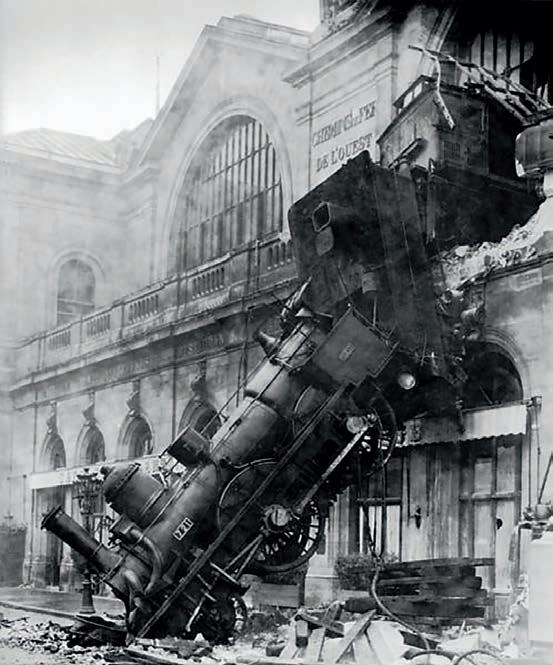
11 minute read
R a i l w a y B r a k i n g f o r M o d e l E n g i n e e r s
the completion process Not only that but it is evident that there is a knowledge gap and this article is intended to help bridge that gap and stimulate interest in the subject
Throughout this article, the Imperial system of weights and measures is used
Why adopt power braking?
The author’s first experience with the business of braking was after constructing his 3½ inch gauge tank locomotive Jubilee He set up about 30 feet of track in the garden and steamed the engine He was fairly young then and naturally eager to see it go. Bystander No.1, elder brother, remarked, “Now you’ve made it go how do you stop it?” This was followed by both heels digging two tramlines into his dad’s fondly manicured lawn, not to mention hot ash setting it on fire The experiment came to an abrupt conclusion but the lesson had been well and truly learned Given the small scale of model locomotives and the light loads of the day, braking was generally achieved using hand brakes on drivers’ trollies, which is still the norm today in the smaller gauges. In 1966, the author visited the ‘Surrey Hills Live Steamers’ in Melbourne, Australia and was offered a drive of a five-inch gauge petrol driven locomotive fitted with air brakes Two things stuck in his mind about that experience the hospitality and friendship of the club members extended to a seafaring ‘pommie’ and the superb braking control of the engine and its train
Since those early days the hobby has graduated to larger and larger scales Nature decrees that as the linear dimension of an object increases, its volume expands in relation to its cube On this principle, a 3½ inch gauge standard gauge type engine might weigh say 70 lb and doubling this to 7¼ inch gauge the weight goes up to around 600 lbs A 3½ inch gauge passenger engine might pull four passengers and a couple of cars with an all up weight of some 800 lb Its 7¼ inc h gauge counterpart could be hauling an all up weight of some 5,000 lb at speeds up to 10 mph Under those conditions, it is uite impossible to expect a trolley brake to dissipate the considerable amount of kinetic energy of such a train - an effective braking system acting on all vehicles is essential
In the late 1970s, our society became set on the road of the so called ‘service economy’ with the litigation industry forming a prime ‘service’ This has bred plenty of opportunity for claims against clubs, societies and even individual drivers if accidents occur Our legal framework rightly requires us to exercise a duty of care to limit risks to the safety of ourselves and our fellow citizens
The rules
The regulatory framework for the operation of miniature railways is predicated on the Health and Safety at Work Regulations 1974 In pursuance of this legislation, the current ‘Guidance’ HS2020
Brake system continuity
for ‘Managing the health and safety at passenger carrying miniature railways’ is now in place. On the subject of braking, Clause 41(d) states ‘the vehicle has adequate braking provisions for parking, normal and emergency braking’ Whilst the author considers this statement rather feeble it is the effective law that attends should an enquiry or prosecution be brought in the event of a mis hap (Author’s note The former TN produced by HMRI was more specific on this topic and is worthy of consultation )
So now we know the rules which apply to our gauges. This puts the onus on us all to ensure that our operating practices are safe Let’s keep it that way
Braking principles
The scientific principles which govern the braking of miniature trains are in essence no different to that of their main line counterparts For main line operation the theoretical and practical lessons have been well learned resulting in the publication of the ‘Railway Group Standards’ which mandate how safety of operation on Network Rail is achieved Braking is covered in several of these standards (available on the web at www rssb co uk) the most relevant being GM/RT2045 ‘Braking Principles for Rail Vehicles’ This document sets out some prime requirements which apply equally to miniature gauges, these are
● Brake systems must be safe and reliable
● Continuous and automatic operation of the power brake must be provided.
● The system must operate in all foreseeable weather and climatic conditions
● A parking brake must be provided
It should thus be obvious that whatever medium is used to power a braking system, it must be safe and always work when required
‘Continuous’ means there is a series of brake system connections throughout the train as shown in fg 1
‘Automatic’ means whenever there is any interruption of the continuity system, the train is automatically brought to a stand For instance, if a train division occurs, the ‘ pass comm (communication cord)’ is operated or the guard applies his brake valve ther relevant provisions are
‘Fail Safe’ means that if any critical system component fails, the system cannot be rendered inoperative In all safety systems, the principle of ‘de-energise to apply’ is adopted to ensure fail safe operation.
● A guard’s brake valve must be fitted to enable the brake to be applied by the guard and the brake continuity proved
● The normal convention for operation of the driver’s brake valve on steam locomotives is anticlockwise to apply and clockwise to release or towards you to apply and away for release (different on modern trains!)
Friction
Friction is the primary means used to dissipate the energy of motion What is friction?
● It is difficult to define precisely but we can observe its effect
● It occurs when materials are either in contact or rub together in sliding contact under the influence of a mechanical force
● Different materials exhibit varying frictional characteristics
● Friction varies with speed, pressure and temperature.
● The energy due to motion (kinetic and wheel rotational energy) is normally dissipated by FRICTION The principle of ‘Conservation of Energy’ applies (heat is work and work is heat)
● With electric drives, the energy can also be dissipated by dynamic braking but a friction medium is still necessary to provide braking to a stand
● The rate at which a train can be braked depends on three main variables friction, brake force and speed
The coefficient of friction (pronounced mu) is simply the force applied to a material in contact with another divided by the normal reaction
For example, if a force of 20 lb is applied to one of the materials and a force of 100 lb is applied normally (at 90 degrees) to both of them, the coefficient of friction would be 0 2 The friction at the point where sliding just takes place is known as the coefficient of limiting friction
Figure 2 shows a rail vehicle brake block applied to a wheel When the product of brake force F and the coefficient of friction between the brake block and the wheel rim is less than the product of the coefficient of friction between the wheel rim and the rail and the normal force on the wheel Q – wheel slide will not occur For this reason, it is always necessary
At 80mph, wheel F has a peripheral speed of 7040ft/min
At 10mph, wheel S rotates at 360rpm
Both wheels have the same rim speed at the rail - 880ft/min to limit the brake force F so that wheel sliding and consequent wheel flats do not occur This limit is referred to as the ‘brake percentage’
In fg 3, an essential truth by which we, as model engineers benefit, is the fact that a model 7¼ inch gauge wheel, of say 9¼ inches diameter, would be the th scale e uivalent of a 6 foot 2 inch full size wheel.
The rim speed of the model wheel at 10 mph works out at 880 ft per minute and it rotates at 360 rpm The full size wheel at this speed has the same peripheral speed but only rotates at 45 4 rpm
At eighty mph the wheel revolves at 360 rpm and has a rim speed of 7,040 ft per mi nute The issue here is that friction at the higher speeds is much reduced and the model operates at a speed where the available friction is comparatively high.
Figure 4 illustrates how the friction force varies with speed At high speeds (above 60 mph) the friction is low, both between the rail and block interfaces with the wheel and thus the rate of retardation is correspondingly low To the left of the diagram, the friction effect can be seen to be significantly increased, a gr eat advantage for miniatures One downside however, is that during a prolonged brake application, the temperature of the brake block/wheel interface will increase leading to lower effective brake force and possible wheel damage, a plague in full size but hardly an issue with miniatures
So now the influence of friction, brake force and speed on the rate of braking can be appreciated.
Brake systems
A b r a k e s y s t e m i s t h e a r r a n g e m e n t o f t h e v a r i o u s c o n t r o l a n d f u n c t i o n a l i t y o f t h e b r a k e s e
There are basically three systems which can practicably be used for the braking of miniature trains
● Vacuum (atmospheric air)
● Compressed air
● Spring applied.
Each system has its own advantages and disadvantages Spring applied brakes are not considered in this article because the means of isolating this type of brake adds complication when working trains
The vacuum brake system is eminently suited to steam locomotives Vacuum is easily created by use of an ejector worked by a small flow of live steam Provided the system is well engineered, it should be very safe and reliable. There are a number of dos and don’ts to observe in designing and making such a system and if these are satisfied the result will prove most acceptable
A (simple) air brake system is perhaps better suited to battery or I C engined locomotives There are a few more components to make for an air operated system but it can be just as safe and reliable as an equivalent vacuum system
The advantage of the vacuum system lies in its simplicity but it does require relatively large brake cylinders since a system operating at 21 inches of mercury only has a maximum air pressure of 10 lb/in2 to work the brake An air brake system may work at any safe desired pressure and the brake cylinders may be correspondingly small yet provide the same brake force as an equivalent vacuum system
The crunch comes when considering the rolling stock that needs to be compatible with the installed system. British Railways spent a significant fortune in fitting dual braked systems in the 1950s and 60s during the change over from vacuum to air braking So, which system do you fit The choice he variability of brake retarding force with speed depends on several factors and should be well thought out by individual clubs and societies
Figure 5 shows a typical system for a trailer car
T h e b r a k e c y l i n d e r s o f b o t h v a c u u m a n d a i r o p e r a t e d s y s t e m s d e s c r i b e d h e r e i n e m p l o y a b a l a n c e d p i s t o n p r i n c i p l e W h e n t h e b r a k e i s r e l e a s e d , b o t h s i d e s o f t h e p i s t o n ( i g n o r i n g t h e s m a l l a r e a o f t h e p i s t o n r o d ) a r e b a l a n c e d e i t h e r b y e q u a l v a c u u m o r e q u a l a i r p r e s s u r e W h e n o n e s i d e i s ‘ r e l e a s e d ’ a i r p r e s s u r e o f t h e a t m o s p h e r e o r f r o m t h e a i r b r a k e r e s e r v o i r a p p l i e s t h e b r a k e
Figure 6 shows a vacuum brake scheme for a steam locomotive The resistance to leakage of any vacuum system is a key requirement. It should be remembered that the old axiom, nature abhors a vacuum’ applies absolutely
Figure 7 illustrates a simple air brake system, the heart of which is the air compressor
The air brake system described differs greatly from that used in full si e being simplified to work in the inverse manner as the vacuum brake
I t w i l l b e n o t e d t h a t o n a l l t h r e e d i a g r a m s a r e l e a s e v a l v e i s s h o w n T h e p u r p o s e o f t h i s i s t o a l l o w a t r a i n t o b e m o v e d w h e n t h e r e i s a s y s t e m f a i l u r e o r t h e t r a i n r e q u i r e s t o b e s h u n t e d w i t h t h e b r a k e i s o l a t e d T h i s i s a c c o m p l i s h e d b y v e n t i n g t h e r e s e r v o i r s i d e t o a t m o s p h e r e w h e n e i t h e r t h e v a c u u m o r c o m p r e s s e d a i r i s v e n t e d f r o m t h e t r a i n p i p e W i t h o u t t h i s t h e b r a k e w o u l d r e m a i n a p p l i e d w h i l s t e i t h e r t h e v a c u u m o r a i r r e s e r v o i r s r e m a i n c h a r g e d T h e s e r e s e r v o i r s p r o v i d e t h e e n e r g y s o u r c e w h i c h o p e r a t e s t h e b r a k e s .
Next Time
We discover how we can create a vacuum simple brake system for an powered locomotive
Martin Gearing presents an ideal beginner’s project with great potential for the more experienced builder.
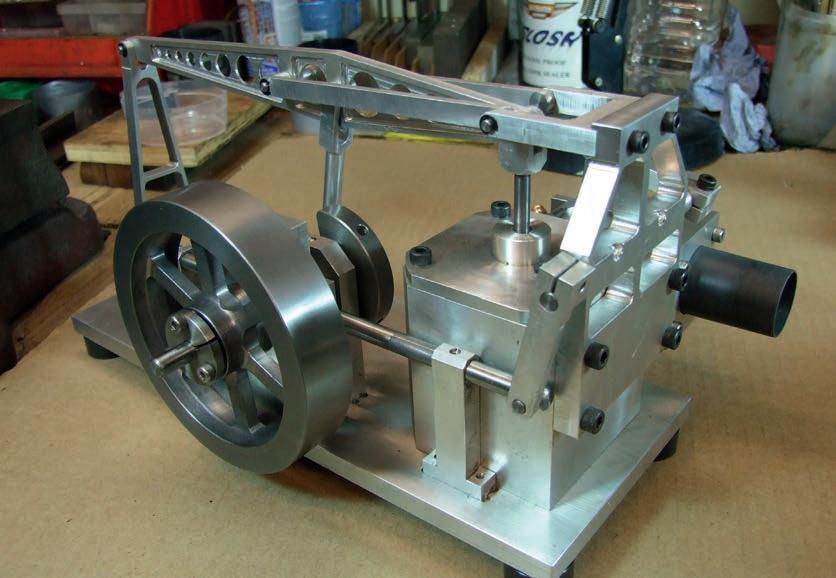