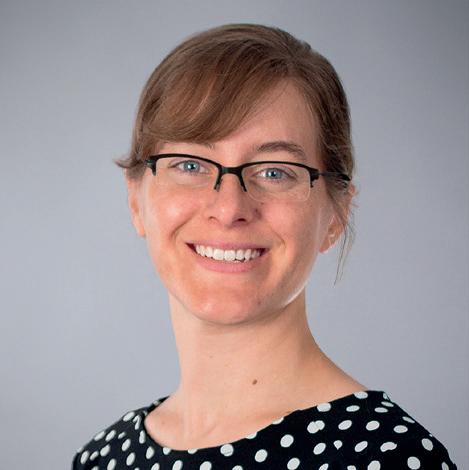
5 minute read
Adhesives: Surface control
from MPN NA Issue 18
by MPN Magazine
ROSE ROBERTS, SENIOR CUSTOM APPLICATIONS & MATERIALS ENGINEER, AND MATTHEW NICHOLS, MATERIALS & APPLICATIONS ENGINEER OF BTG LABS EXPLAIN HOW CONTROLLING SURFACE CLEANLINESS CAN SAFEGUARD THE FUTURE OF MEDICAL DIAGNOSTIC TESTING.
SURFACE CONTROL
COVID-19 has highlighted how infectious diseases can spread at alarming rates and paralyze entire societies. Diagnostic testing is one of many effective tools that can be used to help prevent disease proliferation. Diagnostic tests depend on reliable medical devices that produce consistent results for each test.
CONTROLLING MEDICAL DEVICE PRODUCTION PROCESSES Manufacturing process control is especially critical when producing medical devices. Incorporating surface quality specifications for materials used in medical device design enables manufacturers to make products that perform consistently in the field and provide reliable test results.
Polymeric testing devices such as diagnostic slides or microplates are handled, cut, cleaned, and coated during their assembly. Each of these steps has the potential to affect the caliber of products; quantitative control of these steps during the manufacturing process ensures the quality and reliability of these devices.
CONSISTENT SURFACE QUALITY IS KEY FOR RELIABLE DIAGNOSTIC TEST RESULTS Effective diagnostic testing methodologies are predicated on consistent, predictable behavior of body fluids as they interact with the surface of a device. This frequently requires cleaning, surface treatment, and perhaps coating. These surfaces need to be prepared to a consistent level of chemical cleanliness and composition.
Lateral flow assays (LFAs) are an example of products that need consistent, predictable wetting properties. Enzyme-linked immunosorbent assays (ELISAs), which are used to test for COVID-19, are one type of LFA. ELISA tests depend on capillary flow between two closely spaced surfaces. Reliable capillary flow requires surfaces that are reproducibly clean on a molecular level. Even a monomolecular layer of a contaminant can impede this capillary flow and cause device failure.
CAPILLARY FLOW AND VACUUM DEPOSITED COATINGS Hydrophilic coatings facilitate successful capillary flow. A common method of applying these coatings to diagnostic plates is through vacuum deposition processes.
Physical vapor deposition (PVD) and chemical vapor deposition (CVD) are two of the vacuum deposition methods used to apply these molecularly thin coatings on surfaces. Consistently applied coatings drive consistent wetting behaviors and, therefore, achieve reliable testing results.
MICROPLATE WELL DENSITY A single 3.25” x 4.5” microplate may contain more than 1500 wells. Individual wells can have diameters of 3 mm and depths of 10 mm. These wells are frequently coated in batch vacuum processes. The miniscule cell size and submicron coating thickness makes testing the uniformity of these coatings extremely challenging.
Figure 1: Clean, high energy surfaces pull liquids to the surface, creating a low contact angle. Contaminated, poorly treated, low energy surfaces cause the liquid to bead up, resulting in high contact angles.
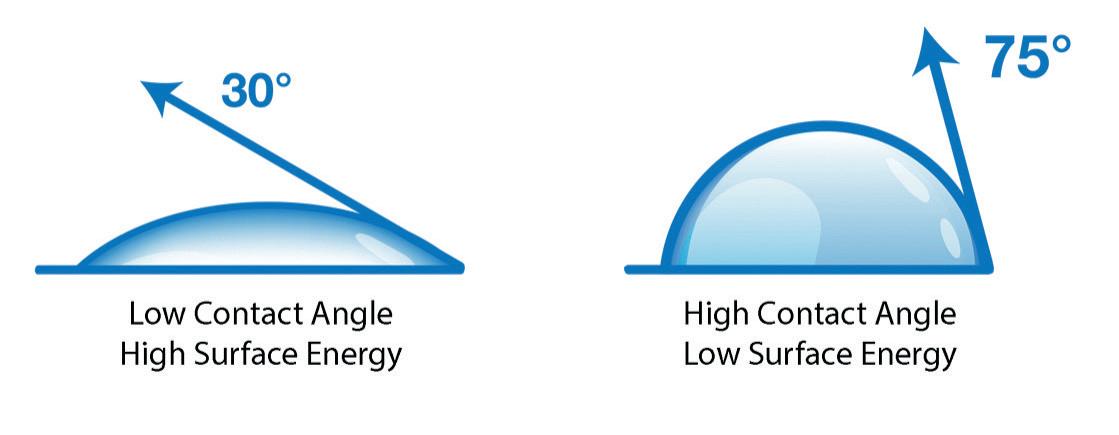
Few appropriate techniques exist for quantitatively ensuring quality and consistency of important device surface properties. The century-old technique of contact angle measurement, however, can be adapted to provide an excellent quantitative interrogation of these properties.
WATER CONTACT ANGLES Contact angle measurements provide vital insight into the chemical state of a material surface. When a drop of liquid is deposited on a surface, the surface will repel or attract the droplet, causing it to bead up or flatten out, respectively. The attraction between the surface and the water is quantified by measuring the angle formed between the substrate surface and the drop edge.
A surface that will be coated or bonded will be chemically clean and have a high surface energy. This is characterized by a water droplet that spreads to form a low contact angle across the surface. This indicates that there are many active chemical groups on the surface pulling the water droplet to the surface (Figure 1). The way that these chemical groups attract the water droplet indicates how a coating or adhesive will spread. If the water droplet does not spread, neither will the coating. A high contact angle indicates the presence of a surface contaminant or the need for additional surface preparation before bonding or coating. When a coating has been homogenously applied, contact angles will be uniform across the surface.
Various types of coatings are used in the medical industry. As described above, when capillary action is required for diagnostic devices and a hydrophilic coating is in place, contact angles should be low (high surface energy). Alternatively, hydrophobic coatings, like those used for catheter applications, require high contact angles (low surface energy). In either case, contact angles provide a direct method for quantifying the surface wetting properties both before and after applying a coating or adhesive.
VALIDATION OF MEDICAL DIAGNOSTICS COATINGS
For general applications there are handheld devices available that enable rapid contact angle measurement at any location on the production floor and on any material surface. This mobile ability to measure contact angles is highly adaptable and of great value to many manufacturers.
Rapid water contact angle testing performed by the Surface Analyst line of products provides an effective method to validate surface state including cleanliness, treatment level, coating presence and uniformity.1 The Surface
Analyst is used to validate surface quality on many types of medical diagnostic devices. Integration of the Surface Analyst with an automated collaborative robot allows measurement of the surface quality inside individual microplate culture wells. The Surface Analyst takes these measurements by depositing a tiny drop of purified water straight down into the culture well.
Robotic deployment ensures precise positioning of the camera and the water droplet. Automation of rapid water contact angle measurements allows manufacturers to validate coating presence and uniformity on medical device surfaces by producing reliable and consistently repeatable contact angles.
For microplate applications, statistical sampling techniques are used to establish how many individual wells need to be evaluated to generate statistically valid results. Once these statistical models have been established, manufacturers can develop “pass/fail” parameters for the production process.
Accurate and rapid validation of medical device surface properties has been made possible through new and innovative technology such as the Surface Analyst line of products. With the support of materials science experts, medical device manufacturers can now achieve statistical process control of their coating, printing, bonding, sealing, and cleaning operations. This statistical process control helps ensure that medical diagnostic devices will consistently perform as expected.
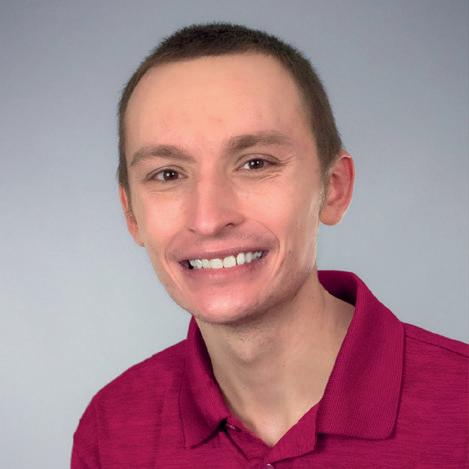
Note: Surface Analyst is a Trademark of BTG Labs.
REFERENCE
1. https://www.btglabs. com/products?utm_ campaign=Publication%20
Articles&utm_source=mpn-futureof-medical-diagnostic-testing-relieson-surface-cleanliness-article&utm_ medium=june-2021-product-pg