HoloCare’s pre-surgical planning hologram technology
HP on the future of medical 3D printing
Bumper 7-page Med-Tech Innovation Expo preview
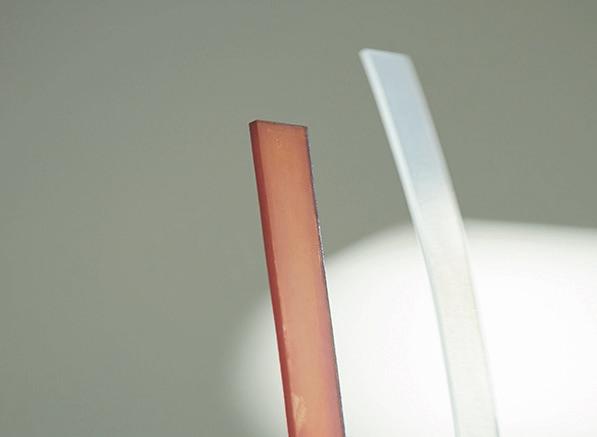

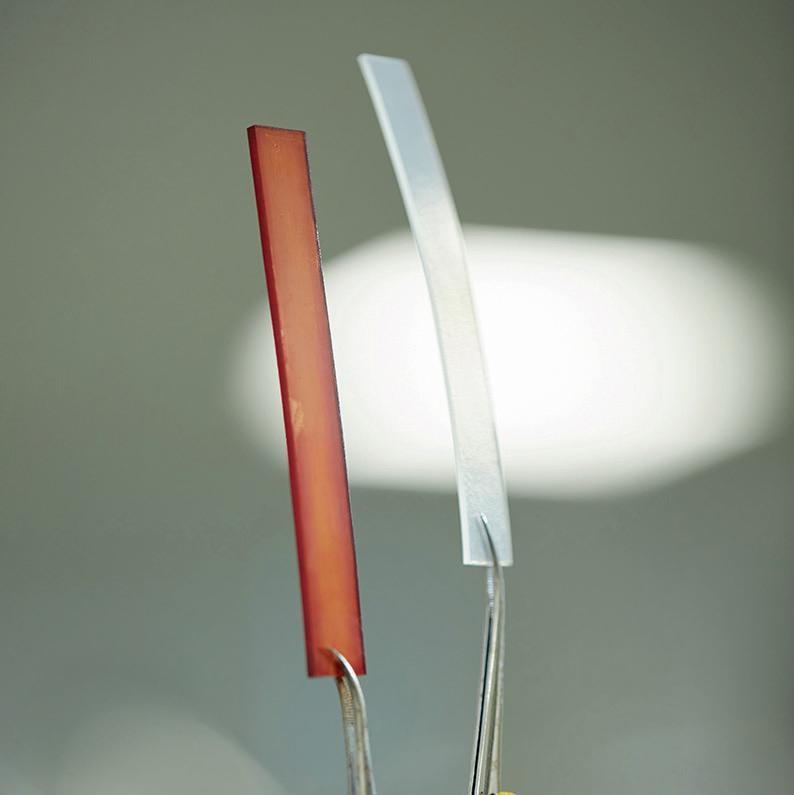
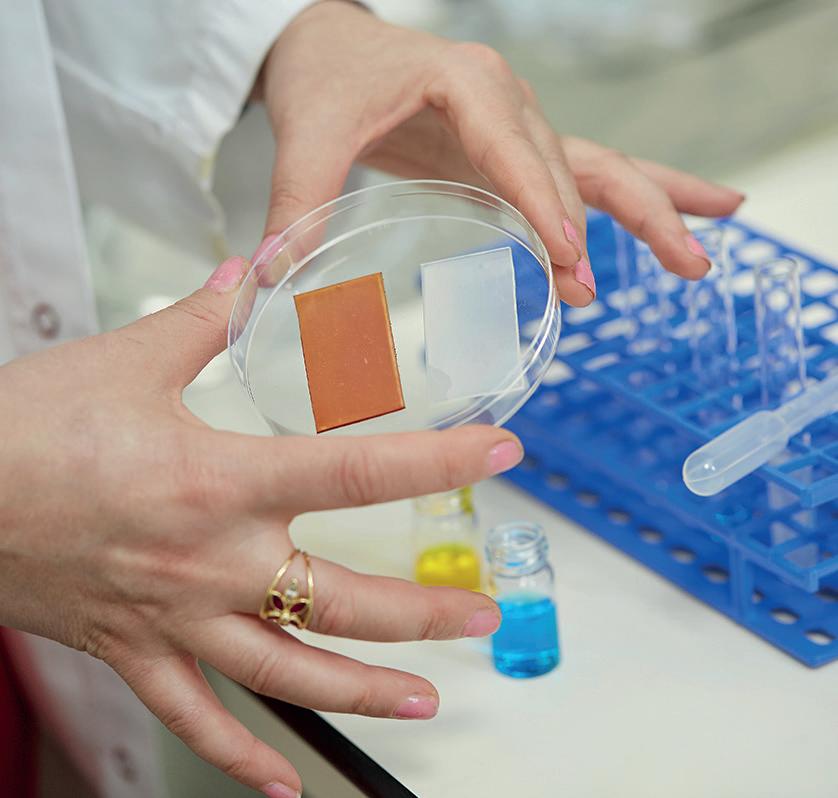

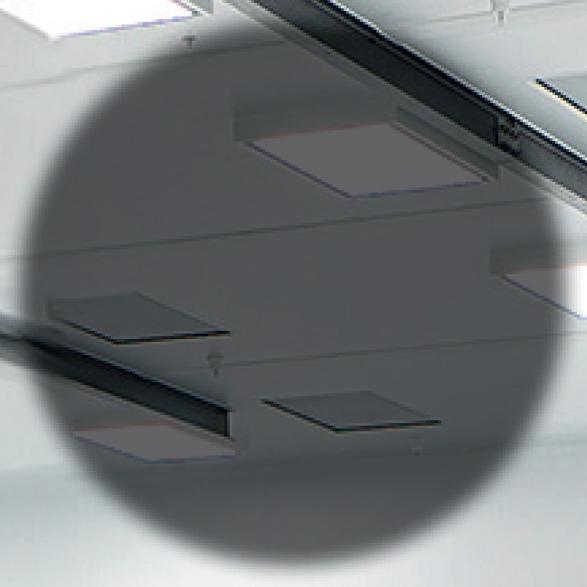


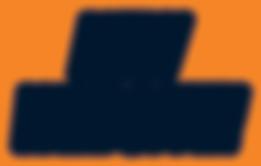

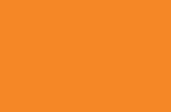

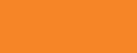

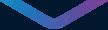
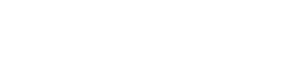
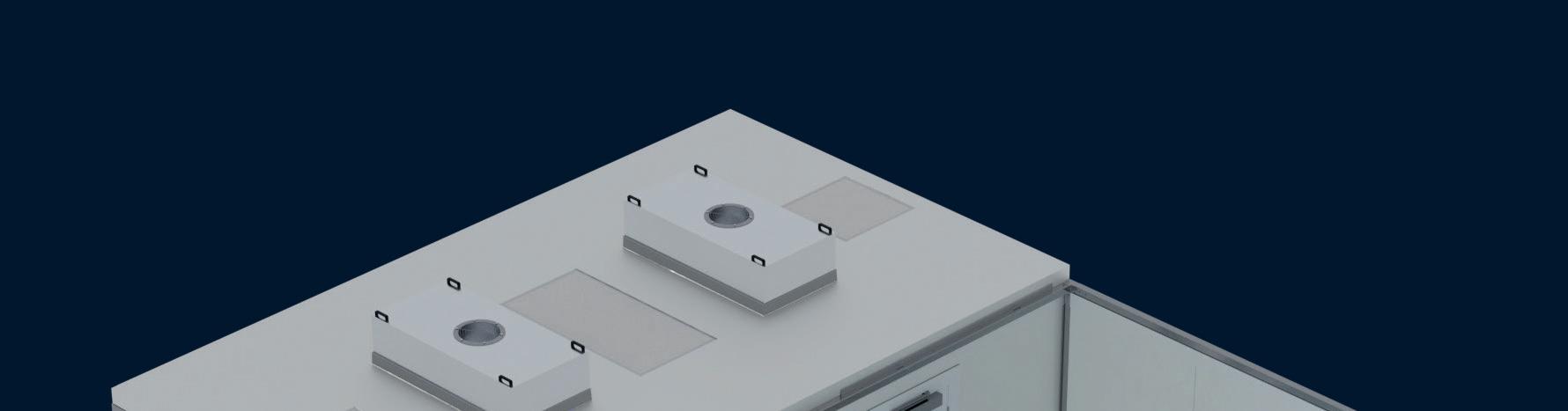
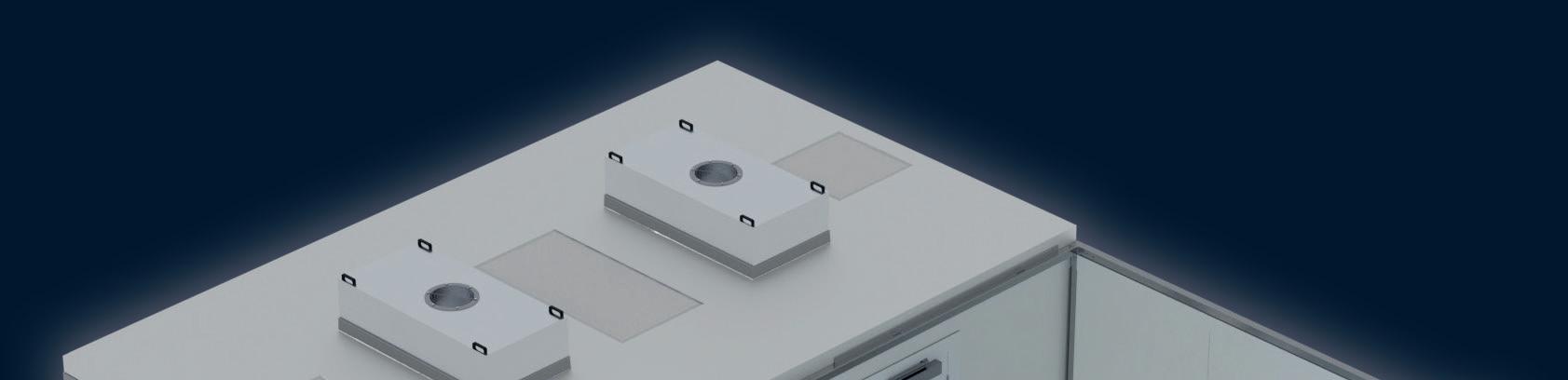


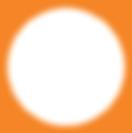


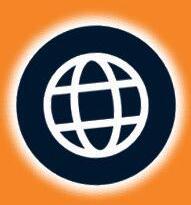
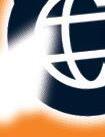
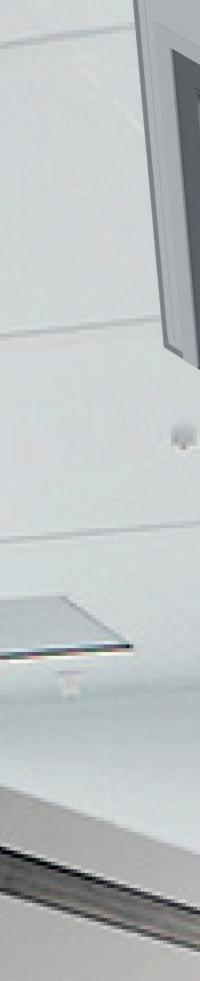
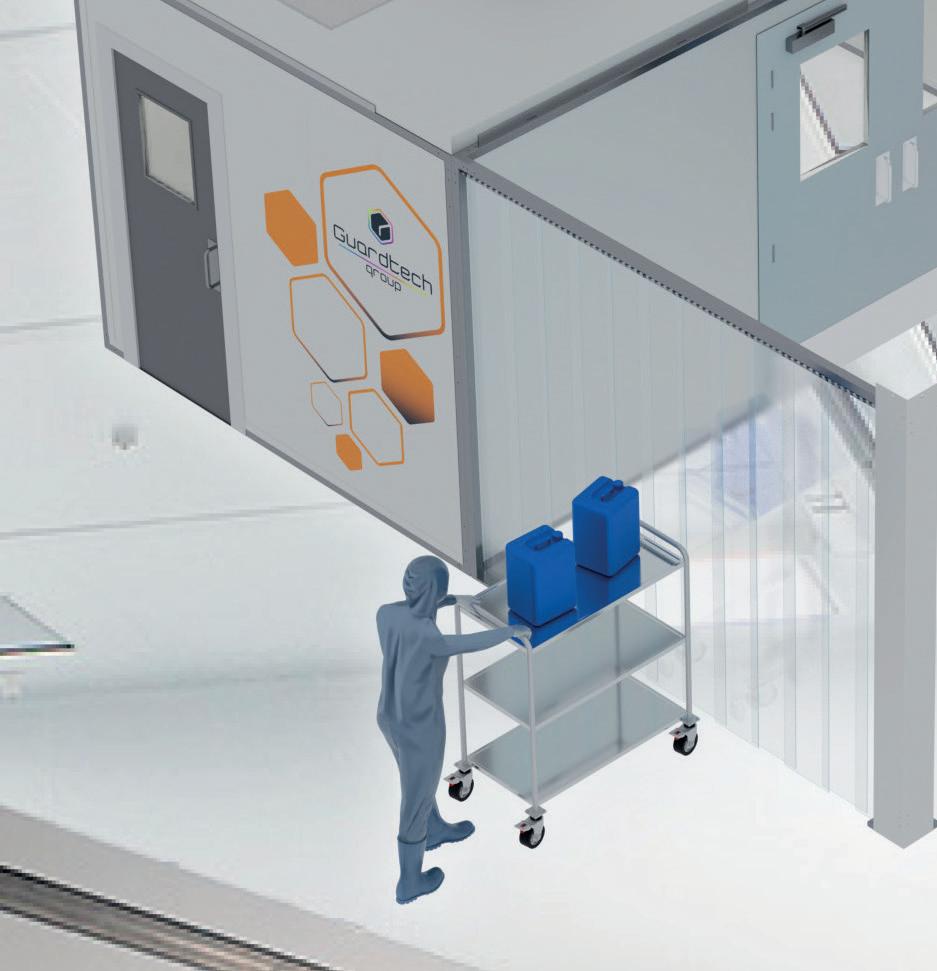

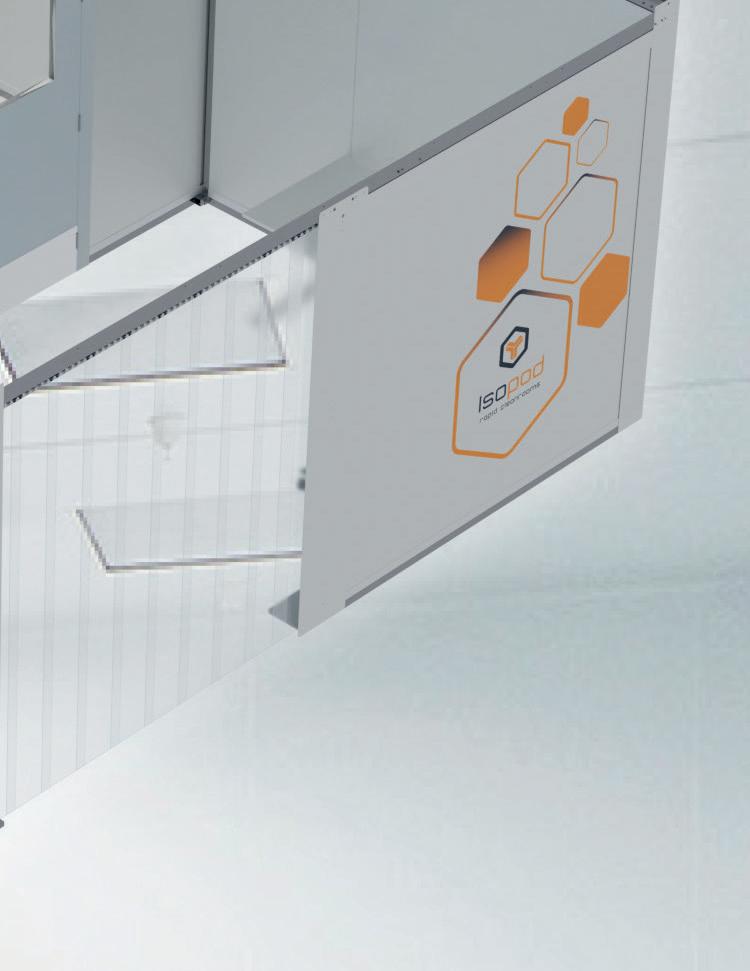
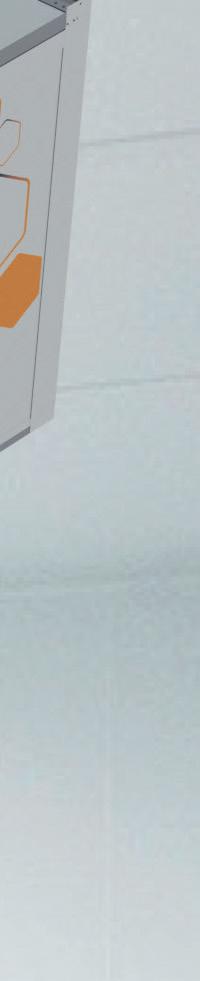
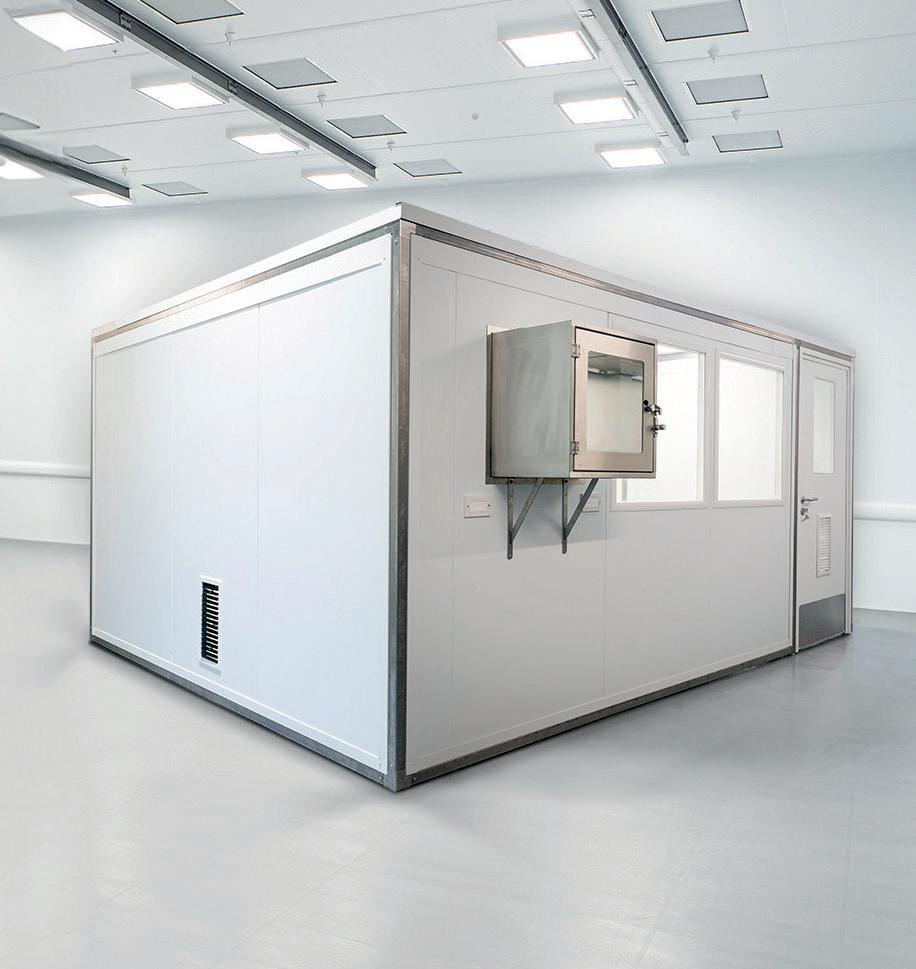
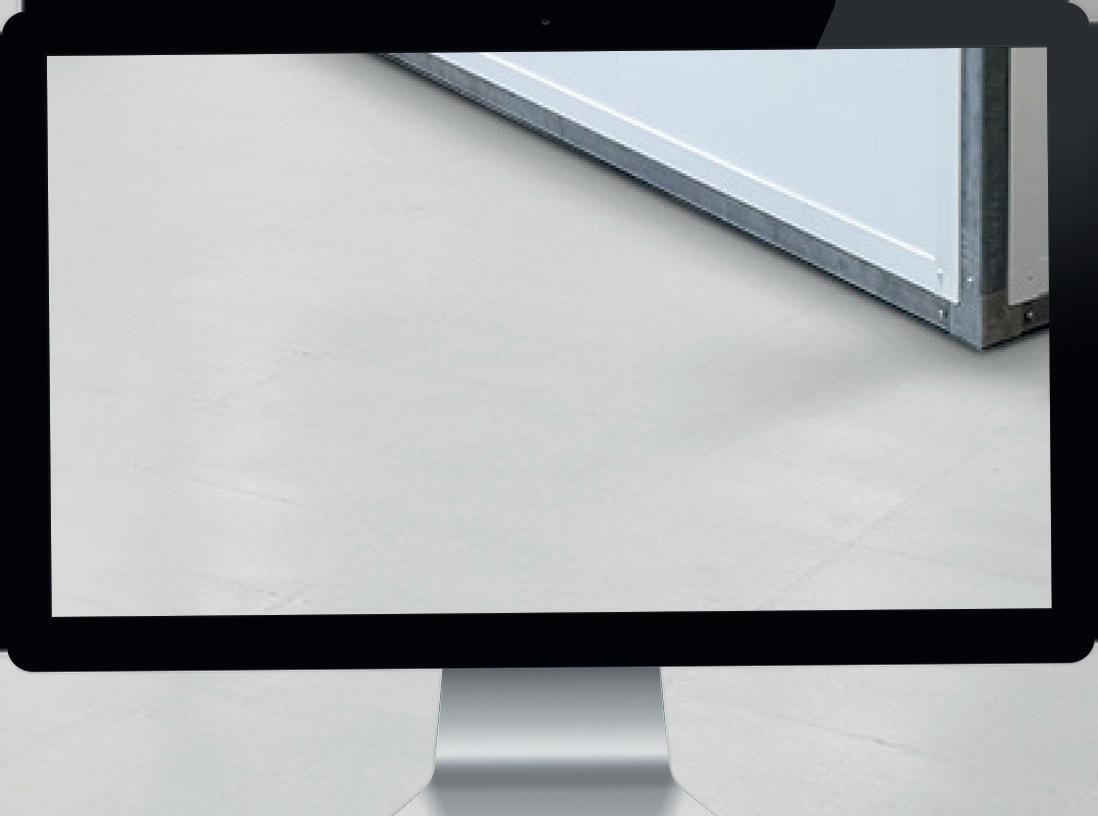
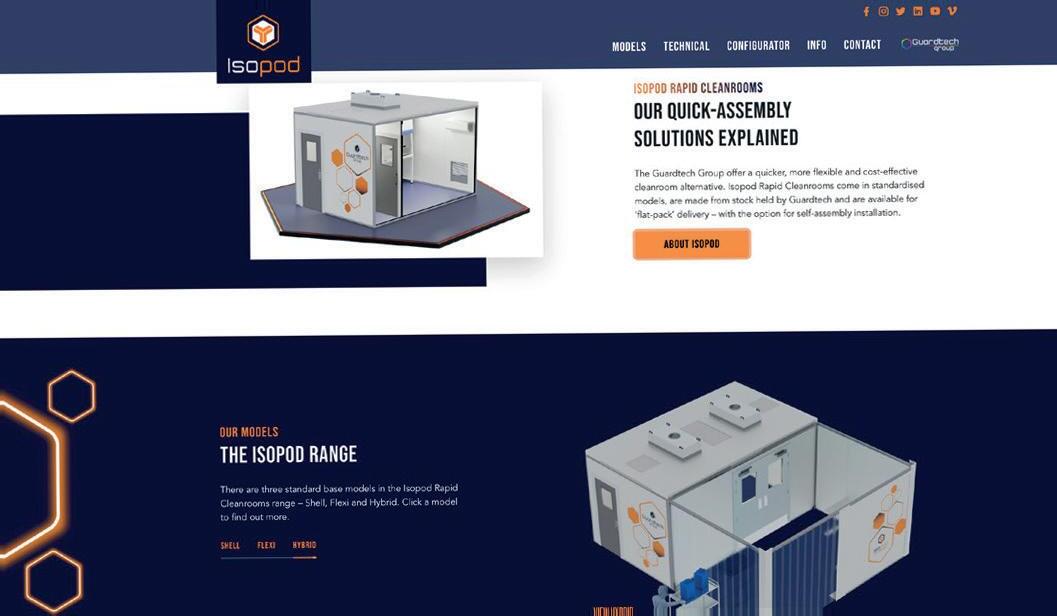
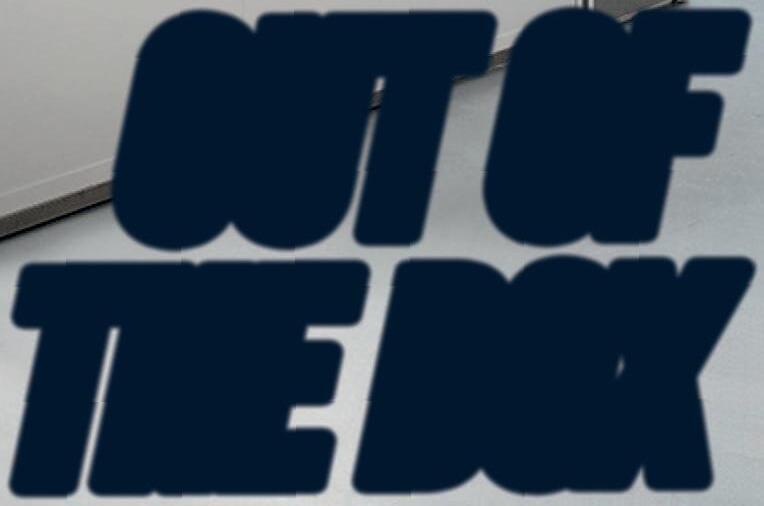
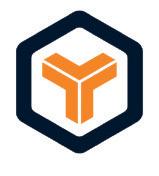
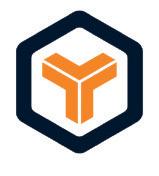
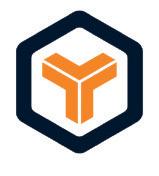

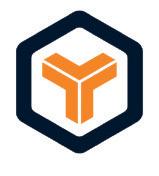
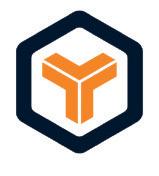
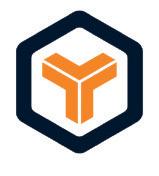
HoloCare’s pre-surgical planning hologram technology
HP on the future of medical 3D printing
Bumper 7-page Med-Tech Innovation Expo preview
19.
Editorial Content Producer Oli
Johnson introduces himself to the MTI audience and speaks of his excitement for the future
6. On the cover BioInteractions details how its surface active therapeutics are used for the prevention and protection of medical devices against infections
9. Expo News
A bumper 7-page preview of Med-Tech Innovation Expo 2024, with information on what you can find on the show floor, and previews of our conference sessions featuring our expert speakers
22. DIGITAL HEALTH
Oli speaks to HoloCare CEO Alison Sundset about the company’s interactive 3D hologram technology
34.
Making MedTech
A round-up of some of the latest industry news from MTI’s website
editor | oliver johnson oliver.johnson@rapidnews.com
head of studio & production | sam hamlyn publisher | duncan wood
3D printing
Oli speaks to BMF CEO John Kawola about the company’s role as an advisor at the University of Nottingham
HP’s Melanie Shelton speaks about why the future of medical 3D printing depends on tight workflow integration
25. Regulation
Itoro Udofia of TÜV SÜD, explores IEC 60601 and the challenge it brings to medical device manufacturers
Tautvydas Karitonas of Test Labs explains the significance of meeting the MDR deadline for UK manufacturers
29.
Microfluidics
Rapid Fluidics CEO Paul Marshall discusses advantages of using AM for microfluidic devices
31. Metrology
22
Patrice Kelty of MMT talks about the company’s Glebar P5K Gauging System
vp sales & sales talent | julie balmforth julie.balmforth@rapidnews.com
group portfolio sales manager | caroline jackson +44 (0)1244 952 358 caroline.jackson@rapidnews.com portfolio sales manager | helen hickey +44 (0)1244 952 374 helen.hickey@rapidnews.com
5-6 JUNE 2024
Med-Tech Innovation Expo 2024 is finally here, for those of you reading this before the 5-6th of June, there is still time to register for free, and for those of you who have picked up a copy on the show floor, welcome, we’re delighted to have you.
Before we get into what is in store for this issue, allow me to introduce myself. My name is Oliver Johnson, and I have spent the past two years as Junior Editorial Content Producer on MTI’s sister publication TCT Magazine, covering every aspect of the 3D printing/additive manufacturing industry. Additive is still relatively new compared to other manufacturing technologies, but there are some incredible developments happening in this field, especially in terms of healthcare.
One of my favourite medical applications I covered during my time on TCT was a ceramic bone replacement material from Lithoz that is biocompatible, and can grow with the natural human bone if implanted in a child who may have a skull defect.
Since the departure of my predecessor Ian Bolland, I have now taken on the role of Editorial Content Producer on Med-Tech Innovation News. I am incredibly excited to share this issue of the magazine with you, we have insights from HP, MMT, Test Labs, TUV SUD, Rapid Fluidics, Europlaz and more, as well as original interviews with CEOs from Boston Micro Fabrication and HoloCare.
You will also find a bumper show preview section, seven, yes, SEVEN, whole pages of content. Here you will find out what is new to the expo for 2024, as well as learning what is in store on the conference side of things with previews for a selection of the sessions on both days.
Our cover story for this issue is from BioInteractions, a company focusing on surface active therapeutics for the prevention and protection of medical devices against infections. You can visit BioInteractions at Med-Tech Innovation Expo on stand A20.
See you soon!
I can’t wait to meet all of you at the show, please do come and say hello, as well as moderating on the Med-Tech Innovation Conference stage, I will be making my way around the show floor, producing short-form video content for our social media channels.
After working on this title for what will be nearly three months by the time the show opens its doors, I can honestly say I have had an incredible time already, with a trip to Ireland to visit numerous life sciences companies and an issue of the magazine under my belt already, I can’t wait for what the future holds.
Keep an eye out on the website and in the magazine for new types of content and design changes over the next few months or so, and don’t forget to follow us on LinkedIn and TikTok so you don’t miss our video content direct from the show floor at Med-Tech Innovation Expo.
Using Surface Active Therapeutics for the prevention and protection of medical devices against infections is becoming more and more important, as the number of healthcareassociated infections (HCAIs) rises. While researchers have been able to pinpoint some causes of HCAIs, there is still a need to protect complex surfaces, like implants, from device-related infections, and surgical equipment to be protected from germs and microbes. Safeguarding all surfaces in healthcare is critical to evolving the infection prevention infrastructure for patients, professionals, providers and visitors. The demand for implantable devices to be included within the evolving infection prevention infrastructure keeps increasing, as using medical implants protected with a highly effective localised antimicrobial coating improves the safety to patients by reducing device related and surgical site infections, enhances the longevity of the implanted device which leads to superior therapeutic results for patients and increasing health-outcomes.
New developments in an advanced category of coatings—Surface Active Therapeutics (the application of highly effective and localised residual therapeutics on to a wide range of substrates and geometries such as catheters, drainage systems, ventricular devices, heart valves and neurological stents) — are the state-of-the-art solutions for all medical devices today. Enhanced antimicrobial coatings, such as TridAnt®, create a continuously protective shield over the surface, comprised of a polymeric matrix which combines active and passive components to provide complete protection against pathogens. The polymeric matrix ensures the fastest contact-kill mechanism, the broadest spectrum efficacy and continuous residual protection. In addition, it has the ability to disrupt and prevent biofilms, therefore offering a new way to combat a wider range of infections more effectively, efficiently and for the entire lifetime of a patient.
Arjun Luthra, BioInteractions’
Commercial Director, discusses how the company’s surface active therapeutics are being used for the prevention and protection of medical devices against infections.
Overall, these coatings are proven to provide monoclonal protection, which kills the broadest spectrum of pathogens, including gram-positive and gramnegative bacteria, as well as enveloped and non-enveloped viruses, fungi and spores such as E.coli, MRSA, Influenza, Norovirus, Clostridium difficile and SARS-Cov-2, for the lifetime of a patient. TridAnt® continues to provide superior benefits for devices and has been shown to disrupt as well as prevent biofilm for the lifetime of the device. The technology provides protection against pathogens on a wide range of geometries and substrates ranging from soft materials such as silicone as well as woven and non-woven fabrics all the way to hard
materials such as metals (stainless steel and nitinol) and polymers (polyamides, polycarbonates, and polyurethanes).
TridAnt® is a unique Surface Active Therapeutic which provides a localised effect and therefore is completely safe to use in all environments within the body. It has been tailored specifically for life-time class 3 implants, which are implanted inside chronic areas of the human body. Its unique polymeric matrix is biocompatible and only targets microbes (prokaryotic cells). In addition, it is only effective at the surface which provides enhanced safety from the multi-action coating, unlike other eluting coatings. As a result, TridAnt®-coated medical devices are protected consistently with a highly effective, fast, durable, safe, localised shield that disrupts and prevents biofilm for the entire lifetime of the device.
What do future medical device innovations and trends look like?
There have been impressive products released over the last few years in the areas of surgically implanted devices, but many of them have to be removed and re-inserted or they are accompanied with extensive drug regimens for the entire lifetime of a patient. This has prompted developers to introduce biocompatible coatings that can meet not only the clinical but also the engineering requirements for these devices. Devices such as total artificial hearts (TAHs), ventricular assist devices (VADs), vascular stents, and prosthetic mechanical heart valves are examples of technologies used to assist vital organs in functioning normally. However, they share a common constraint: lifetime hemocompatibility, specifically thrombosis.
Surface Active Therapeutic technologies are a stateof-the-art way of providing superior biocompatibility, lifetime antithrombogenicity and significantly reducing the risk of stenosis. BioInteractions have developed Astute®, an advanced antithrombogenic coating which has been used successfully on chronic, blood-contacting medical implants for over 25 years. Astute® is a Surface Active Therapeutic that combines an active component with additional passive components to mimic the natural endothelial layer.
The active component gives the coating the ability to interrupt the blood cascade mechanism, preventing platelets from activating and hinders thrombus formation. The additional passive components prevent blood components from depositing on to the device surface. This multi-faceted approach provides superior hemocompatibility to the surface without any reduction in performance for the lifetime of the patient.
In addition, the burgeoning development of miniaturised and minimally invasive procedures includes a variety of challenges like decreasing the amount of tissue trauma by way of reducing friction during the insertion and removal of the devices. This can lead to improved surgical outcomes, less pain and more comfort during recovery.
At BioInteractions, we have sought to meet this challenge by developing a Hydrophilic Coating called Assist™, which is lubricious, flexible and significantly reduces friction. It has been applied to a wide range of medical devices, such as joints without particulate formation and delamination in high-stress and high-movement applications. Assist™ also fills in the microstructures of the surfaces which improves the laminar flow of liquids. This significantly reduces the deposition and adhesion of bodily components on the surface, enabling the devices to remain functional and safe whilst being implanted within the patient. Assist™ is instantly activated through wetting, eliminating the need for pre-soaking the surface. This not only saves preparation time for the devices but also allows for a straight-forward deployment of the device.
What are the major issues customers are dealing with today?
Universally, medical product developers and manufacturers navigate a highly regulated and particularly constrained environment. Under today’s European Union (EU) regulations, medical devices are considered medicines and are therefore tested by the European Medicines Agency (EMA) following the same tests and approval processes that drugs do. Our Product Pathway Partnership team closely work with customers to navigate all areas including optimisation of the application
process, fixture design and tooling, biocompatibility testing, regulatory compliance and providing coating services as an organisation’s commercial manufacturing partner. We provide guidance along a strategic pathway with a focus on offering a flexible approach to meeting all of the ever-revolving regulatory demands on a wide variety of devices coated with our technology. The aim of our Product Pathway Partnership is to enable customers to get to market in the most efficient and effective way possible.
Alongside the expanded Product Pathway Partnership, our integrated service streamlines the research and development of new innovative coating materials using its 30 years of expertise and a range of novel analytical resources to create the optimal coating for your device. BioInteractions’ experience and broad technology portfolio allows us to create bespoke coatings for a wide range of applications building on the innovative solutions provided today. This unique aspect of the service draws on our expertise and knowledge in applying innovative solutions to a wide variety of devices and enables us to provide revolutionary and state-of-the-art solutions for our partners.
Where can you meet the BioInteractions team?
The BioInteractions team will be at MedTech Innovation Expo between 5th - 6th June 2024, on Booth A20 in Hall 2. To organise a meeting or a call, please email Isabel Pedreira at isabel@ kredoconsulting.com.
REOMED medical transformers provide the highest levels of safety, efficiency, and precision – count on us for the best solution for your medical application. Contact us now.
REOMED – Your partner in advanced medical technology.
Find out what’s in store for this year’s Med-Tech Innovation Expo on the show floor and on the conference stages.
Visitors at this years Med-Tech Innovation Expo, taking place on 5-6th June at the NEC in Birmingham, can expect to hear expert insights from an impressive list of names curated by the MTI team at the Med-Tech Innovation Conference, and can meet and interact with our exhibitors on what by the time the show opens could be the biggest show floor in the history of the event.
The expo floor features renowned names in the industry such as Medilink, NIHR, Shawpak, Boddingtons Plastics, BioInteractions, Renfrew, Ultrapolymers, Neilpak, and many more.
At the heart of the expo is the startup zone. This will be home to the nine start-ups that are participating in PITCH@Med-Tech Innovation Expo on the second day of the show, where they have 5 minute slots to discuss their company in front of judges from expert organisations such as Innovate UK, NIHR and more.
is the Med-Tech Connect Lounge, a location perfect for networking with old and new clients. Use the Event Hub app to set up meetings with exhibitors and speakers, so you can start filling up your diary, expanding your network and maximising your time at the show.
New for the show this year, is the show floor social at the end of the first day, sponsored by Kirkstall Precision Engineering, BioInteractions, Neucin and PBC. This will be a great networking opportunity and a chance to meet others in the industry in a more relaxed and informal setting.
Across the show floor there will also be live product demonstrations, allowing visitors to get hands on with the technology and see how it can impact your business. Also featuring this year
The conference programme, which is packed full of expert knowledge, kicks off on day one with a keynote presentation featuring experts from Leeds Teaching Hospitals NHS Trust and Johnson & Johnson MedTech. On day two, returning to deliver a keynote presentation for the second year in a row, David Lawson, Director of Medical Technology at the Department of Health and Social Care will give an update on new initiatives that have been launched in the UK, one year from the launch of the UK Government’s inaugural MedTech Strategy.
Thursday, 6th June 2024 10:00-11:00 Med-Tech Innovation Conference Stage Med-Tech Innovation Conference Stage
“In Conversation: Leeds Teaching Hospitals NHS Trust and Johnson & Johnson MedTech”
Wednesday, 5th June 2024 10:00-11:00
Creating a thriving health innovation ecosystem to improve health outcomes and reduce inequity through industry partnership: in conversation with Leeds Teaching Hospitals
NHS Trust and Johnson & Johnson MedTech
The Med-Tech Innovation Conference kicks off with an exciting keynote session featuring influential leaders from Leeds Teaching Hospitals NHS Trust and Johnson & Johnson MedTech. Scheduled for Wednesday, 05 June 2024, from 10:00 to 11:00, this session will delve into the creation of a thriving health innovation ecosystem aimed at improving health outcomes
and reducing inequity through strategic industry partnerships.
Attendees will gain valuable insights from Hugo Breda, Managing Director of Johnson & Johnson MedTech UK &
Ireland, and Bala Balaguru, Director of External Affairs. They will be joined by Professor Phil Wood, Chief Executive of Leeds Teaching Hospitals NHS Trust, and Professor Tze Min Wah, a leading figure in Interventional Radiology. This esteemed panel will explore how their collaboration is driving innovation, enhancing healthcare delivery, and tackling disparities within the health sector.
This keynote is essential for all stakeholders in the medical technology field who are committed to advancing patient care. Don’t miss this opportunity to learn from and engage with top experts who are at the forefront of medical innovation. Join us to be part of the conversation shaping the future of healthcare.
“The Government MedTech Strategy – One Year On”
Following the publication of the Government’s inaugural MedTech Strategy last year a range of new initiatives have been launched to deliver on a vision of right price, right product, right place. In April the Department of Health and Social Care published a One Year On review which referenced key initiatives including the Innovative Devices Access Pathway (IDAP), designed to streamline access for novel game changing technology, the Health Technology Accelerated Adoption Fund (HTAAF), providing ICSs with rapid adoption funding, and we set out our areas of priority going forward, including a commitment to introduce a standard methodology to apply value based procurement for MedTech.
David is looking forward to presenting at this year’s Expo to reflect on progress made and set out areas of key priority and focus over the
coming months. There is a shared challenge to ensure that patients are able to access the most effective medical technology, and to use medical technology as a catalyst to improve patient outcomes and improve productivity of the health system to meet an ever-increasing demand. This is not an innovation challenge. We have a large array of available innovations that are already in use within our health system and a pipeline of new and existing innovations coming through. We are one of the strongest centres for innovation globally in terms of research and development and clinical excellence. The challenge is adoption, first, how do we select those technologies that should be adopted at scale, and second once identified how to we ensure adoption is followed through across the health system. In David’s keynote he will set out the work that the Department of Health and Social Care is doing to meet this challenge and what more needs to be
Thursday, 6th June 2024
13:40-14:40
PITCH@Med-Tech Innovation Expo is a great way to round off the Expo with the session just after lunch on day 2. Those who are eligible to pitch are all those who’ve taken a ‘Pod’ on the Startup Zone, which is sponsored by the NIHR and Innovate UK for the 4th year in a row. Six of the startups have had funding from the NIHR i4i Programme, although, like many startups in MedTech, they are likely to have had non-dilutive funding from most available sources including Innovate UK and possible SBRI Healthcare as well.
The 6 i4i funded companies reflect the diversity of the programme’s portfolio covering medical devices and digital health products ranging from rehabilitation to femtech.
All the startups will have 5 minutes to pitch, which includes time for any Q&A by the judges.
The judging panel reflects the Startup Zone sponsors and the organisers of the event. Ably chaired by Dr Jo Smart,
Introducing Health-Tech Stage News LinkedIn and TikTok accounts
During the expo, Med-Tech Innovation News will be creating short-form social media videos, directly from the show floor. If you are familiar with our sister publication TCT Magazine, you may have spotted this type of content being produced at shows such as Formnext 2023 and TCT Asia 2024.
Exhibitors at the show will be showcasing what is on display at their stand, talking through their technology and how it works, and providing expert insights into their particular field of MedTech. The videos will be recorded, edited, and posted onto the Med-Tech Innovation News LinkedIn and TikTok accounts
we have Professor Tom Clutton-Brock (NIHR), Mr Andrew Shortt (Innovate UK, Business Growth) and Olivia Friett (Medical Plastics News).
While the judges are deliberating, the funders will also have 5 mins each to pitch – same rules!
The winner of PITCH@Med-Tech Innovation Expo will get a full interview with MedTech News to be published in an edition soon after the event.
on the same day, so make sure you are following us on both of those social media platforms.
Follow us to see daily face-toface interviews conducted by the experienced Med-Tech Innovation News editorial team, daily updates direct from the show floor, and firsthand expert insights. You won’t get this type of content anywhere else.
The videos produced on the TCT social media channels at Formnext 2023, the first foray into this new type of content at Rapid News Group, were a major success, achieving close to 100,000 views in just over a week.
Med-Tech Innovation Conference Stage
Wednesday, 5th June 2024 15:00-15:30
Dive into the intricate world of MedTech supply chain management with Med-Di-Dia. This presentation will unveil strategies essential for navigating compliance and ensuring quality in the ever-evolving landscape of medical device manufacturing. The talk will focus on critical ISO13485:2016 and FDA CFR 21 Part 820 requirements relating to supply chain, purchasing, traceability and
continuous improvement practices. From supplier qualification to risk mitigation, Jacob will explore the critical steps MedTech manufacturers must take to uphold regulatory standards and maintain product excellence and safety. Discover how stringent quality assurance protocols and collaboration with suppliers are the cornerstones of a robust supply chain. Gain insights into
managing supplier changes without compromising compliance or quality.
Join this talk as Jacob discusses regulatory requirements and best practices, empowering you to optimise your supply chain for success in the dynamic Medical Device industry. Don’t miss this opportunity to elevate your understanding and stay ahead of the curve in supply chain management.
Introducing Health-Tech Stage
“Global Medical Device Material Compatibility Challenge”
Wednesday 5th June 2024 15:00-15:20
Medical devices contribute toward the treatment and recovery of millions globally. However, these devices often face premature failure due to incompatibility with infection prevention and control practices. This seminar will explore the critical need for comprehensive material compatibility studies, highlighted by regulators such as the FDA and notified bodies in the EU.
The COVID-19 pandemic exposed significant vulnerabilities in medical devices, emphasising the urgent need for compatibility with stringent cleaning, disinfection, and sterilisation protocols. Additionally, the global push for sustainability demands the development of more robust, reusable medical devices. Healthcare systems, influenced by both external pressures and budgetary constraints, are
imposing stricter tender requirements to ensure product reliability and safety.
Key topics include the impact of cleaning agents on materials, the risk of contamination, and the regulatory emphasis on safety and performance throughout a device’s lifecycle. Case studies of FDA recalls will illustrate common compatibility issues, such as polymer degradation. The seminar will also address how certified laboratory testing can support manufacturers in meeting regulatory demands, enhancing product reliability, and ensuring patient safety. Participants will gain insights into the collaborative efforts required between device and disinfectant manufacturers to meet evolving standards and maintain market competitiveness.
Introducing Health-Tech Stage
“Transforming Chronic Pain Care: Simulation, AI and Machine Learning”
Wednesday 5th June 2024
14:00-14:20
At the MedTech Innovation Expo, Xi Engineering Consultants will present on how advanced techniques like simulation, AI, and machine learning are revolutionising chronic pain care. This talk will showcase how these technologies enhance the precision and effectiveness of spinal cord stimulation, providing new hope for patients.
Spinal cord stimulation has been employed for nearly five decades to alleviate chronic pain conditions, particularly neuropathic pain stemming from nervous system lesions (such as Sciatica or Complex Regional Pain Syndrome). These conditions often result from various sources like physical trauma, infections, or degeneration. To develop effective treatments for such pain management issues, researchers focus on understanding how electrical currents, generated by electrodes implanted in the spinal column, can be modulated.
Simulation and data analysis play vital roles in this research. Neuromodulation Specialists collaborated with Xi Engineering Consultants to utilise finite element modelling techniques (using COMSOL Multiphysics software) to investigate the distribution of electrical
fields within the spinal cord under different electrode configurations. This involved combining computational simulations with clinical insights to identify promising protocols for dynamically steering electric fields within the spinal cord structure.
Through simulation and data analysis, Xi Engineering Consultants explored various electrode drive configurations which may show promise in improving treatment effectiveness. High-frequency interferential (IF) neurostimulation represents a cutting-edge approach to pain management, offering significant potential for altering local metabolic processes with widespread effects. By applying current from multiple circuits operating
at slightly different frequencies, IF stimulation generates interference patterns that result in a low-frequency beat. This beat may penetrate neural tissues more effectively than conventional stimulation methods, as evidenced by recent studies demonstrating its short-term safety and efficacy in treating chronic pain. Two specific protocols examined were single-axis and parallel-axis interferential stimulation (SAIF/PAIF), which enable the steering of electric fields vertically or laterally to target specific areas of concern.
“Innovation in Healthcare – User Centred R&D”
Thursday, 6th June 2024 13:00-13:30
At Charco Neurotech, the CUE devices have been developed as non-invasive, wearable medical devices for people with Parkinson’s. Using focused vibrotactile stimulation and cueing, the CUE devices help alleviate symptoms such as stiffness, slowness, rigidity, and freeze of gait. To date, over 3,200 people use a CUE device daily.
The inspiration behind the CUE devices came from working closely with people with Parkinson’s, exploring how various stimulations might help day-to-day, and delving deeper into the characteristics of these stimulations. Patient-centric research and development was a key process.
In summary, by using simulation and data analysis techniques, researchers are advancing our understanding of spinal cord stimulation and developing more effective treatment protocols for chronic pain management. These core services of simulation and data analysis enable the optimisation of electrode configurations and stimulation protocols, ultimately improving patient outcomes and quality of life. Visit xiengineering.com to learn more about Xi’s capabilities in the medical sector using simulation, data analysis, and machine learning. Xi Engineering Consultants are also exhibiting at MedTech Innovation Expo at stand C39.
The session will discuss the process the company undertook to ensure people with Parkinson’s are at the core of development, meeting their needs and care.
Med-Tech Innovation Conference Stage
Thursday 6th June 2024 14:00-14:30
Coming up with a new idea for a technology that could help to improve outcomes for patients is hard enough, but building a business around the technology can often be even more challenging.
Securing patent and other intellectual property (IP) protection at an early stage can help growing MedTech businesses to ringfence their innovation’s commercial potential in the form of exclusivity rights and use it to secure the finance needed to bring it to market, for example, by attracting investors or licensing the IP.
IP protection can give businesses many options for commercialising
their technology, but one of the keys to a successful IP strategy is one that aligns with the goals of the business, and establishing this early on may save time and money.
Knowing when, where and how to file a patent application is crucial and could make the difference between commercial success and failure. Being aware of the patent landscape is essential in fast-developing fields of innovation and could help to avoid getting caught up in a costly and time-consuming infringement action. It’s also important to have a good understanding of patent eligibility criteria to ensure your IP budget is being spent wisely.
Introducing Health-Tech Stage
“The promise of 3D printed implants – ARBURG plastic freeforming with medical certified materials”
Wednesday 5th June 2024 15:40-16:00
Arburg, manufacturer of injection moulding machines for more than 60 years, has been continuously developing a unique additive manufacturing machine for almost 10 years: the freeformer for industrial additive manufacturing. This is the process of manufacturing components in premium quality and stability from a wide range of original substances, material combinations and colour combinations. The highly flexible production process is easy and intuitive to access and can be configured to meet specific requirements.
Both the production of individual parts and low volumes from qualified standard granulates and the customisation of mass-
produced articles can be handled with ease. Even production in clean room environments is possible. By combining fundamental research with continuous technical advances, we are able to offer you both extensive expertise and practical technology to enable you to take into industrial additive manufacturing.
The ARBURG Plastic Freeforming (APF) technology is predestined for Healthcare application because it allows you to select the materials of your choice, to modify the parameters to develop your own products intrinsically, while keeping the technical characteristics and performance of the used material. Especially for medical grades, bio- or recycling materials, and for Material
development, this is a prerequisite. This opens not only opportunities in medical devices, textiles or orthesis but also in implants and pharmaceutical applications.
The freeformer can also use conductive materials in order to realize smart devices and individualisation/ customisation is the main characteristic of Additive Manufacturing. As it is a new manufacturing technology, the regulations are “growing” but ARBURG knows the legislation topics from the injection-moulding experience. Using the approved materials and threating them the same way as in injection moulding reduces considerably the barriers because the constraints we know in house.
Biocompatibility/Toxicology
Sterilization
Environmental
Process
Software
Software
Clinical
Training/
Packaging/Transportation/Stability/Shelf
Med-Tech Innovation Expo brings together leaders, engineers, innovators, and manufacturers, connecting them with technology and innovation to facilitate the design and manufacture of life-changing medical devices. The UK is home to one of the largest medical technology industries globally, with an annual turnover of 27.6 billion GBP, including over 5 billion GBP in exports. It also leads the world in research capabilities with universities building on an existing rich history of ground-breaking medical innovations. As the home of medical device manufacturing in the UK, MedTech Innovation Expo is at the centre of this exciting sector, and the exhibition showcases the entire ecosystem of market leading technology suppliers, machines, materials, software and service providers.
At Med-Tech Innovation Expo you can connect with almost 200 suppliers and see the entire spectrum of advanced technology, materials, and solutions available. The show is co-located with TCT 3Sixty, the UK’s definitive industrial 3D printing and additive manufacturing event, brought to you by Med-Tech Innovation’s sister publication TCT Magazine.
Med-Tech Innovation Conference Stage
“WMHTIA – The Power of Collaboration”
Wednesday, 5th June 2024 15:30-16:00
From pioneering the first clinical use of the X-Ray to the evolution of life-saving pacemakers, the West Midlands has always stood at the forefront of groundbreaking Health Tech innovation.
However, despite the growing community of innovators in the region, commercialising new products has become increasingly challenging. Fragmented support infrastructure, limited funding & investment opportunities, coupled with routine regulatory hurdles, contribute to a high rate of attrition during the crucial stages of product development.
The WMHTIA sets out to tackle these challenges by uniting the region’s key players under one cohesive programme, allowing innovators to focus on what truly matters – driving their ideas forward.
With the combined expertise of 20 partners spanning academia, business, and NHS – the WMHTIA provides access to essential services that are pivotal in critically developing technologies and driving them towards market access.
Unlike conventional accelerators, the scale and support model of the WMHTIA – which tailors a bespoke development path for every engaged innovator – facilitates the process of converting technologies from concept to real-world implementation.
Come to this talk, and find out how the collaborative nature of the WMHTIA is supporting a growing community of more than 200 innovators.
Thank you to our knowledge partners: Medilink UK, Boddingtons Plastics, Innovate UK, and NIHR, and our media partners: British Plastics and Rubber, Manufacturing Quality, Medical Plastics News, Packaging Europe, The Engineer, and TCT Magazine.
ENJOY THE SHOW!
The WMHTIA is funded by the Department for Science, Innovation and Technology, in partnership with Innovate UK and the West Midlands Combined Authority.
“Displacing single-use medical plastics with seaweed”
Thursday, 6th June 2024 13:30-14:00
Of the 60 million inhalers distributed per year only 0.5% are ever recycled. Olivia will discuss the burden of single use plastics in the medical sector in the context of new policies and supply chain procurement.
The talk will discuss the solution that FlexSea is providing- 100% biobased circular materials- and demonstrate
the successes of medical device pilots using FlexSea material so far. The talk will place emphasise on the need for sustainable solutions to: plug into existing pathways, not demand further resources, nor place extra effort on consumers.
Olivia will bring attention to the barriers sustainable solutions face in the medical sector and how we can all collaborate to other come these (NHS procurement, large corporates, SMEs, government & public sector).
In the fast-paced world of medical technology, the demand for reliable and highquality power solutions and advanced display technologies has never been greater. As healthcare professionals push the boundaries of medical science, they require equally innovative support systems to ensure the safety, efficiency, and reliability of their lifesaving equipment. Enter Relec Electronics, an established supplier of power supplies and display technology, tailored specifically for the medical industry.
Fingers on the Pulse of Power: Medical-Grade Solutions
At the heart of any medical device is its power supply - the critical component ensuring devices operate flawlessly in the most important moments. Relec Electronics stands at the forefront of this vital field, offering an extensive array of medical power supplies that meet and exceed global medical standards, including the revered EN60601-1 and UL60601-1 certifications.
Unparalleled Protection with 2 x MOPP
Most noteworthy in Relec’s arsenal are the power supplies boasting 2 x MOPP (Means of Patient Protection) - the highest level of protection against electrical shock for both patients and operators. This elite standard underlines Relec’s commitment to safety and reliability in environments where there’s no room for error.
Versatility and Customisation
Relec’s range is as vast as it is impressive, featuring low power plugtop and desktop devices, chassis mounting supplies from 40W to 300W, and configurable units up to 24kW. This diversity ensures that whether for laboratory analysis, diagnostic equipment, or life-sustaining machines, there’s a power supply fit for the task. Moreover, the willingness to collaborate on custom or variant solutions signifies Relec’s flexibility and dedication to meeting unique industry needs.
Clarity in Every Pixel: Display Technologies
As the medical industry evolves, so too does the complexity of
its diagnostic and monitoring equipment. Clarity, precision, and adaptability are paramount, qualities embodied in Relec Electronics’ range of display technologies.
Tailored for the Medical Field
Relec’s display range, treated with optional anti-bacterial coatings and customisable for surgical glove compatibility, represent the pinnacle of medical-grade technology.
Offering sizes from a compact 0.9” to an expansive 31.5” and above, alongside varied brightness levels, interface types, and touch panels, these displays are engineered for every medical application imaginable. From patient monitoring systems to complex diagnostic machinery, Relec’s displays bring critical data to life with unmatched clarity.
Life-Saving Applications
The versatility of Relec’s display solution range finds them at the heart of a broad spectrum of medical applications. Whether in the lab, operating room, or patient bedside, these displays ensure critical information is presented with precision,
aiding in diagnostics, patient monitoring, surgical procedures, and more.
A Partner in Medical Innovation
Working hand-in-hand with the medical industry, Relec offers expertise, customisation, and a commitment to quality that goes beyond the standard. It’s this partnership approach that has cemented Relec’s position as a key player in medical technology.
As the medical industry continues to advance, the need for specialised, reliable technology partners becomes ever more critical. Relec Electronics stands ready to meet this challenge, offering a synergy of power supply and display solutions that not only meet but exceed the demands of modern medical applications. With a steadfast commitment to innovation, customisation, and safety.
Where the pace never slows in healthcare and reliability is non-negotiable, our Medical Rugged Tablets stand out as
the essential tool for medical professionals. Crafted to thrive in such dynamic environments, these tablets come in a variety of sizes, ranging from the 7 inch to 10.1 inch, ensuring there’s a perfect match for every need within the medical practice. We offer a diverse range of add-on accessories designed to tailor your device precisely to the requirements of your practice. Whether it’s for charting patient data, scheduling, or in-the-field care, our tablets are not only durable and dependable but are specifically designed with healthcare professionals in mind.
For those on the frontline of medical technology, looking to elevate your equipment’s reliability, safety, and efficiency, the choice is clear. Reach out to Relec Electronics today, and let’s power the future of healthcare together.
www.relec.co.uk sales@relec.co.uk 01929 555800
LinkedIn: https://www.linkedin.com/ company/relec-electronics/
Facebook: https://www.facebook. com/relecelectronics
X: https://twitter.com/RelecElectronic
YouTube: https://www.youtube. com/@relecelectronicsltd2564/
Afull ISO 13485 management system requires many different procedures and record types to be compliant, all of which require maintenance with surrounding change control, review, and approval processes. The labour-intensive nature of a QMS leaves strains on time and resources for any business to remain fully compliant.
Choosing QMS software to assist with common compliance challenges such as document management and control, corrective and preventive action management, supplier evaluation, and internal auditing can be both daunting and time consuming, it can be difficult to get a clear understanding of the products on offer, whether
or not they will be good fit for your business and what the long-term cost will be.
ACTIV, INTUITIVE QUALITY MANAGEMENT SOFTWARE.
Designed by ISO experts, Activ is a fully equipped electronic QMS software which provides a reliable, simple to use methodology to help you maintain your Quality Management System and reduce ISO-related risks. The software is modular, making it both affordable and scalable, as you only pay for what you need.
BOOK A PERSONALISED DEMONSTRATION.
At Advena we are used to helping clients with the many challenges of ISO compliance
and during your demonstration of Activ we will not only show you how the software can assist with transforming manual processes into electronic workflows, plus the standard version history features, but we take great pride in addressing specific administrative pain points you may have and showing you how Activ can address them.
Whether you’re about to start your QMS journey or are a compliance expert looking to improve the efficiency and effectiveness of your management system, Activ’s powerful and flexible tools can transform the way you manage your resources, helping you to ensure audit-readiness at all times.
For 25 years Advena have been providing regulatory consultancy services to a multitude of global manufacturers of medical devices and cosmetics from our base in Warwickshire. We pride ourselves on our attention to detail, excellent reputation, and unwavering professionalism. Having worked with over 300 clients, we are one of the UK’s longest standing and most experienced consultancies. Our team of consultants have over 35 years’ experience in regulatory affairs and quality management and will confidentially help you bring your product to market.
If you would like to find out more about Advena or Activ, please visit our website www.advenamedical.com
AOli Johnson speaks to John Kawola, Chief Executive Officer of Boston Micro Fabrication about the company’s role as an advisor for multiple projects at the University of Nottingham.
t the University of Nottingham, teams of researchers are taking part in a UK grant-funded project that began in 2023, that is working to develop a playbook for standardising 3D printing in medtech and life sciences applications. Boston Micro Fabrication (BMF), an MIT spinout that specialises in micro 3D printing, is working as an advisor for the university on this project, which is titled “Dial Up”. This project runs alongside follow up work funded by an MRC project, the “Acellular/Smart Materials – 3D Architecture: UKRMP2 hub”.
Boston Micro Fabrication CEO John Kawola was also recently asked to serve on the advisory board for another project based in the University of Nottingham’s Biodiscovery Institute, after it received a grant to focus on designing bio-instructive materials for translation ready medical devices. The goal of the EPSRCfunded “designing bio-instructive materials for translation ready medical devices” project is to address major compatibility issues of implanted medical devices.
Speaking to MTI about the company’s role as an advisor, John Kawola, CEO of BMF said: “There’s really two roles, one is they are using our platform as a way to make samples and potentially to make devices, but really the first phase is to make samples, so that’s one. And then I’ve been part of the advisory board to the grant project. As an advisory board, we play the role to listen to updates, try to advise the team on direction, and progress.”
Kawola spoke about the specifics of the surfaces of medical devices: “You might have a surface that has cones on it, or small circles or cavities, or concave half circles, and what you’re trying to do is optimise, for example, with
catheters, you’re pretty much only interested in minimising infection, so you’re trying to keep bacteria away. In cases of implants, you’re trying to do two things. You’re trying to keep bacteria away, but also encourage cell growth on top of the device. And these topologies are small, have really small features, and that’s where BMF generally thrives. Our focus is on doing micro-level components, typically in medical device, electronics or life sciences.
“University of Nottingham is using our platform to create samples, I’ll call them chips, and they are being used to study different topologies and different polymers to try and optimise that sort of bacteria vs cell growth optimum they’re trying to get to.”
According to Kawola, the end goal of the research that began in 2023, and set to be completed by early to mid 2025, is to create a ‘welldocumented’ playbook that can be licensed by the medical device community. If there is more work to be done after 2025, the teams will seek additional grants to continue the project.
Below: (left to right) Prof. Ricky Wildman, John Kawola, Prof. Felicity Rose
Regulation is a crucial topic of discussion in the MedTech community, and can often be a headache for medical device manufacturers when trying to bring a product to market in multiple countries. The project at the University of Nottingham is aiming to create a playbook for medical devices that can be used all over the world,
Kawola told MTI about how the research in the playbook will improve regulatory processes for medical device companies: “The medical device manufacturers, the Medtronics, the Johnson & Johnsons, and the Strykers of the world, are developing these devices and they have to get the regulatory requirements, for example from the FDA in the U.S., and that includes the device, the material, and its typically on those companies to get the approval. Now, what helps is when you have a body of knowledge or research to show, and if the body of research is large and complete and validate, that can be valuable in the FDA application where the medical device company has to go through regulatory approval, but they may not need to go through and replicate all those tests over and over again, because the body of research has already been done.”
In modern healthcare, the integration of advanced technologies is paramount in delivering accurate diagnoses and optimal patient care.
Smiths Interconnect, a leading name in connectivity solutions, is a leader in providing stateof-the-art medical connectors. These connectors play a pivotal role in ensuring the reliability and efficiency of medical equipment, contributing to the advancement of healthcare practices.
Designed to meet the exacting demands of medical applications and the preservation of signal integrity—an essential requirement in the transmission of critical data within medical environments. The D04 product range is manufactured with premium materials to ensure
durability, even in the face of frequent sterilization processes and exposure to harsh environmental conditions within medical settings.
The Smiths Interconnect D04 Connector range offer a high density contact count, up to 82 contacts on the standard configuration and up to 10,000 mating cycles. Insulation resistance greater than 5000 MOhm at 500 VDC and meets the electrical requirements of EIA-364-05 to 70 test procedures. All of this contributes to the accuracy of data transmission, ensuring the reliability of vital information in medical diagnostics and treatments.
The D04 provides TouchProof push-button quick disconnect and finger proofing isolator for added safety. It is
easy to assemble due to the D shape layout which significantly reduces capacity for incorrect mating. It can also be used single handed allowing medical staff more flexibility when providing care.
The robust locking mechanisms in the D04 connectors offer maximum reliability and stability and minimizes the risk of disconnections or interruptions, enhancing the overall dependability of medical equipment.
The D04 range is extremely versatile and caters to a wide spectrum of medical devices and applications. Whether used in diagnostic imaging equipment requiring highspeed data transfer or surgical tools necessitating low-latency connections, the D04 range
proves to be adaptable and reliable. This versatility makes it an ideal choice for medical equipment manufacturers seeking standardized connectivity solutions across diverse product lines.
The D04 range is not only technically advanced but meet the highest regulatory benchmarks and essential industry standards and certifications.
As healthcare continues to advance, the D04 connectors play a crucial role in elevating the standards of reliability and performance in medical applications, ultimately benefiting patient care and outcomes.
Aerco can help with the component selection process to ensure you have the right part at the right time.
In Leeds, UK, Crispin Orthotics has made waves in the orthotics industry with its innovative approach to manufacturing, powered by 3D printing technology. The firm deployed its first 3D printer back in 2016 and since then has built a thriving business delivering 3D-printed orthoses, such as ankle-foot orthoses (AFOs), spinal supports, wrist braces, helmets, and face masks. In fact, there aren’t many orthotics and prosthetics (O&Ps) the 3D specialist can’t print.
The key to the company’s success? How it’s integrated all its workflows with its 3D printing lab. Crispin scans body parts at one end of the spectrum, creates computer images with another, and then sends them on to technicians who use other applications to create, adjust, and generate super-accurate models of what they hope to produce. The models are then exported to computer aided design (CAD) software for final adjustments before moving to modern HP Multi Jet Fusion printers for production.
If it sounds involved, it is. However, compared to traditional processes that can be a headache and take weeks to complete, using 3D printers in tandem with existing workflows is fairly simple and much faster. Indeed, 3D-printed O&P, implants, models, and medical devices can be ready for patients in mere days or even hours.
Again, the key is integration. We believe an increasing number of healthcare organisations around the world are going to shed traditional 3D printing approaches, where you park your machine in a back room and will instead look for ways to integrate them with other systems.
Now, what do we mean by integration? We are referring to situations where your 3D printing processes are able to receive digital inputs from as many areas of the organisation as possible. For example, if you have a central 3D printing lab in a hospital (about 400 hospitals worldwide do), you want to ensure everyone from your surgeons, radiologists, nurses, technicians, and engineers to your accountants and lawyers, can see, review and participate in production of medical components.
Some medical organisations accomplish this by deploying commercial solutions. Others hire third party service providers to handle everything for them. And then there are those that take a hybrid approach combining commercial solutions with applications they’ve built themselves (even though customising your own software can add time and expense). Whatever the case, it is important to have a system in place for ensuring seamless integration of 3D printing operations and workflows across the organisation.
When medical organizations do that, they suddenly realize all sorts of benefits. Here are some significant improvements we see on the horizon:
• Point-of-production control: Connecting 3D printing to other parts of the organisation minimises dependence on outside suppliers, which means you’re less exposed to global supply chain disruptions. It can also reduce your lead times, ensure greater quality control, and let you keep a closer eye on how well you’re meeting regulatory requirements.
• Cost savings: On-site 3D printing reduces logistical costs associated with traditional manufacturing processes, such as shipping, inventory management, and warehousing. It also lets you produce parts or products on-demand, avoiding vendor or service provider markups.
• Confidentiality: Even with NDAs in place, every time you send a 3D printing design to an outside vendor, you are at risk. Someone on the other end might deliberately or inadvertently share intellectual property with people they shouldn’t. All sorts of bad things can happen. Keeping design and production inhouse, on the other hand, helps minimise such risks and head off potential calamities.
• Improved sustainability: 3D printing parts and products onsite means you’re not shipping them all over the place, which in turn reduces carbon emissions from planes, trains, and automobiles. Because you’re typically 3D printing on-demand rather than in bulk, you also avoid having to store items in facilities that use energy for lighting and environmental systems. What’s more, studies show you waste less material with 3D printing than with traditional injection molding. You can recycle more scrap and take advantage of 3D printing materials that have been specifically designed to be re-used.
• Better patient outcomes: We don’t always think of patients as customers or consumers, but they are. Every time they step into a medical office, they’re forming opinions about it.
And more often than not, those views are partly shaped by online shopping experiences that have conditioned them to expect their purchases to show up at their doorsteps within 24 to 48 hours. Well-integrated 3D printing operations help address such “I want it now” sentiments by delivering many medical and dental products in days instead of weeks or months.
The advantages of integrating 3D printing operations with other digital workflows are many and clear. But realising those benefits will take time, effort, and investment. We believe most medical organizations will head down this path because it is where the industry is headed, and missing this trend could hinder business growth and patient satisfaction.
Oli Johnson speaks to Alison Sundset, Chief Executive Officer at HoloCare, about the company’s interactive 3D holograms of organs for surgical decision making.
HoloCare, a Norwegian medtech company that provides AI generated holograms for pre-operative planning, is working with European leaders in technology and healthcare research as part of the project ‘HoloSurge’, a four-year collaboration with a shared goal of reducing the risk of complications during planned surgery. The project received a grant worth 8.9 million EUR in early 2024, allocated by transnational research and innovation funding body Horizon Europe, to further the development of organ hologram technology to power informed surgical decision making.
HoloCare says the technology is set to improve both the surgical process and the decision-making beforehand, potentially reducing complications. This includes issues such as infection, bleeding, organ damage and death, which currently affect up to 48% of
We created the whole of HoloCare Studio during the pandemic, it is made by clinicians for clinicians
liver surgeries, and 60% of pancreatic surgeries according to the company.
Speaking to MTI, Alison Sundset, CEO at HoloCare explained how the company’s technology works: “What we’re doing is we are taking a normal CT image, so in this case a liver, which is our first application, then we put it through our HoloCare studio and we make a 3D model of it using AI. With current care, it takes about a week to
send to another company or if you do it yourself a whole day. We’ve taken it from that to two minutes using AI. We create the 3D model, then it becomes a 3D image which is pushed up into a Microsoft HoloLens, but you can use an Apple Vision Pro, or it can be a 2D image on a 3D screen.”
The technology allows surgeons to explore a patient-specific scan of an organ and plan out precisely what needs to happen in the operation on that patient. Another benefit according to the company is that the scans can be shared in real time with people across the world. A surgeon in one area of a country could jump on a teams call with a surgeon in a different city, and they could both explore the scan on their computers or in virtual reality using headsets and discuss what needs to be done for the procedure.
A method of pre-surgical planning that has made headlines in recent times is the 3D printing of anatomical models, for surgeons to handle the model practically and get a physical feel for what they need to do in the operating theatre. This process can take time, and surgeons in different cities or countries cannot view the same model at the same time.
“You can just pull someone into a meeting and show you a model and we can interact with it. We created the whole of HoloCare Studio during the pandemic, it’s made by clinicians for clinicians,” said Sundset.
Speaking about what the 8.9 million EUR funding from Horizon Europe means for the HoloSurge project, Sundset said: “It means that we can move a little bit quicker with our mission, our vision moving forward is to have it in preoperative planning, but our next goal is to transform it into the operating theatre. So imagine that suddenly you’re able to overlay the organ actually on the body as you are operating, onto a patient. Then you can see it in real time. We are also adding MRI, CT and ultrasound, this will allow us to move on from the liver to another organ, which is in this case the pancreas. Pancreatic cancer is quite difficult to firstly detect, diagnose and operate. So we’re adding the pancreas to the application, the pancreas and the liver are obviously in the same area, the abdomen, so we are calling it the ‘HoloGut’ program. It’s really exciting and we have some huge centres of excellence, one of them being Leeds. It’s going to be a big four years.”
that they would continue surgery. So its really essential that we capture the young surgeons in schools now.”
In the HoloSurge project, HoloCare is working with companies from various different specialisms, which all come together to make the technology what it is, such as specialists in ultrasound and MRI, as well as a patient organisation on board, radiologists and more.
Sundset says that the HoloSurge team was at first nervous that the older, more traditional surgeons would be more apprehensive to the adoption of the technology, but they have discovered that hasn’t been the case. The CEO added: “We thought it would be difficult when you haven’t been a gamer, or you know, my generation, we didn’t grow up with this. So when talking to surgeons and asking, how would you see this, how would you do that, and its taking like half an hour and they’re up and running.”
Speaking on the adoption aspect, Sundset said that the technology is not replacing anything, it is not taking away a CT or MRI, it is adding to something, and is giving an added benefit rather than taking something
Another use for the technology outside of pre-operative planning is its use as an educational tool, and this is something that HoloCare has its eyes on already.
Sundset said: “That comes outside of the CE marks, you don’t have the regulatory hurdle, that goes away because it becomes an educational tool. We have an education piece rolling out in Leeds, on the heart, so a total other arena. Obviously these people will also be the early adopters as well, so the ones who are trained on it, it’s obviously natural
away and making people learn how to adopt that. Surgeons will still see what they need to see with traditional surgery, but they have this as an addition.
Sundset added: “I think generally, technology adoption is a challenge and it takes time, but you have to just make sure that you’ve addressed all the issues. You might imagine how frustrating it would be if you pick up a HoloLens and its not charged. Teething issues that make you think ‘Oh, I hadn’t thought of that’, that somebody has to be the administrator and make sure everything is charged. So small things. And then my worst nightmare is that it becomes like a surgical toy, so its just put on the shelf somewhere and its like, oh it was fun. So as a company, we have to drive that adoption process.”
Sundest told MTI about how the price of the VR technology will come down as adoption increases: “They will come down as more people adopt it for different reasons, even for planning a hospital, for the smart hospitals of the future, everything will be planned in 3D moving forward.”
Surgeons will still see what they need to see with traditional surgery, but they have this as an addition
SCIGRIP Methyl Methacrylate Adhesives offer:
SCIGRIP Methyl Methacrylate Adhesives offer:
SCIGRIP Methyl Methacrylate Adhesives offer:
• Durable bonds to metals, composites, and plastics with little or no surface preparation
• Durable bonds to metals, composites, and plastics with little or no surface preparation
• Durable bonds to metals, composites, and plastics with little or no surface preparation
• Fast curing for optimised throughput
• Fast curing for optimised throughput
• Fast curing for optimised throughput
• Excellent resistance to fatigue, impact, and shock
• Excellent resistance to fatigue, impact, and shock
• Excellent resistance to fatigue, impact, and shock
• Outstanding environmental and chemical resistance
• Outstanding environmental and chemical resistance
• Outstanding environmental and chemical resistance
• Convenient dispensing through side-by-side cartridges
• Convenient dispensing through side-by-side cartridges
• Convenient dispensing through side-by-side cartridges
Let’s start by talking about
Let’s start by talking
Let’s start by
Itoro Udofia, Director, Medical Health Service at TÜV SÜD, explores IEC 60601 and the challenge it brings to medical device manufacturers.
IEC 60601 is a series of technical standards that ensure the safety of medical electrical equipment. It is relevant to manufacturers of medical electrical equipment and systems, and those that manufacture components of medical electrical equipment. The standard series includes, but is not limited to, requirements regarding electrical hazards, mechanical hazards, the spread of fire from the equipment, as well as laser sources and sonic and ultrasonic pressure. It is also applicable for in vitro diagnostic (IVD) medical purposes, including self-test IVD medical purposes.
The rapid technological changes in medical equipment have necessitated prompt revisions to safety standards. The second amendment to the third edition of the medical standard (IEC 606011, Edition 3.2) improved the previous version as it revised outdated references, provided more definitions, and clarified technical issues that manufacturers may have experienced with previous versions.
IEC 61010-1 is the general standard for safety requirements for electrical equipment for measurement, control and laboratory use. Electrical equipment for laboratory refers to:
• Equipment that measures, indicates, monitors, inspects, or analyses materials, or is used to prepare materials
• In vitro diagnostic (IVD) equipment including self-test IVD equipment to be used in the home
• Inspection equipment to be used to check people or material during transportation
Edition 3.2 has around 1,500 single specific requirements. It deals with the general requirements concerning basic safety and essential performance for medical electrical equipment and systems, and serves to ensure that, in both normal conditions and fault conditions, no single electrical, mechanical, thermal or functional failure shall pose an unacceptable risk to patients and/or operators. E.g. related to electrical, mechanical, thermal and functional hazards.
Edition 3.2 includes updates in the areas of risk management, software and usability, use of power supply units, use of safety signs, indicator lights and alarm indicators, maximum overcurrent protection, insulation components, testing & measuring, components that may pose a threat, mechanical and thermal hazards, lasers and optical radiation, ME systems, and EMC planning.
Regulatory bodies across key markets require compliance to IEC 60601, with countries and regions such as the USA, Europe and Asia requiring medical devices to comply with the standard before manufacturers can launch these products in their markets. The requirements are often recognised as State-Of-The-Art (SOTA), which means that for medical devices, this is what is currently accepted as good practice in technology and medicine, not necessarily the most technologically advanced solution.
Manufacturers therefore have to take into account SOTA during the design and construction phase. During
the following production phase, manufacturers have to take into account all changes in standards and scientific knowledge (SOTA) within the framework of their risk management system, until no more new products are placed on the market. The risk management approach requires manufacturers to recognise new internal standards as part of new scientific knowledge. As a minimum, manufacturers have to conduct a gap analysis if new harmonised standards are issued, or new scientific knowledge is available. Gap analysis means retesting, reevaluation and, if necessary, redesign of the medial device.
Medical device manufacturers must also be aware of the varying regulatory transition periods worldwide for IEC 60601-1, Edition 3.2 and navigating the requirements across different markets can therefore be complicated. For example, a transition period of three to four years has been given in most countries and regions, so these
transition periods are not set as a standard period of time across all countries. However, it is also possible that some countries will require standard compliance with the predecessor standard (Edition 3.1) for a longer time.
IEC 60601-1 is a widely accepted standard in the U.S., Canada, the EU, Japan, Brazil, Russia and Australia. To avoid being denied entry into these and other markets, manufacturers with the goal to go worldwide on the market should therefore ensure that their products comply with both Edition 3.1 and 3.2 of the standard. As version 3.2 includes a multitude of many small changes (78 in all), it would normally be considered wise to instigate a gap analysis for all existing products, to ensure that they will meet the new requirements set out in 3.2 edition. However, in reality, the vast majority of manufacturers are conducting testing according to the new standard edition, instead of conducting a gap analysis. This is because new test reports are required anyway for other international approvals and the effort involved is usually comparable.
REO UK, a leading provider of innovative power supply solutions in the medical sector, proudly announces its participation in the upcoming Med-Tech Expo 2024, scheduled to take place at the NEC on the 5-6 June
Med-Tech Expo is a premier event that brings together leaders, innovators, and manufacturers in the medical and healthcare industry. REO UK is excited to participate in this prestigious event, showcasing its latest advancements in Power Supply technology that play a crucial role in ensuring safety in the rapidly evolving landscape of medical technology.
At stand B14 in Hall 2, attendees can explore REO UK’s comprehensive range of products designed to meet the unique challenges of powering the healthcare sector. From precision transformers that integrate safety monitoring to EtherNet isolation devices, our products are tailored to enhance your medical equipment’s efficiency, reliability, and safety.
HIGHLIGHTS AT REO UK’S STAND:
1. REOMED Medical Isolation Transformers: Discover our stateof-the-art transformers that ensure optimal performance and reliability in medical devices.
2. REO Iso-Monitor: our ISOMONITOR monitors the dielectric resistances of both live contacts of the isolation transformer›s output socket against grounding potential and generates a warning signal in the event of a fault.
“We are thrilled to participate in Med-Tech Expo 2024, where we can showcase our commitment to driving innovation in Power Supply technology for the medical industry,” said Mr Steve Hughes, Director at REO UK. “Our presence at this event reflects our dedication to supporting the advancement of medical technology and contributing to the improvement of healthcare solutions.”
Join REO UK at Med-Tech Expo 2024 to explore the future of electrical engineering in the medical field. Our team looks forward to welcoming visitors, engaging in meaningful discussions, and fostering collaborations that will shape the future of healthcare.
For more information about REO UK and our participation in Med-Tech Expo 2024, please visit https://www.reo.co.uk/medical-transformers
3. REO Iso-Net: The REO Iso-Net protects devices and people from electrical voltage spikes on network power cables by disconnecting the EtherNet wiring from the screen connected to the Earth conductor. ● Ultra thin bio compatible protection ● Outstanding chemical, moisture and electrical barrier protection
● High lubricious dry film conformal coating
● Metals, Elastomers, Electronics and Plastic
● Proprietary Dimer is 99.7% pure
● CW Parylene: USP Class VI and ISO10993 tested
● MAF No. 1176 on file with the FDA
Curtiss-Wright Surface Technologies (CWST) provides high quality surface treatments which will improve the life and performance of critical components through its global network of over 68 operating divisions and specialist onsite teams. Our surface treatments have been successfully used by OEM’s in major industries such as aerospace, automotive, oil & gas and power generation for many years.
We are only too aware of the logistical challenges and costs faced by our customers and so we can offer a “One Stop Shop” solution providing a wide range of surface treatments including Controlled Shot and Laser Peening, bespoke and
trade Coating Applications, Thermal Spray Coatings and Parylene Coatings for metal, alloy, plastic and electronic components as well as Analytical Services.
We offer our customers a single source solution and point of contact for all their surface treatments, supporting their requirements through our global network of over 68 worldwide facilities and on-site field teams, improving and reducing turnaround times and costs. We are specialists in protecting components from common failures and reducing maintenance costs for key industries such as aerospace, oil and gas, automotive, medical and general industrial markets.
All currently valid Medical Device Directive (MDD)
CE certificates are set to expire in May of this year, marking a critical juncture for EU and UK medical device manufacturers. This date holds significant weight as the EU Commission had anticipated all manufacturers with products on the EU market to transition to the new Medical Device Regulations (MDR) CE certificate, yet this expectation was not universally met.
The Regulation (EU) 2017/745 (MDR) was established to institute a more robust system of conformity assessments for medical devices in the EU market, becoming applicable since 26 May 2021. This regulation aimed to replace previous medical device directives, with transitional provisions extending to 26 May 2024. However, due to insufficient capacity among notified bodies and manufacturers’ inadequate preparedness to meet the MDR’s heightened requirements before the end of the transition period, the European Commission found it necessary to extend this deadline. Yet, this extension comes with a caveat – it is subject to certain conditions to ensure only devices that are safe and for which
Tautvydas Karitonas, Managing Director of Test Labs, explains the significance of meeting the medical device regulation (MDR) deadline for UK medical device manufacturers & implications on our healthcare systems.
manufacturers have already taken steps to transition to the MDR will benefit from the additional time.
With challenges surrounding Notified Body capacity, the only way to remain on the market is either to possess a valid MDR CE certificate or secure an extension to current MDD CE certificates – achievable only through an MDR-certification application with a notified body. The situation echoes a real-world Thanos snap, posing a serious risk to our healthcare system as a significant number of devices are exposed to this risk.
Consider the scenario: should a manufacturer fail to meet MDR requirements, their products could swiftly be removed from the market, leading to potential shortages affecting patients reliant on critical devices like pacemakers or diagnostic tools. This impact extends beyond patient care, burdening healthcare providers with increased costs as they scramble to source alternative, potentially more expensive devices. Moreover, non-compliance
tarnishes the reputation of manufacturers and suppliers, eroding trust among healthcare providers, patients, and the public. This loss of trust can have far-reaching consequences, damaging businesses and disrupting the healthcare ecosystem.
In the context of the UK—which accounts for 12.1% of all medical devices sold within the UK and EU and hosts the NHS as its largest device consumer— the stakes are particularly high. The NHS’s battles with supply chain issues during the COVID-19 pandemic have underscored the critical need for robust, nearly constant monitoring of supply chains to guarantee a steady flow of compliant medical devices. The looming risk of shortages is not hypothetical but a tangible threat, highlighting the essential need for proactive planning and mitigation strategies.
This regulatory landscape casts a long shadow over medical device research and development. Despite the UK’s Medtech sector being
among the fastest-growing globally, the intensified focus on regulation and compliance is siphoning resources away from innovation, potentially stalling advancements in vital areas such as orthopaedic implants or diagnostic equipment development. More and more, manufacturers are forced to prioritise regulatory compliance over groundbreaking product development, potentially slowing the pace of progress.
It is critical for UK medical device manufacturers and healthcare organisations to ensure they are fully prepared for the MDR deadline. Manufacturers must ensure their devices meet the stringent requirements set by the regulators, while healthcare organisations need to have comprehensive plans to mitigate both short-term and long-term supply chain disruptions. Navigating these regulatory challenges with adaptability and a commitment to innovation is essential for safeguarding the vitality of the UK’s medical device sector and, by extension, the overall healthcare system.
Rapid Fluidics CEO Paul Marshall discusses the advantages of 3D printing for microfluidic devices.
As the name suggests, microfluidics are processes using very small amounts of fluids, typically in the region of tens of microlitres. The example that is most familiar to people is the drops taken from a nasal swab for Covid testing. They are used across the Life Science sector for disposable point-of-care diagnostics; drug discovery and therapeutic development; reproductive health; biodefense; lab-on-a-chip/organon-chip; lab automation systems; environmental testing etc.
Notwithstanding some amazing techniques from novel high-end equipment, the majority of plastic microfluidic devices are created by producing a workpiece with open channels and sealing it with a secondary lid. This applies at both the prototyping and mass manufacturing stages. The channels and features can be created by a variety of means: CNC-machining is a common one for prototyping, as is cast PDMS. Hot-embossing also works well, along with laminating 2D-profiled layers. As an alternative, there’s 3D printing, where companies such as Rapid Fluidics have novel approaches to directly print lids, instead of using sealing processes. The sealing methods often depend on the production method, but there can be crossover. Each has its respective strengths and weaknesses
There are two types of adhesive bonding: One is to apply the adhesive directly to the workpiece (or lid), join, and cure, usually with UV light. The other is to use a pressure-sensitive adhesive (PSA) on film. UV-curing provides an excellent seal, and provided it is cured correctly, causes no material related problem with biological fluids within. PSA film is very quick and easy but can deform under pressure causing variance in channel geometry. The up-side of this is that the flexible film can be used for exactly that, as a valve or a temporary seal.
Diffusion bonding is achieved by applying pressure between the two parts via chemical bond, either following surface treatment such as plasma or solvent exposure, or by increasing temperature. If done correctly, this can produce near-perfect results, if incorrect, the channel geometry can deform significantly, or residual solvents can remain in the channels.
By tracing the edge of the channel with a suitable laser, enough thermal energy is applied to weld the two pieces together, avoiding all use of adhesives via laserwelding. For this to apply, one piece must be able to absorb the thermal energy so either needs to be black or be coated with a suitable IR-absorbing chemical. The configuration of the profiling is extremely important: Too close to the channel edge and weldflash can build up in the channel, disturbing the fluidic flow; too far away from the channel and fluids can be lost due to capillary forces.
3D printing can produce open channels down to 50um very simply using high-resolution LCD and DLP printers, which can then be enclosed using PSA tape or adhesive-bonded lids. High end 3D printers can produce channels
nearer 10um and Two Photon Polymerisation (2PP) can achieve feature sizes in the nano-scale.
The time, expense, and risk of all of these joining techniques can be mitigated by simply 3D-printing a lid directly onto the microfluidic layer, which is possible with advanced techniques developed at Rapid Fluidics to allow removal of uncured resin from within the formed channels and also allow for high aspect-ratio unsupported channels
This has many advantages: the key one being time, but also the lid itself can incorporate additional features such as more channels with vias linking the layers.
Mixing materials to allow for integrated flexible parts or alternating between transparent and opaque layers is possible. Additional components can be included in the fabrication process such as embedded electronics in the form of PCBs or screenprinted electrodes. Glass or similar coverslips can be incorporated for high transparency, and obviously 3D geometry for complex mixing and valve manifolds can simply be included, along with external connectors from mounting features for manifolds, barbed tube fittings, or threaded holes.
A single-layer enclosed part up to 180mm x 110mm, with channel sizes down to 50µm can be printed in around half an hour. That’s half an hour from receiving a CAD file to running fluids through on the lab bench. This means that multiple iterations of a concept with nextday delivery can be evaluated and move toward a final design with hugely reduced timelines.
Though multiple approaches exist to create microfluidic channels, the advantages of 3D Printing are clear, especially when combined with novel manufacturing methods and an experienced team of engineers to facilitate project design and execution.
In the intricate world of medical device manufacturing, precision and quality are paramount. Every step of the process, from initial design to final inspection, must adhere to strict standards to ensure the safety and effectiveness of medical devices. Central to this journey is the equipment that facilitates the manufacturing process, particularly in handling complex measurements and inspections.
At the heart of modern medical device manufacturing lies the intricate process of measurement and inspection. Components must be precisely measured to meet exact specifications, ensuring they function as intended within the human body. This metrology process involves scanning multiple parts or long components, detecting minute defects, and providing accurate feedback for adjustments. It is critical that the technology handle these tasks efficiently and accurately to maintain product quality and regulatory compliance.
The Glebar P5K Gauging System’s versatility shines through in its ability to inspect a wide range of components with exceptional ease. From delicate medical guidewires and arthroscopic shavers to robust titanium fasteners and medical bone drills, the system delivers accurate measurements at the push of a button. This capability streamlines the inspection process across diverse product lines, ensuring consistent quality standards.
The P5K system’s software prowess extends to profiling geometric shapes up to two (2) meters in length, accommodating varying product dimensions effortlessly. Moreover, its automatic communication of production results empowers even the most junior employee to
measure complex dimensions accurately. This democratisation of measurement capabilities enhances operational efficiency and quality control across all levels of workforce expertise.
Furthermore, the P5K system drastically reduces setup times by scanning all parts in a cycle at all stations, providing realtime feedback on diameter, length, and geometric position adjustments to the grinding system. This comprehensive approach not only accelerates the inspection process but also enables precise corrections. The system automatically corrects dress shape, ensuring precision and consistency in a matter of seconds. This seamless integration of data feedback and automated adjustments optimises production workflows, minimizing downtime and maximizing productivity.
UNMATCHED PERFORMANCE:
At its core, the Glebar P5K Gauging System offers unparalleled accuracy and speed. Capable of scanning multiple short parts or one long part in a single operation, this system expedites the inspection process without compromising precision. With a remarkable scanning rate of 16,000 diameter readings per second, operators gain realtime data, empowering them to make informed decisions swiftly.
The brilliance of the P5K system lies in its simple yet powerful user interface. Operators can initiate scanning
with a single mouse click after clamping the part in the fixture. The system presents results clearly as a definitive “Go” or “No-Go,” enabling rapid assessment of product quality on the manufacturing floor. This intuitive interface minimises training time for new operators and enhances overall productivity.
Beyond basic measurements, the P5K system excels in detecting even the minutest defects. Its automatic measurement capability ensures consistency and accuracy, free from any operator influence. Quality managers benefit from comprehensive analysis data and traceability, crucial for compliance with stringent quality standards. The system’s reporting, lot control, and data aggregation features facilitate Statistical Process Control (SPC) analysis, driving continuous improvement initiatives.
With stable calibration and no moving parts, the P5K system offers reliable performance over time. Mounted on precision-lapped granite, it provides a qualified and thermally stable surface for precise measurements. For companies with multiple facilities, the system’s SQL version seamlessly connects to the intranet, centralising data measurements and templates across plants. This integration enhances data management efficiency and consistency across the organisation.
The P5K system empowers operators with advanced control capabilities. It supports point-to-point dimensioning through simple clicks on part features, with unlimited zooming for detailed analysis. Operators can set warning tolerances to preemptively address potential deviations, ensuring proactive quality control. The system also provides size compensation feedback to Glebar CAM.2, GT-9AC, and GT-610 CNC machines, facilitating seamless integration into the manufacturing process.
All data, templates, results, and raw scan information are stored within the metrology system, ensuring comprehensive product traceability. Result data can be easily imported into popular software tools for further analysis and reporting, enhancing transparency and accountability throughout the production cycle.
In conclusion, the Glebar P5K Gauging System represents a paradigm shift in medical device manufacturing quality control. Its combination of precision, speed, user-friendly interface, and advanced analysis capabilities positions it as a catalyst for excellence and innovation in the industry. With the P5K system, manufacturers can achieve unmatched levels of accuracy, efficiency, and compliance, ushering in a new era of precision-driven production methodologies. Incorporating case studies further illustrates the real-world applications and benefits of the Glebar P5K Gauging System, solidifying its position as a cornerstone of automation excellence in medical device manufacturing.
In the ever-evolving landscape of medical device manufacturing, selecting the right contract manufacturer is paramount for ensuring longterm success. The choice of a partner capable of not only meeting immediate production needs but also navigating challenges and uncertainties with resilience is critical.
In an industry where quality, compliance, and reliability are non-negotiable, finding a medical device contract manufacturer equipped to withstand disruptions, adapt to changing market dynamics, and deliver consistently superior outcomes is essential.
There are a number of intricacies when selecting a resilient medical device contract manufacturer including:
Access Regulatory Compliance
– Ensure that the contract manufacturer complies with all relevant regulatory requirements, such as ISO 13485 for medical devices and FDA regulations in the United States. Verify their track record of compliance and any relevant certifications.
Flexibility and Scalability –Choose a manufacturer capable of accommodating your current needs while also having the flexibility to scale production as your business grows. This includes capacity for both prototyping and large-scale manufacturing.
Evaluate Experience and Expertise – Look for a contract manufacturer with a proven track record in producing medical devices similar to yours. Experience with relevant technologies, materials, and
manufacturing processes is essential for ensuring quality and reliability.
Location and Infrastructure – Consider the location of the manufacturer in relation to your own operations and target markets. Proximity can facilitate collaboration and reduce lead times, but it’s also essential to ensure that the manufacturer’s facilities meet your standards for infrastructure, security, and environmental controls.
Intellectual Property Protection – Ensure that the contract manufacturer respects and protects your intellectual property rights. This includes confidentiality agreements, secure handling of proprietary information, and measures to prevent unauthorised access or use of sensitive data.
References and Reputation –Finally, seek references from other clients and assess the manufacturer’s reputation in the industry. Online reviews, testimonials, and case studies can provide insights into their performance, customer satisfaction, and ability to deliver on promises.
The decision to partner with a resilient medical device contract manufacturer is not merely about fulfilling immediate production needs but also about securing a foundation for long-term success in a dynamic industry.
By prioritising factors such as regulatory compliance, supply chain resilience, quality management systems, and collaborative communication, companies can forge partnerships that endure challenges whilst fostering innovation. Investing time and resources in selecting the right contract manufacturer pays dividends in terms of product quality, reliability and market competitiveness.
As the medical device landscape continues to evolve, the resilience of manufacturing partnerships becomes increasingly vital, ensuring that companies can navigate uncertainties and emerge stronger in the pursuit of improved healthcare outcomes for patients worldwide.
As the medical device landscape continues to evolve, the resilience of manufacturing partnerships becomes increasingly vital
A selection of stories from the Med-Tech Innovation News website over the past month, hand-picked by the editor.
The report is the first of its kind to look at attitudes, perceptions and experiences of sustainability across the femtech industry.
Using data gathered from a sector-wide survey, the report revealed that nearly threequarters (72.2%) of respondents think improvements are needed to make the industry more sustainable.
Materials and circularity were cited as top challenges, alongside a lack of funding for sustainable innovation (59.1%). This is despite sustainability being perceived as a key driver for some funders and investors. One respondent commented “Investors are asking for sustainability.”
The survey on which the report is based, conducted by Sustainable Femtech Network, was designed to assess current sustainable practices among femtech, sextech and women’s health companies and to identify existing challenges.
With the femtech market set
to reach an estimated $75.1 billion by 2025, the Sustainable Femtech Network is working to promote and support sustainability across the sector.
Sustainable Femtech Network aims to drive sustainable change through research, knowledgesharing and collaboration across the industry and is open to anyone with an interest in the sector – from femtech founders and employees through to researchers, investors, suppliers and manufacturers.
The Sustainable Femtech Network is run by Oshun Labs, a women’s health innovation lab. Amy Guthrie, network
founder and Oshun Labs CEO, said: “Women’s health and sustainability are intrinsically linked. We fully support the growth of the femtech sector to improve women’s health, while promoting the integration of sustainable practices. For businesses, these goals can be complimentary, rather than conflicting.
“Femtech is a highly innovative sector, and by reporting on the sustainability challenges faced by femtech companies, we are highlighting the need for additional funding and support to implement sustainable approaches and innovations.”
IDA Ireland launches “Where next for MedTech – Key considerations for the future” report
IDA Ireland, the national development agency responsible for attracting foreign investment to Ireland, has announced the release of its MedTech whitepaper entitled Where next for MedTech –Key considerations for the factory of the future.
With insights gathered from diverse industry experts, including World Economic Forum (WEF) Lighthouse companies DePuy and Janssen along with Bausch and Lomb, Baxter Healthcare and more, IDA Ireland says the whitepaper emphasises the continued acceleration of technology disruption and the opportunity for MedTech companies to embrace digitalisation and transformation to remain agile, resilient, and sustainable in a world of ‘uncertainty and complexity.’
“The global Medtech sector is absolutely committed to saving lives and enhancing patient’s quality of life. This demands a
continuous focus on innovation, requiring companies not only keep pace with evolving patient needs but also new technologies,” said Rachel Shelly, Global Head of Life Sciences at IDA Ireland.
The whitepaper outlines how Ireland has built its reputation as an ‘exemplar’ for MedTech advancement, offering an ecosystem that IDA says encompasses innovation, focuses on talent, and is committed to supporting client sustainability and digital transformation.
One example of this according to the agency is Digital Manufacturing Ireland (DMI), a newly launched national centre
University of Birmingham scientists using novel hydrogel to create ‘lollipops’ for mouth cancer diagnostic
Researchers from the University of Birmingham have received funding from Cancer Research UK and the Engineering and Physical Sciences Research Council to create a new ‘lollipop’ diagnostic for mouth cancer using a novel smart hydrogel.
Developed by Dr Ruchi Gupta and colleagues from the School of Chemistry, the biocompatible hydrogel concentrates and labels proteins with a fluorescent marker in a single step, making it suitable for diagnostics that aim to detect low abundance proteins from small sample sizes according to the University.
The hydrogel achieves protein capture via the fluorescent marker (fluorescein isothiocyanate or FITC), which is attached to the hydrogel by a photocleavable bond. On exposure to light, the protein is released from the hydrogel.
of excellence established by the Irish Government to assist Irishbased manufacturers.
Domhnall Carroll, CEO of DMI said: “The synergy between manufacturing companies, technology firms, academia and the DMI team ensures that all the necessary components for a successful outcome are readily available, fostering a cohesive and effective collaborative environment.”
The centralisation of commercial business in Ireland is outlined in the whitepaper and contributes to operational efficiencies and economies of scale by tapping into deep and diverse talent pools.
IDA Ireland says that positioned as a globally recognised MedTech centre of excellence, Ireland emerges as a strategic location in the report, offering essential stability, talent, and an ecosystem for helping companies drive competitiveness and innovation towards the next level.
Initial studies on the gel, published last year in the Royal Society of Chemistry’s Analyst journal, showed the gel offered a concentration factor of 236 with a reference protein (streptavidin), and 50% of the proteins used in the hydrogel were released after 100 seconds exposure to UV light.
Diagnostics are a new landscape for biogels, which up until now have been used for drug delivery and tissue regeneration.
The gel developed by Dr Gupta and the team of researchers offers benefits over existing diagnostic techniques according to the university. The team says it has fewer steps than ELISA-based assays, or preconcentration using beads and electrophoresis, and can be conducted at room temperature.
Cancer Research Horizon’s, the innovation engine built to complement Cancer Research UK’s network, has filed a patent application for the novel hydrogel, and the Birmingham researchers are seeking collaborators or partners to develop further applications.
Analytical Chemistry
Comprehensive solutions for product development and manufacturing
Microbiological & Sterility Testing
Testing Experts in Identification, Quality Control, Environmental, Endotoxin, Cytotoxicity
Biocompatibility Testing
Safety and compatibility testing for all medical device classes - ISO 10993 Experts
Functional & Performance Validation
Reliable functional validation for optimal device performance to ISO 17025 standards
Packaging, Seal & Transit Testing
Ensuring intact and sterile products from shelf to patient
Devices
Devices
Devices