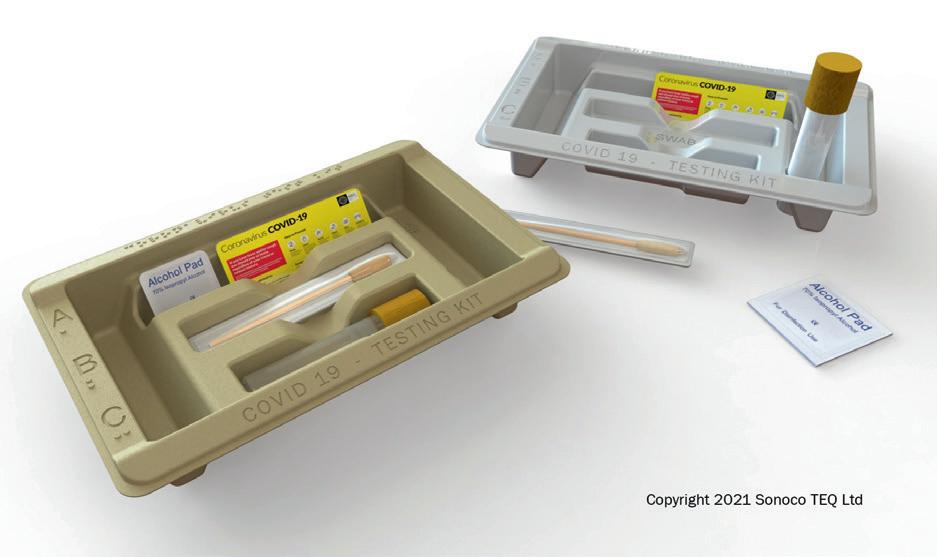
5 minute read
Thermoforming: The heat is on
from MPN EU Issue 62
by MPN Magazine
THERMOFORMING IS PROVING ITSELF A POPULAR MANUFACTURING TECHNIQUE, ESPECIALLY IN THE PHARMACEUTICAL AND MEDICAL PACKAGING SECTORS. TODD MCDONALD, GLOBAL DIRECTOR OF SALES AND MARKETING AT TEQ HIGHLIGHTS WHY.
THE HEAT IS ON
The global market for thermoforming plastics estimated at $35.4 billion in 2020 is now projected to reach a revised size of $51.2 billion by 2027, growing at a CAGR (Compound Annual Growth Rate) of 5.4% during the 2020–2027 period.1
The increasing demand for thermoformed plastics from the healthcare and pharmaceutical packaging sectors is a force driving the market growth over the forecast period. The growth has been triggered by a hike in demand during the COVID-19 global crisis (Figure 1). Demand is expected to rise across different healthcare packaging types including blister foils, pumps, closures and rigid plastics. Demand will also grow for packaging in dietary supplements, such as vitamins and for other essentials such as allergy medication that consumers need during a lockdown, for instance.
The advanced technology of thermoforming has established itself as a favourite manufacturing technique for many industries and applications, with a major benefit being cost efficiency. The stiffness of thermoformed packaging allows manufacturers to create smaller units, offering space-saving benefits; it also offers a barrier to odours, and resistance to oil and grease.
Packaging from cleanroom thermoforming also has the capacity to offer advanced protection of medical devices, the importance of which cannot be underestimated as the quality of the packaging is as important as the medical device contained therein — once the packaging’s integrity is compromised, sterility is lost and the device is potentially ruined.
Figure 1: TEQ started manufacturing COVID-19 testing kit trays earlier this year with a pledge that they offer ‘superior presentation’ and ‘enhanced component protection’.
THERMOFORMED PLASTIC PACKAGING OFFERS THE HEALTH SECTOR A RANGE OF ADVANTAGES:
Accurate product orientation: For those occasions when a nurse has to grab a product, the ability to quickly confirm its orientation is reassuring. With a thermoformed tray, the medical device remains securely in place so it can be removed swiftly and confidently.
Device handling assurance: To ensure a device doesn’t compromise sterility, a nurse may need to control a device’s movement as its package is opened. A thermoformed package is more likely to prevent any unnecessary rotation or accidental removal.
Clarity of products: Thermoformed packaging enables a nurse to see and identify a product clearly so the device can be better presented. It also allows a nurse to spot any defects.
Consistent opening experience: Incorporating a generous peal area in the package design allows a nurse an easy access point for pealing the lid back from the package.
Additional protection: Rigid plastic off ers sensitive medical devices additional protection; for example, a carefully designed package can stop a syringe from depressing.
Increased ergonomics: A pouch can require both hands to twist it open, putting repetitive strain on a nurse’s wrists. With a sealed thermoformed tray, only one hand is needed to open the seal, while the other holds the tray in place.
Other advantages of thermoforming include cost-eff ective tools and moulds, reasonable processing times from design to prototype, large surface-to-thickness ratios, the option to process large and multilayer parts, and a range of machinery that can work with thick- and thin-gauge plastic sheets (Figure 2).
CLEANROOMS
Cleanroom thermoforming is widely used for the production and packaging of pharmaceuticals and medical equipment. This method of thermoforming is done in an ISO- (International Organisation for Standardization) certifi ed cleanroom so that any particulates circulating in the air are kept to a minimum.
Thermoform packaging is extensively used to safeguard sterile instruments and implants. This packaging method permits the use of lightweight, clear plastic enclosures that stop microbial and dust particles from contaminating the sterile item.
Cleanrooms have played a leading role during the horrors of the Covid pandemic as their controlled and sterile environment guarantees cleanliness, preventing potential contamination caused by bacteria or air pollutants.
Companies making medical devices and their packaging have to meet stringent regulations. The ISO, which consists of a group of nongovernmental bodies operating in 164 countries, is entrusted with the power to enforce exacting standards for a range of commercial markets.
In 2016, it published the latest edition of its ISO 13485, which sets out to ensure patient safety by regulating hygiene and contamination control in medical product development. Cleanrooms must have the ability to deal with any air pollutants. Manufacturers use fi ltration units — such as ionisers, carbon fi lters and non-fi lter purifi ers — to control airfl ow and stop airborne particles larger than a predefi ned size from entering.
Another cleanroom contamination prevention tactic is providing a high standard of staff training, ensuring they wear correct personal protective equipment such as gowns, hairnets and overshoes.
Manufacturers are also advised to keep correct supplies and equipment in clean spaces and, where appropriate, dispose of or sterilise them. Cleanroom apparel would normally feature gowns, face masks, sterile gloves, boot or shoe covers, coveralls and head covers. High-quality cleanroom wipes are essential supplies for a cleanroom environment and maintaining its sterilisation. A supply of cleanroom-grade cleaners and disinfectants in spray bottles are also important items of equipment.
Cleanroom tacky mats or sticky mats, which are normally placed at the entrances to cleanrooms so any contaminants stuck to the bottom of footwear can be safely removed, are also found in most cleanrooms.
LOOKING AHEAD
Regular risk assessments ensure ongoing improvements can be made to foil any new contamination threats triggered by ever evolving technologies.
Continued innovation and the advance in technology in the medical sector brings with it unlimited potential.
In years to come manufacturers will face the usual pressures to slash costs and be even more effi cient by introducing more automation on the assembly line, utilising the likes of robots and smart testing. Artifi cial intelligence and machine learning are also expected to play a role by boosting quality standards and early detection of potential issues.
New developments and a move towards more complicated products such as nanotechnologies and the miniaturisation of devices are another new challenge that manufacturers have to face in an increasingly competitive sector.
REFERENCE
1. Research and Markets, “Global Thermoforming Plastics Market to Reach $51.2 Billion by 2027”, April 2021.
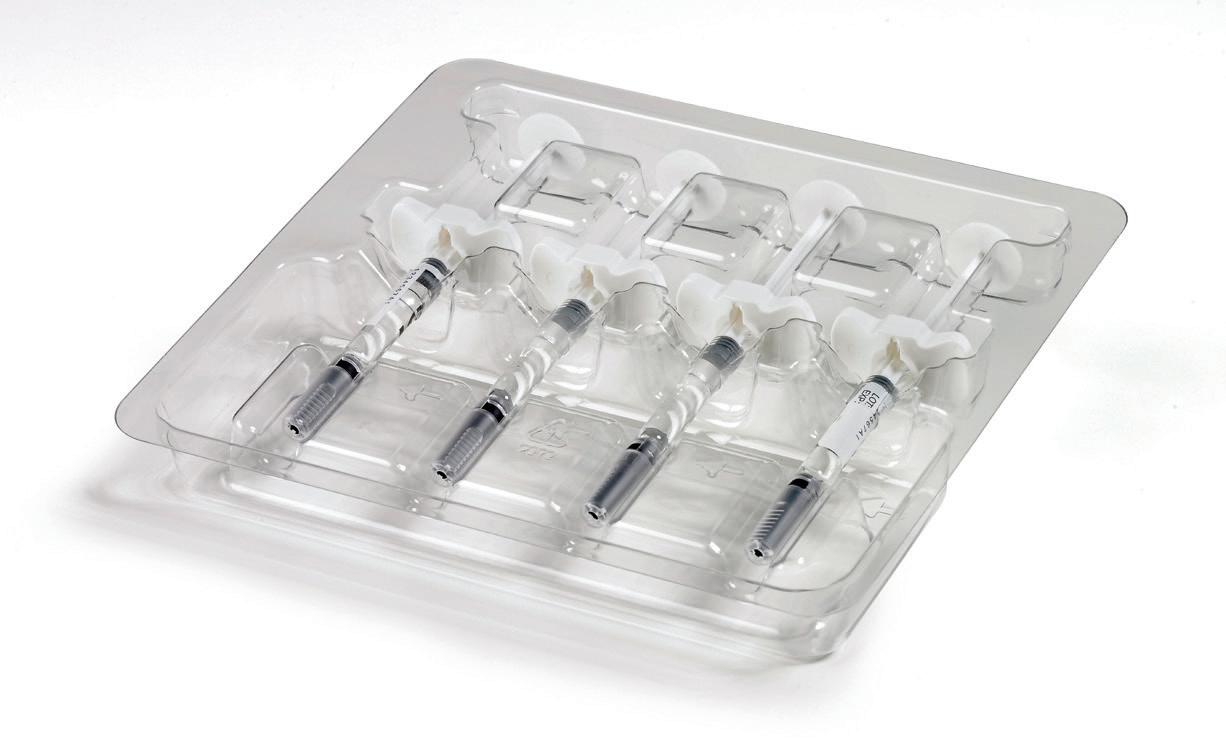
Figure 2: TEQ manufactures custom thermoformed handling trays for a wide range of applications, including dry powder inhalers, auto-injectors, injectionmoulded components, pre-fi lled syringes and pharmaceutical bottles.