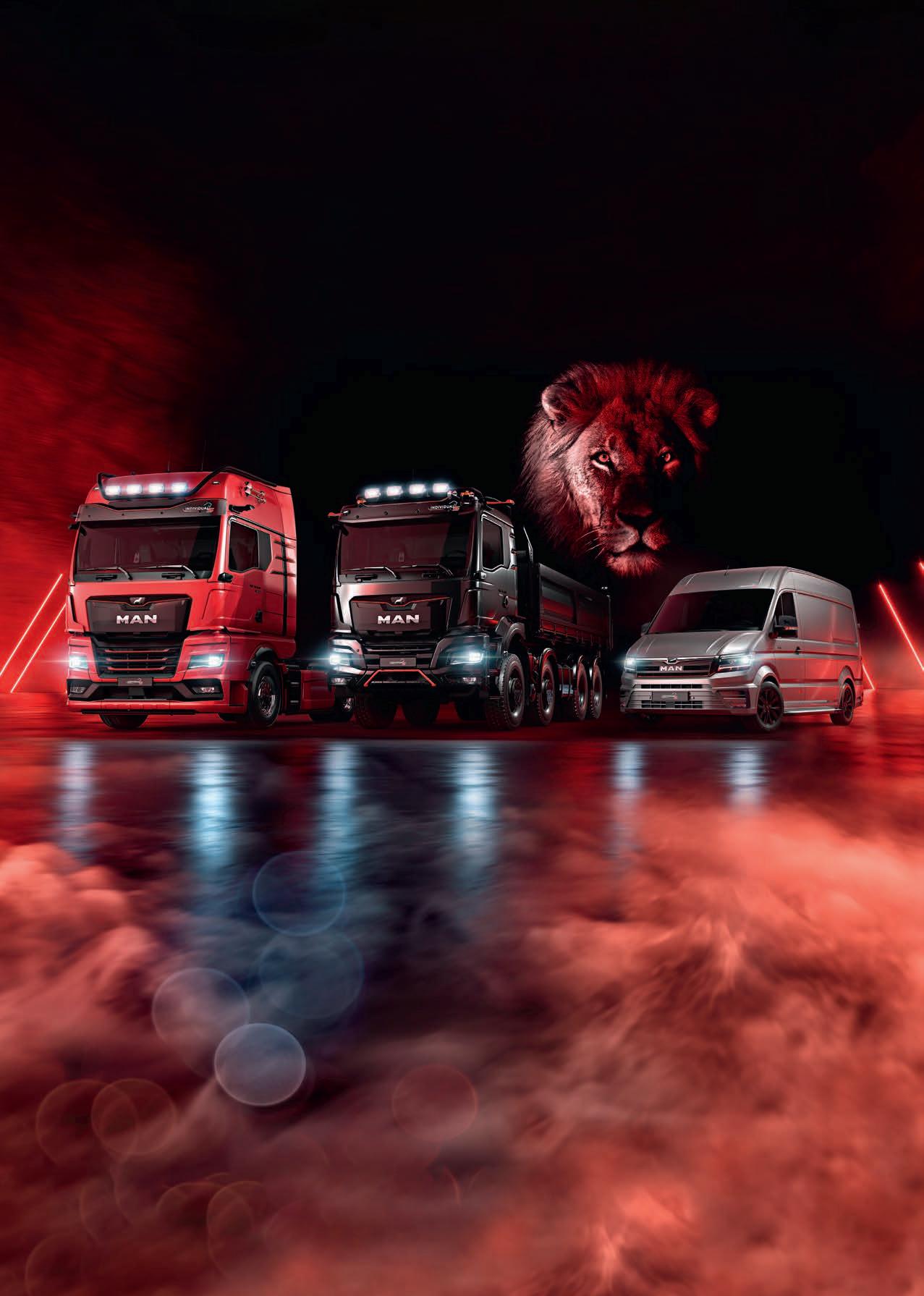
4 minute read
THE PILLARLESS CURTAINSIDER
Lawrence David’s unique Pillar-less Curtainsider trailer has been around for 45 years and was designed to give unrestricted access to the load space to make it easier, safer and quicker to load and unload along the full length of the trailer. Chris Curzon estimates that over 150,000 have been built in that period.
“In the early days it was a registered design but that expired in 1988,” he says. “The original concept was for carrying 10m lengths of timber from Boston and it slowly grew for customers like kitchen manufacturers who needed to carry work surfaces. But the real catalyst for growth was in the late 1990s when health and safety became a bigger issue.”
Advertisement
A conventional curtainsider uses pillars along the side of the trailer to support the roof and these are always under compression.
“To release the pillars to move them out of the way you have to take the tension off and that is likely to cause problems,” says Curzon. “Injuries to fingers and heads have occurred many times. So companies like Walkers Crisps and DS Smith were the catalyst for developing the pillarless curtainsider. Complete access was just part of it – it was all about health and safety.”
Curzon believes that Dawsongroup’s enthusiastic adoption of the LD pillarless concept was a big attraction for operators to take trailers from the company, helping it grow its trailer business.
“Many people have copied the Pillar-less design, but how long have they been building them and how many have they built?” asks Curzon. “Nothing compared to us. We are the only company with that long experience of building the Pillar-less design that has been used to carry everything from crisps to concrete blocks.
“We give a 10-year structural warranty and there is no other manufacturer that can offer that.”
Given the extra strength that is required for a fully self-supporting roof it is surprising that the Pillar-less weighs no more than a conventional curtainsider and it can be built into a 15.65m longer semi-trailer and even a double-deck trailer using the same design that has remained unchanged for 45 years.
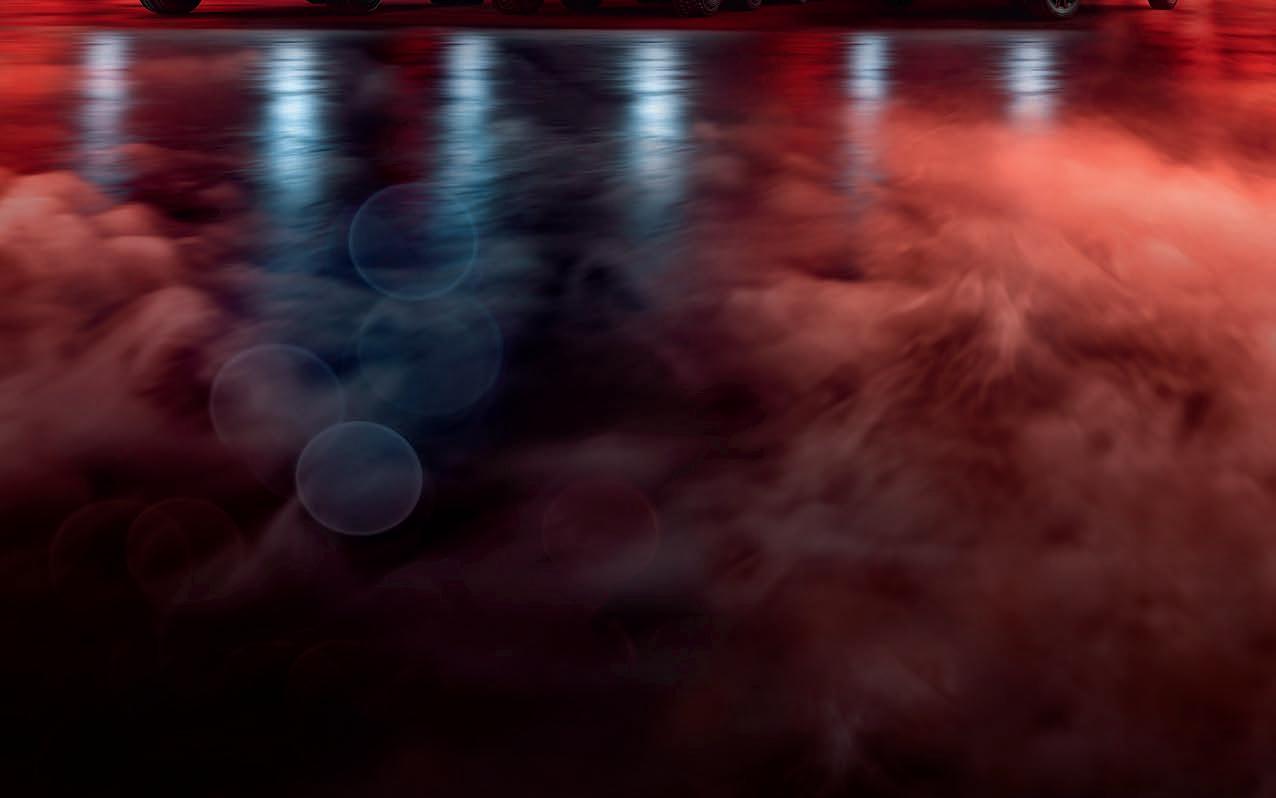
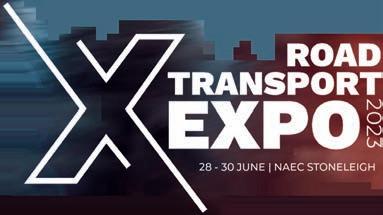
EARLY ADOPTERS OF EN 12642-XL
Lawrence David was one of the first UK trailer manufacturers to build trailers to the EN 12642-XL European load securing standard that was first published in 2006. The standard was controversial at the time as many operators wrongly believed that trailers meeting the EN XL standard did not need additional load restraint as the curtains, doors and front bulkhead were strong enough to retain the load.
LD’s ArmourSheet ‘Plus’ XL load bearing curtains surpass EN 12642-XL and were designed by company founder Lawrence Marshall and his team over 45 years ago.
“If you look back to 2004 we didn’t have to do anything to our trailers to comply with EN 12642-XL,” says Curzon. “The design was already in place for the front bulkhead, the rear doors and the curtains. Everything was load bearing even then and we changed nothing to meet EN 12642-XL, unlike our major competitors who had to completely redesign their trailers.”
John Fletcher says that many operators still do not fully understand what loads an EN 12642-XL trailer can safely carry without internal restraints.
“It only applies to positive-fit loads,” he explains. “If you look around at industries like used tyres they completely abuse trailers and their curtains. We don’t see as many as we used to but a lot of people still misuse trailers.
“Most of our arguments three or four years down the line from build would be about abuse rather than a product specification issue.” major manufacturers use the LD-style product. That is a testament to Dawsons and it did us a massive favour in that we have been able to supply that product to all our customers.
“Some of those trailers are still on the road today after 20 years’ service.”
Around 45% of the Dawsongroup’s trailer fleet are curtainsiders with the remainder being a mix of box vans, flats, skeletals and fridges.
“We have quite a large refrigerated fleet, which at the moment is off the table for LD,” says Fletcher. “But who knows for the future?”
As part of the Polish-owned Wielton Group, LD has
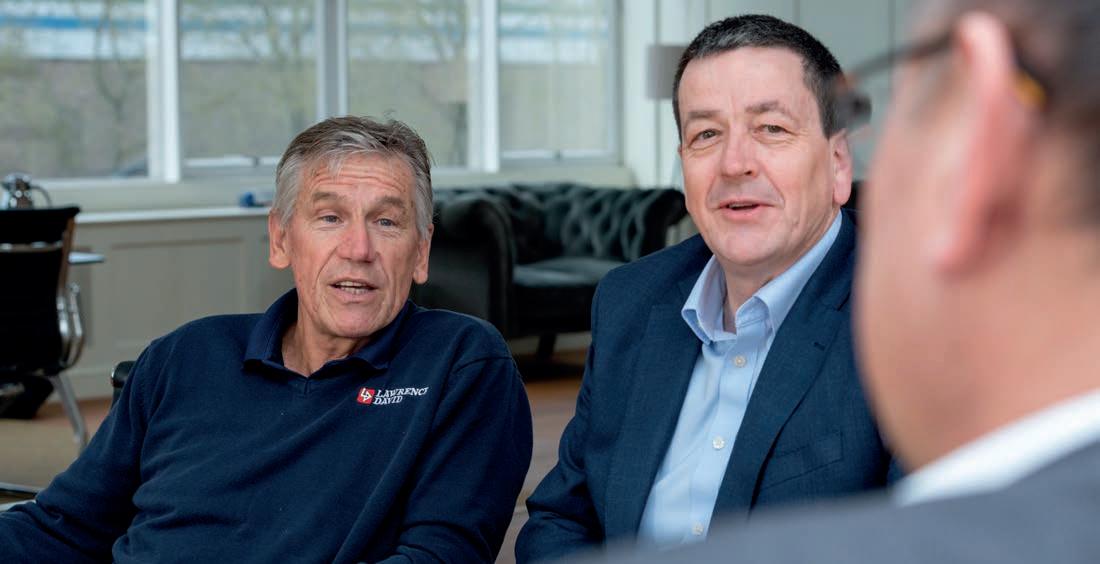
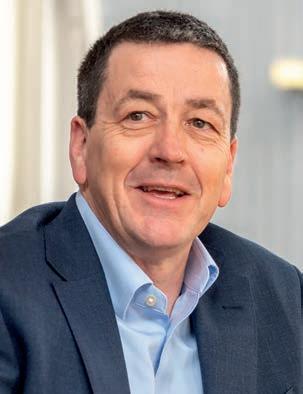
FUTURE PERFECT: Collaboration efforts are now focused on the manufacture of trailers that use less materials and more reusable components access to all types of trailers built by other group companies.
“We are always looking at new models,” says Curzon. “We are bringing in some skeletals and flats for Dawsons. The group produces all types of trailer – except fridges – in Germany, Italy, Spain, France and Poland so we have a wide mix. It is probably the biggest tipper manufacturer in Europe so there is lots for us to go after.
“Fridges are on the agenda and will probably be brought to market in the next 12 to 18 months.”
Green dream
With the current focus on the environment, Dawsongroup is now working with LD to make trailers which use less materials, utilise reusable componentry and are more recyclable.
“We have to think about the environmental impact and how much is reusable,” says Fletcher. “One of the things we are working on is to find an alternative to GRP and still make trailers that are usable and affordable.”
Aerodynamic trailers were at one time claimed to be making a contribution to saving the planet through reduced fuel consumption but Curzon says that, while they may have looked good, there was in reality very little fuel saving.
“We spent £100,000 testing 4m trailers at Mira and proved there was no fuel saving,” he says. “A lot of bigger operators bought into the marketing to enhance their own image. There is nothing wrong with that but the reason you don’t see those trailers any more is that they have realised it isn’t cost effective.
“On a double-deck trailer, if you are prepared to compromise load space, there are aerodynamic advantages to curving the front of the roof. But it’s pointless if you’ve sacrificed the first four pallets.”
Dawsongroup was an early adopter of Axscend trailer tracking technology, first fitting the system back in 2008. While these units do have a battery fitted it lasts for up to 10 years without recharging. But Dawsongroup is investigating the use of roof-mounted solar panels for other uses.
“In the refrigerated sector there are advantages without a doubt if the fridge unit is electric,” Fletcher says. “For a dry freight trailer there is no benefit at the moment. But if the tractor goes battery electric are we going to have to spread the weight of batteries across the trailer? Then it would become more interesting.” n


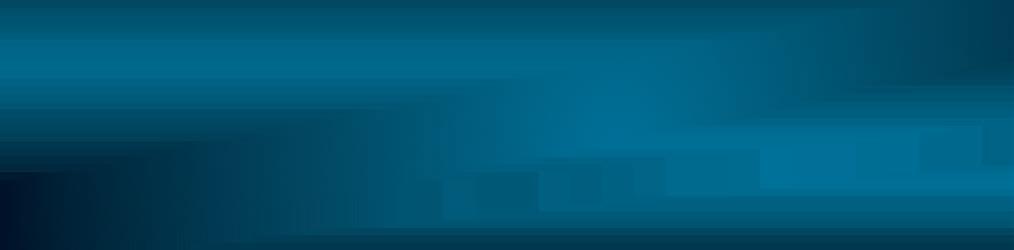
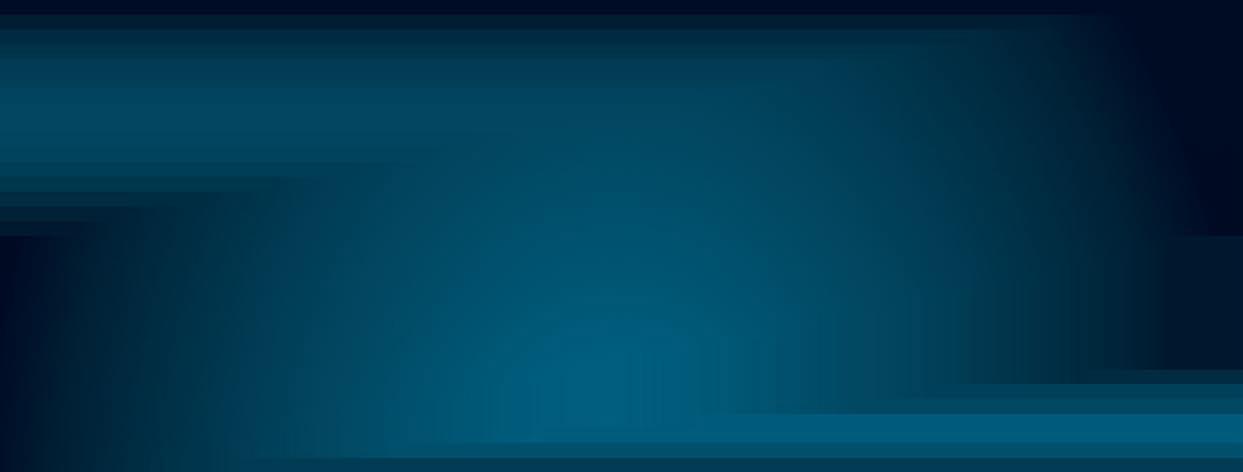
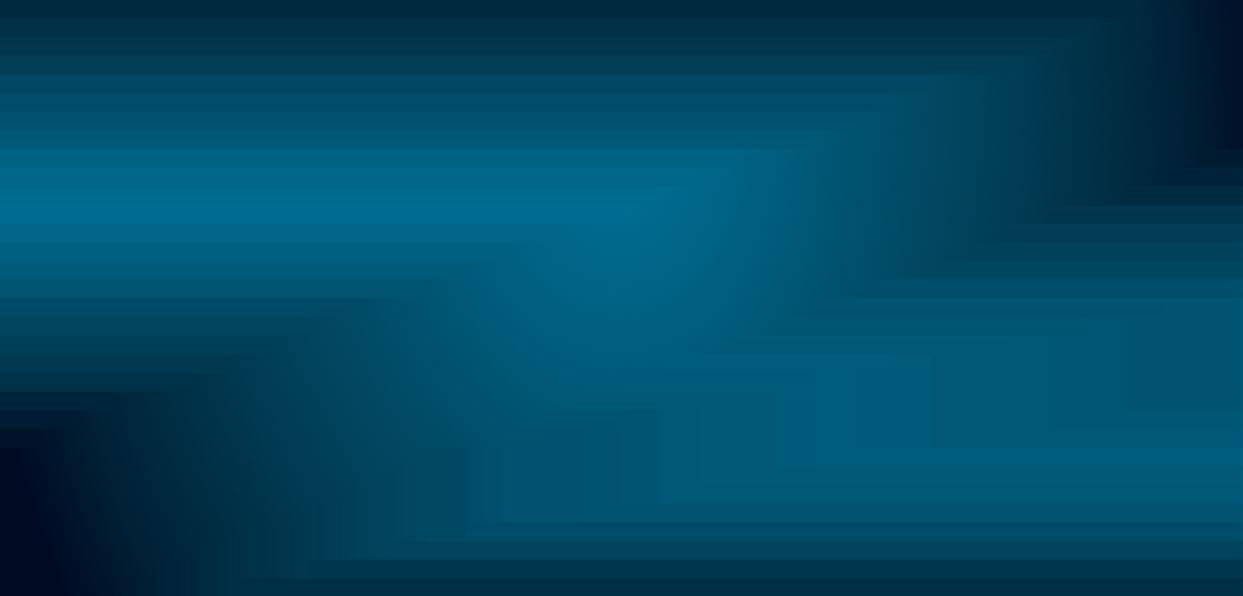
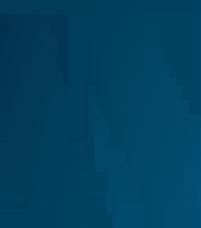
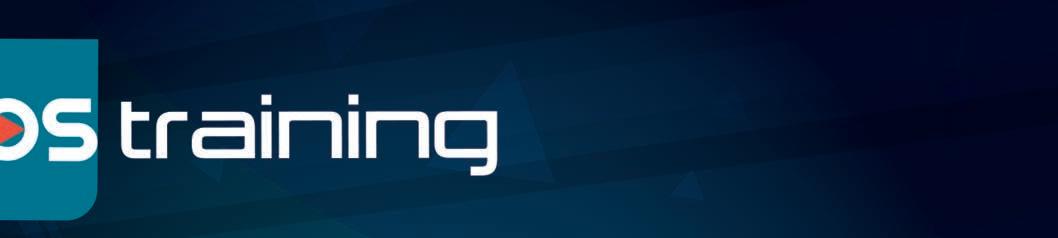
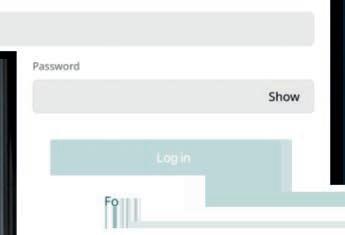

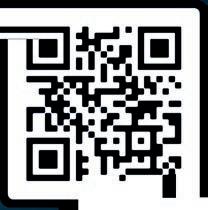