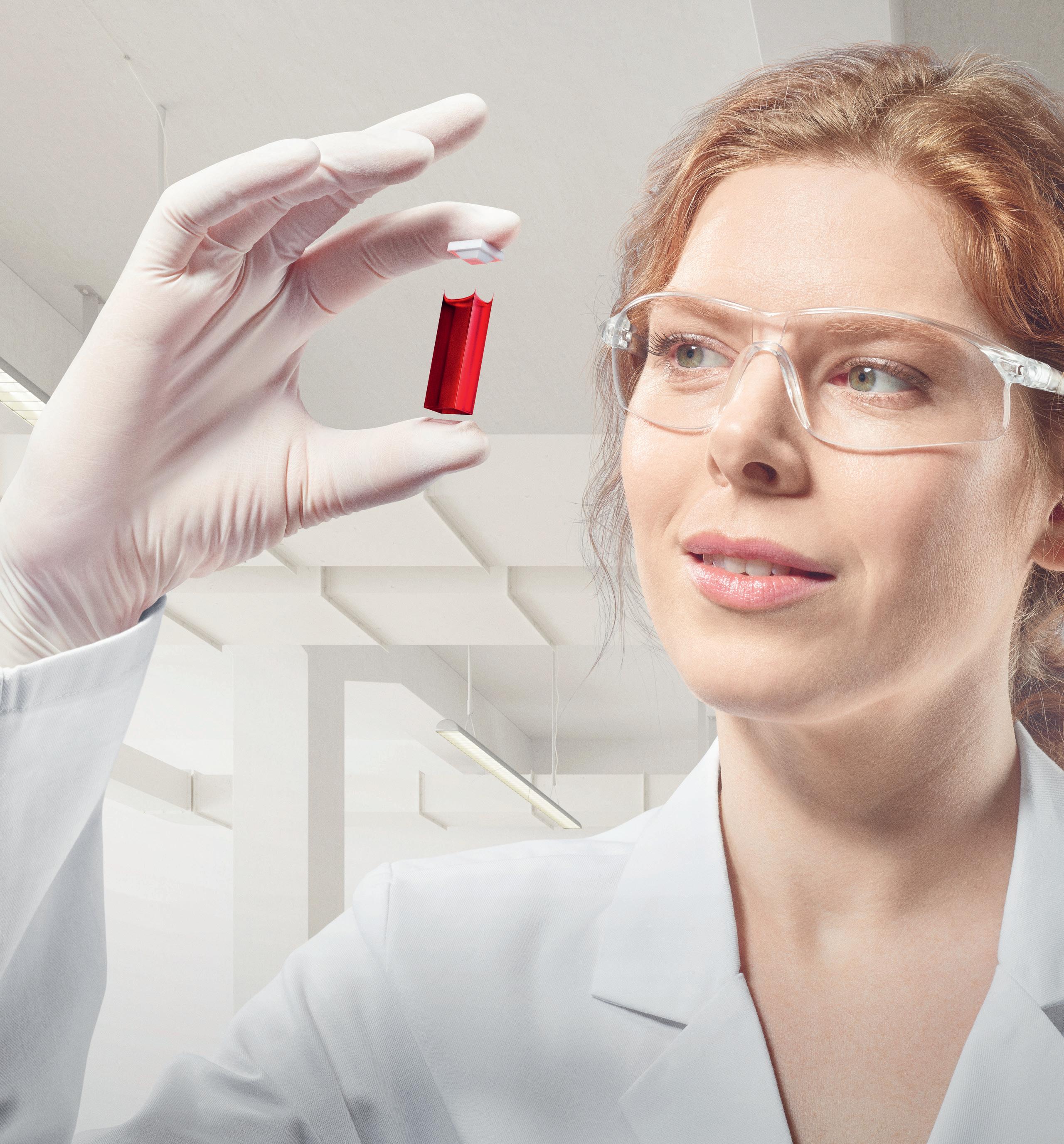
3 minute read
Events: The talk of the show
from MPN EU Issue 62
by MPN Magazine
MPN TAKES A LOOK AHEAD AT THE CONFERENCES COMPLEMENTING THE MEDIPLAS ZONE AT THIS YEAR’S INTERPLAS EVENT.
There are myriad reasons to attend this year’s Interplas (28–30 September 2021, Birmingham, UK) event, but did you know it has its own medical plastics zone? The highly specialised area of manufacturing plastic parts for the medical industry is one of the fastest-growing sectors in the plastics industry and the Mediplas Zone will return once again in 2021 to focus the spotlight on the essential aspects and considerations of medical device manufacturing that are unique to the sector.
Organised in conjunction with Medical Plastics News magazine, this special feature zone will enable visitors to quickly identify the exhibitors showcasing technologies, materials and services relevant to their fi eld.
In addition, the Mediplas Zone will be complemented by a conference track on the Main Stage programme where experts will deliver sound advice crucial to medical device designers and manufacturers on a range of issues. It’ll be great to see you there! Can Attention to the Design of Plastics in Medical Devices Support Patient Safety?
Speaker: SARAH JENNINGS, NATIONAL PATIENT SAFETY LEAD, NHS ENGLAND & NHS IMPROVEMENT Date and time: Wednesday 29 September, 14:00–14:30
The National Patient Safety Team at NHS England & NHS Improvement provide clinical and non-clinical patient safety expertise for the NHS. We utilise information from within healthcare, and patient safety incident data reported into the National Reporting & Learning System (NRLS) when things go wrong in healthcare. This enables identifi cation of new and under recognised patient safety themes and trends. Reviewing medical devices within the ‘system’ of use, including users and the environment, can identify design features that may support the user in maintaining patient safety or present hazards due to the environment in which it is used. This talk will outline the role of the National Patient Safety team and provide examples of how designers and manufacturers of plastic components can support patient safety.
Innovative Drug Delivery for Improved Patient Compliance
Speaker: SIMON CHIDGEY, SALES AND MARKETING DIRECTOR, CONSUMER PACKAGING, BERRY GLOBAL Date and time: Wednesday 29 September, 14:30–15:00
The patient and provider relationship has never evolved so quickly as we observed in 2020. What the future holds in patient care is still to be written, but the use of technology for improved communication and improved patient outcomes across the healthcare system will only grow. This is exactly where some of the greatest innovation and leading patient-centred design is taking hold with Berry Global’s Healthcare Division. Join this seminar to hear how a global leader in inhalation devices has identifi ed a path to bring patient-centred design with the needs of healthcare systems around the world.
Manufacturing Technologies for a Post-Pandemic World — Injection Moulded 3D Micro and Nano-Structured Surfaces for Reduced Antimicrobial and Antiviral Activity on Consumer Goods
Speaker: BEN WHITESIDE, DIRECTOR, CENTRE FOR POLYMER MICRO AND NANO TECHNOLOGY, UNIVERSITY OF BRADFORD Date and time: Wednesday 29 September, 15:00–15:30
The University of Bradford is pioneering research into the production of functional nanostructures on injection moulded components with 3D surfaces. By making signifi cant developments in tooling approaches, processing technologies and characterisation methods, they can produce highly detailed yet robust surface structures using standard engineering polymers that have been proved to reduce droplet adhesion, bacterial attachment and the subsequent formation of biofi lms. This approach off ers a low-cost method for adding physical functionality to moulded products while avoiding the need for additives or coatings which add cost and reduce recycling options.
So clear it’s like it’s not even here: highly transparent CYROLITE® for diagnostic applications.
We invented CYROLITE® over 40 years ago – and we’ve used the time ever since to perfect its properties. The result is highly advanced acrylic polymers that boast out standing optical properties such as superior UV transmittance. At the same time, CYROLITE® offers excellent fl ow properties, thus enabling them to be molded into extremely thin- walled components. It goes without saying that CYROLITE® meets all the relevant USP Class VI, ISO 10993-1, and REACH standards. For more reasons why CYROLITE® is the clear choice, visit www.cyrolite.com.
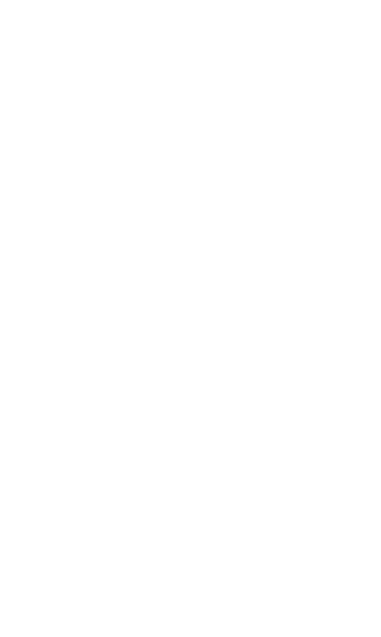
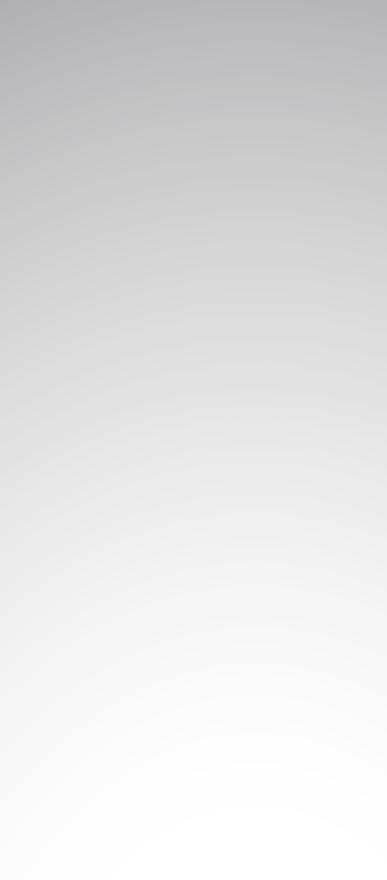
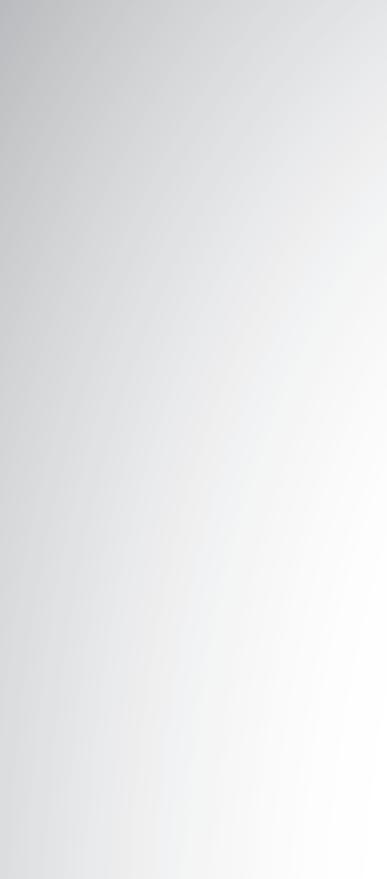