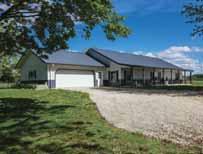
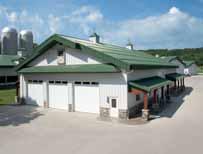
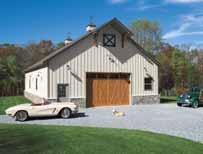
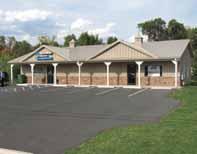
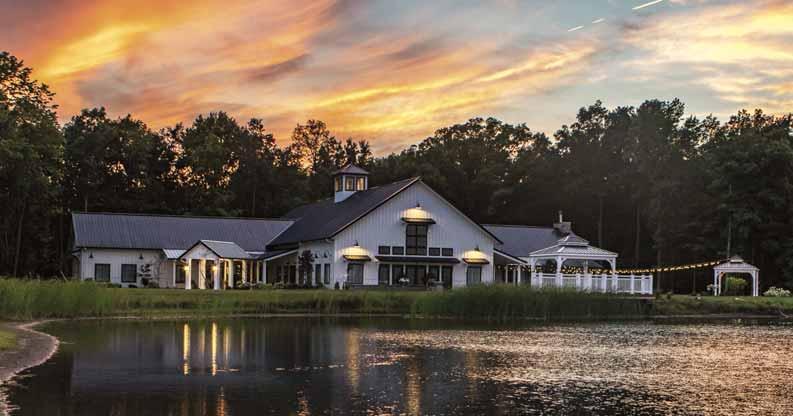
Post-frame refers to a highly engineered wood-frame building system that meets UBC and IBC standards. Post-frame buildings feature large, laminated columns instead of wood studs or poles, steel framing, or concrete masonry. This type of framing system delivers superior longevity and performance than other building types in various climate or soil conditions.
Professional engineers agree that contemporary post-frame buildings are highly engineered and structurally sound for many reasons:
• Superior strength: The exclusive concrete Morton Foundation System™ removes wood from the ground and replaces it with specially designed components and superior materials
• Post-frame buildings transfer load through their columns, typically embedded in the ground or surfacemounted to concrete, allowing the structure to perform well under seismic loading conditions
• Flexibility in design—for example, truss to column attachment options can be customized to your load requirements and climate conditions
Offices. Barns. Homes. Country clubs. Garages. Hobby shops. Post-frame is more versatile than other types of construction because:
• Exterior finishes are almost limitless
• Inside, your layout is completely up to you—since post-frame buildings need no interior support walls, you put as many or as few walls wherever you like.
Insulated post-frame buildings are more efficient than other types of structures. Additionally, Morton offers ways to make your energy dollar stretch even further with the Energy Performer® insulation system.
This type of construction is efficient in many ways. First, you can begin any time of year. Once you begin, the amount of time it takes to get “under roof” for a post-frame building is approximately half what you would normally expect from other construction techniques.
Quick to build. Virtually maintenancefree. Energy saving. Long lasting. Between efficiency in building and efficiency in owning, your decision to build post-frame has both shortand long-term value.
From the smallest fastener to the trusses overhead, Morton leaves absolutely no detail to chance. It’s the only way to ensure you end up with a high-quality, better-looking building that stands the test of time.
Exceptional quality is the hallmark of a Morton. We’re only as good as our materials so we take full control of the entire process. We source and manufacture our own materials. We roll form our own steel, build our own trusses, and so much more. Morton operates seven manufacturing facilities where many of our building components are produced and loaded on our trucks to deliver to your job site. Our vertical integration allows us to provide you the best quality, timeliness and value for your building project.
The difference between a good building and a great building is craftsmanship. Regardless of the materials, a building is only as good as the people who construct it. At Morton, we are true craftsmen, and we strive to build structures that exceed your expectations. All of our crews are full-time and only construct our buildings. These are seasoned professionals who make a career at Morton and participate in continuous training.
Morton offers the most comprehensive warranty coverage in the industry. Our warranty claims are handled in-house, are not passed through to another supplier, and include labor and Morton materials.
We want your building to be one you are proud to show off and pass down to future generations. As a 100% employee-owned company, we are all committed to be the industry leader with a focus on innovation, service, quality, and most importantly, making sure each customer is completely satisfied with their decision to build Morton.
“With their guarantee, their timeliness and their expertise, I don’t think there’s a better building on the market.”
– David M. • Manito, IL“This is my second Morton building. My experience and satisfaction with my first building is why I didn't or wouldn't consider any other brand of building. My first building is 18 years old now and the new building color matches. They look like they were put up at the same time.”
-Dale S. • Denison, IA
Your Morton sales consultant is supported by the full Morton team.
We manufacture our own materials at seven plants throughout the U.S. to make certain we bring you the highest quality available. For example, when your trusses are being built, it’s possible they’ll be part of an inspection by the Truss Plate Institute, a third party quality assurance agency. Nothing gets loaded onto a Morton truck and makes its way to your property until we know it’s the right fit for your job.
Your sales consultant works for Morton until you make a down payment. Then he or she works for you, guiding the entire building process:
• Arranging pre-build details, like concept development, building plans and quotes, site plan, permits and zoning details, budgeting and financing
• Coordination of subcontractors, as needed
The architectural and engineering experts at Allied Design Architectural & Engineering Group, P.C., are an extension of our team, as they have been for many years. Their designs ensure your space is functional, energy-efficient and able to withstand your specific geography and climate conditions.
Delivery is an afterthought for many manufacturers, but we wouldn’t send your precious cargo with just anyone. Morton employees personally deliver your building materials on Morton-owned trucks. That’s how we know the components will arrive safely, on time and be unloaded with the care your building deserves.
• Overseeing each stage of construction and communicating with you throughout
• Extending the partnership after completion by checking on your satisfaction and honoring service needs and warranty issues
They’re not construction workers; they’re professional craftsmen, trained specifically in the art of erecting Morton buildings. Crew foremen have an average of 15 years of employment with our company.
Warranties are an important part of our team. They’re handled directly by Morton. And, since the strength of a warranty is only as good as the strength of the company, you can have confidence that our 120 year old company will be here to stand behind your Morton building.
The difference between a good building and a great building is not only how it functions today, but how it looks, performs and functions years from now. Morton buildings age gracefully because we use quality products and sound construction methods to ensure you have a building you can be proud to own.
Building Types
Farm Shop & Storage
Livestock Facilities
Equestrian
Garage & Hobby Building
Home & Cabin
Retail & Restaurant
Office & Warehouse
Church & Activity Centers
Childcare
Animal Services
Winery, Brewery & Distillery
Fire Station & Municipal
Airplane Hangar
Mini-Storage
Automotive
Roof pitch measures the slope of your roof, indicating how many inches the roof rises for every 12 inches it runs horizontally. For example, a 4/12 pitch means that the roof rises 4" for every 12" it runs. Choose pitch to match or complement other buildings on your property.
4/12 PITCH6/12 PITCH8/12 PITCH10/12 PITCH12/12 PITCH
There’s a Morton Advantage at Every Step.
Gable Steeper Pitch Gable Gambrel Monitor Gable Hip with Gable Open End Porch Lean-To Wrap Around Corner Porch Exposed Truss Dutch Hip Dormer Cupola Turkey Tail Eyebrow Deep Facia Step Facia 4"Morton Buildings foundation options offer strength and dependability for your building. Morton uses ready-mix footings, not concrete cookies which can shift over time. Morton also digs deeper. Using digger trucks, crews are able to set stilts and columns deeper into the ground, providing more stability to your building’s foundation. With a variety of foundation options available, your sales consultant can help you choose the one that best fits your soil type, building codes and building use.
• Good solution in rocky, difficult-to-dig soils
• Works well with poured concrete floor
• Thickened edge meets heavy load requirements
• Ready-mix concrete with reinforcement
• Column sockets anchored to ½" x 10" plated concrete anchor bolts or adhesive anchors
• Laminated column bolted in column socket
• Pre-cast concrete lower column* and optional DuraPlank® upgrade removes all structural wood from contact with the ground
• Concrete strength 2.5 times greater than a typical concrete foundation wall and footing system
• Safe and strong in all weather conditions
• Manufactured in a controlled setting for greater reliability and super performance
• Precast columns eliminate wait time for concrete to develop adequate strength
• Internal threaded adjustment bracket
*Not available on all building styles.
Premium Upgrade (optional)
DuraPlank®, the new patented, optional concrete splashboard is an affordable upgrade to MFS that eliminates all structural wood from contacting the ground for added durability and aesthetics of your structure.
A
Wood Splashboard (standard)
The wood splashboard is a standard feature with the MFS.
Go behind the walls of your building and you’ll see that both our building materials and construction process surpass industry standards.
1 Laminated columns hydraulically compressed during lamination stronger than solid posts of the same dimension
• Using 3-ply lower columns vs. 6 " x 6" solid post
- Laminating provides a straighter, stronger column
- 100% penetration of sapwood treatment which cannot be obtained with square posts because they are treated on the outside only
- Protects against fungal decay and insect infestation
- Preservative = .60 pounds per cubic foot
- Splices staggered for consistent strength
- Lamination gives us ability to add column stiffeners and/or increase dimensional size of lumber for high demand situations (high wind, grade to eaves height greater than 16 ft., etc.)
- All columns fastened with stainless steel, deformed shank anchor nails to secure boards together, even under stress
2 Morton Foundation System™ uses a concrete lower column in the ground
• Morton treats all other wood that comes in contact with the ground
• Splashboards are treated with .15 pounds per cubic foot of preservative
3 Nailers—end wall and side wall nailers made from No. 2 or better visual grade or Machine Stress Rated (MSR) lumber
• 2" x 4" or 2" x 6" depending on your truss and column spacing
• “L” nailers for 12" OC
• Nailers are fastened using ring shank nails appropriate for the design specifications of your building
• MSR lumber has been evaluated by mechanical stress-rating equipment for stiffness, which then determines the lumber’s strength.
• Staggered for strength
4 Specially engineered trusses are densely webbed and centered over each column to increase strength and longevity
• Eliminates the need for knee braces
• Truss heel is 15 ½" high, allowing for a stronger connection to the column and extra insulation, which contributes to better climate control
• Trusses include heavy-duty zinc galvanized gusset plates for added strength and corrosion protection
• Allows more flexibility for door height
• Raised chord trusses available for added height clearance inside your building.
5 Pre-drilled, factory-cut continuous purlin system adds strength, rigidity and uniformity
• Provides additional wind strength
• Helps prevent roof leaks by allowing for a straight line to fasten roof steel
6 An optional protective liner provides additional structural support plus a solid layer of protection from everyday bumps and machinery collisions
• Made from 7/16" OSB
• Installed between the splashboard and the first nailer
7 Trusses sit deep in a saddle for double strength against wind shear
• 15 ½" truss heels allow deep insulation and air space for attic ventilation
• Truss is fastened to saddle on both sides with 4” structural framing screws and two machine bolts
8 To prevent birds from nesting, most Morton buildings provide double protection with 2" x 2" lumber bird blocking behind each column, plus an optional bird wire mesh system
Bumps. Bruises. UV rays. Weather extremes. Your Morton building is constructed to withstand all sorts of elements. It’s made with the industry ’s toughest steel and best paint available for this application.
1 Industry’s toughest steel
• 26-gauge commercial quality Hi-Rib™ steel not only looks good on the roof and exterior walls, it adds unmatched durability
- Arch-shaped ribs are 1" high and spaced 12"—the strongest architectural shape for withstanding water and weight
- Rib height up to 33% higher and steel thickness up to 25% thicker than panels used by other builders
- Our steel panels are compliant with the Underwriter’s Laboratory standards for hail impact and external fire resistance, which can translate into building insurance discounts for some customers
2 Heavy-gauge aluminum 5" or 6" gutters with downspouts sized to match are finished with FLUOROFLEX® 1000
• 41' long gutter sections with rubber gasket available
3 300 Series Stainless Steel Internal Drive® screws painted to match your building
• Many companies claim to have rust-resistant or stainless steel screws; Morton Buildings has developed a stainless steel screw that won’t rust
• Morton screws feature a solid stainless steel head and shank, unlike stainless caps used by others
• Includes an EPDM washer
- Highly resistant to deterioration by UV rays
- Remains flexible in extreme heat or cold
- Forms an excellent seal between the screw and the steel
4 Double hot-dipped galvanized ring shank nails are strong and rust-resistant
• Includes an EPDM washer
- Highly resistant to deterioration by UV rays
- Remains flexible in extreme heat or cold
- Forms an excellent seal between the nail and the steel
5 FLUOROFLEX® 1000 paint retains color after years of weathering
• FLUOROFLEX 1000 underwent extensive laboratory testing before being used in the field. Decades later it is still a tried and true system
• The weathering performance of FLUOROFLEX 1000 is superior to silicone polyester paint
“I really was concerned with having a building that would be of value 20 years from now and not something that’s going to depreciate. Business people from all over Jackson tell me, ‘This place that you’ve built is going to be worth twice what you’ve got into it in 10 to 15 years.’ It makes you feel pretty good when you’ve made an investment that you’re proud of.”
We only use No. 1 Southern Yellow Pine lumber for columns that are hydraulically compressed during the lamination process. Our treated lower columns are treated with .60 pounds per cubic ft of preservative and have a 50-year warranty. Other lumber used is quality No. 2 or better Spruce-Pine-Fir (SPF) with staggered joints for enhanced strength. The correct lumber and spacing is designed for each project. We roll-form our own steel from .019" thick coil, which is up to 25% heavier than the steel many other builders use, and Morton’s panels feature a unique Hi-Rib™ design where the major ribs are 12" on center and 1" high with a gently rounded profile. This combination allows water to flow away from the fasteners and contributes to the strength and long-term attractiveness of a Morton.
Morton offers the FLUOROFLEX® 1000 paint system, which consists of 70% PVDF topcoat or “color coat” and polyurethane primer that utilizes either a GALVALUME® or hot-dipped galvanized metallic coating. This superior paint system provides your building with multiple layers of protection against fading, chalking, paint peeling, and red rust. Because it resists the effects of ultraviolet rays, rain, and pollution, it retains color and gloss far longer than standard consumer or commercial paint coatings. Morton is proud to offer a 35-year warranty against chalking, fading, and peeling of FLUOROFLEX® 1000.
To view a paint color chart, contact your Morton Buildings sales consultant.
1 Overhead, hydraulic and bi-fold doors
• Almost unlimited options when we work with local door contractors
• Bi-fold doors up to 70' wide
• One-piece hydraulically operated doors in a wide variety of sizes ranging from 10' x 10' to 80' x 22'
2 Sliding doors
• A great solution for large equipment on buildings that aren’t temperature controlled
• AlumaSteel® slider—strong and lightweight
- Test 1.8 to 2.2 times stronger than doors used by building brands
- Easy open and close
- Color–matched to your building
- Available in a variety of widths from 4' to 40'
- Five-year warranty with no wind velocity limit
3 Walkdoors
• Our MB910 walkdoor is a cost-effective every day barn door
• MB FiberSteel® premium door
- For heavily used areas
- Foam insulated
- Three styles available
- Three colors available— painted with FLUOROFLEX® 1000
- Fiberglass frame
• Dutch doors available
• Available with or without windows
4 Low maintenance windows and shutters
• Add natural light and improve ventilation
- Pella® windows with double-and triple-pane glazing
• Vinyl shutters
- Raised-panel or open-louvered
- 12" or 15"
- Attractive colors to complement your building
5 Cupolas increase ventilation, enhance beauty
• 2'6" or 3'6" square
• Choose from four styles or custom larger sizes available
• Fan-powered cupola option increases ventilation
6 Wainscot adds style and protection
• Finishes available:
– Steel – Moderra® brick
– Novabrick® – Versetta Stone®
– Masonry – Many others
– Knotty pine
• Add wainscot any time in the life of your building
The post-frame construction process and durable materials make your building a Morton. The accessories you choose make it say “you.”
7 Dormers and porches extend the character and functionality of your Morton building
1 Fully ventilated attics for enhanced air circulation and condensation control
2 Blown-in ceiling insulation with a rating of R-38 or greater with the option to add more insulation to obtain an overall average rating up to R-60
3 15 ½" truss heels allow deep insulation at building sidewall and air space for attic ventilation
4 Air deflectors direct air from vented soffits over the insulation at the eaves
5 Uncompressed sidewall fiberglass blanket insulation has a true R-19 rating
• Walls are nearly 9" thick; six of those inches are insulation
• Option to add thicker walls and more insulation to achieve greater R-Value
• Polyethylene vapor retarder is installed to keep insulation dry and reduce infiltration and heat loss
• Insulation descends below the top of the concrete floor to increase energy efficiency
• Wide blankets of insulation are used (as opposed to standard house construction insulation, which is 14 ½")
Post-frame buildings feature an exceptionally large built-in wall cavity for ample insulation, thereby lowering heating and cooling costs throughout the year. Where newer energy codes require higher levels of insulation, post-frame is a particularly good option because its walls and roof are relatively easy to insulate. Wide column spacing allows for continuous insulation between structural elements, fewer interruptions in insulation material, and less chance of thermal leakage. Where the insulation is interrupted, wooden structural members have natural insulating properties and conduct less heat than most structural steel or masonry components.
In typical steel buildings, the insulation is draped over the roof purlins and compressed when the roofing is applied. This compression can result in a loss of nearly half of the thickness of the insulation, which reduces the insulation’s R-Value. While many steel-framed buildings feature 3" fiberglass ceiling insulation, which provides an R-9.5 rating, Morton’s Energy Performer® insulation system features R-38 insulation on the ceilings.
Building Similarities
60' x 16' x 120' with white steel
7200 SF floor area
6" concrete floor with monolithic foundation
Perimeter insulation R3.6
(1) 6068 glass entry door–west
(2) 3068 walk in doors–south
(4) 4x3 fixed windows–west
(2) 5x4 fixed windows–south
(2) 14x14 insulated OHD R15–south
Natural gas, forced air furnace 80% efficiency
Central air conditioning with an energy efficiency ratio–9
Building Differences
4/12 roof pitch–with attic
6" wall insulation R19
Blown attic insulation R38
Building Similarities
60 ' x 16' x 120' with white steel
7200 SF floor area
6" concrete floor with monolithic foundation
Perimeter insulation R3.6
(1) 6068 glass entry door–west
(2) 3068 walk in doors–south
(4) 4x3 fixed windows–west
(2) 5x4 fixed windows–south
(2) 14x14 insulated OHD R15–south
Natural gas, forced air furnace 80% efficiency
Central air conditioning with an energy efficiency ratio–9
Building Differences
1/12 roof pitch - no attic
3" wall insulation R9.5
3" roof insulation R9.5
The table below lists annual utility usage for the above buildings as predicted by the DOE 2.1E * computer simulation program. Individual results vary based on building use, configuration, location and weather conditions. The table below is for illustrative purposes only, and does not reflect all the conditions which may affect the performance of your Morton building.
Our warranties are handled directly by Morton, not passed through to suppliers. They include:
This 120 year old, financially solid company will be there to honor its warranties. Snow damage, wind damage, roof leaks, preservative-treated lumber, paint fading, chipping, peeling or signs of red rust are not a concern for owners of a Morton building.
• 50-year snow warranty for most buildings—no weight limit
- other builders' warranties have weight limits
• 50-year protection against decay and insect attack on preservativetreated column, materials and labor
• 50-year warranty to repair or replace any failed precast concrete products manufactured by Morton
• 5-year protection against windload damage to AlumaSteel® doors, materials and labor
• 5-year wind warranty—no velocity limit
- other builders' warranties have velocity limits
• 35-year FLUOROFLEX® paint warranty protects against flaking, peeling, chalking and color change on most colors (excludes livestock buildings)
• 20-year FLUOROFLEX® paint warranty protects against red rust (excludes livestock buildings)
• 5-year protection against roof leaks on steel panels—materials and labor
• One-year warranty on materials and workmanship
Learn more about our warranty work from those who’ve experienced it firsthand. We would be happy to provide the names of customers in your area.
All warranties are non-prorated. Warranties subject to changes and/or updates, location and building use.
1 How long has your company been in business?
2 Can you provide a list of buildings that you have constructed in my county? Can I speak to the owners?
3 Can I see buildings that were constructed 10 or more years ago? How have they “held up”?
4 Does the price of the building include the following: permits, zoning fees, material taxes, delivery charges, construction labor, dumpster, toilet facilities during construction, builder’s insurance, and safety equipment?
5 Who is responsible for permits and zoning issues?
6 Who do I contact for warranty issues and claims? (Is the warranty directly from the builder or is it a “pass through warranty” from the builder’s supplier?)
7 Is the building engineered specifically for my use and land conditions?
8 What is the wind and snow load capacity of the building?
9 What unique features add to the energy efficiency of your buildings? How does this compare to other builders?
10 Who is accountable for the project timeline and any problems that occur? 11 Tell me about the materials used in the building. 12 Where, and by whom, are the materials made? 13 Who delivers the materials? Will they be on-time and well cared for? 14 Who constructs the building—employees or contracted labor? 15 What kind of paint is used and what is the process?
18 Are the subcontractors insured? Bonded?
19 Are the construction crews insured and bonded? Can I see proof? Who is liable if a worker gets injured on my property?
20 What kind of training do your construction crews receive? How many buildings a year do they construct for the company?
When we ventured into the construction industry, our goal was to create a product unequalled in excellence. Today, we deliver on that promise from more than 100 locations in 36 states, constructing thousands of buildings each year. We have an active database of nearly 500,000 satisfied customers.
Morton constructed its first machine storage building. By 1950, pre-engineered buildings were added to the list of products and more than 70 buildings were sold that year.
Morton Buildings began as Interlocking Fence Company, selling mail-order fences to farmers. Retail stores followed in the ‘20s.
Dissatisfied with the quality of available building materials, Morton began selfmanufacturing in 1959. Today Morton manufactures from its six plants throughout the U.S.
Product line expanded to include pole barns built using round creosote-treated poles covered with corrugated galvanized steel skin.
Building sales continued to soar and Interlocking Fence was renamed Morton Buildings, Inc. to better reflect the nature of its business.
Early on, Morton recognized the value of aesthetics and offered colored steel on its buildings.
Introduced to the industry 3-ply laminated columns with staggered splices for exponentially more strength and durability.
Long before the “green” movement, Morton introduced the revolutionary Energy Performer® insulation system—so forward-thinking it exceeded energy conservation mandates that would be introduced two decades later. Constantly refined, it remains one of the most efficient systems on the market.
Morton is the first to use 70% PVDF paint (FLUOROFLEX® 1000),representing a major milestone in preserving the color and value of its buildings.
Morton introduces the AlumaSteel® sliding door, still almost double the strength of its nearest competitor.*
Morton is the first to engineer a structurally sound 100' clear span truss design for maximum clearance.
Morton is the first to offer industry leading details for aesthetics and functionality, including wainscot wall panels, clear span gambrel truss design, eyebrow and deep fascia design.
Morton’s Hi-Rib™ steel gets UL classification for resistance to hail impact and external fire. The next generation steel, Hi-Rib II was introduced four years later.
Morton introduces Stainless Steel Internal Drive® screw—a small building element with a big impact.
Morton introduces roofing panels coated with FLUOROFLEX 2000®
The locking system for sliding
was developed.
Morton introduces the hybrid building. Steel trusses and wood framing for superior strength and clear spans up to 150'.
Morton introduces the exclusive Morton Foundation System.
Morton Buildings becomes 100% employee owned
©2023 Morton Buildings, Inc. All rights reserved. A listing of GC licenses available at mortonbuildings.com/licenses. Printed in the U.S.A. Form #2114/5M/6-23. Construction details and material specifications shown are subject to change without notice. Colors reproduced in this brochure are for illustrative purposes only and may vary from actual colors or finishes. Certain features shown are non-stock items and may be purchased through your local Morton Buildings construction center. Options and features shown may not be available on all building types or styles. The statements and opinions about products expressed here are those of specific customers and should not be construed to represent all buildings or products sold, manufactured, distributed or constructed by Morton Buildings.
AlumaSteel sliding door enhanced by offering the PowerSlide Automatic Opener System.
Morton Buildings introduces DuraPlank® pre-cast concrete splashboard