
4 minute read
ROAD MATERIALS UNDER THE MICROSCOPE
by Michelle Goldsmith, Journalist, Infrastructure magazine
The materials used in construction are of vital importance to a road’s safety, performance, maintenance requirements and longevity. They also significantly affect the construction costs of a road project and the total lifecycle cost of the asset. In the first article in a series on road construction materials, Infrastructure takes a closer look at the different layers making up a road and the varying properties required for different applications.
Advertisement
Currently, the majority of Australia’s biggest and most expensive infrastructure projects underway involve constructing or upgrading our roads. According to 2017 estimates, road projects spend around $5.1 million per lane kilometre on average, varying by road class.
The pavement materials contribute significantly to these costs, at an average of $233 per square metre for an urban motorway or freeway, or $114 for a major rural road. Heavily trafficked major roads are the most expensive, while more minor roads with a lower-traffic load tend to be cheaper.
A wide range of materials can be incorporated into roads, with different mixes exhibiting different properties that affect their suitability for various applications and environments. Foremost, the material mixes used for this essential infrastructure must be fit-for-purpose due to the significant implications for the road safety, functionality, longevity, maintenance requirements, and total lifecycle costs.
For any road project, careful consideration of the materials used is required, especially when certain materials are in short supply, or when looking to reduce costs and waste, while optimising infrastructure performance.
MATCHING MATERIAL AND APPLICATION
A variety of factors affect the materials that might be suitable for any given road project. For instance, a heavily trafficked road in a high-rainfall area will have different requirements to a minor local road in a dry area.
Key factors affecting road material suitability include: ♦ The intrinsic physical properties of the material (e.g. structural stability, heat resistance, water permeability) ♦ The intensity of traffic loads ♦ The climate and moisture regime of the environment ♦ The availability of material sources ♦ Budget constraints
The available road materials and their properties have significant implications for the structural design of the pavement and entirety of the road. If suboptimal materials for the application and environment must be used, additional measures will need to be taken to ensure the road meets performance standards. These may include different pavement structures to increase durability, with different material mixes in various layers, or supplementary drainage to limit moisture on the road.
LET’S GET PHYSICAL
Different available materials have different intrinsic properties that will determine their performance in pavement mixes.
Some of the most important physical characteristics of road materials are: ♦ Water permeability ♦ Fines content (the amount of fine soil particles) ♦ Plasticity characteristics (ability to undergo permanent deformation under stress) ♦ Stability ♦ Viscosity ♦ Durability ♦ Toxicity
The relative importance of each of these factors depends on the individual application. Ideally, the more moisture a road will be exposed to, the lower the materials’ water permeability should be to reduce failure risk, and the more important the fines content and plasticity characteristics. Likewise, the higher the traffic load the road will experience, the more stable and durable the materials should be.
A BIG PICTURE UNDERSTANDING OF PAVEMENT
A pavement structure comprises various layers of materials. Each layer spreads the imposed traffic load to the underlying layers, meaning the stress experienced by the materials is
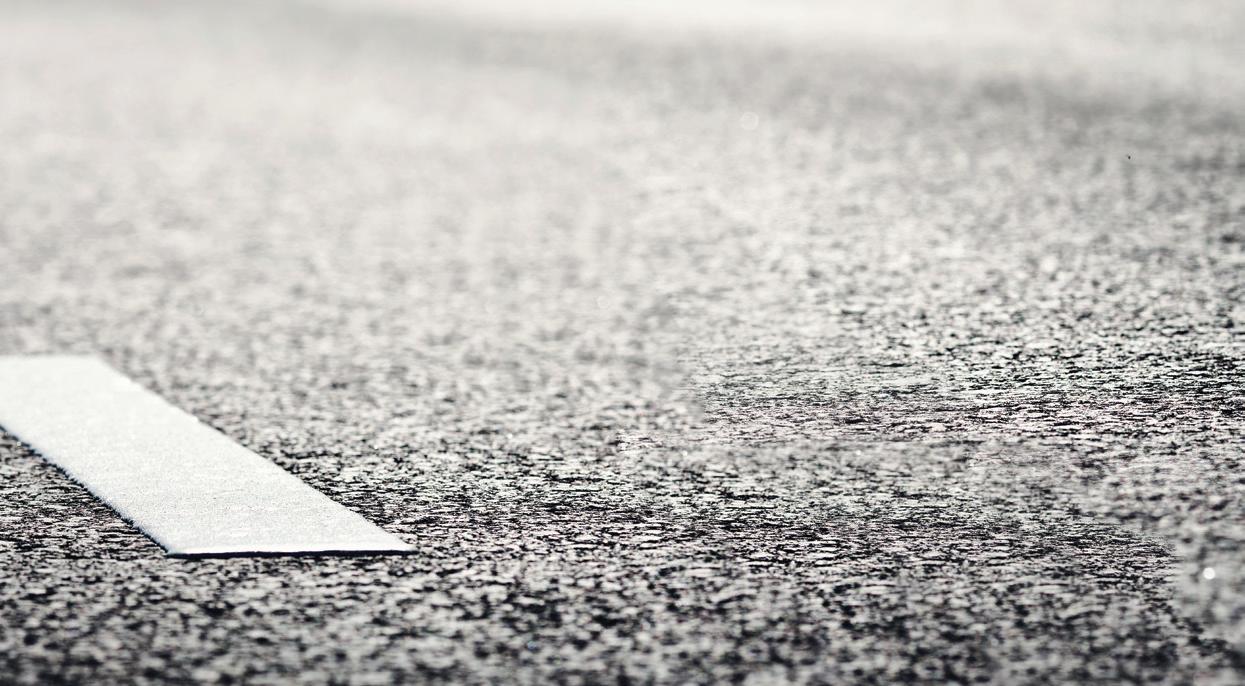
highest at the surface of the road and lowest at the deepest level. As a result, the quality of pavement materials is usually highest at the surface, with quality decreasing by layer as stress is reduced.
A multitude of possible pavement structures are available, incorporating different materials in various mixes in each layer.
The layers can be categorised as: the wearing course (the surface of the road), the basecourse, the subbase, and the subgrade.
Each layer has different requirements, affecting which materials, and in what mix, are suitable.
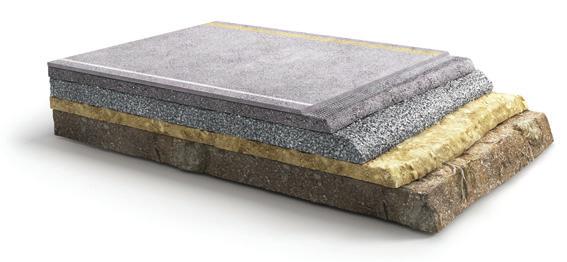
Wearing course
The wearing course, or road surface, experiences the most load stress and exposure to the elements of any pavement layer. It must provide a safe, economical and durable surface in all weather (e.g. not become dangerously slippery when wet) and protect the lower layers from moisture, which could result in damage. Ideally, it should provide a dust-free surface to drive on, reduce vehicle operating and maintenance costs, and extend the lifespan of the overall pavement structure. It is also the visible layer of the road, meaning that its surface characteristics (such as appearance and how it feels to drive on) need to meet community expectations.
Options include: hot mix asphalt, bituminous spray seal, bituminous slurry seal (microsurfacing), and unsealed.
Basecourse
The basecourse provides support to the overlying surface layer and distributes the load to the underlying subbase.
Options include: hot mix asphalt, concrete, unbound granular, modified unbound granular, lightly bound or bound stabilised granular.
Subbase
The subbase provides underlying support to the basecourse and wearing course, and distributes the load to the subgrade layer beneath it.
Options include: concrete, unbound granular, modified unbound granular, and lightly bound or bound stabilised granular.
Subgrade
The subgrade is the bottom layer of the road and provides a foundation for the overlying materials. As such, the strength of the subgrade determines the required thickness of the overlying layers and factors strongly in pavement design considerations.
It is often the in situ material, which has been compacted and prepared to make a formation above the natural surface. Sometimes, stabilisation or modification (such as lime stabilisation) of the subgrade material is undertaken to increase foundation strength.
Options include: in situ granular, and stabilised granular.