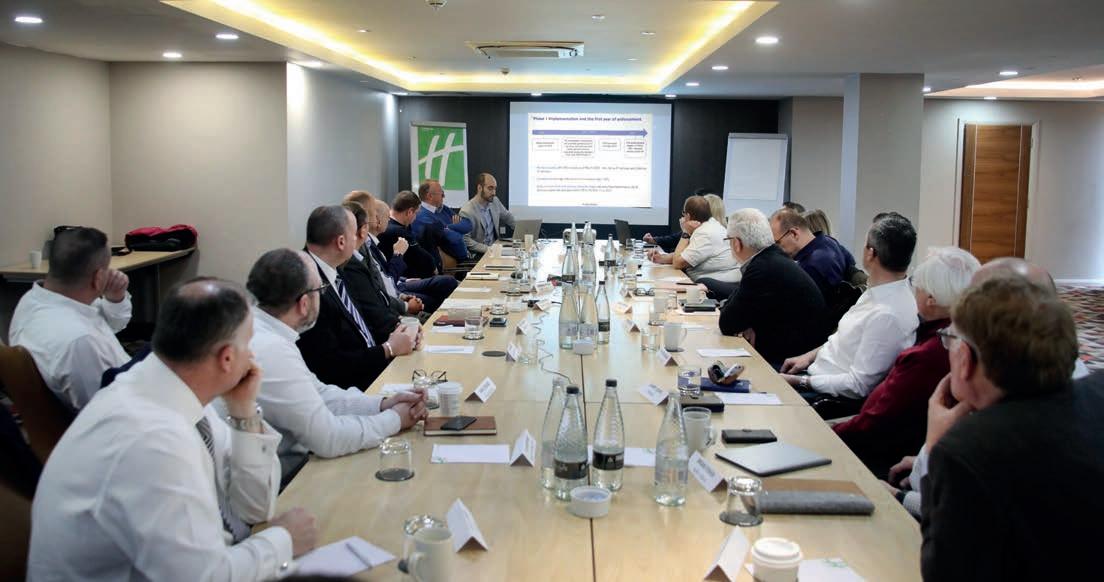
16 minute read
All eyes on DVS
Phase 2 of TfL’s Direct Vision Standard comes into force in October next year. MT gave operators the chance to have their say on how the proposals will affect them
TfL is due to introduce phase 2 of its Direct Vision Standard in October 2024 and its consultation on the amended standard closed on April 3. Just before the deadline Motor Transport, in association with Brigade Electronics, held a roundtable debate with TfL and a group of leading operators to discuss phase 2 and its expected impact.
Advertisement
Steve Hobson, editor, Motor Transport: Welcome to this roundtable in association with Brigade Electronics. We will start with short presentations from TfL, Brigade and DAF on the proposed revisions to the DVS.
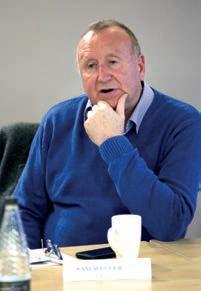
Dr Polyvios Polyviou, strategy and planning manager

– freight, TfL: The DVS was introduced in October 2019 but enforcement was delayed until March 2021 due to Covid-19, and we made a commitment then to raise the minimum requirement from one star to three stars from October 2024 after consulting with industry.
Compliance has been good with 244,892 permits issued as of March 2023 and the average daily scheme compliance rate at 94%. We have seen a reduction in fatalities as a result – fatal collisions have halved since 2018 and serious injuries are down from 39 in 2018 to 17 in 2021.
Jacqui O’Donovan, MD, O’Donovan Waste Disposal: We have gone from 39 in 2018 to 17 in 2021 but the DVS only started in 2021 so the reduction wasn’t because of the DVS. Is that all HGVs?
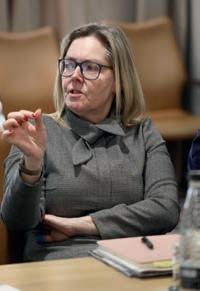
Polyviou: Yes, those are for HGVs and this is showing the trend going down over the last few years. We feel some part of the reduction was due to the DVS.
O’Donovan: Do we have the data on what star rating the vehicles involved were? I think that figure is distorting everybody’s view because while it has halved it isn’t because of DVS.
Polyviou: Yes, it’s a fair comment that the comparison goes beyond the DVS introduction in 2019 and there are more stats publicly available on our website for specifically the first year of operation. We have looked at accidents since enforcement began and they are still going down. Sam Weller, principal city planner, TfL: We are now monitoring the star rating of vehicles and whether the incident was vision-related so going forward we will have better visibility.
Polyviou: So why do we need phase 2? The original Safe System was developed in 2018/19 and it was our policy commitment to review and consult on it and increase the minimum direct vision rating to three stars. This aligns with the London mayor’s wider Vision Zero, which is to have by 2041 zero deaths across the network.
There is more to do because zero-star vehicles accounted for four of the six fatalities in 2021 where vision was cited as a contributory factor by the police.
Based on our learned experience from phase 1 and improvements in technology we commissioned Loughborough University to undertake a review and provide recommendations to us, which we used to put forward our proposed Progressive Safe System. Chris Cooling, senior transport manager, Day Aggregates: Do we know what is the representation of zero star vehicles in the vehicle parc?
Polyviou: I would estimate that of the 250,000 vehicles with permits, around 60% would have zero stars.
You are all familiar with the existing Safe System [right], which has been applied to all zero-star vehicles and details are on the TfL website. The proposed Progressive Safe System will be applied to all zero-, oneand two-star vehicles.
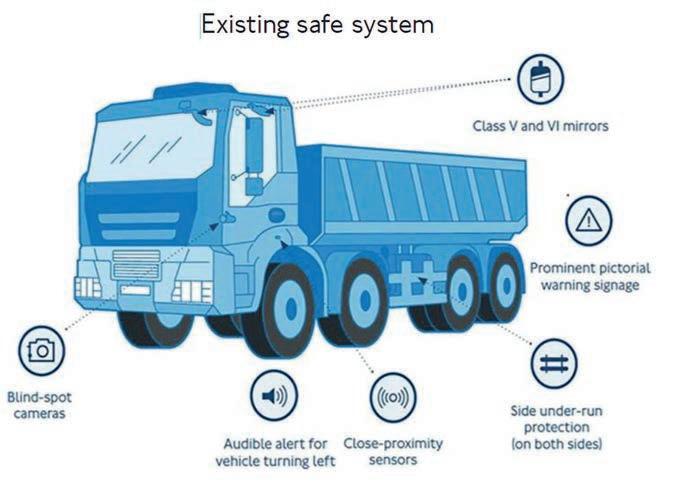
Weller: The proposed Progressive Safe System will require either Class IV, V and VI mirrors or a mirrorreplacement camera monitoring system (CMS) or a combination of both.
The Class IV, V and VI mirrors are now pretty standard on most trucks to improve indirect vision but we have the CMS which are available on Mercedes and DAF trucks. So we are looking at accepting either the mirrors or CMS, which after talking to people are probably better than traditional mirrors because they remove the mirror arm and mirrors to get rid of that blind spot at roundabouts and there is also a benefit in that on articulation the camera will follow the trailer.
One change is that instead of saying CMS ‘should aim to’ eliminate the remaining vehicle blind spot at the nearside, the proposed regulation will say ‘must’. Another new paragraph defines ‘blind spot’ as ‘the area of the road that cannot be seen by looking forward through the windscreen or by using rear-view mirrors’.
Research by Dr Steve Summerskill at Loughborough University has shown that all those in red [below] cannot be seen directly from the cab. Clearly there is an issue there and we need to eliminate totally the blindspot down the side of the vehicle. At the moment some cameras do, some don’t.
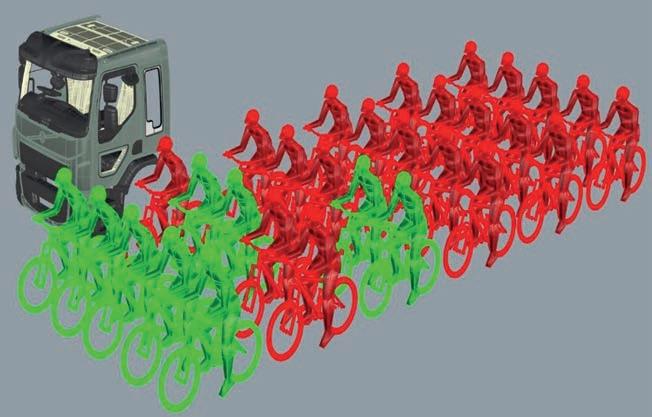
Steve James, senior transport manager, FM Conway: I find that diagram very misleading. That says the bikes in red are invisible to the driver. You are endorsing Class IV, V, and VI mirrors that enable him to see what is there. Weller: Moving on to side sensors, we have had some feedback on this already. On rigid vehicles the sensors ‘must ensure full coverage down the nearside of the vehicle’ and a lot of people have done this already which is really good. It is a recommendation at the moment but will become a requirement to cover the whole of the nearside for all vehicles, particularly the MG3 tippers where the driver is high up and has the blind-spot problem. For articulated vehicles the consultation says sensor systems ‘must ensure full coverage of the nearside of the tractor unit and in addition the semi-trailer’ and that sensors ‘must be suitably positioned to provide sufficient coverage but preventing activation solely on articulation of the trailer’. We have had a lot of feedback because a driver on a shift could potentially tow a couple of different trailers so what we are looking at doing – and this is only a maybe – is recommending something like radar or AI technology fitted to the tractor unit so it doesn’t matter what trailer you are towing. There is technology that fits on the mirror arm or cab that can cover the whole of the nearside of the vehicle without having to fit anything to the trailer. We are aware that drivers do trailer swaps and some trailers are not compatible because of the anti-roll system and ABS so this is something that will avoid connection difficulties. We’ll accept the manufacturers’ statement that it is compliant with UNECE reg 151 at face value.
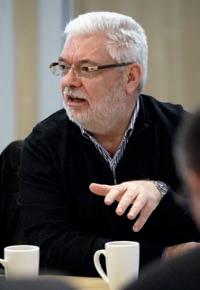

James Ashford, head of UK connected services, Brigade Electronics: Previously you would need two separate sensor systems because the technology to combine them was not out there. As the trailer jack knifes as it turns, the sensors on the tractor are fitted so far back they pick up the trailer, which TfL wants to avoid. Our new Radar Predict will overcome this. It is due to be launched in the summer.
Carl Milton, cement logistics manager – UK, Cemex: One of the issues today is that we are on the cusp of newer technologies and some of what you are requiring is leadingedge technology. As an industry we need time to let manufacturers catch up. We first worked with Brigade back in 2001 developing side scan systems and that technology is quite aged now. Ultrasonics are giving way to radar, lidar and infrared. Weller: Moving on, this is new – a mandated moving off information system (MOIS). There have been accidents at pedestrian crossings where the driver has not seen a person directly in front of the cab. Even with a two-star rating there is a blind spot – I know you have the Class VI mirror but if for some reason he didn’t look in that, at least he will get an alarm.
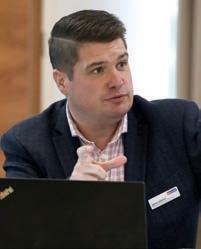
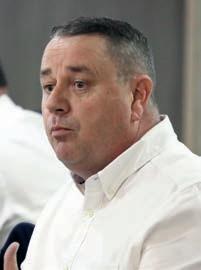
It must be fitted in accordance with UNECE reg 159 and must be active not passive as with all the systems, so when you drive past a bin it doesn’t activate. That would drive the driver mad and then he will just ignore it after a while. We only want the warning to sound when there is a credible risk of collision.
Ian Hartley, vice president operation – network transport and Tradeteam secondary operations: How do we expect a driver to deal with this amount of information? This in itself can become a danger. I can think of certain junctions in London where you would end up not moving because there are that many proximity alarms triggering in your cab. What we are asking drivers to deal with in urban situations, which are difficult enough, should be part of the consideration here.
Weller: That is why we have gone from passive to active [sensors] because we don’t want constant ‘pinging’.
Hartley: The drivers are highly trained to look in their Class VI mirror and we are almost trying to remove their ability to be professional drivers: ‘I can’t move because that alarm has gone off even though I can see everything is alright’.
Weller: I have driven a truck through London so I know what it’s like. Sometimes you might not check your mirror before moving off for some reason and that is how fatalities can happen. This is a safeguard – I’m not questioning the drivers’ professionalism and I know what they go through. But this alarm is a failsafe that may just save a life.
Lee Anderson, transport and assets manager, Menzies Distribution: If the driver is going to ignore the mirror, why would they take notice of a proximity warning? Cooling: This device will appear in the GSR [the EU’s General Safety Regulations] in 2024 and the vehicle parc changes naturally. You asking the industry to retrofit all of this seems pretty flawed to me.
Mike Bennett, legislation engineer, DAF Trucks: One problem is that when we replace mirrors with a camera system you don’t get a Class VI mirror, you get a MOIS or an additional camera that takes away the need for it. The other problem is if you’ve read reg 159 it is not achievable by the aftermarket. That is regulation that covers homologation of new vehicles.
Milton: It is interacting with the other vehicle systems, so to retrofit things like interactive radar systems is inordinately difficult. Trying to bring it forward too quickly is in danger of hobbling the market. If this came in in London a lot of transport wouldn’t be able to run.
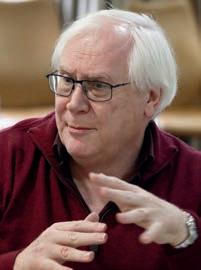
Garry Lewis, transport standards manager, Tarmac: If we are talking about retrofitting 165,000 vehicles in 16 months that is 10,000 a month.
Emily Hardy, UK marketing manager, Brigade Electronics: We are recommending in our consultation feedback that TfL looks at some of the systems out there being honoured for longer, because if people are putting vehicles on the road at the moment and fitting the equipment do they have to strip it off by October 2024 and replace it?
Natalie Chapman, head of public affairs, Logistics UK: It is really important that if businesses are making this investment that it is safe and effective and actually improves road safety, rather than contributing to driver distraction. Reviewing the Safe System and upping the standard is good in principle, but one thing I am concerned about is that we don’t know what proportion of sensor systems are passive rather than active, and therefore how many of the systems that are being fitted in good faith will have to be ripped out and replaced. Has that cost-benefit analysis been done on the impact it is going to have on industry? Lots of fleets have been fitting this kit even before DVS, whether that’s for FORS or just to do the right thing, and to say ‘sorry, your heart was in the right place but you have to rip it all out and replace it at huge additional cost’ sends the wrong message. Yes, up the standard, but do we confine it to new vehicles, so if you’ve already got systems fitted and have a permit can you continue to run it for the life of that vehicle because it is a significant investment?
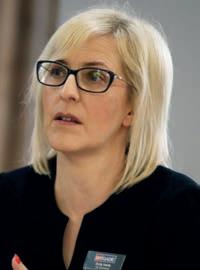
Polyviou: We don’t know exactly how many active and passive systems there are out there and that is a question we are asking, but we have an indication from the operator survey we’ve shared that some of you have filled in for this work.
Lewis: The majority of the vehicles our hauliers are ordering now still have passive systems. Active systems aren’t part of our standard spec and hauliers are asking if the Volvo system will meet the requirements. We are saying ‘put money aside because it looks like it won’t meet the requirements’, yet this is OEM-fitted equipment that is better than a lot of the cheap aftermarket stuff on eBay. We are heading towards what could be a big mess if we aren’t careful.
Nigel Ponton, engineering manager, Cemex: Financially this could be an absolute horror show. You are talking about making it very difficult for people who are already struggling to make a living.
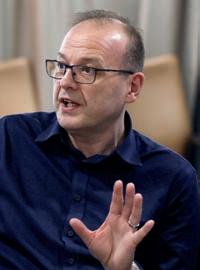
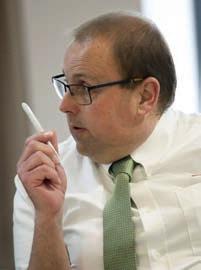
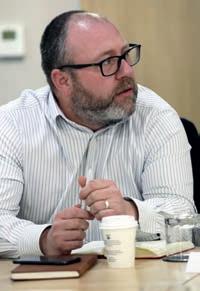
Hartley: Even for large operators like DHL Tradeteam this just makes everything on the shelves more expensive for the population of London. There is also a danger of fragmented schemes in different cities so we will end up with a fleet that is fit for London but not Birmingham or Manchester.
Lewis: One big thing that FORS managed to do was simplify the safety standards for trucks – before FORS, Tideway wanted this and Crossrail wanted that. We got that down to a single set of safety equipment and this is moving away from that ethos and defeating what FORS did. I am leading the GSAG group which is looking at FORS version 7 to try and bring these things into line, but it is a nightmare trying to get the wording right so we have a single standard that works for London and Glasgow or Inverness.
Polyviou: We have to strike a fine balance between adopting new safety technology and hearing all the concerns about cost. We are fully aware of the fine margins the industry is operating on.
Weller: We are also looking at the user experience when it comes to applying for permits, based on the feedback we have had from industry. We recognise there are a couple of issues and want to make the process easier.
Chapman: There are a couple of existing issues, one of which should have been in place when DVS first came in, which was a look-up tool. At the moment if any operator wants to find out if any one vehicle on their fleet has a permit and what star rating that vehicle is, they have to plough through their emails. What they want to do is type in the vehicle reg number and see if it has a permit and the star rating. Operators tell us that if in doubt they just put in another vehicle permit application.
The other issue is the upload time for DVLA data –operators are constantly bringing new vehicles into their fleets and if they have the minimum star rating or are fitted with a Safe System they shouldn’t be keep- ing that vehicle off the road for a week or two because there is an admin issue. Perhaps there should be a period of grace to bring a new vehicle in as long as, if it is stopped, it has all the equipment fitted.
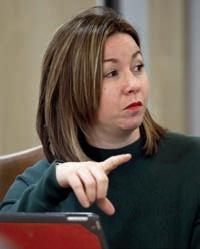
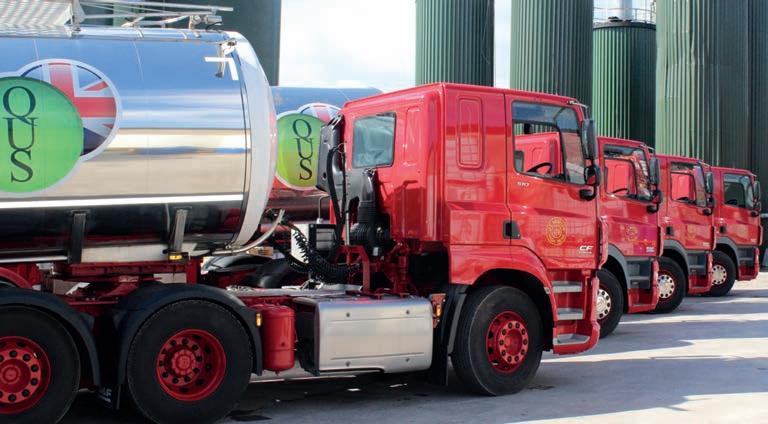
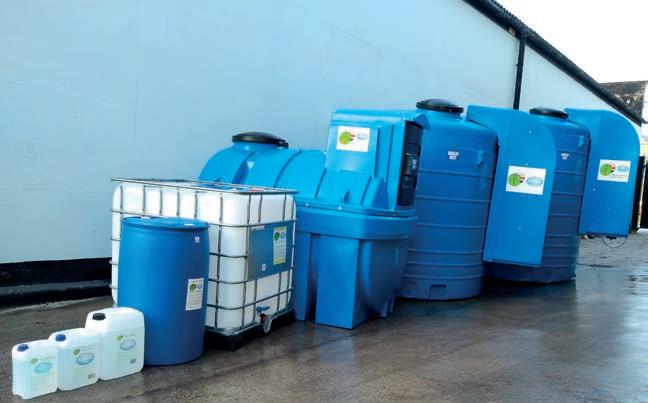
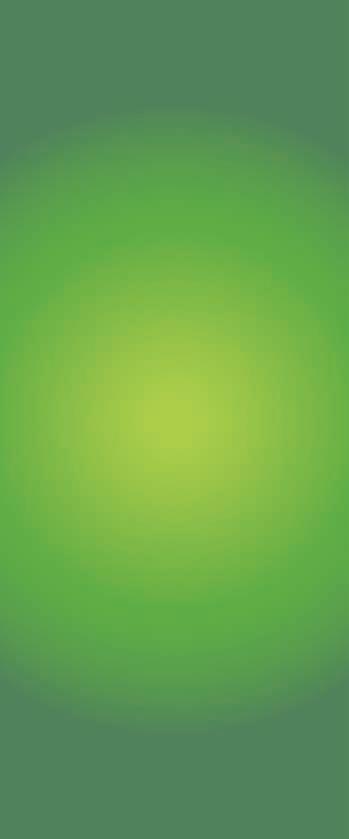

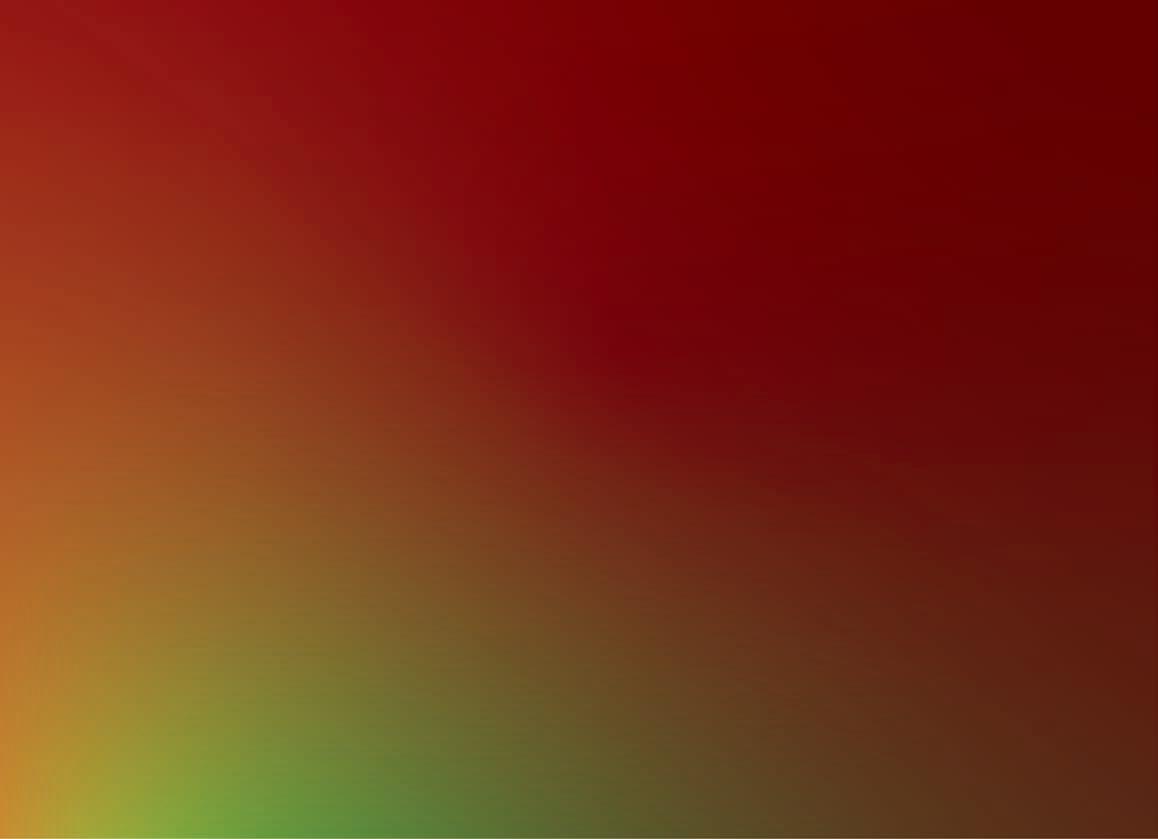
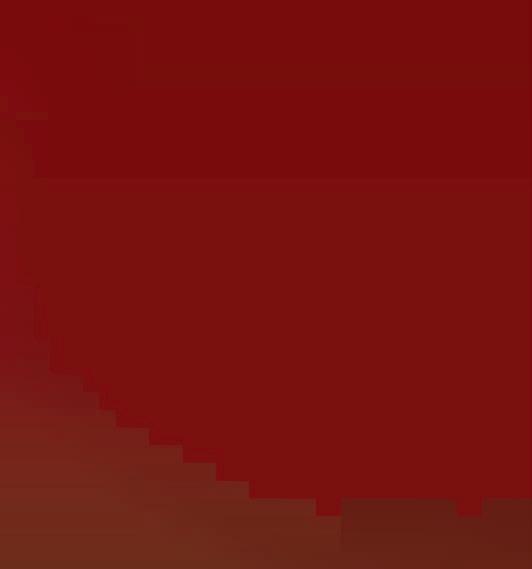

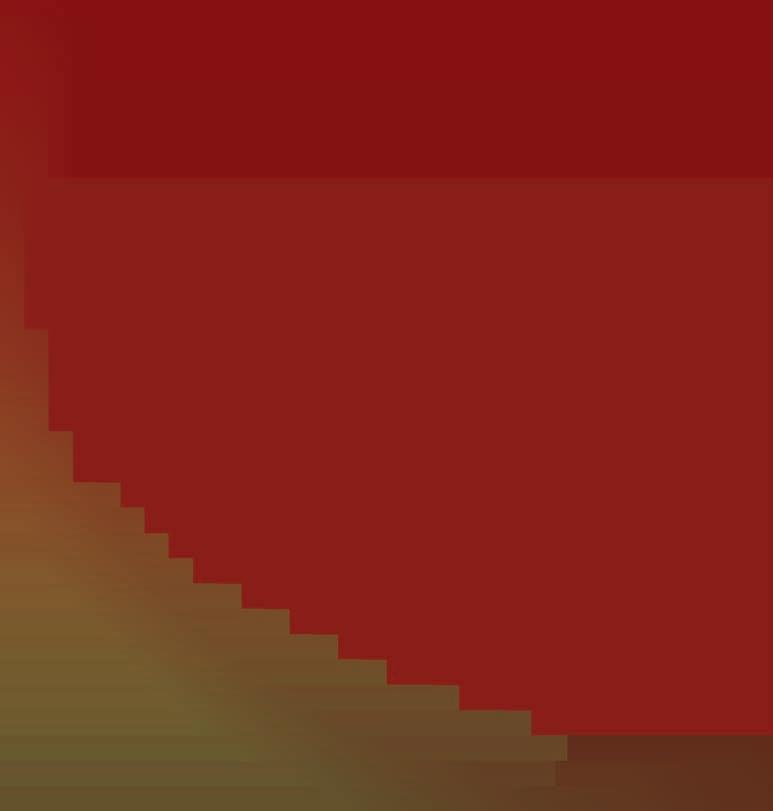
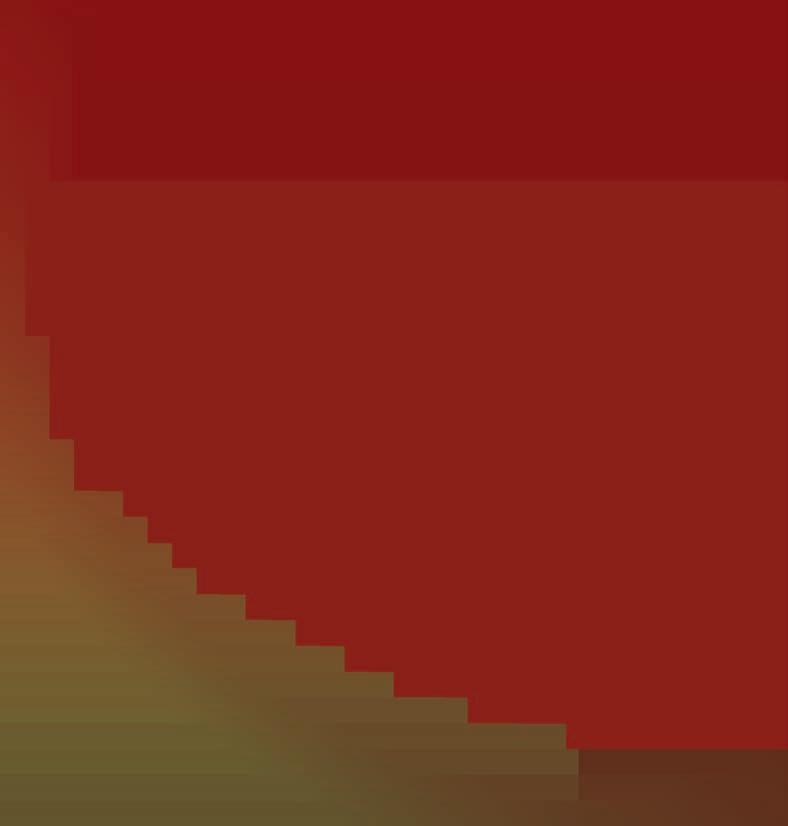
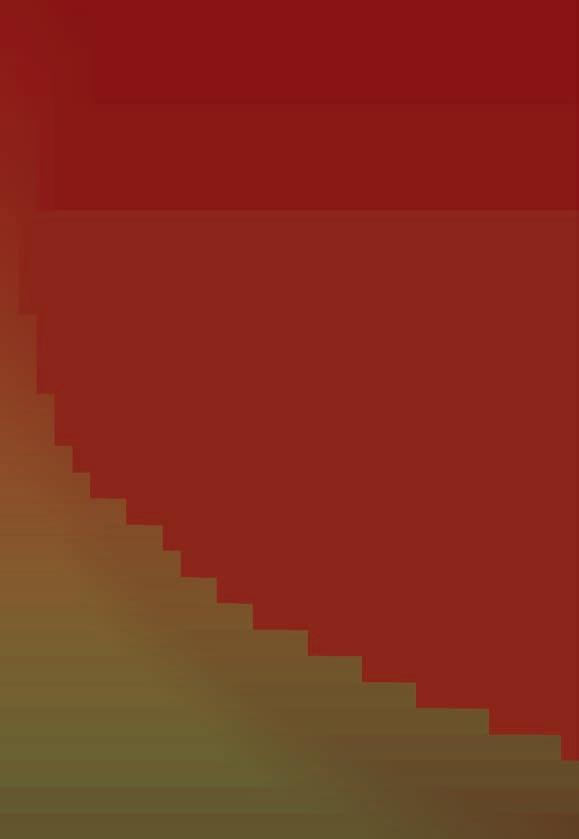

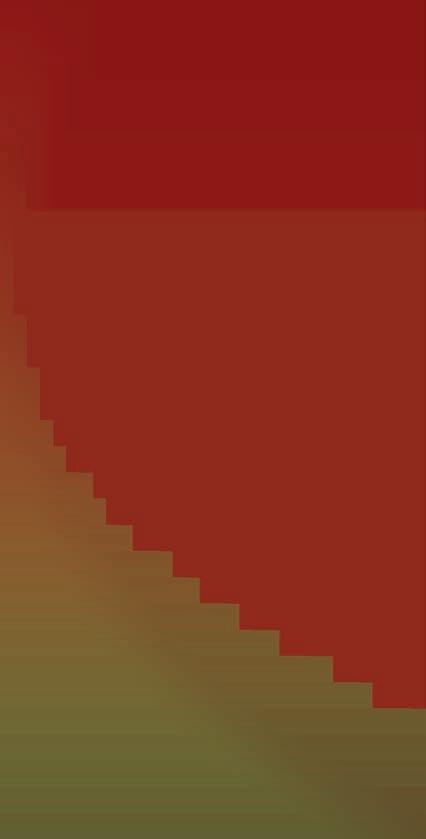
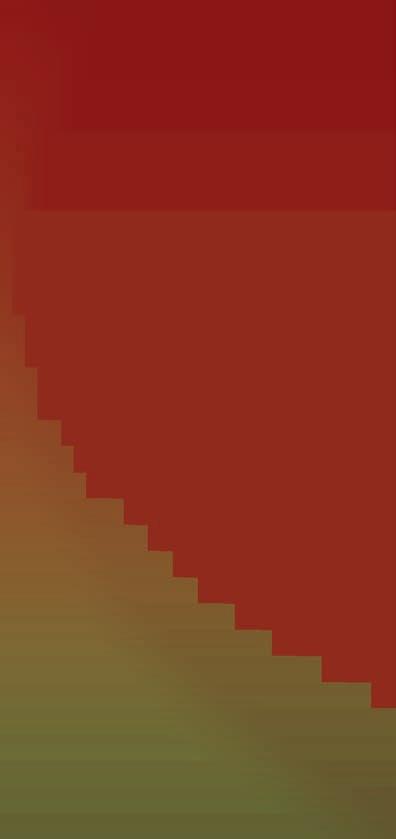
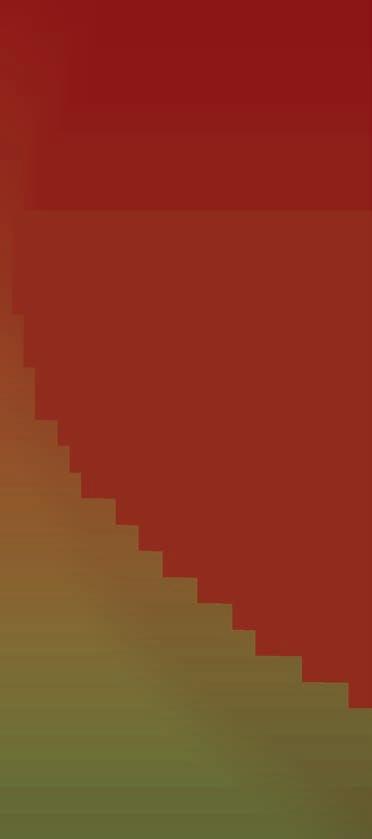
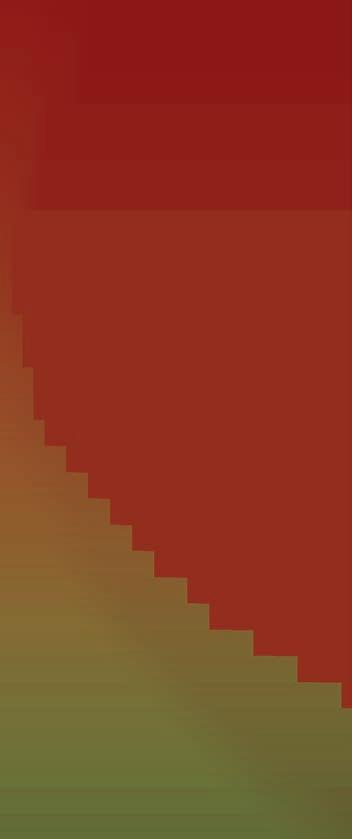

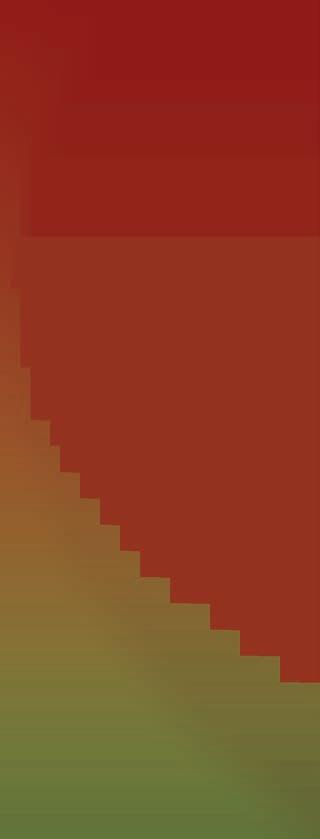

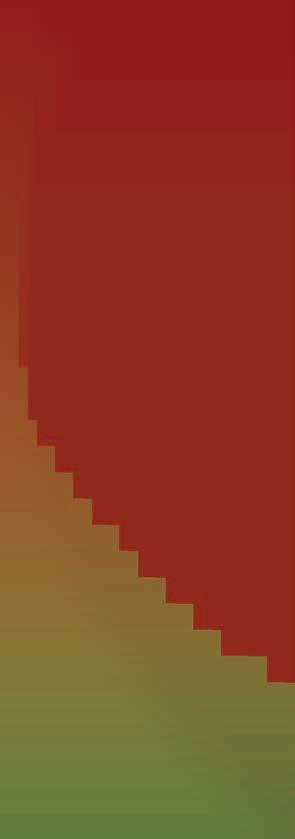
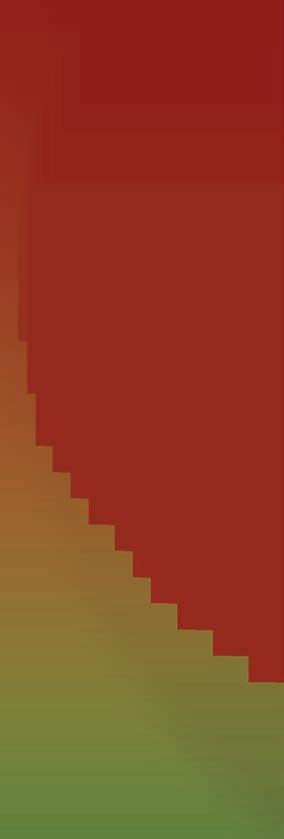
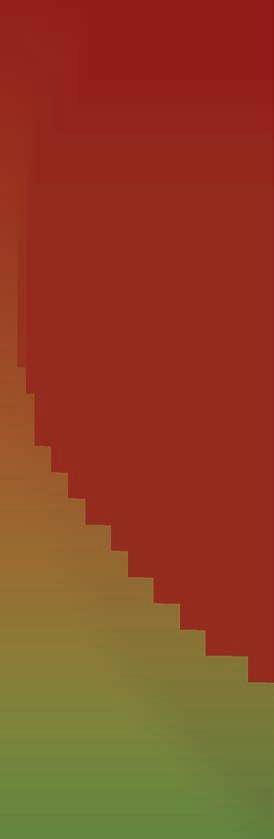


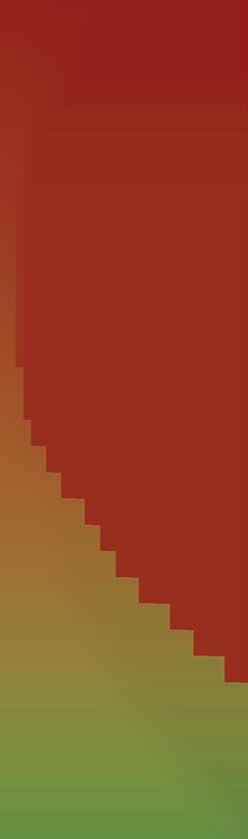

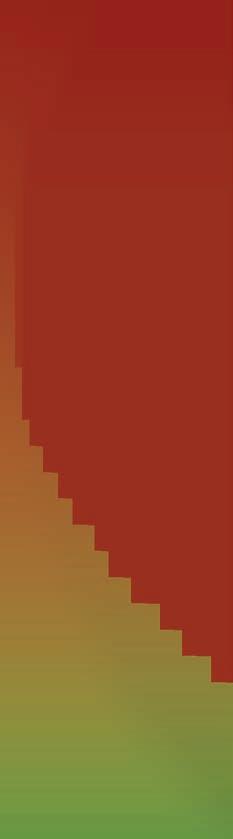
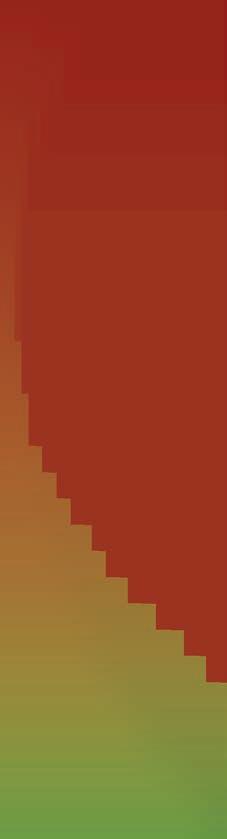


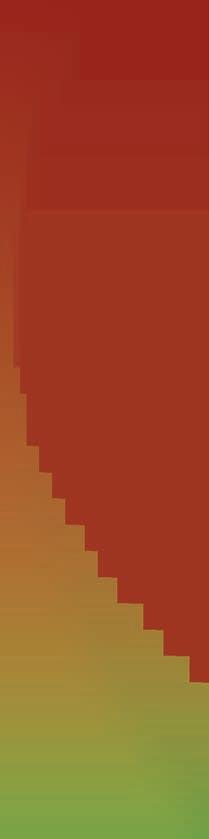
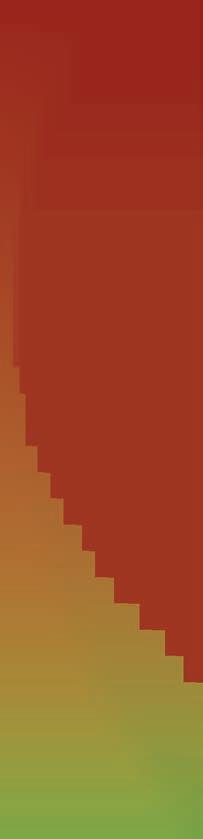
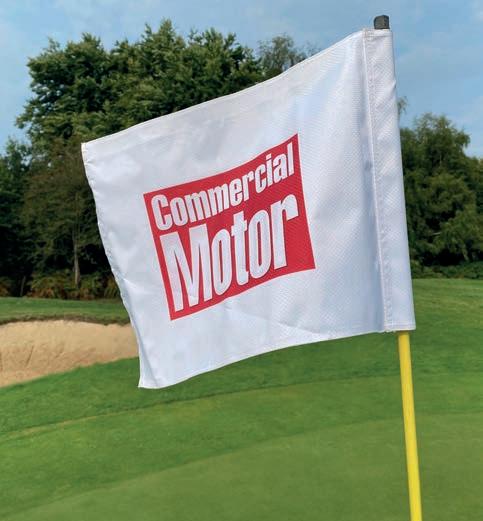
There just seems to be a lot of unnecessary admin and operators need to be given a bit more trust.
Richard Bimson, MD, Bimson Haulage: How much does TfL spend on direct vision? The reason I ask is that this is a two-sided debate. We are looking at it from a haulier and driver perspective and everybody wants to do everything we can to improve safety. What is the mayor spending to educate vulnerable road users about HGVs? Polyviou: A good point. We have a whole team working on VRUs and cycle safety and they do a lot with industry. They go out to schools and I can give you a list of examples.
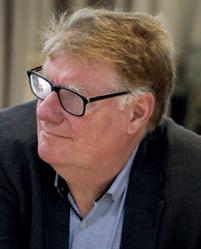
Nick Simmons, CEO, RoadPeace: RoadPeace is a member-led charity for road crash victims and they campaign to make sure no one else goes through what they have been through. Education is an important part of that but getting the message across is difficult. People don’t think about this enough and don’t always engage in the conversation, but when they do it is incredibly powerful. TfL is playing a very responsible role here.
Hobson: I would now like to introduce James Ashford from Brigade Electronics to tell us more about what the proposed Progressive Safe System might look like. Ashford: The current Safe System requires proximity sensors, left turn camera, in-cab audible system and left turn audible alarm. Brigade classes all its sensor systems as active rather than passive because they give a warning to the driver and do not depend on the driver having to look at them. The proposed changes will involve quite a significant investment and while no one is in any doubt that the technology will be of benefit we have to balance the cost versus benefits. From 2024 the nearside camera must eliminate blind spots, active sensor systems must be fitted to semi-trailers, sensors on rigid vehicles must have a range of 2m and a MOIS must be fitted with a range of 2m in front of the vehicle.
On rigids the requirement will be that sensors do not pick up street furniture and that is something that was an issue with the old side detection systems.
We do have an AI-led side detection system that eliminates a lot of the issues put forward by TfL. It is always on if the vehicle is doing more than 20mph and can differentiate between static and moving objects. It will also intensify the audible and visual warnings to the driver as an object moves into the danger zone and a collision becomes increasingly likely.
On artics, sensors must ensure full coverage of the nearside of the tractor and the trailer with a range of 2m of lateral coverage. There are new technologies out there, including our Radar Predict launched in April, that can be fitted on the nearside of the tractor near the fuel tank and look down the whole length of the vehicle including trailers. Technology is coming on in leaps and bounds and installation time is around two hours as opposed to six to seven hours for a traditional side scan system.
There are areas of concern highlighted in our consultation response. The first is the GSR regs 151 and 159. TfL mentions a 2m range but reg 151 contradicts that and says 4.5m so that needs to be cleared up.
Hobson: Here’s Mike Bennett from DAF Trucks. Bennett: DAF Trucks is market leader in the UK with a share of 31%, which means we have the biggest pool of vehicles that require certification or equipment.
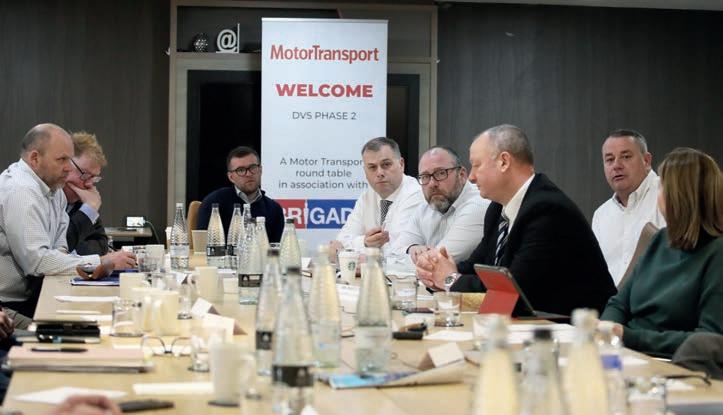
Since 2019 we have provided 25,000 individual certificates of star ratings as well as providing details of over another 150,000 vehicles via mass uploads to TfL. The problem there is that we supply that data as a VIN and a star rating which is what TfL has asked for. However, when you go to look for your vehicle on the system it will ask you for the vehicle registration number, which as a manufacturer we are not especially interested in.
Part of our request to TfL is that the look-up data is in line with the data it requests from us. Every vehicle is uploaded when we get a certificate of conformity but every day I get at least 20 enquiries saying ‘my vehicle is not on the system’. It is – but not under the registration mark so we end up doing twice as much work. We don’t want customers to wait eight weeks for the DVLA and TfL data to correlate so you can get your permit. So we have asked for a grace period of six to eight weeks so the data can correlate. TfL’s current online tool is not fit for purpose and needs a complete overhaul.
The New Generation DAF was introduced in 2021 with a view to both the GSR2 standards and the TfL DVS scheme. Most can meet three stars and some five stars. We have a UK-specific 4x2 tractor unit based on the XD that is the only vehicle in the industry that can achieve five stars without a low-entry cab.
The XG flagship truck can achieve two stars but will need additional equipment to meet the Progressive Safe System. As we move to GSR2 the vehicle will already have the necessary equipment fitted from the end of this year and we want to make sure GSR2 and the Progressive Safe System are aligned, because we do not want to be fitting even more equipment on top of the GSR2.
The LF too can only achieve two stars but we will start fitting the GSR2-compliant equipment from November this year. The UK DfT is somewhat behind in implementing EU rules into UK law so we don’t expect it to be at the same time, but we would like DVS to be in parallel with GSR2 as that is just common sense.
We estimate there are at least 211,000 vehicles with permits which will expire in October 2024, and every operator will have to reapply for a permit by showing the vehicle is rated at least three stars or has a Progressive Safe System fitted. It will be really difficult in 16 months.
What about cost? TfL’s own impact assessment puts the cost to operators at anywhere between £135m and £1.48bn, which is an unbelievable cost. There has to be some way of staggering the implementation process to enable the industry to support that level of cost. Nowhere in your impact assessment did you consider the effect on manufacturers, which was very short-sighted.
Polyviou: This was not a TfL impact assessment, it was done by an independent consultant commissioned by TfL and they were in touch with industry, and some of the people in this group have fed into this.
Bennett: There is a proposal to bring retrofit equipment within reg 151 but it is not in writing at the moment. The way the rules are written does not include retrofit components but that will be brought in, probably as an extension to the approval.
Hobson: Thank you to our presenters and to everyone for taking part in the debate. n
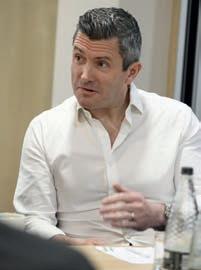
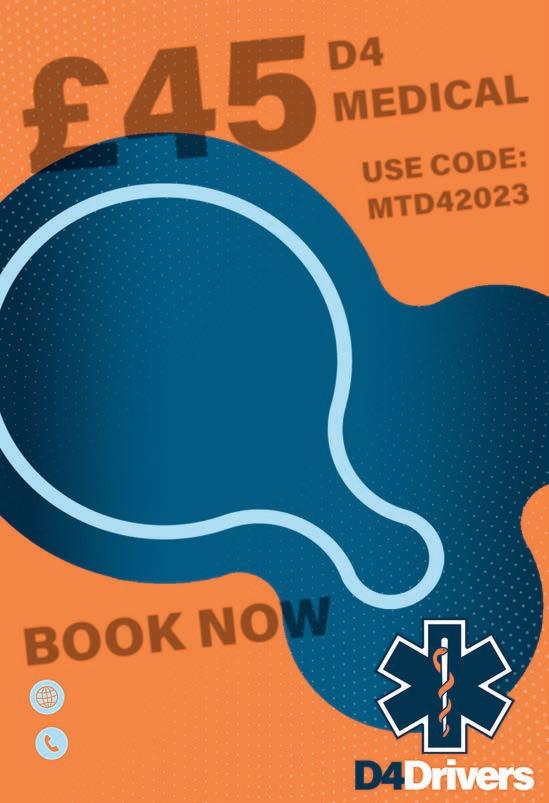

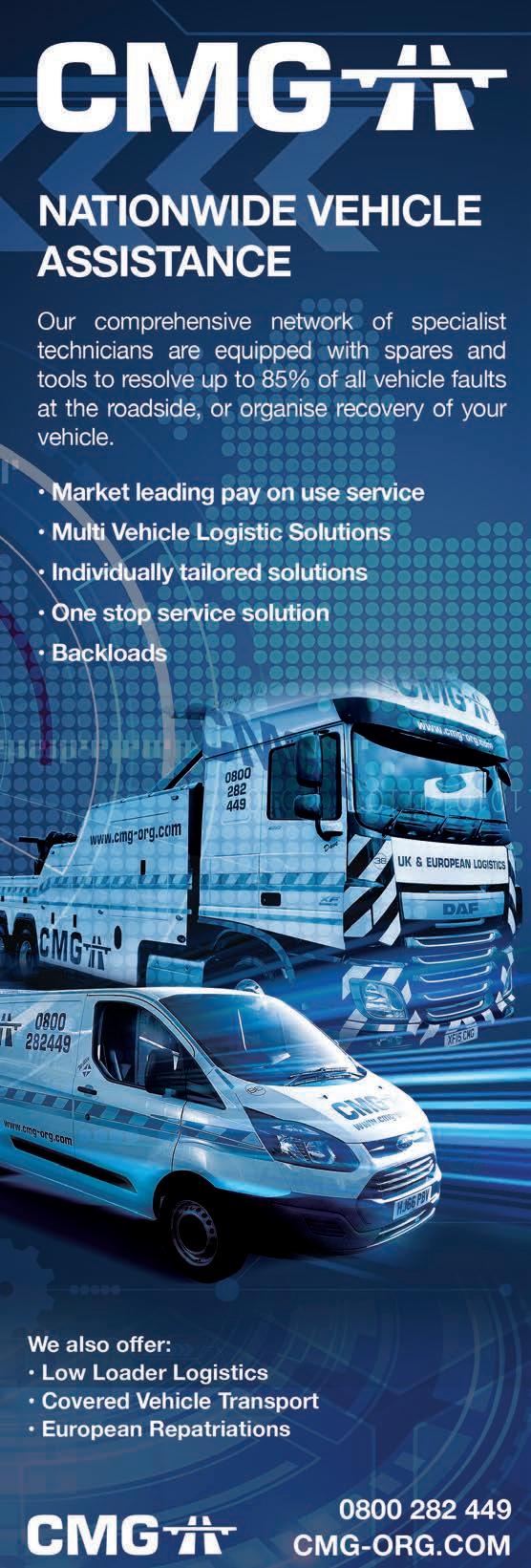
Electric gritter from Econ Engineering
Econ Engineering has launched a new electric gritter truck designed for year-round operation.
The 19-tonne Volvo FE Electric 4x2, which is the first model in the Yorkshirebased company’s ‘Econ Zero’ range, features a range of demountable body options, allowing it to seamlessly switch between fleet roles while maintaining zerotailpipe emissions. This flexibility is possible due to Econ’s innovative Electric Quick Change Body (E-QCB) system. Developed in-house, the E-QCB utilises hydraulic rams to enable the vehicle to switch between demountable bodies in just 15 minutes, all controlled by a single operator. This system allows for the supply of different bodywork options, including a gritter body for winter maintenance, a tipper body for highway maintenance, or a cage tipper for refuse collection and recycling.
The truck was a close collaboration between Econ Engineering’s R&D team, product specialists from Volvo Trucks UK & Ireland, and supplying dealer Crossroads Truck & Bus.
Jonathan Lupton, MD at Econ Engineering, said: “The vehicle operates best in urban environments, where daily mileage is typically less than some longer distance motorway routes. As it is easy to switch body types with this model, customers can benefit from operating the vehicle all year-round. We are committed to evolving our Econ Zero range, and other renewable energy innovations, as the UK’s infrastructure develops in support of this.”
The FE Electric, which recharges in just 2.3 hours with a 150kW DC charger, has a range of 150 miles. It features two electric motors and a 2-speed gearbox.
Christian Coolsaet, MD of Volvo Trucks UK & Ireland, praised the collaboration, emphasising the importance of achieving net zero in all sectors, including winter maintenance.