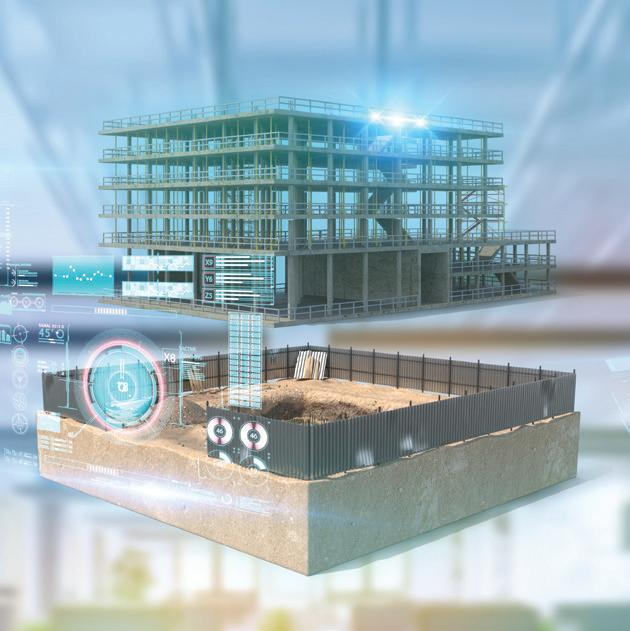
30 minute read
WHAT IS A DIGITAL TWIN?
The last few years have seen digital twins explode in popularity due to the significant benefits around cost-effectiveness and accuracy, and the ability to identify problems before they occur. They are allowing for more informed decision-making, which keeps project costs from soaring and avoids unnecessary delays – issues infrastructure professionals are constantly facing, especially now with the industry’s key role in the post-COVID economic recovery. Here, Infrastructure explores the technology and its impact on construction operations and maintenance.
Advertisement
The concept of a digital twin refers to a digital model of a physical object, process or system. In order to make the model identical, or a “twin” to the reallife subject, the digital model utilises historical and real-time sensor data.
The originators of the term, Dr Michael Grieves and John Vickers, said that a digital twin is “based on the idea that a digital informational construct about a virtual or a physical system could be created as an entity on its own. This digital information would be a 'twin' of the information that was embedded within the virtual or physical system itself and be linked with that system through the entire lifecycle of the system”.
The ability for a digital twin to be able to mirror the developments and changes in an asset is an important function for the infrastructure industry, as it allows for the use of the technology throughout all phases of an asset’s development, including the planning, construction, operation and maintenance stages.
By replicating the physical world in the virtual world, data can be analysed and systems can be monitored to prevent problems before they occur. This allows for infrastructure companies to potentially save costs by using the twin to troubleshoot any issues before the asset is built, and avoid wasting resources, labour and time that would have otherwise been spent fixing a problem.
OPPORTUNITIES AND RISKS
virtual environment where users can simulate and test the impact of changes to assets, products, systems and processes based on real-time data.
Benefits to the infrastructure industry include: ♦ Monitoring of an asset in real time ♦ Virtual scenario modelling and testing ♦ Supporting informed planning decisions, detecting and troubleshooting issues ♦ Providing more accurate predictions of potential problems ♦ Measuring performance and efficiencies of assets and equipment ♦ Information sharing with citizens and businesses
Although the technology is developing quickly, there are still some challenges to overcome. Potential risks of using digital twins include: ♦ The type and quality of data that is shared between the asset and the digital twin may mean that the latter is less accurate ♦ Potential challenges in the digital twin’s functionality with existing assets, products, systems and processes ♦ Digital twins with long lifecycles (such as buildings and infrastructure) may outlast the short lifecycles of data formats.
Design software formats have a high risk of becoming unreadable by modern systems at some point in their service life ♦ Potential disputes over ownership of the data being input into, and contained in, the twin ♦ Due to the high level of complexity, digital twins may be expensive to design and create
IMPLEMENTATION IN INFRASTRUCTURE
The creation of a digital twin often requires a specialist, such as an expert in data science or mathematics that can identify the physics underpinning the physical object, so that the data can then be used to develop a virtual simulation of the original.
Sensors are then integrated into the original asset to gather data about its real-time status, working condition, or position, all of which is then input into the twin. This is achieved through a cloud-based system that receives and processes all the data the sensors monitor. Throughout this process, the twin is able to simulate the physical object in real time, whilst offering insights into performance and potential problems.
To use an example, a factory might employ digital twin technology to measure the effectiveness of its systems and machinery. This would first require the use of historical data to replicate the factory in a digital simulation. Then, the sensors would be able to feed in real-time data to the digital twin user, allowing them to remotely assess the factory activities as they’re occuring.
In other cases, a prototype of an asset (such as a building, railway, or water pipe) can be used before the end product is built, allowing the technology to provide feedback as the end product is refined. In the absence of a physical asset, the twin itself can also act as a prototype. For example, a digital twin of a building before it is built can allow the designers, architects and engineers to identify any potential problems or opportunities for improvement before construction commences.
Digital twin technology has the capability to process complex data and systems, but it can also be simplified depending on the level of data used to construct and update it. For example, a digital twin of a road junction or traffic light might require more complex data in order for the user to monitor peak times, types of vehicles passing through, weather conditions and safety hazards.
However, a simpler digital twin might be beneficial for an energy company that operates a wind farm if it wants to optimise operations but is struggling because of the unpredictability of the weather. A digital twin could use historical data from a certain period of time to see how much energy was generated and in what conditions, then use this to predict the ideal angles for the wind turbines, as well as monitor wear and tear to forecast the lifespan of the assets.
ACHIEVING A NEW SCOPE OF MAINTENANCE
Digital twin technology not only helps to inform decision-making in planning and construction phases, but it can also support companies in maintenance and condition monitoring. If an issue arises in an asset that the asset manager isn’t sure how to fix, technicians can use digital twins to test solutions before applying them to the physical twin, allowing them to ensure safety and effectiveness.
The live data feed provided by the sensors also allows the digital twin to monitor the condition of an asset for issues in real time. This live condition monitoring means digital twins can be used for predictive maintenance, where faulty components or assets at the end of their useful life can be replaced prior to an issue arising. This process also eliminates the need for some manual inspection, and increases safety by allowing the operator or owner to proactively identify and remedy potential problems before they occur.
One example of digital twins being utilised for maintenance and condition monitoring is a project by Victorian Power Networks (VPN) and United Energy (UE) which saw the development of a digital twin using LiDAR data to help with vegetation management of their electricity infrastructure.
VPN and UE own and operate large electricity distribution networks, totalling over 850,000 poles and more than 800,000km of powerline. The energy networks are also responsible for complying with strict regulations, requiring innovative and cost-effective safety solutions for maintaining network infrastructure.
To do this, the companies launched a LiDAR Lab to use digital twin technology as a surveillance method, measuring the distance to a target by illuminating the target with a pulsed laser light, and measuring the reflected pulses with a sensor, to create a digital model of the terrain.
The digital mapping allowed the networks to measure the distance between vegetation and powerlines to within 10cm. As vegetation-topowerline proximity poses significant bushfire risks, the ability to closely monitor these distances affords the networks an important level of infrastructure safety.
It then used LiDAR to develop a digital twin of the entire network for asset management-related activities, such as determining the clearance between the conductors and the ground – a process that is currently done manually.
FUTURE-BOUND ASSET MANAGEMENT
Despite some potential challenges, digital twins are being dubbed by experts as one of the most imperative strategic technologies for businesses and governments, particularly within construction and asset management.
Dr Samad Sepasgozar from UNSW Built Environment said the digital twin is “not a pipedream, but the next frontier of construction management”.
“At the strategic level, the digital twin is a new game-changing approach to construction automation … that will transform the industry quicker than ever before,” Dr Sepasgozar said.
Digital twins have already been adopted by factories and manufacturing industries, automotive companies, aerospace engineers, local governments and councils, as well as the utility, energy and healthcare industries.
Digital twins are expected to unlock new collaboration opportunities among physical world product experts and data scientists in the future, as well as enhancing customer experiences and improving products, operations and services.
INFRASTRUCTURE-BASED SENSOR TECHNOLOGY FOR "COOPERATIVE AWARENESS" PROJECTS
As part of V2X (C-ITS) projects, or when preparing roads for autonomous vehicles, it is necessary to gather data on all road users (cyclists, pedestrians, etc.) in the transport infrastructure.
SICK Sensor Intelligence offers a uniquely broad portfolio of 2D and 3D LiDAR sensors for this purpose that are suitable for harsh outdoor applications. The outdoorScan3 safety laser sensor is the world’s first 2D LiDAR safety sensor to be approved for outdoor environments and is certified in accordance with ISO 13849-1 and standard IEC 62998.
The outdoorScan3 safety laser scanner is designed to allow man and machine to work safely side by side, and thanks to its patented safeHDDM® technology and intelligent algorithms, disruptive weather influences such as rain, snow, sunlight and fog are filtered out with ease. As a result, it offers limitless potential for increasing business productivity and efficiency, both indoors and outdoors.
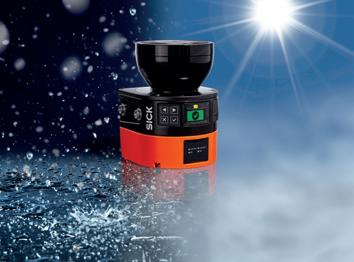

INCREASING SAFETY ON CONSTRUCTION SITES
From basic safety mat replacement and presence detection, through to protecting multiple hazardous areas at the same time, the outdoorScan3 is the ideal choice. Suitable horizontal protective fields can be set up and monitored to protect against the dangers posed by hazardous machines, plants or open spaces.
Radar technology-based sensors from SICK can also be used for similar applications. The MRS1000 multi-layer 3D LiDAR sensor detects and measures objects in multiple dimensions. By collecting large volumes of data on multiple scan layers and from different angles, it can detect and respond to objects on the floor as well as objects that are obstructing the path.
On construction sites, excavators often collide with objects while maneuvering or reversing due to reduced visibility around the rear of the vehicle. The driver assistance system’s sensors must be able to classify objects and their relevance to the collision warning system. The MRS1000 3D LiDAR sensor features an IP67 enclosure and detects up to 55,000 measuring points across four layers, enabling it to recognise objects standing on the floor or located in the vehicle’s travel path in plenty of time. Cutting-edge HDDM+ technology with multi-echo evaluation guarantees precise measurements, regardless of the weather conditions.
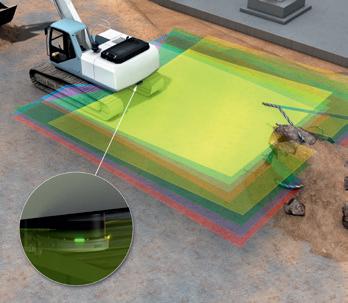
AIRPORT AUTOMATION
High personnel and operational costs necessitate a higher degree of automation in airports, for example, through the automated docking and undocking of passenger boarding bridges. With the outdoorScan3, fast and smooth connection and disconnection can be achieved under extreme weather conditions on the runway. The safety laser scanner also ensures the safety of people in the vicinity whenever the boarding bridge drive unit is moving.

DATA ACQUISITION FOR TRANSPORT APPLICATIONS
Modern traffic management on road, rail and sea routes is geared towards safety, efficiency and a good environmental balance. Rugged sensor solutions provide reliable control and monitoring systems for transportation applications. With solutions from SICK, you rely on many years of experience indoors and outdoors. Laser measurement systems classify vehicles as part of the road toll system, automation light grids reliably detect people at train door systems, and dust measuring devices and gas analysers measure pollutant concentrations in tunnel areas.
The wide range of rugged and innovative products combined with a worldwide service and sales structure has made SICK a market and technology leader in many fields of data acquisition in traffic engineering.
Railway solutions Implement radio frequency identification (RFID) on railroads
Why tagging each train wagon with on-metal UHF RFID tags and mounting RFID long-range readers at the WTMS? The additional information of the unique RFID tag will enable a link between the critical measured values (detected failure) and the specific vehicle, wheel set, axle, brake, and suspension. Using RFID allows you to know in advance the specific part that requires rework. RFID also provides the following benefits: Reducing maintenance costs; Reducing high-cost emergency maintenance; Better planning due to real-time information about the vehicle’s condition; and Higher availability of rail vehicles and better reliability during operation. For more information, please visit: www.sick.com/au/en
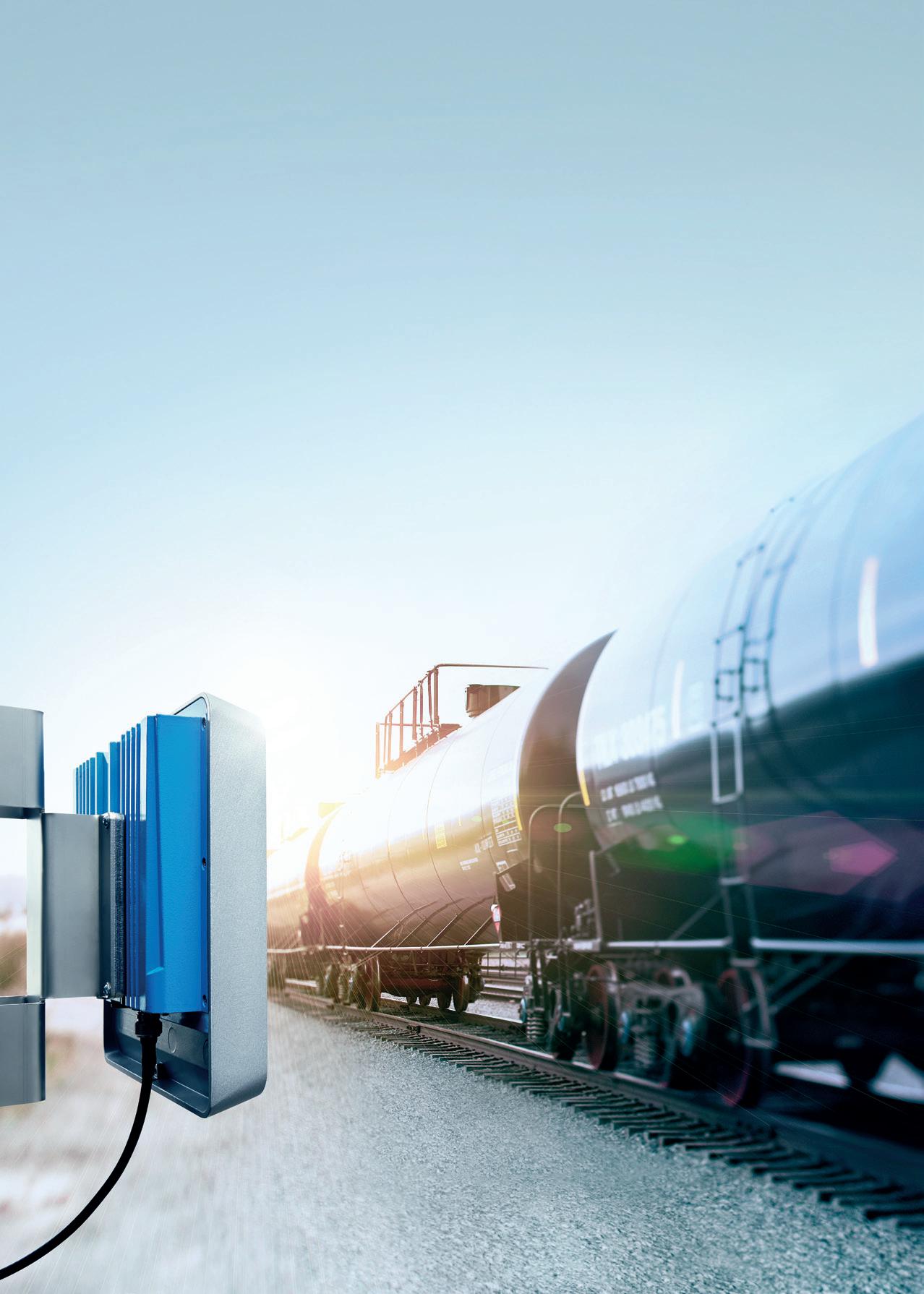
CREATING AUSTRALIA'S FIRST SMART AIRPORT

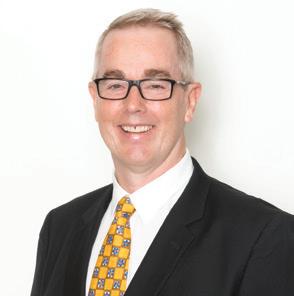
by Tom McCormack, Chief Technology Officer, Western Sydney Airport
As technology continues to influence and shape every aspect of our day to day lives, airports have yet to fully leverage this emerging capability of technology to deliver a seamless and stress-free travel experience.

Over the last 20 to 30 years, airport operations remained largely unchanged – largely reliant on segregated technology systems and manual processes managed by in-person interaction. This has made it harder to respond to changing resource needs and increased strain during peak periods.
In recent years, small evolutionary changes to improve and simplify passenger flow through a terminal have started to become standard practice. Self-service check-in and baggage drops at automated kiosks are commonplace. More recently, upgrades to security and passenger screening queueing ahead of departure are becoming more common and upon arrival in Australia, e-gates for immigration are a welcome change.
As we are designing Western Sydney International (Nancy-Bird Walton) Airport, we’re thinking beyond these discrete systems upgrades and considering how tomorrow’s technology will come together with great design and customer service to create a stress-free experience for our customers.
GLOBAL CHALLENGES OF AIR TRAVEL
From the moment passengers arrive, through check-in, security and immigration to the boarding gate, we want every stage to be fast and easy.
Throughout an airport, there are more than 100 technology systems, ranging from baggage handling to airside access, building utilities to aircraft apron management, and customer information to freight management. In a smart airport, these systems must communicate and work together effectively from your front door to the aerobridge.
A 2019 survey of more than 1,000 Brits found that the single most stressful part of air travel was getting to the airport (63 per cent), followed by baggage collection (49 per cent), and passing through security and waiting for transfers (47 per cent).
Australian airports are prone to the same concerns. We all know the delight of the captain’s announcement upon landing that you are ten minutes ahead of schedule, only to discover there is no operator available to connect the aerobridge to the aircraft. The desperation of the connecting flight dash between terminals, only to discover the flight has moved gates. These situations are frustrating and unnecessary. That’s why we are putting ourselves in our passengers’ shoes, and taking advantage of the latest technology, so we can build the best airport possible.
AN INTEGRATED TRANSPORT JOURNEY
Western Sydney Airport is focused on designing and delivering a fit-for-purpose airport, digitally enabled at the terminal, for our passengers and airline customers. What if we could identify you as a passenger even before you arrived, and you could place your bag on a conveyor belt, and walk through
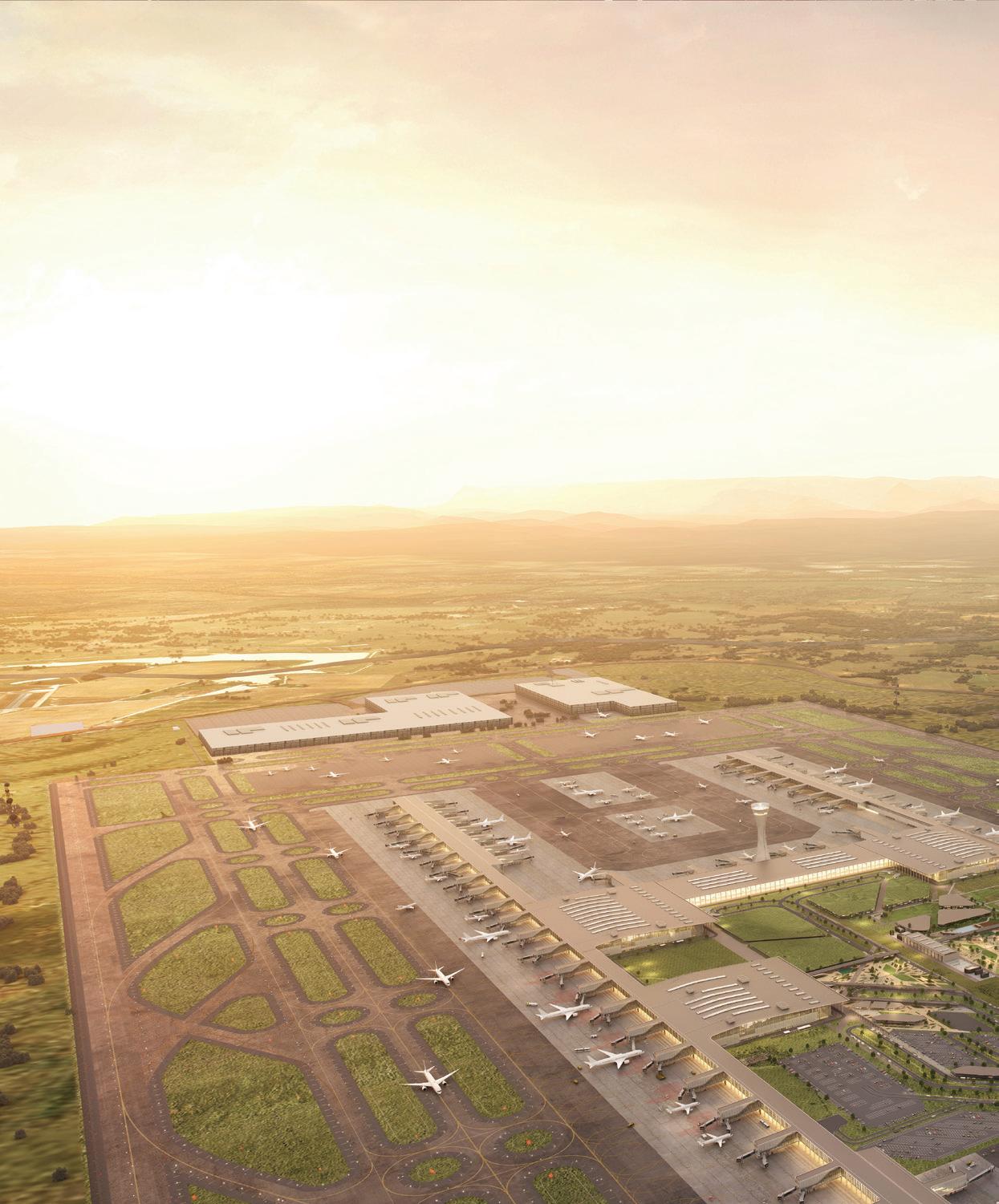
passenger screening without breaking your stride? You could be identified through digital means and smart devices, and be placed safely with other passengers on your flight with ease. Upon arrival, your bag would be returned to you with precision, or could be easily transported to the office, your home or hotel for your convenience on a dedicated service.
On the landside, we are closely collaborating with Transport for NSW, Sydney Metro, Australian federal law enforcement agencies, the Department of Agriculture and a range of other organisations to deliver tightly integrated transport and logistical access for both customers and cargo.
Two new Sydney Metro train stations at the Airport Terminal and Airport Business Park, and integration with the new M12 motorway into and out of the airport precinct, will ensure passenger and freight arrival alike will be fast, more accurate and reliable from kerbside to the plane, safely, seamlessly and stress free.
While we are still early in the design journey, safety, privacy and security is front of mind. The requirements of running a smart and modern airport in a heavily regulated industry are complex. Compliance with federal and state legislation is necessary, and while there’s a lot of work ahead, our team is committed to delivering the people of Western Sydney a game-changing airport that we can all be proud of.
PREPARING FOR A POST-COVID REALITY
A smart airport for passengers and their families means a better passenger journey, a consistent service, real-time information and getting you where you need to go safely. For airlines, efficient and smooth turnaround of aircraft is crucial to maximise asset usage, build profitable routes and demonstrate value for money.
According to IATA’s 20-year global forecast, while the aviation industry is resetting in a post COVID-19 reality, there will be 2.8 billion more passengers per year by 2039. Opening in 2026, Western Sydney International stands ready as the full-service airport of choice for international, ultra-long haul and domestic travel on full-service airlines and low-cost carriers.
Within 20 years, one in two Sydneysiders will call Western Sydney home, and demand for passenger journeys in the Sydney region alone will more than double from 40 to 87 million. Coupled with the power of technology to deliver a seamless, stress free travel experience – Western Sydney International will be the smart choice.
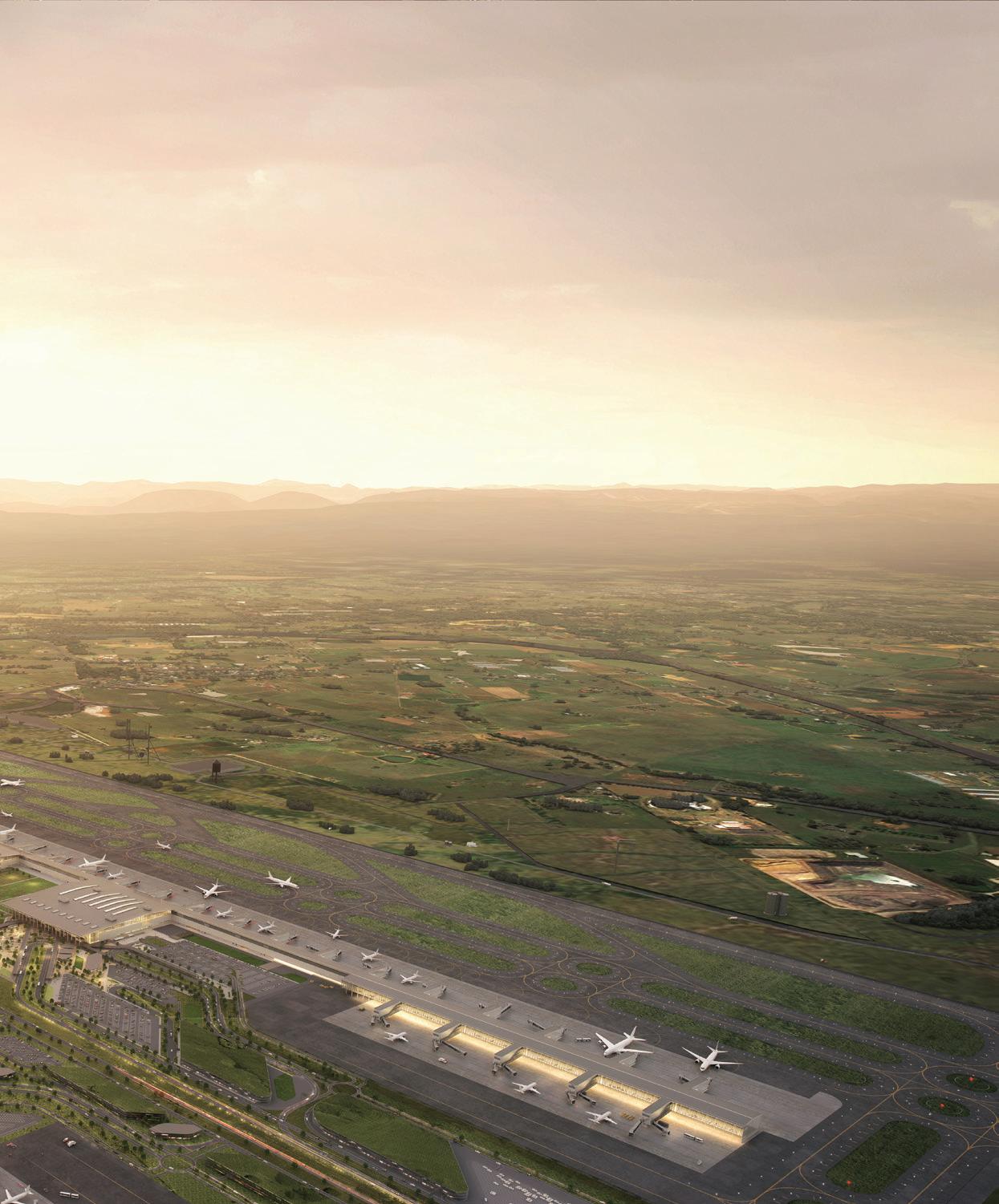
THE DIGITAL TECHNOLOGIES OPTIMISING CONSTRUCTION IN 2021
Recent supply chain challenges caused by COVID have increased costs for major construction projects, creating an urgent need for companies to utilise faster and more efficient ways of building. Some of the new and innovative digital transformation technologies that can help optimise construction include BIM, modular construction, additive manufacturing, big data, augmented reality, robotics, IoT and virtual twins.
In order to keep up with increasing demand, Australia’s construction industry can no longer rely on labour intensive 2D methods to support construction, as they run the risk of creating unnecessary design transactions, or can lack the information consistency needed on projects.
Virtual twins and 3D modelling on the other hand can improve manufacturing and construction efficiency and speed up processes. A virtual simulation of a construction project can identify any potential issues or risks companies might face in the field. These risks can be fixed or mitigated before construction begins, avoiding costly delays. 3D processes can be used in every step of a project’s lifecycle; from design and construction, through to operations and maintenance.
In the recent series of webinars Smart Construction Rendez-vous, run by global leader in 3D design and engineering software Dassault Systèmes, Global Strategic Business Development Director, Prashanth Mysore, outlined the construction simulation technologies that can help accelerate projects, increase construction predictability and improve long-term value for project owners as well as profitability for project contributors.
“Our experience says that 80-85 per cent of project challenges occur in the execution/construction side, compared to 10-15 per cent during planning, so there is an opportunity for construction companies to take advantage of the benefits of emerging technologies like smart construction,” Mr Mysore said.

“It is expected there will be a wider use of technology in construction and construction management in the future, as companies realise the long-term benefits on productivity, efficiency and cost savings.”
SMART CONSTRUCTION AND SIMULATION TECHNOLOGIES ACCELERATING PROJECTS Building information modelling (BIM)
BIM creates a digital prototype of an actual building or asset before it’s built. This enables the consolidation of information relating to the design, simulation, project management and construction functionality. All stakeholders – designers, contractors, suppliers etc. – can access the latest update of the project in 3D, allowing for faster decision-making between all participants collaborating on a single project.
Dassault Systèmes’ 3DEXPERIENCE platform is essentially a unified digital cockpit that monitors construction execution so companies can make informed decisions. It can connect and collect data from machines, equipment and facilities on construction sites, enabling managers to dramatically improve construction performance by accelerating identification of errors and subsequently fixing errors using collected real-time data.
It is a true virtual twin experience model, monitoring live and capturing data that can be used later in operations and maintenance phases. The platform is a lifecycle management system so it not only includes 3D models, but also the project information, simulations and all of the project data in one single source.
Modular construction with 5D
Modular construction is best practice for the manufacturing industry and involves constructing sections off-site then delivering to the location. The 5D methodology for modular construction is essentially an integrated simulation of 3D plus time plus cost. It involves the simultaneous process of creating models while the site work is occurring, with the basis of prefabricated construction being the initial design in 3D. BIM is also used to ensure suitability of the location and the design requirements. Modular construction allows developers and contractors to deliver shorter timelines with less risk, with techniques reducing the length of construction schedule by up to 50 per cent.
3D printing/additive manufacturing
3D printing, also known as additive manufacturing, is currently gaining traction in the industry as it allows you to create construction components or modular parts of buildings. Construction is well suited for 3D printing as the information needed to create a part already exists in the 3D BIM design. It allows for faster and more accurate construction of complex or bespoke items, lowering labour costs and producing less waste.
Big data and predictive analytics
Big data can support fast, accurate decision-making from multiple data sources in real time, making construction sites smarter and improving productivity. For example, when it comes to maintenance and operations, 3D contextualisation of IoT data can help identify specific issues on-site.
Using in-built machine learning algorithms, data scientists can identify a piece of equipment that is causing a maintenance issue. The maintenance log inside Dassault Systèmes’ 3DEXPERIENCE platform helps to identify particular equipment that is causing production stoppages, with the data able to be compared with sensor and historical data. With in-built machine learning and AI algorithms, companies can pre-emptively identify issues with various equipment within maintenance and operations phases.
Augmented reality and VR
Mr Mysore said for an industry that has been notoriously slow to accept technology changes, construction is actually an early adopter of two of the most advanced technologies in existence – augmented reality (AR) and virtual reality (VR). These technologies can visualise blueprints, maximise efficiency and improve workplace health and safety.
VR is used by developers to review real 3D environments of architectural designs. By using a combination of BIM and immersive VR headsets, architects, project managers, civil engineers and the whole project team can identify design flaws and better plan construction projects before they begin. AR is used by project managers on-site to ensure a structure is being built exactly as the design intended, rather than just using line of sight to confirm. This significantly speeds up projects and minimises errors.
Autonomous construction
Autonomous construction is the use of advanced robotics to replace or improve existing processes, making them more efficient and accurate. Mr Mysore said robotics aren’t playing a huge role in construction right now but this will soon change, so companies should get on board early. With the industry facing increasing pressure to construct quickly and in a more reliable and safer way, this is where robots can be useful.
IIoT and execution monitoring
IoT plays an important role as it can connect sites, enhance safety, reduce accidents and improve work processes. Sensors connected to the internet can continuously monitor and manage critical resources at construction sites such as electrical systems and various mobile resources in real time. IoT is commonly used to monitor machines around the site and track progress of work. Sensors mounted on construction equipment and safety hats worn by construction professionals also help optimise the utilisation of manpower and physical assets.
As illustrated, there are a number of constantly evolving technologies available to construction companies and by using smart and lean construction methods, companies can become more flexible and agile, and better prepared for future disruptions they may face.
For more information on these technologies and Dassault’s 3DEXPERIENCE platform, please visit https://ifwe.3ds.com/construction-cities-territories.
INTELLIGENT TRANSPORT SYSTEMS: A REVOLUTION ON OUR ROADS
by Michelle Goldsmith, Journalist, Infrastructure magazine Across Australia and around the globe, Intelligent Transport Systems (ITS) are already making road travel safer, more efficient and more sustainable. Such systems are only becoming more and more relevant as population grows and the number of vehicles on the roads increases, with various ITS technologies offering solutions to decrease congestion, increase efficiency and mobility, and even save lives.
Fundamentally, ITS involve integrating information and communication technologies into transport systems to optimise operations. ITS encompass a broad range of systems and technologies, with varying levels of complexity and automation. While smart systems can be applied to any form of transport, the term ITS is most frequently used in reference to road transport.
The ‘currency’ of any ITS is its data, which is used to improve the transport system’s operations, often in real time. As such, ITS employ a variety of wired or wireless technologies to collect, transmit, communicate and interpret data, with many also including automated control functions. ITS infrastructure may involve technologies integrated into road networks (e.g. roadside sensors), within the vehicles themselves, or both. Essentially, ITS enhances connections between road users, vehicles, road infrastructure and transport system operators.
ITS solutions are generally applied to do one or more of the following: ♦ Improve the mobility of people or goods ♦ Increase safety ♦ Reduce traffic congestion and increase transport efficiency ♦ Inform road users of conditions ♦ Respond effectively to incidents and emergencies ♦ Increase the resiliency of the transport system in case of changed conditions or unforeseen disruptions ♦ Reduce air pollution or improve energy efficiency ♦ Automate billing processes ♦ Achieve policy objectives (such as demand management or transport priority) ITS INFRASTRUCTURE IN ACTION
ITS fulfill various vital functions on our roads, reaping significant benefits for road users and operators, as well as for our broader society and economy.
Traffic management
ITS traffic management is concerned with the overall management of traffic on a road. The ITS detects traffic situations and deploys traffic control strategies. Technology is applied to traffic signalling systems, traffic safety, and route and congestion management.
For example, the busiest roads around Melbourne, including the M80 Ring Road, Tullamarine, West Gate and Monash freeways, Eastlink and Citylink, use coordinated dynamic ramp metering to measure and regulate the number of vehicles entering and exiting in real time. This enables each road to handle the maximum number of vehicles while maintaining traffic flow, reducing travel times and preventing safety issues associated with congestion.
Controlling traffic signals to only allow a certain number of vehicles to merge onto a road at a time helps break up groups of vehicles that might otherwise be competing for space, reducing the likelihood of collisions. Ramp metering signals that become operational during peak times have also been deployed as part of Sydney’s $600 million M4 Smart Motorway project.
Similarly, ITS such as the Sydney Coordinated Adaptive Traffic System (SCATS) employ in-pavement detectors and other sensors at busy intersections to monitor demand for right-of-way and shifts in direction of demand. Traffic signals then adapt accordingly, resulting in a smoother flow of traffic and minimising wait times. The SCATS Priority Engine also allows essential
vehicles (such as emergency services) to be prioritised through traffic lights.
In Queensland, Hold the Red, an innovative intersection crash avoidance system trialled at four intersections in Brisbane and the Gold Coast, demonstrates the potential of ITS to prevent traffic incidents and enhance safety. The system uses radar to predict when a vehicle approaching the intersection is going to run a red light. When this occurs, the system extends the all-red phases of lights at the intersection by two seconds, preventing other vehicles or pedestrians from entering the intersection where they could collide with the offending vehicle.
Traveller information
A common function of ITS technology is to better inform road users about road, environment and traffic conditions. These services enable road users to plan the most efficient route, avoid delays and quickly become aware of any changed conditions, potential hazards or emergency situations. For instance, signs may display current travel times or advise of incidents or lane closures, or real-time information about conditions might be conveyed via highway advisory radio or reflected in GPS data.
Real-time traffic information signs and variable message signs are employed on a variety of roads around Australia, while certain busy car parks use parking guidance systems to advise of parking availability. For example, the Parramatta Parking Finder helps support people with accessibility issues by providing information about accessible parking spaces around the Parramatta CBD including photos of the space and a rating out of five for the size of the space, hoist suitability and kerb ramp access.
Some of the potential benefits of ITS integrated with connected and semi-autonomous vehicles have been demonstrated by a trial undertaken by the Victorian Department of Transport on Eastlink, which involved the operational deployment of semi-AVs and cooperative intelligent transport systems (C-ITS). The project developed a DSRC messaging platform that delivered real-time road warnings in a high-speed environment, with high reliability and precision (to location and lane), without interfering with the existing tolling system. Emergency management and response
The real-time monitoring capabilities of ITS can greatly reduce emergency response times, saving lives, preventing secondary incidents and reducing disruptions. For instance, if a collision occurs, the relevant authorities are alerted, and the nearest emergency vehicle is located and dispatched to the scene. Other drivers on the road can be alerted through dynamic signage and signals may change to prevent too many vehicles entering the area of the accident until it is safe to do so.
In South Australia, on the section of the North-South Corridor between Torrens Road and River Torrens, a Thermal Video Incident Detection System detects slowing, stopped or wrong direction vehicles within 5-15 seconds, fast-tracking incident response actions. These include notifying drivers of lane closures and congestion using variable message signs and monitoring the situation with CCTV pan-tilt-zoom cameras.
Meanwhile, the Queensland Police Service employs drones and motorcycles to expedite serious crash scene clearance times, allowing traffic managers to estimate the duration and severity of congestion impacts and use existing ITS technologies to help manage congestion and prevent secondary incidents. Using drone technology to map crash scenes, the Forensic Crash Unit has reduced scene mapping time by 50 per cent, reducing road closure times and traffic congestion, while also improving the quality of evidence captured at scenes.
In Brisbane, a structural health monitoring system has been developed to detect damage to the iconic old Sir Leo Hielscher Bridge (the Gateway Bridge) in real time, before it can affect public safety. These are just some of the ways in which ITS are currently transforming Australian road travel, with much more to come.
As the field of ITS continues to develop rapidly, the deployment of smart systems on our roads can help address significant social, economic and environmental issues. With the costs of congestion predicted to rise to as much as $40 billion by 2030, and over a thousand lives still lost on our roads each year, we cannot afford to miss this opportunity to reap significant benefits at a relatively low cost, leveraging data to revolutionise road transport.
WHAT’S IN STORE FOR THE FUTURE OF DIGITAL TWINS?
The 2020 NSW Spatial Digital Twin is part of the Western Sydney City Deal partnership that brought together federal, state, and local government under a set of 38 commitments. The Digital Twin was part of the project’s commitment to coordinating information that supports planning and broader liveability targets.
»3,396km2 of 3D mesh »Over 1 million images captured »28,500 gigapixels of visual information »Under 6cm pixel resolution
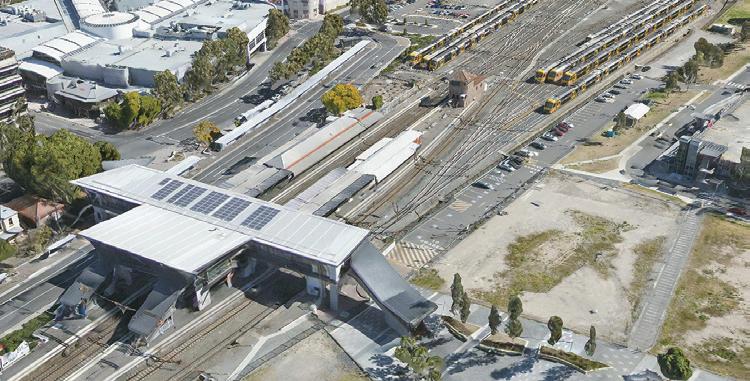
Aerometrex 3D Model of Penrith Station as seen in NSW Spatial Digital Twin.
Data has become its own type of infrastructure, and the NSW Spatial Digital Twin is an asset that will benefit private industries, government, and the public for years. The project has set a standard for how digital twins will be made and used for planning and visualisation.
The NSW Spatial Digital Twin incorporates the largest 3D modelling project ever undertaken, with the final product including 3,396km2 of seamless 3D mesh captured at under 6cm pixel resolution across the greater Western Sydney region.
Key to this endeavour was Australian 3D modelling expert Aerometrex, who captured and processed the necessary 3D data to underpin the NSW Spatial Digital Twin. It spent several months capturing, processing, and combining the imagery.
OPEN SOURCE 3D MESH DATA
What makes the NSW Spatial Digital Twin so remarkable is its open-source presentation, publicly accessible through a browser-based web portal. That foundational information source brings compounding efficiency benefits as government, private industry, and the general public can all refer to a central and consistent data source.
Victor Dominello, the NSW Customer Service Minister, said the high availability of aggregated data will help with planning future development.
“Using the digital twin, we can model where we put the roads, hospitals, schools, etc. with precision planning like we’ve never done before. This is truly transformational technology and the best thing about it is that it’s open source – industry can use it, councils can use it, everybody can get involved and build this asset together for all of us,” Minister Dominello said.
Open source 3D mesh data reduces costs and time frames for infrastructure planning regardless of the project size. Every project stakeholder uses the same validated source, making duplicate data investments unnecessary. 3D visualisation gives all stakeholders a more tangible and dynamic sense of space. Users can see and understand space and how the change will impact it.
COMPLEX POST-PROCESSING TASK
Aerometrex used fixed-wing platforms carrying an array of image sensors to capture an area so large at such high detail. Aeroplanes were the ideal tool for the job, but it’s an intricate task when the busy Sydney Airport is within the capture zone. The post-processing task matched the capture process for complexity and scope. Aerometrex’s team had to turn 1.1 million images, adding up to 28,500 gigapixels of visual data, into usable 3D tiles for Data61 to build into the web portal.
— Rob Clout, 3D Sales Manager, Aerometrex
NSW’s Spatial Digital Twin shows the value in making open source assets. They encourage and accelerate economic activity through centralised and consistent data. The concept of Digital Twins has already progressed past the proof-of-concept phase and to a mature product.
Jurisdictions of all sizes are investing in digital twin asset creation because the returns on investment are substantial. Better spatial data improves the multitudes of activities that involve the alteration of structures and space.