REPAIR, MAINTENANCE & DIGITAL COMPLIANCE
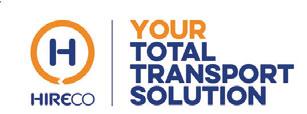
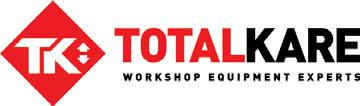

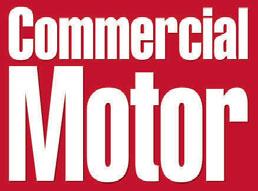

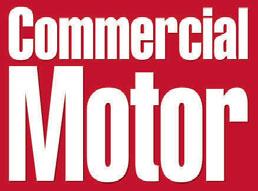
As the road haulage sector moves forward from restrictions imposed by the Covid-19 pandemic, businesses are facing a new challenge of supply chain disruption.
Demand for new HGVs is robust, yet a shortage of key components and raw materials is lengthening lead times and hampering vehicle deliveries to operators.
Operators may therefore find they need to keep existing fleets on the roads longer, with a keen focus on repair and maintenance more important than ever.
This survey looks at strategies for repair and maintenance trends, as well as views on digital compliance, set against the challenging backdrop of today’s operating sector.
It examines the vehicle repair and maintenance strategies adopted by operators, focusing on the choices they make and reasons for their choices.
We also take a look at the role digital aids and technology are playing when it comes to fleet compliance and maintenance regimes.
This supplement was produced in conjunction with Jaama, Hireco and Totalkare.
This report is based on a survey of readers of Motor Transport and Commercial Motor. The research was conducted in July 2022 to get operators’ views on repairs, maintenance and digital compliance strategies. A total of 283 respondents participated in the survey.
More than half (54%) of respondents have purchasing responsibility for spare parts and supplies, while 24% have purchasing influence.
More than one-in-four respondents (27%) are at senior management level, while 20% are owners or partners. A further 17% are in MD/CEO/ board director/chairman roles, while another 15% are middle managers.
The average fleet size (based on vehicles over 3.5 tonnes) for the companies in the survey is 155 trucks, which shows larger operators are more widely represented this year, compared with last year’s survey, where the average fleet size stood at 88. One-third of the companies have fleets of one to five vehicles, while 13% have fleets of more than 100 vehicles.
The average turnover of the companies surveyed is £69m, again vastly higher than last year’s average turnover of £34m; 12% have turnovers of more than £100m, while 29% have turnovers of less than £2m.
Looking at sector split for those responding, we can see that third-party logistics operators
account for 41% of the companies in the survey, while 35% are own-account operators. Public sector accounts for 4% and municipal and waste 7%. The remaining 13% comprises operators in a variety of sectors, including recovery, agricultural and contract hire.
Choosing the right repair and maintenance (R&M) solution for an operator’s fleet is a crucial decision to get right, and remains a moot point for them, as our survey reveals.
Two-thirds of operators taking part in our survey preferred to outsource R&M work – 35% to a main dealership and 31% to a third-party workshop – whereas 31% keep maintenance in-house, and the rest a mixture of approaches.
There were noticeable differences in approach between third-party logistics providers (3PLs) and own-account operators. Some 26% of 3PLs
have in-house R&M facilities compared with 32% of own-account operators. Of the threequarters of 3PLs that preferred to outsource, this was evenly split between main dealerships at 37% and independent garages at 36%. Ownaccount operators outsourcing were more likely to opt for a main dealership (41%) over a third party workshop (32%).
The survey also suggested that larger fleets were more likely to have an in-house workshop function, with 39% of those running 50-plus trucks opting to do so compared with only 28% of those running between one and 50 vehicles.
When it comes to sourcing and purchasing spare parts for fleets, just under half (46%) of operators went directly to a manufacturer, with a third preferring to use third-party suppliers.
In a question posed by sponsor Jaama, respondents were asked what they found the most time-consuming area when it came to R&M: document management (31%) and scheduling of maintenance (30%) topped the list of functions cited by operators, followed by 18% suggesting capturing of defects being the most time-consuming.
With the average age of commercial vehicle fleets continuing to rise, retaining high levels of compliance remains a major priority. Jaama’s Key2 fleet management system covers all the bases for cars, CVs and plant.
Jaama’s Compliance Manager, an integrated module within Key2, is fully configurable and enables managers to create their own regular, variable and one-off vehicle-related events such as servicing in accordance with manufacturer requirements, MoTs, and commercial vehicle inspections to ensure they are never missed.
Functionality within Compliance Manager includes historical events being stored against the asset record to enable fleet managers to check whether historic events are being completed; prematurely, on time or late. It then auto-creates the due date for the next event, such as a service, MoT, or inspection.
It can also remove events and record a reason for removal if a vehicle has a Statutory Off Road Notification (SORN) or is used seasonally and provides a full event history audit trail.
Compliance Manager also integrates with Maintenance Exchange, Jaama’s new maintenance and compliance platform that streamlines the exchange of vehicle maintenance information and connects with its fleet, asset, and driver management solution Key2.
The end-to-end system allows fleets to book maintenance, authorise work and manage invoicing and auditing of vehicle maintenance work. It also enables all required documentation, MoT certifications, vehicle inspection sheets, servicing, and routine maintenance documents to be shared between service and repair centres, vehicle owners/operators and the DVSA.
An increasing number of Jaama’s new customers have procured Key2 to help them securely manage the increasing amount of electronic documentation required to run their van and truck fleets.
Go Plant Fleet Services rolled out Jaama’s Key2 fleet management system to administer its 3,000 HGVs and specialist vehicles, and 600 items of plant. With its drivers and vehicles working in demanding environments, such as highways and construction sites, compliance was a key consideration when finding a new fleet management system.
Group IT and innovation manager Rhianna Greaves said: “A major benefit is Key2 gives us the ability to store electronic records on our vehicles and track MoTs in real-time across our fleet, which is key to delivering vehicle compliance. We can now also record warrantyrelated claims and follow them up with dealers.”
Operators opting to outsource their R&M have a wide choice of packages available to them, whether using main truck manufacturer dealerships or local independent garages.
The majority of operators tended to opt for a contract with their maintenance providers (72%), while the remaining 28% preferred an ad-hoc approach. Those choosing a contractual route was up substantially from 65% last year, however this may reflect the increase in larger operator respondents compared with the 2021 survey. Indeed, 79% of those running more than 50 trucks opted for an R&M contract, whereas this figure dropped to 69% picking a contract when running 10 or fewer vehicles.
We looked at operator preferences in terms of the type of contract. Half of those with contracts preferred a price-per-truck option, with a further 39% opting for a fixed price-per-month model. Only 4% chose a price-per-km model.
Some maintenance providers, particularly those linked to truck manufacturers, offer tailored R&M packages. These are often tiered, with top-tier packages providing complete service contracts, moving down to more basic contracts offering service, MoTs and so on. We asked respondents their preferred option: 63% opted for a top-tier contract, which included features such as roadside
Basic contract (including MoT, preventative maintenance and tachograph calibration)
Mid-tier contract (including maintenance, service, guarantee or warranty extensions)
Top-tier contract (including features such as roadside repairs, zero tolerance on downtime etc)
repairs and zero tolerance on downtime. The largest operators were significantly more likely to pick a top-tier option (74%) than operators running up to 10 trucks (59%).
Mid-tier contracts that included maintenance, service, guarantee or warranty extensions were chosen by 21%, down from 25% in 2021. And 16% went for a basic contract – substantially down from 30% in 2021.
The top reason cited for those not using an R&M contract was ‘too expensive’ for 40% of respondents, while 27% felt it did not meet their operational needs; 18% did not want to commit to a contract, while other reasons listed included warranty cover, unreliability of dealerships and long waits for workshop slots.
Woodland Logistics, one of the largest national dedicated and general transport logistics suppliers, was one of the first companies to trial and benefit from Hireco’s Electronic Braking Performance Monitoring System (EBPMS) and Telematics Tracking systems.
Woodland, which provides full-fleet transport solutions for high-profile manufacturers across the UK as well as general transport logistics, has seen its performance, safety capacity and costefficiency improve as a direct result of trialling this next-generation technology.
The EBPMS monitors the stopping energy and amount of braking pressure applied to a vehicle, and in doing so builds up reports that replace traditional brake tests; this means the tests are reducing from being required four times a year to just once a year. In addition performance readings can be called on at anytime, giving brake performance vision when required.
Telematics tracks data in real-time to improve productivity and operational efficiency, using tools including tracking systems, geozone reporting, trip history and speed analysis.
Paul Eve, head of fleet for the Woodland Group, said: “We’ve been really impressed with the tracker and EBPMS systems. Since using them, they have proved to be successful in all aspects they cover.
“In particular, the tracker helped us with the pin point location of one of our trailers after it was stolen. It was vital we located the trailer as soon as possible and by having the tracker fitted we pinpointed it within seconds and established where the trailer was swiftly, with the load safe.
“We’ve seen the potential for our vehicles having more time on the road, less downtime and fewer breakdowns, as well as improving driver safety. We’re now looking to extend the use of this technology to more of our fleet.”
Tom Baker, asset performance manager from Hireco, said: “Customers are reaping the benefit of our performance technology, which is straightforward to install and makes a positive difference from the moment it starts being used. With the ability to reduce brake test requirements by up to 75%, and by being able to monitor vehicles in real-time, means the commercial, performance and safety advantages of the EBPMS and telematics systems are clear.
“Through our smart technology, customers can rely on Hireco to be their total transport solution, enabling peak performance of their assets.”
With nearly one-third of respondents (31%) choosing an in-house option for R&M, the survey looked at reasons why. Some 41% said they have always done it that way and have facilities established on-site, which suggests a significant amount of inertia in the market.
Just over one-quarter of respondents said inhouse R&M gave them more control over fleet compliance, booking MoT slots, and servicing tests, while control of costs was a top reason for 16% of operators and easier management of downtime for 11%.
Kitting out an in-house workshop can be a significant investment for operators, so we asked where the most likely source of larger items would come from: 54% bought from a generic garage equipment supplier, while 40% headed to a particular equipment manufacturer to make major purchases.
Under-vehicle inspection pits are a key function in any vehicle workshop and 46% of respondents said they would use a proprietary manufactured pit for their fleets. However, nearly one-third (32%) created a home-made pit solution for vehicles and the remaining 22% cited various methods such as post ramps and hydraulic lifts.
Larger operators were more likely to invest in a specialist manufacturers’ inspection pit,
with 62% opting for this, compared with those running 10 or fewer trucks, who were evenly split between homemade and manufactured pits (41% for both).
Moveable vehicle lifts were the preferred lifting option for more than half of operators (56%), while 17% opted for fixed lifts. The remaining quarter of respondents cited a mixture of lifting technology, or did not use lifts.
In a question posed by sponsor Totalkare about smaller workshop equipment, the most popular items to likely buy in the next 12 months were trolley/bottle jacks, torque tools, compressors, mobile brake testers and workshop furniture.
a buying group
a garage equipment supplier
Mercedes-Benz dealer Motus Truck & Van has partnered with workshop equipment experts Totalkare for the supply of vehicle lifting equipment for its new truck and van service and parts centre in Witham, Essex.
The commercial vehicle specialist provides new and used sales and servicing for Mercedes-Benz vans and trucks across the south-east and East Anglia. Its new 2,500sq m facility in Witham features nine full-length truck and trailer bays with eight more available for van maintenance and repair.
Completing the facility, Motus Truck & Van has created a dedicated, external vehicle wash bay area finished with a fully galvanised Y-MECH lift from Totalkare that is purpose-built for vehicle wash applications.
Available in platform lengths from 6m to 13m
and with a range of lifting capacities from 25,000kg to 35,000kg, the Y-MECH provides optimal working space around the lift for the maintenance, repair and under-chassis washing of heavy-duty vehicles. It can be surface- or recess-mounted to suit requirements and features mechanical safety latches and rollover/ roll back protection to guarantee maximum safety.
Motus Truck & Van’s Y-MECH lift features a 13m platform length and 35,000kg lifting capacity, with lighting installed for increased visibility underneath the vehicle. Totalkare will support the lift with a service contract that includes two field service engineer visits a year.
Motus Truck & Van head of aftersales Paul Smith said: “Our new truck and van service centre is a flagship development of which we’re all very proud. Under-chassis washing of vehicles is not only crucial ahead of MoT testing but makes maintenance and repair tasks more pleasant for our workshop operatives, and Totalkare’s Y-MECH is the ideal solution for this.”
Brian Young, national accounts manager at Totalkare, said: “Totalkare has been supporting Motus Truck & Van for many years with a variety of vehicle lifting and testing equipment, and we’re delighted to have supplied and installed this Y-MECH lift as part of its fantastic new site in Witham.”
Whether an operator chooses to outsource R&M work or carry it out internally, it is vital for transport managers to keep a tight rein on their fleet maintenance regime. Their role requires them to ensure vehicles remain roadworthy at all times, comply with all legal requirements and ensure comprehensive records are in order and acted upon when necessary.
Not only do transport managers have to do this to keep vehicles and drivers safe while staying on the right side of the traffic commissioner, but they also have to drive efficiencies into the wider operation by minimising HGV downtime and reducing fuel emissions and costs.
We asked operators how their transport managers preferred to keep track of maintenance records. It was quite an even split between those opting for a predominantly digital-based system (46%) and those preferring paper records (41%), while 9% had a combined approach. A small minority (4%) of operators said they did not keep track of maintenance records as they relied on a third party to do so.
Weekly checks of maintenance records were the most popular with respondents to our survey, with nearly half (47%) doing this. This was followed by 23% of operators checking records every 28 days (to possibly align with DVSA Earned Recognition KPI requirements) and an equal 23% checking records six-weekly to tie in with PMIs. The remaining 7% ranged from those checking R&M records daily through to periods up to 10 weeks.
Digital compliance software has advanced significantly over the past few years, with systems developed to check everything from vehicle idling through to workshop scheduling and everything in-between.
The most popular use of digital compliance equipment was for maintenance and inspection report scheduling, with more than half of operators using it for this purpose (55%). This was closely followed by driver walk-around checks and defect reporting systems (52%). Other uses included MoT initial pass rate monitoring, tyre-pressure monitoring and incident reporting.
In a question posed by sponsor Hireco, 71% of respondents said they thought a digital checklist for drivers to help them go paperless would be a helpful compliance aid.
A well-run fleet maintenance regime plays a crucial role in the DVSA’s flagship Earned Recognition scheme.
The voluntary scheme is a way for operators of all sizes to prove their fleet meets required compliance standards by regularly sharing performance information with the DVSA.
To do this, operators must use a DVSA-validated IT system for vehicle maintenance and drivers’ hours records, which will monitor an agreed set of key performance indicators.
Every four weeks, the system tells the DVSA if any KPIs have been missed by a set amount. If this happens, the DVSA will work with operators to help fix any problems. The DVSA does not have any direct access to operators’ data or systems.
Benefits to businesses for signing up to Earned Recognition include proving they are an exemplary operator when bidding for key contracts, but it also means their vehicles are less likely to be stopped during roadside checks or to receive on-site visits.
Around 11% of respondents to this survey had joined the DVSA scheme, but a further 26% were looking to join in the next 12 months, which shows an increasing interest in the initiative.
Larger operators running 50-plus HGVs were far more likely to have signed up to Earned Recognition, with 18% already on-board and a further 23% looking to do so in the next year. While the smallest operators (1-10 trucks) showed only 6% had joined up to date, a significant number (27%) planned to in the next 12 months.
Medium-sized operators, with between 11 and 49 trucks, revealed that 13% had already joined the scheme and a further 27% planned to do so.
you a member of the DVSA’s Earned Recognition scheme?