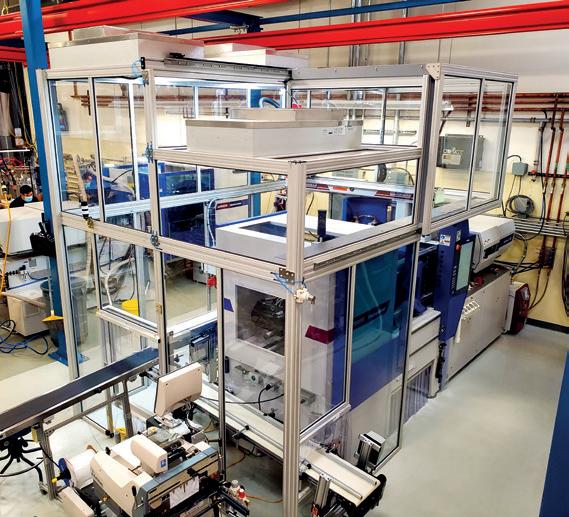
5 minute read
Digital Spy
from MPN EU Issue 67
by MPN Magazine
ACCREDITATION UPDATE
https://www.freudenberg.com/#
FREUDENBURG ANNOUNCES TUBING FOR BIOPROCESSING
Freudenberg Medical, a manufacturer of medical and pharmaceutical devices, components and tubing, has introduced HelixFlex, a thermoplastic elastomer tubing designed for use in pharmaceutical and biopharmaceutical applications.
“With HelixFlex, we complement our siliconebased HelixMark and PharmaFocus Premium tubing lines and therefore continue our journey of providing additional products and technologies to our pharmaceutical and biopharmaceutical customers as a one-stopshop. HelixFlex is the next critical milestone in that endeavor.” states Rüdiger Gall, general manager & director corporate marketing at Freudenberg Medical.
The recently introduced HelixFlex high purity thermoplastic elastomer tubing adds to Freudenberg’s existing pharma product portfolio of silicone tubing and fl uid transfer products for bioprocessing, drug and vaccine manufacturing, fi lling and sampling, peristaltic pumping, laboratory, and medical device applications. EXTRUSION UPDATE
https://www.ptaplastics.com https://p-r-i.org/medaccred/
PTA Plastics receive MedAccred accreditation
PTA Plastics, a plastic injection moulding company, fi rst learned about MedAccred accreditation when plastics assembly was being phased into the programme and the company grasped the opportunity to take part in the pilot, helping to create the audit criteria.
“As soon as we heard about the MedAccred programme of accreditation we knew it could help us build on our existing relationships in medical devices and open doors with new customers,” says Greg Fish, PTA corporate director of quality.
“It is very detailed and quite daunting, but as we did the preaudit self-assessments and began to understand the criteria, we sorted out a manageable plan to progress quickly through the stages.”
Signifi cant process improvements were made because of the audits. PTA Plastics reduced fi nishing defects by 86% and reduced internal scrap from 2.78% to 1.81% of parts produced.
EXPANSION UPDATE
https://helmee.com
HELMEE IMAGING ANNOUNCES OPENING OF ITS US BASE
Helmee Imaging, a developer, manufacturer and marketer of unique CSD imaging technology for challenging surface inspection applications, has launched Helmee Imaging, Inc., a wholly owned U.S. subsidiary based in Cumming, Georgia. The new company will provide sales with technical and application support for its customers throughout North America.
“The customers we work with have increasingly demanding needs for surface quality inspection where traditional methods, such as cameras or human visual inspection, do not work reliably or quickly enough,” said Juha Saily, regional development manager for Helmee Imaging Inc. “Our CSD technology off ers higher resolution, more accurate inspection results and higher throughput than human visual inspection. It is the only inprocess inspection technology that works on parts with that works on parts with complex geometries and complex geometries and mirror-like surfaces.” mirror-like surfaces.”
CSD (Covered Stereo CSD (Covered Stereo Defl ectometry) is a Defl ectometry) is a patented machine vision patented machine vision technology that enables technology that enables automated quality inspection of fl at, curved and complex parts with highly refl ective and clear surfaces. CSD can detect virtually any type of microscopic and larger 2D and 3D defects.
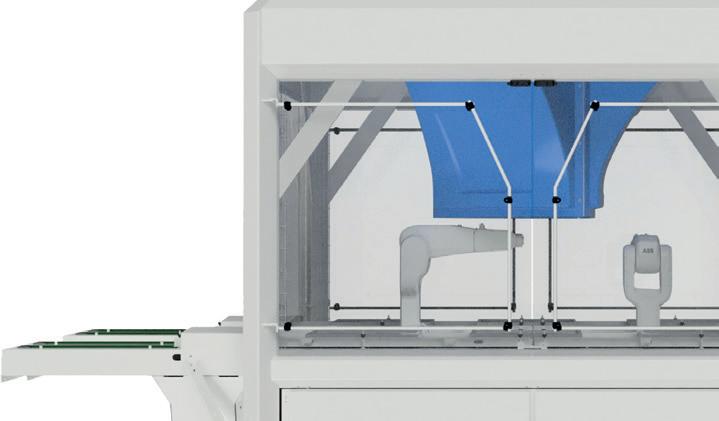

https://www.aim3d.de/en/ AIM3D presents the Voxelfill process
With the Voxelfi ll process, AIM3D is overcoming inhomogeneous strength issues by achieving defi ned, selective densities in the component.
By using the 3D extrusion technology of the CEM process, AIM3D has developed a Voxelfi ll strategy that overcomes these limitations and increases the cost eff ectiveness of the CEM process. Voxelfi ll can also be used for multi-material components and is suitable for constructing 3D components using plastics, metals and ceramics.
With the Voxelfi ll approach, components are no longer created exclusively in layers, but utilise crosslayer fi lling by using so-called voxels as volume areas.
The Voxelfi ll strategy comprises two process stages: 1. Generation of a lattice structure: the CEM system repeats this structure up to a defi ned
THERMOPLASTIC UPDATE
height of the volume elements, then at this point the previously created cavities are fi lled by injecting thermoplastic material with the extruder 2. Filling phase of the voxels: now the more important component of this 3D printing strategy is deployed: when the volume areas are fi lled, this does not include fi lling all voxels in one plane.
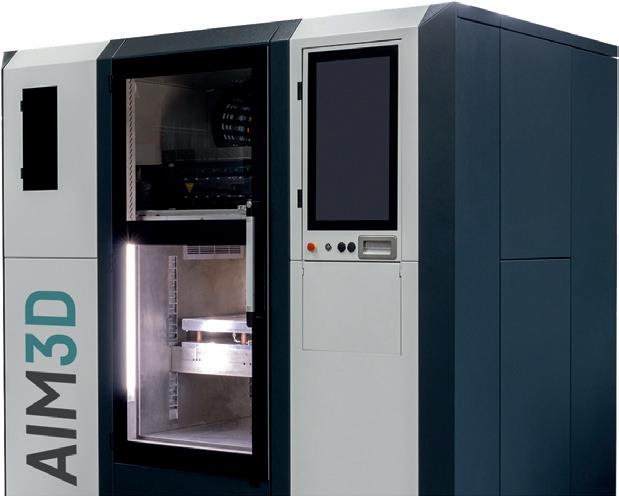
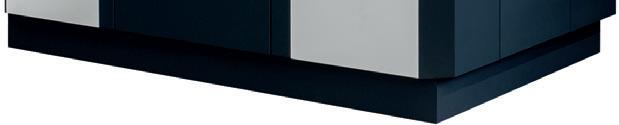
https://www.dreyplas.com/en/ Dreyplas announces thermoplastic UHMW-PE for extrusion
By adding Lubmer L5000 from Mitsui Chemicals to its portfolio, the distributor DREYPLAS now has an ultra-high molecular weight grade of polyethylene (UHMW-PE) in pellet form which can be processed like conventional thermoplastics, also suiting it to the extrusion of pipes, hoses and profi les.
One of the fi rst adopters is Novoplast Schlauchtechnik in Halberstadt, Germany. Working hand in hand with DREYPLAS, Novoplast has developed a now patented process for manufacturing hoses from Lubmer L5000 as a continuous reel product.
Known by the product name PE Ultra, these hoses are used in industrial, medical and other applications. Lubmer LS4140, a blend based on chemically coupled PA6 and UHMWPE components, is suitable for similar applications requiring elevated temperature resistance.
Thanks to being recyclable as polyolefi ns and the possibility of remelting production scrap and returning it to the production cycle, Lubmer extrusion and injection moulding grades provide environmentally responsible, sustainable solutions. APPOINTMENT UPDATE
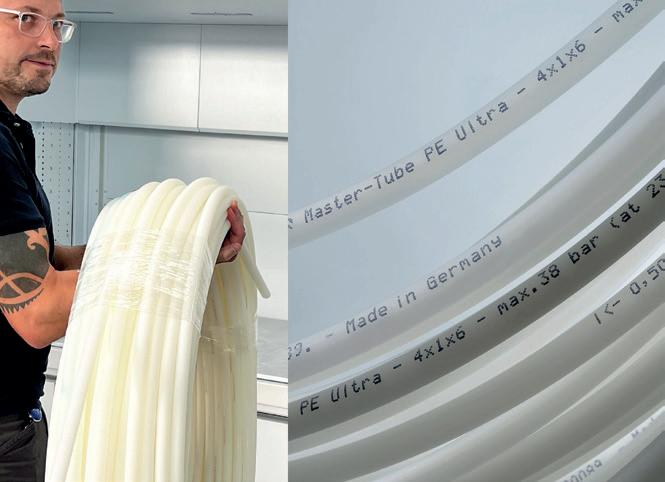
https://www.rqmplus.com
RQM+ appoints new Head of Mergers and Acquisitions
With more than 20 years of experience in the MedTech industry, Mahofski has held various positions at RQM+, including overseeing M&A integration and business development. He previously served as VP of engineering for Circadiance and as a project manager for MEDRAD. In his new role at RQM+, Mahofski is responsible for identifying and pursuing acquisition opportunities that complement its core regulatory services and provide a comprehensive range of fully integrated outsourced solutions to help get MedTech products to market faster and ensure ongoing regulatory compliance.
“We’re rapidly becoming the organisation that will help medical device companies connect the dots from concept through market deployment and maintenance, expediting patient access to life-improving technologies,” said Mahofski. “In the coming years, we will continue to expand our off erings to support MedTech customers throughout the product lifecycle.”
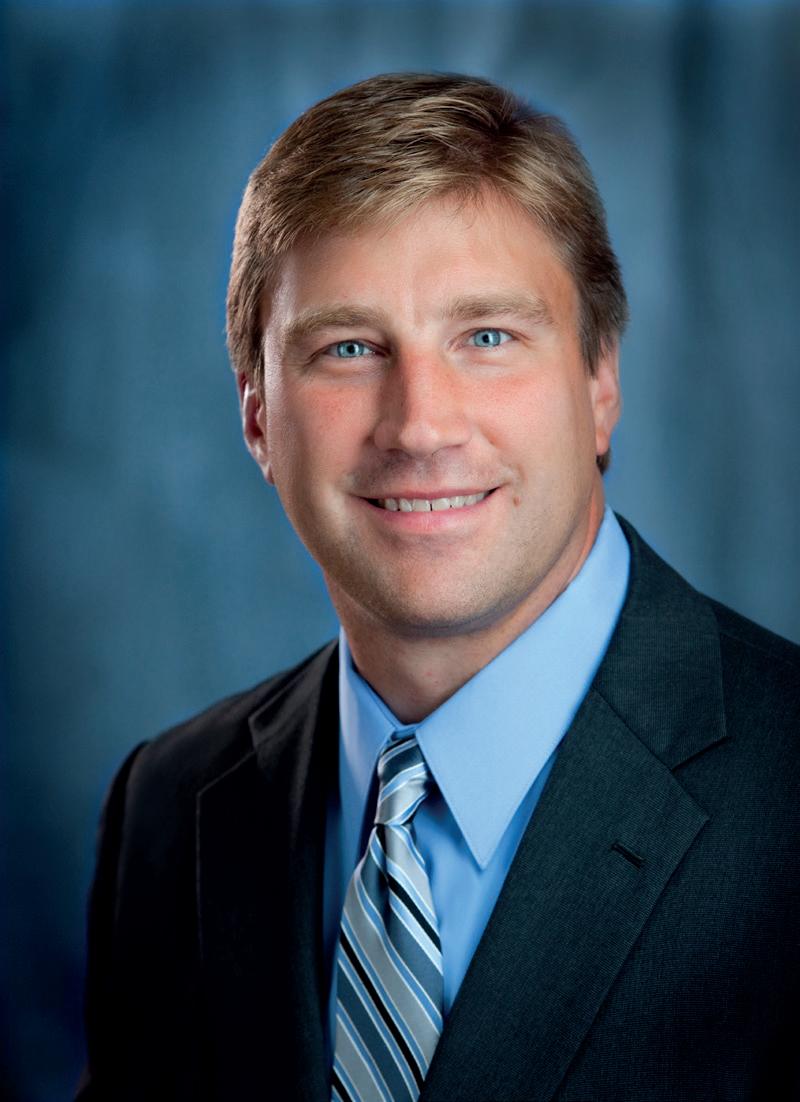