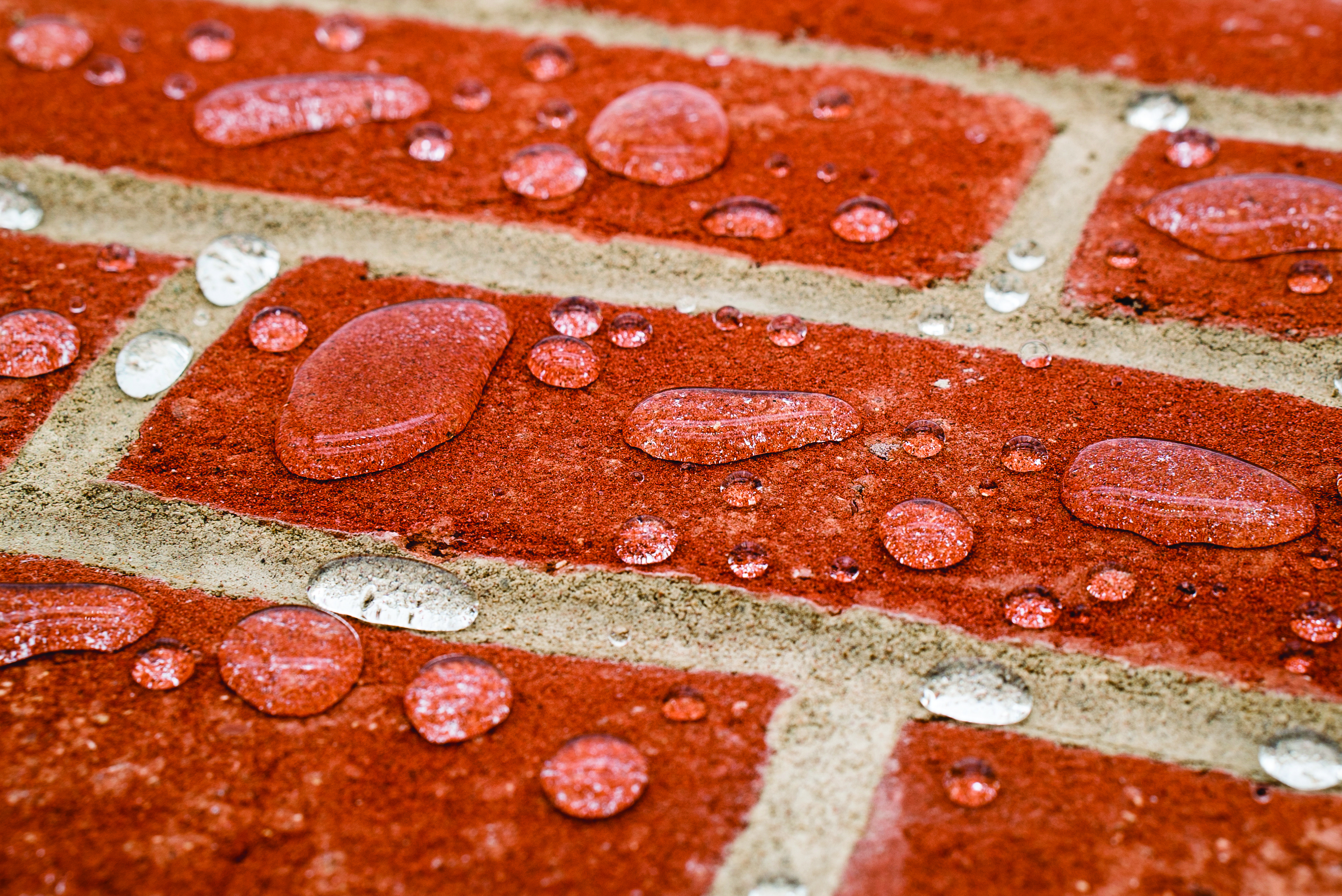
7 minute read
WE FIX LEAKY CHIMNEY SYSTEMS - PART III
WE FIX LEAKY CHIMNEY SYSTEMS - PART III
By Stuart Karanovich, Business Development Manager, SaverSystems
This is the third article in a three-part series covering water penetration and remediation in masonry chimneys. In the first two articles, we discussed water repellents and chimney crowns. In this article, we will discuss flashing. To read the first two articles, please visit issuu.com/ncsg and find the August and September issues.
When I spoke with Jim about writing these articles, I told him that our experience at SaverSystems has shown that if we covered these three areas, we would be able to help chimney technicians understand and solve 80-90% of the water issues they encounter in the field. There will always be that “exotic” water leak that will drive you crazy chasing it, but if you cover the crown, facing, and flashing, you will be successful in most cases.
What Is Flashing?
Broadly defined, flashing is an expansion joint between two dissimilar materials. Its purpose is to allow those materials, each having different temperature coefficients, to expand and contract at different rates without allowing water to penetrate, or to direct moisture out of a structure. The most common and obvious place this occurs is at the intersection of the roof and the chimney.
According to the Brick Industry Association (BIA), wherever you have an intersection of two dissimilar materials in a chimney structure, you should have flashing. This means that in addition to flashing the chimney/ roof intersection, flashing would be appropriate at the intersection of the crown and the chimney, as well as at the base of the chimney and the foundation if it is an exterior chimney. We will discuss these three areas later, but first let us examine some of the common materials we may find flashing a chimney.
Flashing Materials
Copper
Copper is an excellent choice for chimney flashing. It has the ability to be easily worked and shaped, coupled with the ability to withstand wide temperature ranges without buckling or warping. Copper will not usually react with mortar in a negative fashion even when embedded in wet mix. Copper flashing may stain surrounding brick, but this is not usually an issue.
Stainless Steel
Type 304 Stainless steel is also another suitable material for chimney flashing. While not as malleable as copper it can be formed and shaped, and provides excellent resistance to reaction with chimney materials as well as temperature and water resistance. The Brick Industry Association recommends that stainless steel flashing be no less than 0.01 inch (0.25mm) thick.
Galvanized Steel
While we see galvanized steel used as chimney flashing, its suitability for this purpose is marginal. The durability of galvanized steel as a flashing material is largely a factor of the thickness of the zinc coating in the manufacturing process. The thicker the zinc, the longer lasting the coating.
Problems arise though when bending galvanized steel of sufficient zinc thickness, as the coating tends to crack. This in turn leads to exposure of the base metal to the elements, and the associated rusting and staining of the chimney and surrounding areas of the roof. For these reasons, galvanized steel is probably best avoided as a chimney flashing material.
Aluminum
Aluminum is another material we see used as a chimney flashing. The newer aluminum flashing that I see being used is coated. This coating is designed to prevent the reaction that will take place between the aluminum and the alkali content in fresh mortar. These are defined as ionic salts and will cause deterioration of the flashing.
The Big Three
As I stated earlier, the Brick Industry Association recommends that wherever you have a juncture of dissimilar materials, you should have flashing to ensure that water penetration does not occur. We will concentrate on three areas in this article. They are the intersection of the base and foundation, crown and chimney, and the chimney and roof.
The Base/Foundation Intersection
If the chimney is an exterior chimney, and extends from the grade adjacent to the structure, then base/foundation flashing must be considered. Boiled down to low science, the base/ foundation intersection should be treated in much the same manner as an ordinary brick cavity wall. The BIA recommends that at this junction be flashed. The flashing should extend completely through the brick and angle upwards behind the external brick wall, terminating in a mortar joint of the internal wythe, with weep holes located above, but in close proximity of the flashing.
The Crown/Chimney Intersection
The intersection of the crown and chimney is often overlooked as an area in need of flashing. To be honest, I have been met with pretty stiff resistance and a few raised eyebrows when this subject is discussed in the field and at our training seminars. I have never personally seen a chimney flashed in this method, but as described on the BIA website, I have to ask why – it makes sense.
They recommend that flashing be placed under the crown, extend through the brick wythe and turn up against the exterior wall of the flue liner. The opposite end should form a downward drip edge above the exterior of the chimney face.
The Chimney/Roof Intersection
This is probably the most common type of chimney flashing we see. Where the chimney intersects the roof must be flashed correctly or we will allow water to penetrate to the interior. Both base and counter flashing are required to adequately protect the structure.
Base flashing should extend a minimum of four inches up the face of the chimney and roof line. The counter flashing should be lapped over the base flashing no less than three inches, and should extend through the chimney wall and be bent to an upward angle to collect the water which may drain down the back face of the brickwork on the exterior of the chimney. Proper sealing of all the joints and laps in both the base and the counter flashing is essential to ensure the integrity of the flashing.
Reality
After this discussion about what we might see in a perfect world, how many chimneys do we encounter in the real world that meet these standards? If you are like me, the answer is not very many. Too often, we encounter flashing that is improperly installed, covered in roofing cement with extensive cracking, or it simply was never installed.
The good news is that every improperly flashed chimney is an opportunity to solve a customer’s problem and to improve your bottom line. If you have the training and skills to remove and replace or repair metal flashing, this is obviously a good solution. If you do not replace metal flashing, or your customer is not willing to finance that type of repair, there is also good news.
Elastomeric Flashing Repair
If the flashing at the intersection of the roof and chimney is missing or damaged, an elastomeric flashing repair may be your best option. It has the advantage of being extremely durable, quick to install, and cost effective to the homeowner. Elastomerics are used because typically this intersection will show a fair amount of movement as the chimney and roof heat up and cool down, and when cured, an elastomeric will allow that movement while maintaining a watertight seal. Navigate to chimneysaver.com for more information.
Conclusion
Flashing plays an important role in the ability of a chimney to resist water penetration. With water damage being the number one threat to the longevity of a masonry chimney, doesn’t it make sense to check for proper flashings at every job and offer your customers viable solutions that will protect their investments in their homes and positively affect your bottom line? ■