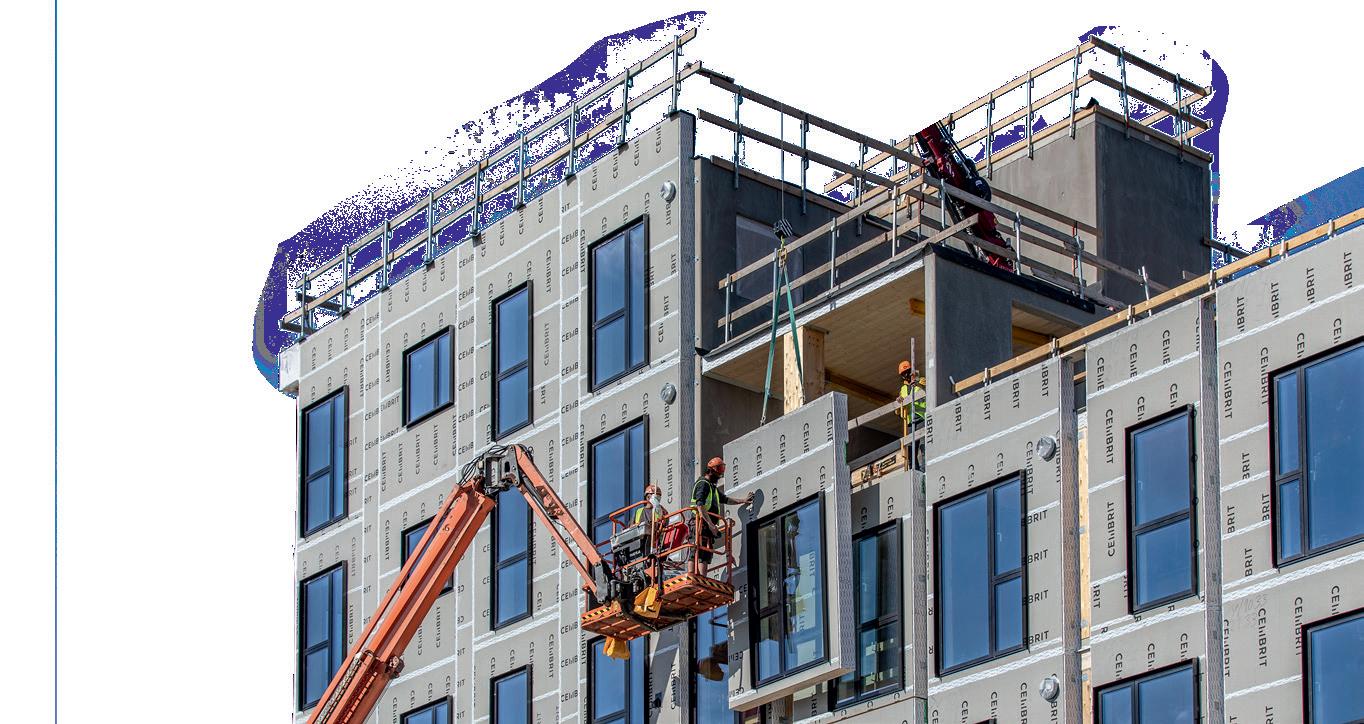
3 minute read
Award-winning BIM design of multiple timber façade cassettes
When designing a number of different façade cassettes for the 35,000 m2 large UN17 Village, we automatically mass-produced 3D models and working drawings that could be put directly into production. An efficient method that automatically combines various programmes made it possible and helped us win a Tekla BIM Award.
The housing construction UN17 Village is in many ways an enquiring project that examines different ways to comply with the UN’s Sustainable Development Goals. The residents' health is paramount, and as one of the sustainability aspects, the project contains the so far tallest timber construction in Denmark. In that spirit, it was also relevant to work innovatively with digital design, and it made sense to put the efforts in the many timber cassettes that constitute the substance of the buildings’ façades. A varied architectonic expression and the static details mean that there is a great deal of different cassettes which makes it very time-consuming to model manually. Automation was therefore in high demand, and that is exactly what we introduced.
Advertisement
The combination of Tekla, parametric design and openBIM made it possible to autogenerate 3D models of the many different timber cassettes with working drawings that could be handed over directly to the cassette manufacturer. The underlying technique was based on a good method to extract and combine large amounts of data from our own Tekla model, the architect’s Revit model and from the window manufacturer.
The efficient work procedures and the good cooperation between the parties were the reasons why we in 2022 won a regional Tekla BIM Award that covers constructions in Denmark and Norway. Every year, the award is granted to a project that transforms the way we build and helps develop the construction industry.

Concept development
The first step in the process was to develop a general structural concept for the cassettes which was achieved through an iterative process with the contractor CG Jensen. To reduce the amount of waste, the elements were designed to match the lengths of timber available from the supplier to the extent possible. Furthermore, the design team found a way to avoid the use of laminated timber which resulted in a considerable CO₂ reduction and a cost reduction.
When the general design concept was in place, a small number of Tekla components were developed to prepare for parametric modelling and control of all the cassettes via Grasshopper-Tekla Live Link.
Automatic data flow
The next challenge was that the cassettes have many variations and different attributes which means a host of data distributed between several sources. The engineering work was made in Tekla, but the architect used Revit for their design which contains information on placement and size of windows and doors. In addition, the window manufacturer held a lot of data, while the contractor had to deliver information on production flow and installation plans.
We wanted to combine all this data in the tool Rhino Grasshopper for parametric design of the cassettes. We therefore started by developing a data structure for what information to integrate and how. The link in the data structure and the relation between the models were created by comparing the three-dimensional locations of all elements.
Thanks to Grasshopper-Tekla Live Link and Revit plugins, data were easily integrated in Rhino Grasshopper along with the other information from the window manufacturer and the contractor. Afterwards, Rhino Grasshopper could automatically feed data to the Tekla component which was customised as a kind of template for the numerous types of cassettes. From the Tekla component, the many different cassettes were distributed to the actual Tekla model that could generate working drawings to the manufacturer. The drawings could be used directly due to a very high Level Of Detail of 450 LOD.
Building techniques of the future
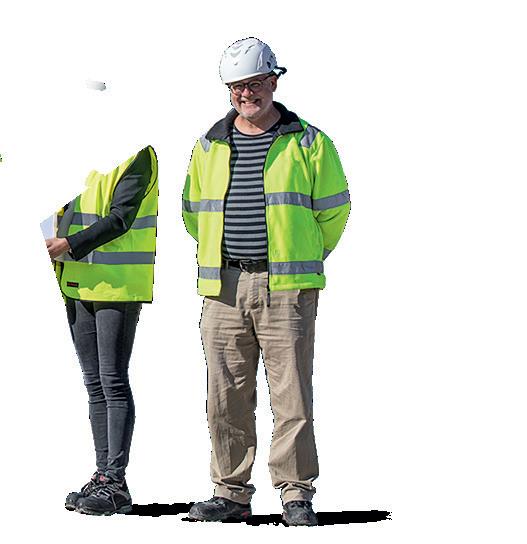
The combination of Tekla Structures, parametric design and openBIM really proved its worth in this project. Even though the trinity was already known for solving challenges in advanced structures, this project illustrates that the value of the efficient automation process can be as significant as for less challenging building structures. Especially when the end product is drawings that are ready for production.
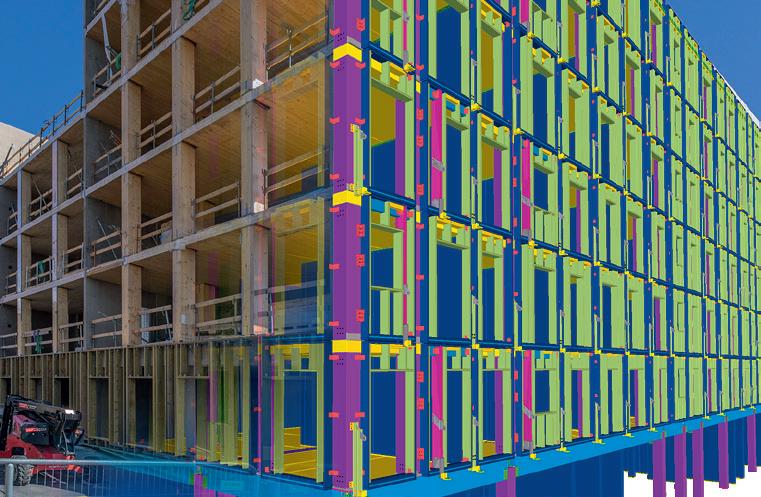
When innovation does not seem to be decisive to finish the project, the construction industry sometimes has a tendency to stick to traditional procedures, but the results of this project show great potential for automated work procedures even though it requires a bit more preparatory work. We are therefore pleased that our BIM specialists and other experts made an extra effort and even were honoured with an award.
