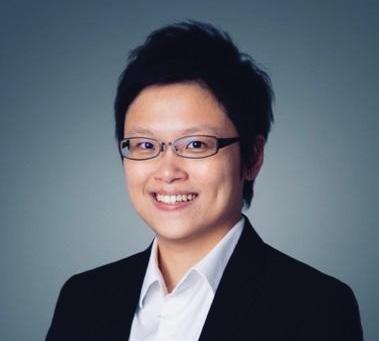
6 minute read
technology innovator – Yi-Chieh Huang
AN OUTSTANDING ADVANCED SEALING
TECHNOLOGY INNOVATOR – YI-CHIEH HUANG
Advertisement
Mechanical seal design and manufacturing company SPE has launched several innovative sealing products for industrial equipment applications. The nuclear, petrochemical, pharmaceutical, mining and wastewater industries in over 40 countries use SPE's products. The company's Chief Operating Officer, Yi-Chieh Huang, is a significant driver behind this success.
Huang holds an MIT Sloan MBA degree and has over 14 years of experience in the machinery manufacturing and sealing technology equipment fields. Huang combines mechanical engineering expertise and business acumen to champion sealing systems’ product development and technology commercialisation of sealing systems for energy industry applications.
Furthermore, Huang has been admitted by several prominent international professional organisations such as the American Petroleum Institute, American Fluid Sealing Association, Taiwan Nuclear Grade Industry Association, Society of Manufacturing Engineers, American Society of Mechanical Engineers, and API-682 standards committee in industrial specification development.
Developing technologies to meet end user needs
During her career, Huang has invented over 30 patented technologies covering over 20 advanced seal designs with comprehensive technology commercialisation. Huang developed high-performance seal products offering excellent reliability and significantly longer mechanical seal mean time between failure (MBTF) for equipment. Huang championed efforts resulting in more than US$3.5 million annual cost savings by improving equipment MTBF.
Further, Huang's team implemented sealing technology upgrades for a chemical plant in China. The facility reduced maintenance costs by $3.6 million within three years, allowing the end user to achieve 40K+ tons of chemical compound production annually.
Huang's R&D team designed the APD-series products for API682 applications for hazardous, flammable and toxic processes requiring a grander scale of a mechanical seal's reliability for improving pump operating life with lower emissions and reduced end user lifecycle sealing costs. They work in various critical operating conditions with a wide temperature range of -40oF to 500oF and pressures up to 570 psi.
For lower rotating equipment electrical consumption, Huang developed CARFB, the first complete cartridge seal design with multi-segment tandem rings. CAR-FB seals are for industrial blower applications operating in temperatures up to 720oF to avoid dry running, prevent toxic gas leakage, and reduce power consumption by over ten per cent. Moreover, Huang's team lowered nitrogen consumption by upgrading a next-generation non-contacting seal with a unique spiral pattern.
For wastewater treatment, Huang's team launched the CL99SS series seals with over 35 per cent part interchangeability for five to 35 per cent of suspended particle-containing slurries, including sulfur dioxide leakage reduction and plant spare parts inventory by about 50 per cent when over 70 per cent of the pumps have the CL seal line of products installed. The CL series products handle short periods of dry running and eliminate the need for a complicated piping system, reducing water consumption. Also, CL series seals can align shaft misalignment for up to +/-0.5mm and extend MTBF by at least 50 per cent.
Responding to new government policies
In response to new government ecological policies, Huang's team reduced equipment Volatile Organic Compound (VOC) emissions below 500 ppm on average and less than 50 ppm in specific sealing technology. Typically, dual seal buffer pressure is at least 40 psi higher than the process, requiring an external resource and increasing energy consumption. Huang's LD series invention requires under 30 psi because of its automatic balancing structure with high sealing performance. This technology greatly improves the sealing heat exchange rate. It has a 15 per cent higher recirculation efficiency than the average dual cartridge seal, increasing the pump's operating reliability by at least 20 per cent, saving about 25 per cent maintenance time.
In summary, Huang contributed many extraordinary dynamic fluid sealing sector innovations, making industrial environments better. "I am enthusiastic about providing a technical solution for various market segments according to market demands. We demonstrated SPE's technical strength by innovating and leading industrial sealing trends and thereby improving industrial environments. Our clients' needs always inspire us to create meaningful innovation," Huang said.
Going deeper underground:
world-first layflat hose technology for mine dewatering
Accounting for around 98 per cent of Australia's Economic Demonstrated Resources (EDR) of iron ore (about 28 billion tonnes) and as the largest supplier to the global seaborne iron ore trade, the iron ore mines in the Pilbara region of Western Australia are a leading powerhouse for the Australian economy. These mines are at the forefront of best practice for efficiency and safety, and – along with other Australian mines as a whole – are highly rated across the world for their skilled processing and ore extraction techniques. Crusader Hose, an innovative Australian manufacturer, has produced a world-first flexible rising main for ultra-deep bores – Flexibore® 400 – to help support Australia’s mining industry remain world-class.
Crusader Hose, a Melbourne-based company with over 35 years in manufacturing layflat hose, has a strong connection with the mining, pump and drilling industries, having built relationships with players in these sectors over many years through industry networks, site visits and trade shows. As a result, Francois Steverlynck, the Managing Director for 30 years, understands the importance of water extraction in mining operations. Submersible pump securely
“Mines are extending attached to Flexibore hose and digging deeper, and ready for installation. are, therefore, reliant on water transfer systems which can handle the greater pressures at these deeper depths,” Francois said. Power cable securely snaked along the Flexibore hose
160kW pump and power cable on truck.
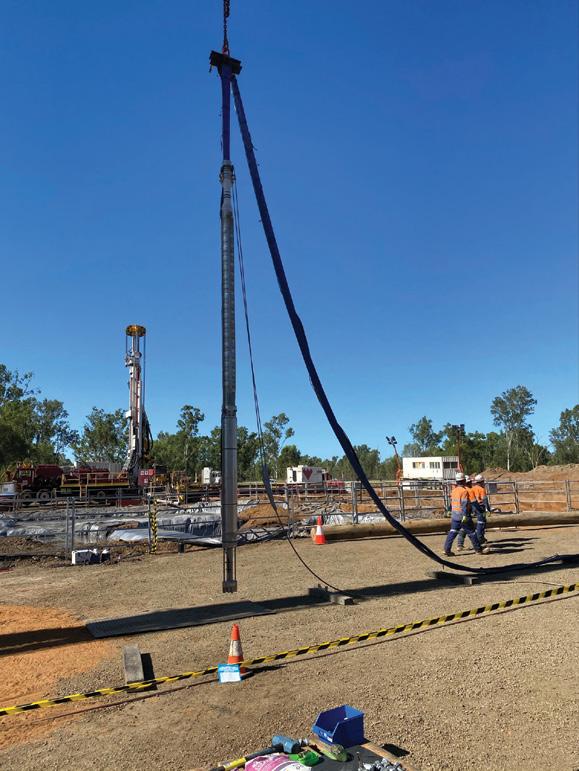
A recent breakthrough by the Research and Development Team has been the development of ultra-high-pressure hose for the extraction of bore water.
Several years in the making, this breakthrough was made possible by a series of upgrades along the manufacturing chain.
Apart from loom modifications, the polyester fibre used in weaving the textile reinforcement is of a higher calibre than what is used in lower-pressure Flexibore® products; the tenacity of these higher-calibre fibres is unparalleled.
The $1 million investment in a new extruder system has brought world-class quality to this very important process. As a result, the Flexibore® 400 series hose is the highest pressure layflat hose in the world for groundwater pumping, boasting a burst pressure of 100 bar or 1000m. Groundwater now can be safely pumped from 400m below.
Committed to supporting mining operations

Crusader Hose is committed to supporting mining and the Australian economy by investing in technology to design and manufacture world-class hose systems for both vertical and horizontal dewatering.
“Flexible rising mains such as Flexibore®, have been the system of choice for many Australian mines for in-pit bores due to the simplicity with which the submersible pumps can be retrieved and installed,” said Francois.
The typical installation method uses a roller, crane or mechanised spool, as the riser pipe is one continuous length. In the most recent installation, after the 380m of hose was laid out and power cables were attached, the 160kW pump was lifted by a crane then lowered 15-25m at a time by repositioning the lifting clamps along the hose. This system has proved to be less time-consuming and arduous than using steel or fibreglass pipe.
“The Flexibore® 400 is a pioneering achievement in the history of our company, which we believe is a world first,” said Francois.
“This Australian development will hopefully be keenly adopted by more mining companies, to enable them to keep at the forefront of productivity and profitability.”
www.pumpindustry.com.au
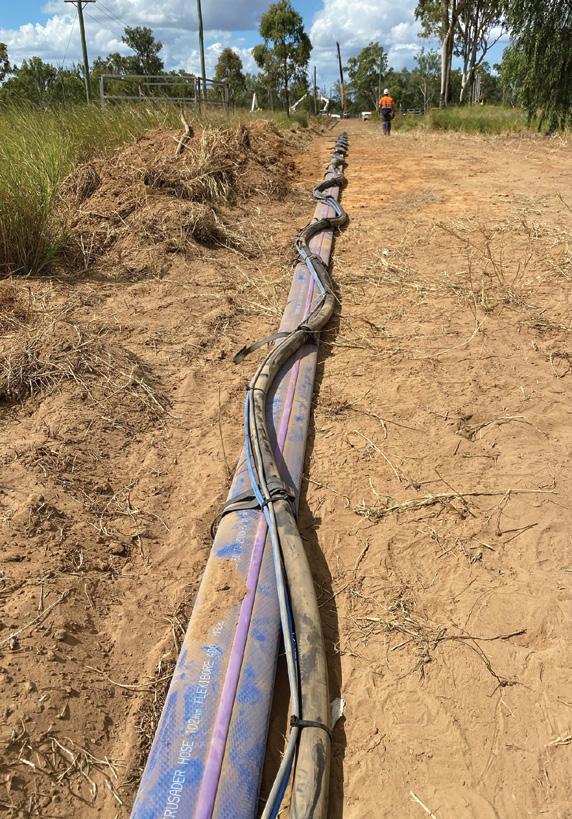