DESIGN FORWARD


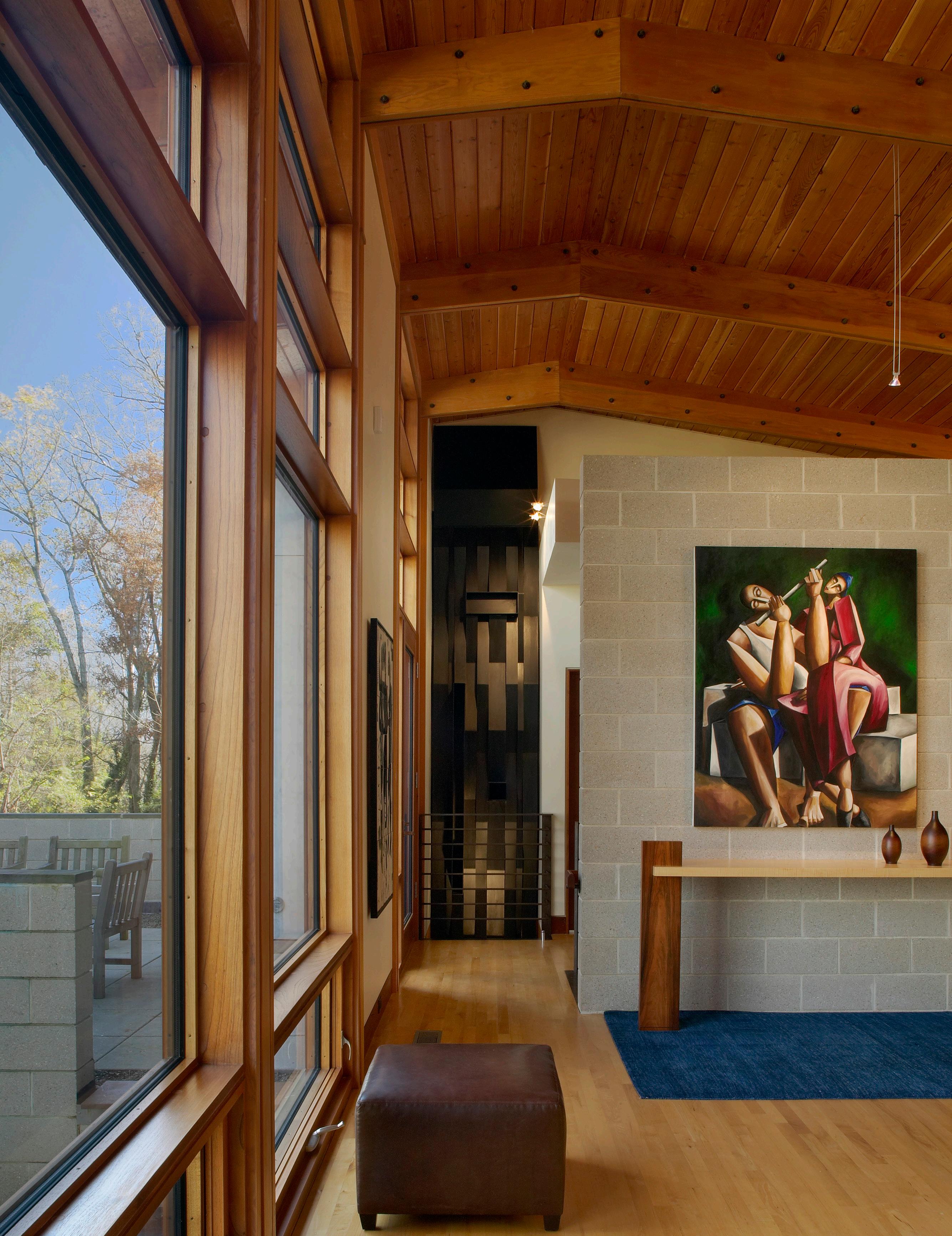

01 02 03 04
A brief history of the beginnings of timber construction to the adoption of heavy timber in Europe, Canada, and the Pacific Northwest to the rise of mass timber in the Southeast.
This section dives into the types of mass timber, best design practices, the fabrication process, trees’ natural aesthetic qualities, and current code requirements for construction.
Research into the environmental and economical benefits of mass timber. We will explore the science behind mass timber and the efficiency it can bring to a project.
A collection of precedent projects from smbw’s history, proformas from select mass timber projects, and aspirational designs that are pushing the boundaries of sustainable design.
Appendix: Abbreviations & Definitions
The natural environment, and it’s correlation to the history of mass timber, is inexplicably tied to those who called America home long before the United States was established. It is important to recognize the indigenous people who lived here before and whom we still have so much to learn from.
We would like to respectfully acknowledge the People who have stewarded this land throughout the generations.
While there are many examples to reference, the Plankhouse is one of the most common examples of Indigenous architecture. Typically a winter house, plank house designs are between eighty to hundred feet long and designs can vary from region
to region mainly due to the materials available, their geographical location, and what time of year the building is for.
Pictured right, Achaf-Hammi “house made of cedar” of the Confederated Tribes of Grand Ronde, is a typical Pacific Northwest Plankhouse is constructed of cedar planks. Four corner posts are the bear the majority of the structural load for the building, while larger houses will have additional posts running through the middle.
The circular door at the front of the plank house is to slow down any possible intruders forcing them to crouch down to enter the Plankhouse. Lower ranking and younger members of the tribe slept closer to the entry to protect the elders.
In 1983, Austrian architect Hermann Kaufmann, who is often referred to as the godfather of mass timber, started his own practice, Hermann Kaufmann + Partners, and later founded one of Europe’s first dedicated institutes for timber construction at the Technical University of Munich, with the aim of reviving wood as a modern construction material.
In the early 1990’s an innovative wood product known as Cross-Laminated Timber (CLT) was introduced in Austria and Germany. Mass timber has rapidly risen to prominence through its reputation as a naturally regenerating, globally abundant and incredibly versatile alternative to carbon-intensive steel and concrete construction.
By the early 2,000’s, construction of CLT had increased. This increase in production can be partially attributed to the ‘green building movement’. The movement established programs to equip construction professionals and workers with the skills needed to address mass timber construction. By critically looking at existing building codes, creating incentives for sustainable design, and setting up sustainable initiatives to assist in reaching overall environmental goals, the movement also enhanced CLT’s efficiency, product approvals, and improved marketing and distribution channels. Another contributing factor to CLT’s growing popularity is the perception that CLT, like masonry and concrete, is a heavy construction system. Today, Europe continues to lead the world in timber construction with it being home to sixty of the world’s eighty four tall timber structures (eightplus stories), according to a 2022 count by the Council on Tall Buildings and Urban Habitat. New policies across the continent suggest that Europe’s momentum in timber construction isn’t slowing down.
In France, public buildings - including those constructed for the 2024 Paris Olympics - are mandated to use bio-based materials. By 2025, France requires that twenty five percent of major refurbishments and new construction use bio-based materials, increasing to fifty percent by 2030. Life cycle embodied-carbon analysis is also mandated for residential buildings, schools, and select commercial-building types, with limits set to tighten in stages. At a supranational level, the European Commission is considering an EU-wide requirement to measure the life cycle carbon emissions of construction materials. They are also exploring a
provision for EU member states to develop national building-renovation plans to reduce embodied carbon. However, these policies and programs being introduced across Europe remain widespread and wide-ranging causing stumbling blocks across the industry. As Hermann Kaufmann said in an interview with Dezeen in 2023:
“This whole chain needs the right knowledge to get moving,” Kaufmann added. “This is happening at the moment and it could happen relatively quickly. But it won’t explode. It will be an evolution, not a revolution.”
In North America, mass timber is notoriously associated with the Pacific Northwest and Canada. The timber industry has been stitched into the fabric of the American West culture and is now integrated into the architecture of their cities. This is mainly due to Oregon and Washington consistently being the nation’s top softwood lumber producers. According to a study done by Forest Economic Advisors LLC in 2021, Oregon and Washington account for twenty nine percent of the nation’s softwood lumber.
In 2015, the National Design Specification for Wood Construction (NDS) and International Building Code (IBC) introduced CLT as a specified construction type that opened up a whole new chapter for wood construction in America. Suddenly there was a groundwork of common regulations to build with mass timber elements that complied with the current code creating the opportunity for more mass timber buildings to be built and for designers to push the material and building codes’ limits. In 2018, Oregon became the country’s first state to revise its building codes to allow for mass timber structures exceeding six stories, now with an upper limit of 18.
The early 2020s brought significant funding to Oregon Mass Timber Coalition (OMTC) when OMTC was awarded a $41.4 million grant from the Economic Development Administration as part of the Build Back Better Regional Challenge. This funding supports OMTC’s mission to become a national leader using mass timber to boost affordable housing production, provide good jobs, and restore forest health.
The state wide effort to re imagine the role of mass timber found an unexpected champion in the Port of Portland. The Port had recently chosen to use mass timber for their new main terminal roof at Portland International Airport (highlighted later in this book).
Portland embraced locally sourced mass timber and worked with partners to set sustainable sourcing criteria that created opportunity for foresters and businesses across the region. With 100% of the wood volume (2.6 million board feet, to be exact) coming from within 300 miles of the airport, the Port saw the possibility for mass timber’s role as a catalyst for regional economic development.
While North America is making massive strides in the mass timber industry, there is so much more work to be done. In an interview for Dezeen’s Timber Revolution series, Canadian mass-timber pioneer, Michael Green, advocates passionately for mass timber construction, but cautions designers that it shouldn’t just be a nice box to check, saying:
“Too many architects are saying, ‘Oh, I did a masstimber building. Check the box. I’m a sustainable architect’.”
“There is no such thing as being a sustainable architect.”
“I do think mass timber is the best of the best right now,” he continued. “I encourage everybody to pursue it. But don’t rest on those laurels.”
As the Southeast catches up in mass timber advancements, fabrication labs and timber farms are emerging across the region, gradually driving up demand of mass timber construction.
The previous section referenced a study done by Forest Economic Advisors LLC in 2021 that Oregon and Washington combine for twenty nine percent of the nation’s softwood lumber, but the same study shows Oregon and Washington are followed closely by Alabama, Georgia, and Arkansas and combined account for twenty six percent. Recognizing this strong supply base in the Southeast, TimberLab, the fabrication team behind the Portland Airport project, launched a new fabrication lab in Greenville, South Carolina in 2024.
A large contributing factor to the rise of mass timber construction in the south is Southern Yellow Pine. Historically, North American mass timber have been composed of fir, spruce, and pine found abundantly in the Pacific Northwest. The Southern Yellow Pine has spiked in popularity in the past decade due to its durability, fast growth, and highly renewable nature.
While the demand is on the rise for southern lumber, there is still a lack of lumber producers in the southeast. In fact, three of the five leading producers of southern lumber are based in Vancouver, British Columbia. As the trends show the demand for southern lumber continues to rise, others are expected to follow TimberLab’s lead by opening facilities in the Southeast extending the reaches of sustainable lumber capabilities in the region.
While the sourcing of mass timber from the southeast is important by itself, it matters just as much for major organizations to adopt mass timber construction within the region and across the country. Construction is underway on the Walmart Home Office Campus in Bentonville, Arkansas, where Gensler is serving as Design Architect for the office buildings and Executive Architect for the overall campus design. Mass timber will be the primary structural material for the campus, representing an evolution in its implementation. With more than 2.4 million square feet of office space, the company’s new campus is the largest mass timber corporate campus currently under construction in the United States.
In Baltimore, Maryland, Johns Hopkins University’s new student center is set to be more than 60% mass timber. Designed by Bjarke Ingles Group, fabricated by StructureCraft, and built by Clark Construction, Johns Hopkins is putting sustainability at the forefront of the vision for the future of their campus.
Meanwhile, TimberLab’s Greenville, South Carolina lab recently provided the glulam timber and crosslaminated timber (CLT) fabrications for a LS3P designed four-story 100% mass timber building in Wilmington, North Carolina -v utilizing the region’s Yellow Southern Pine.
There are still many challenges to overcome and lessons to be learned with mass timber. As seen in Europe, Canada, and the Pacific Northwest, nothing happens overnight, but learning from those who have laid the foundations has already yielded influential results. Harrison Tucker, CEO of the Charlotte-based development company Space Craft, which is building the first mid-rise hybrid mass timber apartment building in the Southeast, has said:
“You think about these mill buildings from around 1900—they’re some of the best buildings we have in the Southeast. I think we’re creating a new stock of that.”
Introduction
Mass timber is a key component of sustainable design, known for its ability to reduce carbon footprints and support energy-efficient building practices. While it may not single-handedly solve global climate issues, mass timber contributes to a more sustainable future by offering a renewable, biodegradable alternative to traditional construction materials. Sustainability may be the key reason to consider mass timber, its natural beauty and the desire to bring nature into our built environment is increasingly drawing people to this method. Mass timber has the remarkable ability to transform a space, infusing it with life, energy, and a tranquillity. In environments that might otherwise feel dull or uninspiring, mass timber not only meets the structural and design needs but also aligns with the
sustainability goals while enhancing mental wellbeing. Its unique combination of form, function, and natural warmth sets it apart from any other building material.
Code
This section explores the creative processes involved in assembling mass timber, along with the latest code updates. It is important to note that as this type of construction is growing, the code is evolving to keep pace as new innovations are constantly driving sustainability efforts forward. This document utilizes the current IBC requirements, but when starting a mass timber project it is best practice to consult your local building codes as they might not yet reflect the latest IBC mass timber construction allowances. With that in mind, let the fun begin...
Mass timber refers to a category of framing styles characterized by the use of large, engineered wood panels, often paired with engineered wood columns, and beams. Panels are most frequently used in horizontal applications for floors and roofs, but can also be used vertically for walls. Mass timber is often combined with other building systems to achieve benefits greater than those offered by each system alone. Examples include mass timber floors and roof with light-frame wood walls, steel elements in long-span floor systems, and concrete foundations, podiums, cores, and floor toppings.
Misconceptions About Mass Timber
Mass timber is not heavy timber. Heavy timber is usually associated with large cross sections of solid wood members for the creation of beams, purlins, and
columns. It often utilizes tongue-and-groove decking for its floor and roof construction. Mass timber is also not stick framing that is most commonly used in multi-family construction. Stick framed structures typically rely on 2x4 and 2x6 dimensional lumber and require additional materials for finishes and code requirements.
Types of Mass Timber
Mass timber assemblies come in several types, including cross-laminated, glue-laminated, dowel-laminated, nail-laminated, and structural composite lumber. Variations in strength, rigidity, pliability, and finish make each assembly suited to specific applications. Following is a brief overview highlighting the main attributes of each type.
CLT is composed three, five, or seven layers of solid-sawn lumber oriented perpendicular to one another and glued to form structural panels. CLT can be used for floors, roofs, and walls.
GLULAM is created by combining solid 2x_s lumber members parallel to each other on their wide faces with adhesive between layers. GLULAM is most commonly used to create columns and beams.
DLT panels are made from solid lumber. Typically 2x_s oriented on edge and fit with hardwood dowels. The dowels hold the boards side-by-side, while friction adds dimensional stability. DLT is commonly used for floors and roofs.
Similar to DLT, NLT is created from solid dimensional lumber with 2x_s oriented on edge. NLT is fastened with nails or screws instead of dowels to create larger structural panels. It is commonly used for floors and roofs.
SCL is a family of engineered wood products created by layering dried and graded wood veneers or strands with moisture-resistant adhesive into blocks of material known as billets. Billets are subsequently re-sawn to specified sizes with SCL most commonly used in beam and column construction.
CLT is known for its exceptional strength, stability, and stiffness. These three qualities create two-way spanning capabilities for a high performing structural outcome.
Panels of cross-laminated timber are prefabricated and precise. Coordination between the design team and fabricators is essential during the creation of the panels as openings are pre-cut in the factory before being shipped out to the project site for on field assembly.
A typical panel dimensions can vary from four to twelve feet wide and sixteen to sixty feet long with layers typically one and three eighths thick depending on the manufacturer.
CLT is commonly composed of softwood, including spruce-pine-fir (SPF), Douglas fir, and southern yellow pine.
The 2021 and 2024 IBC allow CLT meeting minimum size requirements in buildings up to 18 stories in Type IV-A construction, up to 12 stories in Type IV-B, and up to nine stories in Type IV-C.
Glulam can be fabricated in almost any shape, though straight elements are most common for columns and beams. Jigs may be used to form curves, bends, and different radii making gluelaminated timber a versatile structural member able to accommodate unique building forms.
A typical glulam beam and column size ranges from six to seventy two inches deep and up to a hundred feet long.
While usually used to create beams and columns, glue-laminated timber can be made into panels (the abbreviation “GLT” is used when referring to panel assemblies) that are two to four feet wide and up to sixty feet long.
Glulam and GLT have the same code references and manufacturing standards. They are permitted under IBC Section 2303.1.3 when manufactured and identified as required in the ANSI 190.1 Product Standard for Structural Glued Laminated Timber and ASTM D3737 Standard Practice for Establishing Allowable Properties for Structural Glued Laminated Timber (Glulam).
Also know as Brettstapel, DLT is the term commonly used for solid timber construction that does not generally use glues or nails. Fabricated from softwood planks joined with hardwood dowels, this straightforward construction method has the potential to utilize low grade timber that would otherwise be unsuitable for use in construction, to form loadbearing solid timber panels for walls, floors and roofs.
The all-wood composition makes it easy to use with computer-numerical controlled (CNC) machinery such as lathes, routers, and mills and can be modified in the field with hand tools.
A typical panel size runs two to twelve feet wide and up to forty feet long.
Widely used to meet acoustic ratings or other objectives, various profiles can be created to address specific detail requirements and aesthetic preferences with finger-jointed laminations being the most common.
DLT is often used with accompanying third-party evaluation reports that address code compliance.
NLT has been used for more than a century but is undergoing a resurgence as part of the modern mass timber movement. Historically, NLT has been used for the construction of warehouses and other large buildings due to it’s natural acoustic qualities.
Typically nail-laminated timber panel sizes range from two to four feet wide and sixteen to forty feet long.
NLT members are usually fabricated off-site although on-site fabrication is possible for experienced contractors but not common practice in the construction field.
Different visual profiles, such as alternating lumber sizes, can be used to achieve desired acoustic qualities or other objectives.
NLT is recognized prescriptively as mechanically laminated decking in Chapter 23 of the IBC.
Structural Composite Lumber (SCL)
SCL is sawn to consistent sizes and exhibits highly predictable physical and mechanical properties.
Within structural composite lumber lie a few variations in assemblies:
Laminated Veneer Lumber (LVL) is produced by bonding thin wood veneers with their grain aligned parallel to the length of the panel.
Parallel Strand Lumber (PSL) is manufactured from veneers clipped into long strands and oriented primarily along the strong axis.
Laminated Strand Lumber (LSL) is made from flaked wood strands.
Oriented Strand Lumber (OSL) is made from flaked wood strands with a smaller length-tothickness ratio than LSL.
SCL products are permitted under the IBC Section 2303 when manufactured according to ASTM D5456: Standard Specification for Evaluation of Structural Composite Lumber Products.
Nate Swift, from the architecture team, visited TimberLab in Portland, Oregon this fall, where he explored the manufacturing facility and sat down for a chat with Senior Project Engineer, Andrew Ratzke, to better understand the fabrication process.
Born out of Swinerton, a national construction firm since 1888, TimberLab opened their own independent fabrication lab in 2020 that produces an estimated 800,000 sq. ft. of timber annually. In 2023, they launched a second facility in Greenville, SC to assist the growing southeast market. TimberLab’s mission is “to accelerate the mainstream adoption of mass timber in the U.S. commercial construction market to benefit the planet and its people through a world where buildings have a low carbon footprint and high community impact.”
Notable projects include the Portland International Airport that boasts 3.3 million cubic feet of locallysourced mass timber, a full mass timber office building on Live Oak Bank’s Wilmington, North Carolina campus, and University of Arkansas’ new i3R research facility.
Q: We have talked a lot today about how collaboration is key to the success of any mass timber project. Assuming as fabricators you are in constant communication with both the design team and on-site construction team, can you explain what the coordination steps look like from the fabrication facility side?
A: Exactly. We like to be in communication as early as we can with the design teams. This allows us to work with all the different system designs that go into a building to create a solution that works both from a design and efficiency point of view. Mass timber really flips the whole construction process on its head. Most of the time is spent offsite coordinating and fabricating penetrations and connections so the on-site work is minimal.
Q: When receiving designs from the architect, how much effort is there to get the mass timber members ready to be fabricated?
A: There is about four to six months worth of work for our team to be ready for the actual fabrication to start. When TimberLab receives the BIM model, we basically re-build the entire model. This enables us to add all our details, confirm penetrations, specify assembly instructions, and verify that all the systems will work with the mass timber structural configuration. During this time is when we are gathering the wood supply to create the assemblies so when the architect gives the final design approval, we are good to go.
Q: What are some of the challenges you are seeing that mass timber is having to overcome?
A: Honestly, a lot. From an industry side, there is still not the widespread belief that a building constructed completely out of wood can stand up to the fire prevention requirements of some building types. We have done extensive testing to prove it can, but then you have to wait for codes to catch up. From the construction side, its mainly just if coordination is slightly off. It can set back the whole project timeline that kills the cost savings you see in construction time. It can be the result of low supplies, late involvement from other trades, miscalculations in the off-site assembly, on-site inaccuracies from other trades, or lack of skilled workers that can really kill the project’s speed.
An extensive process from start to finish, mass timber requires constant communication between the design team, fabrication facility, and on-site construction team. This is the journey a typical GLULAM member goes through during the fabrication process.
After months of coordination between the design team and fabricators, members are ready for fabrication. Each one is carefully labelled so the first to be fabricated is also the first to be constructed. Beams are arranged within truckloads, with the first fabricated at the bottom for efficient unloading. To perform this coordinating gymnastics, each member has a special naming convention and QR code that link to the drawing sets. B stands for beam. The first two numbers refer to the building number. The next number is building story and remaining digits for assembly member.
Each GLULAM member arrives to the facility two to three inches longer on each end to address manufacturing tolerances. The additional tolerance allows TimberLab to make a perfectly square and clean cut end prior to fabrication.
Once the beam is cut to the correct size and cleaned up, it is run through the CNC machine. The precision of the CNC machine ensures that all of the proper penetrations, and cuts for each GLULAM member are accounted for during fabrication. These details ensure each GLULAM member has the required added connections for on-site construction.
After the GLULAM member has gone through the CNC process, it is given an inspection and label based on the amount of post fabrication work needed. Green means ready for steel connection installation. Yellow means light work needs to be done before its ready for the connectors. Red means either the member is unusable or major work is needed to prepare the member for the next stage. All of this work is done by hand.
To minimize on-site assembly requirements, the steel connections are usually pre-fabricated and assembled in the facility before heading off to the site. This makes on-site construction quick and efficient, maximizing the cost saving benefits of mass timber construction.
Lastly, the finalized prefabricated GLULAM members go through one more sanding and treatment application, typically a natural water based protection layer that limits moisture absorption and maximizes timber performance during pre-construction, installation, and into the finished building’s life cycle. The members are then carefully stacked in the coordinating order for onsite construction.
For mass timber construction to be financially beneficial, all trades must be working in harmony to communicate connections on and off site. This consistent communication ensures adherence to tight project schedules during the construction phase of the project. The ease at which mass timber projects are constructed accounts for the added benefit of considerable financial savings to clients.
Typically the thickness of a mass timber member is dependent on the load bearing and fire prevention requirements. Pictured right is a six ply GLULAM beam after a three hour fire test. Because of wood’s natural qualities a char layer will form during a fire protecting the interior of the mass timber assembly. As noted in NDS Section 16.2.1, the nominal char rate of 1.5 inches per hour is used for solid sawn and GLULAM members. The three hours far exceeds the two-hour fire resistance rating that most building codes require.
A unique consequence of working with wood is, well, it’s uniqueness. Each type of wood has it’s own grain, coloring, and aging. Picking the right species often comes down to the aesthetic desires of the owner. While there are any number of species to choose from, sustainable efforts will only be fully achieved by choosing from the local selection, as shipping wood is expensive and has a substantial impact on the project’s carbon footprint. The aesthetics of locally sourced timber will differ regionally. Wood from Scandinavia will not look like wood from Oregon and wood from Oregon will not look like wood from Virginia. Pictured from back to front is a treated/new Douglas Fir from Oregon, Yellow Southern Pine from the American Southeast, and matured Douglas Fir from Oregon (five to ten years old). Spruce, Pine, and Fir or SPF are noted to be the most common and sustainable woods for mass timber assemblies as they are a fast growing and high performing species.
In mass timber buildings, the structure is often the interior finish too. While creating a beautiful natural design, it leaves the internal systems exposed. This requires special coordination between all trades. Questions of the quantity and location of penetrations must be answered before the fabrication process can start. In cases where the design demands the systems be hidden, precise spacings between beams and columns require trades to work together closely.
When fabricating and installing GLULAM beams, it is crucial to coordinate and label balanced and unbalanced beams. The label tells the on-site team the orientation the beam must be installed to prevent bowing since wood will naturally bow when spanning between supports. Based off of the type of connection, a beam is either balanced or unbalanced. Failing to coordinate these will produce weaker beams and gaps between the beam and the load above. The image to the left has a label, TOP, to indicate this is an unbalanced beam meaning the installation orientation is important. Balanced beams do not receive a label as the outside members are the same.
Most rigid boards sit at the bottom of the assembly to prevent one directional bowing
Rigid layers are on both top and bottom of the assembly to prevent two directional bowing
Manufacturing standards requires that when a GLULAM member is over twelve inches wide, it is made of multiple planks that overlap one and a half inches. While it would make sense for a sixteen inch wide member to be made of a two by four and two by twelve, it is cheaper and more efficient for it to be created by a two by four sandwiched between two two by sixes. This is because a tree can produce more two by fours or two by sixes as opposed to wider planks. Capitalizing on these efficiencies results in major cost savings.
Structural Design
Modular Elements
Mass Timber Details
BY MERGING FUNCTION WITH THE INNATE NATURE OF PLACE, AND BY EMPLOYING STRATEGIES TO ADDRESS INEQUITY, OPPORTUNITIES FOR HEALING CAN EMERGE WHERE VIBRATIONS MANIFEST THROUGH TIME AND SPACE TO RENDER LEGACY IN EXPERIENTIAL FORM. AS DESIGNERS, LET US NOT LOSE SIGHT OF THE FACT THAT WE’VE MADE OUR MOTHER SICK, SO WE MUST DO OUR PARTS TO RESTORE HER WELLNESS, AND BE STEWARDS FOR JUSTICE... hmmm... “JUSTICE”...
FROM “TO BE JUST... STEWARD SOME LIFE LYRICS”
BY QUINLIN B. MESSENGER
THE FUTURE CAN BE JUST - DESIGN IT.
Introduction
Mass timber has many qualities that makes it prime for sustainable design. Wood naturally has low embodied carbon compared to other building materials, which indicates fewer greenhouse gas emissions, and they retain the carbon absorbed by the trees while they were growing. Simply put, low embodied carbon plus stored carbon results in a lower carbon impact. Wood is also natural, renewable, and can contribute to energy efficiency and biophilic design. Lastly, as a building material, it is durable, adaptable and reusable.
In terms of energy efficiencies, wood benefits from a low thermal conductivity that steel and concrete can not match. And though any structural system can be
designed to have air tight connections, the precise manufacturing of mass timber systems can provide exceptional air tightness. As a result, wood buildings are much easier to insulate to high standards.
All of the inherent qualities of wood make mass timber a great start towards a sustainable building, but choosing mass timber is just the tip of the iceberg. A choice that is often overlooked in the building’s life cycle is the very start. Choosing to use locally sourced wood from sustainable tree farms is just as important as choosing to build with mass timber. Transportation emissions, shipping costs, and the lack of support for the local economy can be just as harmful to the environment as building with standard materials.
The word carbon dioxide is thrown around quite a bit when talking about sustainability, but it is a broad term. On the most basic level, carbon dioxide naturally occurs through volcanic eruptions, wildfires, and human respiration and can be generated inorganically through the burning of fossil fuels for power and transportation. In the natural order, the earth’s atmosphere absorbs the carbon dioxide to combine with other gases to tramp the sun’s solar energy that maintains a habitable climate vital for life on earth. The issue we now face is we now produce too much carbon dioxide causing the atmosphere to tramp more heat than required. Thus, we have global warming.
According to Architecture 2030, the built environment is responsible for over forty percent of the annual global carbon emissions. Along side the built environment, concrete, steel, and aluminium make up twenty three percent of the total global emissions with most of those figures in result of the built environment. These high impact areas introduce a substantial opportunity for embodied carbon reduction through thoughtfully written policies, design, and intentional material choices. As our population increases, the need for sustainable practices and climate friendly materials has become
more urgent. Wood and mass timber design has emerged as a leading solution to the challenges posed by climate change.
A general rule of thumb is less embodied carbon plus stored carbon equals a lower carbon impact on the environment. One way to achieve this, and the whole reason for this document, is through building more wood buildings.
Before jumping into why mass timber is a great solution to lowering the carbon impact of the building industry, let us define the basics:
Embodied Carbon
Represents the carbon emissions released during the life cycle of building materials, including extraction, manufacturing, transport, construction, and disposal.
Stored Carbon
Also referred to as carbon sequestration, is the process of capturing and storing atmospheric carbon dioxide. This process is naturally done by plants, soil, rock, and the ocean.
Mass timber works as a viable solution to lower carbon impact because the manufacturing of wood products requires less fossil fuel based energy than other common building materials like concrete or steel. The majority of the energy comes from renewable biomass, like bark and other residual fibers, that would otherwise go to waste.
“Every year, 17,000 buildings constructed with other materials could be built with wood. In most cases, it costs about the same to build with wood, and yet the environmental benefits are significant. Building with innovative wood products from sustainable, properly managed forests is a relatively easy way to alleviate a sizable amount of U.S. carbon emissions.”
– Jennifer Cover, President and CEO, WoodWorks, Testimony to the Committee on Energy and Natural Resources, United States Senate
As trees grow, they absorb carbon dioxide from the atmosphere, release the oxygen, and incorporate the carbon into their wood, leaves or needles, and roots. This carbon is referred to as biogenic carbon. When trees are manufactured into building materials, the wood continues to store this carbon. Wood is fifty percent carbon by dry weight. This can drastically effect the amount of carbon released into the atmosphere. By example, vinyl flooring can have up to twenty times the amount of emissions of wood flooring over a building’s entire life cycle. See the chart on page 28.
By substituting wood for fossil fuel-intensive materials reduces embodied carbon and keeps carbon out of the atmosphere for the lifetime of the structure (longer if the wood is recycled or reclaimed), we take a few more important steps toward reducing the building industry’s carbon footprint.
Reuse, reduce, and sequester are vital strategies for moving to a net zero built environment. This includes looking at opportunities to renovate existing structures with more efficient systems and materials, being mindful of the new materials we select to go into our buildings, and the use of carbon sequestering materials like wood.
In the recent past, a building touted as net zero referred to solely the building’s operational energy. The energy used during a building’s operation to power, heat, and cool the structure. With
improvements in energy efficiency, renewable energy options, and more efficient design techniques, many buildings have been able to achieve net-zero operational energy. This is where no off-site energy is required for standard performance, and net-zero operational carbon, where associated carbon emissions are zero through the use of renewable energy sources. Historically, these types of buildings have been call net-zero energy buildings or net-zero buildings.
As advances in sustainable design develop and the need for stricter climate regulations increase, the definition of net-zero has evolved to refer to the building’s overall carbon impact. This includes both the operational and embodied carbon totals. But it is important to remember that wood contains biogenic carbon, carbon removed from the atmosphere through the process of photosynthesis, and must be accounted for when looking at the whole building’s life cycle. Wood will retain the embodied carbon for the lifetime of the building, but can release some or all of the stored carbon upon the end of the building’s life depending on how the product is handled. This released carbon will no longer be available to offset the embodied carbon emissions.
Another way a structure can be considered as a net-zero building is through carbon offsets. This is when a building will not reach net-zero on it’s own through either its operational carbon or embodied carbon emissions. But the owner of the building has the desire to achieve net-zero, they can purchase an offset to compensate for the carbon emissions produced. These offsets are then calculated into the overall carbon of the building. Moat often this accomplished by financially aiding climate projects that focus on social impact, renewable energy advancements, technical solutions, or natural based solutions.
Due to the variety of ways net-zero can be defined, it is important for all members of a project to determine the type of net-zero the building is hoping to accomplish. This will eliminate confusion when sharing sustainability accomplishments with the public. While there are a number of ways to achieve net-zero goals, mass timber construction is a proven strategy to reduce carbon emissions. A helpful tool to analyse a project through a sustainable lens and establish a carbon friendly game plan is by completing a Whole Building Life Cycle Assessment.
When building with wood, you have to take into account embodied carbon and stored carbon when calculating the entire carbon offset of a mass timber building. The Life Cycle Assessment (LCA) is an all encompassing guide to project the offset of any building over it’s entire life span. It is a systematic approach that compiles and analyses all the inputs, outputs, and potential environmental impacts of a product or system over its lifetime. In regards to buildings, a Whole Building Life Cycle Assessment (WBLCA) is a more common tool to utilize. This analyses a building as an entire system as opposed to the LCA which looks at each element separately, in example a singular mass timber wall. The Whole Building Life Cycle Assessment has become an effective tool to measure embodied carbon and other environmental impacts associated with buildings at a holistic level. As the WBLCA is more approachable and relevant to the purposes of designing and construction sustainable buildings, the focus of this section will be on the WBLCA.
It is important to consider the whole building life cycle in the early planning stages of a mass timber project. The word whole is key to note. Sustainability starts at the source. Later we will dive into the importance sustainable tree farming and where you get your wood products can make or break sustainable efforts, but for now note that carbon emission calculations start before the first shovel hits the dirt. In fact, variables such as raw material sources, supply chain processes, transportation distances, construction practices, design choices, building location, and climate and operating practices all combine to determine the lifetime carbon impact of a building.
The assessment is governed by several international standards, primarily the ISO 14040 and 14044. Additionally, ISO 21930, which provides the framework and requirements for Environmental Product Declarations (EPDs) for construction products and services, defines the following four stages of the life cycle as Production Stage, Construction Stage, Use Stage, and End of Life Stage. There is an optional fifth stage that refers to the reuse, recycle, and recovery of
materials. Each stage is broken into sub sections referred to as modules. Here is a deeper dive on the four main stages:
Production Stage: Modules A1-A3
A1: The harvest or extraction of the raw materials.
A2: The transportation of those raw materials to the factory or mill.
A3: The actual manufacturing of the product itself. See the fabrication process on page 18.
Construction Stage: Modules A4-A5
A4: The transportation of the product to the construction site.
A5: The installation and / or the construction process.
Use Stage: Modules B1-B7
B1: Occupational use of the building
B2: Building maintenance
B3: Building repairs
B4: Replacement of building elements / systems
B5: Building refurbishment
B6: Operational energy use
B7: Operational water use
C1: The deconstruction or demolition of the building.
C2: The transportation of waste to the disposal or processing site.
C3: Waste processing
C4: The final disposal of that waste.
If products are to be reused at the end of the existing building’s life on another building, it is important to separate those products in Module D to avoid double counting between the new and existing building.
It is important to define the scope of the system undergoing the Whole Building Life Cycle Assessment as it may vary depending on the goals of performing the assessment. Structural engineers may care about the mass timber structure while the design team may be more focused on finishes
and non structural elements throughout the building. To assess the overall impact a building will have on its global warming potential (GWP), it is imperative to include all systems relevant the overall building performance, like structural elements, building envelope, finishes needed to meet fire and acoustical requirements, and components of the assembly required for acceptable vibration performance.
There are a massive amount of considerations to acknowledge when approaching the WBLCA and it can become overwhelming. Thankfully, there are plenty of resources and tools out there to make the assessment digestible. A great source is the non-profit, WoodWorks. They have free educational resources, articles, professionals, and partners that are happy to help understand the process of designing and building wood forward buildings.
Location, Location, Location
While the notion that mass timber is a Pacific North West, Canadian, European fad has been correctly assumed the past few decades, that is no longer the case. In a world with increasingly extreme temperatures, we are forced to face the reality of climate change meaning sustainable design and mass timber construction is here to stay. The south east is a widely untapped resource for MT production, but that has changed in recent years. With the rise of mass timber production, it is important to source materials from a forest that is sustainably managed.
Transportation
Almost as important as choosing to use mass timber for your project is choosing the right fabrication lab as your source. If you are building in Virginia and use a fabrication lab in Oregon, the finished product will have to be shipped across the country losing all sustainability efforts in the offset of vehicular emissions. It is imperative to use locally sourced product and fabrication when selecting a manufacturer.
Energy Efficiency
Besides the carbon benefits of wood frame buildings, there is high efficiencies to be gained from an operating standpoint compared to that of a steel or concrete structure. Due to it’s thermal conductivity, it is much easier to insulate than other building assemblies.
While SMBW has not done an outright mass timber building, the firm has designed many projects focused on natural materials including mass timber assemblies in both structural elements and highly designed detailed show pieces.
Pulling from the information from the non-profit, WoodWorks, compiled from building owners, contractors, engineers, and architects, this section breaks down the numbers and long term financial benefits for choosing mass timber construction.
Really cool projects! There are many ways to design and build with mass timber. Taking a look at buildings pushing the envelope in sustainable design to draw inspiration for what is possible to build right now.
Luckstone Headquarters
Crushed Stone Supplier
Location: Richmond, VA
Market Sector: Corporate
Size: 85,000 sf
Year Completed: 2008
Architect: SMBW
This corporate headquarters pays tribute to the surrounding landscape and the stone it supplies through creative space solutions and a material palette of wood and stone.
The synthesis of the physical attributes of the space with the client’s evolving corporate culture create offices that are open, collaborative, and formally connected to the landscape through eight outdoor rooms.
Through thoughtful analysis, smbw preserved and enhanced the existing facility’s best qualities - highlighting the dialogue between the building and its natural surroundings. The courtyard spaces are uniquely shaped as the building embraces the landscape. The quiet presence of the existing low-slung structure of Luckstone’s Headquarters is preserved through an intentional design solution that nestles the massive scale of the new three-story expansion into the hillside.
Exterior glazing washes the interior with natural light while simultaneously allowing for visual connections between volumes of space. Internally, cheerful color palettes and natural materials visually activate the interiors creating an environment that is warm, comfortable, and invigorating.
Luckstone was keen to emphasize the natural qualities of wood throughout the building. This is evident in the various scales throughout the project, from large mass timber elements to Spanish Cedarclad walls and fine details using lyptus wood, cherry, and walnut.
GLULAM DECKING
STRUCTURAL 5-PLY GLULAM BEAM
STRUCTURAL 12-PLY GLULAM BEAM
HSS 8 X 4 WRAPPED IN A DECORATIVE GLULAM BEAM
The use of wood in Luckstone’s Headquarters is highlighted throughout the structure of the new addition. The design team utilized Glue Laminated (GLULAM) beams created out of douglas fir trees, exposed roof assemblies, and High-Speed Steel (HSS) columns wrapped in decorative glulam planks. The exposed structure promotes the overall mission to evoke the senses of being constantly surrounded by nature despite the building functioning as a corporate headquarters. As seen in the image below, bringing the outdoors inside was the cornerstone of the architectural vision from the first sketch.
This connection with nature, extending from the inside out, is best exemplified in one of the headquarters’ long hallways (see image right). Despite the limited number of eye-level windows in this hallway, the exposed mass timber structure imparts a light and warm atmosphere that is typically rare in corporate offices. The above detail showcases how the architecture and structural engineering teams exposed the structure, accentuating the natural qualities of the wood.
Wood
With sweeping views of Virginia’s country side, both architect and client advocated for an experience that allowed employees to interact with nature visually and physically. Choosing the right material was crucial to facilitate this vision.
Lyptus wood, a blend of two types of eucalyptus trees, was selected for it’s sustainability qualities and inherent beauty. Within eight years, it can produce about ten feet of usable wood. In another eight years, ten more feet can be cut and a single tree can be cut three to four times before it stops producing usable wood. It is a brittle wood that does not have a consistent finish making Lyptus Wood ideal for decorative details.
Luckstone HQ utilizes the Lyptus wood as an art piece with planks of the wood stacked on top of each other at various depths. The uneven coloring of Lyptus wood proved an effective representation of the natural strata of the rocks in Luckstone’s quarries.
Location: Portland, OR
Market Sector: Civil / Aviation
Size: 1,000,000 sf
Year Completed: 2026
Architect: ZGF
Designed to welcome travelers into the heart of Oregon, the new PDX terminal transports passengers straight into nature. The Port of Portland had a clear mission for the expansion and approached the project with distinct goals: Keeping the terminal operational; prioritizing sustainability; creating flexibility and adaptability to allow for future innovations; and building an airport that transcends functionality and represents the best of the region.
ZGF joined forces with TimberLab, highlighted earlier in this document, to fabricate over 3.3 million board feet of Douglas Fir.
Entering the newly renovated terminal core, the stunning 9-acre mass timber roof invites visitors to take a walk among the trees. The roof’s undulating form boasts the history and the possibilities of Oregon’s forest product innovation by showcasing wood that was sustainably and locally sourced from landowners and tribes within a 300-mile radius of the airport. Hyla Woods, Skokomish Tribe, Anne and Richard Hanshcu, and the Nature Conservancy provided the beautiful Douglas Fir material for the lattice.
PDX stands as the apotheosis for what is possible when sustainable building projects are built with intentionality. The foundations of such sustainable design incorporate positive conservation, community, and equity. Each piece of wood used in the remodel can traced back to its forest of origin. The airport serves as a love letter to the small families, Pacific Northwest Tribes, and other landowners that contributed to land stewardship and local economies across the region.
The full stories behind the farmers, tribes, and mill workers that produced this beautiful timber can be found on TimberLab’s project profile on their website.
PDX is the first major airport in the U.S. with a mass timber roof. Inspired by the sun filtering through a forest, the lighting strategy consists of 49 skylights of different shapes and sizes that filter daylight through the mass timber roof’s lattice and large skylight openings. The expansive 9-acre roof is constructed from 3.5 million board feet of wood, comprised of three different wood products: mass plywood panels for the roof diaphragm, GLULAM beams, and 3 x 6-foot timbers for the lattice.
The beams were designed to eliminate the need for steel hardware; minimizing the need for metals, reducing cost, and aesthetically highlighting the natural beauty of the wood. The peaks and valleys of the roof design conceal a throng of systems within its structure and contributes to its seamless appearance. Adding to the grandeur of the design, 34 Y-shaped columns hold the 18-million-lb, 400,000-sq-ft roof in place.
Individual pieces of wood are visible in the PDX terminal roof, making the enormous structure feel like it has been handcrafted. This connects it to the human experience on a very grand scale. The GLULAM beam and lattice over story is a basket weave of arches and scalloped shapes, inspired by traditional weaving techniques indigenous to the region.