
By Lewis Black By Lewis Black
New production sources for tungsten are critical for increased global supply
Little known tungsten has a multitude of use cases
In the wake of the pandemic, as manufacturers ramp back up to produce everything from automobiles to airplanes, they will face the normal litany of production challenges, which includes dealing with a strained supply chain on certain critical raw materials, such as tungsten.
Tungsten is the most valuable material you’ve never heard of. Tungsten is frequently used to make items that aren’t considered everyday products, but nevertheless are critical for almost everything that’s important, such as core drilling bits and diamond drilling bits used by the mining industry.
Among the most durable elements found on earth, tungsten is also used in more everyday items such as lamps, transistors and alloys, as well as construction tools and components in airplanes and automobiles. It is one of the most important raw materials on Earth.
Tungsten is valuable because of its strength and durability, and because it offers one of the highest melting points of all elements on the periodic table. There would be no rockets or aerospace propulsion systems without it.
However, sourcing tungsten has been a great challenge since there are no mines in the U.S. that produce this precious raw material.
China’s tungsten domination
China controls the market for nearly 35 precious minerals and metals that are important to the U.S. for production and manufacturing, and tungsten is among them. According to the United States Geological Service (USGS) in its Mineral Commodity Summaries 2019 report 2, “World tungsten supply was dominated by production in China and exports from China." Furthermore, the second largest tungsten supplier, located in Vietnam, had sourced 6 million metric tons last year. Other regions outside of the U.S. such as Russia, Austria and the United Kingdom are also known to have important tungsten sources.
The issue at hand is that China has limited the amount of tungsten exports that can be shipped to the U.S., and this has caused great concern about the overall supply chain of tungsten. "China's government regulated its tungsten industry by limiting the number of mining and export licenses, imposing quotas on concentrate production, and placing constraints on mining and processing," according to the USGS’ 2019 report 2.
Tungsten and the global supply chain
Fortunately, new entrants into the market have begun tungsten mining projects throughout the world. These efforts are critically important to increase supply levels and exports back to the U.S., which will benefit the overall global supply chain of tungsten for production and manufacturing.
One project of particular importance is the Korea Tungsten project located in the Sangdong Mine of South Korea, which hosts one of the largest tungsten resources in the world. This mine was the leading global tungsten producer for more than 40 years and it has the potential to produce 50% of the world’s tungsten supply. The project has become a center of focus recently for resource experts, miners, investors, shareholders, and other interested parties around the globe.
Global economies are anxiously awaiting production of tungsten from this region, especially since it will ease China’s stranglehold on the overall supply. What’s more, U.S. manufacturers are keenly watching, since additional supply of tungsten from South Korea would help avoid expensive U.S. import tariffs of goods shipped from China.
Here’s hoping the Sangdong Mine will be only one example of relief U.S. and global manufacturers will see from the mining and production of tungsten as a means to enhancing its global supply chain, sorely needed for some of today’s most important uses. PE
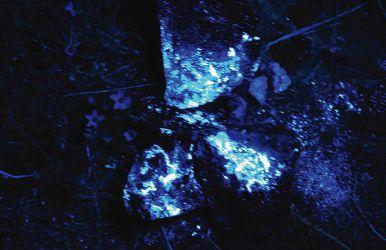
Lewis Black is CEO of Almonty Industries, involved in the mining, processing and shipping of tungsten concentrate.
INSIGHTS
ENTERPRISE ASSET MANAGEMENT
By Craig Greenhalgh
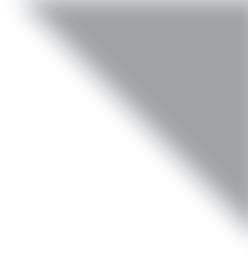
How to increase ROI and ef ciency with EAM
The management of physical assets, from tools and equipment to movable fleets and infrastructure, is critical for asset-intensive businesses. Whether the goal is to grow revenue, reduce downtime or improve asset performance, an effective asset management and maintenance system holds the key to greater efficiency — not to mention the role it plays in improving maintenance strategies, with asset failure costing businesses 10 times more in repairs and lost production than it does to implement a proactive approach to maintenance. The asset management and maintenance market is dominated by two tools? computerized maintenance management system (CMMS) and enterprise asset management (EAM) software. While on the surface, these two solutions seem to do the same thing, they do not. Whereas both are geared toward maintenance management, EAM provides a more robust and complex approach that goes beyond the capabilities of a CMMS.
Think again
Although similar in their approach to maximizing the performance and useful life of physical assets, there is a defined difference between a CMMS and EAM toolset. For example, both systems are designed to optimize asset maintenance, offer cloud-based subscriptions and provide various inventory tracking features. But that’s just the beginning when it comes to EAM; the natural stepping stone for a fast-growing organization wanting to greatly increase its efficiency when managing assets.
As lines continue to blur between the two asset management models, particularly with the advertisement of EAM/CMMS hybrid models, it’s important for asset-intensive business owners to know the difference between EAM and a CMMS (see Figure 1).
What a CMMS is
A CMMS does exactly what it says on the tin; it manages maintenance in a computerized system. Although capabilities can vary and tools can be added to work alongside a CMMS, its capabilities are limited to managing the maintenance of physical assets. However, EAM tools have an additional focus on asset performance analysis and total cost of ownership (TCO).
That doesn’t necessarily mean a CMMS is the wrong choice. The right system will provide tools to streamline maintenance operations and deploy a proactive maintenance approach, whether preventive, planned or predictive. Its ability to manage work orders and assist with spare parts at a reasonable purchase price makes it an attractive solution for most small to medium maintenance operations.
What EAM is
EAM is a more powerful, robust and complex tool in terms of asset maintenance management. A focus on maintenance management is just a fraction of its capabilities, providing enterprises with detailed data regarding their most critical physical assets.
Typical features of an EAM system include work order management; supply chain and inventory management; maintenance, repair and operations (MRO) planning and procurement; project management; accounting; safety and compliance; and big data analytics to gauge TCO.
Figure 1: Asset-intensive business owners should know the difference between EAM and a CMMS. Courtesy: Comparesoft.com
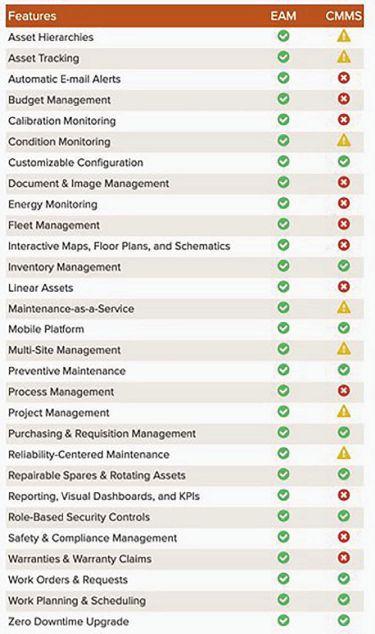