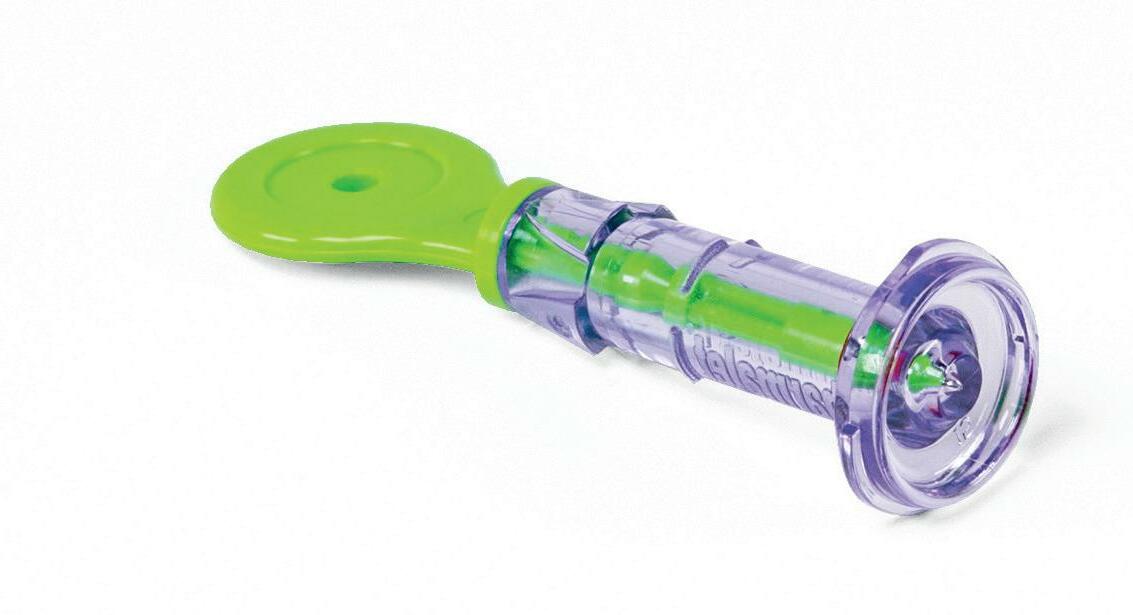
5 minute read
Digital Spy
from MPN NA Issue 21
by MPN Magazine
DRUG DELIVERY UPDATE
www.covestro.com Covestro and PharmaJet take the sting out of vaccinations
Covestro is collaborating with PharmaJet over needlefree injection technology.
The PharmaJet systems require a polycarbonate material to meet the specifications of the syringe and vial adapter while standing up to gamma radiation and ethylene oxide sterilization, with Covestro supporting PharmaJet’s material needs. “We needed a polycarbonate resin that was suitable for our biotech applications and came from a vendor we could rely on,” said Chris Cappello, president and CEO, at PharmaJet. “Covestro has provided great support to PharmaJet in the fight against COVID-19, allowing the collaboration to achieve better immunological results than needle and syringe delivery.”

www.guill.com
Guill Tool, a global manufacturer of extrusion tooling, has shared the latest generation of Series 800. The 2-to-6 layer extrusion tooling is designed to produce the highest quality, highest material-efficient 1/8” to 6” OD tubing for automotive, medical, appliance and industrial applications.
The redesigned Series 800 produces extrusion and layer definition of Fluropolymer and other materials for all multi-layer, multi-lumen medical tubing, as well as fuel line constructions, multilayer PEX pipe and drip irrigation applications, among others. The Guill design further allows thin layer combinations of polymers and adhesives to .02mm or less.
Guill offers its line of crossheads and inline tubing dies in fixed and adjustable center, for single or co-extrusion applications. The tooling is designed to process all compounds and features the company’s patented, precision Feather Touch Concentricity adjustment, the Seal Right System, which combines with the Feather Touch system to eliminate polymer leaking.
INJECTION MOLDING UPDATE
www.ana-u.com
ANA-U relies on injection molding technology from the Wittman Group
For just under three years, ANA-U has been producing molded parts from natural substances under the “Green Quality” brand. These consist of 100% plant-based renewable materials and are compostable just like wood.
The Green Quality molded parts are manufactured on an all-electric from Wittman Battenfeld. The EcoPower 160/750 is equipped with a fully integrated Wittman W918 robot, which removes the parts and deposits them on a conveyor belt. A Wittman Tempro basic C90 temperature controller and a Gravimax 14 gravimetric blender are also integrated in the machine’s UNILOG B8 control system.
Ewald Ulrich, founder and CEO of ANA-U, is very satisfied with the equipment from Wittman Battenfeld. Ewald Ulrich comments: “Molded parts made of renewable raw materials require production machinery with high precision and extended options for parameter setting. This is provided in every respect by the EcoPower 160 from Wittman Battenfeld. In addition to the high quality of the machine, the perfect training programmes and excellent customer support were decisive factors in reaching all our ambitious project goals.”
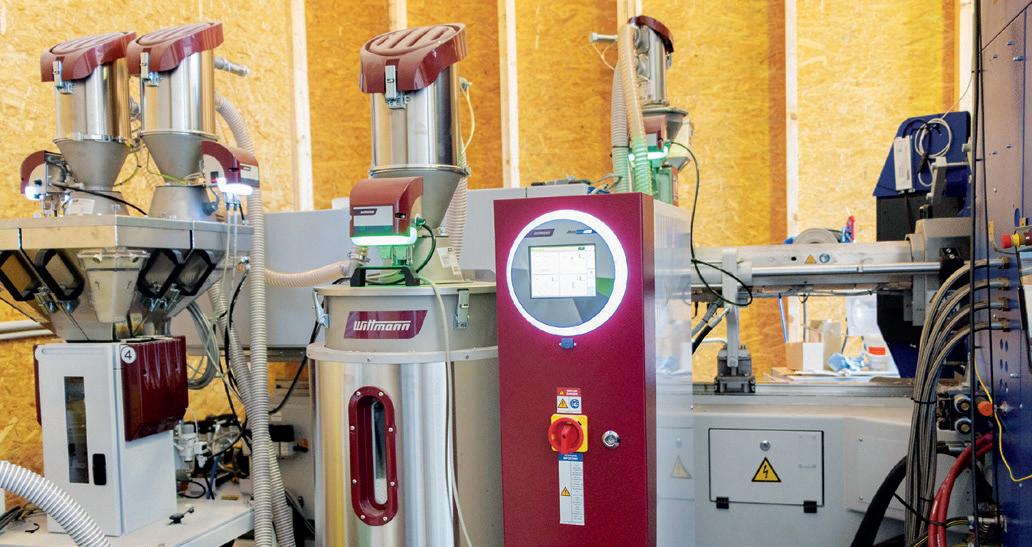
www.parxmaterials.com
CLINICAL STUDY SHOWS EFFECTIVE HPV TREATMENT
Cervical cancer is the fourth most common cancer among women worldwide. More than 95% of cervical cancer is due to the human papillomavirus (HPV), and HPV types 16 and 18 are known to cause at least 70% of cervical cancers.
A current strategy to prevent cervical cancer is by administering a vaccine that works best when administered prior to exposure to HPV, recommended for girls in the age of 9 to 14 years. But a treatment for patients infected with HPV is not available today.
Parx Materials, together with a number of partners in China, has developed a foam and a gel product to treat vaginal HPV-infections. These are easy to administer products that can treat HPV infections in a user friendly and cost-effective manner. The gel or the foam product is administered by the patient themselves and does not require a physician. The products are currently in the process for medical class 2 certification in China, which is expected to be completed in June 2022. LABELING UPDATE
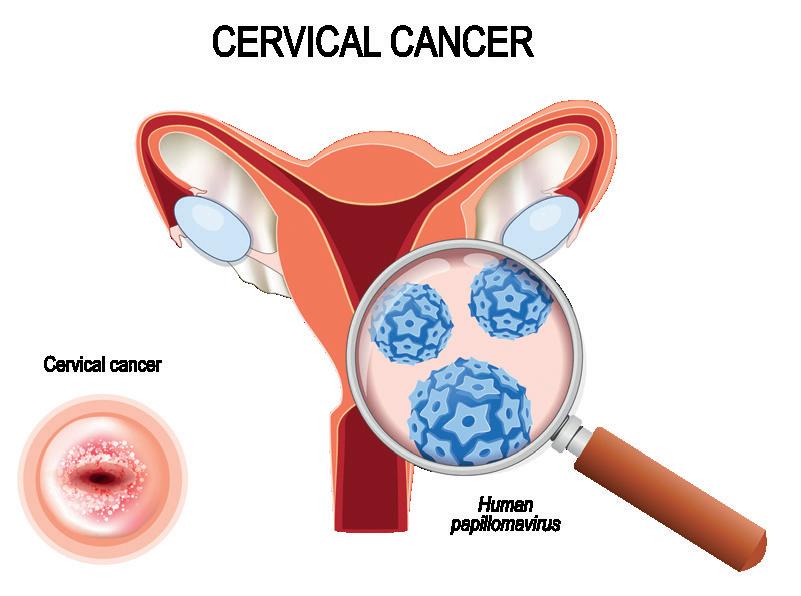

https://p-r-i.org/medaccred/ Launch of new MedAccred programme labeling, printing and UDI focus area
COLLABORATION UPDATE
www.owenmumford.com/en Owen Mumford and Stevanato Group strike Aidaptus auto-injector deal
Owen Mumford has signed an exclusive agreement with Stevanato Group for the Aidaptus auto-injector.
Stevanato Group will mold the components for Aidaptus and provide final and sub-assembly equipment, while also offering market-leading pre-filled syringes to enable pharmaceutical customers to create the final product for patient use. Assembly of the components will be undertaken by both Stevanato Group at its global manufacturing sites and by Owen Mumford at its automated assembly center in the UK. a self-adjusting plunger rod that automatically adapts to the individual plunger positions and different fill volumes in each syringe, with no change parts required.
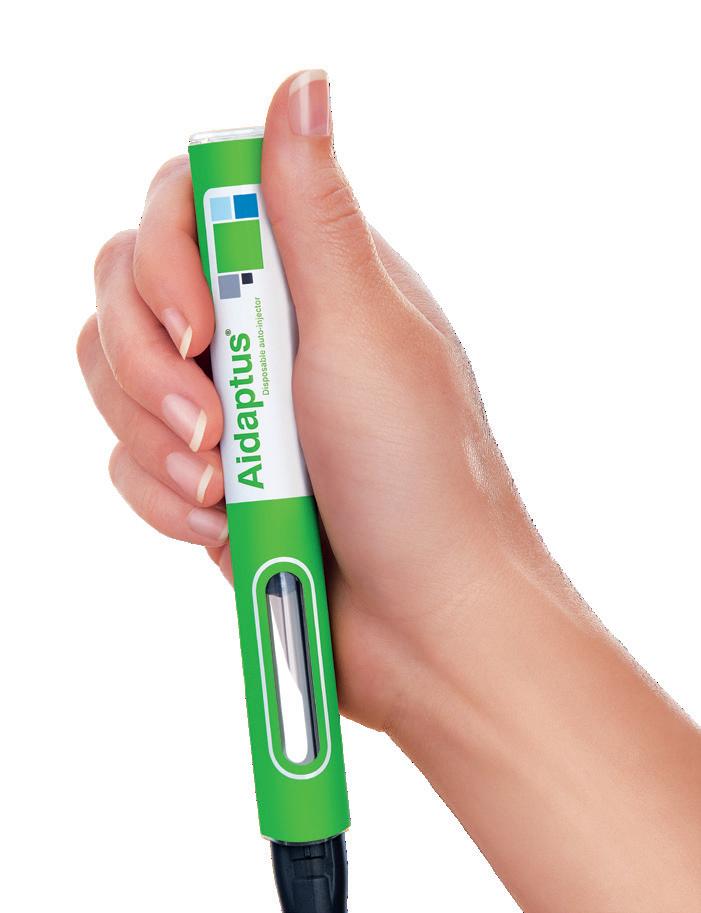
Aidaptus is a 2-step, single use autoinjector with a versatile design that accommodates both 1mL and 2.25 mL prefilled glass syringes in the same base device. It also features plunger sensing technology with Medical device OEMs have launched a new MedAccred critical process focus area for Labeling, Printing, and Unique Device Identifier (UDI).
This will ensure that medical device information provided to medical staff and patients is reliable, accurate, complies with regulatory requirements and, most importantly, improves patient safety. The new assessment will help the medical device industry avoid costly warning letters and recalls by driving the adoption of stringent manufacturing process controls. It comes in response to changing and increasingly complex global requirements which place extra burdens on content management, product labeling, promotional material and UDI.
Paweena Limjaroen, PhD, senior director of global labeling and packaging at Edwards Lifesciences, is chairing the new MedAccred Labeling, Printing and UDI Task Group to develop the industry MedAccred audit criteria, select subject matter expert auditors, and determine which companies meet the rigorous industry requirements to provide oversight for this critical process area. Limjaroen commented:
“In today’s ever-changing medical device-labeling landscape, it is more important now than ever to ensure labeling documentation is regulatory compliant. The MedAccred Labeling, Printing and UDI Task Group’s role is to provide medical device companies with structure and requirements to assist.”
Medtech | Digital HealthTech | Medical Plastics | Manufacturing | Software | Inspection and Metrology Regulation | Design | Early-Stage | Innovation | Pharmaceutical | Manufacturing