
2 minute read
Testing playground surfaces
PUT ANY CHILD on a play structure and often one of the first things they will do is climb to the top.
Through this they get to experience risk taking, learn climbing skills, and explore their physical range of motion. However, research suggests that playground equipment is associated with nearly one third of falls to children requiring hospital admission and a recent report from Safekids, the national child injury prevention service, states that falls from heights greater than 1.5 metres increase the risk of injury to 4.1 times that of falls from 1.5 metre heights or lower.
The standards governing the safety of play equipment and safety surfacing are NZS 5828:2004, which specify the requirements for surfacing to be used in children’s playgrounds and specific requirements for areas where impact attenuation is necessary. It recommends the factors to be considered when selecting playground surfacing and gives a method of test by which impact attenuation can be determined – this test gives a critical fall height for surfacing.
The Ministry of Education’s Property Handbook states “The design and maintenance of play areas and playground surfacing is covered by NZS 5828:2004, Playground Equipment and Surfacing. It is a ministry requirement that school playgrounds meet these standards.”
Standards New Zealand has also introduced two handbooks to assist schools in achieving compliance with the Standard – SNZ HB 5828.1:2006, General Playground Equipment and Surfacing Handbook and SNZ HB 5828.2:2006, Supervised Early Childhood Facilities –Playground Equipment and Surfacing Handbook.
Under the standards, all school playgrounds are required to have safety surfacing within the fall area of the play equipment.
33
The schedule should list all components that require inspection and the methods of how to carry this out. If you discover a defect that would put safety at risk, it will need to be corrected without delay.
Standards NZ has produced a guide – SNZ HB 5828.1:2006 General Playground Equipment and Surfacing Handbook – that provides a number of inspection checklists based on a risk management framework, to identify and address potential hazards and playground risk and assist in establishing inspection and maintenance processes.
Those conducting tasks on playgrounds such as inspections, maintenance or repairs should be competent to reduce accidents and risks.
If you want to bring an older playground up to the current safety standard levels, there are a number of qualified auditors in New Zealand that have been trained to the recognised Royal Society for the Prevention of Accidents (ROSPA) Level 3 or equivalent grade of compliance. These inspectors are trained to recognise the types of accidents that can occur in a playground and can assist in identifying problem areas and completing relevant documentation.
Likewise, if you are in the market for a new play structure, it is essential that the structure is certified to the correct level of compliance – NZS 5828:2004 – which stipulates that play structures need to be safe and covers head and limb entrapments, fall and impact types and the fall zones surrounding activities and structures. Carrying out regular inspections and undertaking maintenance as necessary can help to ensure your playground is safe for years to come.
By Michael Cox, sales and marketing manager, Playground Centre
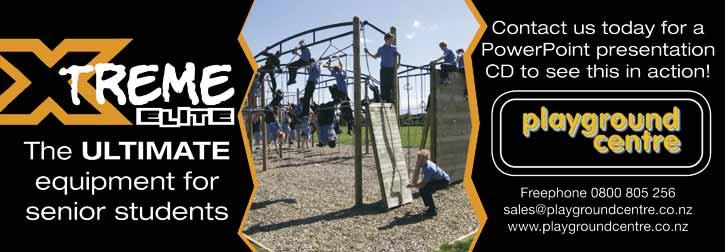