
7 minute read
Brompton Technology
Brompton Technology’s Business Development Manager, Rob Fowler, Product Manager, Thomas Walker and General Manager, Asia, Elijah Ebo.

BROMPTON TECHNOLOGY
Experiencing a meteoric rise since its formation in 2011, Brompton Technology has revolutionised the world of tour-ready LED video processing. Peter Iantorno takes a trip down to the company’s London HQ to meet the team behind the tech.
The Brompton Technology team is a busy one – a very busy one. Since it was formed in 2011, the company has experienced rapid growth that has seen several new product launches as well as an ambitious expansion into China, so the fact that TPi was able to catch the majority of the senior leadership team all together in one room was a minor miracle in itself. Settling down in Brompton’s head office in West London, Managing Director, Richard Mead, brought us up to speed with the company’s origin story. “In order to talk about Brompton Technology, you must first talk about another company: Carallon,” he began. Carallon was set up 15 years ago by a group of engineers who had all worked previously at Flying Pig Systems – now part of ETC-owned High End Systems. “We enjoyed working together
but, for various reasons, we decided to move on, so instead of going our separate ways, we thought ‘why not start again on our own?’” The company started doing contract work for the likes of ETC and Martin Professional, which remain active Carallon customers to this day. “However, fairly quickly we started to come up with our own ideas and we wanted to take them to market,” explained Mead. And in order to keep some separation between Carallon and the products it developed, separate companies and brand names were created. The first of these in 2005 was Pharos Architectural Controls – “which does all the lighting control for things like the London Eye,” Mead commented, and next in 2011 came Brompton Technology. “We’d spent years going onto job sites and having conversations with video technicians,

who told us they had inadequate kit for working in live events,” Mead explained, when asked about the motivation for starting Brompton Technology. “We have made a habit of looking for niche markets that we don’t feel are being served well enough.” The first application the company explored was LED video processing. “We had originally planned to diversify into other areas of video, but we were so successful that it became the first and the last,” Mead commented. Th e Managing Director continued on how his company found its niche. “If you’re dealing with an LED video wall made up of hundreds or even thousands of individual panels, where do you plug in the video? We give the user somewhere to plug in the video that can take the signal, split it for all the individual panels, transmit it to the panels and make sure it displays in a nice, synchronised image – and do all that really quickly.” To that end, the first product to emerge from Brompton Technology’s R&D department in 2012 was the Tessera M2 – the company’s flagship HD LED processor – along with its first receiver card. “We started a collaboration with VER,” Mead explained. “Essentially, they pre-ordered our entire first run of the product – and for a company doing R&D, knowing that you’ve already sold out before you’ve even finished making it is really helpful.” By the start of 2013, Brompton Technology’s LED processing was being used by VER on the biggest live televised show of the year: The Academy Awards – “That was quite a stressful weekend!” Mead recalled. However, while the VER deal was undoubtedly an early success, Mead reflected that it also presented a challenge. “We became so closely associated with the rental house, it took some hard work to persuade other rental companies that we weren’t just a VER product,” Mead commented. “And that was one of the main jobs that
Rob had when he came in,” he added, bringing Brompton Technology’s Business Development Manager, Rob Fowler, into the conversation. Since joining Brompton Technology in 2013, Fowler has seen the company go from strength to strength – something he puts down largely to the wealth of industry experience within the team. “Everything we do is informed by our users,” he told TPi during a tour of Brompton Technology HQ. “It helps that many of our team are drawn from the live production industry and have decades of combined experience of shows and the rental staging sector. That helps not just in their own experience but also in the closeness they have with our customers. Seeing how they work and listening to their experiences has given us the inspiration behind many of our most eye-catching and celebrated fixtures.” The company’s early success presented its fair share of stumbling blocks – not least the fact that for every different panel a Brompton Technology system was used for, the R&D team had to come up with a different design that allowed the receiver card to fit. To remedy this, in 2014 the company released its R2 receiver card which, measuring just 68mm by 32mm and using the widely available DDR2 SO-DIMM socket, fit into pretty much any panel design out there. “That was a key step; it meant that we could just produce one card and leave it to others to fit it into their products,” Fowler recalled. “It was game changing.” By 2016, pushed on by the universal appeal of the R2 receiver card, sales started to grow rapidly. “We started getting adoption from a lot of big rental companies,” Mead recalled. That year also saw Brompton Technology launch two lower cost processors – the T1 and the S4 – “which meant we could deliver more cost-effective options for people who couldn’t afford the M2, which was always designed for the top-end tours and events”. The next task on the agenda for Brompton Technology was to strengthen its ties

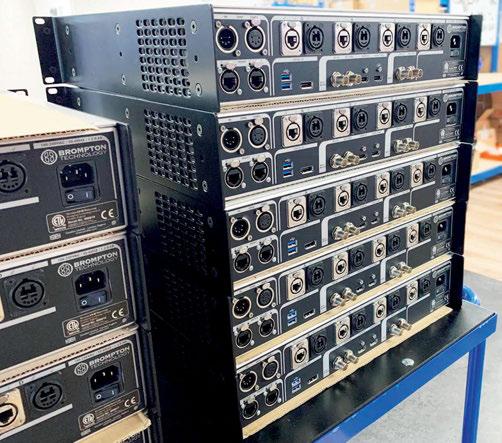
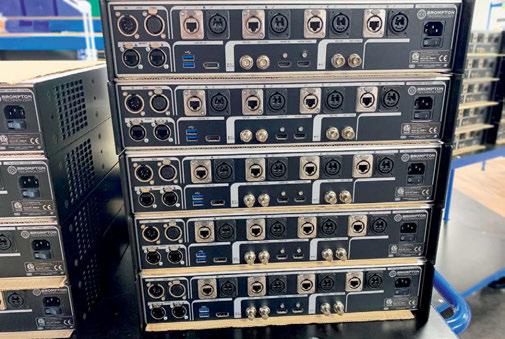
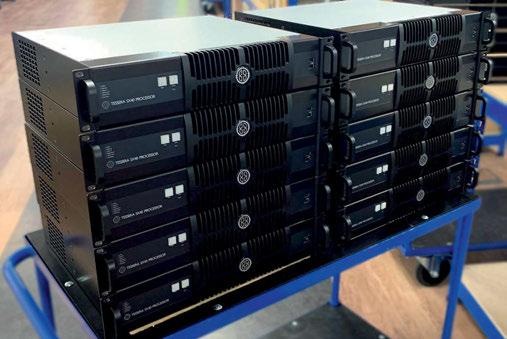
with Chinese panel manufacturers. “We needed to ensure we had a team who understood how the manufacturers operated and supported them in integrating our product,” Mead said. To that end, the company hired Elijah Ebo, who joined as General Manager, Asia. Mead commented: “Elijah built a team to do exactly that – including setting up our own office in Shenzen.” Brompton Technology now supports around 20 panel manufacturers in China, and even runs free classes for its employees to learn Mandarin. “It’s about more than just learning the language,” Ebo explained. “We have to embrace the Chinese culture. Listening and reacting to our Chinese customers has made such a difference to the way that Brompton has been able to do business in that part of the world.” An d whether it’s in China, the UK or somewhere else, listening and reacting to customers has always been a focal point for Brompton Technology. “The quality of technical support is critical to our brand identity,” Mead commented. “We made a decision that every single member of our customer-facing team would be technically proficient. Even people with a sales responsibility all come from a technical background, so they have been there and done it. They can use the product and can answer technical questions about it.” The next milestone for Brompton Technology came in 2018 with the launch of the company’s first 4K processor: the Tessera SX40. “At that point, the market had been telling us for at least a year that we needed to have 4K,” Mead recalled, explaining why Brompton was later to market with 4K than some of its competitors. “We’ve always taken a view that if we put a product out there, it needs to be reliabe. We assume every one of our products is going to get used on the Oscars the day after we start shipping, so everything has to be absolutely ready before we send it out.” Unsurprisingly, the SX40 has been incredibly successful, thanks in part to its smart integrated data distribution solution. Product Manager, Thomas Walker, explained in more detail: “For a HD video product, you need four or ideally six 1GB ethernet outputs to carry that much video data out to the panels,” he began. “If you go to 4K, you’ll need 24 separate 1GB ethernet cables, and that’s going to be a nightmare on any tour. To remedy this, the company developed a 10GB data distribution unit, the XD. “You just hang it on the truss and cable to the screen from that box, which means you only need to run one or two cables instead of 24,” Walker said. “It’s all plug-andplay and everybody loves it.” Looking to the future, Mead is in no doubt as to what direction Brompton Technology is going in. “We’re looking forward to releasing what we believe will be our next big thing: support for HDR video content,” he commented. “Our previews have had a great response, and we will pull back the curtain fully at LDI.”
“The quality of technical support is critical to our brand identity. We made a decision that every single member of our customer-facing team would be technically proficient. Even people with a sales responsibility all come from a technical background.” Brompton Technology Managing Director, Richard Mead
TPi Photos: Brompton Technology & TPi www.bromptontech.com