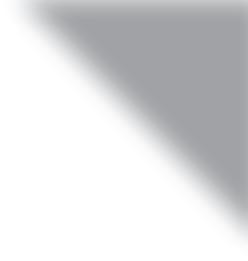
15 minute read
Install medium voltage cables in petrochemical plants
SOLUTIONS
ELECTRICAL DISTRIBUTION
Advertisement
By Garrett Nariman, PE
How to ensure code requirements for hazardous environments are satis ed
Figure 1: When it comes to operating mediumvoltage equipment, petrochemical facilities come with many unique challenges. Courtesy: Samuel Engineering M edium voltage (MV) equipment is commonly encountered in today’s petrochemical facilities. Electric motors operating at 2.3 kV to 15 kV are often deployed for larger horsepower equipment such as compressors and pumps.
Petrochemical facilities come with many unique challenges (see Figure 1). Principal among these is the presence, or possible presence, of flammable concentrations of gas in the atmosphere, or release of flammable liquids due to equipment failure.
Electrical systems installed in these demanding and hazardous environments must satisfy the requirements of NFPA 70-2020: National Electrical Code (NEC).
Specific requirements for MV wiring methods are often grouped at the end of relevant NEC articles. These MV requirements can either amend, or completely supersede the low voltage requirements. The design process can often require one to completely understand both the low voltage and the MV sections. Add the requirements for classified areas into this mix, and it is easy to see where confusion may set in. This article explains some of the more common aspects of MV cable installations in hazardous environments and how to ensure code requirements will be satisfied.
Conductor sizing
A typical MV motor feeder circuit often originates at a motor control center starter cubicle or a switchgear circuit breaker compartment. These are typically located in a non-hazardous location remote from the motor. From the source, one or possibly more MV cables are usually routed in cable tray to the load (see Figure 2). Because of the thickness of MV cable insulation and required bending radius due to the metallic tape shield, cable tray is most often preferred over conduit for MV applications (see Figure 3).
The conductors must be sized in compliance with NEC Articles 430 and 311 with necessary adjustments for cable tray fill and spacing per Article 392. Note that according to Article 430, MV motor conductors are not sized based on motor full load amps (FLA) as is done for low voltage motors, but instead selected based on the motor overload protection setting. Additionally, the grounding requirements for MV circuits are grouped at the end of Article 250. These requirements supplement and modify the previous sections of this long article. Note that cable selection based on ampacity requirements must be done according to the requirements of Article 311 factoring in derating for ambient temperature and mutual heating effects encountered in grouped underground installations rather than relying solely on manufacturers data sheet values.
Classified area considerations
Once the cables and cable tray are properly sized for the load served, requirements for the portion of the circuit that lies within the classified area must be considered. For this discussion, assume this scenario consists of the cable and tray going out to the load and the cable terminations at the load. The discussion s focused ion Class 1 Division 2 (C1D2) Group D environments, which are
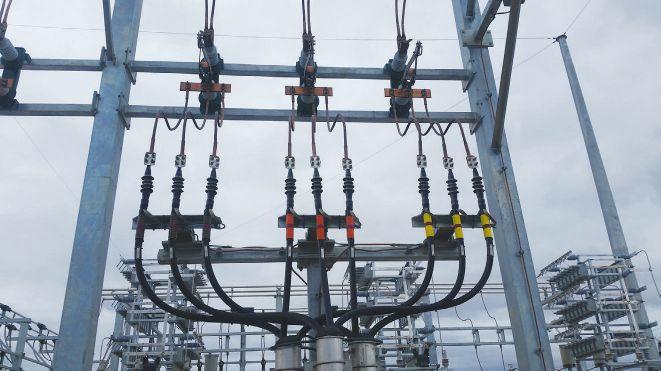
SOLUTIONS
ELECTRICAL DISTRIBUTION
Figure 2: Medium and low voltage cable trays leaving an electrical substation routed on pipe supports to individual loads. Courtesy: Samuel Engineering common in petrochemical facilities. It will also touch on the differences between Division 2 and Division 1 installations. The requirements for electrical installations in hazardous areas are specified in NEC Articles 500 and 501 for North America, or alternately Article 505. Before the circuit design is approached, the classification, division, group and extents of the hazardous area must be evaluated. As required by NEC Article 500.4, this information is documented on area classification plans, details and often elevation drawings. The authority having jurisdiction (AHJ) will need this information to verify the adequacy of the electrical design.
With this background information in hand, the MV circuit design and material specifications can proceed. One question that is commonly asked at this point is “do I need a special MV cable type for classified areas?”
This is one of those areas where confusion often arises. In MV applications, “Type MV” cable is normally selected. The use, installation and construction of Type MV cable is detailed in NEC Article 311. However, if one looks in section 311.32, “Uses Permitted,” no mention of classified areas is found. However, below this list is an informational note stating the “Uses Permitted” is not an all-inclusive list.
One should search through Article 501 and read section 501.10 “Wiring Methods” to see that Type MV cable installed in cable tray with approved termination fittings is approved for C1-D2 locations. If your installation is in a Division 1 location, you may likely specify Type MC-HL cable. Furthermore, this cable is allowed only for industrial facilities with limited access and full-time qualified maintenance onsite. The “HL” stands for hazardous location. The “MC” stands for metal clad, so you will need to specify the correct fittings to properly terminate the cable armor. This is typically a cable gland. Your C1-D2 cable specification should specifically state “Type MV” and include language requiring that the cable be approved for cable tray use and is sunlight resistant. Although these are fairly standard among manufacturers, having this stated up-front protects the end user from costly rework. Also the cable temperature rating should be specified. Usually this is either the 90 C rated MV-90, or the 105 C rated MV-105 type. The 105 C rating is usually selected to allow for better short-term overload performance and ability to withstand downstream short circuits in feeder applications. Unlike single conductor cables, 3 conductor type MV cables are usually also approved for direct burial.
Cable terminations and sealing
Once a cable is selected and sized, consider cable terminations at the load end. Assume this is designated as a C1-D2 location. Cable termination selection is a complex subject. The termination will be selected according to cable and conductor type, voltage level, indoor versus outdoor, load terminals, among other things.
The size of the enclosure at the motor and whether current transformers (CTs) are required should be determined. Smaller motors often have terminal boxes that are quite confined. Another issue to be considered is most motor terminal boxes are set up for bottom cable entry and often cannot be rotated as with low-voltage motors. Be mindful of cable bend radius requirements found in NEC Article 300.34 (see Figure 4).
Applying the cable, conduit and boundary sealing requirements of NEC Article 501.15 in hazardous areas for MV equipment often causes confusion as well. The text of the NEC does not make this task easier. NEC Article 501.15 is overdue for a rewrite and better explanatory notes. However, it is important to know that the sealing requirements
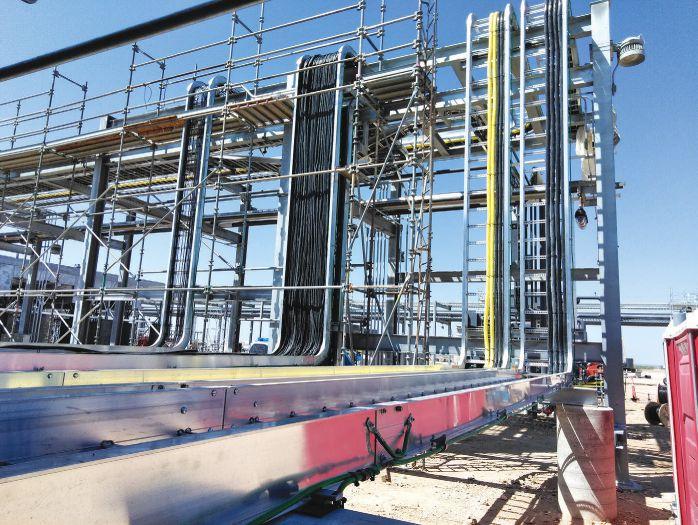
are the same for MV cables and the more commonly applied low-voltage cables in petrochemical plants. In fact, the requirements of NEC Articles 500 and 501 apply equally to both medium- and low-voltage wiring methods. Unlike other articles in the NEC, there is not a separate section created for MV levels to amend low-voltage requirements.
How compliance with NEC Article 501.15 is achieved depends on several variables. Again, for this discussion, assume C1-D2 areas commonly encountered in petrochemical plants. In the case of a typical 3-conductor plus ground Type MV or MC-HL cable with polyvinyl chloride (PVC) jacket, consider first the NEC requirement for boundary seals at the transition from the non-classified to the classified area.
Typically, in petrochemical plants the MV or MC-HL cable will be run in a ladder type cable tray, so the requirements for conduit seals at the boundary do not apply as one would expect. However, be aware that the cable itself may transmit gas across the boundary. That consideration is addressed by NEC Article 501.15 (E)(4), which requires a seal at the boundary for “Cables Without a Gas/Vaportight Sheath.” This wording is one of the areas that causes much confusion. Some questions may arise here such as: “How do I know if my cable has this?” and, “The manufacturer’s data sheet for my cable only refers to a “jacket,” is this the same as the sheath mentioned in this section?”
Unfortunately, the various entities — Underwriters Laboratory (UL), National Electrical Manufacturers Association (NEMA) and the NEC often do not use the same terminology, making things even more confusing. In NEMA/UL terminology, if you have an un-armored Type MV cable, the “jacket” is the outer covering of PVC or similar material that holds the conductors together and provides protection for the contained MV insulated conductors. It can be considered the same as the “sheath” referred to in NEC terminology.
On the other hand, manufacturer’s data sheets for an MC-HL three conductor cable will commonly refer to a continuously welded corrugated aluminum armor as the sheath, while the thin PVC covering over the armor is the jacket. This type of cable can additionally be used in a Class 1 Division 1 location. Be aware that you can also get interlocked armor type MC cables that are not rated for Division 1 environments.
Returning to the original question on boundary seals for multiconductor cables per NEC Article 501.15(E)(4), in the case of non-armored Type MV cables, UL does not require testing to assure the jacket is truly gas/vapor tight. And for the most part, cable manufacturers will not state that the jacket performs as such. However, most MV cable manufacturers point out that the chances of holes forming all the way through the jacket due to manufacturing irregularities are very small.
Most manufacturers test the jacket to comply with UL thickness requirements and for defects during manufacturing, but this will generally not detect small pinholes that could allow gas to enter. This possibility should rarely be a concern as it would take holes in the jacket inside the classified area that allow gas to enter in flammable concentrations, and enough pressure differential through the cable core to drive the gas to the termination in the nonhazardous area, such as a switchgear lineup.
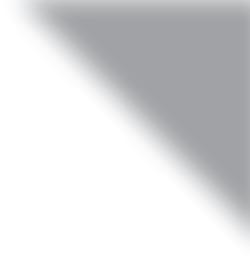
Figure 3: Medium-voltage cables pulled to pump motors via cable tray. Cable trays generally facilitate the larger MV cable bending requirements, save labor and facilitate future expansion. Courtesy: Samuel Engineering
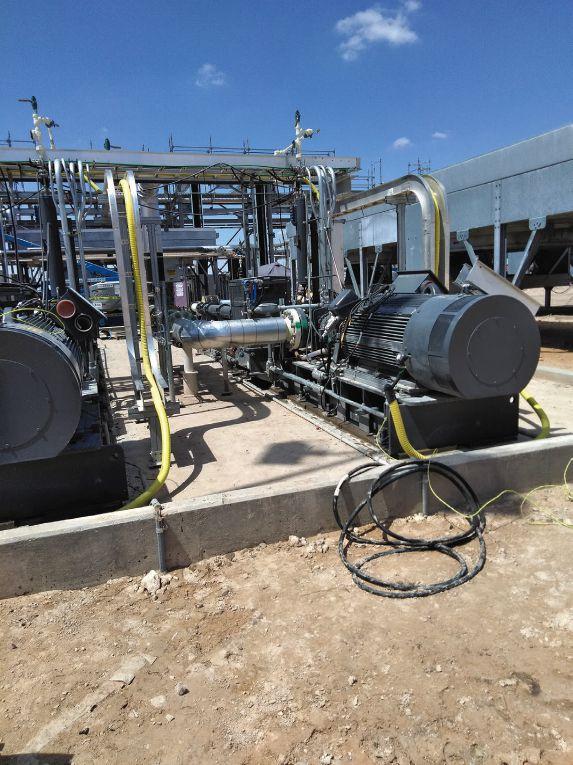
SOLUTIONS
ELECTRICAL DISTRIBUTION
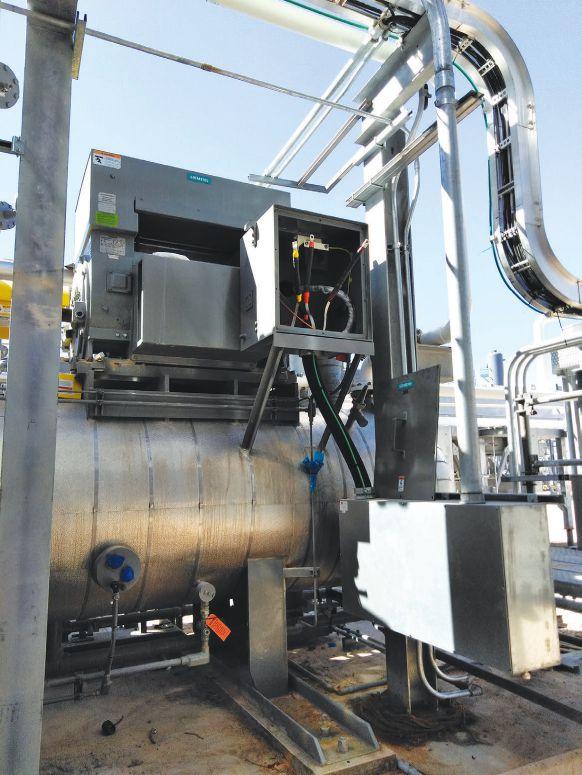
Figure 4: Terminations installed on a medium-voltage cable inside a motor terminal box. MV motor terminal boxes need extra space to properly terminate and land the conductors. Courtesy: Samuel Engineering
The AHJ will need to be on board with this reasoning. If there is any concern for an application, an MC-HL cable may be a better choice for compliance with this requirement. The continuously corrugated sheath is typically pressure tested by manufacturers and allows them to state that the cable is impervious to gas/vapor entry. However, the manufacturer’s data sheets for the cable should be reviewed to confirm this level of performance. Within the confines of the hazardous area, one needs to be mindful of the NEC cable sealing requirements at the terminations. As with requirements for cable boundary seals, the language of the code can be confusing here as well. Consider a typical scenario of a 3-conductor plus ground Type MV cable run in a tray system terminating at a motor in a C1-D2 area.
The cable sealing requirements are spelled out in NEC Article 501.14(E)(1) through 501.14(E)(4). As stated previously, even though the NEC refers to “cables that do not transmit gasses or vapors through the core,” it also notes that the interstices of conductor strands are not considered part of the cable core and may transmit gas. Compact stranding may minimize this but the potential to transmit gas through the strands in sufficient quantity to create an explosion hazard may exist.
At this point, applying cable seals to minimize passage of gas through the cable core aside from the strand interstices should be discussed. Again, there is a disconnect between typical manufacturers’ data sheets and NEC language. This section of the code is not easy to follow and is often not addressed clearly in manufacturers’ data sheets, so compliance may hinge on interpretation by the AHJ. Much this will amount to whether the AHJ considers the cable sheath as gas/vapor tight, and the cable core as capable or not of transmitting gas.
Typical MV cable data sheets will not state performance of cables with respect to these two modes of potential gas transmission. In a practical sense, this prevents NEC Article 501.14(E)(2) and 501.14(E) (3) from being applicable to Type MV cable design in C1-D2 areas unless mandated by the AHJ.
Now consider NEC Article 501.14(E)(1), which requires a sealing fitting to be installed at conduit/ cable entries when the termination takes place inside of an enclosure required to be explosion proof. Most motor terminal boxes for C1-D2 rated motors are not explosion proof. The last part of this section also creates some confusion. It can be interpreted to require cable seals for essentially all multiconductor Type MV cables regardless of the enclosure rating.
Again, if possible, it is advisable to have a conversation with your AHJ to get an interpretation of this requirement as the writing of the Code leads to various opinions on this subject. This may even include no cable seal for cables longer than several hundred feet. Due to the cable run length and fillers in the cable core, some AHJs consider the cable to inherently minimize the passage of gas back to the non-classified area.
If it is deemed by the AHJ that passage of gas through the cable from the C1-D2 area must be addressed, the options available depend on what type of cable is being used. The objective is to minimize the passage of gas through the cable core.
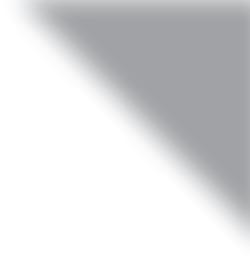
Hot or cold shrink termination kits on the individual phase conductors are installed to evenly distribute electrical stress and protect the exposed conductor insulation. These often can be ordered with a “breakout boot” to seal the cable assembly. While in practice, these may restrict the passage of gas through conductor core and interstices to some degree, manufacturers generally do not test or label their performance in hazardous area applications.
If there is any concern about passage through strand interstices, it is advisable to specify compact stranding on the MV cables. To minimize passage of gas through the cable core if you are using an MC-HL cable, it is probably easiest to select a cable gland fitting listed for MC-HL cable that is sold with a compound applied inside the gland (see Figure 5). The purpose of the compound is to provide an explosion-proof seal similar to the commonly used conduit seals. But whether your terminal enclosure is explosion proof or not, the gland also serves to minimize the passage of gas through the cable core.
If you are using a type MV cable, it gets a little more complicated. If you want to use a cable gland with an MV type cable, you will need to verify the gland is approved for this type of cable. Many are not. The other option is an explosion-proof conduit seal placed at the cable breakout. However, this approach is often challenging as well.
Installation of a conduit sealing fitting on larger size conduits is often difficult, particularly in the congested area around the motor terminal box. Removing the cable jacket and fillers at the seal fitting exposes the shields and insulation to possible damage. More so than low voltage tray cable, even minor damage to MV cable construction can lead to premature failure. It is probably best to have a discussion with the AHJ before this route is taken so that an acceptable strategy to minimize the potential for gas transmission can be established.
Acceptance testing
This leads to the final topic to be discussed: acceptance testing after installation. Most petrochemical plants typically require acceptance testing of MV cables before energization. Some also call for periodic maintenance testing. Usually, this is by means of high potential dc testing, or dc Hi-Pot. This topic is one with a wide variety of opinions and recommendations associated with it and the reader is encouraged to research the wealth of technical papers available and recommendations of cable manufacturers.
Generally, acceptance tests should be conducted in accordance with IEEE 576: IEEE Recommended Practice for Installation, Termination and Testing of Insulated Power Cable as Used in Industrial and Commercial Applications using the recommended voltage level for the cable insulation rating. This is typically considered a “go, no-go” test in that the actual test current leakage values are of less importance than the plotted curve shape with respect to the test time. The leakage values during the test should initially start out relatively high and fall to a stable value for the remainder of the test period, typically 15 minutes. Note that this type of testing is influenced by humidity, moisture in raceways and temperature. These conditions are difficult to control, and the test results should be reviewed by a person with experience in interpreting the results.
Final thoughts
Designing and installing MV cables in petrochemical facilities presents a number of challenges and requires a holistic approach to the entire installation. Specifically, a comprehensive design approach is warranted that includes an understanding of the MV cable construction, an understanding of the terminations, physical limitations of the load equipment and involvement of the AHJ to sort through the relevant NEC requirements. PE
Figure 5: MC-HL cable with gland installed at a medium-voltage motor terminal box. Courtesy: Samuel Engineering
Garrett Nariman, PE is a senior electrical engineer at Samuel Engineering.
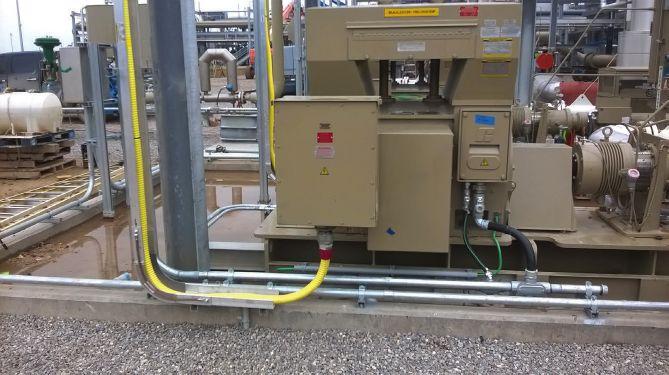