
5 minute read
BPM SFX
BPM SFX
Special effects specialist BPM SFX welcomes TPi to take an exclusive tour of its new facility in Burnley and discover how the company became an industry leader. Stew Hume reports…
Whether you’re a regular at festival sites or in one of the various arenas around Europe, there is little doubt that, at one point or another, you will have seen a BPM SFX logo, with its striking black and orange colour scheme, emblazoned on a hoodie or flight case. Established over 16 years ago, by Managing Director Adam Murray and Operations Director Jamie Holmes, the company was very much a success story from the EDM boom in the early 2000s. Over the years, the company has positioned itself as key player within the European live events industry, this TPi Award winning company provides a whole host of effects, from CO2 jets and confetti blasts, to G-Flames and lasers. But with a wide offering of effects, not to mention a strong recruitment drive for young aspiring crew, it became clear that BPM SFX was going to need a larger piece of real estate. “Our old facility was 3,500 sq ft, whereas this place is a 47,000 sq ft, three-storied building,” stated Murray, as he greeted TPi at the door of the company’s new HQ. The building is a converted, 100-year-old mill in Burnley, Lancashire. While walking around the new state-of-the-art space, there are still clues of the building’s past, which had been used for everything from a sweet factory to a munitions workshop for the military. “I guess you could say it’s all come full circle, although the explosives are somewhat different to what used to come out of the door,” joked Murray. The conversion of the mill has been a passion project for the entire team
since the company took ownership of the building back in July 2015. Bu t the time it’s taken has clearly been worth it. Brand awareness was at the forefront of the renovation, as can be seen on the approach to the building, which is painted black with two Olympic-style fire bowls flanking the reception entrance. Walking through the office space – and receiving a warm greeting from the friendly office dog – the company’s decade-and-ahalf of work is on display, with tour posters and photographs from its wide range of clients, including the likes of Swedish House Mafia, Coldplay and Calvin Harris, not to mention large-scale events such as Creamfields. Al though aesthetics were clearly important during the renovation, functionality was also a major consideration. “The SFX industry saw a dramatic change 10 years ago, as it moved from a niche sector of the market, to a model where you had manufacturers and those who used equipment,” reflected the MD, comparing it to the framework seen in the lighting, audio and video industries. “Before we started looking for a building, we knew we wanted to create a modular warehouse – in the same way lighting rental houses receive kit, which is then serviced and prepped before being sent out again,” he commented. “In the past there was a trend of SFX companies sending out kit and crew to site and then ‘figuring it out’ there. Due to the sheer amount of stock and number of jobs we have, we need to move to a more efficient way of
working.” The new facility includes both indoor and outdoor testing areas, a large-scale state-of-the-art workshop, technical repair room, research and development area, multiple programming rooms and a large-scale prep space for up to 30 people. Not only that, there is also a fully functional gym at the rear of the building, which is free to use for all BPM SFX staff as well as the wider Burnley community. “Right now, we have all the kit that has spent the summer in Ibiza,” stated Liam Haswell, BPM SFX’s Technical Director, as we walked through the warehouse. “This space is ideal for ensuring we give the kit all the maintenance it needs. Especially with the amount of stock we have, you need to be efficient in how you service everything.” Al ong with keeping all the gear prepped, the new facility creates an ideal space to train the collection of up-and-coming pyro technicians BPM SFX brings in each year. “We run a very employment-based framework,” commented Murray. “It’s a decision I made quite a few years ago when we decided to get off the road. The business was growing so quickly, and I would rather have one of our team dealing with clients from day one. It gives production managers a level of consistency, which they seem to appreciate. It also means I have the time to deal with more of the administrative work.” In total, the in-house team consists of 22 people, covering everything from marketing and accounts to warehouse workers. “We really do run a family business – even though none of us are related,” laughed Murray. “We are there for all our staff and try to be as supportive as possible.” He explained that this included various incentives such as a weekly lunch open to all staff, along with off-site staff accommodation to new starters. “We’ve got a lot of young men and women starting with us, so to have the accommodation where they don’t have to worry about bills or other personal admin means they can get off on the right foot.” On the subject of new employees, TPi asked Murray what he looked for in a potential new recruit. “The reality of the situation is that this job is hard work,” he asserted. “Whether you come with a first-class education or straight from school, there is no particular CV that I’m looking for. Mainly because we train all new starters from day one. In many ways, I’d rather have a fresh mind who has pride and passion.” “T he in-house training, we perform here is rigorous,” stated Haswell. “It’s not about just about learning and operating about the SFX and laser elements we offer. Special heights training, first aid training, gas safety training, dangerous goods handling and transport training, IPAF and plant driving licences are all given as mandatory external training courses to our full-time staff. It better equips them to be able to perform their jobs
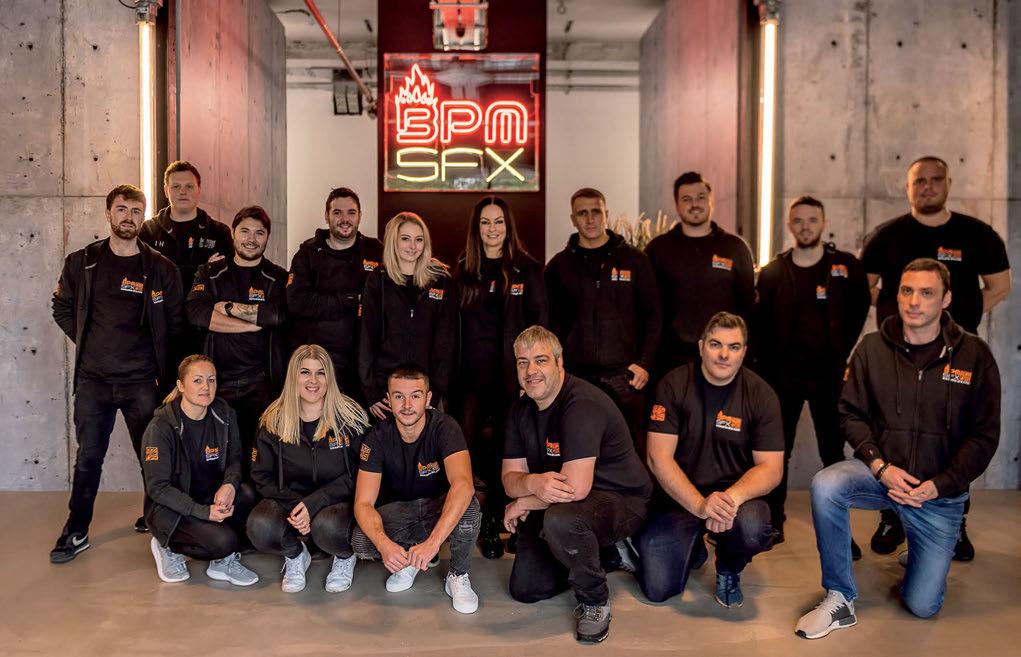
knowledgeably, safely and to the best of their ability in an industry where safety of everyone come first.” Al though the world of SFX has become more complex with the proliferation of DMX-enabled fixtures and the incorporation of complex control protocols, Murray asserted that safety remains the top priority. “The main priority is not client or artist satisfaction – it’s that everything is always safe on stage,” he stated. “It’s why our junior techs work between 100 and 150 events before they will even fire a show, to ensure they are competent and experienced enough to make each live environment safe.” Haswell also discussed the importance of imparting knowledge on the new members of staff. “With DMX control being such a major part of new fixtures, we provide training for MA Lighting grandMA2, which is essential for these modern riders,” he stated, explaining how LDs tend to ask for more control of the effects nowadays. “It’s an interesting trend,” chipped in Murray, who spoke of the recent Snow Patrol tour, where BPM SFX worked closely with LD Davy Sherwin to incorporate of one of the company’s latest offerings, Wahlberg Winches. “We brought in the Wahlberg Winches at the start of this year,” said Murray. “With our sector of the industry growing, we are always looking to provide new options for clients and automation is one such element.” The BPM SFX team first came across Wahlberg while working in a residency in Ibiza. “The winches allow our lasers to be sent back into the roof, which has increased our stage display options for clients no end,” said Murray. “We spent three months on R&D trying to ensure the data and power were in one slick package. The Wahlberg control system has come on leaps and bounds and we’re excited to see where it leads.” As this year draws to a close and an already packed schedule of tours beckons, the end of 2019 and the start of 2020 is shaping up to be busy for BPM SFX. Not only is the company’s touring schedule full, but it has also begun to make serious moves into the TV and film industry having recently taken an office in Media City, Salford. Yet another example of the company expanding into new territories in the global events market. Keeping a constant eye on new trends, Murray and his hard-working team are always pushing the boundaries, offering new and exciting effects on live events. The company seems to be setting the benchmark for this side of the industry and continually redefining what is possible with special effects. TPi Photos: Anthony ‘Mr B’ Black www.bpm-sfx.com