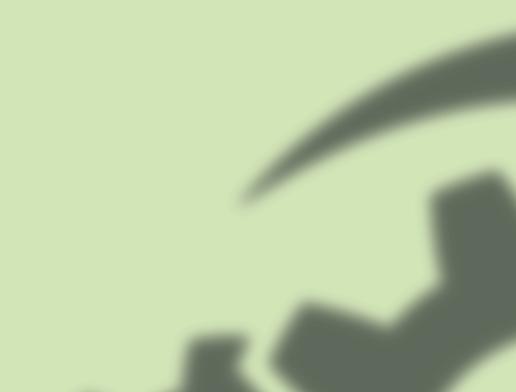
14 minute read
Injection molding
from MPN NA Issue 22
by MPN Magazine
ENGEL DISCUSSES HOW INTEGRATED SOLUTION CAN BOOST EFFICIENCY AND HOW AUTOMATED PRODUCTION OF OPHTHALMIC PRODUCTS CAN BE DONE IN THE SMALLEST POSSIBLE WORK AREA.
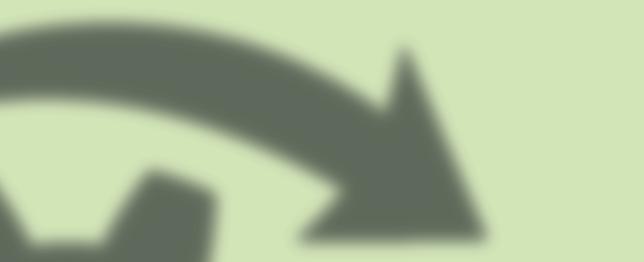
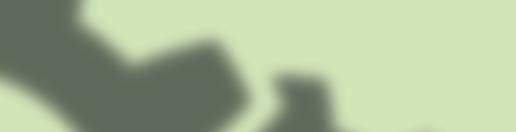
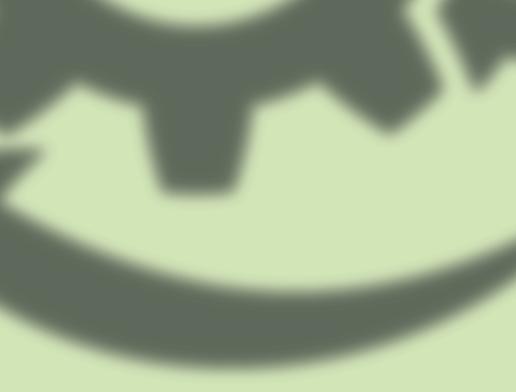
Connected to a cleanroom, Aptar Radolfzell produces an innovative multiple dosing system for the administration of eye drops. The dosing system is microbiologically sealed and does not require any preservatives. In production, high precision needs to be combined with effi ciency. For series production, ENGEL supplied two new production cells, each consisting of e-victory injection molding machines and integrated easix articulated robots.
In Germany alone, millions of applicators for eye drops are used. The symptoms for which liquid medications are dripped into patients’ eyes are manifold. What all eye drops used to have in common was unavoidable contact with bacteria after opening. The systems commonly seen on the market are therefore often single applicators whose contents can only be used for a few hours after opening. Aptar Radolfzell, an Aptar Group Inc. company, produces a sustainable alternative: a multiple-use dosing system with bottles of 5 and 10 ml capacities. As a self-contained system, it provides the necessary protection against microbiological contamination that reliably prevents premature expiration of the drug. “Our applicator delivers the drug drop by drop and is free from preservatives. That is the added value of the system,” says Ingo Korherr, production manager at Aptar Pharma, summing up. “The advantages here are that this is not a one-off application, which is not ecological and produces a lot of waste. The multiple dosage system can be used for several weeks, and it is more ergonomic to apply at the same time,” adds Ralf Fichtner, site manager at Aptar Pharma in Eigeltingen in southern Germany.
In ophthalmology, one of the Aptar Group’s product lines, the strategy of manufacturing all plastic parts in-house, has been successfully implemented. This has largely been achieved with ENGEL manufacturing systems.
TIE BAR-LESS CLAMPING UNIT ENSURES HIGH-PRECISION MOLDING The ophthalmic squeeze dispenser (OSD) consists of a total of seven plastic parts with varying degrees of complexity and one metal part. To produce the applicator and the spray pins, capital was invested in two new production cells for the Eigeltingen location; this is Aptar Radolfzell’s second production location in addition to Radolfzell.
The applicator with a diameter of 15 millimeters is produced from polypropylene (PP) in a 32-cavity mold equipped with a partial hot runner on an ENGEL e-victory 740/220 injection molding machine with a clamping force of 220 tonnes. The total shot weight is 30.5 grams. An ENGEL e-victory 50/90 with a clamping force of 90 tonnes produces the spray pin from TPE with a total shot weight of 1.97 grams in a 16-cavity full hot runner mold. Both parts are productcarriers, i.e., they come into contact with the medication.
Where the plastic parts are highly fi ligree, complex at the same time, and are also produced in a multi-cavity mold, hybrid e-victory injection molding machine with an electric injection unit and servo-hydraulic clamping unit often off er benefi ts. The reason for this is the tie-bar-less clamping unit, which provides suffi cient space for large multi-cavity molds even on machines with comparatively low clamping forces. Patented force dividers distribute the clamping force evenly across the mold mounting platens, ensuring consistently high molding precision across all cavities. These were the factors that tipped the scales at Aptar in favor of capital expenditure on machines from the e-victory series. As ENGEL sales representative Jürgen Fridrich adds: “What was required up front was very high repeatability, shot for shot, and very high availability of the entire production cell in each case.”
“Let’s not forget the very strict demands on the mold and the part, which necessitate a high level of precision – requirements which the e-victory series meets in full. The servo-hydraulic clamping unit side from ENGEL runs like clockwork,” says Andreas Gräber, manager of injection molding services at Aptar Pharma.
Ralf Fichtner adds: “We process polyolefi ns, especially PP and PE. There are certainly more dimensionally stable plastics. The tolerance range with two decimal places in which we manufacture our parts, requires very high precision of the mold, the injection molding machine, and the entire process. Polyolefi ns with this precision are certainly not standard, and this is exactly what we specialize in. The challenge is to achieve this precision in a cost-eff ective way in multi-cavity molding with a high level of process stability.”
INTEGRATED CONTROL UNIT FACILITATES CHANGE TO ARTICULATED ROBOT The production process is fully automated and 100% monitored. SPC checks of the parts are also an integral part of the process. After completing the respective injection molding cycle, the parts are removed by ENGEL easix articulated robots, including separation of the cavities, which is important for traceability. In other applications at Aptar, ENGEL linear robots handle the parts.
The fact that the control unit for the ENGEL robots is fully integrated into the control CC300 control unit of the ENGEL injection molding machines, made the change to articulated robots particularly easy for Aptar. “One major advantage is that I can see everything on the machine display and do not have to walk around the machine. Of course, I have the hand-held unit for the process settings and teach-in, but that is a one-off thing, otherwise I can control everything from the machine, and it is very easy. The employees are familiar with the user interface and do not have to readjust or learn anything new, but can apply what they know 1:1,” says Andreas Gräber, summing up.
The manual robot panel and the smart ENGEL CC300 control unit access one and the same database. Another benefi t is that both systems coordinate their motion sequences with each other. This reduces the handling time in some applications. 500 MILLION DOSING UNITS A YEAR As an expert for innovative medication delivery systems and packaging solutions, Aptar pursues a two-supplier strategy in-house. Of the total of 85 injection molding machines with clamping forces of 35 to 250 tonnes, ENGEL machines account for more than 60 percent. Some 850 employees produce more than 500 dosing units annually at both locations. With several global good manufacturing practice (GMP) production sites, Aptar Pharma ensures both a reliable supply chain and local support for its customers. The division of the company focuses on injection molding technology. “We buy in other processing technologies strategically,” explains Ralf Fichtner: “The answer to the question as to what we do in-house, and what we don’t, is driven by the complexity of the parts to be produced.” of the parts to be produced.” After all, the company name, Aptar, is derived from the Latin word aptare. And that means to adapt, which refl ects the company’s philosophy the company’s philosophy in practice.
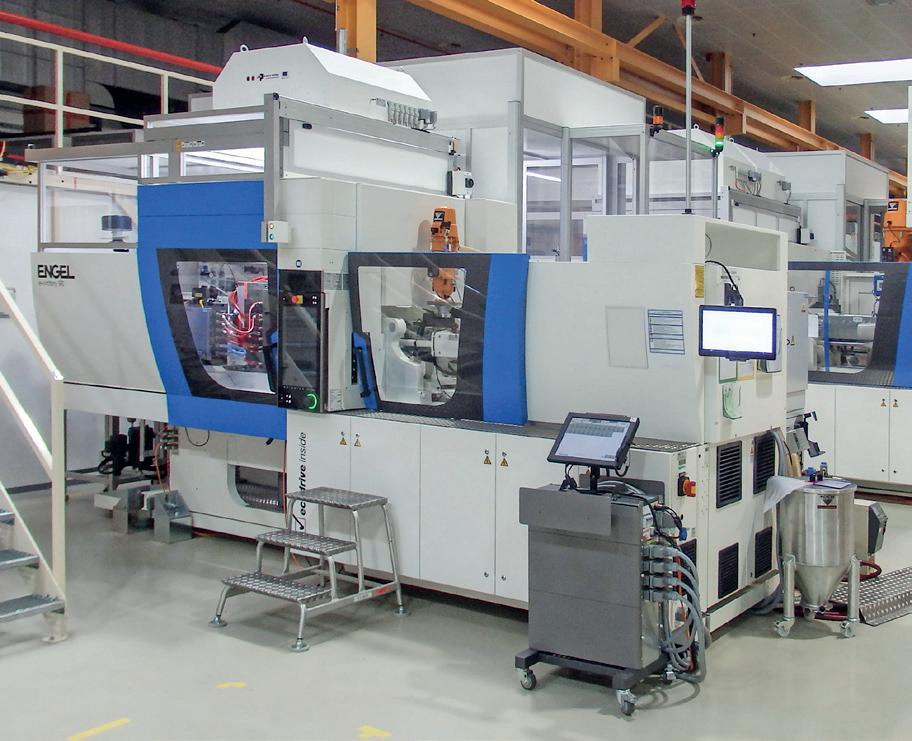
The injection molding machines and automation are encapsulated in cleanroom-compatible production cells in compliance with ISO 7 requirements.
The applicator (right top) and spray pin (right bottom) are produced on the two new ENGEL e-victory injection molding machines. The dosing systems consist of eight parts all told, seven of which are made of polymer materials.
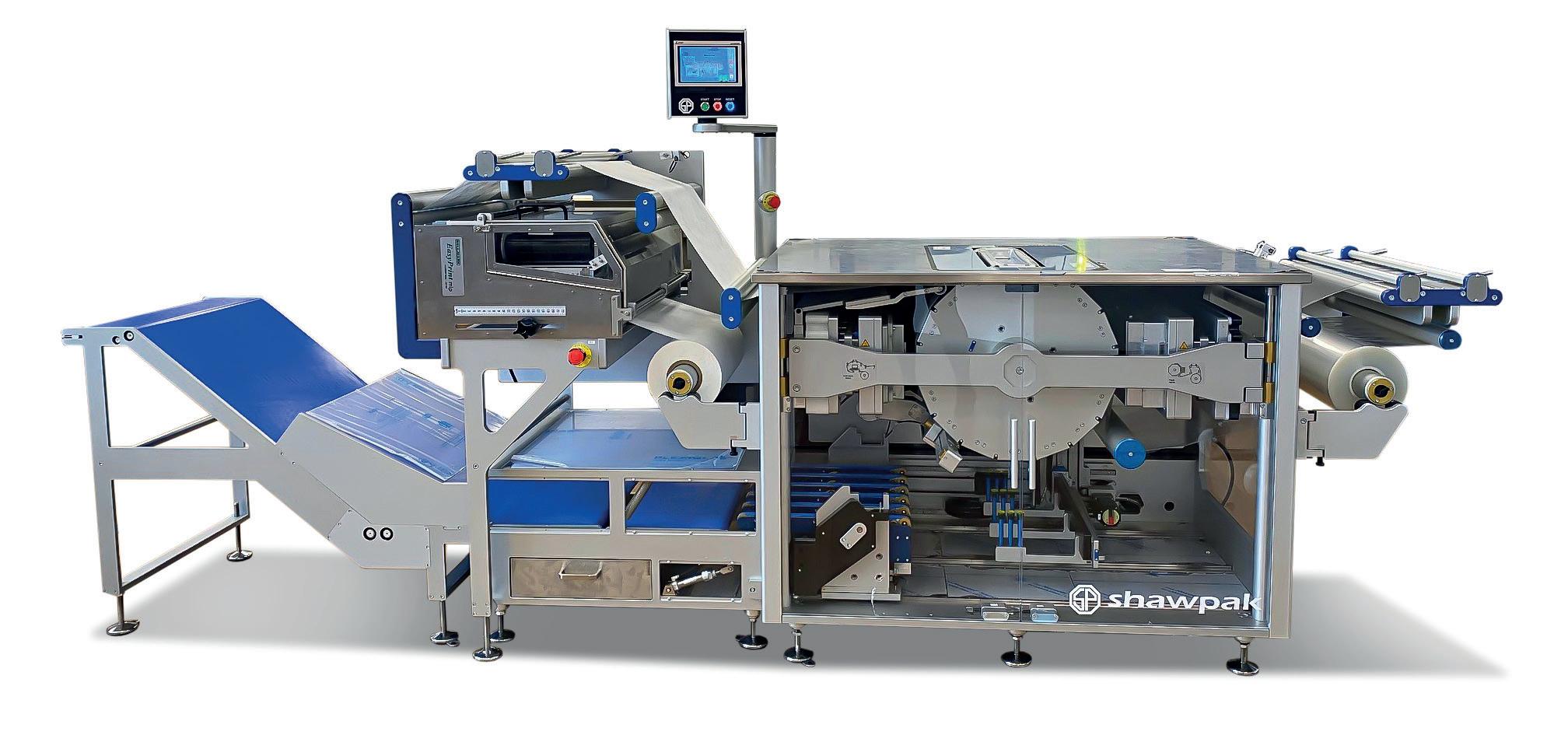
IT’S HEATING UP
ALAN WADE, OPERATIONS DIRECTOR AT SHAWPAK, SHARES HOW THE COMPANY PLANS TO KEEP AHEAD OF THE THERMOFORMING COMPETITION.
Shawpak is a UK manufacturer of a range of packaging equipment for medical devices, including rotary thermoforming machinery.
The start of Shawpak began in 2013 when David Shaw, CEO, thought that the size of a long linear thermoforming machine - which was six meters long - could be condensed into a smaller machine, but with the same input.
Alan Wade commented: “Our CEO, David Shaw had an idea at the end of 2013, to make a smaller rotary thermoforming machine.
“We started developing the fi rst machine and took it to the fi rst trade show, Medica, in Dusseldorf. The machine received such a great response that we knew we had to promote the machine commercially.’’
The shawpak thermoforming machine uses a rotary drum to form, fi ll and seal the medical devices unlike the traditional linear thermoformers. The benefi t of wrapping this around a drum reduces expensive clean room space, as it’s so compact, reduces waste on blister packs and also increases fl exibility to change tools over.
Riverside Medical Packaging has played a huge role in developing the shawpak machine. With their experience in packaging, they were able to assist in fi nding the advantages that the shawpak machine provides and overcoming many of the disadvantages that thermoforming machines generally have. While thermoforming is a huge industry, Shawpak intends to stay ahead of the game. Wade discussed several ideas that could benefi t the growth of the company, including making assemblies in advance to put into stock, so when a customer wants something, they can pull the assembly and build, rather than manufacture from new, which can reduce time signifi cantly.
A great way of staying ahead is being out there and meeting potential customers. Shawpak stays busy with medical expos around the globe; the company exhibited at Med-Tech Innovation Expo in 2022 and has signed up for 2023, as well as MD&M West, Compamed and more.
Not only do Shawpak exhibit at expos, but the company also held its own in-house expo over three days, in July, called Shawmed. The expo consisted of showcasing many of their own machines, a factory tour of Riverside and opportunities to speak to their related companies – Amaco Flexible Print Solutions, SP Automation and Robotics and Sterimed Infection Control.
Shawpak’s range also includes the Pouch Machine and the Pouch Sealer. The Shawpak Pouch Machine launched at the start of 2021, Shawpak says it represents the best solution for packaging fl at medical products.
Shawpak is now developing their own rigid blister making machine. Tony Crofts, sales director explained: ‘’To compliment our range of medical packaging machinery we are now developing a rigid blister making machine which forms the blister, die cuts the outer profi le and stacks them ready for use in production.
“This along with our pouch making machine gives our customer the full fl exibility in making their packaging on demand from roll stock rather than relying on their supply chain to deliver the packaging they require and keeping months of stock to ensure supply doesn’t run out. The tooling can be quickly changed to give the customer full fl exibility and control, it allows you to make the blisters and pouches you require just ahead of time and not keep pallets of stock taking up space and tying up cash.‘’
Shawpak’s newest addition to the range, the Shuttle Machine, is also coming soon.
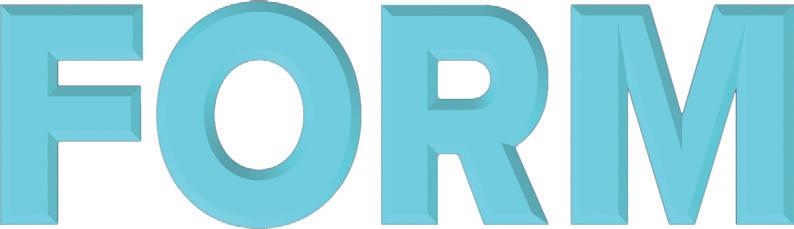
BRIAN GOLDEN, SALES DIRECTOR, AMERICAS, GN THERMOFORMING EQUIPMENT, SHARES HOW THE MEDICAL PACKAGING INDUSTRY LEADS THE TREND TOWARDS THERMOFORMING AUTOMATION.
Automation of the thermoforming process has been embraced in the medical packaging industry more quickly than in other markets. Originally, this trend was driven by stringent quality requirements and the need for high levels of repeatability. Automation has also brought other benefi ts of strategic importance to medical packaging producers, including facilitating higher and more predictable throughput, as well as helping to address the challenges of attracting, training, and retaining a quality manufacturing workforce.
STRONG FLANGE AND COMPLEX GEOMETRIES The shape of the packaging typically diff ers for medical products. The entire package must withstand the temperature and pressure extremes of the sterilization process. The fl ange must have the required thickness and rigidity, and smooth surface, to accept and maintain a hermetic seal to the Tyvek lid. The sidewalls must also have adequate and consistent strength and thickness to prevent cracking and leakage during transport and handling.
The most challenging aspect of medical packaging design is often the complex geometries required to isolate individual items into separate compartments and to lock each item in place. When properly designed and manufactured, undercuts allow each part to be snapped into place and held securely.
ELIMINATION OF AIRBORNE PARTICULATES Most medical packaging applications call for enclosing the thermoforming machinery in a protective enclosure to minimize exposure to airborne particulates that can cause gaps during the hermetic sealing process. It is imperative that measures are taken to eliminate static that will attract particulates and to ensure that the cutting process does not generate particulates that can migrate to the product.
Enclosing the machinery is important not only for protection against particulates but also for isolating the system from ambient air and temperature that cause fl uctuations in the heating of materials and in the air pressure of pneumatic components.
INCREASING AUTOMATION These various special requirements for medical packaging have led to the wide-scale adoption of Form/Cut/Stack thermoforming systems. Simpler and less costly Contact Heat systems are suitable for only a small fraction of medical packaging applications because they lack plug assist capabilities required for complex geometries and the higher clamping forces that Form/Cut/Stack systems off er.
Form/Cut/Stack systems are usually enclosed in a protective envelope protecting the process and the product from airborne particulates and ambient temperature and humidity, and they can be more fully automated and therefore more precisely monitored and controlled, especially machines with 100% servo motors and drives. Investment in automation off ers many advantages in medical packaging manufacturing - more precision and control result in much higher repeatability, which means higher quality products as well as fewer defects and less waste. The process improvements achieve faster cycle times and predictable output, for higher throughput and scalability.
Precise control and repeatability are also critical to the calibration and production consistency required by the strict standards and government regulations for medical packaging, such as ISO 11607:2019. Automation may also include vision systems and other inspection technology that provide automatic, continuous real-time quality control. In general, the more automation, the greater the opportunity to collect data for process improvement and for traceability.
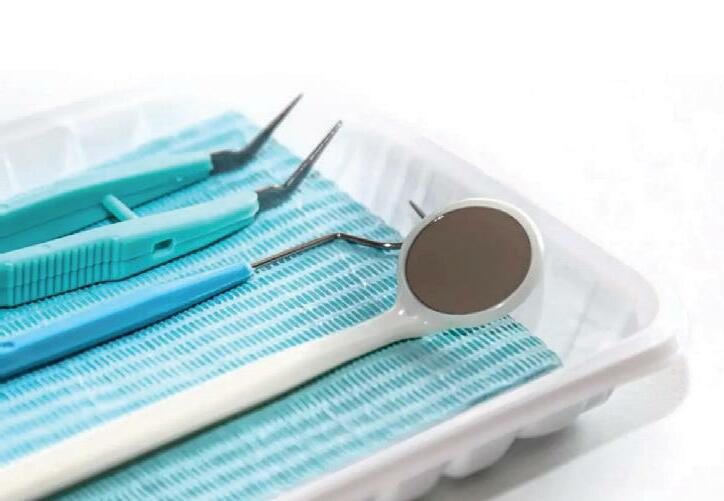
EASE OF OPERATION Instead of requiring one or more operators per production line, a single operator can cover multiple lines. First of all, this requires that the machines autonomously perform the forming, cutting, and stacking processes with little or no hands-on engagement by the operator. For high volume production, robotics are increasingly employed to automatically perform downstream packaging and palletising functions. But the autonomous operation of these functions is only one element of automation.
The procedures for changing tooling between SKUs and for replacing roll stock also need to minimize human error and eff ort. The right tooling needs to be
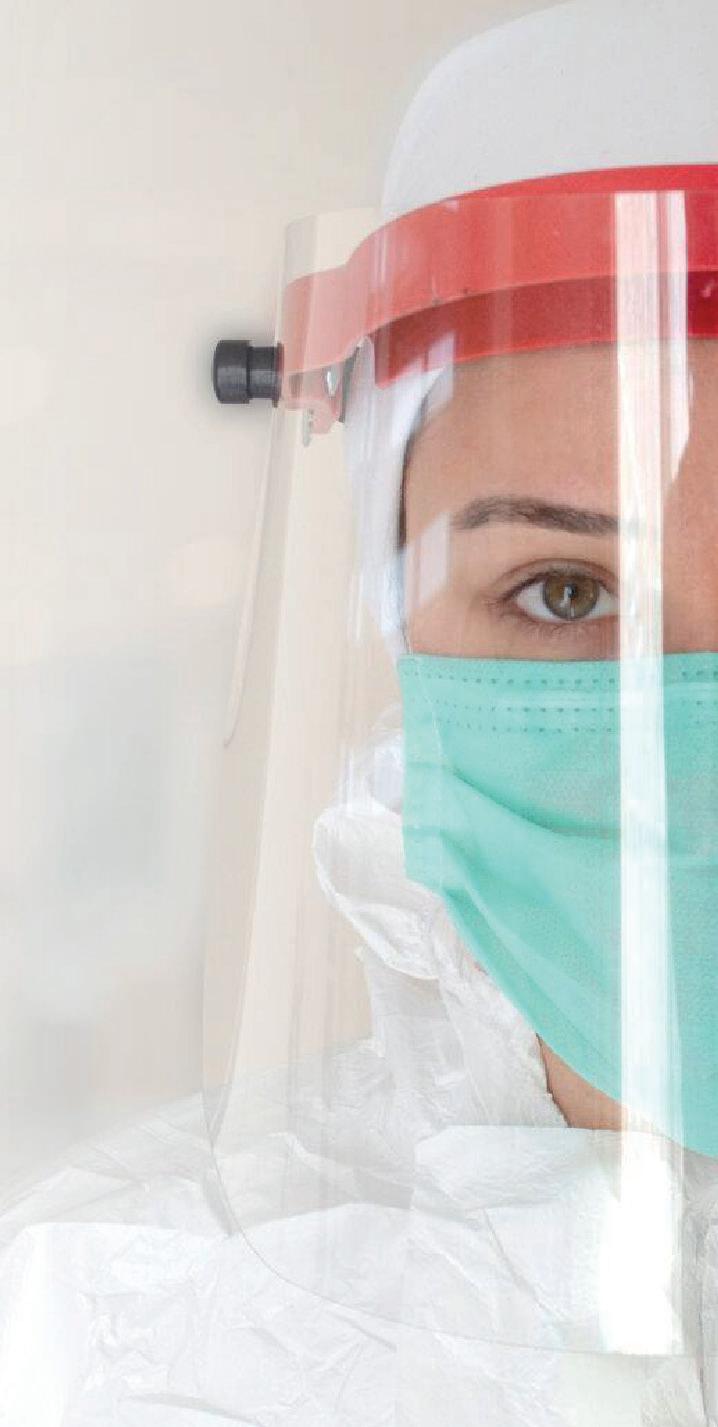
installed in exactly the right way, for every production run, and roll stock can weigh 1500 lbs. Thermoforming equipment should be designed with procedures and tools for streamlining these processes and preventing errors and with ergonomic aids for lifting and correctly positioning heavy objects.
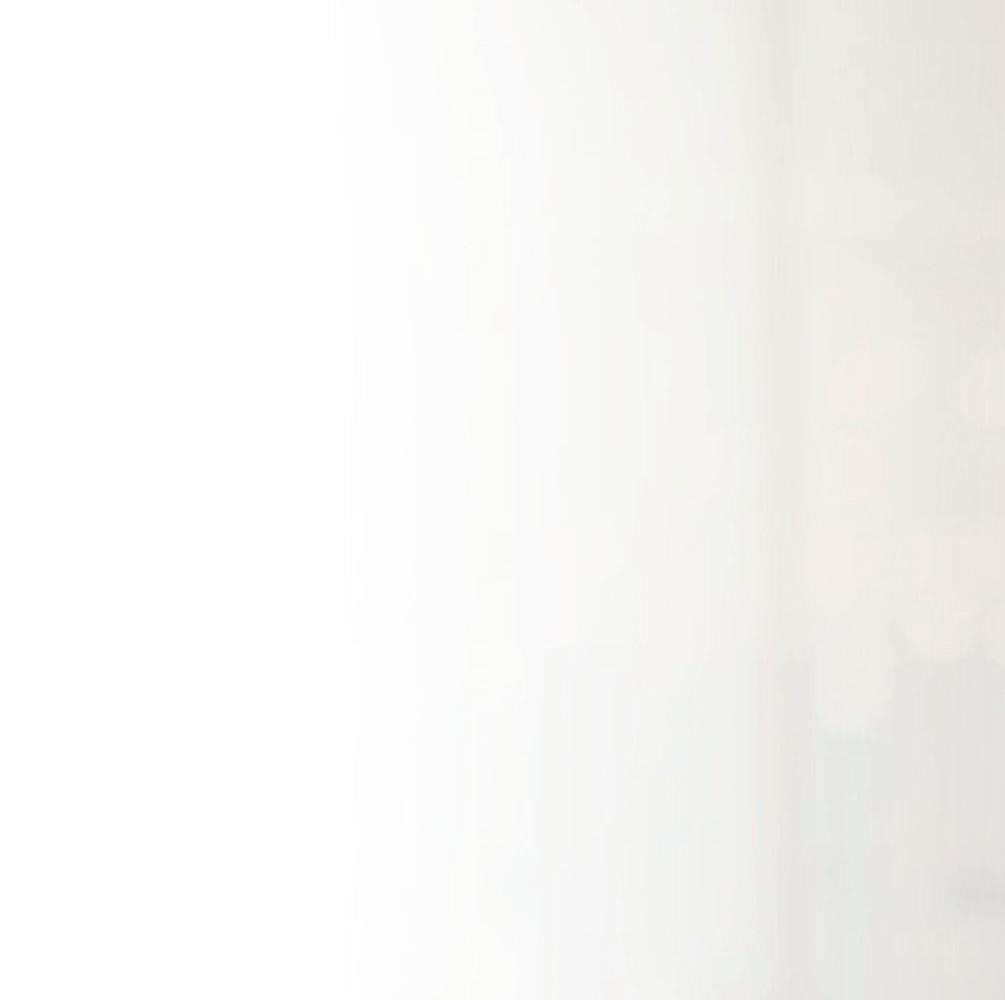
LOOKING FORWARD The whole concept of a Form/ Cut/Stack thermoforming machine is to integrate and automate these multiple functions in a single system. Medical packaging manufacturers have been at the forefront of the trend toward automation, initially driven by the need for high quality, repeatability, and traceability. Automation also increased scalability and throughput. The third driver of automation is the need to address labor shortages and high turnover by making processes more productive and less labor-intensive, and easier to learn.
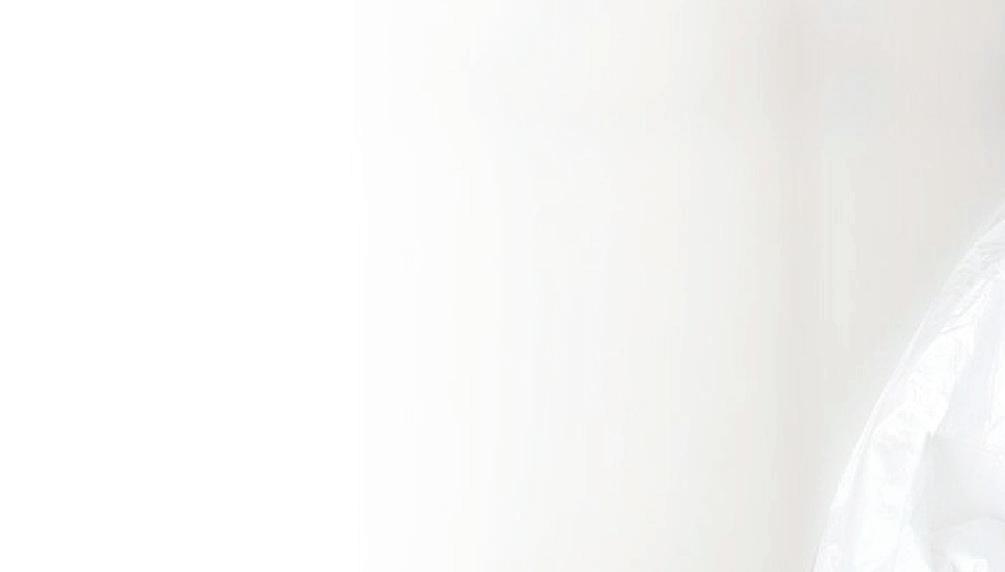
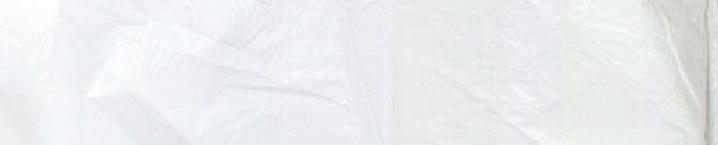
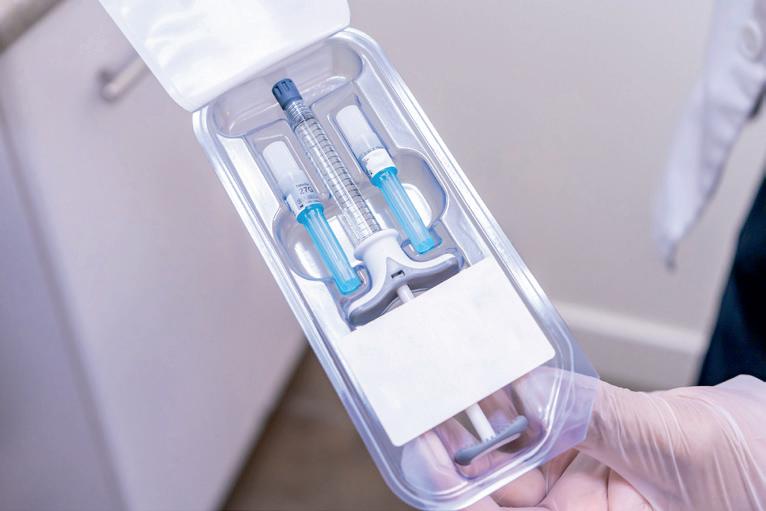
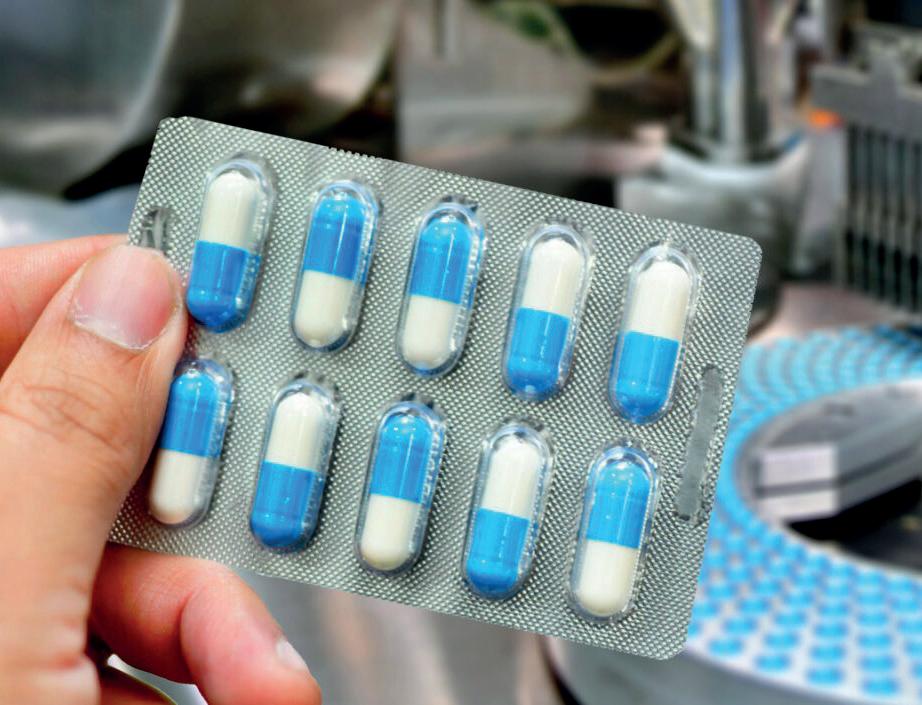
Plastic Material Changes Require Latest Plastic Welding Technologies
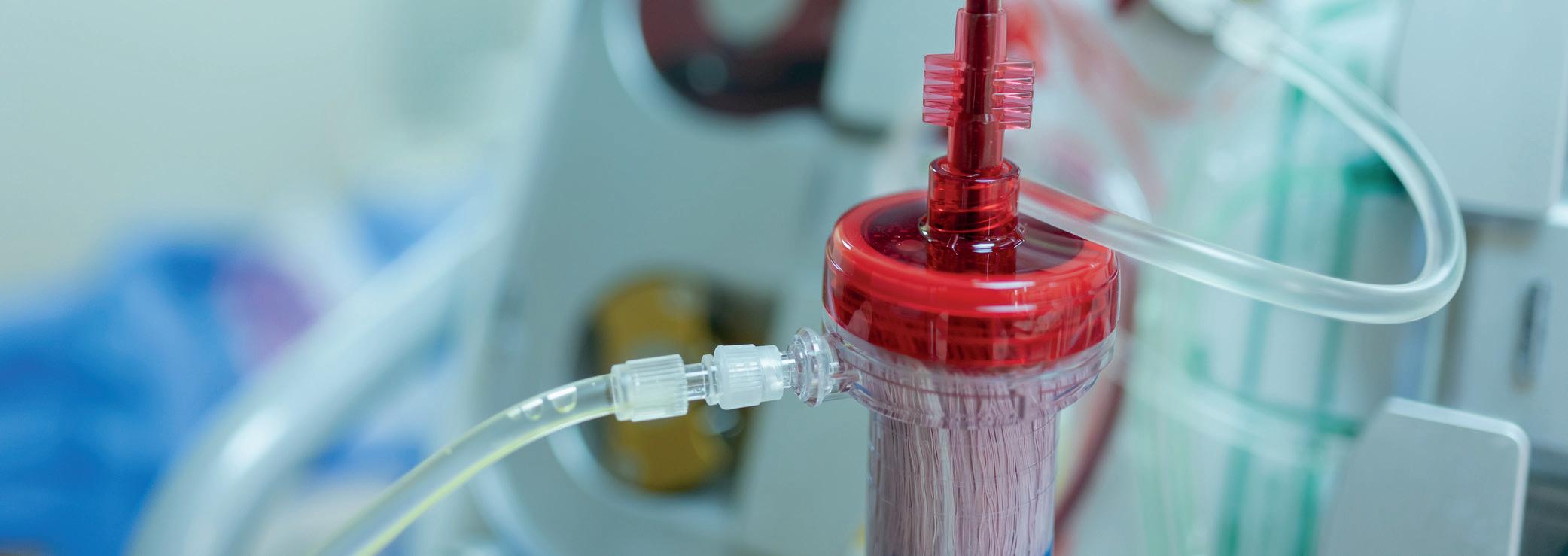
Market pressures are driving medical device designers away from PVC and PC, yet replacements like PE and PP do not respond well to traditional plastic joining methods. Reliable assembly requires advanced BransonTM ultrasonic and laser welding systems from Emerson. They produce ultra-clean, aesthetically superior welds for today’s preferred materials while also delivering design flexibility, process efficiency, energy saving and sustainability advantages.
Learn more at: Emerson.com/Branson Come and speak with an expert at:
K-Show, Hall 11 Booth F55, 19-26th Oct 2022.
The Emerson logo is a trademark and a service mark of Emerson Electric Co. © 2022 Emerson Electric Co.