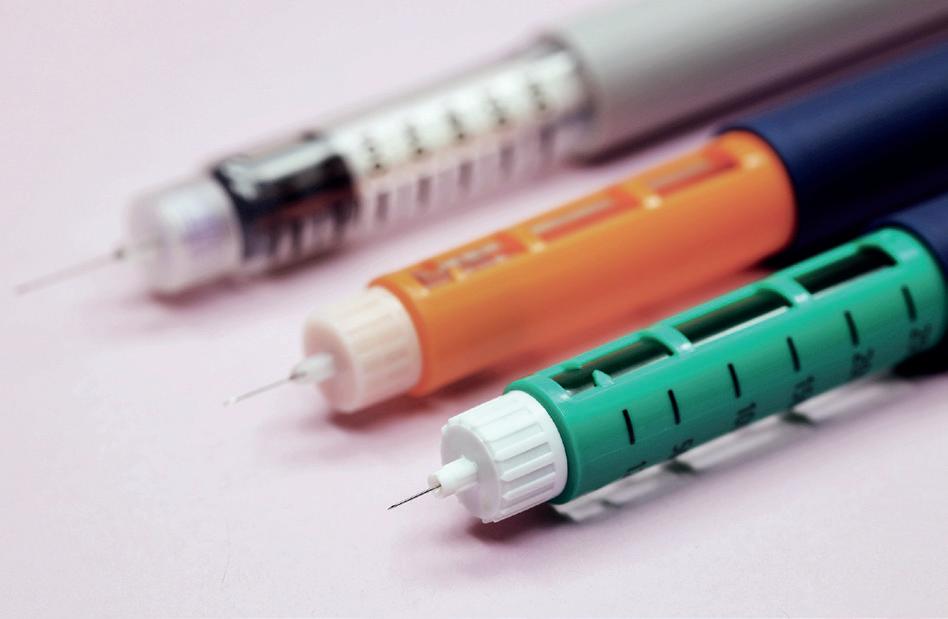
13 minute read
Cover story
from MPN NA Issue 22
by MPN Magazine
SANDI SCHAIBLE, SENIOR DIRECTOR OF ANALYTICAL CHEMISTRY AT WUXI APPTEC, SHARES THE IMPORTANCE OF COMPLETE CHEMICAL CHARACTERIZATION.
EXTRACTING THE TRUTH
Plastics are everywhere in medical device manufacturing. Whether we’re talking about a fi lter, bag, container, delivery system or implantable device, these days, chances are, plastic is part of the equation. While plastics and polymeric materials can enhance performance and pricing, these materials do carry risk of their own. Manufacturers need to understand these risks as they develop their products, plan for production and identify both materials and component suppliers as well as laboratory testing partners to support their submission and lifecycle management of their products. They need to understand the key tenet that not all plastics are created equally.
Plastic and polymeric products, parts and components can include signifi cant numbers of chemical constituents. Some of these constituents are expected, but many are unexpected and can be potentially harmful. Additives, excipients, and release agents along with impurities, can pose signifi cant diff erences in plastics that, at surface level, appear to be equivalent. It is these chemical constituents that can leach from the products and compromise patient safety. Extractables and leachables (E&L) testing is the most eff ective way to extract, detect and identify these potentially problematic compounds so that a thorough risk/safety assessment can be conducted to determine the risks.
Extractables testing challenges products using aggressive solvents under exaggerated conditions. The point of extractables testing is to generate “worst-case” data to create a conservative approach to safety. Leachables testing or simulated use extractions investigates compounds that have migrated from a plastic component under clinically relevant or “normal” conditions utilizing drug products, placebos, or more clinically relevant extraction solutions.
Regulatory bodies are becoming more and more interested in understanding complete chemical characterisation, looking for extractables and leachables data. Because even common materials or those with a long history of clinical use can contain chemicals of concern. Per ISO 10993-1, most medical devices require extractables or exaggerated extractables studies and a toxicological risk assessment, with potentially additional chemistry to mitigate risks to fulfi materials characterisation endpoints. For drug manufacturers, the release of USP <1665> and <665> signals a keen interest in the extractables and leachables in the plastic components of the biomanufacturing process in addition to the extractables and leachables work that has been conducted for years with regards to container closure and stability studies.
EXTRACTABLES LEACHABLES
The point of extractables testing is to generate “worst-case” data to create a conservative approach to safety. Leachables testing investigates compounds that have migrated from a plastic component under clinically relevant or “normal” conditions utilizing drug products or more clinically relevant extraction solutions.
SHIFT YOUR MINDSET ON E&L TESTING The goal of an E&L study is to detect and identify all the chemical constituents above an analytical threshold, including chemicals that are unexpected. It takes a committed laboratory to do the work needed to identify compounds, a report with “unknowns” can cost delays and require retesting.
Robust, well conducted E&L studies require a commitment by the laboratories to provide complete characterisation; they must identify the unknowns. Many chemistry laboratories advertise E&L capabilities, but a lab designed specifi cally for them is diff erent. It means building an infrastructure that includes the instrumentation, cross-functional skill sets and staff to generate and interpret the data in meaningful ways.
For example, liquid chromatography-mass spectrometry (LC-MS) is a highly sensitive platform used to detect semi to non-volatile compounds. When it comes to plastic medical products, typically the most chemicals are found using LC-MS. And this is often when chemicals of concern are found. There are no commercial databases of LC-MS compounds, and even the most comprehensive private databases contain only a fraction of possible chemicals derived from E&L studies. So it takes the eff ort of expert chemists doing compound elucidation to get to identifi cation. But, without the identifi cation, an E&L program is incomplete and often, unusable for a toxicologist doing a risk/safety assessment.
To reiterate, manufacturers need to know how committed their laboratory testing partners are to identifying all potential hazards. Complete identifi cation is complex and resource intensive. Working with a lab that specializes in complete chemical characterisation will yield the best results.
ASK THE RIGHT QUESTIONS Thoroughly vetting potential partners can save manufacturers from unexpected charges and unanticipated problems down the road. Understanding your lab testing partner’s method of identifying chemicals of concern and level of rigor is critical. To this end, manufacturers should dig deeply into any potential partner’s experience. Helpful questions include:
● How long has the laboratory been conducting E&L studies? How many programs have you run? ● Can you commit to the elucidation and complete identifi cation of all components? ● Is complete identifi cation included in the price and timeline that you provided? Or is this extra? Successful partnerships require more than experienced practitioners, so it is essential to also ask about project management and communication. Helpful questions include:
● What is your on-time delivery record? And, when does the clock start? Upon receipt of the test article? ● E&L studies often yield unique situations. Can you commit to proactive communications when these arise? ● What support do you provide after analytical testing concludes?
What if regulators have questions?
Finally, manufacturers must understand the services they are purchasing—and those they are not. Some laboratories charge extra for identifi cation or identifi cation beyond what can be found in a commercial database. Other laboratories claim they have the capacity to take on a new E&L program but fail to deliver on time when the process proves more complex than anticipated. Asking the right questions when vetting partners allows manufacturers to make informed decisions, achieve regulatory success and market safe products.
A FINAL WORD ON E&L TESTING Plastic and polymers have become the dominant materials in medical products, but several factors contribute to their safe use. Manufacturers cannot assume that just because a plastic or polymer has been used before or is commonly used that there will not be potential safety concerns. E&L testing helps manufacturers fi nd the unexpected chemicals that may, or may not, potentially impact safety. A robust E&L program should detect and identify all chemical constituents and provide a clear picture to assess risk. Manufacturers are right to question any laboratory testing partner that cannot deliver complete data about their container, delivery system or device.
Medical diagnostic equipment & biotech applications
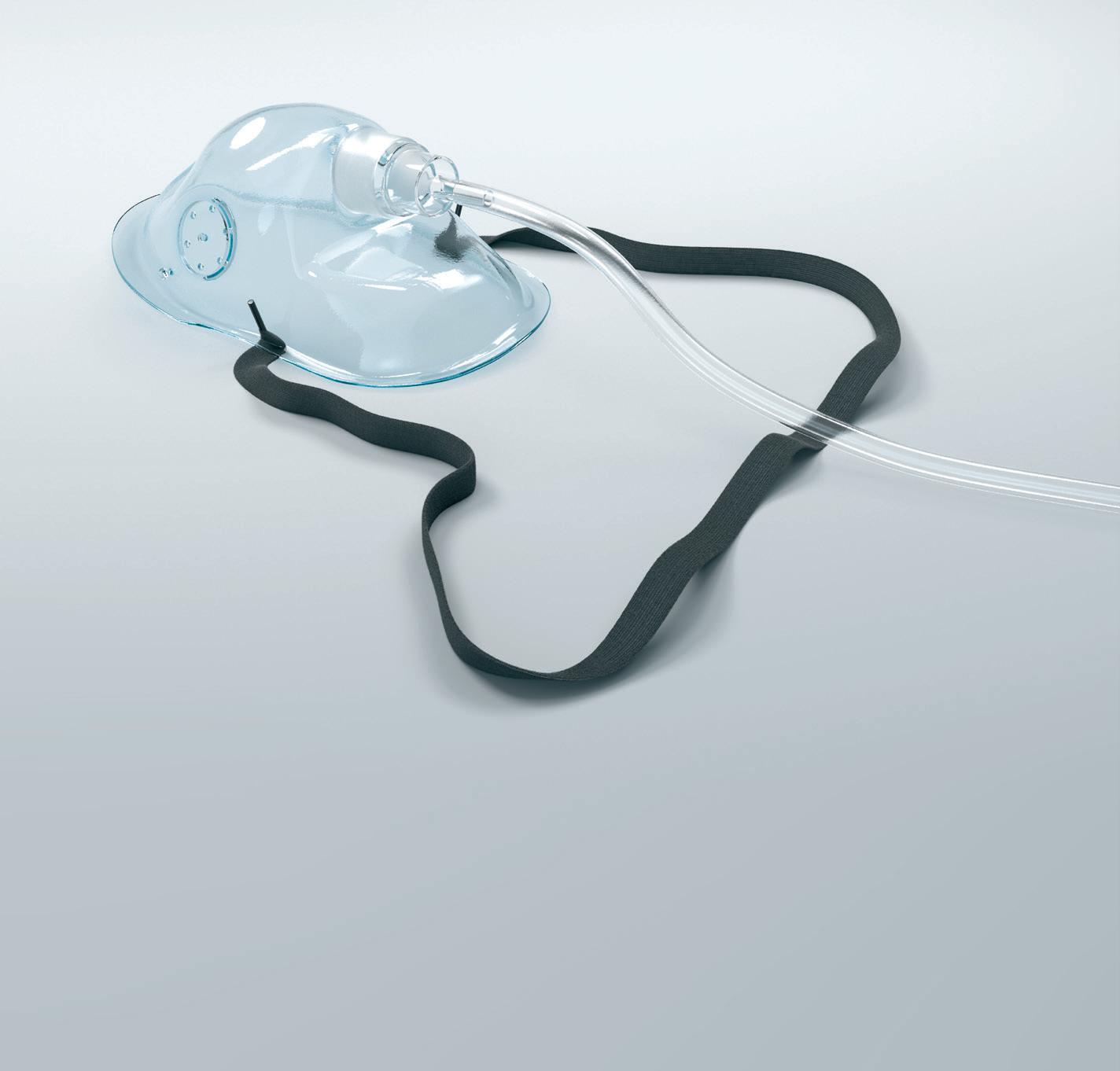
ALBIS offers the medical industry an unparalleled choice of standard, technical and high-performance polymers from renowned producers. This offering is complemented by customized polymer compound solutions tailored to customer’s needs and made by ALBIS’ sister company, MOCOM.
Our products comply with the requirements of the VDI 2017 Medical Grade Plastics Directive. We support numerous projects in the medical sector, pharmaceutical packaging and diagnostic equipment and biotechnology, putting technical and regulatory requirements at the heart of our work, so that we can define the most appropriate material for each application. Our regional experts draw on in-depth knowledge of the medical and pharmaceutical industry to provide you with a powerful service offering that integrates technical support, product safety and risk management. Contact us to learn more about our solutions and assortment of medical polymers and compounds: healthcare@albis.com
albis.com
CHOOSING THE RIGHT PARTNER FOR YOUR NEXT MEDICAL DEVICE.
Learn more at
www.lubrizol.com/Health/Medical
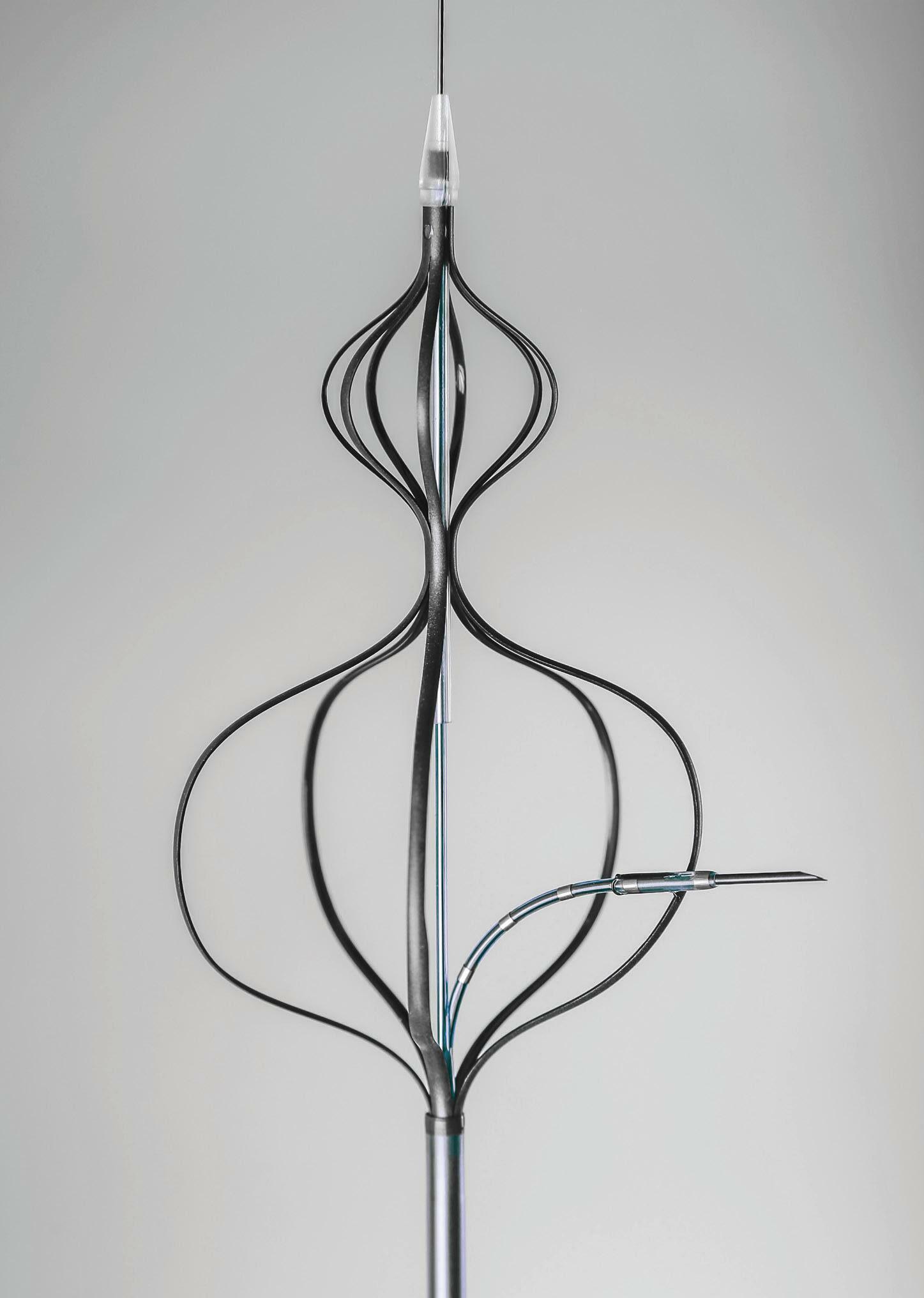
9911 Brecksville Road Cleveland, OH 44141-3201 USA
©2022 The Lubrizol Corporation, all rights reserved. All marks are the property of The Lubrizol Corporation. The Lubrizol Corporation is a Berkshire Hathaway company. 22-0119902
TILMANN PETERSON, HEAD OF BUSINESS DEVELOPMENT MEDTECH & CORPORATE PLANNING, AMSILK, SHARES HOW TO OPTIMIZE INTERACTIONS BETWEEN THE HUMAN BODY AND IMPLANTS.
Spider insider
Over the last decade, we have seen a lot of improvements and developments made within the implants industry, whether it be in the quality of silicone or the improved texture of implant surface. The mission for the next decade is to optimize the interactions between the implants and the human body, reducing the risk of rejection, infection and capsular formation.
AMSilk is a biotechnology company developing a range of vegan silk biopolymers that can be applied in various medical devices. The overall aim is to enhance the bio compatibility of medical devices. The properties of such coated implants include anti-adhesion and increased hydrophilicity. This results in reduced infl ammation and capsular formation, less invasive stress and better handling during surgical procedure.
One problem with implants is in some cases the body can identify it as a foreign object and cause the immune system to respond and reject it. If the body attacks the implant, it can result in serious complications such as pain, infection or capsular formation, all of which can require further surgery.
Spider silk coatings have the potential to prevent infection-caused infl ammation and to reduce post-operative issues caused by implants, minimizing the risk of further medical intervention. Together with its biocompatibility and biodegradability properties, biofabricated spider silk has the potential to be part of a strategy to reduce complications of implant applications.
As well as reducing the risk of implants being rejected, spider silk coatings can prevent infections by forming a surface on which bacteria cannot grow. Engineered spider silk coatings work by creating a ‘bioshield’, a non-stick surface which has an anti-adhesive eff ect on bacteria so that it does not adhere to the implant shielding it from bacteria and thus infection. This unique silk technology is safe and bioharmonic for the human body, and is also non-immunogenic, non-infl ammatory and non-toxic.
Biofabricated coatings have the potential to become a powerful tool in the fi ght against antimicrobial resistance (AMR). AMR is a major concern, with medical procedures such as surgery becoming extremely diffi cult, or even impossible, due to an increase in resistant infections. AMR has the potential to aff ect people at any stage of life with resistance to even one antibiotic causing serious problems. Many medical advances are dependent on the ability to fi ght infections using antibiotics.
Current pharmaceutical coatings available on the market can have high antibacterial eff ects however, this can create an environment that’s diffi cult to control. Non-active ingredients, such as AMSilk’s, promote a positive acceptance of implants and limit negative body reactions in a controlled way.
The unique biofabrication process reprograms microbes enabling them to produce silk proteins. The microbes are grown in large-scale stainless-steel vessels, fed with natural and renewable raw materials such as sugar. Upon a trigger, they start to produce the silk proteins. The biofabricated silk polymers are vegan, completely biodegradable and produced only with renewable resources, and thus are truly environmentally friendly making a contribution to a future zero-waste society. In the near future, we will need new directions concerning the fi ght against infections, which have to be far beyond the simple use of antibiotics. In this respect, coatings made of silk proteins are an important step towards a new generation of biocompatible surfaces and bioharmonic solutions to better patient outcomes after surgery.
The multiple benefi ts of silk polymers can be adapted to the needs of various market segments, enhanced skin comfort whilst also improving bacteriostatic and hygienic properties. These individually developed solutions will enable the medical sector to address industry challenges in the best possible way.
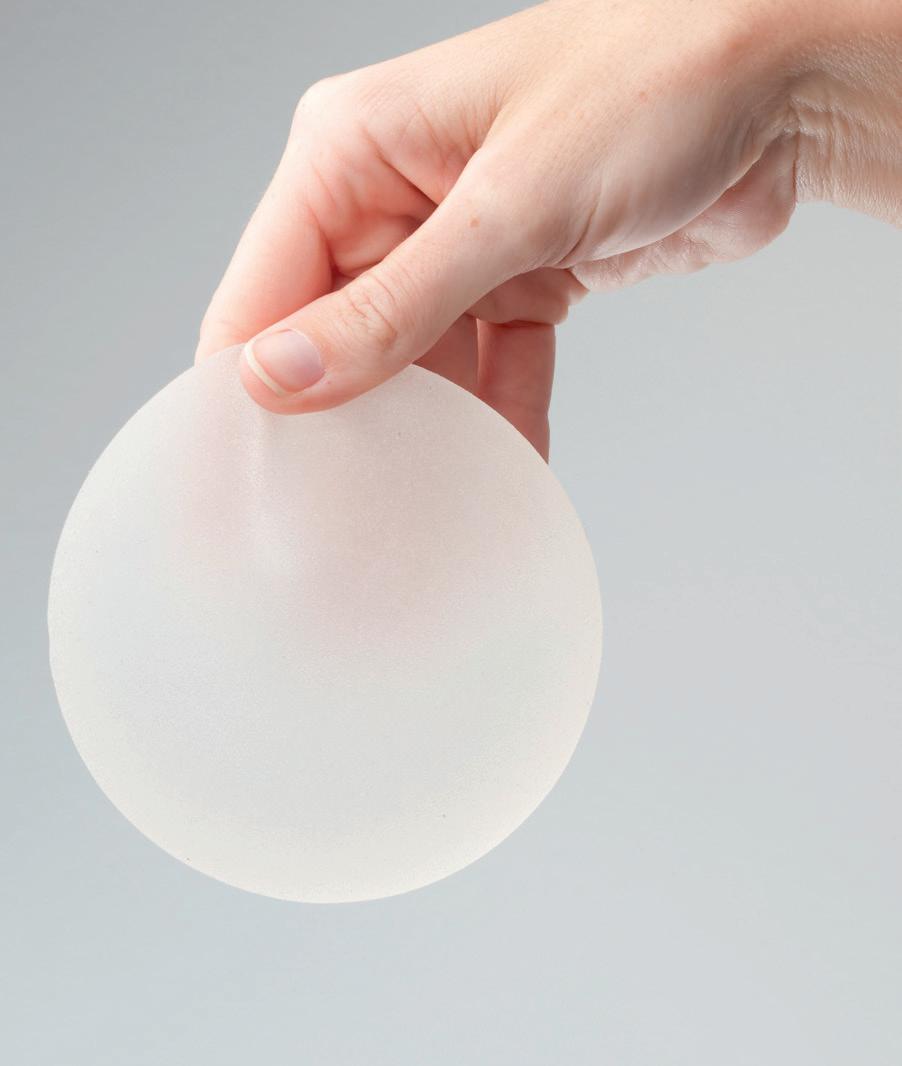
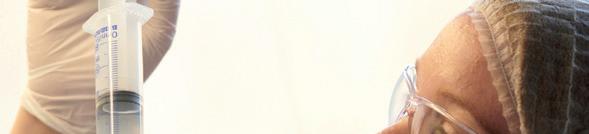
ALAN HUTCHINSON, PRINCIPAL SCIENTIST AT BROUGHTON, DISCUSSES THE CHALLENGES AND TRENDS WITH EXTRACTABLES AND LEACHABLES.
Up for the challenge


Extractables and Leachables (E&L) testing aims to reduce the safety risk to end-users of products such as pharmaceutical medicines or Electronic Nicotine Delivery Systems (ENDS), from the container closure system of the product.
E&L testing in the ENDS community is a recent requirement, with new regulations introduced as part of US Premarket Tobacco Product Application (PMTA) guidance. In contrast, in the pharmaceutical industry, E&L testing has been part of the required safety evaluation of products for a while. As pharmaceutical requirements are more developed, the materials used for these products are more consistent and understood. For the ENDS industry, the hope is that the use of grades of materials like those used in the pharmaceutical industry will become more prevalent over time.
CHALLENGES One of the major challenges with performing leachables studies is the common requirement to meet lower detection limits, which challenges both the instrument vendors and the laboratory scientists. Highly skilled and experienced analysts are required to develop instrument methods and sample preparation techniques to meet these low analytical evaluation thresholds, and state-of-the-art mass spectrometry instruments and software are needed to detect these low levels and process the data. The formulation of the product can contribute to this issue of sensitivity in so-called dirty matrices such as e-liquids, as their natural fl avors and biological samples can make it increasingly problematic to detect lower levels in a forest of peaks due to formulation interference.
Another challenge is a historical lack of clarity regarding the guidelines for designing and performing E&L testing. This has been a slow process and alignment of approaches would be valuable.
TRENDS The greater emphasis on performing risk assessments as a fi rst step of the E&L process is a main trend. This helps focus the studies and determine where eff ort is best placed to quickly and effi ciently de-risk any concerns from the container closure system. To perform a valuable risk assessment, the knowledge and information, as well as the expertise of the Subject Matter Experts (SMEs) performing the risk assessment that inputs into a Failure Mode and Eff ects Analysis (FMEA) style process, is essential.
This helps to focus eff ort and can reduce testing if previous data can be used to bridge to past studies. E&L studies are expensive and timeconsuming, and using previous relevant data will reduce costs and accelerate E&L projects.
The use of high-resolution accurate mass instruments for the analysis of E&L samples is becoming more widespread with E&L projects, helping to identify leachables and reduce the number of unknown compounds reported. Accurate mass instruments can help target leachables in complicated matrices, which can reduce the sensitivity burden by removing interferences from the formulation.
THE FUTURE In the future, it would be helpful to see the further alignment of processes and methods for performing E&L projects, and this would benefi t spectral libraries for identifying leachables. The development of response factor libraries for determining uncertainty factors would help in determining improved analytical evaluation thresholds for methods.
We are starting to see the use of automation for the sample preparation methods required for sample clean-up and enrichment. More use of automation can only help with the consistency of data and reduce the time taken.
The improvement of knowledge around E&L processes and materials, and the standardization of materials used for products, will mean that E&L assessments become a more desk-based activity. For pharmaceuticals, we are already seeing this with common industry-grade materials being used; within companies, the same materials are being used across product ranges. ENDS products will likely follow this path and in the future, cleaner, bettergrade plastics and rubbers will also become common across that industry.
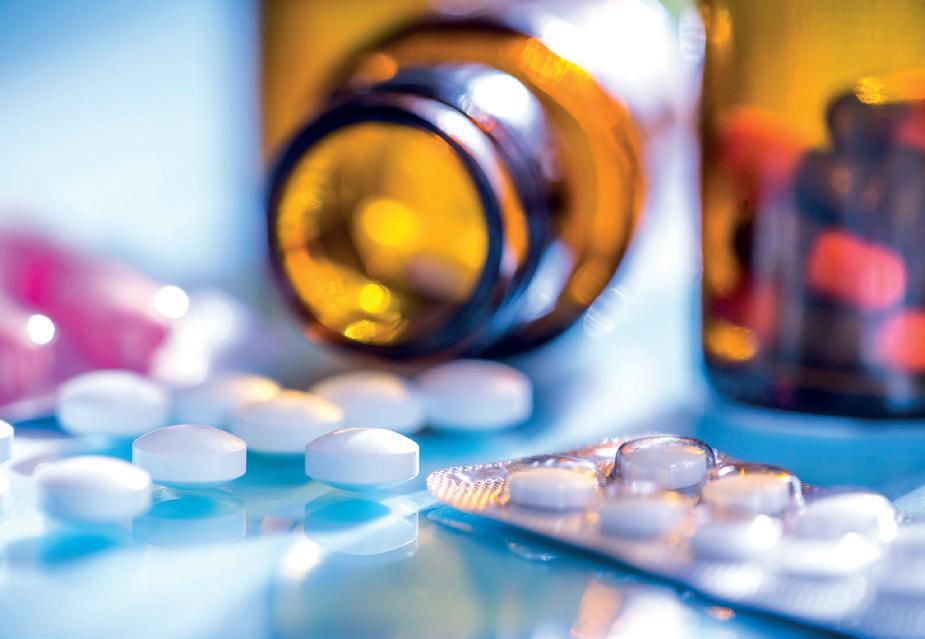
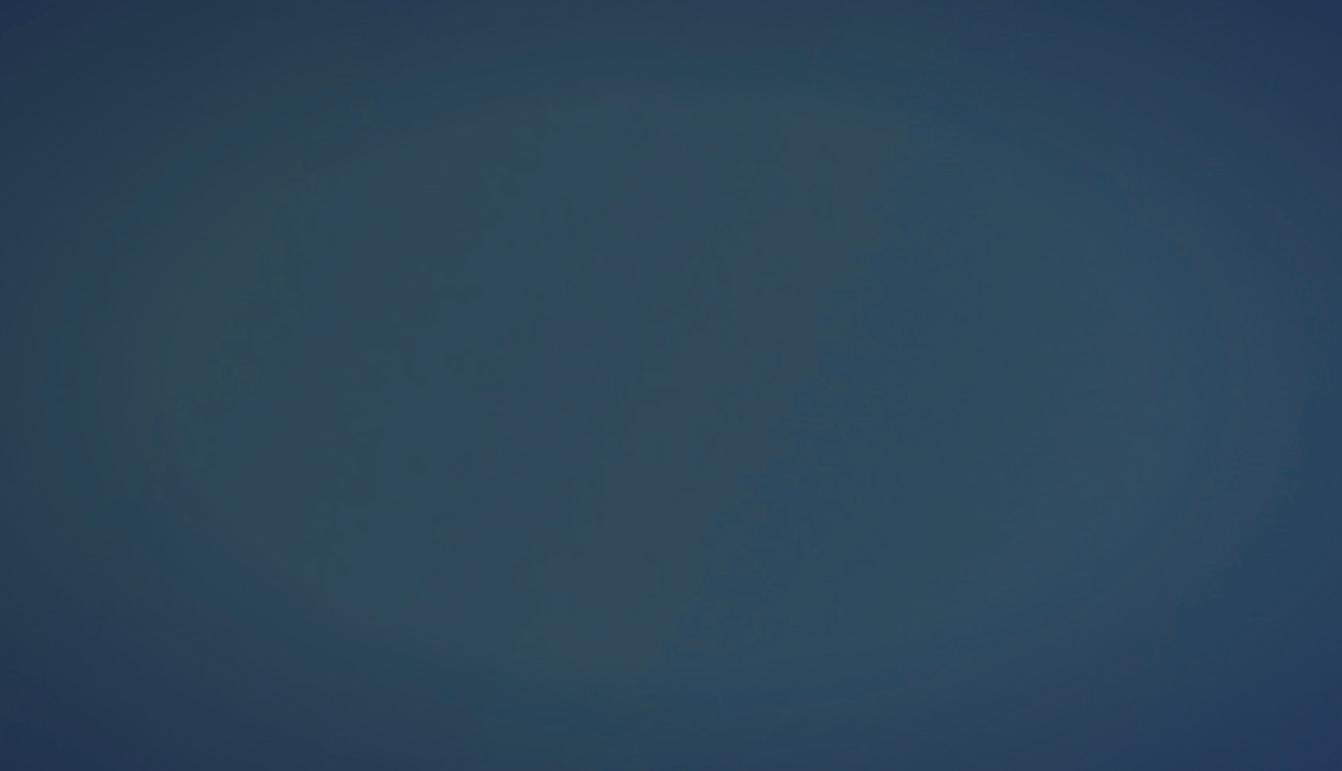
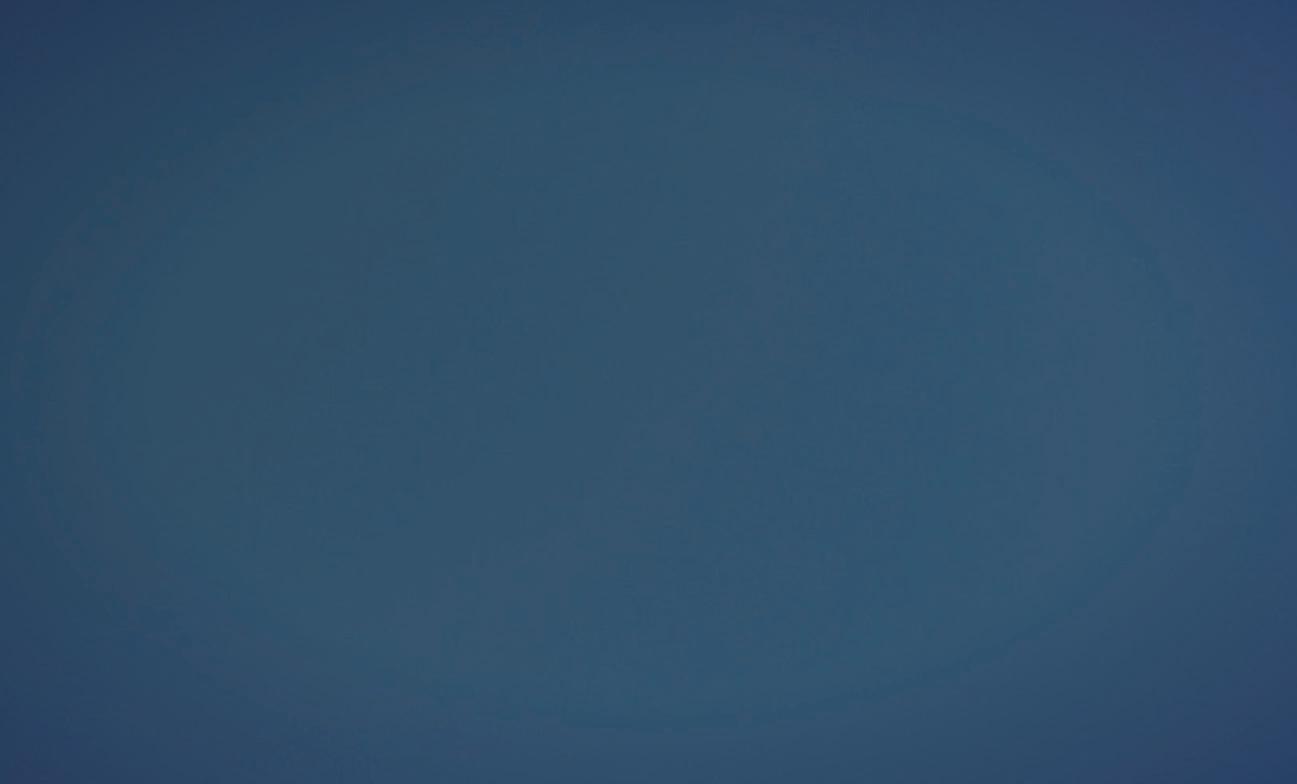
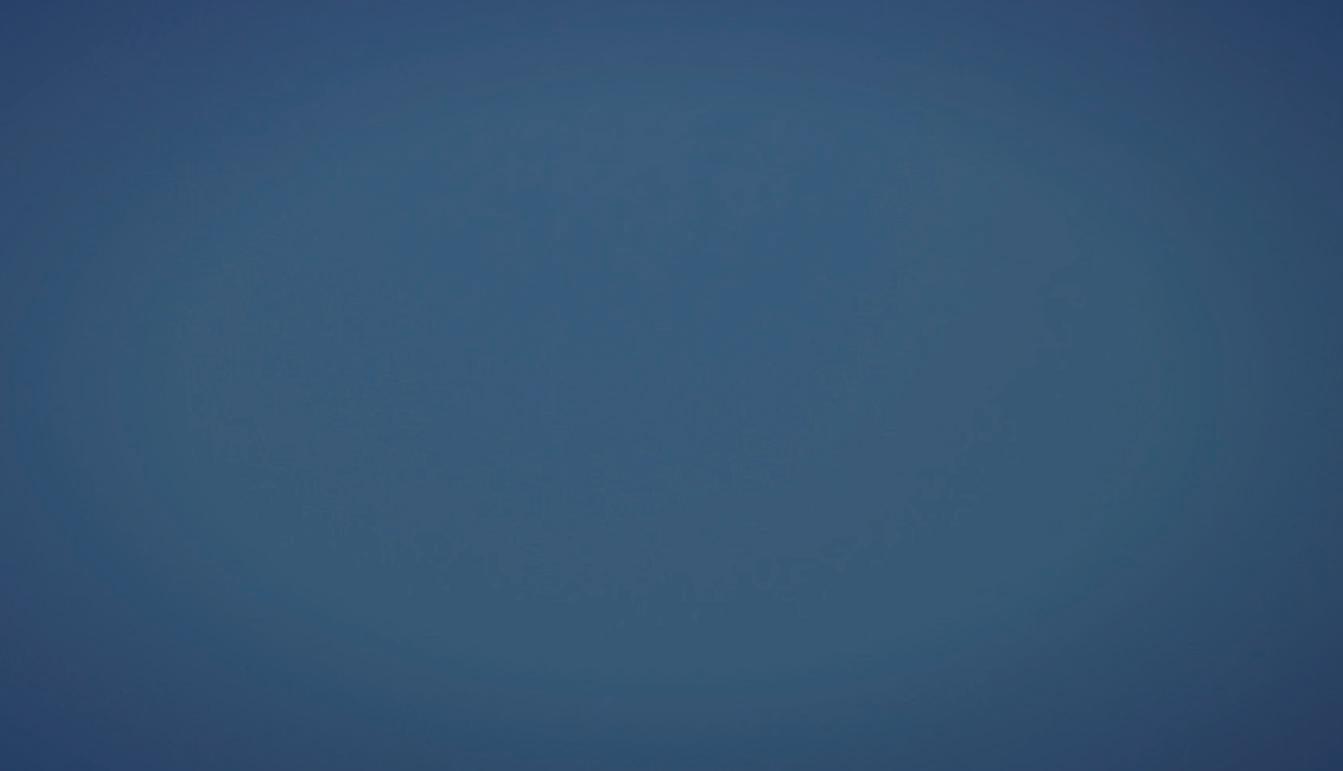
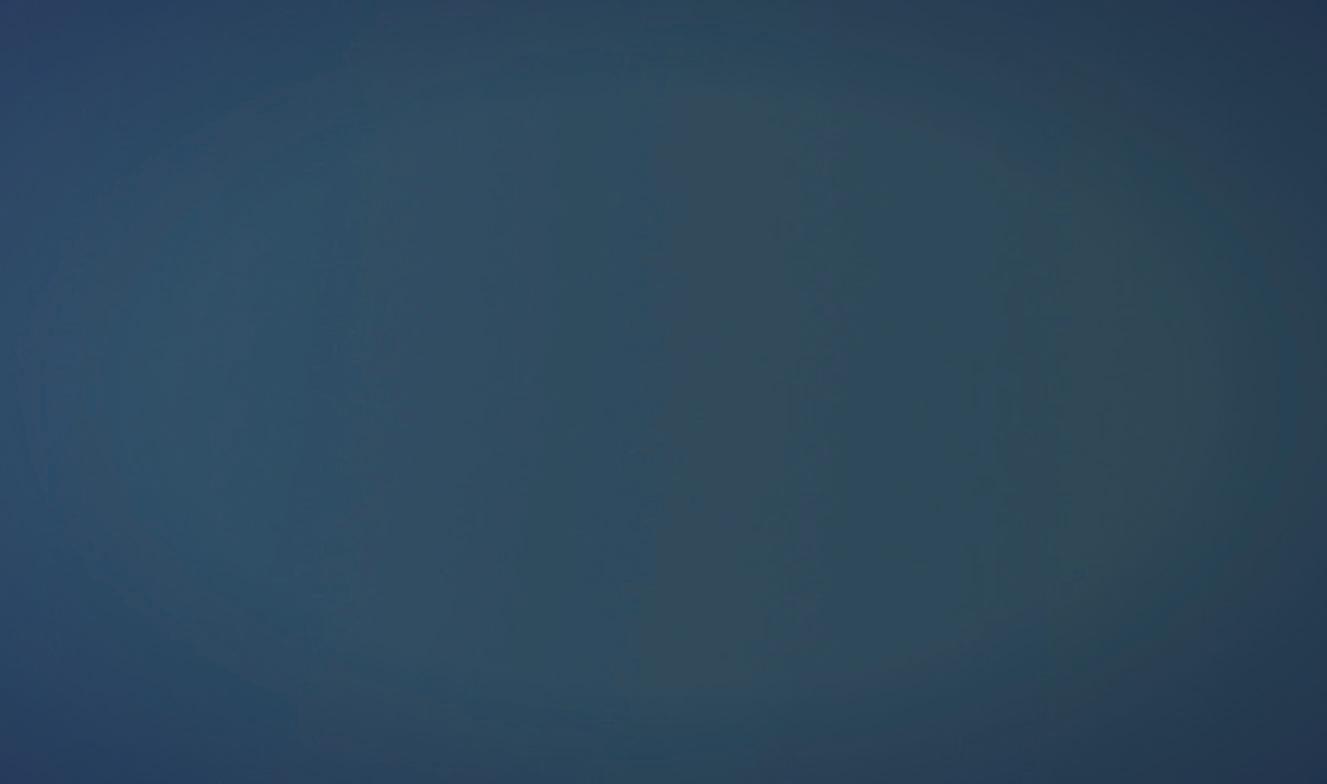





North America’s largest and most influential Additive Manufacturing event.
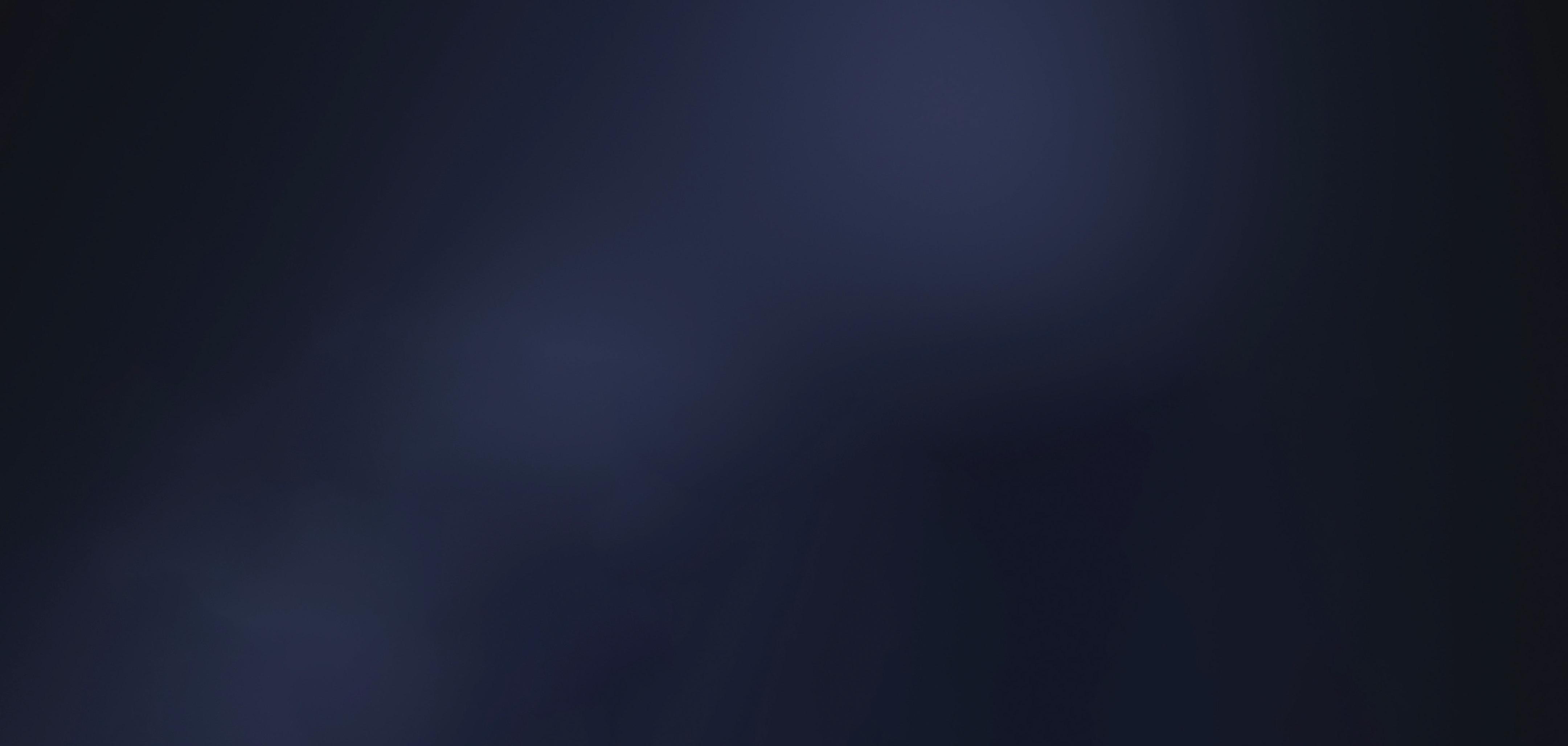








