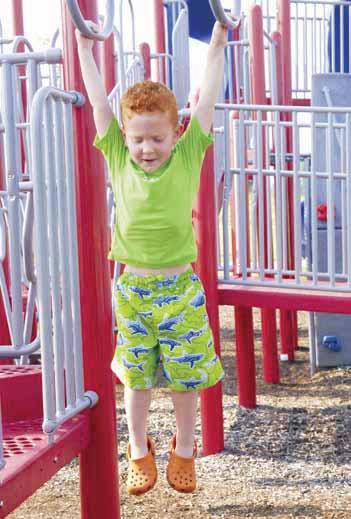
1 minute read
Maintaining a safe playground
The safety material used is required to meet the NZS5828:2004 for the height of the equipment, and to have been certified to meet that standard.
There are a variety of materials available which provide impact attenuation, including rubber tiles, mats, slabs, continuous synthetic surfacing (either prefabricated or formed in-situ), and loose particles such as gravel, sand, wood chips or bark.
For loose fill systems your surfacing provider should provide a certificate of compliance and stipulate the depth required to comply with NZS 5828:2004.
If installing a rubber wet pour system, the supplier should provide a certificate of compliance. A further site test will be required following installation because of the variation in depth when laying, unless the rubber wet pour is laid on a certified shock pad.
Surface impact testing imitates a fall that a child may have that impacts the head.
The test method uses a Triax 2000 device which measures the head impact criteria from specific fall heights, tested as specified in the standard. When testing the impact capability of the surface, the maximum height of the equipment is used to determine if the surface complies with that equipment.
The maximum fall height under NZS 5828:2004 is three metres and your compliance certificates should state what height the surface should meet.
Over time these surfaces do break down through environmental factors, and general wear and tear. Schools should periodically test these surfaces to determine if they still meet the critical fall height.
Maintenance of playground surfacing is important to ensure correct depths are maintained and that the surface is in good condition and free from foreign objects. Manufacturers are required to provide maintenance information for the surface they supply.
However, testing your playground surface can ensure your play facility continues to adhere to the New Zealand Playground Standard.
By Philippa Bollond, Future Landscapes.
Playgrounds at their very best!
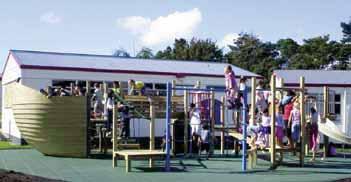