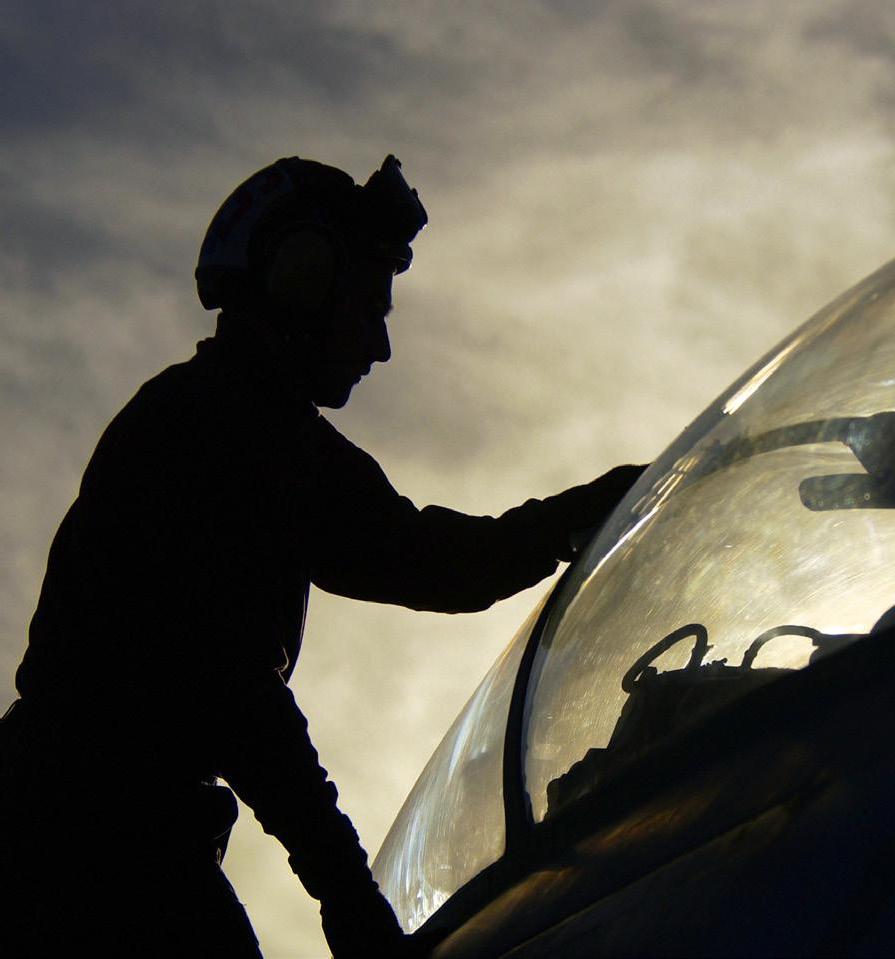
9 minute read
DO WHAT`S RIGHT
Scene Camera Operator: PH1 Brien Aho, USN
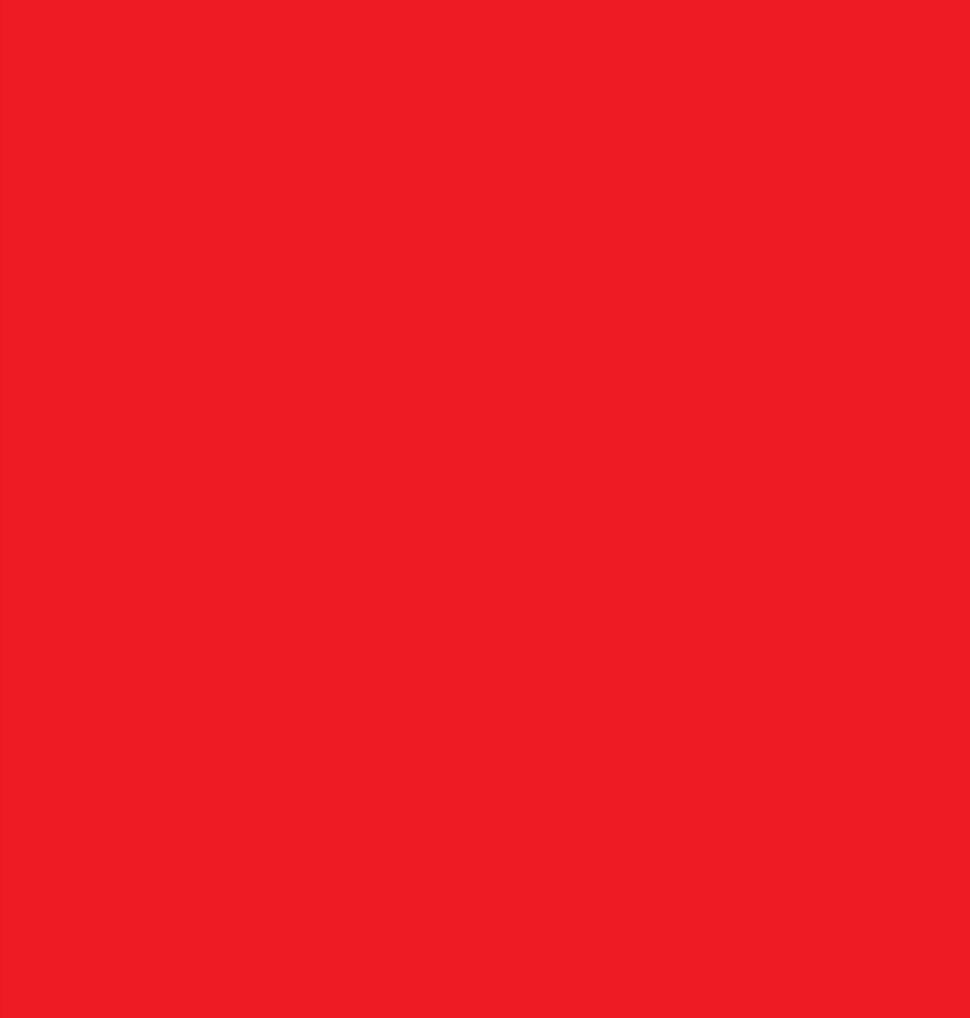
Advertisement
By AT2 EDWARD HOLM
It was a typical day. Our squadron had just finished a 10-month deployment and half the squadron was still on leave. After we did a FOD Walkdown, my LPO came back from the maintenance meeting and said we had a Radar Altitude (RADALT) issue on Aircraft 305 that required maintenance. Being a CDI for the last six, almost seven years, I knew what needed to be done. I was the only qualified tractor driver in the shop, so I went through the right steps necessary to check one out.
I grabbed a tool tag, checked it out in the tool log and headed over to airframes to check out their tractor. An AM3 in airframes signed out the tractor to me and gave me the 52 cards. I headed out to the front of the hangar where it was parked. As I walked up, one of our QARs was doing a pre-op on the tractor I just checked out. Before I even attempted my pre-op, he said, “Don’t use this tractor.” I quickly glanced around the front of the hangar to see another tractor that belongs to our squadron. Instead of taking the time to walk back in and check out this tractor, I performed the pre-op on it, hooked up the power cart and proceeded to aircraft 305 to perform the RADALT maintenance.
As we were wrapping up the RADALT on 305, the Line Division supervisor drove up in the tractor I had been told not to use. He parked the tractor in front of the nose of aircraft 305. He wanted to swap tractors to complete aircraft moves and mentioned the gas pedal might be sticking. Now at this point, I should have said, “No, I don’t want to use this tractor.” I should have informed him that QA just said the tractor should not be used. If I had said one thing, I could have prevented the mishap that was about to ensue. As a leader and a seasoned second class, I should have spoken up. The swap occurred and I hopped into this tractor that I knew had issues. The pedal stuck before I even switched it into drive.
Once in drive, I could feel the tractor inching forward even with my foot on the brake. In my head, I figured this was going to be an easy job and drove the tractor between two of our aircraft so I could hook up to the power cart. I rolled in front of the power cart as I’ve done so often and tried to put the tractor in reverse. I kept hearing the engine rev and rev, but the tractor would not go into reverse. At this point, I figured why not just go forward, between the two aircraft and take the tractor back to the hangar. I can’t get it to reverse, so why not just take it back to the hangar and get the power cart at a later time? I attempted to do this. As soon as I let off the brake, I felt the tractor lunge forward, impacting the starboard wing of one of our aircraft. This is one of the reasons we don’t drive in between aircraft. These are the precautions we get trained on. The impact stopped the tractor. I immediately shut it off and ran to Maintenance Control and told them what had just happened. In the coming weeks, what ensued was a series of investigations resulting in a Class B mishap with 1.4 million dollars in damages. Could this have been prevented? Of course, I should have said, “No, I’m not taking this tractor.” I should have informed the Line supervisor when he initially drove over to me that he shouldn’t be driving that tractor, to begin with.
I knew that tractor had issues and I shouldn’t have tried to drive it between aircraft. I could have told the Line supervisor, “No, it is not OK to take the good tractor I have.” I should have walked back into the hangar and checked out the good tractor as soon as QA told me the tractor from airframes was bad. Not following the correct procedures and even taking shortcuts can have disastrous consequences. The impact caused damage to the aircraft launcher, outer wing and aileron.
Weeks later, the Line supervisor and I had gone to DRB and we both lost our tractor qualification. We had to make multiple statements to QA, the command and safety. I had to go to medical to make sure I wasn’t under the influence. The number of hours wasted, which could have been utilized elsewhere, was damaging to the entire squadron.
Additionally, I damaged my reputation as a leader, undermining my leadership. How could I expect to be a leader if I don’t even follow the correct procedures myself? As leaders, we need to do the right thing and say “no” when you see something being done improperly. The proper procedures are there because these types of mishaps have happened before.
One missed step ends in disasters like this. Simple and easy actions such as tagging out broken GSE could prevent huge mishaps. The biggest thing I have learned from all of this is always to follow procedures, small or big, it doesn’t matter. Be a leader and do what’s right, never take anything for granted and do everything correctly by the book.
DO WHAT`S RIGHT
By AT2 EDWARD HOLM
It was a typical day. Our squadron had just finished a 10-month deployment and half the squadron was still on leave. After we did a FOD Walkdown, my LPO came back from the maintenance meeting and said we had a Radar Altitude (RADALT) issue on Aircraft 305 that required maintenance. Being a CDI for the last six, almost seven years, I knew what needed to be done. I was the only qualified tractor driver in the shop, so I went through the right steps necessary to check one out.
I grabbed a tool tag, checked it out in the tool log and headed over to airframes to check out their tractor. An AM3 in airframes signed out the tractor to me and gave me the 52 cards. I headed out to the front of the hangar where it was parked. As I walked up, one of our QARs was doing a pre-op on the tractor I just checked out.
Before I even attempted my pre-op, he said, “Don’t use this tractor.” I quickly glanced around the front of the hangar to see another tractor that belongs to our squadron. Instead of taking the time to walk back in and check out this tractor, I performed the pre-op on it, hooked up the power cart and proceeded to aircraft 305 to perform the RADALT maintenance.
As we were wrapping up the RADALT on 305, the Line Division supervisor drove up in the tractor I had been told not to use. He parked the tractor in front of the nose of aircraft 305. He wanted to swap tractors to complete aircraft moves and mentioned the gas pedal might be sticking. Now at this point, I should have said, “No, I don’t want to use this tractor.” I should have informed him that QA just said the tractor should not be used. If I had said one thing, I could have prevented the mishap that was about to ensue. As a leader and a seasoned second class, I should have spoken up. The swap occurred and I hopped into this tractor that I knew had issues. The pedal stuck before I even switched it into drive.
Once in drive, I could feel the tractor inching forward even with my foot on the brake. In my head, I figured this was going to be an easy job and drove the tractor between two of our aircraft so I could hook up to the power cart. I rolled in front of the power cart as I’ve done so often and tried to put the tractor in reverse. I kept hearing the engine rev and rev, but the tractor would not go into reverse. At this point, I figured why not just go forward, between the two aircraft and take the tractor back to the hangar. I can’t get it to reverse, so why not just take it back to the hangar and get the power cart at a later time? I attempted to do this. As soon as I let off the brake, I felt the tractor lunge forward, impacting the starboard wing of one of our aircraft.
This is one of the reasons we don’t drive in between aircraft. These are the precautions we get trained on. The impact stopped the tractor. I immediately shut it off and ran to Maintenance Control and told them what had just happened. In the coming weeks, what ensued was a series of investigations resulting in a Class B mishap with 1.4 million dollars in damages. Could this have been prevented? Of course, I should have said, “No, I’m not taking this tractor.” I should have informed the Line supervisor when he initially drove over to me that he shouldn’t be driving that tractor, to begin with.
I knew that tractor had issues and I shouldn’t have tried to drive it between aircraft. I could have told the Line supervisor, “No, it is not OK to take the good tractor I have.” I should have walked back into the hangar and checked out the good tractor as soon as QA told me the tractor from airframes was bad. Not following the correct procedures and even taking shortcuts can have disastrous consequences. The impact caused damage to the aircraft launcher, outer wing and aileron.
Weeks later, the Line supervisor and I had gone to DRB and we both lost our tractor qualification. We had to make multiple statements to QA, the command and safety. I had to go to medical to make sure I wasn’t under the influence. The number of hours wasted, which could have been utilized elsewhere, was damaging to the entire squadron.
Additionally, I damaged my reputation as a leader, undermining my leadership. How could I expect to be a leader if I don’t even follow the correct procedures myself? As leaders, we need to do the right thing and say “no” when you see something being done improperly. The proper procedures are there because these types of mishaps have happened before.
One missed step ends in disasters like this. Simple and easy actions such as tagging out broken GSE could prevent huge mishaps. The biggest thing I have learned from all of this is always to follow procedures, small or big, it doesn’t matter. Be a leader and do what’s right, never take anything for granted and do everything correctly by the book.