
11 minute read
Cover story
from MPN NA Issue 21
by MPN Magazine
KEVIN LADOW, MEDICAL PRODUCT MANAGER USA WEST AT JUNKOSHA, REVIEWS THE NEXT STEPS NEEDED BY END USERS AS PATIENT CARE CONTINUES TO TOP THE AGENDA FOR HEALTHCARE SETTINGS.
The Journey Towards Intelligent Catheters
The journey towards intelligent catheters is an important one, both from the clinician’s and the patient’s perspective. Their development is necessary to accelerate the shift from costly, burdensome surgical treatments towards cost-effective and minimally invasive interventions. To treat a wider range of patients and types of disease, it is crucial to have smaller and more flexible, high signal capacity catheters at the surgery team’s disposal. This type of tool will provide surgeons with the highquality imaging to precisely identify patient anatomy to help maximize the safety and efficacy of the procedure. Decreasing the size and increasing the flexibility of these catheters will help the physician more effectively navigate demanding patient anatomy, resulting in efficient and accurate devices or therapeutic delivery. Together, these advancements result in tangible, direct benefits for the patients, such as greater access to safer, less invasive procedures, with quicker recovery times.
Intelligent catheters, with new diagnostic and therapeutic capabilities, will enable the development of new, advanced therapies for diseases that are currently treated by complex surgical procedures. This will allow for more individuals to be treated and minimize risks, improving quality of life and reducing death rates for these patients. Intelligent catheters will allow a wider range of functions to be integrated into single, small devices in a cost-effective and industrially feasible manner. Since catheter-based procedures are typically done on an outpatient basis, they do not require an expensive OR suite or recovery in a hospital bed.
To this end, solutions such as Multi-Filar Cables and Multi-Channel Transmission Cables (MCT) represent a breakthrough in the design of medical device cables that take us closer to the next generation of these important devices.
The innovation behind the Multi-Filar active cables is significant. Multi-Filar cables can have a capacity of up to 60 lines and are designed to provide not only increased functionality but also more signals into formerly inaccessible areas of the body.
Using Junkosha’s PTFE lamination technology, single strand configurations are joined into a Multi-Filar assembly that can be used in electrophysiology catheters for applying pacing and recording protocols from inside the heart, ablation and balloon ablation catheters for atrial fibrillation as well as cardiac mapping.
The Multi-Filar technique also allows for easier assembly of the signal or power wires into the final medical device, making the overall manufacturing process simpler and more cost-effective.
The manufacturing process is complicated, which Junkosha has refined by being able to accommodate the specific requirements for the final product design. For example, each individual strand can be color coded in the material, in accordance with specific industry standards or to make connection operations more simplified in downstream operations. The bond strength between the individual strands can be adjusted to maximize strength for challenging assembly conditions or optimized for difficult separation processes. MultiFilar configurations allow for joining dissimilar single strand alloys together in one package. This flexibility in alloy selection is suited for applications like thermocouples, micro cables that need a high strength member for load bearing or assembly operations and electrochemical process cells.
MULTI-CHANNEL TRANSMISSION CABLES Multi-Channel Transmission (MCT) cables are another step towards intelligent catheters. MCT represents a significant improvement on existing shielded twisted pair, coaxial and Flexible Printed Circuit technology and enables new data-rich signals to be utilized in therapies such as Intracardiac Echocardiogram, Ultrasound Endoscopy and Intravascular Ultrasound (IVUS).
Existing catheters use shielded twisted pair or coaxial constructs to support signals along the device. This established technology has driven advances in catheter design and facilitated the delivery of many essential interventional, intervascular diagnostics and therapies. However, the progress towards miniaturization and flexibility has been hampered by the standard coaxial approach which comprises a core conductor, insulation, and a shield wire. Physics and electromagnetics have prevented the development of smaller cables and have inhibited catheter flexibility.
In contrast, the new MCT cable design includes four times the amount of signal lines per individual cable, while preserving signal to noise performance. This is thanks to Junkosha’s shielding/grounding design. Whereas the traditional catheter requires two coaxial cables to run in parallel carrying two individual signal streams, MCT enables multiples of four signals to be brought together in one cable.
Early prototypes have achieved a 32% reduction in the size of the cable, a critical factor in the attainment of future procedures within narrower vessels. The MCT approach also provides a greater degree of flexibility compared to the existing approaches which promises major advances in the scope of medical procedures, especially within endoscopy. Overall, this innovation addresses the mutually exclusive needs of small size and signal integrity simultaneously. This in turn unlocks opportunities for catheter manufacturers to deliver valuable, previously unrealised options, to clinicians. LOOKING AHEAD The pace of change in the medical device sector is increasing continuously. An example of this is the development of mapping catheters, which are used during cardiac and electrophysiological therapies. Mapping catheters help physicians to discover and evaluate the electroanatomical layout of the heart and surrounding area. Previously believed to be impossible, catheterbased solutions are now available to accurately pinpoint problems within blood vessels and the heart. Interventional procedures utilizing intelligent catheters rather than highrisk surgery will allow medical teams all over the world to decrease the risk to all patients, decrease recovery times, and to develop new therapies to heal diseases that until now have been impossible to treat.
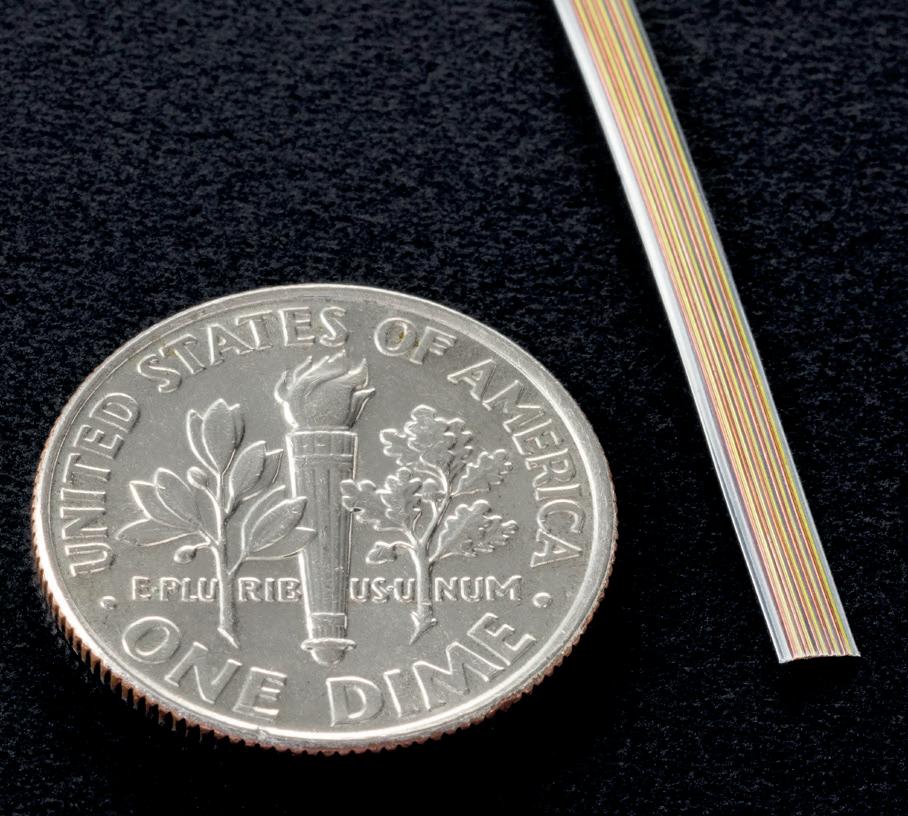
As the requirement for complex catheter-based procedures increases, the need for innovations such as the Multi-Filar Cables and the Multichannel Transmission Cables become paramount to enable them. Solutions such as these are continually pushing the boundaries of what is possible with minimally invasive devices and intelligent catheters, unlocking opportunities for OEMs to deliver improved patient outcomes, quicker recovery times, and lower costs of care. These solutions will be key to expanding the capabilities of medical teams around the world, helping reach maximum levels of medical quality and patient care, even in areas where, traditionally, medical resources have been scarce.
TEXAS MEDICAL TECHNOLOGY HAS BEEN BRINGING PPE TO CANADA DURING THE PANDEMIC. OLIVIA FRIETT HAS SPOKEN TO TEXAS MEDICAL TECHNOLOGY TO LEARN MORE ABOUT IT.
Protecting the nation
Texas Medical Technology, a manufacturer and distributor of medical supplies, is partnering with Indigenous Medical Industries Canada (IMIC). They’re building a Personal Protective Equipment (PPE) factory on an Indian reservation in Canada to produce medical equipment that the company and community feels is severely lacking.
IMIC was founded to bring healthcare to Canadians. During the pandemic, the local governments were struggling to protect the communities, so IMIC stepped in to help. Texas Medical Technology specializes in the sale and distribution of medical equipment at low prices.
Omri Shafran, CEO of Texas Medical Technology said: “I think the pandemic provided a huge mirror and showed each country a reflection of their preparedness. With no ability to protect themselves, healthcare providers are dependent on China for PPE. It creates a very fast race between all countries to become independent, from the perspective of PPE.
“These communities deal with many issues including Covid like lack of drinking water, food security, access to timely health care, etc. We hope to improve at least one of them i.e. spread of Covid and the overall need for PPE in their communities.”
IMIC has stated that it is aiming to provide essential medical clothing, PPE and devices to not just the First Nation, but all Canadians. The use of disposable surgical gowns, shoe covers, PPE kits, digital thermometers and PPE safety machines will help keep the Covid cases at an all-time low.
With sustainability being such a huge topic today, choosing the right fabrics is no easy feat. “We are going to use a very innovative product, for example, a new coat for the SMS with copper. This protects the fabric for a longer time and kills the virus once it hits the surface.” Shafran said. “We are very aware and care about our planet, so therefore we use SMS fabric. We are going to incorporate more environmentally friendly products in the future.”
Copper has been shown to have antibacterial properties, meaning it’s a popular choice for PPE. The use of SMS (spunbond-meltdown-spunbond) fabric is favored for face masks as it has great water repelling capabilities. They believe that Canada is one of the most innovative markets in pushing their indigenous communities and in helping them have equal opportunities to enter the job market. In addition to helping protect the nation, 10% of the profits of the joint venture will go towards helping Canada’s Indigenous populations further improve their overall access to healthcare.
Texas Medical Technology has also shared with MPN that they are hoping to bring more medical products to the community in the future: “We are going to bring very innovative products to the Canadian market. We have a lot of Israeli startups, for example, which are looking to sell their products in Canada—as well as in the US. We are going to present an innovative diabetic skin care product as well as innovative female hygienic solutions.”
In addition to helping protect the nation, the factory will create many new job opportunities.
MICHAEL BUTLER, KEY ACCOUNTS MANAGER AT EMERSON SHARES THE STORY ON HOW THEIR BUSINESS ADAPTED TO THE PANDEMIC.
How one molder addressed face mask shortages…
At the outbreak of the COVID-19 pandemic, governments, military establishments and healthcare systems everywhere were scrambling to locate suppliers of personal protective equipment (PPE) after demand skyrocketed in spring 2020.
In Northern Ireland, the situation was no different, as Health and Social Care Northern Ireland (HSCNI) confronted the critical shortage. Northern Ireland’s health minister, Robin Swann, said: “The demand for PPE in the first surge of the pandemic placed tremendous strain on the health service. We had to urgently consider how best to meet the challenge of protecting our health and social care staff while safely treating COVID-19 patients.” To fill the supply gap, HSCNI turned to the region’s manufacturers.
Quality technician Lisa McBride (below) demonstrates Denroy products to economy minister Diane Dodds (left) and health minister Robin Swann (second left). Chief executive of Invest NI Kevin Holland and chief executive officer of Denroy Group Kevin McNamee. At about the same time, Denroy Group, based in Bangor, Northern Ireland, a major designer and producer of injection-molded products for aerospace, medical, automotive and hair-care products, experienced a significant contraction in its aerospace business due to the pandemic. Seeking ways to redeploy unused engineering and production capacity, Denroy responded to HSCNI’s request and obtained approval to rapidly tool up, produce and deliver more than 1 million medical face shields to HSCNI for use by frontline medical workers. During the summer and fall of 2020, the company also decided to develop, produce and market a consumer-focused face mask, called the Bubl. Made of clear, molded plastic, this washable, reusable mask features two circular filter ports that contain prefabricated filter elements made of layered, nonwoven fibers. The design allows users to replace the filter elements with new elements every few days.
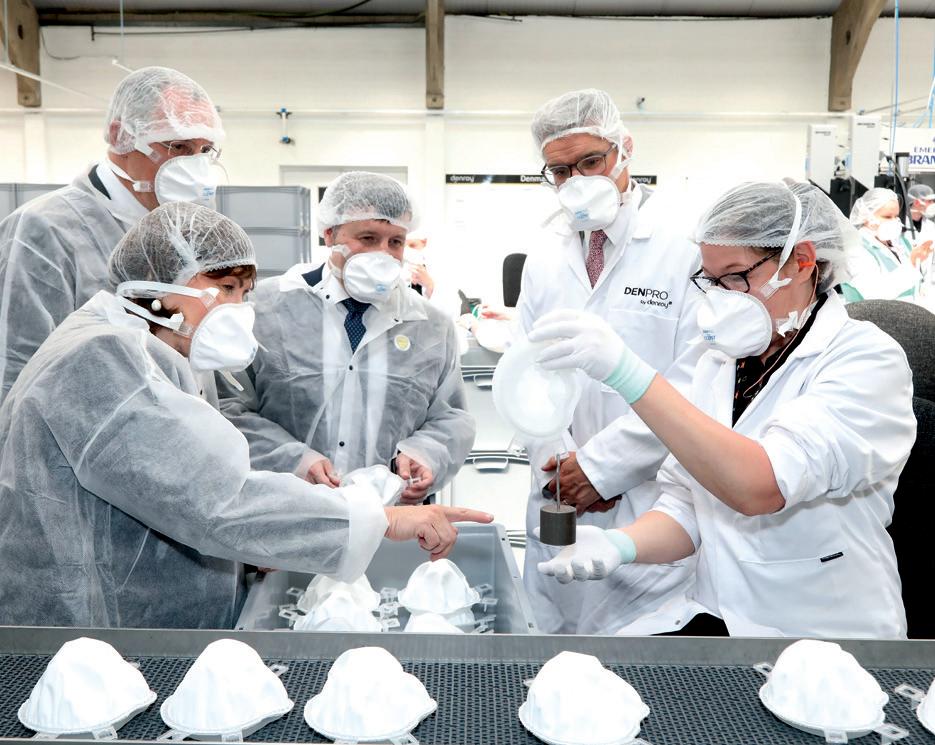
Medical and clinical personnel in contact with COVID-19 patients require a greater degree of protection than typical surgical masks provide. Such protection is provided by medical-grade face masks that combine a leak-resistant face seal and highly effective filtration of airborne droplets and particles. CE standards define two types: FFP2 face masks provide a minimum of 94% particle/droplet filtration with a maximum outside air leakage of 8%, while FFP3 masks provide a minimum of 99% particle filtration and maximum leakage of just 2%.
“Designing a high-grade medical face mask is all about balance,” explains Denroy’s CEO Kevin McNamee. “To attain BSI and CE approval, the mask must pass strict testing criteria on filtration, breathability and internal CO2 levels. In addition, it must also provide the highest possible level of comfort and visibility and be simple to fit and remove. Of course, balancing these factors is challenging, since a minor change to improve on one requirement can have a significant effect on others.” He credits medical and clinical experts, together with HSCNI procurement experts, for the “invaluable” advice that helped Denroy finalize the design of the Denpro FFP3 medical face mask.
Instead of the typical FFP3 mask designs that rely on a heat-formed shell made of filter material, the Denpro mask is built around a lightweight, injection-molded frame that includes holders for four user-adjustable elastic straps. A soft filter “cup” made of four nonwoven fabric layers is bonded onto one side of the frame, while a comfortable, face-hugging thermoplastic elastomer (TPE) foam seal is bonded to the other. The combination gives the Denpro mask a great fit, all-day wearer comfort and plenty of highperformance filtration capacity.
MANUFACTURING CHALLENGES Because of the COVID-19 emergency and the urgent need for PPE, McNamee says that the timelines for every aspect of the Denpro mask development were dramatically compressed.
According to McNamee, “The FFP3 medical mask development, CE approval, tooling, production equipment design and establishment of a new production facility were all conducted at a rapid pace, with the product moving from concept to production in five months. The FFP3 factory is now fully operational with an annual capacity of over 10 million Denpro masks.”
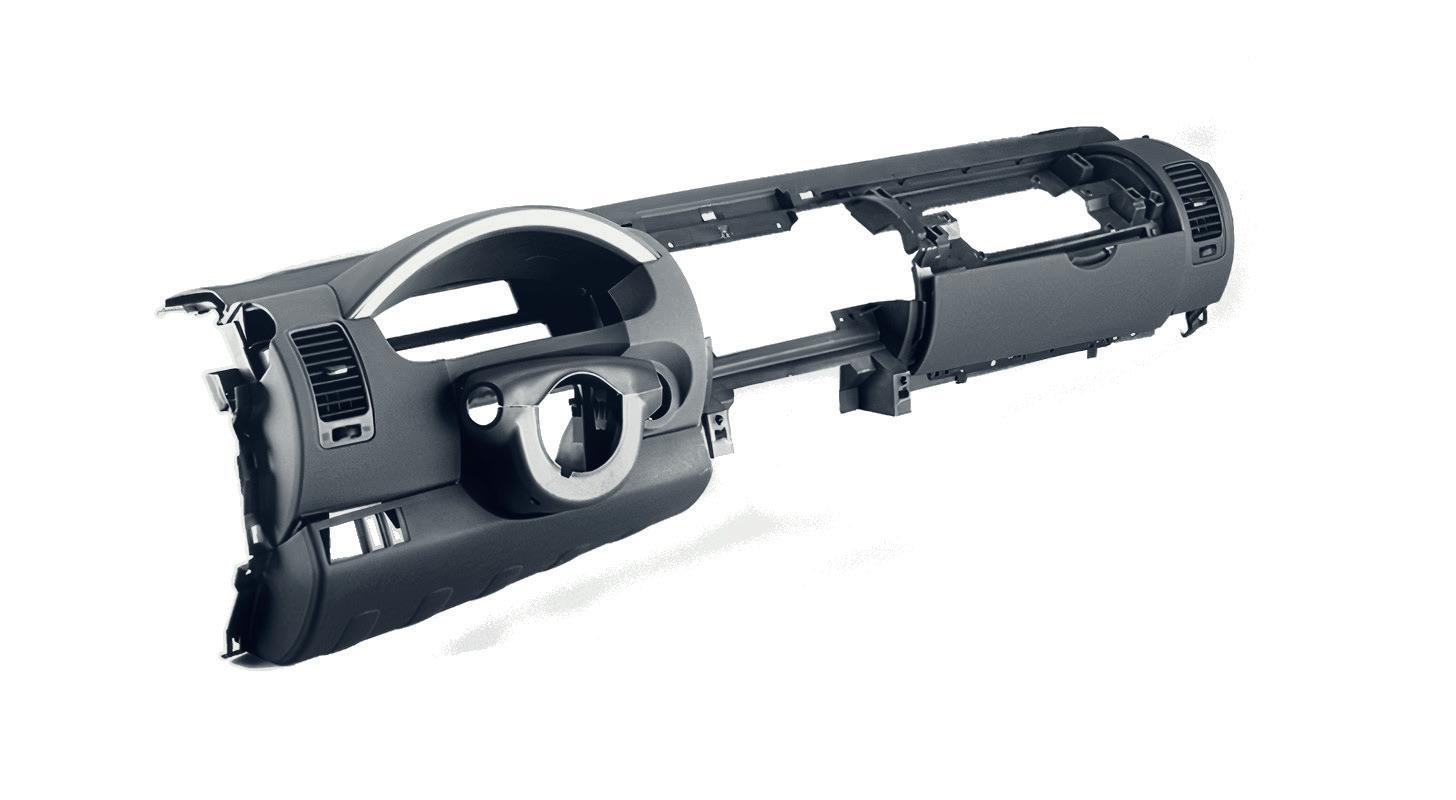
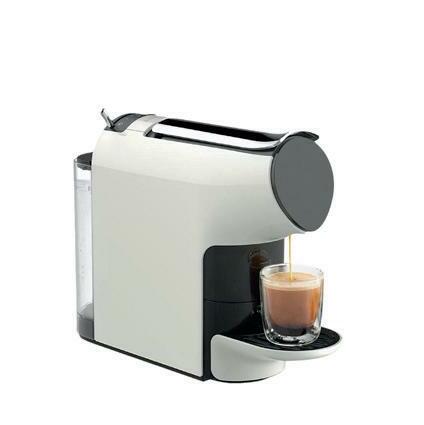
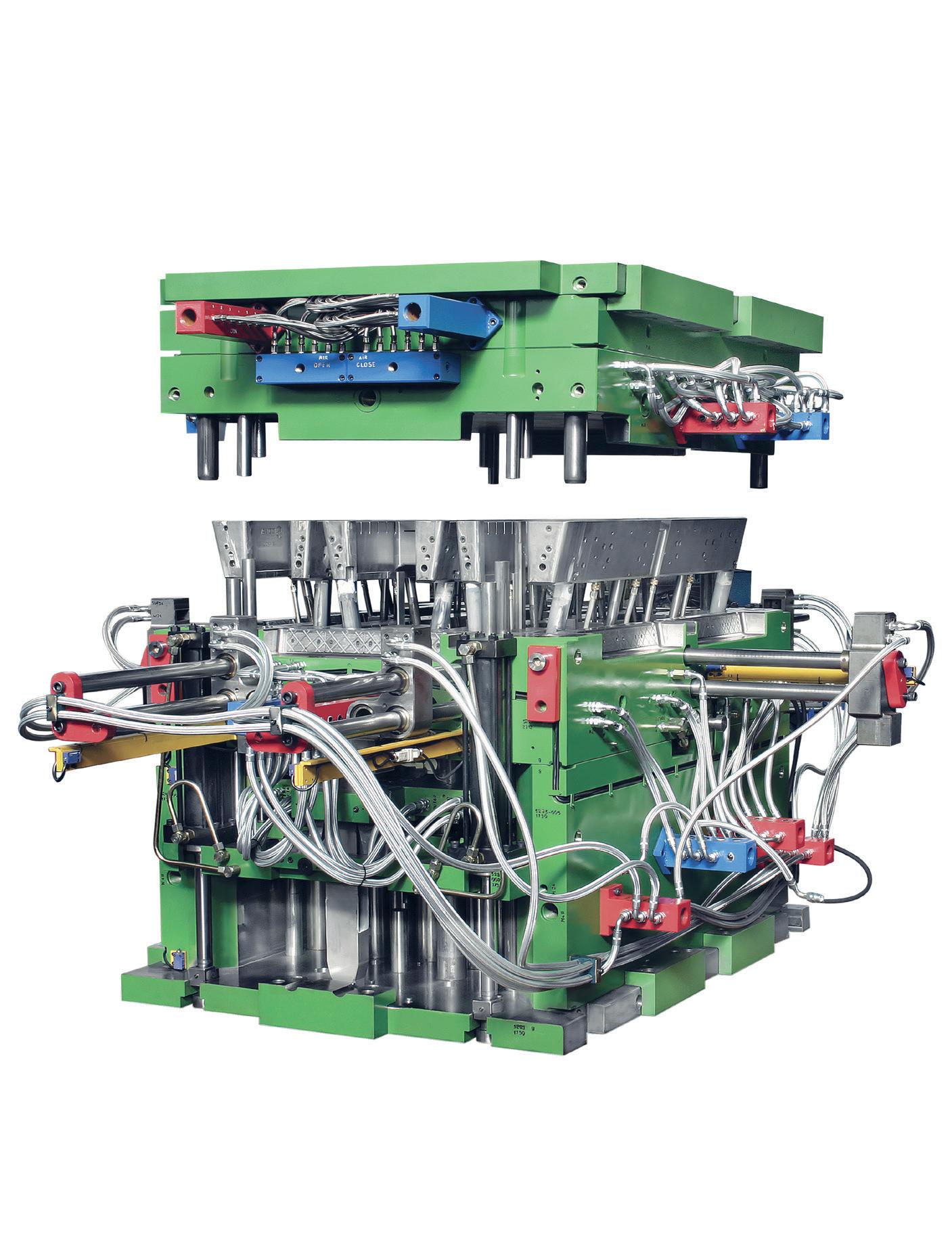
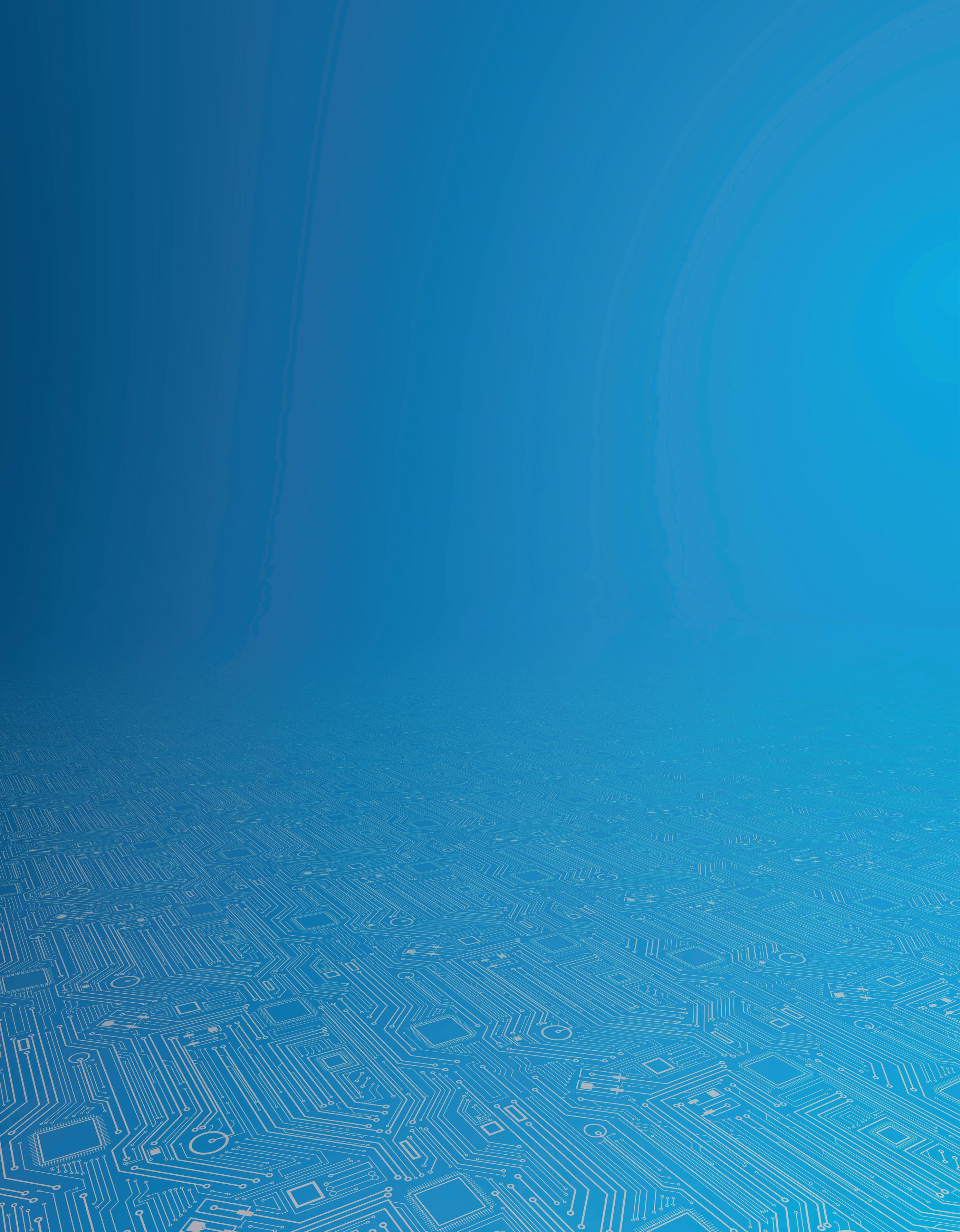
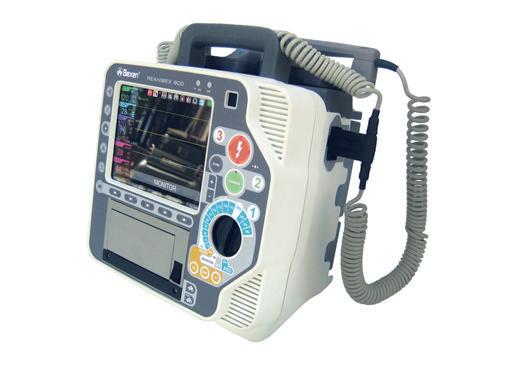
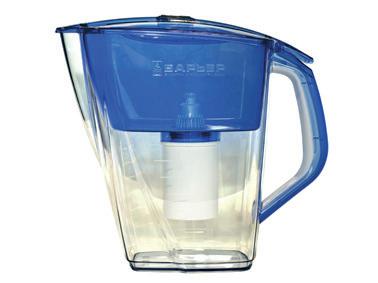
