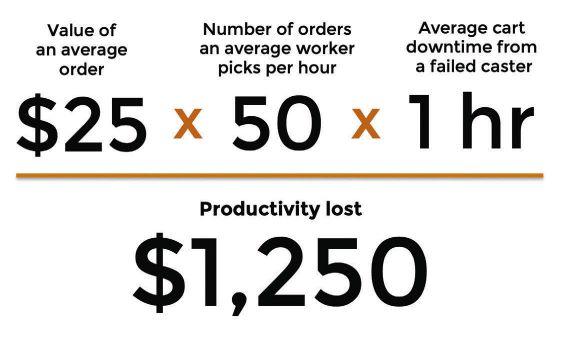
8 minute read
Seven shortcomings of commodity casters
SOLUTIONS
MATERIAL HANDLING
Advertisement
By Eric Hassen
Seven shortcomings of commodity casters
The right application-speci c casters and wheels can help optimize work ow
“I f it ain’t broke, don’t fix it.” But if it is broke, don’t keep replacing it with the same inferior part. That logic applies to “commodity casters,” the wheel systems on the undersides of the material handling carts and platform trucks plant floor associates use every day. Original equipment manufacturer (OEM) cart manufacturers often specify inferior-quality casters and wheels that aren’t built to last so they can keep purchasing costs down for end users.
Too often these commodity casters quickly show signs of wear, if not completely fall into disrepair, within six to 12 months of service. This, in turn, can result in issues like unplanned downtime, excessive noise and even workplace injuries (see Figure 1).
In manufacturing and distribution center environments, more forethought is warranted about the wheels and casters on carts. To specify the right casters, it’s prudent to consider factors like load requirements: how far, at what speed and for how long the cart will be moved; flooring surfaces; and more. There are many things to consider rather than just making a go at it with the default caster and wheel that comes with the cart.
Commodity casters aren’t designed to address specific applications, whereas advances in application-specific casters and wheels can provide custom solutions to match precisely how they’ll be used on the floor.
There are several inherent shortcomings in OEM casters that can lead to tangible, measurable issues in a plant’s operations. The following is a breakdown of the top seven:
1. Reliability
Many OEM carts have poor quality casters that fail prematurely. Most commodity casters use a standard kingpin design, the most common point of failure in a caster. The kingpin will likely stretch out over time, causing the housing to come loose, bearings to fall out and push-pull actions to require more effort. Failed casters directly result in lost productivity when carts and trucks are taken out of commission.
2. Ergonomics
Casters with a high rolling resistance cause physical overexertion by associates, the primary cause of workplace injuries. If it takes more effort to push or pull, it increases the chance for injury. The U.S. National Safety Council pins the average insurance claim per workplace incident at $60,000 to $80,000.
Lower back strain caused from pushing and pulling carts is a leading workers’ compensation claim in the United States. It happens regularly due to repetitive motion and overexertion from associates. These behaviors account for nearly 20% of injuries and illnesses in the workplace. Only the common cold accounts for more lost days at work.
Commodity casters typically have standard swivel leads, which are harder to push, pull and maneuver. A standard swivel lead has a short distance roughly straight up and down from the center point of the kingpin to the center point of the
Figure 1: Typical cost of unplanned downtime. Courtesy: Caster Connection
Figure 2: Application-specific casters can come with an extended swivel lead. Courtesy: Caster Connection
axle. Application-specific casters can come with an extended swivel lead (see Figure 2). This added distance enables reduced push-pull forces, improved maneuverability and decreased noise and chatter.
3. Safety
The wrong wheel built for the wrong operation can cause a failure that compromises the load being carried and, in turn, the operator pushing or pulling it. Figure 3 shows what happens when the wrong wheel was used in a tugging operation. This is a polyurethane on aluminum wheel that has de-bonded. That means it was spinning too fast and created heat from the bearing that worked its way up to the core. It got so hot the glue that holds the polyurethane onto the core melted and caused the tread to fall off. If a cart is taking a 90-degree turn with a full load and the caster fails, it’s likely to cause a severe injury to the operator and any associates standing nearby.
4. Versatility
Commodity casters are inherently not versatile. By design, they’re one size fits none. There’s no factoring in of any operation-specific dynamics that
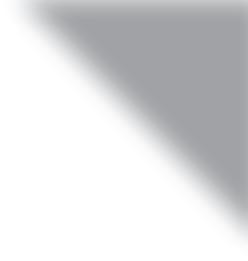
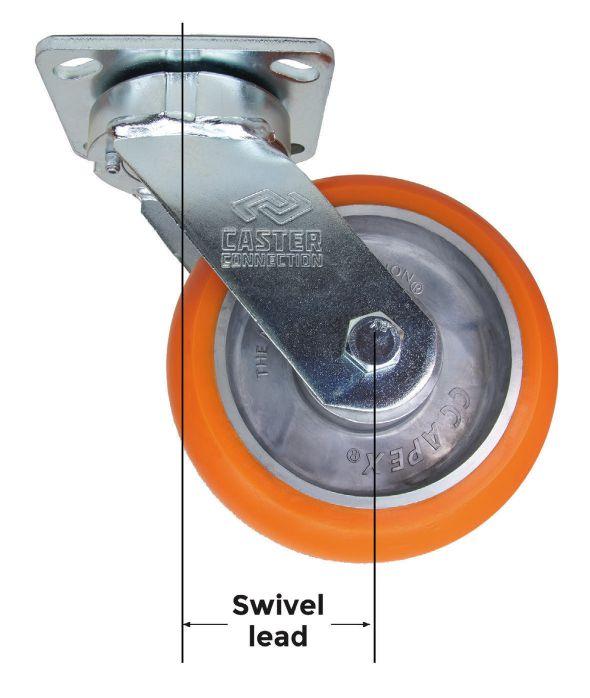
Ford Motors case study
Ford Motor Company’s issues with casters centered on durability, or lack thereof. The parts on its casters were failing at a high rate, around the six-month period. This is fast for a caster.
Second, the plant was experiencing a high volume of push-pull issues with its carts. Associates were having a hard time and incurred an injury. Ford wanted to make sure any caster solution would lower the push-pull force on a fully loaded cart and help prevent injury.
Third, caster-related noise in the facility was an issue. Ford uses power tuggers that pull three or four carts in a row, and those tuggers were making a lot of noise due to chatter and flutter associated with the casters.
Caster Connection sent an individual onsite to assess the applications being run at the plant, the carts being used and the casters. The recommended solution resolved all three issues.
First, a proper swivel caster with the proper raceway was specified to eliminate the durability issue. Next, proper wheels and bearings were used to help reduce push-pull forces by 35%, and without having to change Ford’s internal processes. Finally, for the noise issue, proper wheel tread was specified to essentially add a built-in shock absorber to reduce the noise by roughly 16%.
Using the proper caster for specific applications can have a dramatic effect. Noise, push-pull and bottom-line return on investment (ROI) were improved in this instance, and a commodity caster that used to last six months was replaced by one that was now lasting more than three years.
SOLUTIONS

MATERIAL HANDLING

would improve productivity or durability of the part. The correct casters for the application, on the other hand, can solve more than one problem for an operation. And properly specified, they can be versatile enough to improve operations at multiple facilities and on multiple types of carts and trucks, keeping part number ordering and inventory at a minimum. The right caster can be standardized across an entire corporate network.
5. Maintenance
Plant and distribution center maintenance teams likely are kept busy doing many higher priority tasks than changing, greasing and running maintenance on casters. Commodity casters typically have open raceways with constant need for greasing, which takes valuable time. The right application-specific caster can minimize a plant’s maintenance, repair and overhaul (MRO) expense.
Purchasing teams often reorder the same part because that’s what is known and familiar. The more they’re aware of other options and how they can impact operational safety, productivity and the bottom line, those options become more likely to be chosen in the future. When casters break, and they commonly do, they need to be replaced with the correct caster for a plant’s specific operation.
6. Floors
Caster wheels made from phenolic and other inappropriately hard materials collect debris that imbed into the wheel’s tread. Debris retention can damage floors. Further, the wrong caster tread for the application can wear a groove in the floor, causing an automated guided vehicle (AGV), if used, to go offline and interrupt production.
OEM casters typically use inexpensive tread materials, and often they’re rather hard. Phenolic, glass-filled nylon and polyolefin are common examples. When there are multiple carts with hard treads on their wheels that consistently traverse over debris and in the same pattern, they’ll wear grooves into the floor. They’ll also travel over thresholds, elevators, dock plates and even extension cords. Hard casters often don’t do very well when they encounter gaps or bumps. The smaller the wheel, the more difficult it can be. They’ll get stuck and cause operators to overexert themselves to move the cart. Properly specified casters and wheels, conversely, can be softer, larger and more forgiving on gaps or raises in the floor.
7. Noise
The wrong wheel and caster combination can cause an aggravating amount of noise. Consider having a tugging application that uses a standard lead swivel caster. That’s a short distance between the center point of the kingpin and center point of the axle, and when the caster gets moving as fast as 5 mph, it can start chattering and fluttering back and forth because it doesn’t have any room to trail. This can cause a tremendous amount of noise, particularly when carts are unloaded and there is nothing to keep those casters on the ground. A loose raceway can cause loud noise as well. The wrong material can create excessive noise because there’s no resiliency to the tread.
Considering multiple variables, a caster made with specific polyurethane or rubber wheels can be softer and significantly reduce the amount of noise.
Final thoughts
Manufacturers and distribution centers don’t have to live with commodity casters. Awareness of the specific shortcomings inherent in commodity casters and knowledge about what application-specific alternatives are available and how they can improve operations are key to making the best purchasing decisions. PE
Figure 3: The photo shows what happens when the wrong wheel is used in a tugging operation. This is a polyurethane-on-aluminum wheel that has de-bonded. Courtesy: Caster Connection
Eric Hassen is director of business development for Caster Connection, a manufacturer and distributor of high-performance casters, wheels and other material handling products based in Columbus, Ohio.