
4 minute read
3 LCAmethodology
3.1
Declaredunit
Advertisement
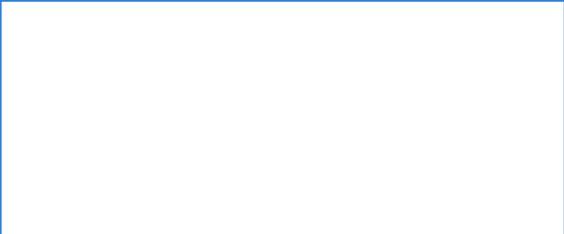

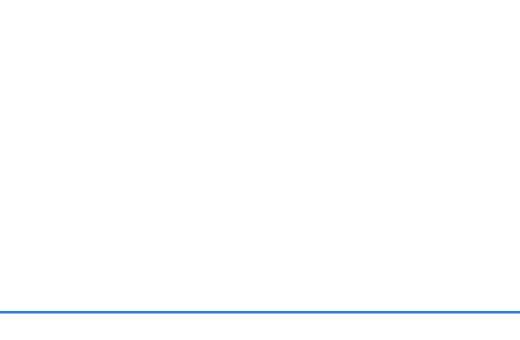
The functional unit being declared is1m2 of pre-finished steel profilewith a working width of 1035mm for the reference profile, and the composition isdetailed in Table6. In the sNMD functional descriptions, the category is‘Outer walls; non-construction’or ’41.1 exterior wallfinishes’.
3.2Scope
ThisEPD can be regarded asCradle-to-Gate (with options)and the modulesconsidered in the LCAare;
A1-3: Production stage (Rawmaterial supply, transport to production site, manufacturing)
A4& A5: Production stage (Transport to the construction site and installation)
B1-5: Usestage (related to the building fabric including maintenance, repair, replacement)

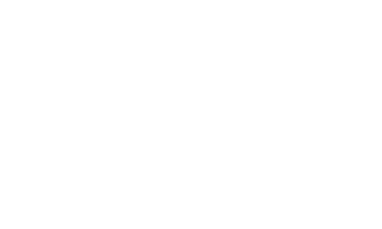
C1-4: End-of-life (Deconstruction,transport, processing for recycling & reuseand disposal)
D: Reuse, recycling and recovery
The life cycle stagesare explained in more detailin Figure 3.
Table6 Material composition ofreferenceprofileper declaredunit
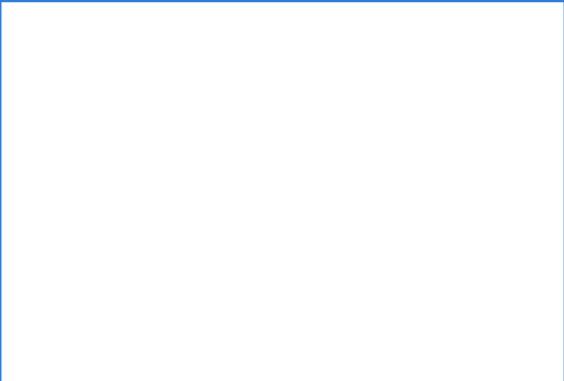
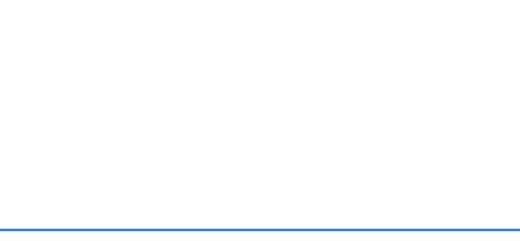
ModuleD:Benefits&loadsbeyondthe systemboundary
Includesimpactsfrom;
•Profilereuse(12%)andrecycling(87%)
ModuleC:End-of-lifestage
Includesimpactsfrom:
•Deconstructionofprofiles
•Transportfromsitetoend-of-life
•Processingofprofilesforreuseor recycling
•Disposaltolandfillofsteel(1%)
ModuleB:Usestage
Includesimpactsfrom;
•Useorapplicationoftheprofilesona building
•Maintenance,repair,replacement, refurbishmentofprofiles
ModulesA4&A5:Construction processstage
Includesimpactsfrom;
•Deliveryofprofilestosite
•Installationofprofilesatconstruction site
LifeCycleAssessment ofSABwall profiles
ModuleA1:Productstage(primary processing)
Includesimpactsfrom;
•Rawmaterialextractionandprocessing (ironore,coal)
•Steelmaking&productionofcoldrolled coilatIJmuiden,PortTalbot&Llanwern
•Preparationofrecycledscrap
•Hotdipmetalliccoatingandproduction ofpre-finishedsteelatShotton& IJmuiden
•Productionofpaintsforcoatings
•Responsiblesourcingofmaterialsto BES6001standard
ModuleA2:Productstage(transport) Includesimpactsfrom;
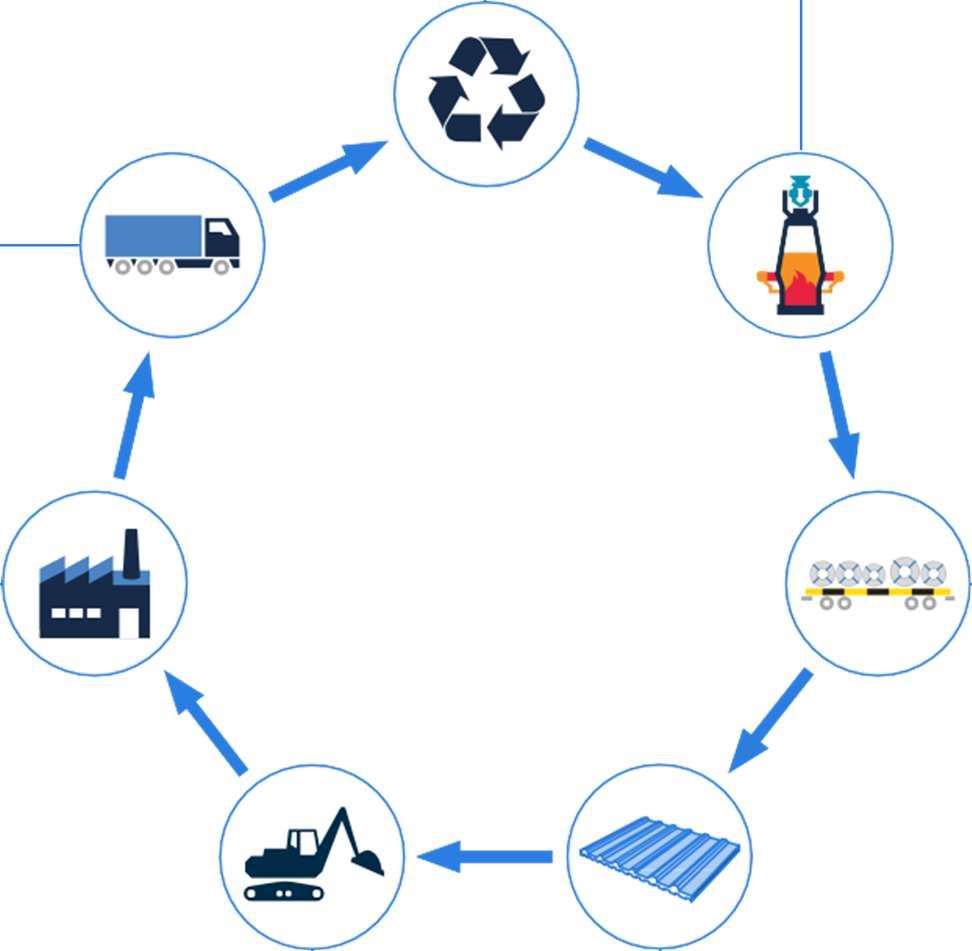
•Transportofpre-finishedsteelto profilemanufacturingsite
ModuleA3:Productstage(panel systemmanufacture)
Includesimpactsfrom;
•Profilingofpre-finishedsteel
3.3Cut-off criteria
Allinformation from the data collection processhasbeen considered, covering all usedand registered materials, and allfueland energyconsumption. On-site emissionswere measured and thoseemissionshave been considered. Data for allrelevant siteswere thoroughlychecked and also cross-checked with one another to identifypotentialdata gaps. No processes, materialsor emissions that are known to make a significant contribution to the environmentalimpact of the pre-finished steelprofileshavebeen omitted. On thisbasis, there is no evidence to suggest that input or outputscontributing more than 1%to the overallmassor energy of the system, or that are environmentally significant, have been omitted. It is estimated that the sum of anyexcluded flowscontribute less than 5% to the impact assessment categories. The manufacturing of required machinery and other infrastructureis not considered in the LCA.
3.4Background data
For life cyclemodelling of the profiles, the GaBiSoftware System for LifeCycle Engineering isused [20]. The GaBi database containsconsistent and documented datasetswhich can be viewed in the online GaBi documentation [21]
Where possible, specific data derived from the production processesof TataSteeland SAB-profielwere the first choice to usewhere available. Data wasalsoobtained directly from the relevant suppliers, such as the paint which is used in the coatingprocess.
Specificdata [26] were used to model the primarysteel manufacture at TataSteel, using Ecoinvent 3.6 [27,28] to complywith the requirementsof the NMD. All other relevant processesandlifecyclestageswere modelled using Ecoinvent background data (including energy and transport), available as part of the GaBisoftware.
3.5Data quality
The data from the production processes of Tata Steel are from 2016and 2017, and data from SAB-profielare from 2018. The technologieson which theseprocesses werebased during that period, are those usedat the dateof publication of this EPD. All relevant background datasets are taken from the GaBi software (including the Ecoinvent database), and the last revision of all but one of these datasetstook place lessthan 10 years ago. However, the net contribution to impactsof thesethree datasetsis small and relativelyinsignificant, and therefore, the studyisconsidered to be basedon good quality data.
3.6Allocation
To align with the requirementsof EN 15804, a methodologyisapplied to assign impacts to the production of slag and hot metalfrom the blast furnace(co-productsfrom steel manufacture), that wasdeveloped by the World Steel Association and EUROFER [22] Thismethodologyisbased on physical and chemical partitioning of the manufacturing process, and therefore avoidsthe need to useallocation methods, which are based on relationships such as mass or economic value. It takesaccount of themanner in which changesin inputsand outputsaffect the production of co-productsandalsotakes account of material flowsthat carryspecific inherent properties. Thismethod isdeemed to provide the most representativemethod to account for the production of blast furnace slag asa co-product.
Economicallocation wasconsidered, as slag isdesignated asa lowvalue co-product under EN 15804. However, asneither hot metal nor slag are tradable products upon leaving the blast furnace, economic allocationwould most likelybe based on estimates. Similarly
BOF slag must undergo processing before being used asa clinker or cement substitute. The World Steel Association and EUROFER also highlight that companiespurchasing and processing slagwork on long term contracts which do not followregular market dynamics of supplyand demand.
Processgasesarise from the production of the continuouslycast steelslabs at Port Talbot and IJmuiden andare accounted for using the system expansion method. Thismethodis also referenced in the same EUROFER document and the impactsof co-product allocation, during manufacture, are accounted for in the product stage (Module A1).
End-of-life assumptions for recovered steel and steelrecycling are accounted for asper the currentmethodologyfrom the World Steel Association 2017 LifeCycle Assessment methodologyreport [23]. Anet scrap approach isusedto avoid double accounting, and the net impactsare reported asbenefitsand loads beyond the system boundary(ModuleD).
In order to avoid allocation between different coatingsproduced from the same line, specificdata for the manufactureof each paint type wasobtained, and the amount of paint applied was considered, based upon the thicknessof the coating.
3.7Additional technical information
The main scenario assumptionsused in the LCA are detailedin Table7. The end-of-life percentagesare based upon valuesin the sNMD Determination Method document [8]
The environmental impactspresented in the ’LCAResults’section (4) are expressed with the impact categoryparametersof LifeCycle Impact Assessment (LCIA)using characterisation factors. The LCIAmethod usedisbasedupon that of the CML [24] and denoted in GaBibySBK-NMD Jan 2021.
3.8Comparability
Care must be takenwhencomparingEPDsfrom different sources. EPDsmaynot be comparable if theydo nothavethe samefunctionalunit or scope(forexample,whethertheyinclude installationallowancesin the building),or if theydo not followthe samestandardsuchas EN 15804. Theuseof differentgenericdatasets forupstreamor downstreamprocessesthat formpart of the productsystemmayalsomean thatEPDsarenotcomparable.
Comparisonsshouldideallybe integratedintoa wholebuildingassessment,in orderto capture anydifferencesin otheraspectsof the building designthatmayresultfromspecifyingdifferent products. Forexample,a moredurableproduct wouldrequirelessmaintenanceandreduce the numberof replacementsand associated impactsoverthe lifeof the building.
Table7 Main scenario assumptions
Module Scenarioassumptions
A1toA3–Productstage
A2–Transporttotheprofilemanufacturingsite
A4–Transporttoconstructionsite
A5–Installationatconstructionsite
B1toB5–Usestage
C1–Deconstruction&demolition
C2–Transportforrecycling,reuse,anddisposal
C3–Wasteprocessingforreuse,recoveryand/orrecycling
C4-Disposal
D–Reuse,recycling,andenergyrecovery
Manufacturing data from Tata Steel’s sites at IJmuiden, Port Talbot, Llanwern and Shotton are used, as well as data from SAB-profiel at IJsselstein
The Colorcoat® manufacturing facilities are located at IJmuiden and Shotton. The pre-finished steel coils are transported from IJmuiden to IJsselstein, 69km by road. From Shotton, they are transported a total of 280km by road, and 406km by using the cross channel ferry from Hull to Rotterdam. A30 tonne payload truck was used for all road journeys
A transport distance of 150km by road on a 30 tonne capacity lorry was considered representative of a typical installation
Based on data collected from 10 typical UK installations by a Tata Steel supply chain partner for the installation of cladding systems on site
This stage includes any maintenance or repair, replacement or refurbishment of the profiles over the life cycle. This is not required for the duration of the reference service life of the profiles
Deconstruction is primarily removal of the profiles from the building and is also based upon supply chain partner data
A transport distance of 100km to landfill or to a recycling site is assumed, while a distance of 250km is assumed for reuse. Transport is on a 30 tonne load capacity lorry
The profiles that are recycled are processed in a shredder. There is no additional processing of material for reuse
At end-of-life, 1% of the steel profiles are disposed in a landfill, in accordance with the data in the Determination Method document
At end-of-life, 87% of the steel is recycled and 12% of the steel profiles are reused, in accordance with data in the Determination Method document