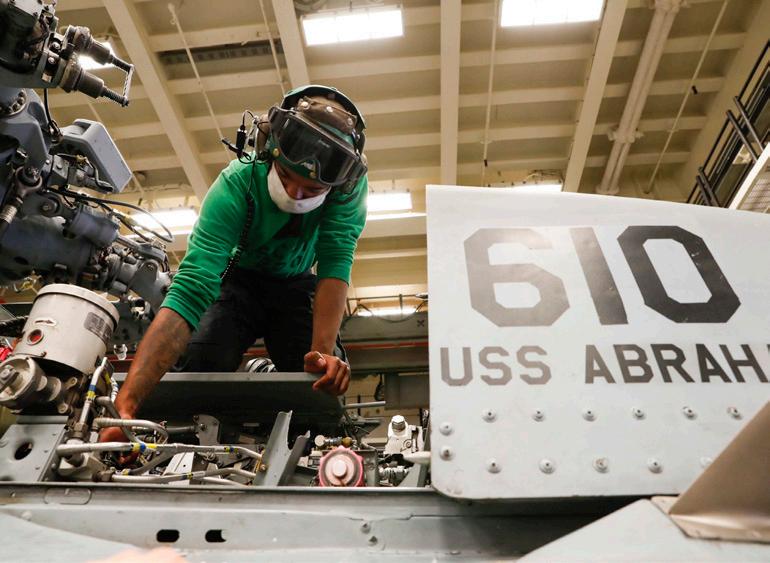
6 minute read
Not Your Kid’s Lego
Above:Photo by MC2 Christopher Janik Below: Photo by MCSA Oswald Felix Jr.
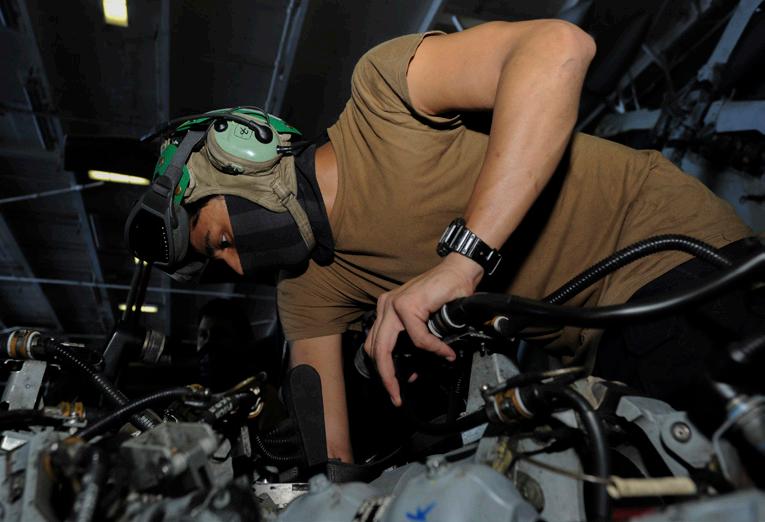
Advertisement

Above: Photo by MCSN Caitlin Flynn Below:Photo by Seaman Juel Foster
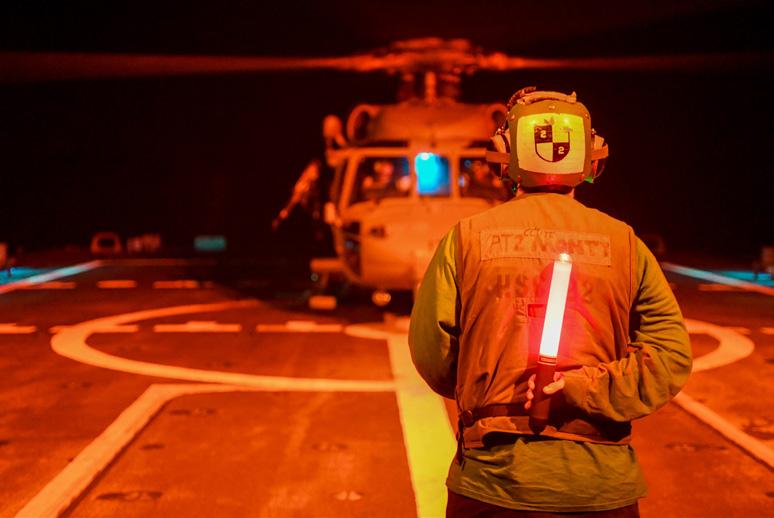
By LT Salmini Schuyler
Trident 615 was transferred to HSC-9 from another squadron. The aircraft had come out of preservation and required an extensive rebuild that took over a year. To get the aircraft up required that all special inspections (7-546 days), a Phase “D” inspection, an acceptance inspection, a post-planned maintenance interval inspection, post-preservation inspection and unscheduled major maintenances be complete. One requirement of the 546-day Special inspection is to remove, inspect and reinstall the flight controls. Along the way, Trident 615 encountered a few unexpected hiccups, but otherwise, the aircraft was ultimately rebuilt and ready for a functional check flight (FCF). The whole process, including FCF, lasted 12 months.
Trident 615 went begrudgingly into flight and did not want to stay there. Multiple maintenance issues arose over three months. One problem was a leaking primary servo. Replacing the servo requires detachment of flight controls. The work was assigned to the airframe shop and a seasoned aviation structural mechanic second class (AM2) was sent to the aircraft. He did what he had done many times before - pull out the inspection card and conduct the appropriate maintenance publication. While working, he noticed the lateral pushrod was installed upside down. He immediately notified maintenance control and the aircraft was grounded for further investigation.
The AM2 was well aware of the effects downing Trident 615 would have. The upside-down pushrod would diminish any chance of Trident 615 making an upcoming critical detachment. He knew that such an error would put the entire airframe shop in the spotlight and that someone could potentially lose his or her qualifications. Nevertheless, he was mature enough to make the tough call, without hesitation, preventing what could have been a fatal outcome. The discrepancy the AM2 discovered was potentially life-threatening due to a lack of redundancy in the control linkages. These linkages happen to be tough cylindrical rods connected by bolts, directing the 3,000 pounds per square inch servo pressure to change the pitch of rodor blades. Due to complex control mixing and helicopter aerodynamics, a missing input to the swashplate would render the entire rotor head uncontrollable.
Therefore, material or mechanical failure in the linkages would likely result in the total loss of the aircraft and crew.
The pushrod that was found upside down is nearly symmetrical. There is, however, an almost undetectable difference on the forward portion of the pushrod, which is engineered for two reasons. First, it helps drive some of the rotor head load into the airframe. Second, it aligns the pushrod against the bolt. When the pushrod was installed upside down, it caused the bolt to be loaded in an upward motion, taking the entire force of the rotor head.
Additionally, the pushrod was now able to rotate a few degrees due to a lack of alignment. There was no need to look at the engineering force diagrams to realize the potential for a mishap. Once the bolt was removed, it showed significant wear. Trident 615 had only been flying for three months. The regularly scheduled inspection of this bolt would not have taken place for another 16 months. The question remaining is, how did the incorrect installation occur? To answer this requires a closer look at the maintenance process. Flight controls must be installed in a systematic order -- in the correct orientation and position.
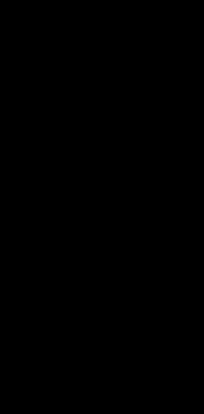
However, this must be done while in an awkward position. Imagine yourself lying down on top of the helicopter with your head rotated and your arms stretching to reach the controls below the swashplate. To double-check your work, you have to turn your head again to look at the computer’s image behind you, rotated 90 degrees from your orientation. Then, you are passed a control rod that is nearly symmetrical and has to match correctly with the image. The process is like putting a Lego set together with the instructions upside down and with identical pieces! The AM2 said, “It is very easy to install a pushrod the incorrect way. Sailors installing the pushrods for the first time have significant trouble with the correct placement of the parts. It takes a trained eye to see the minute differences that ensure the proper orientation.”
There are, however, several safety measures in place to prevent incorrect installation. Maintenance manuals have multiple cautions and notes that stress the importance of orientation. Additionally, each rod is labeled with stickers indicating “FWD”, “AFT” and “bolt” positions. However, the safety labels on the control rods were illegible due to the significant amount of wear.
Worn labels have, unfortunately, become accepted in the MH-60S community. They can be found throughout the fleet and seldom have replacements been written. Experienced airframers stress the importance of tagging and ensuring correct labeling on all parts as you remove them. One of our squadron’s most experienced airframers regularly uses a permanent marker to indicate proper orientation if a label is too worn to read. The AM1 admitted that this is a good practice but not directed explicitly in any publication or instruction. There are multiple sets of eyes on an aircraft between preflight, turnover, daily, periodic and special inspections before it flies a mission.
However, most of those eyes are not those of experienced airframers skilled at detecting discrepancies with flight control orientation. To help prevent future mistakes, a technical publication deficiency report (TPDR) is being written to ensure correct labeling or, better yet, add a prominent, color-coded mark.
Accepting something as seemingly mundane as worn labels almost led to a significant mishap. Blame does not rest on the shoulders of any one individual. Maintainers and pilots alike should be encouraged to question and correct ambiguous situations, like worn labels that fall below basic safety standards.
Thankfully, our squadron has encouraged individuals to speak up if they see the conditions for potential mishaps and in this case, it likely prevented the loss of an aircraft and lives. Routine acceptance of what may seem to be insignificant discrepancies can aggregate into much more significant and more serious casualties.
Luckily, the solution is simple: If you see something unsafe, say something. Do not accept anything less than the optimum. From the cleanliness of the quarterdeck to the quality of the tools in the maintenance shops, the little things done right keep our squadrons in the fight.
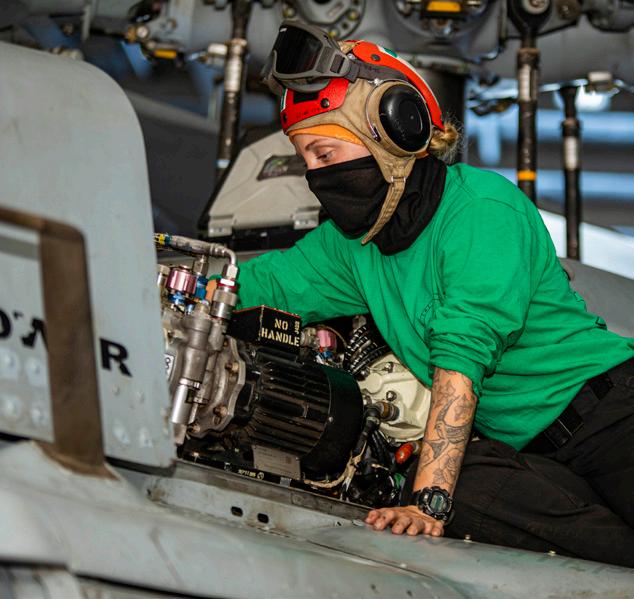
Above: Photo by MCSN Jacob Hilgendorf Below: Photo by Petty Officer 3rd Class Terence Frank Deleon Guerrero
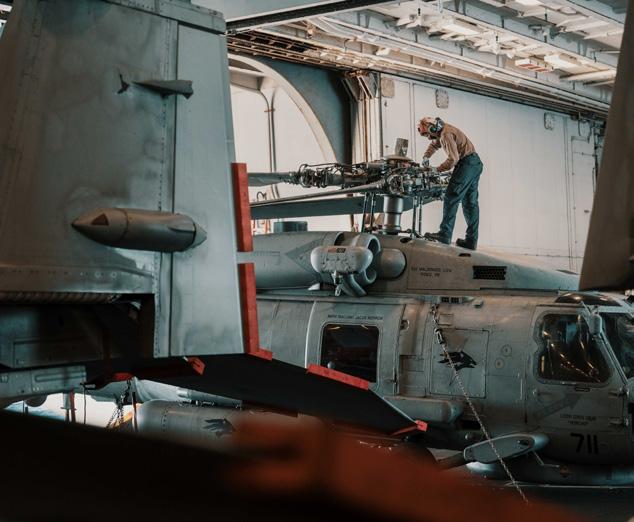