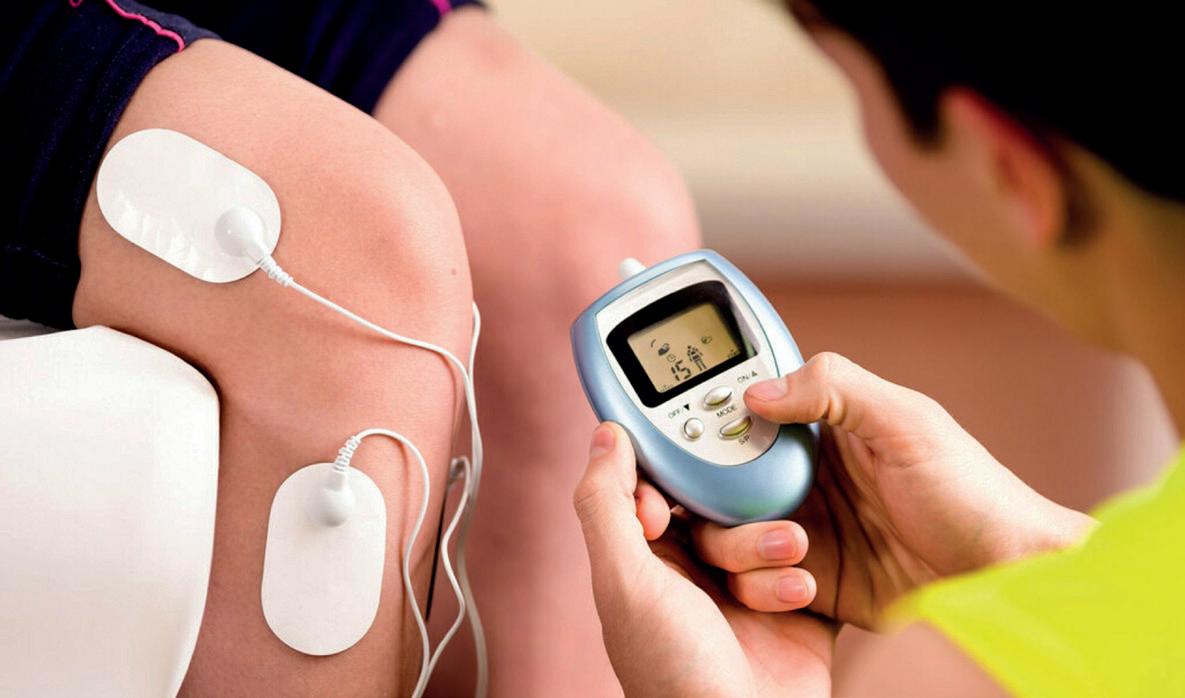
6 minute read
Elastomerics
from MPN EU Issue 67
by MPN Magazine
MATTHEW BONGERS, PRODUCT DEVELOPMENT ENGINEER, AND AUDREY SHERMAN, DIVISION SCIENTIST, FOR 3M MEDICAL SOLUTIONS DIVISION HIGHLIGHTS THE IMPORTANCE OF ELASTOMERIC ADHESIVES
Can tapes nlock INNOVATION? INNOVATION?
Tapes are often viewed as a simple material, secondary to device function. They don’t power a medical device and don’t compute, store, or display any data. While all true on the surface, these assumptions are rooted in a crucial misconception.
When a closer look is taken, it becomes clear that tapes are a critical part of enabling a device to function as it’s intended. Tapes can adhere device components together and stick the device to the skin, doing both for the device’s intended wear time. When either of these functions fails, the device could fall apart or detach from skin, aff ecting its ability to help the person using it to transform their health.
Not just any tape will do, especially when sticking to skin. Tapes with elastomeric backings – ones that can stretch, recover, and then stretch again – make many modern devices capable of functioning the way they do and the potential for future innovation possible.
TAPES HELP MAINTAIN SKIN HEALTH
Tapes must accommodate unique challenges to be successful, regardless of their function in the overall device design. If they’re holding components together, they must do so without interacting with other materials or the device’s ability to track data.
If they’re sticking a device to skin, they need to have an elastic and breathable backing, which allows the skin to breathe and expel moisture while stretching and fl exing just as skin normally would, all the while holding something that very much does not stretch – like a rigid backing or device – on top of it. This is where elastomeric tapes can really shine.
Skin may reject whatever is stuck to it by forcing the tape off or react to it by developing a rash or other irritation. The device’s ability to reliably fulfi l its duty then diminishes.
Creating next-gen devices requires that tapes be designed into the system early. Selecting the best one should start with reframing the tape’s performance criteria from what properties the tape needs to possess to a more holistic approach: what the device needs to achieve. Your materials partner can better identify options that serve the device’s entirety, rather than options that meet a narrower set of expectations.
TAPES HELP SAVE ON HEALTHCARE COSTS
When a tape cannot perform the way it needs, there’s a domino eff ect that goes beyond a singular layer.
It could mean data is no longer reliable or being collected. The person using the device then cannot track their health status and adjust their behaviour when needed. Their care provider can no longer use that information to consult and treat. Health could worsen and additional care may need to be sought.
When tapes are performing optimally, they can allow longer device wear times and maintain skin health. Health statuses can be tracked, and therapy extended from the comfort of homes. And the body’s largest organ can function, without being jeopardised by something meant to help it.
TAPES HELP USHER IN IMPROVED DESIGNS
It’s not enough to create a device that reliably and accurately tracks the data it needs to track. It also needs to accommodate the end user’s preferences and fi t into their daily lives as seamlessly as possible.
Tapes have the potential to help solve some of the toughest design challenges. They can off er more fl exibility in slimming down profi les and weight because they take up less space than mechanical fasteners. Elastomeric tapes can make devices more comfortable to wear and stay adhered longer because of their ability to stretch and move with the skin.
In a world with rapidly transforming devices, designs need to be innovative and utilise all the advantages they can to make it to market successfully.
OLIVIA FRIETT SPOKE TO BIANCA CARVALHO, ASSISTANT MANAGER OF SALES, KURARAY, TO DISCUSS MEDICAL TPE GRADES
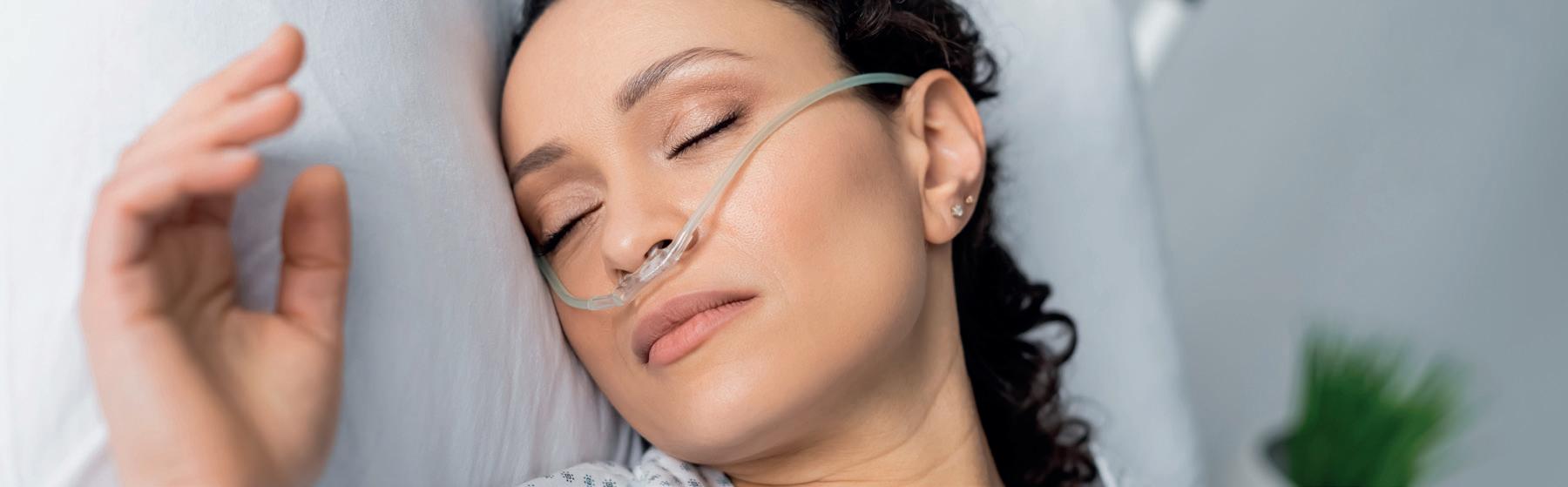
All STR TCHED Out
With so many different thermoplastic options, it’s difficult to know what’s best for different medical devices.
Elastomers specialist, Kuraray, has been in the business for 96 years. The company has been producing styrene block copolymers since the 70s, as well as having over 20 years’ experience with HYBRAR material in medical application for flexible PVC replacement.
HYBRAR POLYMER
HYBRAR is a special type of block polymer. It has vinyl content in the chemical structure, so the materials allow a much better compatibility compared to polypropylene.
Bianca Carvalho, assistant manager of sales, Kuraray, explained: “This is a very soft block polymer. You can produce a TPS compound based on the mixing of the polypropylene or some polyolefins with the HYBRAR without the need to use a plasticiser. This is one of the biggest advantages of HYBRAR.”
THE SEPTON 4000 SERIES
The Septon 4,000 series is also a little different from the conventional block of polymers. The conventional one is known as SEBS structure where there is the hard block based on isoprene and middle block based on butadiene. “With Septon 4,000 series, we have a mix of butadiene and isoprene on the soft block. This allows to have a polymer that has better elasticity. It also allows the material to absorb and hold more oil, so you can increase the oil amount in the TPS application.” Carvalho said.
“We also have Septon 4033, this has one of the best transparencies in the market. TPS compounds are usually translucent, but Septon 4033 is transparent.”
The Septon 4000 series has the biocompatibility test for cytotoxicity and skin sensitisation, pyrogen and blood compatibility, so that it can be used in the medical sector.
Carvalho noted that some of the benefits of Septon 4000 in comparison to other SEBS include higher oil absorption and retention, higher tensile strength, and good elongation.
THERE ARE MANY TPE OPTIONS TO CHOOSE FROM
There are several categories of different types of Thermoplastic Elastomer (TPE) - inside the TPE you have TPS, TPU, TPA, TPV etc.
“We have a good compatibility with general materials like PP. You can have a solvent bonding, but you can also hand bond with other polypropylene based particles like connectors without any issues.” Carvalho explained.
“With TPV, you mix a polypropylene base with EPDM, and have a crosslink material together with the polypropylene, whereas with the TPS, you basically only have thermoplastic materials. You don’t have a rubber, such as EPDM. So, with the TPV, there’s always this crosslink in one of the polymers.”
REGULATION
Carvalho stated that Kuraray’s biggest challenge is related with the European Medical Device Regulation. The regulation becomes more and more restricted over the years, and this affects a lot of the supply chain itself, and the raw material.
Carvalho said: “With the challenges that we’ve had in the past two years for the supply chain, we can’t easily make adjustments, like raw material. For the medical sector, this created some disruptions. We were luckily able to avoid negative impact, and we had no impact at all in the supply chain for medical customers. I think this is something very important.”
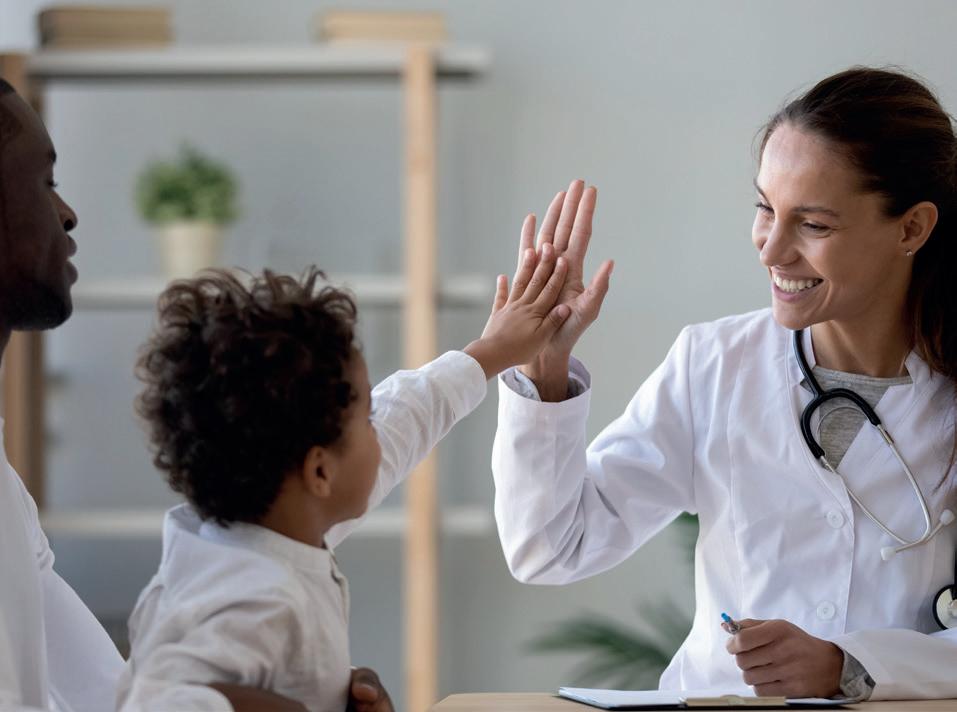