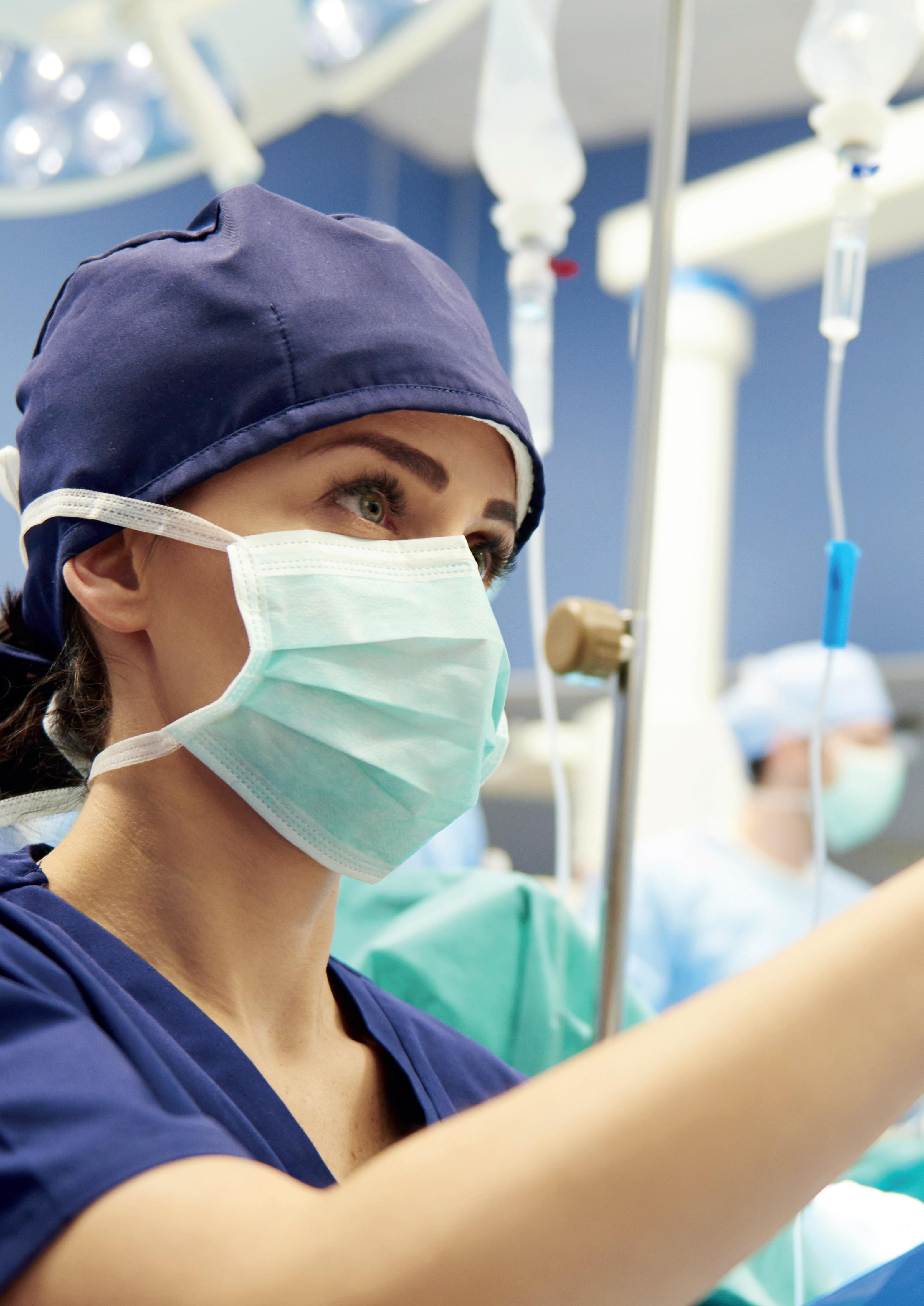

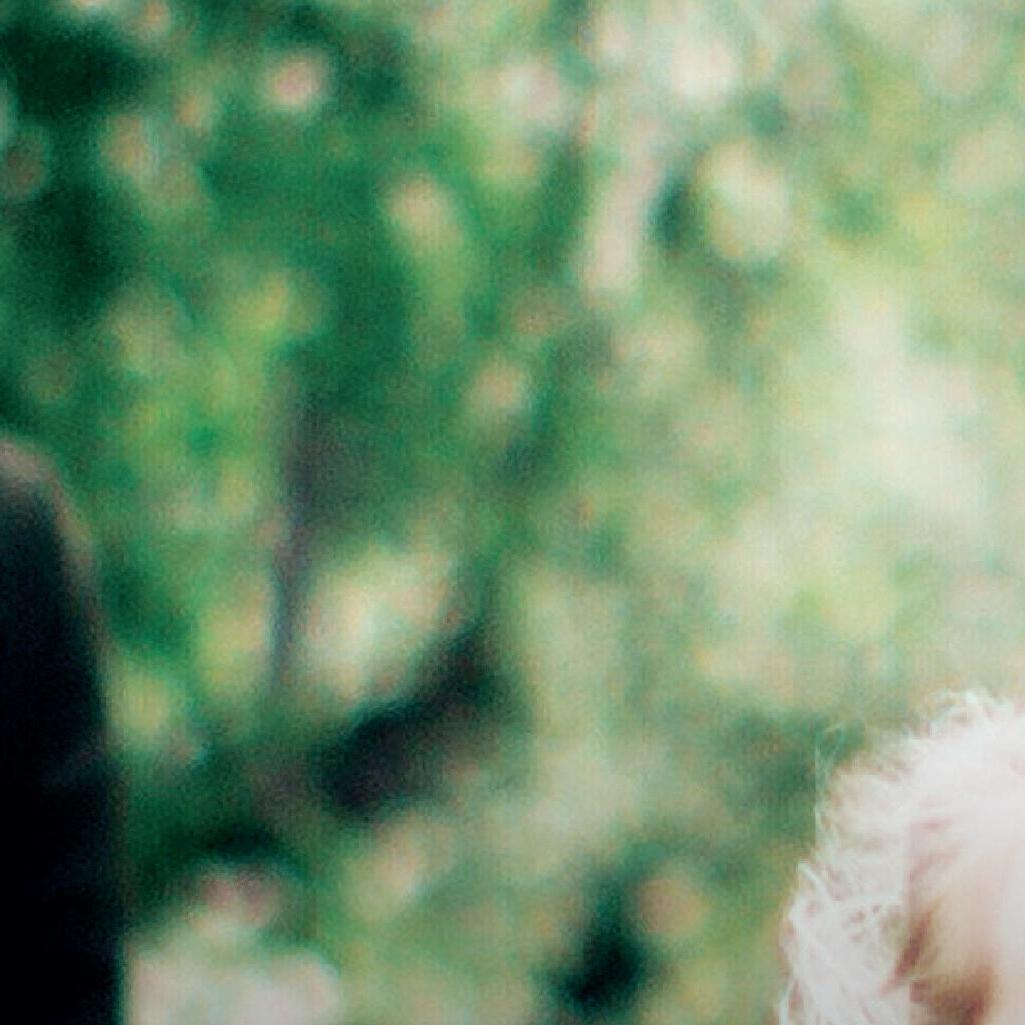
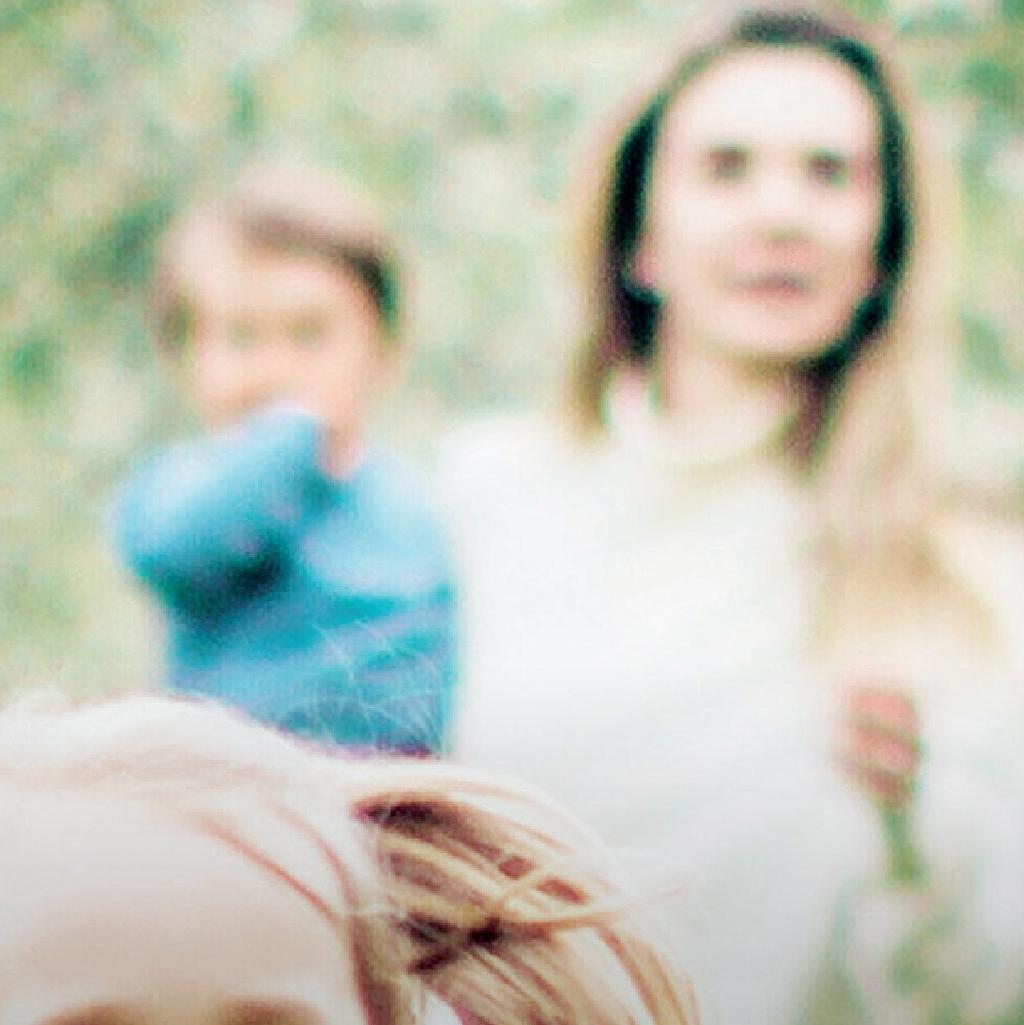
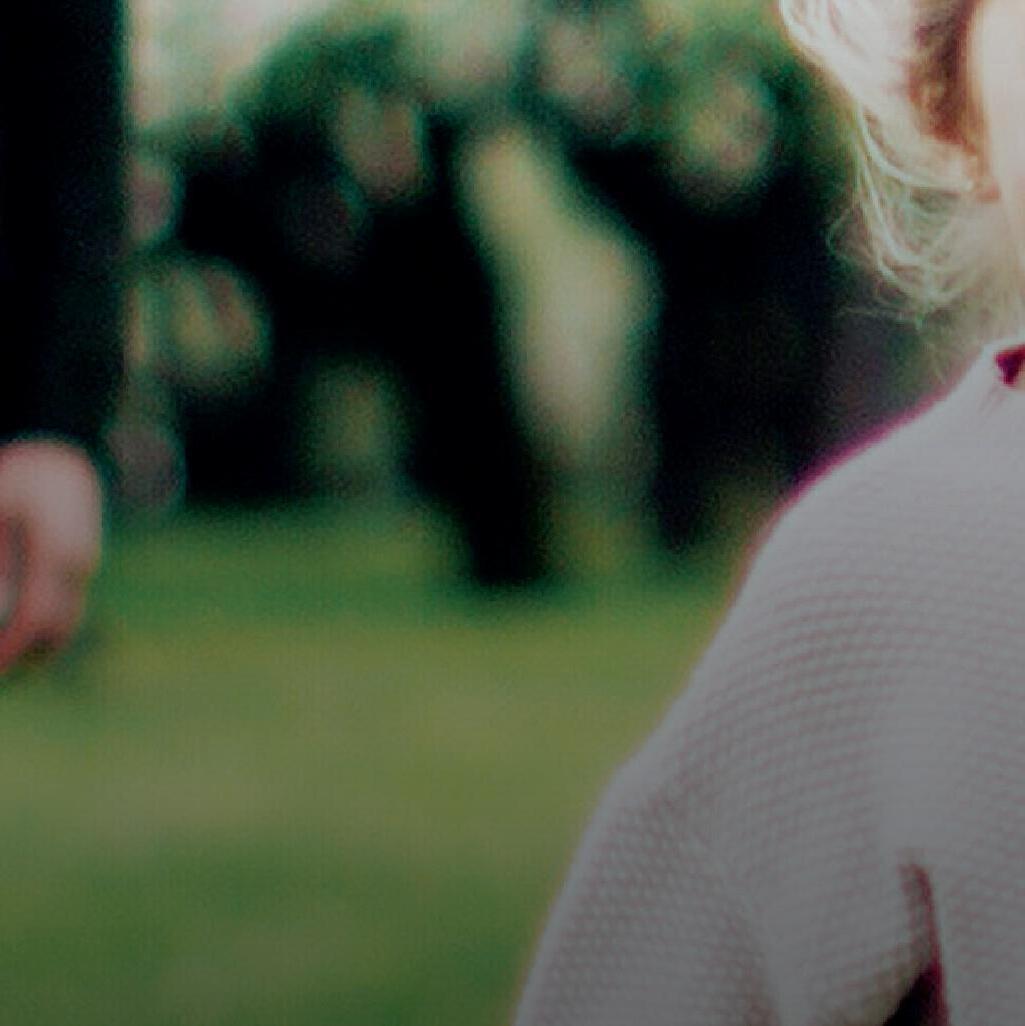
Thermo Fisher Scientific is a global leader in allergy and autoimmune in-vitro diagnostics, providing accurate and clinically relevant testing solutions to aid in disease diagnosis and patient management.
We are united under a single Mission –to enable our customers to make the world healthier, cleaner and safer.
Our approach is to enable growth and innovation within the global medical and scientific community and to help researchers, organizations, and companies solve some of the world’s most pressing issues.
We are committed to making a difference and believe creating a better tomorrow starts with the actions we take today.
editor | oliver johnson oliver.johnson@rapidnews.com
head of studio & production | sam hamlyn
publisher | duncan wood
vp sales & sales talent | julie balmforth julie.balmforth@rapidnews.com
group portfolio sales manager | caroline jackson +44 (0)1244 952 358 caroline.jackson@rapidnews.com
Rapid Medtech Communications Ltd. 3 Office Village, Chester Business Park, Chester, CH4 9QP
MTI PRINT SUBSCRIPTION –QUALIFYING CRITERIA
UK & Ireland – Free Europe – £249 ROW – £249
FREE on iOS and Android devices
Subscription enquiries to subscriptions@rapidnews.com
The Publisher endeavours to collect and include complete and current information in Med-Tech Innovation, but does not warrant that any or all such information is complete, correct or current. The Publisher does not assume and hereby disclaims any liability to any person or entity for any loss or damage caused by errors or omissions of any kind, whether resulting from negligence accident or any other cause.
Med-Tech Innovation does not verify any claims or other information appearing in the advertisements contained in the publication and cannot take any responsibility for any losses or other damages incurred by readers in reliance on such content.
All submissions are handled with care. Every precaution is taken to ensure accuracy, but the Publisher cannot accept responsibility for the accuracy of the information here.
©Rapid Medtech Communications Ltd.
No part may be reproduced or transmitted in any form without the prior permission of the Publisher.
2046-5424
Ibring to you this issue of Med-Tech Innovation fresh off my first ever trip to MEDICA & COMPAMED. What a way to immerse yourself in the medical device and medical manufacturing industry. I was only in attendance from Monday afternoon until Wednesday afternoon, but I was able to take in so much during that whirlwind three days.
The size of the event exemplifies the sheer magnitude of our industry, with companies from all over the world coming together to showcase the latest innovations in medical technologies. I was able to speak to a few companies at both MEDICA and COMPAMED, and learn about some of the innovations that were launched. You will hear from Coveris, BioInteractions, Teknor Apex, Trelleborg, Syensqo, Staiger, Accunea and Henkel, all in the MEDICA + COMPAMED review section of this issue. Keep an eye out for video interviews recorded on the show floor, coming soon.
Also in this issue, Laura Friedl-Hirst, Founder, Managing Director and Principal Consultant at LFH Regulatory discusses the main regulatory changes in the UK and the EU in what has been a year full of them, and talks about how to understand some of the main updates for both regions and understand the potential impact on businesses.
The medical manufacturing sector is continually evolving. Advancements in design techniques, manufacturing processes and materials continue to reshape the industry. Additionally, with the rise in digital technologies, particularly AI, these changes are driving regulatory transformations, creating both challenges and new opportunities.
In this changing environment, having access to accurate, timely and insights is critical.
To support you in navigating these changes, we’re excited to announce the launch of Med-Tech Insights (med-techinsights.com) in January 2025. Building on the success of www.med-technews.com and www. medicalplasticsnews.com, this rebranded platform will deliver comprehensive coverage of the latest innovations, developments and policy changes across the Sector, providing you with insights to help you stay ahead of the curve.
You’ll benefit from a modern intuitive design, with featured sections on Device Manufacturing, FemTech, Digital Health & AI and Materials. In-depth articles, exclusive video and written interviews crafted by our expert content team will focus on what’s driving the sector. Weekly newsletters will be tailored to each section, delivering essential insights directly to your inbox.
Looking ahead, Med-Tech Insights will also be live, taking the centre stage at Med-Tech Expo, the UK and Ireland’s largest Medical Device Manufacturing trade show, held in June 2025 at the NEC. At the event, we will lead the conference discussions and host live debates with the industry leaders on the pressing topics in the sector.
It’s exciting times.
Oli Johnson, Editorial Content Producer
Derek Laffey, Global Marketing Manager at Teknor Apex discusses how the company is committed to innovation and excellence in the world of polymers, and introduces the new product line that was launched at COMPAMED 2024.
08. MEET THE EXPERT
Providing direct support to the Quality Leader and company Directors, Cristina Antoniu helps to ensure that Pentagon are producing quality product with every production run.
09 & 11. MEDICA + COMPAMED review
Editorial Content Producer Oli Johnson speaks to a range of companies that launched new products or exhibited at MEDICA + COMPAMED 2024.
New pumping technologies, such as the Lee Company’s piezoelectric disc pumps, generate pressure and use a closed loop feedback system to act as an all-in-one pump and regulator solution, eliminating the need for separate compressors and regulators.
Tandem Patents works with innovative engineering companies across many different technology areas and help them obtain, manage and enforce their intellectual property rights.
Dave Walsha, Sales and Marketing Director of Electro Mechanical Systems explores the role of precise laser alignment in the development of corrective eye surgeries.
Laura Friedl-Hirst, Founder, Managing Director and Principal Consultant at LFH Regulatory discusses the main regulatory changes in the UK and the EU over the past 12 months.
16. SPONSORED – ADVANTECH
Medical imaging technology demands increasingly sophisticated and efficient hardware solutions. Integrating Advantech SQRSD5N high-end DDR5 5600 48GB SODIMM modules into these systems represents a significant leap forward in meeting these demands.
MEDTALK PODCAST
Latest updates, expert insights and feature length interviews from the makers of Med-Tech Innovation News, The Femtech Series, European Pharmaceutical Manufacturer and Medical Plastics News.
Listen for free wherever you get your podcasts
Derek Laffey, Global Market Manager at Teknor Apex discusses how the company is committed to innovation and excellence in the world of polymers, and introduces the new product line that was launched at COMPAMED 2024.
As we celebrate our 100th anniversary in 2024, Teknor Apex remains committed to pushing the boundaries of polymers. Our journey has been marked by a relentless pursuit of excellence, working closely with our customers to develop innovative solutions that advance the life sciences and medical device industries.
LEGACY OF PARTNERSHIP AND INNOVATION
For decades, Teknor Apex has been a trusted partner to the healthcare industry. Our deep understanding of the unique challenges and stringent regulatory requirements has enabled us to deliver tailored polymer solutions that meet the highest standards of quality and performance.
By leveraging our expertise in multiple polymer technologies, including polyvinyl chloride (PVC), thermoplastic elastomers (TPEs) and engineered thermoplastics, we offer a comprehensive range of materials that address a wide array of healthcare applications.
THE APEX, FLEXALLOY, AND MEDALIST FAMILIES
Our industry leading product lines - Apex, Flexalloy, and Medalist - have become synonymous with reliability and innovation. These families offer a diverse range of both general use and application-specific materials, each with its own unique set of properties and benefits.
• Apex:
Our flagship PVC brand, Apex offers the widest range of non-DEHP compounds on the market. With superior clarity, lot to lot consistency, and excellent radiation sterilization characteristics, Apex grades are ideally formulated for critical device components like IV, blood therapy, enteral feeding and airway tubing, as well as for molded components like connectors and luer locks.
• Flexalloy: High-performance PVC elastomers provide exceptional strength, durability, and flexibility for demanding medical device applications like pump segment tubing or any component demanding a higher level of performance beyond the limits of standard PVC.
• Medalist:
Our diverse families of TPEs are excellent alternatives to silicone and other high-price materials, offering flexibility and rubber-like elasticity. Medalist TPE’s offer excellent clarity and can be recycled, setting them apart from other less versatile materials.
THE MEDALIST MD-90000 SERIES: A NEW ERA OF BIOPHARMA TUBING
The recent launch of the Medalist MD-90000 Series at COMPAMED marks a significant milestone in our commitment to advancing biopharmaceutical tubing solutions. This innovative product series aims to solve a unique challenge in biopharma tubing: exceptional clarity with low spallation. For those who may be wondering what spallation means, it is the dislodging of small granules of tube material as the rollers of a pump wear away the outer wall of the tube, pass after pass. The tube breaks down due to this loss of material, causing it to weaken and eventually fail. The tiny particles of tubing that are scraped off can build up in and around the pump in a measurable
amount. Spallation can lead to tubing failure regardless of the plastic material and can create microplastics, a growing problem the industry is actively working to address.
easily recycled. In the coming months Teknor plans to release a fresh round of test data that will demonstrate the exceptional performance of MD-91760 and MD-91970 post-gamma sterilization, as well as a full package of data around burst strength, welding and heat sealing, and low temperature performance.
meet the highest standards of quality and reliability. By maintaining strict quality control measures, we deliver consistent and reliable products that meet the demanding requirements of the healthcare industry.
Our success is rooted in our collaborative approach to innovation. We work closely with our suppliers to integrate the latest advancements in polymer technology into our compounds. By leveraging their expertise, we can develop cutting-edge solutions that meet the evolving needs of the medical device and biopharmaceutical industries.
To further strengthen our partnerships with customers, we have established a network of Application Development Centers of Excellence. These state-of-the-art facilities provide a collaborative environment where customers can work side-by-side with our technical experts to develop and optimize their products. Equipped with advanced processing equipment, our centers allow customers to test their formulations and applications under real-world conditions, accelerating time-to-market.
Our commitment to quality is unwavering. Our world-class quality laboratories are staffed with highly skilled technicians and equipped with advanced testing equipment. From mechanical testing to chemical analysis, we rigorously evaluate the performance of our materials to ensure they
The healthcare industry is subject to a complex and ever-changing regulatory landscape. One significant development in recent years has been the global phase-out of Di(2-ethylhexyl) phthalate (DEHP) due to concerns about its potential health risks.
Most low-spallation materials are opaque, meaning designers are forced to make a tradeoff when it comes to pump tubing material selection whereby clarity is sacrificed for spallation performance. Working closely with a key supplier, Teknor’s R&D team iterated through various formulation cycles to land on two new grades that offer industry-leading spallation performance coupled with unbeatable clarity. The MD-91760 and MD91970 set a new standard for TPE tubing materials, meeting the highest level of pump performance without sacrificing clarity and avoiding the wear and failure observed with previous generation TPE products. In addition, these compounds offer improved compression set and, unlike silicone, can be
Teknor Apex has been at the forefront of this regulatory shift, developing innovative, non-DEHP formulations that meet the stringent requirements of the healthcare industry. By leveraging our deep understanding of polymer science and our strong relationships with suppliers, we have been able to successfully transition our product portfolio to comply with these new regulations.
Our regulatory team has worked tirelessly to ensure that our products meet the latest standards and certifications. By staying ahead of the curve, we have helped our customers avoid costly product recalls and regulatory compliance issues.
As we look to the future, Teknor Apex remains committed to driving innovation and delivering superior polymer solutions to the healthcare industry. By leveraging our deep expertise, collaborative approach, and unwavering focus on quality, we will continue to shape the future of healthcare for generations to come.
Cristina has had a pivotal role within the quality team at Pentagon for over 4 years. Initially joining as a Quality Inspector, the sharp eye for detail and meticulous approach to investigation and issue resolution has seen her role develop into a Quality Analyst. Working closely with the production team her hands on approach combined with her high level of commitment to drive forward the quality of the products we produce is commendable. Providing direct support to the Quality Leader and
company Directors, Cristina helps to ensure that Pentagon are producing quality product with every production run.
Working in line with the ISO9001:2015 certified quality management system, quality is at the very heart of Pentagon’s manufacturing processes. Unique in the offering of both full mould tool manufacture and volume production from one site of UK Manufacture you can be confident that your components will be produced to exceptional standards.
● Ultra thin bio compatible protection
● Outstanding chemical, moisture and electrical barrier protection
● High lubricious dry film conformal coating
● Metals, Elastomers, Electronics and Plastic
● Proprietary Dimer is 99.7% pure
● CW Parylene: USP Class VI and ISO10993 tested
● MAF No. 1176 on file with the FDA
www.pentagonplastics.co.uk
websales@pentagonplastics.co.uk
Editor Oli Johnson provides a round-up of some of the launches from this years MEDICA and COMPAMED shows in Düsseldorf.
Sustainable packaging company
Coveris announced the launch of its new brand at COMPAMED 2024. It said that following extensive investments in its medical production facilities, it would consolidate its capabilities and medical offerings under one brand name, MediFlex. The company says that the establishment of the brand distinguishes its medical portfolio from other non-food applications, reflecting the heritage of its Rohrdorf and Halle sites as leaders in the medical packaging field. The company says that all medical packaging is produced using renewable electricity, embodying its commitment to its ‘No Waste’ principles.
Jan-Willem Bruijsten, Segment Director Medical, Coveris told MTI: “MediFlex is not new, it is the Coveris healthcare division, which has been around for 45 years, so it’s an established product line. Now with the MediFlex brand, we gave it a new name, but it’s the same people, same product.”
UK biomaterial company
BioInteractions announced the launch of its new surface active therapeutic coating for medical devices, AstutePlus. The new development is based off of the company’s Astute technology, which it says is the strongest antithrombogenic coating, highest efficacy, and most effective antithrombogenic coating in the world. The efficacy of the coating can be sustained for decades at a time,
with the most recent results showing that the efficacy can be maintained for over 30 years, meaning that implants can be placed for the lifetime of a patient.
With AstutePlus, fibrin sheath can be completely prevented from forming. With CVC catheters, there is around a 70% failure rate because of fibrin sheath alone. AstutePlus offers the ability to prevent clots, deactivate the blood, prevent a fibrin sheath from forming, ensure that nothing grows on the outside of the device, and ensure that the efficacy is maintained for as long as is needed.
Arjun Luthra, Commercial Director of BioInteractions said: “If we need to put an implant into a patient for years or decades at a time, we are comfortable to do it because of the AstutePlus solution.”
Leading up to MEDICA 2024, adhesives giant Henkel announced a partnership alongside polymer specialist Covestro and flexible printed electronics manufacturer Quad Industries. The companies aim to accelerate customer developments for advanced medical wearables and to drive the adoption of innovative printed electronics solutions, especially for stretchable materials in healthcare applications. At the show, the company was presenting a range of products including printed
sensors for diagnostics and hygiene, medical wearables, medical heaters and antennas for medical wearables at the Wearable Technologies pavilion. The partnership was highlighted by the presentation of a patch demonstrator, an ECG pad for continuous patient monitoring of heart activities.
Pia Schmiedel, Business Development Manager – Printed Electronics, Henkel talked MTI through some of the medical patches that have been created through the collaboration: “We at Henkel are the material supplier for these types of medical patches, we are supplying skin adhesives and the conductive inks, so all the printed electronics which go into it, which could be silver chloride inks, silver inks and dielectrics, which are printed in a screen printing process.”
Syensqo made its COMPAMED debut at the 2024 show, showcasing its range of high-performance polymers for the healthcare and pharmaceuticals industry. The company is known for its Zeniva PEEK material, and was presenting a new application featuring the material at the show from its partner GLW Medical Innovation. At the booth, visitors were able to get a close look at implantable fracture plates that were 3D printed in titanium, then reinforced with Zeniva PEEK.
Federico Baruffi, Global Marketing Manager at Syensqo said: “This is an exceptional application because you combine the properties of metal and the properties of plastics. Our material here brings lightweighting, and also the possibility to increase the radiolucency, it is possible to see through this sample in an MRI for example. What we bring is exceptional biocompatibility, but more specifically also the strength. So the material being reinforced with carbon fibre and implantable, we can make sure that it is stiff enough to fixate the bone without risk of breakage.”
operated fixed volume dispense pumps
The pumps feature a revolutionary port head design that allows tubing connections and manifold mounting This enables the designer to test the fluidic system using connections to soft tubing, and then once the system design has been finalized, the same pump can be manifold mounted using standard O-rings
The electrical interface of the pumps feature a contoured end cap that provides secondary connector retention and is compatible with standard AMP connectors
● 12 or 24vdc
● 10, 25, 50, 100 or 175μL dispense per Shot
● Inert wetted materials
● Low power consumption
ontrolling & dispensing precise volumes of fluid, down to the microliter and nanoliter range, is a common challenge in production processes. Whether you’re designing a high throughput production line for lateral flow assays, consumable manufacturing, drug discovery or inkjet printing, the success of the system is often based on control of three main variables: pressure, nozzle or orifice precision, and valve speed.
INKJET PRINTING –CONTROLLING THE MENISCUS
Within inkjet printing, the quality of the print output hinges on the precision with which ink droplets are formed and land on the substrate. Controlling the geometry and
stability of the meniscus, that is, the surface curve of the ink droplet when in contact with the nozzle, is most critical for proper droplet formation and jetting.
Too high a vacuum can lead to air ingestion and starvation, while too low a vacuum can result in nozzle plate flooding or ‘wetting-out’. Pulsatility in the ink reservoir can lead to periodic changes in print output.
Many current systems use a motor-driven diaphragm pump to provide the negative pressure in the ink reservoir. Such pumps are pulsatile and offer limited controllability, meaning that additional components such as pulsationdampers and proportional valves are required to achieve acceptable printhead performance.
The pulsation-free output
of the Lee Company’s piezoelectric disc pumps and their infinite turn down ratio ensure there is no pressure variation in the printhead, eliminating the need for those additional components. At just 29 mm in diameter and 5 grams, the disc pump is small enough to be directly integrated with the printhead.
PRECISION REAGENT DISPENSING - TIMEMETERED DOSING
The consistent control of dispensed fluid volume, or droplet size, is a critical factor when dispensing reagents in the production of lateral flow assays or rapid diagnostic tests.
For these types of applications, time-metered dosing systems offer simplicity while providing accurate liquid dispensing across a wide
range of dispense volumes –from nanoliters to millilitres. Manufacturing tolerances of the orifice can lead to differences between various dispensing channels. Burrs can lead to splitting streams or unwanted satellite droplets. The speed, or response time, of a dispense valve controls how quickly fluid is ejected from a nozzle, and how little fluid can be dispensed at a time. A faster actuation speed creates more predictable dispenses because flow starts and stops very quickly.
New pumping technologies, such as the Lee Company’s piezoelectric disc pumps, generate pressure and use a closed loop feedback system to act as an all-in-one pump and regulator solution, eliminating the need for separate compressors and regulators.
Teknor Apex, provider of custom plastic compounds for the healthcare industry, announced the expansion of its medical-grade thermoplastic elastomer (TPE) portfolio, with new grades specifically designed for biopharmaceutical tubing applications. Derek Laffey, Global Market Manager, told MTI about the new materials, the MD-90000 Series, from the Medalist line: “They offer a lot of very diverse qualities and application opportunities. In biopharma tubing we specifically chose to develop a new series aimed at solving several problems encountered in the biopharmaceutical tubing space, one of which is spallation.”
Laffey added: “These are leading-edge, next-generation TPE materials for biopharmaceutical transfer tubing and pump segment tubing. The additional benefit is that the material offers exceptional clarity, not only can you greatly reduce the occurrence of spallation, but you can also greatly improve the clarity of the tube. We think that this is an evolutionary step in TPE materials used in pump segment and fluid transfer for biopharmaceutical manufacturing.”
Staiger, a German company developing and producing customer-specific solenoid valves and fluidic manifolds at its plant in Erligheim, showcased its latest production innovations, the ‘world’s smallest’ electronic pressure regulator with integrated solenoid valves, ‘the first’ proportional solenoid valve with a metal membrane, and a
media-isolated microvalve with a 5mm outer diameter. Andreas Genesius, Managing Director & CTO at Staiger told MTI: “This year at COMPAMED we launched our brand-new 5mm media-separated valve, which is the perfect valve for dispensing for any IVD application. We can go down to droplets that are 30-40 nanolitres, but we can also dispense micro and millilitres with that valve.”
At COMPAMED 2024, polymer specialist Trelleborg showcased its entire line of manufacturing capabilities, which can all be customised as per customer requests. At the show, MTI spoke to Trelleborg about its global network, which allows it to serve customers around the world.
Florance Veronelli, Sales Manager, LifeScience Solutions at Trelleborg told MTI: “We have large facilities in China and Australia, and also an expanding footprint in Europe, as well as experts all over the world in engineering to make sure that we have the right design for manufacturability to find an efficient process and everything under the roof of one quality management system. With that, we can really make sure that the customer receives the same quality that they require everywhere in the world.”
Linda Muroski, Business President for Trelleborg Medical Solutions added: “I think from our customer perspective, our customers are really looking to make sure that they have in country for country or in region for region, after COVID, and the supply chain constraints everyone had, this (the global network) has been very important to them. Sometimes you’ll hear a customer say they want a dual source, because they don’t want to have all their products produced in your factory in whatever city. So what we’re able to do is to create a second source in a different region completely,
so there’s this big separation for them. I think that oftentimes allows us to be the single source for the customer, but doing it in multiple regions, so they have that supply chain continuity.”
Accunea Ltd. presented its new multifunction biosensor at COMPAMED. The company is aiming to halve the 1-in-5 donated kidneys that go unused because of a lack of objective viability assessment technologies.
“Few people realise that Chronic Kidney Disease kills more people than cancer” Dr. Robert Learney, CEO of Accunea told MTI.
Accunea Ltd. has collaborated over the past year with a selected group of experts in biosensing and microfluidics, coordinated by the EU Microfluidics Hub.
“Working alongside best-in-class companies across Europe including BiFlow Systems, Jobst Technologies, Micronit and Joanneum Research has really unlocked our ability to deliver actionable insights at the point of care for transplant surgery,” Learney added.
Accunea is currently fundraising to assess RenoSure in a human study at one of Europe’s busiest transplant units. They are supported by leading surgeons at the UK’s largest transplant centres, and a growing number across Europe, who see RenoSure’s potential to improve clinical decision-making and increase transplant numbers.
Learney said: “The first version of our sensor showed excellent results in a small human study, but we identified a number of technical challenges which our partners have since managed to solve. By showcasing this device at COMPAMED, we aim to inspire potential partners and investors to come and open new conversations around transforming pre-transplantation organ assessment and organ availability.”
Tandem Patents was founded in 2016 by Chartered mechanical engineer and qualified UK & European patent attorney, Adrian Sewell.
We work with innovative engineering companies across many different technology areas, particularly medical devices, and help them protect and commercialise their intellectual property (IP) rights whilst navigating any competitor IP rights.
We are based near Leeds in Yorkshire so are well-placed to serve the UK and we have consultants in York, Harrogate, and Ireland. A trusted and well-established network of overseas attorneys ensures we can also support our clients’ needs internationally in all major jurisdictions.
Our key focus is to provide a professional, commercially minded, and practical service, whilst maintaining a friendly, honest, and transparent relationship with our clients.
Whether you are seeking to protect a new product or process, avoid infringing or invalidate a third-party patent, and/or reduce your corporation tax, we would be delighted to hear from you.
Dave Walsha, Sales and Marketing Director of Electro Mechanical Systems explores the role of precise laser alignment in the development of corrective eye surgeries.
According to UK Biobank data, around 4% of the UK’s population has had laser vision correction (LVC) since the nation’s first laser eye surgery was carried out in the late 1980s. In the years since, there have been significant improvements in LVC effectiveness, healing times and safety. Due to its relatively low risk and high success levels, LVC has become one of the most popular elective surgeries, with conservative estimates suggesting over 100,000 Brits undergo the procedure each year.
As well as correcting vision problems such as short-sightedness (myopia), long-sightedness (hyperopia) and astigmatism, laser eye surgery can also be used to treat more serious conditions that can cause blindness. These include diabetic retinopathy and complications after cataract surgery.
THE BEGINNINGS OF LVC
In the three and a half decades since the UK’s first LVC procedure was undertaken, the methods used have greatly evolved.
Early procedures involved mechanical microkeratomes, which are surgical instruments with an oscillating blade used to create a thick, hinged flap in the cornea during laser eye surgery. The ophthalmologist would then lift the flap and correct the patient’s vision using a laser to reshape the corneal tissue. While safe, the procedure can be uncomfortable for the patient and is prone to complications stemming from the way the cornea is cut. For example, if the flap is too thick, this can cause the cornea to bulge forward, leaving the patient with suboptimal vision.
Mechanical microkeratomes may also suffer from power losses and the jamming of mechanical parts. While these devices have advanced in recent years, microkeratomes are now much
less widely used in LVC surgeries than they once were.
FEMTO FIRST
Today, the most common LVC method uses a femtosecond laser. Named after its laser pulses that last only a femtosecond (10-15 seconds), the laser technology paved the way for Femto Laser-Assisted in Situ Keratomileusis (LASIK) procedures. Femto LASIK allows for precise and predictable flap creation, with the vision correction then conducted using an excimer laser. The short duration of the laser’s pulses means that creating the flap takes around ten seconds per eye, increasing patient comfort when compared with mechanical microkeratome LVC. Femto LASIK can also improve healing times due to its less invasive nature.
In recent years, small incision lenticule extraction (SMILE) has also emerged as an alternative. Although this procedure is currently only suitable for patients with myopia or astigmatism, it still offers several benefits. For patients with dry eyes, thin corneas or higher levels of myopia who would not be eligible for LASIK surgeries, SMILE offers a viable option since it does not involve the creation of a flap.
Instead, the ophthalmologist uses a femtosecond laser to carve a sixmillimetre disc of corneal tissue, which is then removed through a two-to-fourmillimetre keyhole incision made by the same laser. The elimination of the potential complications caused by the corneal flap allows patients to resume
physical activity more quickly than with Femto LASIK.
STEPPER MOTOR SUPPORT
Be it Femto LASIK or SMILE, none of the modern methods of laser eye correction would be possible without motor-controlled femtosecond laser alignment. When it comes to moving the prisms, filters and mirrors that allow for precisely defined and rapid pulses, stepper motors are the ideal choice.
Stepper motors differ from other motor types, such as servo motors, in that they can operate with high precision even in an open-loop control system. This means that an encoder is not required, simplifying both the electrical and software configuration required for an accurate drive system. Stepper motors have exceptional stopping accuracy and responsiveness, making them well suited to applications that demand high levels of precision, including LVC microsurgeries where optical components need to be positioned and aligned.
To ensure high motion control performance, there are several things to consider before selecting a stepper motor. In order to function effectively without an encoder, the chosen motor should match the application’s size and rating requirements. You should also think about the application’s required step resolution, power supply and speed profile.
EMS is a leading supplier of FAULHABER Precistep motors, which range from six to 66 millimetres in diameter. Precistep motors can hold their position even when the power supply is turned off, thus avoiding the earlier issue faced by mechanical microkeratome procedures during power loss. Their long service life also means that ophthalmologists needn’t worry about reduced equipment performance or downtime.
With around half of the global population predicted to be myopic by 2050, femtosecond-based laser eye surgery is likely to continue growing and evolving. Precise motion control is essential not only to improve the effectiveness of the procedures, but also to ensure their safety.
In
Drive
Webinars
Laura Friedl-Hirst, Founder, Managing Director and Principal Consultant at LFH Regulatory
discusses the main regulatory changes in the UK and the EU over the past 12 months.
The requirements for medical device and in vitro diagnostic are constantly evolving, especially with changes such as the United Kingdom’s (UK) departure from the European Union (EU) following Brexit and the introduction of Artificial Intelligence (AI). Keeping up with compliance requirements can be daunting for those developing or selling such products for the EU and UK.
This year has seen numerous regulatory changes and updates, highlighting the lack of regulatory structure in the UK and the publication of many Medical Device Coordination Guidance (MDCG) documents to help manufacturers navigate and comply with EU legislation where regulations have been unclear.
As we approach the end of 2024, it is crucial to reflect on some of the main changes for both regions and understand the potential impact on businesses.
In January, the UK introduced legislation allowing CE-marked medical devices to be placed on the Great Britain (GB) market. Transitional timeframes for accessing the GB market with CE marked devices are as follows:
• General Medical Devices compliant with the Medical Devices Directive 93/42/EEC (MDD) or Active Implantable Medical Devices Directive 90/385/EEC (AIMDD) with a valid declaration and CE marking can be placed on the market until the sooner of the certificate’s expiry or 30 June 2028.
• IVDs compliant with the In Vitro Diagnostic Directive 98/79/EEC (IVDD) can be placed on the market until the sooner of the certificate’s expiry or 30 June 2030.
Medical imaging technology demands increasingly sophisticated and efficient hardware solutions.
Integrating Advantech SQR-SD5N high-end DDR5 5600 48GB SODIMM modules into these systems represents a significant leap forward in meeting these demands. The primary objective of this project is to enhance the performance, reliability, and capacity of medical imaging systems, ensuring they can handle the intensive workloads and large datasets generated during imaging processing.
Medical imaging systems require substantial processing power and memory bandwidth to handle complex computations and large data transfers. High-end imaging techniques generate especially massive amounts of data, causing memory to struggle when capped at 32GB, leading to limited processing times and potential data bottlenecks. In addition, a long-lasting solution is essential for this project. Our solution is built with original Micron ICs to ensure robust longevity, which is crucial for medical devices.
Medical image systems, such as CT scanners and ultrasound machines, have revolutionised diagnostics by providing detailed internal views of the human body, facilitating early and accurate diagnosis of various conditions. To meet the growing demands of these systems, there is a continuous need for high-performance, high-capacity, and highreliability DRAM solutions.
systems.
This
Leveraging the high-speed 5600MT/s and 48GB capacity of DDR5 memory, this project aims to significantly enhance the performance of medical imaging systems. This upgrade enables faster processing of large datasets and real-time image rendering. The built-in PMIC and on-die ECC functions of the DDR5 5600 prevent data corruption, ensuring the integrity of medical imaging data.
48GB,
Additionally, this project requires a durable solution, and the DDR5 5600 48GB, built with original Micron ICs, ensures high quality and longevity.
Integrating SQR-SD5N DDR5 5600 48GB SODIMM memory modules into high-end medical imaging systems strategically addresses existing performance and capacity challenges. Leveraging the advanced features of SQRAM, such as DRAM longevity support and customisable solutions, this project ensures that medical imaging systems can meet the rigorous demands of modern diagnostics. Ultimately, this enhancement aims to improve patient care and operational efficiency.
• Industrial-Grade Micron ICs with lifetime warranty
• On-die ECC error correction mechanism, enhancing reliability
• 30μ″ chamfer edge gold fingers
• 24-hour high-low temperature and humidity test
• Conformal coating & sidefill (optional)
• Wide operating temperature range (-40 ~ 95°C) (optional)
• Free SQ Manager 2.0 Software to monitor DRAM health status and overheating alerts
CONT FROM PAGE 15
• General Medical Devices and IVDs. Medical devices including custommade devices, compliant with the EU Medical Device Regulation 2017/745 (MDR) and IVDs compliant with the In Vitro Diagnostic Regulation (IVDR) can be placed on the market until 30 June 2030.
Additionally, Class I medical devices and general IVDs under the MDD or IVDD, which did not require a notified body for conformity assessment, can only be placed on the Great Britain market if a notified body would be required under the EU MDR or IVDR.
But why has this happened and what does this mean for organisations with existing CE marked devices?
Extended Market
Access:Manufacturers will have more time to transition to the new UK regulations whilst still being able to sell CE-marked devices.
Planning and compliance: Currently, there is only draft text for Post Market Surveillance requirements (SI 2024), and there is no clear understanding of what the regulation will look like under UK legislation. This situation allows the UK to establish the necessary regulations in a timely manner while giving manufacturers time to transition as needed. This approach ensures that manufacturers can continue to supply the GB market with devices without causing a disruption in supply.
On 21st May, the Medicine and Healthcare Products Regulatory Agency (MHRA) published its ‘Statement of policy intent: international recognition of medical devices”. This policy is intended to allow medical device manufacturers to use device clearances in other regulatory jurisdictions to ease entry to the Great British market by recognising other international regulators’ approvals.
Such recognition is intended to be available for devices with clearances in Australia, Canada, the EU, and the USA, with certain exceptions but has not yet been confirmed.
Most recently in November, the MHRA published a new consultation “Medical Devices Regulations: Route to market and in vitro diagnostic devices” for the GB market with the aim to seek views from stakeholder on the following four key areas until 5th January 2025:
1. International Reliance: Medical devices and IVD’s can use the UKCA (UK Conformity Assessed) process to access the GB market either by self-certification for low-risk devices, or by conformity assessment and certification by an Approved Body. There is future scope to enable the UKCA process to be complemented by the international reliance scheme to enable market access for devices already approved in comparable regulated countries.
2. UKCA Marking: Remove the current requirements for devices which undergo the UK conformity assessment process to bear a UKCA Marking.
3. In Vitro Diagnostic Devices (IVD): Updates to the classification to proportionately regulate IVD devices according to their risk.
4. Assimilated EU Law: Remove the revocation date of four pieces of assimilated law to avoid disruptions. This proposal, alongside more specific transitional provisions –would ensure a smooth transition to a future regulatory framework, which aims to protect patient safety, improve access to innovative medical devices, and support innovation.
In summary, the MHRA’s consultation reflects GB’s intention to adopt international recognition in its medical device regulations. By seeking feedback from key stakeholders, the aim is to streamline market access for manufacturers, making the process quicker and more efficient. This approach not only supports the introduction of innovative technologies but also ensures that patients benefit from the latest advancements in medical devices.
On 9th May, the MHRA introduced the AI Airlock and regulatory sandbox for AI as a Medical Device (AIaMD). This
pilot project aims to help the MHRA identify and address the challenges of regulating standalone AIaMD.
The regulatory sandbox model was established because AI technologies are difficult to test using traditional trial methods. The AI Airlock project’s collaborative approach is designed to identify and manage evidence requirements more effectively, to support areas such as data gathering and validation using real world data from within the NHS.
The insights gained from collaboration between the government, regulators, and industry will guide future AI Airlock projects and shape both UK and international AIaMD guidelines. The results of the pilot will be used to help develop forthcoming guidance and principles around proportionate regulation of AI within medical devices. This includes working with Approved Bodies on UKCA marking and partnering with trusted regulatory bodies for international recognition of medical devices.Top of FormBottom of Form
The European Union (EU) is also considering the advancements of technology by adopting the AI Act 2024/1689 which is a legal framework specifically for Artificial Intelligence. Although the AI act has not been created with medical devices in mind, there is a need to consider this with devices incorporating an AI aspect. The key date for implementation is 2nd August 2027 for AI medical devices.
The AI Act focuses on several key areas to regulate artificial intelligence effectively:
1. Risk-Based Approach: It categorises AI systems based on the level of risk they pose, ranging from minimal to high risk level, this ensures that higher-risk AI systems are subject to stricter requirements.
2. Conformity Assessment and Certification: AI systems must undergo rigorous conformity
assessments and obtain certifications to ensure they meet the required ethical and safety standards.
3. Transparency and Accountability: It mandates that AI systems be transparent about their operations and decisions which includes providing clear information about how it works and any potential impacts.
4. Human Oversight: AI systems consider high risk must include mechanisms for human oversight to ensure they can be monitored and controlled by humans to prevent unintended consequences.
5. Data Governance: It emphasises the importance of high-quality data for training AI systems.
6. Enforcement and Penalties: It establishes enforcement mechanisms and penalties for non-compliance, ensuring that AI developers and deployers adhere to the regulations.
Regulation (EU) 2023/607 sets out the requirements of manufacturers to extend their certification under the MDD and AIMDD certification. The extended transitional timeframes looked to assist notified body with ever struggling resource as well as the time and cost constraints to manufacturers. Extended timeframes are as follows:
31 December 2027 – Class III and IIb implantable devices excluding sutures, staples, dental fillings, dental braces, tooth crowns, screws, wedges, plates, wires, pins, clips and connectors;
31 December 2028 – All other class IIb devices, class IIa device and Class I devices placed on the market in a sterile condition or having a measuring function.
The deadline for manufacturers to apply for the extension has now passed (24th
May 2024) with the signed Notified Body agreement by 24th September 2024. Any manufacturer who missed these deadlines or those who are bringing new devices to market will need to comply with the new regulations.
As a consultancy, one of the main questions we are commonly asked is the costs associated with Notified Body accreditation. Earlier this year, the European Commission provided a useful list of Notified Bodies fee lists. This should aid manufacturers to understand approx. costings to get through the certification process.
Throughout 2024, both markets have undergone numerous changes, with no signs of slowing down. These developments reflect the ongoing preparation for advancements in healthcare technologies, particularly in software and AI. They also emphasise the importance of staying current with the regulatory landscape to ensure compliance and foster innovation.
Dymax adhesives, sealants, coatings, gaskets and encapsulants for medical device assembly offer:
• ISO 10993 certication
• Cure in seconds
• Quality assurance features including Encompass™ for visible cure and placement veri cation
• A wide range to choose from; nd the most suitable for your substrates and application
• Technology from a global leader in UV curing materials and systems
In addition to materials, we offer matched application and curing equipment for a complete process.
Find out more from Dymax’s most experienced distributor in Europe. 01865 842842
info@intertronics.co.uk intertronics.co.uk
A Global Technology led Contract Manufacturing business with ISO 13485 accredited facilities, and FDA 21CFR820 and MDR compliant.
Offering:
• Product Design, Development and Process Optimisation
• ISO 14644 accredited Cleanroom Class 7 & 8 assembly and production production
• Ensuring regulatory compliance
• Accelerated time to market supported by our global innovation centers, focusing on design, innovation and sustainability www.rosti.com
Innovative solutions engineered to your specific requests. Working together to create quality medical products that enhance lives.