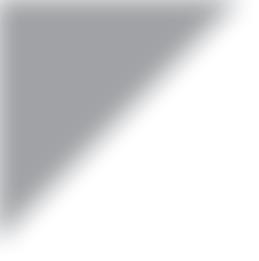
36 minute read
Next-gen trim cuts rotary valve cavitation
INSIGHTS
ENTERPRISE ASSET MANAGEMENT
Advertisement

With this collective arsenal of data gathering tools, businesses can store and analyze large amounts of information such as purchase costs, repair history, energy usage data, audit trails and more. By being able to collect such data, businesses can take full advantage of what an EAM solution is intended for: efficient asset lifecycle management.
Importance of lifecycle management No matter the type or size of a business’s operations, all asset-intensive organizations rely on the proper upkeep of their assets, particularly in industries like manufacturing and utilities where large assets such as machinery and infrastructure make up a large portion of operations. Which is why, for organizations that center revenue around the output of their assets, successful asset lifecycle management is vital.
There are four stages of asset lifecycle management: planning, procurement/acquisition, operation and maintenance, and disposal/replacement. Whereas a CMMS is geared more toward the operation and maintenance phase of an asset’s lifecycle, EAM tools have the capabilities to function at all four stages.
One person who knows the benefits of deploying an efficient asset management and maintenance system is Ryan Batchelor, maintenance manager at Britvic Plc.: “We only run 24 hours, Monday to Friday. At the weekends, we shut down for planned maintenance activities…So when we start up on Monday, we’ve got smooth sailing for the week,” he said.
Being able to control the lifecycle management of each physical asset in one centralized system can be a revelation for asset-intensive businesses. Not only does it simplify data analysis and help to seamlessly share information across the right departments, but it also benefits businesses by prolonging optimal performance levels, supporting preventive maintenance strategies and ensuring compliance with regulatory standards. PE
Figure 2: An EAM is much more than just a maintenance management tool. Courtesy: Comparesoft. com Craig Greenhalgh is a research analyst at Comparesoft. com.

INSIGHTS
2021 REGULATORY AND COMPLIANCE
By Maggie Estrada and Rick Spurlock
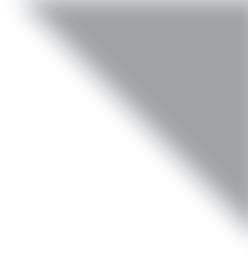
Evolving environmental policies will have big impact on power generation industry
Policies and regulations support shift from fossil fuels to clean energy
Within the power generation industry, policies are rapidly changing to require a higher percentage of clean energy plants — such as wind, solar and more recently battery storage — to replace various combustion technologies like boilers, once-through cooling plants, and simple-cycle and combined-cycle turbines. Furthermore, in many states, especially in California, additional policies are being proposed to move up the effective year the percentage of clean energy plants must be implemented.
This greatly impacts the power generation industry, as existing fossil-fueled power plants are not able to obtain renewed power purchase agreements (PPA) and thus will switch to merchant plants to sell power on the open market. However, operations and management (O&M) companies are seeking O&M contracts for wind, hydro, solar and battery storage to add to their operating portfolio.
Gas turbine units, especially those with simplecycle technologies, are implementing “fast-start” and “low-load” capabilities in order to augment power, as renewable units reduce or stop daily generation. These operating scenarios have to be evaluated against existing air permit limits and requirements to ensure compliance can be met, which often then necessitates operational testing. Permit modifications may be required to adjust permit language in order to accommodate for these specific operating scenarios.
Biomass plants play an important role in utilizing forest and agriculture wood waste to reduce open burning and minimize waste in landfills. Plant operators and managers have been working closely with policy makers to ensure biomass is included in the renewable mix. Many companies are also exploring new technologies, such as carbon capture and liquid hydrogen at biomass plants, to find the interconnections and implement them throughout the infrastructure.
Top predictions 2021 1. A big push to move up the clean energy
compliance date. For instance, in California, we can expect to see a push in legislature to get to 100% clean electricity well ahead of the current target of 2045. Senate Bill 100 requires the whole California economy to be net zero by 2045, and President Joe Biden’s new plan calls for 100% clean electricity nationwide by 2035.
2. The power generation industry will place a heavy focus on achieving 24/7 clean energy.
This year, expect to see movement toward a new 24/7 clean energy standard, which will place more focus on the times of day that are not as well served by solar and wind renewables. Currently, those times are dependent on fossil fuel power plants. This will result in a greater need for 24/7 renewables, such as biomass and geothermal, as well as for longterm energy storage.
3. The growth of carbon capture technologies
and innovation. A recent Lawrence Livermore study spotlighted the need for carbon capture and storage. For states and the nation as a whole to reach their ambitious climate change goals, carbon capture is a must. Carbon capture has encouraging potential and could radically alter the energy landscape because it allows for continued use of highly energy dense and efficient carbon-based fuels (e.g., coal, natural gas and oil) without contributing additional carbon gasses to the atmosphere.

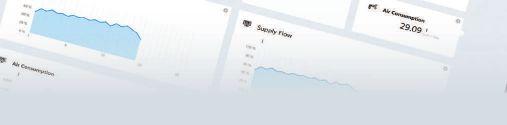

Smart IoT Compressed Air Device Delivers Advanced System Diagnostic and Energy Effi ciency

Saving energy is easier than ever before thanks to the MSE6-E2M. Achieve your energy effi ciency and sustainability targets while optimizing process equipment performance. Intelligent assembly features include:
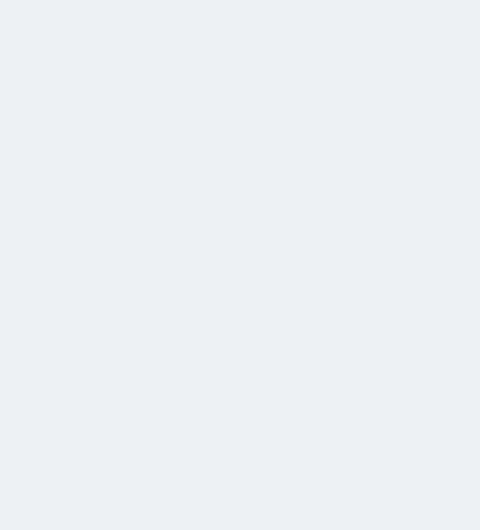
• Zero compressed air consumption in standby mode • Monitors the system for leaks • Ensures maintenance in the event of leaks • Enables effective real-time monitoring of relevant process data
INSIGHTS
2021 REGULATORY AND COMPLIANCE
Cost of compliance
The cost of environmental compliance has grown significantly over the last few years, and plants now find themselves in a fragile balancing act between cost and compliance. The main costs associated with environmental compliance can be broken down into the following categories:
• Emissions control equipment operations and maintenance costs, along with emissions monitoring equipment, operations and maintenance. This includes permit fees, control equipment (e.g., baghouse, electrostatic precipitator, stormwater filtration, hazardous waste storage areas, etc.) and monitoring equipment (e.g., continuous emission monitoring, automated storm water monitoring, meter calibrations and more). • Consumables used for compliance, such as anhydrous ammonia, limestone, waste drums and hazardous waste disposal fees.
• Engineering compliance equipment, which encompasses engineering studies, RATA/source emissions testing, and toxic emissions inventory testing and reporting.
• The labor for record keeping, tracking and compliance monitoring. Within the last two decades, many plants have had to hire a full-time employee whose job is to solely focus on maintaining compliance.
• Regulatory-requested additional emissions testing. • New and modified emissions and effluent standards. Recent lower limits require power plants to further improve or replace their control equipment prior to limits becoming effective.
Measuring the results
It’s critical to establish environmental metrics to track trends and determine where resources are necessary. Resources include additional budgets for equipment maintenance or replacement, best practice measures (BMP) implementation, the addition of plant staff focused on environmental tasks, and corporate environment support staff to provide immediate and thorough regulatory guidance and support. PE
Maggie Estrada is the vice president of environmental at IHI Power Services Corp. Rick Spurlock is the director of operations at IHI Power Services Corp.
INSIGHTS
THE AGE OF ANALYTICS
By Mohamed Abuali, PhD
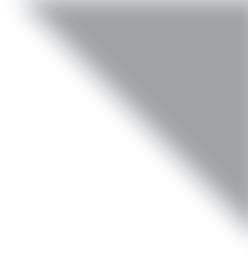
Post-pandemic, employee wellness powered by predictive analytics
Who else is tired of talking about Covid-19?
What if we reframe the Covid conversation to focus on what it’s really all about? Creating smarter, safer access to manufacturing operations, and enabling plants to focus on employee wellness and business continuity.
Regardless of whether we’re talking exotic Covid variants or the common cold, the bottom line is plant management and associates alike want healthy employees that feel good about themselves.
While the pandemic got the conversation going, manufacturers already faced considerable workforce development challenges. For one, they lack needed data. Application of analytics to that data can slow rising healthcare costs and improve employee wellness. policies and protocols that lead to good productive outcomes.
Handwashing stations and hand sanitizers are all well and good, but do they positively impact plant safety and, at the same time, boost operations productivity and continuity of operations? Besides machine uptime, how do manufacturers impact “employee uptime”?
Consider the possibilities following: • Analytics to ensure healthy employees enter the plant • Data for a 360 view of plant/employee health • Mitigation of insurance and sanitation costs • Scalability to all plant locations for enterprisewide wellness.
With the Internet of Things (IoT) for data gathering and growing availability of analytics platforms, organizations have options to engage with employees for improved health and productivity.
A.I. for wellness
What will be different about a day at the manufacturing plant once predictive analytics for employee wellness is implemented?
Arriving employees are greeted at an interactive kiosk and are asked to take a survey about any immediate health issues and a quick vitals check. Employees enter the plant after clearing both checks. If an employee’s answers fall outside pre-determined parameters for temperature or other health parameters, access may be denied. That employee is directed to the plant health resource. This is the extent of impact to plant employees. Plant leadership can be confident employees entering the plant each day are healthy.
Data gathered on employees is sent to a private, secure cloud for analysis and tracking, with compliance to HIPPA and GDPR regulations. From there, the plant decides the metrics important to track and gain insights. Plant administrators can monitor high-risk zones, and are made aware of the number of safe and denied entries.
Diagram courtesy: IoTco
Balancing health, infections and revenue
Manufacturers want the cleanest, safest and healthiest environments possible. Plant management teams want
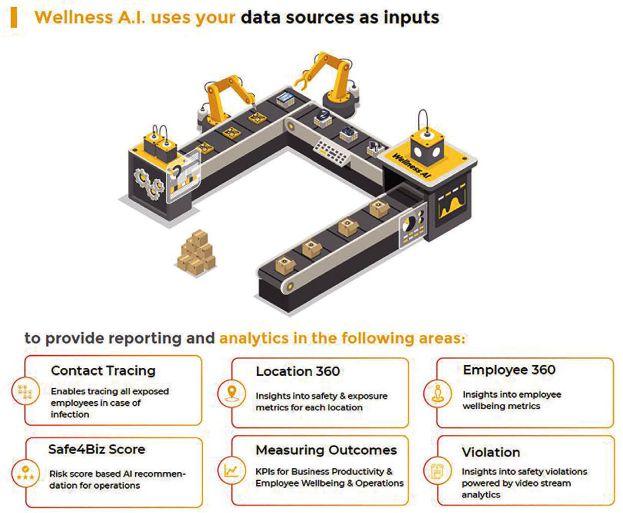
INSIGHTS
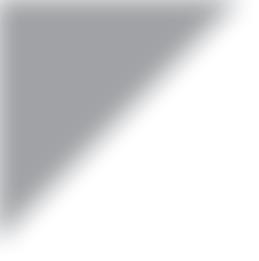
THE AGE OF ANALYTICS
Additional options for implementation include smart cameras throughout the plant that apply image-based A.I. techniques to send violation alerts if employees are not wearing masks or if there are large gatherings in potential hotspots like cafeterias or washrooms.
Additionally, wearable technology gives human resources managers the ability to gather and apply data to healthcare models in new and innovative ways. Individuals can see how their activity compares to others with similar profiles. The automatic, continuous and accurate log of activity and biometrics motivates participants to achieve their health goals.
The application of biometric data and predictive analytics in population health management can manifest health improvements in many areas including increased morale and productivity, as well as early and proactive interventions if health issues arise.
Predictive analytics and applying A.I. for employee wellness deliver a complete 360-degree view of all locations and the ability to drill down into individual plant locations. This is important because each plant may have unique metrics needed to determine overall safety. For example, if one plant has a higher average age of employee with greater chronic illness, this plant may need to be more cautious when an employee becomes ill so as not to spread illness to other high-risk employees. It is crucial to use analytics to track overall risk per employee or per location.
Delivering outcomes
Perhaps the biggest takeaway for the manufacturing industry in 2020 is that businesses that rely on their employees’ ability to safely be on-premises must find new ways to manage operations.
Many plants have embraced technology to automate production of goods as well as AI technologies for their asset health and OEE improvements. Using data analytics and “Wellness A.I.” to evaluate employee health and wellbeing is a next step in operational efficiency.
After all, aren’t your employees your most valued asset? Investing in the overall wellness of the manufacturing plant team will undoubtedly directly impact the ability to sustain operations and revenue.
The proactive management of employee wellness provides health and cost saving benefits to the manufacturing HR and EHS organizations. Predictive analytics and wearable devices, combined with smarter, safer access to manufacturing plants, are poised to transform factory health and safety management.
Key takeaways
Creating smarter, safer access to the manufacturing enables plants to focus on employee wellness and business continuity.
In addition to machine uptime, manufacturers are also looking for “employee uptime” and considering analytics to support healthy employees, increased productivity, reduced sick days, and lower costs.
Many plants have embraced technology to automate production of goods as well as AI technologies for their asset health and OEE improvements. Using data analytics and “Wellness AI” to evaluate employee health and wellbeing is the next step in operational efficiency. PE
Easy to Use • Powerful Software Priced Right
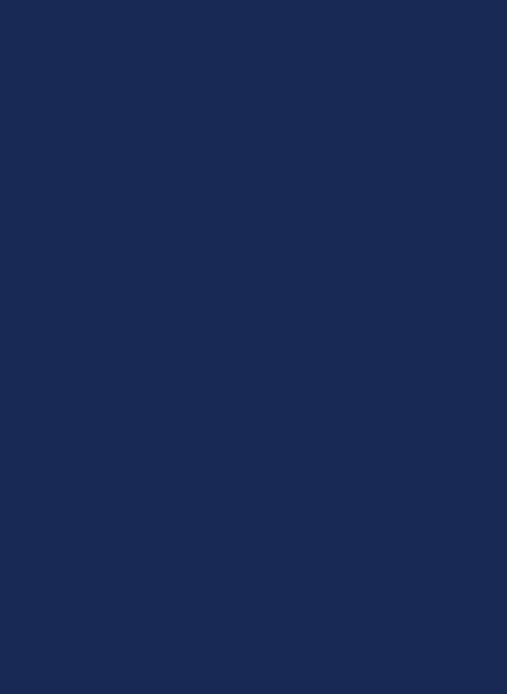

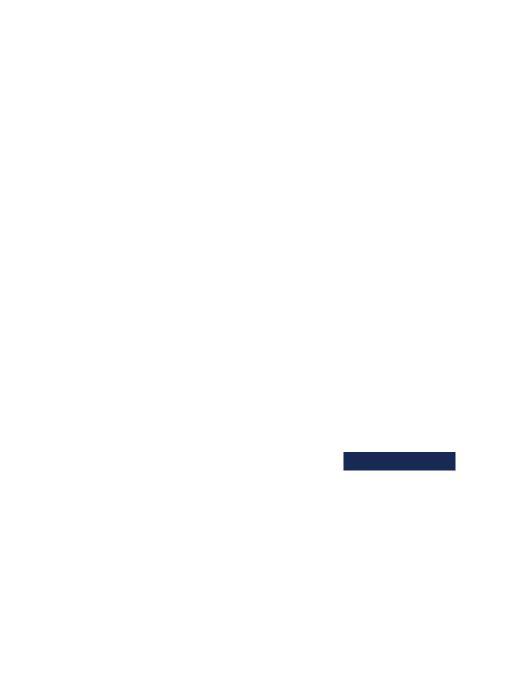
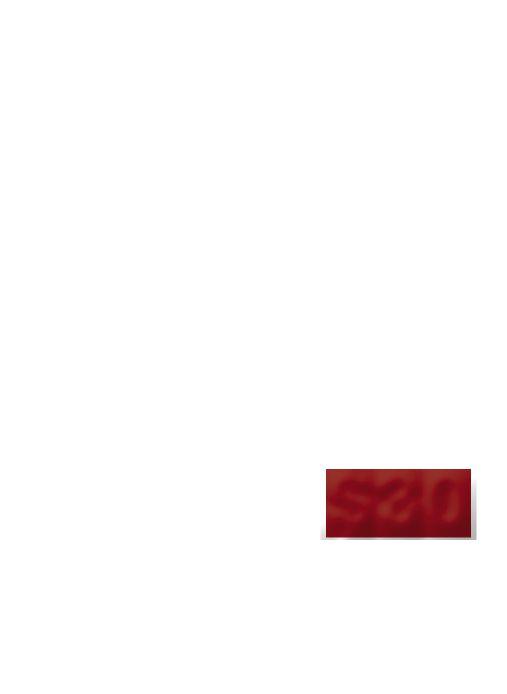
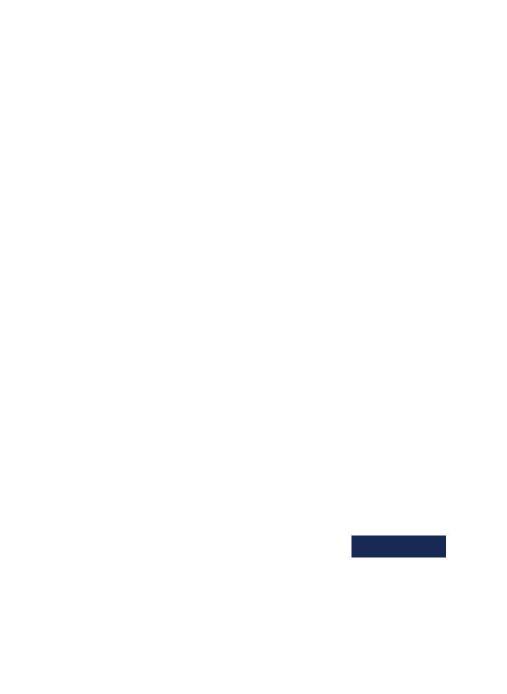

Full-featured CMMS
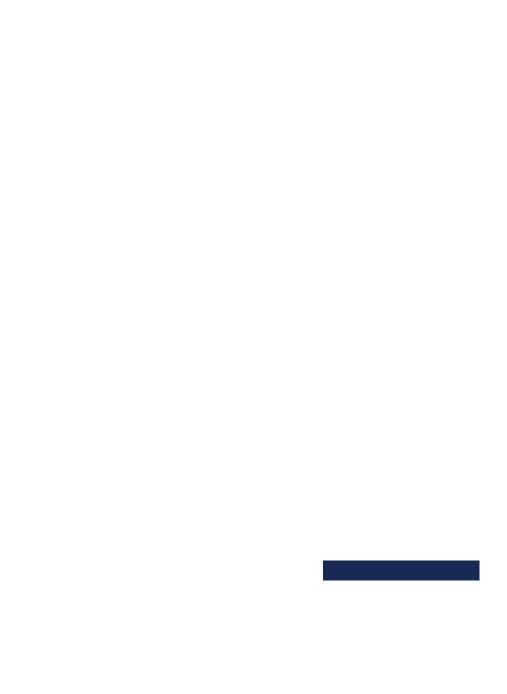
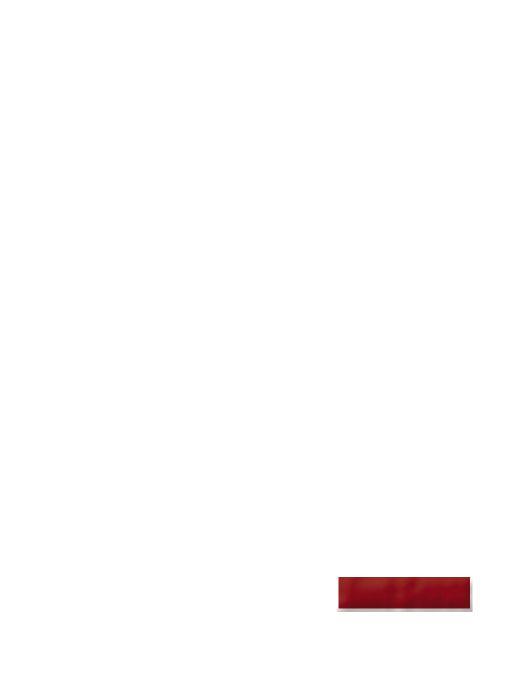

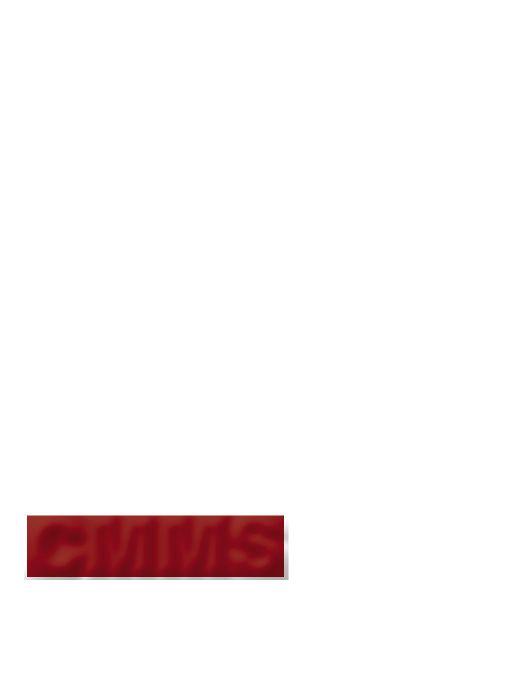
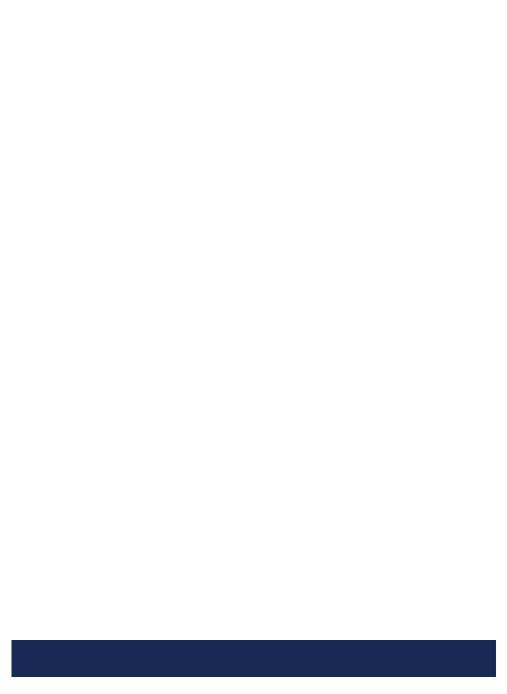

For as low as $30
per Month!
Or, own it starting at just $495!
(800) 922-4336 • mapcon.com
Dr. Mo Abuali is the CEO and managing partner at IoTco, the internet of things company. He is a strategic and transformative technology and business management leader with a 20-year record of achievement driving and sustaining change in manufacturing. Mo serves industrial and manufacturing clients in automotive,aerospace & defense and others, providing digital transformation, Industrial IIoT and predictive analytics technology and services, as well as the IoT Academy for Industry 4.0 Training. Mo has a doctorate degree in Industrial Engineering and has worked with companies like IBM, P&G, Omron, and Toyota.
INSIGHTS
DIGITAL TRANSFORMATION
By Julia Quintel and Johannes Papst
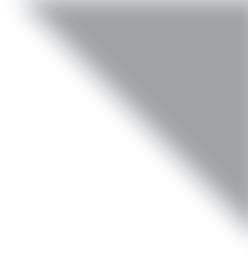
Five digital transformation trends in manufacturing for 2021
Survey shows the COVID-19 pandemic has supercharged the demand for digital offerings and Industry 4.0 technology
As much as the COVID-19 pandemic will be remembered for its chilling effect on business and economic activity, apparently it has had quite the opposite impact on industry’s zest for digital transformation and Industry 4.0 technologies.
Based on a survey of 900 C-level executives across industries, the consulting firm McKinsey concluded in October 2020 the COVID-19 crisis has brought about a years’ worth of change in just a few months’ time. Not only have companies “accelerated the digitalization of their customer and supply-chain interactions and of their internal operations by three to four years” as a result of the pandemic, McKinsey observed, “perhaps more surprising is the speedup in creating digital or digitally enhanced offerings. Across regions, the results suggest a seven-year increase, on average, in the rate at which companies are developing these products and services.”
All of which portends a period of frenetic digitalization activity in the industrial sector throughout 2021 — activity that, looking at companies across the global industrial manufacturing and automotive landscape, likely will be focused in these five areas:
1. A decisive move to modular production as part
of a broader focus on operational flexibility.A growing customer appetite for customized products is prompting manufacturers to explore new ways to make mass customization a profitable proposition. To that end, we see more manufacturers embracing modular production approaches that integrate tightly with other parts of the business.
Within an automotive factory, for example, multiple modular workstations could be established, each with their own assembly itinerary (e.g., one module to assemble battery-electric vehicles, and another to assemble hybridelectric vehicles). When efficiently configured and intelligently connected to the broader enterprise, this modular approach can make mass customization viable. In a simulation of flexible-cell automotive manufacturing, the Boston Consulting Group found that worker utilization increased by 12%, “which in turn can lead to a similar reduction in labor cost per vehicle.”
The ability to capture these types of efficiencies on the plant floor is largely predicated on an intelligent, end-toend approach whereby smart factory assets are connected to the broader enterprise. This enables a manufacturer to factor in short-term signals from sales, manufacturing, suppliers and even directly from customers — including lateorder changes, labor shortages, quality issues and machine breakdowns — and then make in-the-moment decisions on the shop floor based on their overall business impact.
2. The ascendance of extended business networks.
The pandemic-related disruptions of 2020 have made manufacturers laser-focused on resiliency in 2021. Many have looked to evolve beyond the traditional supply chain, with its inherent limitations, to a network or ecosystem construct that extends beyond company borders. More companies will move to multishoring, geographic diversity and extended business networks that include multiple tiers of suppliers, business partners, logistics providers, distributors, resellers, wholesalers, retailers and more to alleviate supply chain risk, in what amounts to an acknowledgement by manufacturers that their best chance of success comes with collaboration across the entire value chain.
This construct enables members to connect and exchange data in a safe and interoperable way to achieve real-time visibility, collaborate efficiently and take quick, sound, data-informed actions. A manufacturer would gain the ability to choose suppliers based on their proximity (to reduce emissions) or on in-the-moment component availability, for example. Having full visibility across the network enables a company and others that are part of the network to adjust on the fly to changing conditions. The recently announced Automotive Alliance is an example of how six companies within the automotive value chain are exploring an open B2B network.
3.A growing reliance on edge computing prompts a heightened emphasis on cybersecurity. As more manufacturers embrace edge computing to enable greater realtime flexibility, automation and adaptability within their plants and production processes, they also are moving to fortify cybersecurity at the edge. Amid a 2,000% year-
INSIGHTS
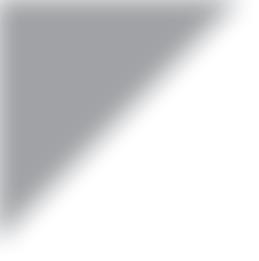
DIGITAL TRANSFORMATION
over-year surge in cyberattacks on operational technology (OT), it’s expected there will be major ongoing investment in security planning and in measures to protect networks and data that are increasingly vulnerable as manufacturers’ use of connected assets grows.
4. A major movement to mainstream sustainabil-
ity initiatives. Decarbonization, net-zero emissions, the Circular Economy — more manufacturing companies will move these once-peripheral initiatives into their core operational and business decision making in 2021, joining companies like Bosch, BMW and many others that already have made sustainability a strategic imperative. They’re motivated by their own shifting strategic priorities as well as by the growing emphasis their shareholders, customers, business partners and, of course, regulators are placing on sustainability.
Digital capabilities (track and trace, advanced modeling, digital twin, etc.) can help companies execute on their commitment to sustainability. This enables them to factor “green line” considerations into decisions across their business and to measure, report and articulate the impact their operations have in areas such as carbon emissions. In 2021 and beyond, more companies will likely turn
over-year surge in cyberattacks on operational technology to Industry 4.0 technologies to help model and develop processes tailored to the Circular Economy principals of minimizing waste and maximizing reuse. Initiatives like Climate 21 and Plastic Energy/GreenToken are developing digital tools and processes to help companies do just that. 5. A renewed emphasis on human resources — not the department, but rather the people on whom manufacturers rely to produce quality products, innovate and deliver positive customer experiences. “Even in the age of robotics, industrial manufacturers cannot run without skilled workers,” observes a 2020 study from Oxford Economics. Ensuring that employees have the necessary skills and training to work collaboratively with intelligent machines and make decisions on the fly will be a key priority for manufacturers in 2021, as will keeping those employees — still manufacturers’ most important asset — safe inside the plant. PE
Julia Quintel and Johannes Papst are solution managers in SAP’s discrete manufacturing industry business units responsible for Industry 4.0 initiatives for automotive and industrial manufacturing.
MEDIA SHOWCASE FOR ENGINEERS
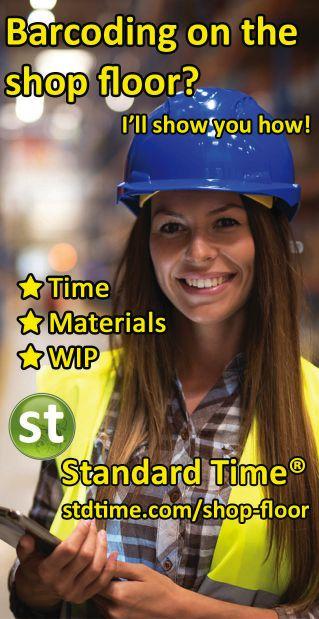


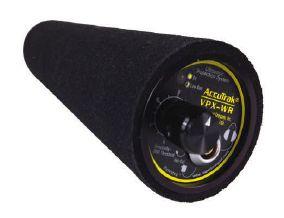
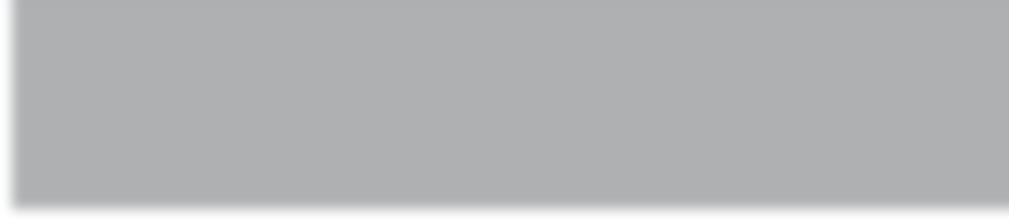
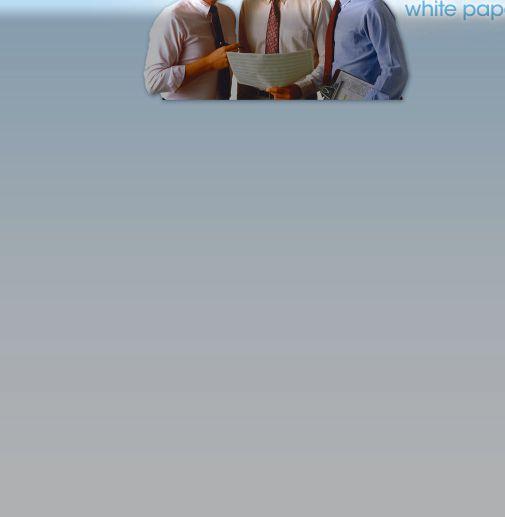
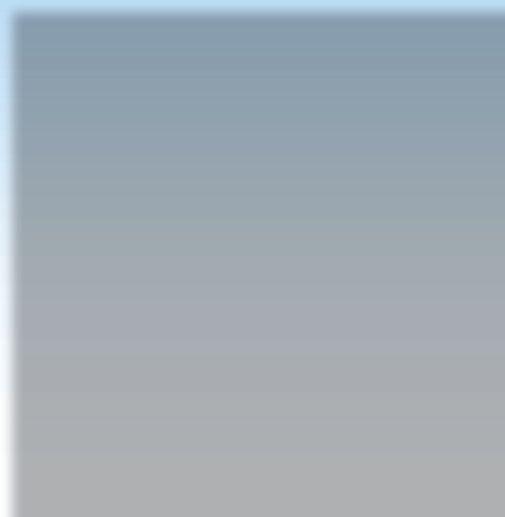

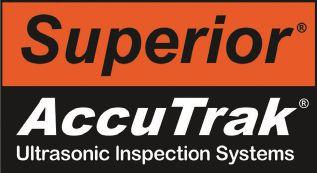
The Ultimate Air & Gas Leak Detector
AccuTrak® VPX-WR
Find Compressed Air Leaks Fast!
• Also any Gas, Refrigerant or Vacuum • Rugged Design for Harsh Environments • Sealed to Resist Water, Oil, Dust, Chemicals • Professional’s Choice for Air Leak Surveys
SuperiorSignal.com/PE
Engineering is personal.
So is the way you use information.
CFE Media delivers a world of knowledge to you. Personally.
CFE Media is home to some of the most trusted names in the business.
Consulting-Specifying Engineer Control Engineering Plant Engineering Oil & Gas Engineering
SOLUTIONS
MOTORS & DRIVES
By Thomas H. Bishop, P.E.
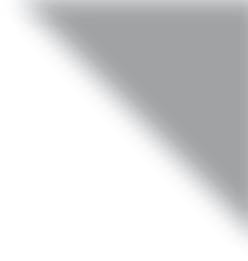
Recognize service conditions for motors and generators
Figure 1: A motor in an application that could be classified as “usual.” Courtesy: EASA W hen selecting a motor for a new application or solving a problem with an existing one, it’s important to verify the motor will operate normally in the conditions the application presents. Although these situations may not occur often, it’s helpful to understand the differences between the usual service conditions most motor designs assume and the unusual service conditions that can lead to unreliable operation and costly shutdowns.
Good starting points for this discussion are the definitions of usual and unusual service conditions in the National Electrical Manufacturers Association (NEMA) Standard MG 1: Motors and Generators (MG 1). The International Electrotechnical Commission (IEC) Standard 60034-1: Rotating Electrical Machines, Part 1: Ratings and Performance, also addresses application conditions (see Clause 6) but to a lesser extent, so the focus here is on MG 1.
Usual conditions
MG 1, 1.6 defines usual service conditions for a wide variety of motors and generators. These include general-purpose alternating-current motors, general-purpose direct-current small motors, general-purpose generators, industrial direct-current medium motors and industrial direct-current generators.
According to MG 1, general-purpose ac motor designs have “standard ratings with standard operating characteristics and mechanical construction for use under usual service conditions without restriction to a particular application or type of application.” Its definitions of the four other motor categories share this characteristics: mechanical construction suitable for use under usual service conditions. Since the manufacturer designs the mechanical construction for a specific type of motor (e.g., a general-purpose ac motor), the variables that could affect successful operation are the usual service conditions.
According to MG 1, 14.2, the usual environmental/service conditions include (see Figure 1): • Exposure to ambient temperature in the range of -15°C to 40°C, or 5°C to 40°C for watercooled machines (to prevent water from freezing). For machines rated less than 3/4 hp and all machines (except water-cooled) that have a commutator or sleeve bearings, the minimum ambient temperature is 0°C. • Exposure to an altitude of 3,300 feet (1,000 meters) or less • Installation on a rigid mounting surface • Installation in areas or supplementary enclosures that do not seriously interfere with the ventilation of the machine.
Each of these items deserves fuller explanation.
Ambient temperature. Motor nameplates frequently indicate the maximum ambient rating of 40°C but rarely state the lower ambient temperature limit. Nevertheless, operation below the minimum or above the maximum ambient temperature normally is not permissible.
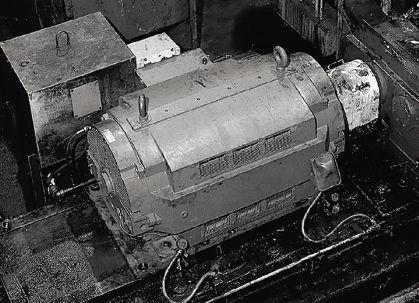
SOLUTIONS
MOTORS & DRIVES
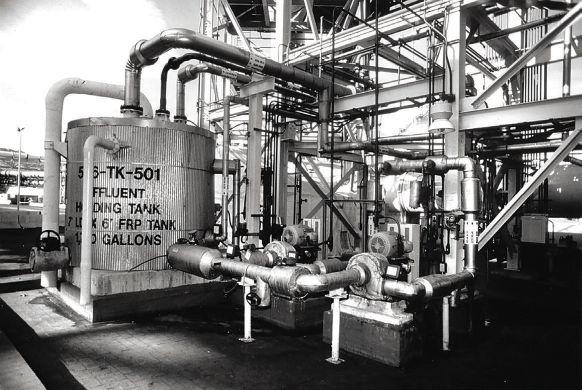
Figure 2: Motors exposed to an unusual condition of chemical (possibly explosive) fumes. Courtesy: EASA
A best practice is to check with the motor manufacturer regarding operation outside of the usual ambient temperature range. At low temperatures, bearings and lubrication may be the primary concerns. At high temperatures, the winding, as well as bearings and lubrication, may be the main issues.
Caution. The ambient rating on nameplates applies to what we often term “room temperature.” The temperature rise, or maximum winding temperature, rarely appears on motor nameplates and is beyond the scope of this article.
Altitude. Operation above 3,300 feet (1,000 meters) is not normally permissible without derating the motor power rating. Temperature rise may provide guidance for operation at such altitudes without derating the motor’s power rating, but as mentioned earlier, that is beyond the scope of this article.
Rigid mounting. Most motors mount on a rigid base, so this is seldom a concern. Consult the motor manufacturer about other mounting arrangements (e.g., a cantilevered base supported by belt tension).
Ventilation. An uncompromised ventilation system is the normal condition for a motor. An example that violates this rule would be to place a compressor motor, air compressor and controls inside an enclosure such as a cabinet.
Unusual conditions
MG 1, 14.3 provides a list of unusual service conditions and recommends consulting the manufacturer if any of them may affect motor construction or operation (see Figure 2), including exposure to: • Combustible, explosive, abrasive or conducting dusts • Accumulated dirt and debris that may interfere with normal ventilation • Chemical fumes; flammable or explosive gases • Steam, salt-laden air, oil vapor • Damp locations, radiant heat, vermin infestation, atmospheres conducive to the growth of fungus • Abnormal shock, vibration or mechanical loading from external sources.
The list of unusual exposure conditions in MG 1, 14.3 is not intended to be exhaustive or complete, because that would be too voluminous for practical use. To better appreciate what constitutes unusual service conditions, consider their opposites. From that perspective, exposure should be to clean, dry (but not too dry) air with no mechanical or physical disturbances, e.g., conditions that would be expected for factory testing new motors.
As with exposure conditions, the list of unusual operating conditions in MG 1, 14.3 is not intended to be exhaustive or complete. Among the items it covers are: • Electrical supply voltage and frequency o Excessive departure from rated voltage or frequency, or both o The ac supply voltage more than 1% unbalanced • Operation at above rated speed (see Table 1) • Operation in a poorly ventilated room or a pit • Operation in an inclined position • Excessive mechanical forces o Repetitive abnormal overloads o Torsional impact o Frequent starting or reversing o Electric braking.
As with the list of usual conditions, each of these unusual conditions merits more discussion.
Electrical supply voltage and frequency.
Unusual service conditions exist if voltages exceed ±10% of motor rated voltage, frequency exceeds ±5% of rated (+3%/-5% per IEC 60034-1, 7.3), or both. Voltage unbalance greater than 1% among phases also is an unusual service condition.
Operation at above rated speed. This could be a concern for a motor powered by a variable frequency drive (VFD). Table 1 provides overspeed limits for induction motors.
Poor ventilation and pit operation. Poor ventilation resembles unusual exposure conditions already mentioned. Likewise, operation in a pit may lead to problems with dampness or possibly submergence.
Operation in an inclined position. Small and medium horizontal motors typically can operate in an inclined or even a vertical position, but those
orientations are classified as unusual service conditions. Changing the motor’s orientation could affect its lubricant pathways, preventing grease from reaching the bearings. On oil-lubricated motors, it could cause leaks.
Excessive mechanical forces. Excessive mechanical forces, such as overload and torsional impact, are obviously unusual service conditions because they can lead to premature shaft failure. Frequent starting or reversing also can result in excess mechanical load, as well as stator and rotor overheating due to the high ratio of starting to full-load current (typically from 5:1 to 8:1).
Similarly, electric braking can cause above-rated current during braking, and rapid heating if the braking power is still applied after the motor is at rest.
Final thoughts
Knowing the differences between usual and unusual motor service conditions may not be something you’ll use often. But this information will be invaluable when it’s time to choose a motor for a new application or to troubleshoot a problem or failure. PE
TABLE 1: Overspeed limits for induction motors
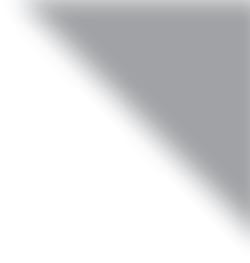
Synchronous speeds (rpm) Overspeed, percent of synchronous speed
Less than or equal to 200 hp (150 kW) Greater than 200 hp (150 kW)
1,801 and over
1,201 to 1,800
1,200 and below 25 20
25 25
50 25
Thomas H. Bishop, PE is a senior technical support specialist at EASA Inc., St. Louis. The Electrical Apparatus Service Association (EASA) is an international trade association of more than 1,800 firms in about 70 countries that sell and service electromechanical apparatus.
PRODUCTMART

OIL MIST & SMOKE IN YOUR SHOP?
www.mistcollectors.com Tel: 1-800-645-4174
Input #106 at plantengineering.hotims.com
Go online to view all Plant Engineering eBooks! Sponsor an eBook today!

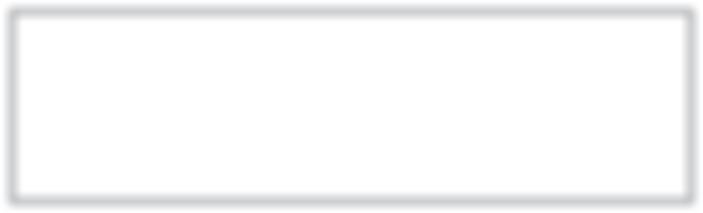
www.plantengineering.com/ebooks
Need Work Benches
In Stock-Factory Direct ?
workbenchmarket.com
Input #107 at plantengineering.hotims.com
www.mrshims.com
Belt/Sheave Laser Alignment System
New Green laser delivers these important benefits: ● Reduces Vibration ● Eliminates downtime and productions ● At an affordable price ● Visible indoors and Outdoors ● Brightness great for long distances
Mr. Shims
your answer to better alignment for rotating machinery
(1-800-727-4467) 1-800-72-SHIMS
Input #108 at plantengineering.hotims.com
SOLUTIONS
CASE STUDY
By Jim Sirois
Circuit breaker promotes automotive-plant energy ef ciency
Figure 1: Equipment for cold testing engines. Image courtesy: Siemens G reen technology is topic of interest in today’s automotive industry. At the forefront of these endeavors are innovations that focus on environmental issues through sustainable manufacturing practices. In addition, major automotive companies are looking for ways to reduce energy consumption.
To this end, DigiTek, a provider of innovative test solutions, proposed designing and implementing a new way of monitoring energy usage at one Midwest automotive plant. Specifically, the solution needed to provide integrated power monitoring, replacing separate current transformers.
It also had to communicate with a programmable logic controller (PLC) and human-machine interface (HMI) over a network and eliminate a potentially dangerous 480VAC electrical connection to a door-mounted monitor. This type of connection is typical in many existing power monitoring applications.
For this application example, we’ll explore how the Siemens 3VA6 circuit breaker fit the bill — reducing costs, promoting energy savings and improving worker safety at a 3-million-square-foot facility in Kokomo, IN.
Specialist in automotive testing
Based in Livonia, MI, DigiTek is a decade-old company that designs, engineers and delivers innovative test equipment for transmissions, engines and other powertrain products in the automotive and off-highway industries. The company’s solutions include a wide variety of production tests — everything from leak testing to electric vehicle (EV) battery testing, to full engine testing.
“We specialize in advanced propulsion testing systems,” said Tom James, who helped found DigiTek in 2010. “Our machines meet the automotive industry’s strictest standards of repeatability, and we’ve proven we can do this well.”
In fact, despite the company’s short history, it has already gained the attention of major automotive and off-highway companies like GM, Caterpillar, John Deere, Hyundai and many more. It has also expanded its services to five other countries — South Korea, China, India, Mexico and Italy.
“Although we’re relatively small and operate in a niche market, we’re unique in our ability to deliver high-end test equipment and engineering services at the level that we do,” James says. “We’re also actively pursuing markets that are trending toward electric vehicles.”
DigiTek’s SiEVT end-of-line (EOL) test machine, for example, currently tests front-wheel drive (FWD) hybrid transmissions. The company also routinely conducts EV battery tests, as well as electrical and advanced propulsion tests for electric motors, fuel cells and sensors. As green technology continues to rise in popularity — with global sales for EVs projected to cross 60 million vehicles by 2040 — these testing processes have become all the more important, making powertrain electric test systems indispensable to EV quality and safety.
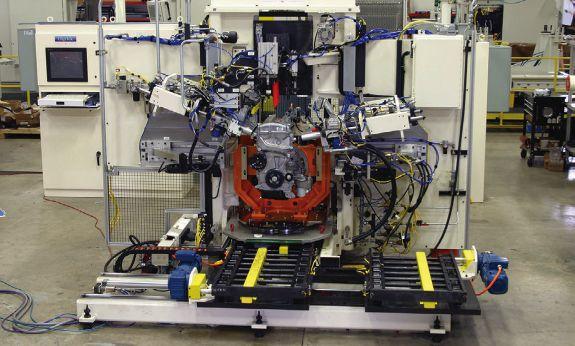
Cost-effective energy monitoring
With the automotive industry trending toward energy efficiency, DigiTek was recently tasked to provide a safe, cost-effective solution for monitoring energy consumption in the Kokomo plant. At the time, the automotive giant was using separate current transformers, which are often difficult to install and mount securely. In addition, a separate monitor screen, which was mounted on the door of the panel, required a 480-volt connection.
“Each time maintenance personnel wanted to inspect the panel, they had to open the door,” explains Jim Sirois,
vertical market development manager, control products at Siemens. “But having the 480-volt connection on the door was potentially dangerous. Over time, the wires could become loose — creating a potential hazard for operators and maintenance personnel.”
To come up with a solution, DigiTek consulted Siemens, whose products DigiTek was already familiar with and used in the Kokomo plant. “Siemens is accepted globally by our customers,” said James. “Many of our customers are large, global corporations and so they prefer global solutions.”
To meet the applications requirements, the SiemensDigiTek team selected the Siemens 3VA6 Circuit Breaker, which reliably protects circuits and starter combinations in industrial applications, infrastructure and buildings. Thanks to its integrated power monitoring method, it effectively replaced the separate current transformers in the panels. Able to communicate with PLCs and HMIs over a plant-wide network, the 3VA6 also includes open interfaces and standard protocols — PROFIBUS, PROFINET, Modbus TCP and Modbus RTU — for seamless integration into existing technical infrastructure and automation environments. As a result, it eliminated the need to bring 480 volts to a door-mounted monitor — or have a separate monitor at all.
For circuit protection
The 3VA6 is ideal for any machine that requires circuit protection. It has communications and power metering capabilities integrated into it — both of which break new ground for circuit breakers. “Typically, these were all separate systems,” Sirois said. “But now, you have a single unified piece of equipment that can communicate directly with plant personnel who need the information.”
In addition, the 3VA6 complies with UL, IEC, and CCC standards, enabling users to take advantage of its functionalities in Europe, North America and Asia. It is said to be the only circuit breaker on the market to offer pre-cut probe holes in its terminal shields. Other circuit breakers integrate shields that cover everything, making it difficult for electricians to check the voltage. In those cases, “To get the cover off, the electrician must first shut off the overhead bus plug — turning what should be a 30-second process into half an hour,” Sirois said. “Having precut voltage probe holes is a huge convenience for our customers, allowing them to quickly perform their safe electrical lockout procedures.”
Other notable features of the circuit breaker include: • Line protection from 40 to 1000 amps • Breaking capacity up to 200 kilo amps at 480 volts AC • Electronic trip unit • Three- or four-pole versions • Integrated measuring function for current, voltage and energy values • Communication via PROFIBUS, PROFINET, Ethernet IP, Ethernet (Modbus TCP), Modbus RTU • Wide range of internal accessories — auxiliary and alarm switches, shunt trips and many more — that are universal to the product line.
Improving safety and saving
The circuit breaker successfully lowered hardware and installation costs, improved safety and promoted energy savings in the Kokomo plant — all while providing a single point for configuration and monitoring.
Worker safety. The circuit breaker eliminated a potentially hazardous voltage connection to a panel door — improving the safety of operators and other personnel coming into regular contact with it. The device provides a single point for configuration and monitoring accessible via TIA Portal, Powerconfig configuration software, or directly using the circuit breaker keypad.
Time and energy savings. Configuration software facilitates commissioning and maintenance work,
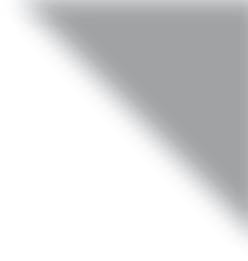
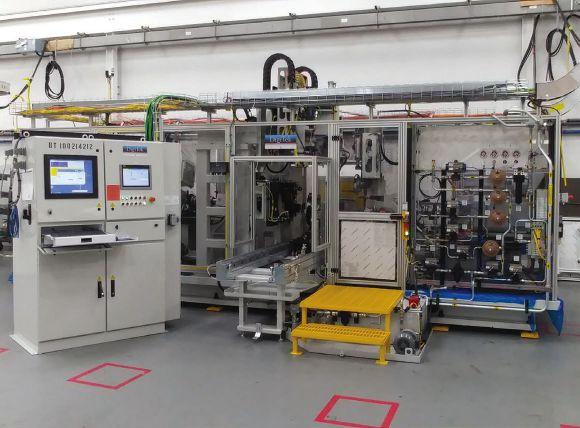
Figure 2: One of 25 final test stands for transmission testing. Image courtesy: Siemens
Figure 3: DigiTek shop floor, fully loaded with 12 machines. Image courtesy: Siemens
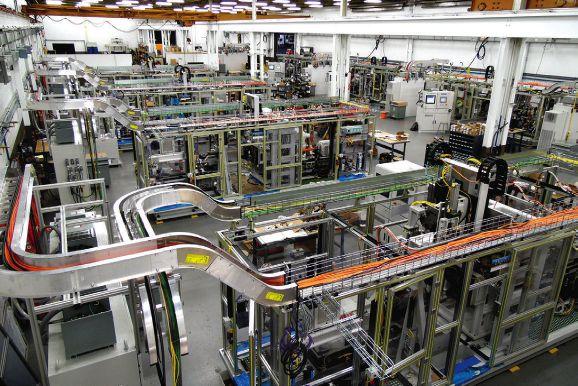
SOLUTIONS

CASE STUDY
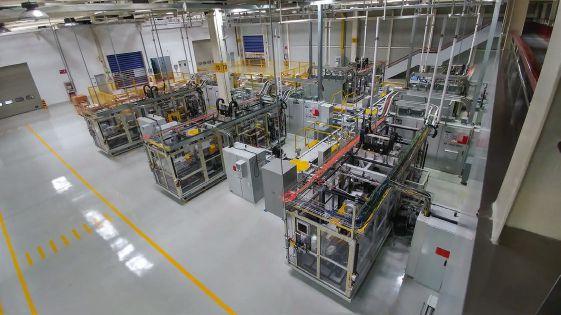
Figure 4: DigiTek system installation in Shanghai, China. Image courtesy: Siemens while power monitoring software manages and archives the acquired energy data for analysis. “Thanks to the 3VA6, personnel have a good idea of the plant’s energy consumption — shedding light on how they can lower their bills,” Sirois says. “Seeing how specific pieces of equipment consume energy also gives them a heads up about potential maintenance issues.”
Ease of use. Chuck Coak, DigiTek’s lead electrician for the Kokomo plant project, describes the circuit breaker as simple and straightforward to use. “When we first hooked the 3VA6 up, we had to configure it to the right voltage and current level,” Coak said. “There were no issues with this process; the software was easy to use and can be freely downloaded from the Siemens website.” Cost savings.By replacing the separate current transformers, the 3VA6 provided a clean, professional-looking installation that reduced the number of components — lowering hardware costs by as much as 17 percent.
Optimizing EV testing
DigiTek has big plans for the 3VA6 circuit breaker in its EOL test equipment. Whether a hybrid or automatic standard gear transmission, engineers can use the device to see if one motor demands more power than another. They can also use it to quantify internally regenerative transmissions, which tend to mask some power consumption. “Electric vehicles are becoming more popular, and we could use the data from the 3VA6 to optimize our electric testing process,” James says. “Better understanding the role of the motor in the powerchain is critical.” PE
Jim Sirois is vertical market development manager for control products at Siemens Smart Infrastructure USA.
Bedrock® Open Secure Automation White Paper Series - Chapter 2 Empowering Power
Albert Rooyakkers | Founder, CEO & CTO
Automation system power supplies are finally getting the recognition they deserve. Whether on backplanes, standing alone or providing back-up, power supplies have traditionally been viewed as commodities. But today, as businesses are interconnecting more devices carrying higher volumes of strategic data, power supplies are coming into their own as key enablers of digital transformation. If random power transients, inclement weather, cyberattack, or other forces disrupt the power, all data can be lost. Moreover, disruptions in process continuity can cost companies millions with connected equipment in jeopardy.
To leverage the amount of performance and diagnostic data that is increasingly open to them, today’s power supplies must be smart and connected, with greater storage and processing power than their predecessors. To safely realize the cost and performance benefits available to them through interaction with other applications, the cloud and public networks, power supplies must embed cyber security. And, as more companies deploy automation in remote sites, power supplies must be able to withstand vibration, humidity, contaminants, extreme temperatures and other stresses — even electromagnetic pulse (EMP).
Read this white paper to learn how to prevent your automation system power supplies from short-circuiting your digital transformation. Register to download here: https://cfe.dragonforms.com/PE_WP_OSA
The Importance of a Proper Lubrication Program
David Reh | Director of field engineering and training services, Lubriplate Lubricants Company
Proper lubrication is essential to maintaining the bottom line, but starting a lubrication plan can seem to be an overwhelming proposition. Not having an effective program can result in hundreds of hours of downtime and lost production. Where does one begin faced with such a daunting task? This article will discuss methods to implement a comprehensive lubrication program, or how to possibly improve one already in place.
The first thing that should be done is to define the program’s goals and objectives. Many plants want to consolidate inventory, reduce costs, and to ensure that the correct products are being used in the right places, especially in regard to any applicable legislation or food grade lubrication requirements. A qualified lubrication expert can assist with each of these goals, and advise you on what may or may not be a practical plan based on their experience.
Even a seemingly small accomplishment can be crucial. Some examples might include consolidating multiple gear oils into a single one, inventory reduction, or identifying an opportunity to save money through the advantages of using a superior lubricant. A few successes like these along the way help to keep the ball rolling.
Implementing a color‐coding plan, tagging equipment, and employee training are also smaller sized goals that can be accomplished fairly quickly with a moderate effort and reap much larger benefits in the long term. Another example of this is oil analysis. Oil analysis can be a good place to start, because it can be started on critical equipment without a lot of effort, and carries with it a potentially large return on the initial investment.
With each small part of the project that is completed, employees become more invested in the continuance of the program as it builds towards the conclusion a comprehensive lubrication program that saves money in the long run.
Lubriplate provides it’s customers with a complete extra services package. These services include a technical support hotline and e-mail, complete plant surveys, customized, color coded lubricant tags, lubrication maintenance software, plant user training and no charge oil, fluid and grease analysis. For more on this subject and customer assistance call 1-800-733-4755 or e-mail LubeXpert@lubriplate.com
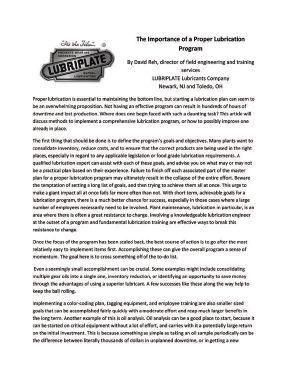

www.lubriplate.com
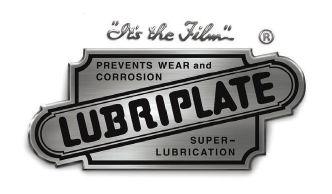
Download the paper at: www.lubriplate.com/Resources/White-Papers/