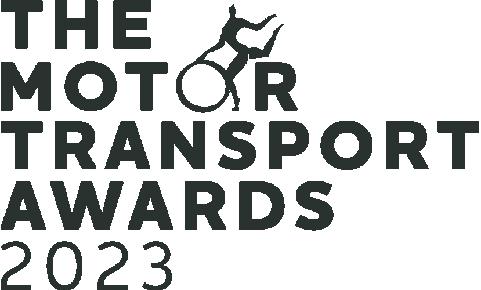
3 minute read
Best Use of Technology Award
Partnered with
JM Clark
Advertisement
JM Clark’s AIOne solution provides real-time visibility into operations, enabling better decision making and streamlining of business processes. The AI-based route optimisation algorithms allowed the business to reduce the time spent on route planning, invoicing turnaround time and paper-based processes.
The platform’s cost effectiveness has helped improve their bottom line, and reduce environmental impact. Created with Omnia Smart Technologies, AIOne has addressed operational challenges such as manual processes, allowing the company to improve its cashflow by invoicing promptly and reducing costs through better route planning.
JM Clark implemented the technology because of its comprehensive planning and scheduling tool; driver app; electronic proof of delivery; and its digital job and customer management. The business now has full visibility and control of live and historic data.
“Using tailor-made technology to overcome problems, reduce costs and step away from manual processes is first-rate,” said judges.
Palletways
Initially born from the operational need to capture and harness accurate data on individual pallets instantly and on the go, Palletways ID is the result of two years of research and development to deliver greater real-time visibility and information on health and safety for staff and customers.
Palletways ID has developed the world’s most sophisticated forklift truck-mounted sensor technology that combines four key data collection elements, with imaging, barcode scanning, weight measurement and cubing/dimension measurement in one, while the forklift is in motion. Sensors capture the weight and measure each pallet’s side and height for cubing and automatically store the data. Palletways ID has successfully flagged more than 7,000 pallets weighing over 1 tonne, a significant boost to health and safety. The system also flags any discrepancies on size or weight.
“A great efficiency improvement with clear health and safety benefits,” said judges. “A great combination of technologies being used to improve accuracy and decision making.”
Prohire

Prohire launched an in-house division called ProGreen to support its operations and help the firm move into alternatively fuelled vehicles. After working closely with their client, Wiltshire Farm Foods, ProGreen decided to develop a 100% electric temperature-controlled van.
Turning to suppliers CoolKit, GAH, Geotab and Trailar, the electric fridge van, capable of reaching temperatures as low as -18C, was built on a Maxus eDeliver 3 platform returning a 150-mile range and 600kg payload. It is capable of making around 60 delivery drop offs per day and, based on a normal mileage of 20,000 miles per year, is estimated to save 5 tonnes of CO2
ProGreen and Wiltshire Farm Foods have full visibility of the electric van’s performance thanks to its telematics system. Importantly, Prohire’s ProGreen division is about “more than just acquiring vehicles,” and aims to support businesses as they transition to alternative fuels.
“ProGreen has made a great leap forward on the journey to electric vehicles,” said judges.
Stobart
Communication issues made apparent during the pandemic led Stobart to better engage with its drivers, improving their access to important tools and information through the creation of a bespoke app.
The ESL Connect App has been developed in partnership with Enterprise and supports the operational delivery of Stobart’s network. The app has enabled the business to plan in real time thanks to the reporting of driver absence, holiday bookings, shift swaps, and other planning matters. Drivers are also able to report wage queries 24/7 and can receive important notifications.
“So many processes and functions have been combined. Although the app is nothing new, the rollout and functionality shows how Stobart is utilising technology to improve the business efficiency,” said judges.
Vantec
Autonomous HGVs have been widely discussed for several years but working examples of the technology are few and far between. Vantec, however, can lay claim to having not only developed a proof of concept, but made the project operational.
Their V-CAL (Vehicle Connected Automated Logistics) 5G Automated Logistics project created a network on a 500m private road between Nissan Motor Manufacturing UK’s (NMUK) site and Vantec’s Turbine Business Park site and deployed a self-driving EV truck that delivered parts to NMUK autonomously using a remote control teleport rig.
The next stage of this project aims to create a safe, autonomous supply chain as well as contribute to decarbonisation and will move from one self-driving HGV to three, in which one tele operator will monitor and control remotely to transport product to NMUK. Judges said: “A company with an eye on the future making a contribution towards decarbonisation.”
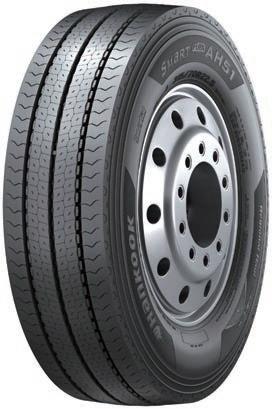
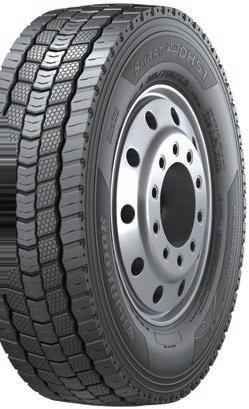

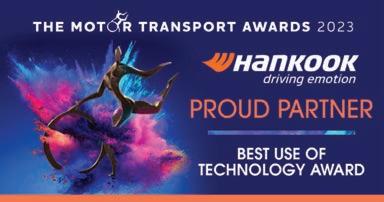