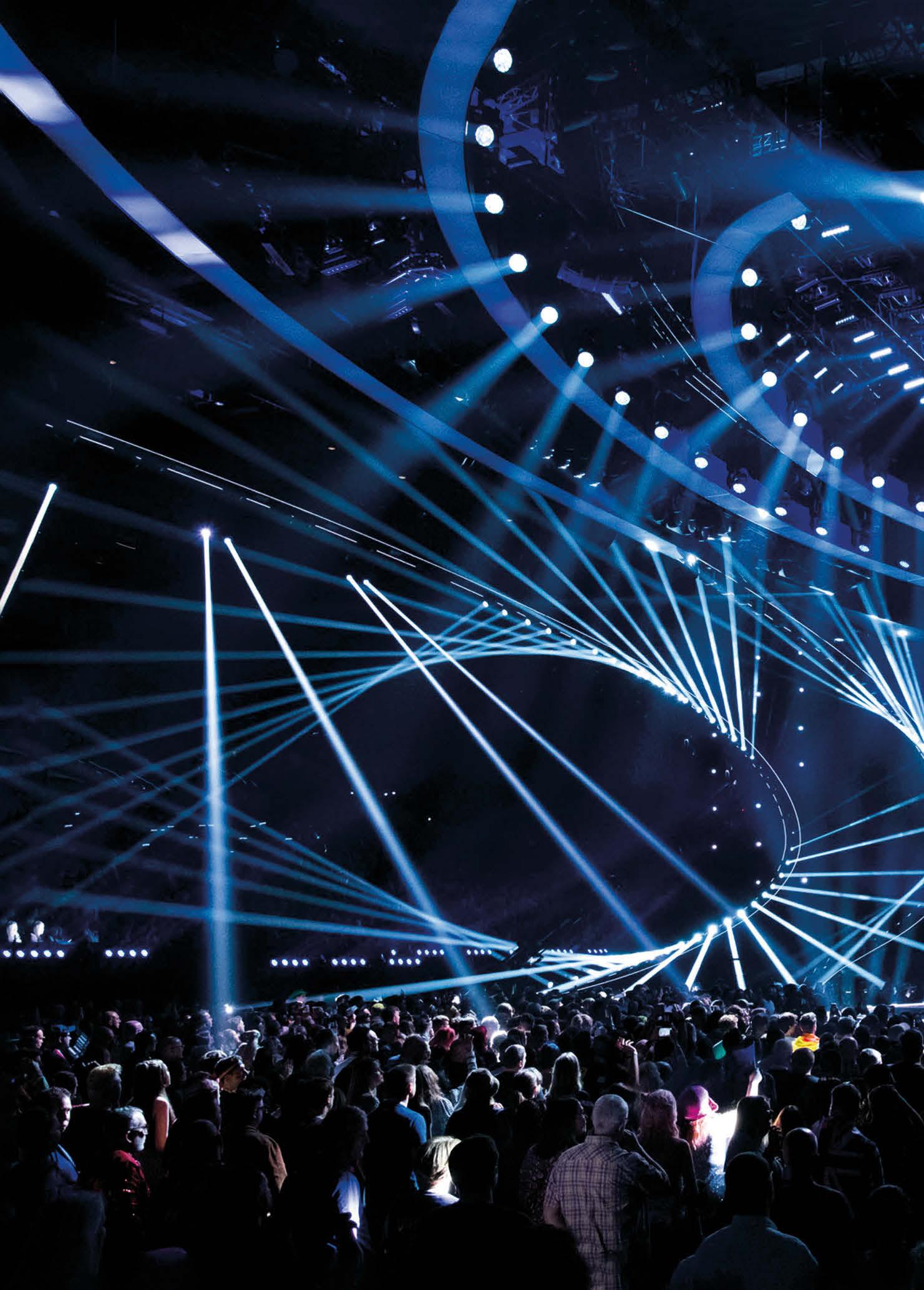
19 minute read
UNITED BY MUSIC (AND TECHNOLOGY): EUROVISION SONG CONTEST
Live entertainment specialists unite on the banks of the river Mersey to create the most watched and technically impressive music competition of all time on behalf of Ukraine…

With 160 million viewers and thousands on site, the prowess of the live entertainment industry was thrust into the spotlight in May, as the UK hosted the Eurovision Song Contest 2023 on behalf of Ukraine, welcoming 37 delegations to the biggest music competition in the world. Behind the scenes, collaboration among some of the best technical suppliers and minds the sector has to offer was key to the success and legacy of the operation.
Eurovision has become something of a ‘white whale’ for me. So, walking into Liverpool’s M&S Bank Arena ahead of the first of nine live shows was a truly stupendous experience. With over 600 rigging points, 140 tonnes of steel ground support structure, and 1km of steel truss added to the arena, it is a production unlike any other. The arena alone featured eight miles of cabling, over 2,000 lighting fixtures, 200 custom staging decks with 950 sq m of staging for the main stage and 500 sq m for the green room, as well as 2,000m of secure fencing site-wide.
Technical Directors, Luke Mills and Gary Beestone were engaged by Executive in charge of Production, James O’Brien to manage and coordinate the technical elements of the arena production, while the EBU and host broadcaster, BBC managed the logistics, camera focus and broadcast elements of the show. Starting work on the project in the first week of December, the duo soon realised that despite their decades of experience, Eurovision presents its own unique set of challenges.
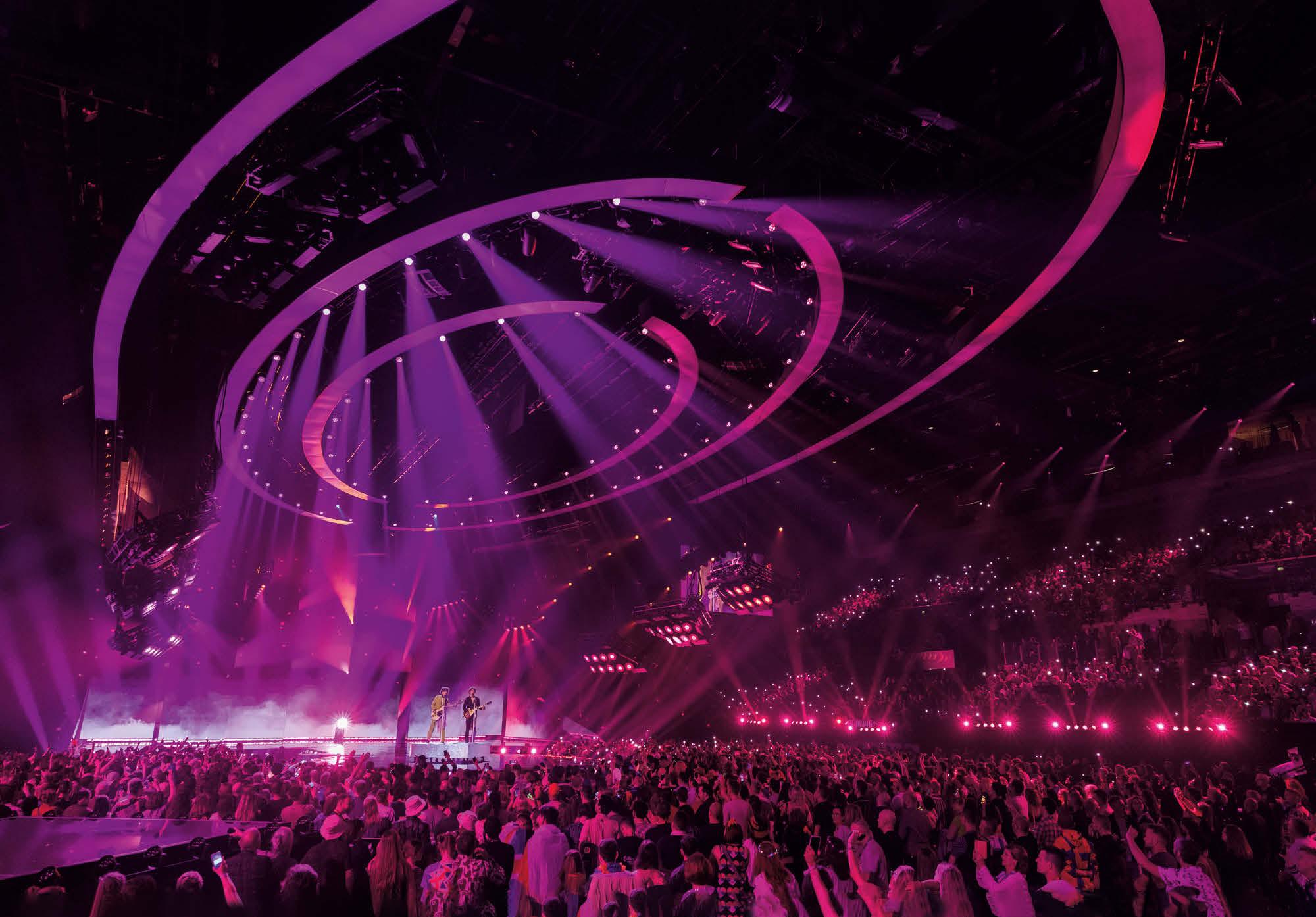
“It may sound naïve, but we didn’t anticipate how much of a competition it is. Each delegation, whether they have a simple or complicated technical performance, gets the same amount of rehearsal time.”
This time pressure was compounded by additional ticketed dress rehearsals on top of the two broadcast semi-finals and final, with an average of 9,000 attendees.
As is to be expected for an event of this nature, the procurement process was transparent and rigorous, yet also extremely efficient. Condensing their usual process due to time pressures, Mills and Beestone sent RFQs based off the preliminary staging design and schematics for the show before the negotiation and value engineering phase until they arrived at the budgetary, appointment and building phase of the project. “We used our collective experience of who was capable of delivering this project, as well as value for money and service to choose which suppliers were approached.”
The roster featured: Aggreko (power), Britannia Row Productions (audio), Black Skull Creative, Creative Technology (video), ES Global (staging), Faber Audiovisuals (video), LED Creative (LED lighting), Neg Earth Lights (lighting), NorthHouse Creative (content), Ogle Hog (video), Opertec (cameras), QED Productions (video), Riedel Communications, Stage One Creative Services (set construction), Showforce (crewing), Unusual Rigging, Yellow Studio (set design), WiCREATIONS (LED automation) and ER Productions (special effects), among others.
“We have worked with most of the technical suppliers before and their experience was vital,” Mills added. “Every Eurovision pushes the envelope creatively and technically, and we wanted to do that, but we were also aware of the time and budgetary requirements, so we had to ensure with innovation came stability and the ability to deliver the show safely.”
Thankfully, where Eurovision falls within the live events calendar is advantageous by design, according to Mills. “Festival season hasn’t quite started yet, and most stadium or arena tours are in production rehearsals or preparing to go on the road, so it falls at the sweet spot after Christmas where there’s a lot of kit on shelves.”
Following his seven-week residency in Liverpool, Mills reflected on the feat. “The level of detail and coordination required was epic, with a lot of equipment having to fit into one arena. Our biggest technical challenge was the economy of space,” Mills said. “We had to upgrade the roofing to build on the total amount allowable in the roof with a secondary stage truss system ground supported underneath to take even more load in.”
For the roof to withstand the dynamic load required, collaboration among technical suppliers was integral. Technical Designer, Malcolm Birkett created a 3D model which the core departments could access, review, share and disseminate technical information.
The ceiling arrangement, which Mills referred to as a ‘layer cake’ method, featured an ES Global master grid, Unusual Rigging’s
Movecat and static lighting trusses, and an LED ceiling created by a combination of Creative Technology and Faber Audiovisuals, in addition to a WICREATIONS automation system.
The sidewalls were also built collaboratively and assembled by Stage One, with LED panels on the bottom half of the set ground stacked as well as flown with LED Creative neon solutions and lighting fixtures, which had to be accessible during the build, maintenance and derig.
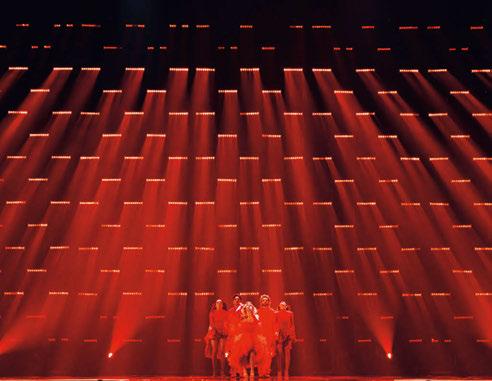
“From a design point of view, we wanted a flexible platform for each delegation to create a unique set, despite sharing the same stage and largely, the same tools,” Mills remarked, noting any additional set piece extras were provided by individual delegations.
In partnership with the UK, Ukrainian-based Opertec brought its wealth of experience and expertise, having been involved in a handful of past Eurovision campaigns. There was also a creative Ukrainian team working alongside Black Skull Creative, Ukrainian floor managers and members of the visual departments.
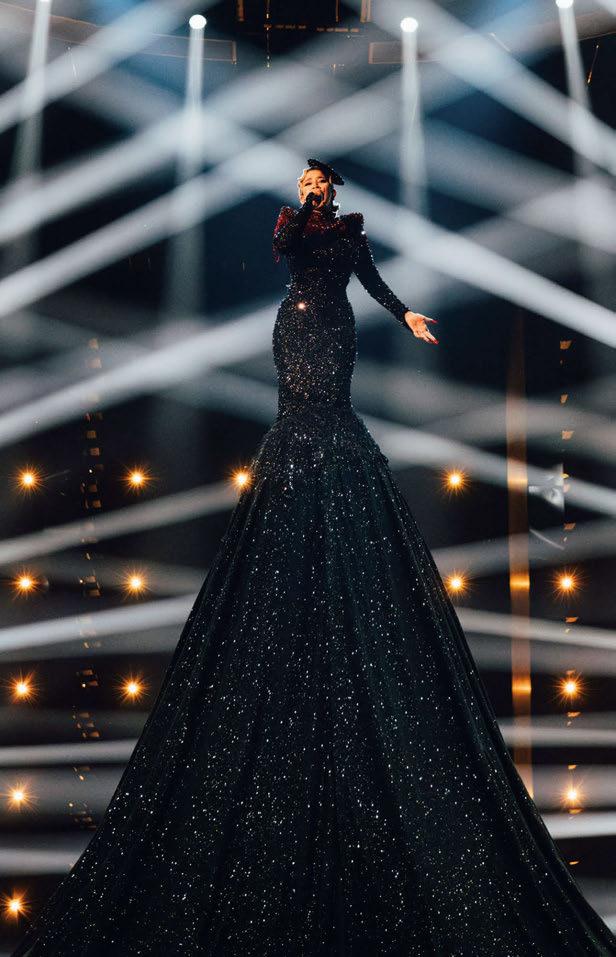
“Our goal was to make this production as collaborative as possible. It was an extremely humbling experience and speaking to them about their experiences back home put things into perspective.”
One of Britain’s most multicultural cities, Liverpool took to Eurovision with open arms. “We were welcomed by everyone. The entire city was buzzing – particularly the venue team, who were incredibly forthcoming, accommodating, and helpful. The ACC and M&S Bank Arena was the perfect space,” Mills recalled. “A highlight of mine was successfully navigating the complicated load-in. We achieved something amazing within a short space of time.”
The technical team included Production Coordinator, Sophie Scotchford; Fitup/ Overnights, Gavin Eldridge; Systems, Nick Joyce; Staging/Scenic, Chris Booth; Drafting, Tom White and John Venier; Set Carpenters, Pete Squires and Gibson Arpino.
‘EVERYBODY RELIES ON US’
Although the messaging of this year’s event was ‘united by music’, that could feasibly be rebranded to ‘united by Riedel Communications’ when it came to powering the show’s vast communications network.
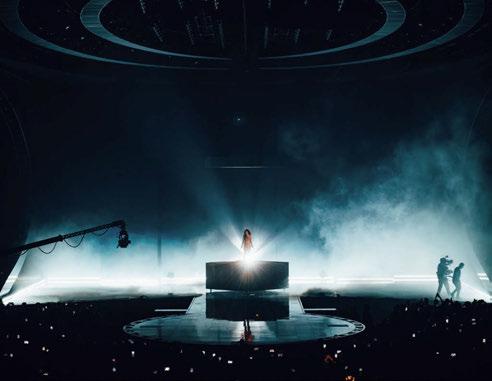
Hu Min Lee, Senior Project Manager at Riedel Communications, has been involved in spearheading the delivery of Eurovision’s sitewide communications and accreditation for the past five years. As well as radio infrastructure and accreditation, the team installed turnstiles, fibre cabling, distributed radios and set up MediaNet and media communications for engineers sitewide, including OB vans. “Everybody relied on us, which is why we were the first in and almost the last out of the venue,” Lee remarked.
With 26 communications engineers on site for the final and a further six members of crew brought in for the dismantling, Lee built his team around those with experience of highend projects. “This type of show came with its own language,” he said, citing the international nature of the crew with engineers from the UK, Germany, Portugal, Hungary, Denmark, Croatia, and Switzerland. “There was a mixture of language and experience, which is particularly beneficial for commentator communications.”
This year’s event saw the deployment of around 200 intercom panels and 180 Bolero wireless intercom systems. Lee reflected on the biggest technical revolutions of the company’s 15-year relationship with the EBU and Eurovision. “We relish providing solutions for our clients and where else better than the Eurovision Song Contest? This was the perfect demonstration of technical ingenuity.”
With AES3, the team had to define and navigate where to put the cabling and matrixing, which is no longer a consideration with the emergence of AES67. Commentators also used to use ISDN codec, which is no longer sought after, so moving to a Z/IP server was another revolution in addition to the development of Bolero. “Having a wireless intercom system with six buttons was a gamechanger to meet the demand for a show like this,” he explained. “This was a project where hundreds of people demand communication in real time, so we couldn’t go fully digital.”
Instead, 170 Boleros – which are half the size of analogue radios required for a show like this – provided the production teams increased flexibility to communicate. “It was a pleasure to collaborate with the EBU, BBC and the Eurovision Song Contest team on this unique event,” he concluded.
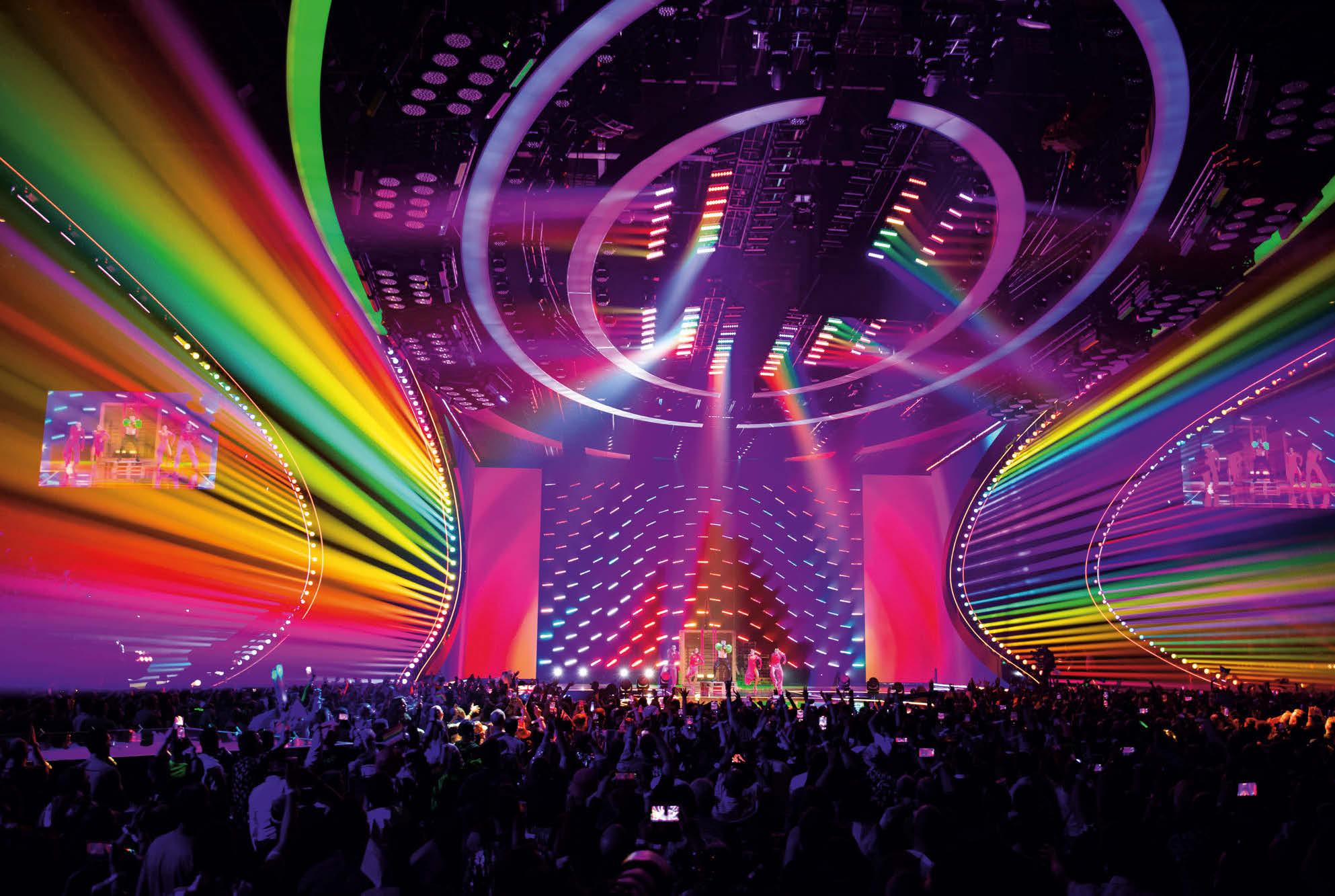
‘THEIR SHOW IN OUR HOUSE’ Black Skull Creative, in collaboration with sister company, Black Skull Studio under the guidance of Creative Directors, Ross Nicholson and Marvin Dietmann, were entrusted with the task of creating performances for Armenia, Australia, Austria, Cyprus, Denmark, Italy, Germany, Georgia and the UK, alongside Jay Revell and Paul Gardner.
Having come second in the competition last year as part of UK entrant, Sam Ryder’s delegation, Black Skull Creative’s Dan Shipton assumed the role of Lead Creative Director. He collaborated with Executive Producers, Lee Smithhurst and Andrew Cartmell, the famed Martin Österdahl and Lead Commissioner, Rachel Ashdown to define what Eurovision 2023 would look like from the UK and Ukraine’s point of view.
“We wanted to reframe the public’s perception of Eurovision. This contest transforms artists into global superstars, and when we look back on the UK’s history with the competition, we perhaps haven’t taken it seriously enough. While that began to change last year, we wanted to build on that with amazing production values. We also wanted to map out how best to honour Ukraine and make it their show in our house,” Shipton said. “We couldn’t have done this without the amazing team involved. We wanted to take production values to the next level, and on any production, there are many factors restricting what you can do, but the brilliant thing about Eurovision is the fact that you bed into the venue and have the luxury of time to perfect things, which allows space for creativity to thrive.”

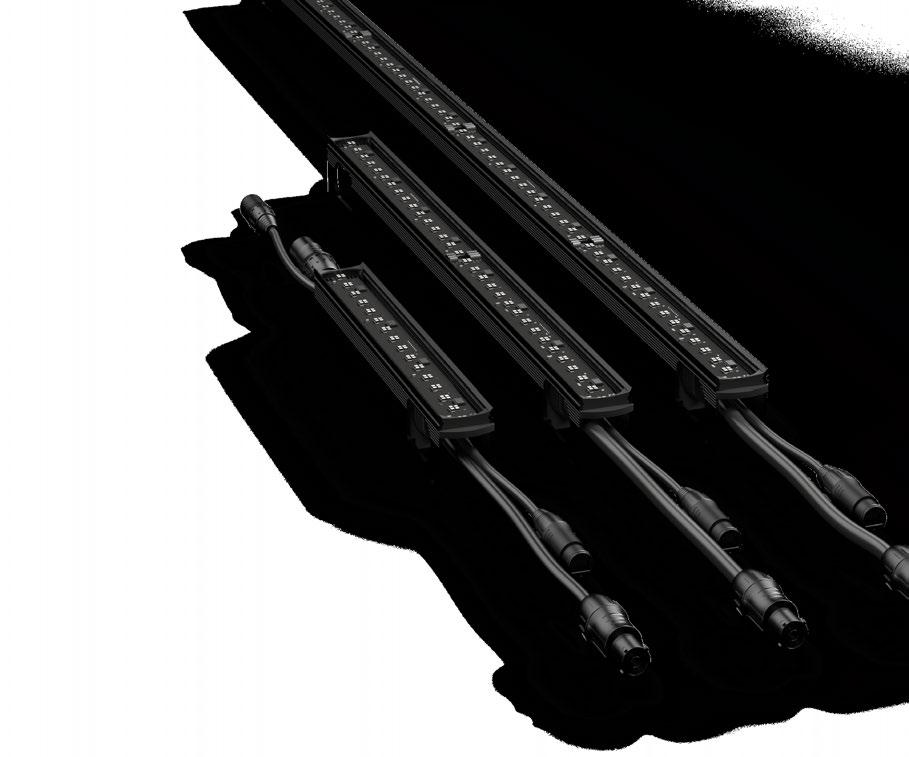
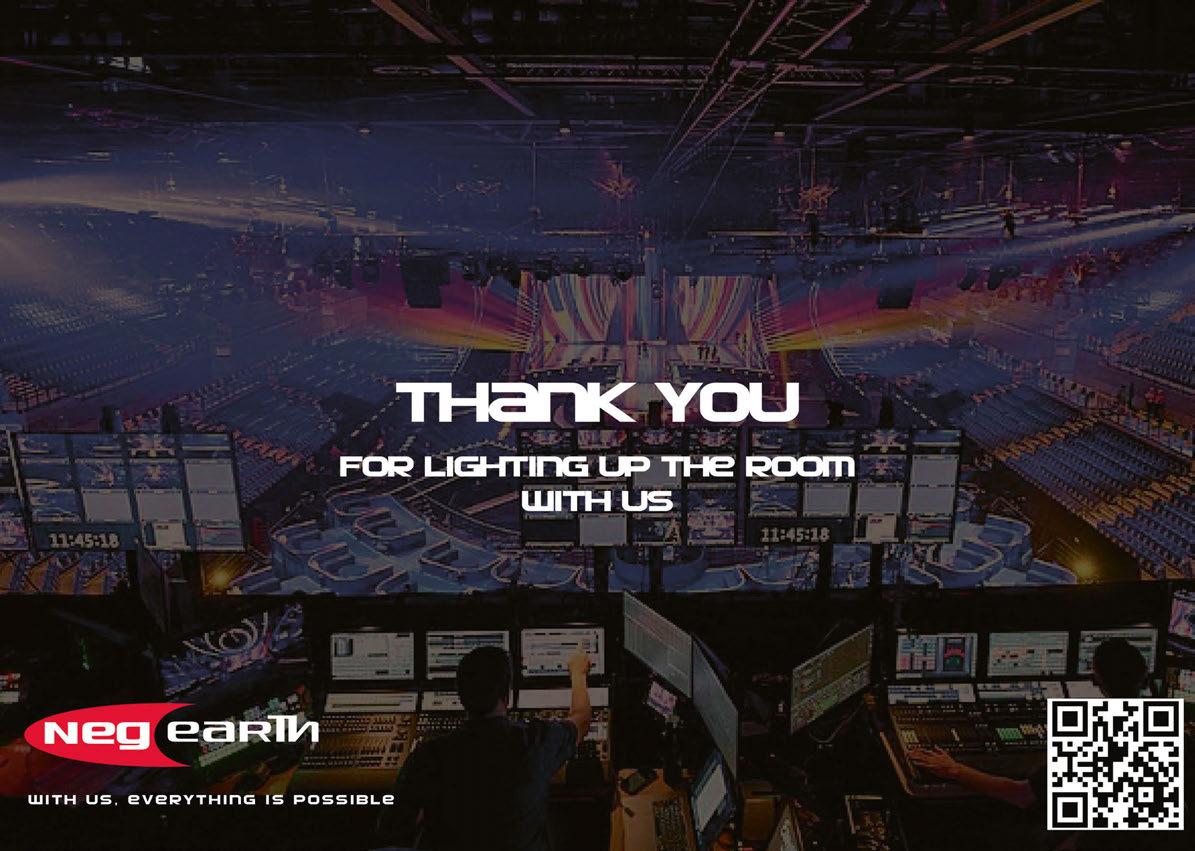
In line with this year’s messaging, the stage design concept was created to reflect the ‘united by music’ slogan with the architecture of the set symbolising an open-armed welcoming hug for the people of Ukraine and Europe.
Tasked with heading up a brief which included logistical requirements such as multiple areas to perform, theatrical set pieces providing automation to help transform the stage, and an on-camera greenroom for all the delegations was New York-based design outfit, Yellow Studio.
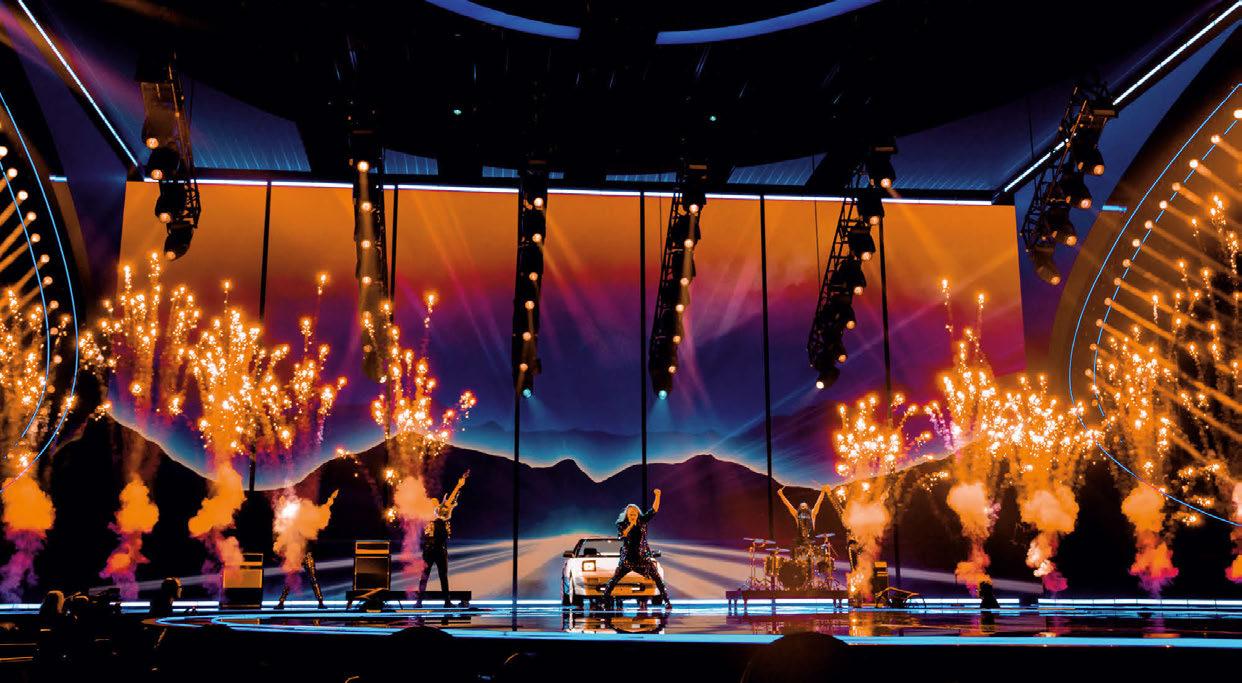
“We started the design process in Rhinoceros 3D software modelling different concepts by our design team. Once we decided on one approach, an OBJ file was delivered to our renderer who works in Cinema 4D to create all our visuals,” Julio Himede, founder of Yellow Studio, explained. “We are proud that our original concept from the first sketches in Rhino to the final product stayed consistent.”
The fast and furious turnaround between acts was a challenge the stage design had to meet head on, as Himede recalls. “The changes need to happen in a 50-second interval, therefore, the design needs to offer multiple ways for props, set pieces and talent to come in and out of the main stage. These changes are required to function even if there is a malfunction in the automation and technology integrated in our design.”
Himede commended the “dedicated professionals” who worked on the show for over six months. “Together, we delivered a polished and well executed production,” he concluded. “The ‘united by music’ message relates not only to the delegations competing, but the hundreds of professionals involved, and the friendships made along the way.”
‘WE LIKE TO RISE TO A CHALLENGE’
“Eurovision is on the bucket list of every person who operates in this sector, and with the eyes of the industry and millions watching at home, as well as the short timeframe, it was a daunting prospect which has ultimately paid off for us,” WICREATIONS Key Account Manager and Automation Designer, Geert Stockmans began. “The world remembers the ‘failing sun’ last year, so there was a certain reluctance to depend heavily again on automation technology.”
Due to WICREATIONS’ attention to detail and proven track record on the world’s biggest stages, the firm was entrusted to develop a bespoke automated LED solution using stock rental equipment which met on-stage safety concerns, applicable standards and regulations. “We have gained a high level of expertise in automating LED screens with attention to detail, pixel alignment, the centre point of gravity control, verticality and perpendicular hanging,” Stockmans explained.
With production initially reluctant on automation due to last year’s failure, screens one and seven could only travel 2m upstage, while two and six could travel furthest, as well as rotate like screens three, four and five. However, no delegations harnessed the 360° manoeuvre due to the short eight-week timeframe between design, installation, and rehearsals with a test build in between.
“The biggest challenge was the timeframe, but we like to rise to a challenge at WICREATIONS,” he said, praising the collaboration among Creative Technology and Faber Audiovisuals for LED product and on drawing level and Neg Earth Lights and Unusual Rigging to ensure all rigging parameters were met. Automation was a necessity to create access to the stage. “There was a lot of flexibility in the stage look and feel, allowing delegations to create their own performance, so the automation had to match this level of flexibility.” Stockmans pointed to this flexibility as important so each performance could be different. “Using our proprietary technology, the crew adapted to requirements very fast without the need to liaison with third parties,” he noted.
WICREATIONS’ wider project staff included: Project Manager, Jasper Rosiers; Safety
Consultant, Blumano; Automation Engineer, Lesly Van Rompaey; Crew Chief, Stano Kusik; Automation Operators, Joey Poortman and Roger Smissen; Automation Assistants, Martin Rumler, Darren Clive Pitt, Fran Bradley, Senne Diels and Tomasz Kadlubek; and Structural Design Engineers, Wessel Fortuin, Ward Van Hassel and Tim Bernaerts.
“This is one of the most watched live broadcast shows in the world and is recognised among industry peers as an ‘industry showcase’,” Stockmans concluded. “We were overjoyed with the outcome and have had several enquiries from creatives about using this system in their shows in the future.”
‘A ONCE-IN-A-LIFETIME GIG’
With 165,000 channels of lighting control, 23,700 individual light sources, and 2,500 moving heads, the lighting team used nine consoles to power 28,000 lighting cues, while 15 follow spots were operated by 10 professionals and five theatre technology students from LIPA and Cheshire College. “This is a once-in-a-lifetime gig, firstly doing
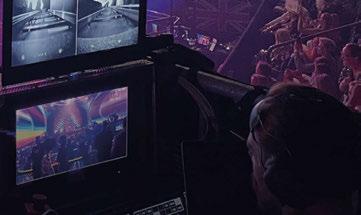
Eurovision and secondly, in the UK with the BBC,” commented Lighting Designer, Tim Routledge. “I stopped taking bookings for 2023 as soon as it was announced that it would take place in the UK on the off chance!”
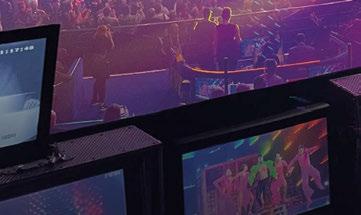
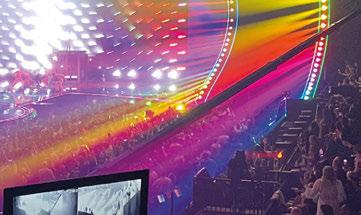
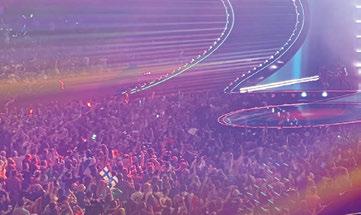
Routledge assembled a team including frequent collaborators, James Scott of Suluko as Associate LD – who shared the bulk of the planning, communication and waves of changes submitted by all delegations – and Previsualisation and Associate LD, Morgan Evans, who created the initial previsualisation with Syncronorm Depence R3 and on site liaised with all delegations taking their notes from the viewing room.
With all 37 delegations and interval performances using the same ‘toolbox’, the lighting rig had to be dynamic and flexible. “We choose fixtures that are reliable, look great on camera and provide us with a range of looks. We used the rig to create different architectures within the venue and maximise bang for buck,” Routledge said, pointing out the various automated trapezoids dubbed ‘Svoboda 3000’ by the crew, in homage to
Josef Svoboda – which were made up of Ayrton Zonda 9 FX lights edged with GLP FR10 as just one focal point of the lighting design and key to the flexibility of the rig.
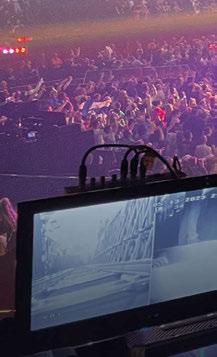
Despite having 2,200 moving heads to play with, Routledge believes some of the most impactful looks of the show were when artists emerged out of darkness, harnessing negative space with a stripped-back look. The team referenced Netherlands, Georgia and France as “creatively wonderful” performances, which tapped into a smaller footprint of fixtures to create an impactful set.
Evans harnessed creative tools like Vectorworks and Depence R3 for previsualisation. “It started as conceptual to envisage the set design and lighting together. However, the BBC was interested in the outcome and wanted to share still renders and animations created using Depence R3 on social media,” he recalled. “We ended up revealing more of the lighting rig than would ordinarily be revealed by a host broadcaster.”
Eurovision normally releases still renders; instead this was two-minute animation, which demonstrated the various facets of production. “We set a high expectation by releasing it so early on that we had to live up to it; I think we’ve set a benchmark for future renditions of the competition,” Evans stated proudly.
Control came in the shape of MA Lighting grandMA3 full size and light consoles with MA3 PUL and PUM processing units. This year’s event also marked the first Eurovision to use MA3 software on such a large scale, with the company on hand to assist. “I was dubious of the leap to MA3 software at first, but it was rock solid,” Routledge commented. “We were able to create effects that were simply impossible to do in other software.”
Morgan collaborated with Syncronorm to fine-tune the deployment of Depence R3 software. “Syncronorm rebuilt and upgraded certain elements of the software to withstand up to 300 universes, making this the largest Depence R3 project to date. Using grandMA3 MVR and viz-keys through the Depence R3 workflow was also a massive benefit.”
With this new update, Syncronorm raised the real-time system performance so that Depence supports up to 1,024 DMX universes.
This made it possible to previsualise lighting, automation, and video with over 3,000 fixtures on more than 300 DMX universes required.
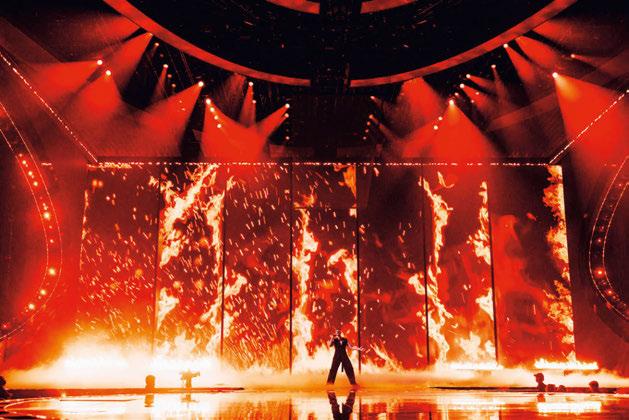
“We are proud to have contributed to this unique project with extensive support for the lighting team,” Syncronorm’s Andre Portmann said. “Depence version 3.1 was developed in parallel with the ESC and specifically made available for pre-programming an ongoing production. The design team was able to rely on the strong performance, realistic render quality, and fixture accuracy of the software. Otherwise, it would not have been possible to realise all delegation shows in such a short time period, making Depence an integral part of the production process.”
Meanwhile, the team was in regular contact with all delegations to discover what equipment they were using in advance – which could often change due to a range of factors. “Because of the volume of changes happening day to day, having a single source of data coming from Vectorworks mean that via the MVR workflow we were able to relay changes quickly and accurately to all team members in a very efficient manner. Depence would be updated alongside the MA3 sessions receiving updates,” Scott explained.
A separate programming team handled additional notes overnight. “We couldn’t have done this without them, and the long hours of effort they put in to make this a reality. We rented our own ‘roadie kitchen’ to keep morale and spirits high among those long programming days,” Routledge recalled.
Outside of rehearsals, the designers didn’t have any direct contact with the delegations. “Every delegation is in it to win it, so even if they request something we personally would not choose as designers, we take on board their feedback and work with it,” Routledge said.
An added challenge is creating a “cohesive and varied” show, despite the running order being set in stone. “This year, a lot of delegations requested red lighting and heavy smoke, so we strive to present those ideas in a varied or dynamic way by using different fixtures and effects,” Routledge explained.
Gaffer, Chris Rustage and Technical Manager, Brad Purse of LED Creative oversaw the build and deployment of 2,000m of LED product and 80 Byte Controllers spread out across the arena, as well as set extras for certain delegations and special acts on stage.

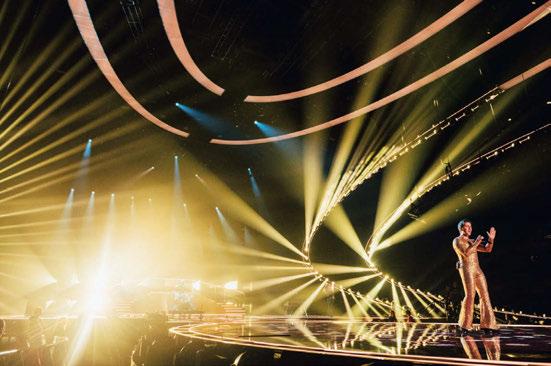
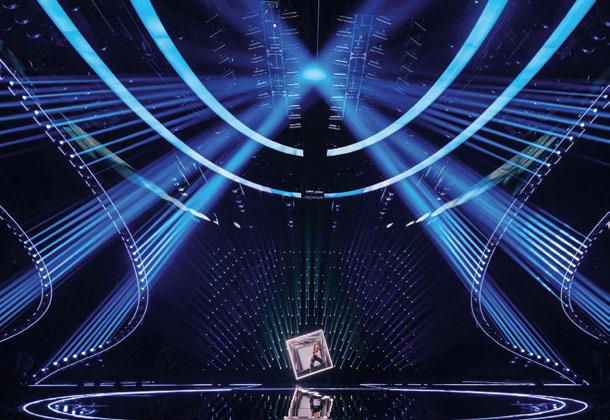
By te Controllers, considered LED Creative’s flagship product, received an upgrade for the biggest music competition in the world.
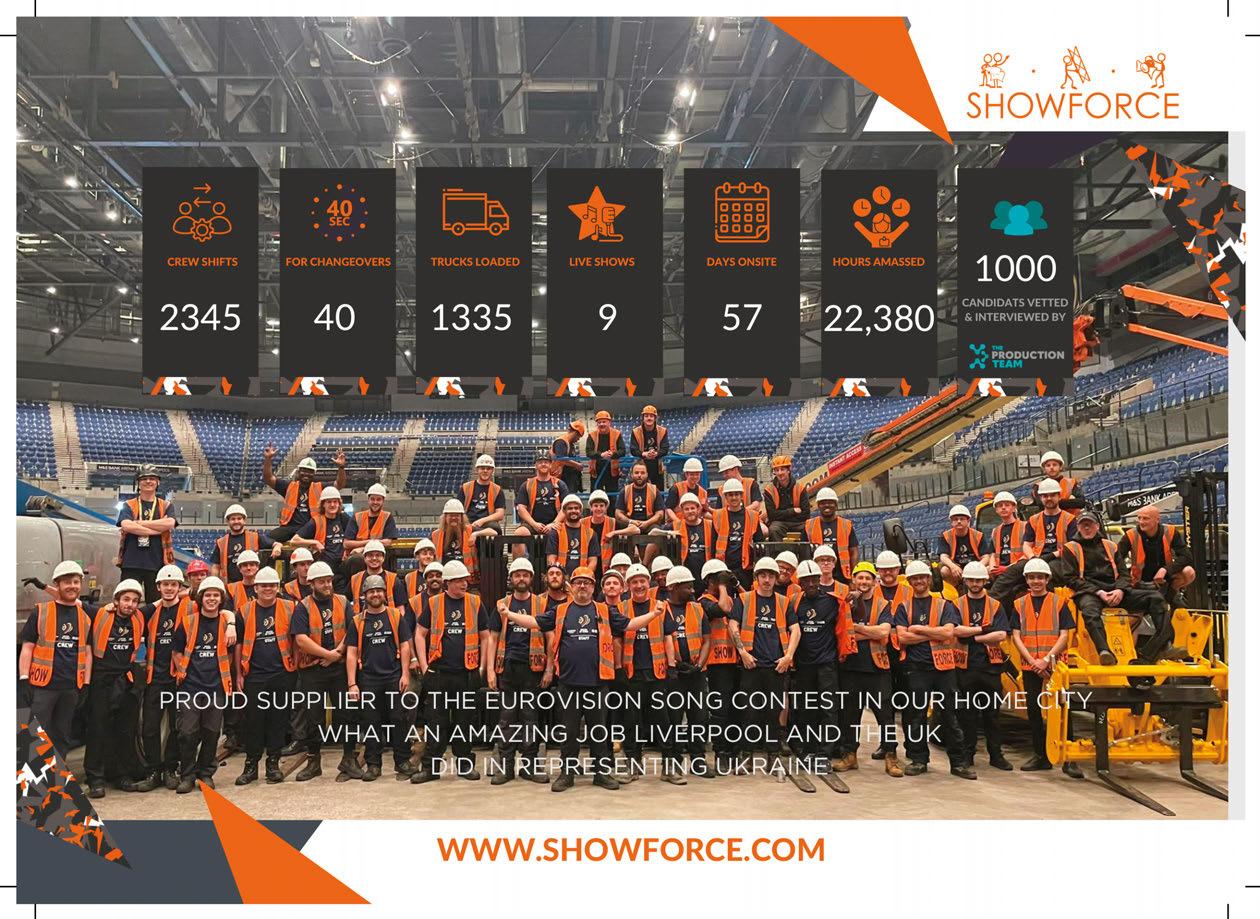
“Pixel tape tends to be low voltage, which incurs problems with the amount of intensity you can get out of it; for big shows we often run into requests from designers for it to be brighter, so we have revamped it with slightly higher voltage for Eurovision,” LED Creative’s Tim Rees commented. “We have received lots of praise from the industry for our work, particularly Israel’s set extra, a ‘cascade of squares’, which looked spectacular.”
The rig featured some of the top lighting sources on the market, including ACME Pixeline IP; Ayrton Cobra, Karif-LT and Magic Blade-R; Claypaky Sharpy X Frame, B-EYE, Scenius Unico, Sharpy Plus Aqua, and Sharpy X Frame; Chroma-Q Color One 100; Robe BMFL Blade, FORTE, Spiider, PAINTE and RoboSpot followspots; Color Kinetics iW Blast TRX; Litepanels Astra; SGM Q-8 and P-2; Martin Professional Sceptron and MAC Aura PXL,
GLP impression FR10 Bar; Astera Helios Tube, Titan Tube, Pixel Brick, AX5, AX9 and mounted HydraPanels; CHAUVET Professional Colorado PXL 16; and Prolights ECL Panel.
Among the array of Robe fixtures on the rig, Routledge proclaimed: “Robe FORTE is the finest moving key light on the market, which we use for its key light and followspot capabilities. It is flicker free, which is ideal for a broadcast show, and its tint channels are unrivalled.”
Wahlberg Lifting Columns were also integrated into the oval stage, which Routledge dubbed as “cost effective” and a “neat” addition, which could hide lighting fixtures or lift them 1.8m into the air. “Using Warhberg Lifting Columns helped us to change the architecture of stage design,” Routledge said, praising the involvement of the lighting supplier. “We were thrilled Neg Earth Lights were on board. They did the UK proud, and they went the extra step –from the preparation and packaging of the kit to their expertise on site and even a little box with biscuits for the crew to have during tea breaks.”
Delivering the 10 Gbps Network System with redundancy on the scale required was a challenge that Neg Earth Lights’ control department embraced. “Many Zoom calls with the team were spent to develop the correct architecture capable of delivering reliability and speed on a system of this scale,” Lead Project Manager, Damien Jackson said. “This allowed us to extend our relationship with Luminex and collaborate with new partners, particularly NETGEAR, who have provided us with outstanding support.”
Neg Earth Lights invested in NETGEAR M4250 and M4300 AV-Line switches. “These proved to be a great choice; the system monitoring capacities were exactly what we needed, and the switches were rock solid,” Jackson said.
Having been so engrossed in the minutiae of the day-to-day, Scott recalled losing sight of the monumental task at hand, with little period to reflect between the build, rehearsals and showtime. “We kept having to pinch ourselves to remind each other that we were working on the Eurovision Song Contest,” Scott laughed, noting that it wasn’t until the first rehearsal with Norway that the design team realised the lighting was Eurovision-worthy. “This was the most joyous project I’ve been involved in,” added Routledge.
Despite orchestrating some of the biggest shows in recent history, Routledge found the Eurovision atmosphere to be the best. “It was off the charts and one of the nicest things about working on this project has been receiving well wishes and messages from people who you are inspired by or respect in this industry.”
Part of Routledge’s pitch was the integration of Ukrainian creatives within the lighting team. “We discovered the amazing Zhenya Kostyra, who designs lighting for Dancing with the Stars and The Voice in Ukraine, as well as being the world’s loveliest man. It was one of his dreams to be part of the show and after an awful 18 months, we were delighted to have him involved. He also knew all the Ukrainian camera team including host, Julia Sanina. It was great to have a team of great Ukrainians in the camp who had worked together before!”
The wider lighting team featured: Moving Light Programmers, Tom Young and Alex Mildenhall; Keylight Programmer, Marc Nicholson; Followspot Caller, Louisa Smurthwaite; Overnight Programmers, Adam Marshall and Alex Passmore; Gaffer and Crew Chief, Keith Duncan; Gaffer, Marc Henry; Technical Manager, Joao Magalhaes; Network Technician: Richard Shout; Network Technician, Alan Watkins and Vision Supervisor, Daryl Bidewell. “We’re proud that we had a 50% female crew and a wealth of expertise on site,” Routledge remarked. “The LIPA and Cheshire College students were all brilliant additions.”
Neg Earth’s team comprised: Lighting Technicians, Cara Wiseman, Ed Swygart, Shelley Parker, Chris Taylor, Jonny Nunn, Nick Gregson, Holly Brightman, John Hetherton, Katie James, Jamie Gorman, William Frostman, Adam La Femina and Mary Webb.
“Our warehouse lighting team prepped over 2,000 fixtures in just over a week without waiving the standard of preparation the crew and customers expect,” Jackson added. “It’s been great to witness how everyone, regardless of the size or scope of their role, has embraced the opportunity and thoroughly enjoyed being a part of it.”
‘A WELL-OILED MACHINE’
As custodians of over 150 microphones and 1,200 individual streams of audio, Britannia Row Productions ensured that every note was crisp and intelligible as well as providing sitewide sonic coverage. Josh Lloyd, who assumed the role of System Engineer and Designer, specified the PA system, as well as the nuts and bolts, the consoles of choice and how everything tied together to create a redundant system. He consulted with George Hogan to oversee RF and help execute and programme the network and support on site.
Br it Row supplied signals for broadcast and an RME Madiface XT and Pro Tools playback system, which Lloyd referred to as “the spine of the show”, delivering timecode that Riedel Communications distributed to CuePilot.
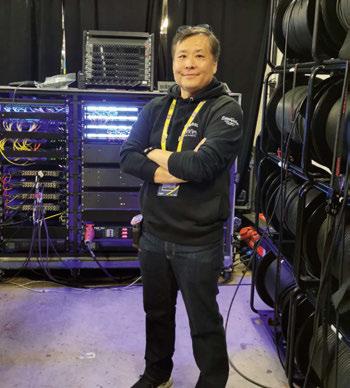
“The flow of this show was unrelenting with certain rules that must be adhered to, like providing up to six microphones or headsets per delegation,” Lloyd explained. “However, technical execution was down to the vendor, audio designer and the constraints imposed by the venue. We designed a system that meets those requirements, while delivering what the BBC and OB vans required.” Brit Row also handled the sound for the picture postcard broadcast VTs between each performance. “The sound effects that came from the OB truck are triggered centrally – by what the cue is – by MIDI that is distributed over the network, which was strange to be using in 2023 but that’s how it works best.”
The other brief was resilience. “Eurovision is a well-oiled machine,” Lloyd said. “A lot of the crew were involved in past editions, and although we had already completed the design, we sense checked with the likes of DiGiCo, who have a history with the contest.”

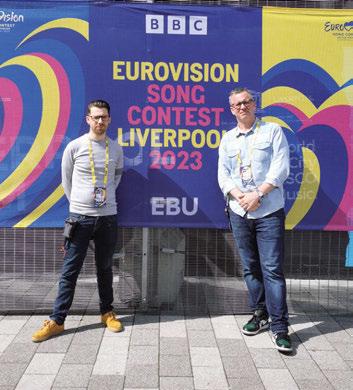
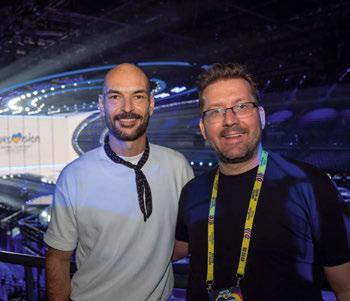
DiGiCo Quantum 7 and SD12 were the FOH consoles of choice with Quantum 7, SD11 and a Yamaha QL1 monitor console selected for monitors. As in prior years, Shure ADX2FD handheld microphones, ADX1 beltpacks and AD3 plug-on transmitters as well as 40 channels of Shure PSM 1000 in-ear monitors were used by the performers. Stage monitors came in the shape of d&b audiotechnik M4, M2, V-SUB and D80 amplifiers.
“A lot of processing was done over IP; using niceties such as iPads for Wave Tool make it comfortable for those working backstage,” Lloyd added. “IT and networking are increasingly important as a sound engineer. We had to deliver from an IT perspective as much as the nuts and bolts.”
Digital Specialist Engineer, Rob Priddle managed the digital infrastructure, analysing any issues and checking the sound levels in the room to meet BBC guidelines. “This was one of the biggest shows on the planet with three series of ProTools and RF spanning the entire arena. Most people have two antennas at the side of stage, while this stage had 26 around the whole room, so even the studios and dressing rooms are mapped,” Priddle noted.
Shure mic feeds were processed digitally by DirectOut Technologies PRODIGY.MP units running for media conversion. “They’re a wonderful box; with this event, we used them in a redundant ‘fall over’ mode for contingency. We had one for Pro Tools, another for RF, and a pair which handled PA,” Priddle said.
The L-Acoustics PA system featured the brand-new L2 and L2D loudspeakers, as well as familiar L-Acoustics architecture in KARA II, K2, A15 Focus, A15 Wide, KS28, KS21, 5XT, LA7.16, LA12X and LA4X. “As a TV event, the PA doesn’t have as much room in the roof as lighting and video. The design has been done to give maximum thought to the broadcast.”