
2 minute read
IMRL in the Workcenter
By AMC Mark Pugh
The Individual Material Readiness List (IMRL) details specific quantities of aviation support equipment a command needs to support its maintenance requirements. Each IMRL contains equipment particular to a type, model and series aircraft, as well as equipment that can be used on multiple aircraft types; e.g., aircraft tow tractors and tow bars.
Advertisement
An average-sized squadron’s IMRL contains hundreds of support equipment line items; the aircraft intermediate maintenance department (AIMD), Marine Aviation Logistics Squadron (MALS) or Fleet Readiness Center (FRC) contains over 1,000 items.
In past assessments, the Naval Safety Center has found multiple issues with workcenter IMRL programs, ranging from workcenters retaining or not turning in broken or NRFI (not ready for issue) equipment – to maintaining many times the number of IMRL items actually needed. Additionally, we often find broken or unused parts collecting dust under a bench and many times are reported in a ready for issue (RFI) status.
Each command has an IMRL manager responsible for maintaining and updating the list. Workcenter IMRL Petty Officers or NCOs assist in this effort and tell the manager what the workcenters need to perform a job. It is their responsibility to inform the manager of any deletions, additions or corrections to the IMRL to ensure adequate equipment is available to support the mission. Properly managing the IMRL and expediting repair or replacement helps alleviate the risk of unsafe processes and potential workarounds. Workcenter supervisors should keep these responsibilities in mind when assigning the workcenter IMRL program collateral duty to junior personnel. Often, these personnel are tasked to visit other commands to borrow specific IMRL items that may not be available or are nonoperational. If your workcenter is maintaining excess inventory, lighten your workload and turn in excess items so it is available for others to access.
Frequently, items may have been issued to a command operating under a detachment concept. If this is no longer the case, work with your command IMRL manager to have your excess assets tailored to fit your current command’s operations. This will release critical IMRL items for other commands that may be waiting for them. Preservation is an option, but keep in mind the work that goes into maintaining records and performing preservation checks must be complied with. Good IMRL managers should consistently ask themselves these questions: Do we have enough people to maintain the IMRL assigned? Is there time available to properly perform preoperational checks when required? Do we need additional items to perform maintenance per the publications? If I am going to be away from my duties, who will manage my IMRL?
In summary, managing the IMRL is the workcenter IMRL manager’s responsibility. The command’s mission readiness and preventing unauthorized workarounds absolutely rely on a well-run program. Conducting these actions will ensure its success:
• Commands must take a closer look at their protocols and determine if there are breakdowns or workarounds in the system that are contributing to waste and unsafe procedures.
• Keeping qualified Sailors who have the experience and knowledge base to maintain the IMRL is important.
• Accountability is the name of the game. Excessive gear and a lack of appropriate personnel to maintain and manage the gear is not a best practice.
• You will rarely be issued additional IMRL items above your allotted amount.
• It takes your individual vigilance to ensure safety and there is no better time to start than now.
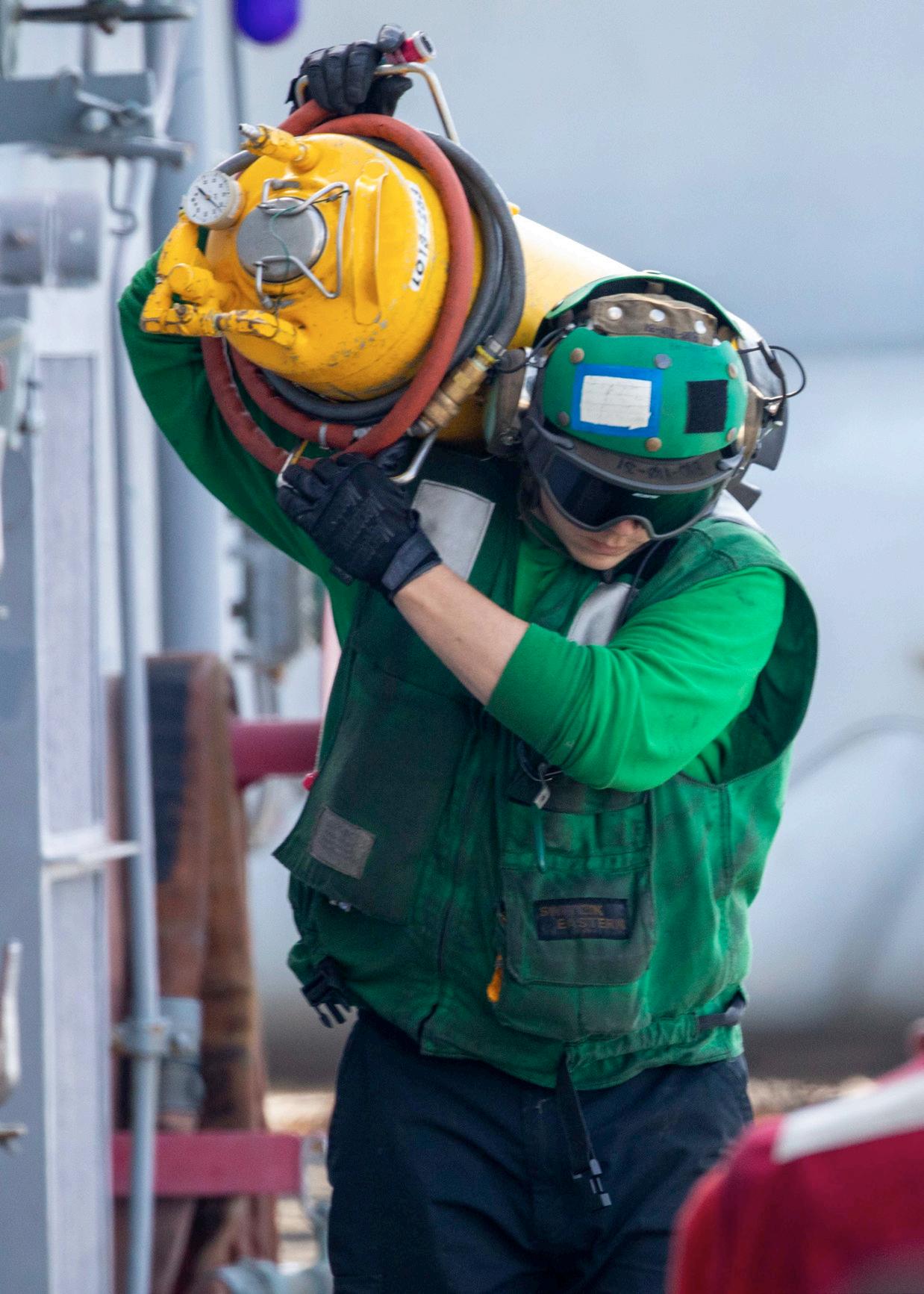