
6 minute read
Signatures and WHS Requirements
COMPLeTInG SAFeTY DOCuMenTS, SuCH AS SAFe WORK MeTHOD STATeMenTS (SWMSs), HAS BeCOMe A PART OF THe eARLY MORnInG RITuAL FOR OuR InDuSTRY. BuT HOW IMPORTAnT IS IT TO ‘SIGn’ THeSe DOCuMenTS? WHeRe AnD WHen DO YOu neeD TO OBTAIn SIGnATuReS AnD WHAT FORMAT IS ACCePTABLe?
Must you sign at all?
In new South Wales, whether it is a SWMS, policy, JSA or toolbox talk, there is no explicit requirement for a physical signature to be included on any safety document or SWMS under the Model Work Health and Safety Act or the Work Health and Safety Regulations. There is a requirement for workers to ‘acknowledge’ a confined space entry permit, but that is about as prescribed as it gets. The Model Code of Practice for Construction Work (the Code) provides that an “SMWS may include details of workers who have been consulted on the SWMS, the date the consultation occurred and the signature of each worker acknowledging their participation in developing the SWMS”. Safety documents and SWMSs are not legal contracts or deeds, but they can be considered legal documents that are admissible in court. The Code does not express that signatures on SWMSs are a control measure; therefore, when considering the SWMS, the presence or absence of a signature will not be the smoking gun needed to address business owners’ non-compliance. However, the Code includes an example SWMS, which sets out the information that must be included, and other information that should be included. notably, the sample provides a space for workers to sign and date the document. While the Code does not mandate signatures on SWMSs, it is generally considered that an actual signature from the worker is evidence that they have: been taken through the SWMS, provided their feedback on the steps, and led to the person conducting a business or undertaking’s (PCBu) assessment that the worker understands the SWMS.
A code of practice is admissible in court proceedings as evidence of what is known about a hazard, risk or control, and to determine what is reasonably practicable in the circumstances to which the code relates. However, compliance with a code is not mandatory, providing that any other method used, provides an equivalent or higher standard of work health and safety than a code suggests.
Obtaining signatures AIR CONDITIONING AND VENTILATION DURING NSW/ACT BRANCH from workers is a good way to mitigate risk and show evidence of compliance. BUSHFIRES AND CORONAVIRUS
What format is acceptable?
HSeQ professionals have long used ‘wet ink signatures’, where workers sign with ink and paper, as a strategy to meet their obligations, especially in paperbased HSeQ Systems. The aims of collecting signatures include: Demonstrating consultation, representation, and participation (Part 5 Model WHS Act); Showing that review and revision of a control measure has taken place (Part 3.1 Model WHS
Regulations); Proving information, training, and instruction (Part 3.2 Model
WHS Regulations); and ensuring compliance with, and review of, a SWMS (Part 6
Model WHS Regulations). Before you decide to go out and give your workers writer’s cramp by signing every bit of paper you have, you may want to consider other options. Another perfectly acceptable method is ‘electronic signatures’, which are widely used as they reduce costs and increase efficiency. An electronic signature includes: Checking a box or a ‘click to accept’ button; Typing a name; Pasting an image of a signature; Drawing a name or initial with a stylus or by hand on a touchpad; or electronically signing with a service such as DocuSign, eSignature, and Adobe Sign. You don’t need to stop there; you can think out of the ‘sign here box’. Mobile apps that are password protected do not even need to be signed. Hitting the ‘submit’ button will usually provide a time and ID stamp, sometimes even with geolocation. That is even better than a signature. Apps can also extend beyond SWMSs to other safety tools. For example, you can record your toolbox talks on video using your trusty mobile phone. If everyone agrees to be filmed, there would be enough evidence to bypass the added requirement to sign as well. This will also allow you to review how well a toolbox talk was delivered. Developing online quizzes is one of the best ways of achieving compliance, as workers can complete the quiz to verify their understanding of instructions. We wrote and developed the neCA Redbook Quiz just for this reason.

Pre-Coronavirus, air quality was a high priority issue with bushfires and dust. We were told to: protect ourselves by staying indoors Reading tracking software, such as with windows and doors closed and one of the many features available avoiding outdoor exercise. on neCA’s Safety eLITe HSeQ system, adjust our air conditioning systems to recirculate the air and shut off fresh air supplies. is another superior method to signing. This sends, tracks and stores authentic records of everyone who should read and acknowledge It is worth noting that air quality in any documents or instructions. Canberra in recent months reached more than 22 times the hazardous rating. While last December, some Sydney suburbs had air quality more than 10 times the hazardous amount. Fast forward a few months and, in our new coronavirus reality, the advice is to improve ventilation. Consider other ways to increase the supply of fresh air; for example, by opening windows and doors. Improve the circulation of outside air and prevent pockets of stagnant air in occupied spaces by using, for example, ceiling fans or desk fans or opening windows. Turn off recirculation and use a fresh air supply in your mechanical ventilation systems. Although the risk of air conditioning spreading COVID-19 in the workplace is believed to be low, it is recommended, if you use a centralised ventilation system that removes and circulates air to different rooms, that you turn off recirculation and use a fresh air supply. However, you do not need to adjust air conditioning systems that mix some of the extracted air with fresh air and return it to the room as this increases the fresh air ventilation rate. Unless of course, you have to re-adjust the settings to turn the fresh air supply back on after the bushfire season. Also, you do not need to adjust systems in individual rooms or portable units as these operate on 100% recirculation. Good ventilation can help reduce the risk of spreading coronavirus, but it can also lower indoor air quality during the bushfire season, back-burning operation or dust storms. There has never been more demand to be able to adjust and control fresh air settings of indoor spaces. So, for operators and duty holders of indoor spaces on the East coast, to have maintained the best possible indoor air quality, you should have shut off your fresh air back in October 2019 due to the bushfires, and you should have opened it up to full around February/March 2020 due to coronavirus. With back-burning planned in the coming months you should consider how you are going to shut it off again. Operators of indoor air spaces should speak to their HVAC technicians on how best to adjust the fresh air settings depending on the outdoor air quality and the risks created by the pandemic. Adjustments may need to be made daily. Should you require any assistance or further clarification, please contact your local NECA Branch.
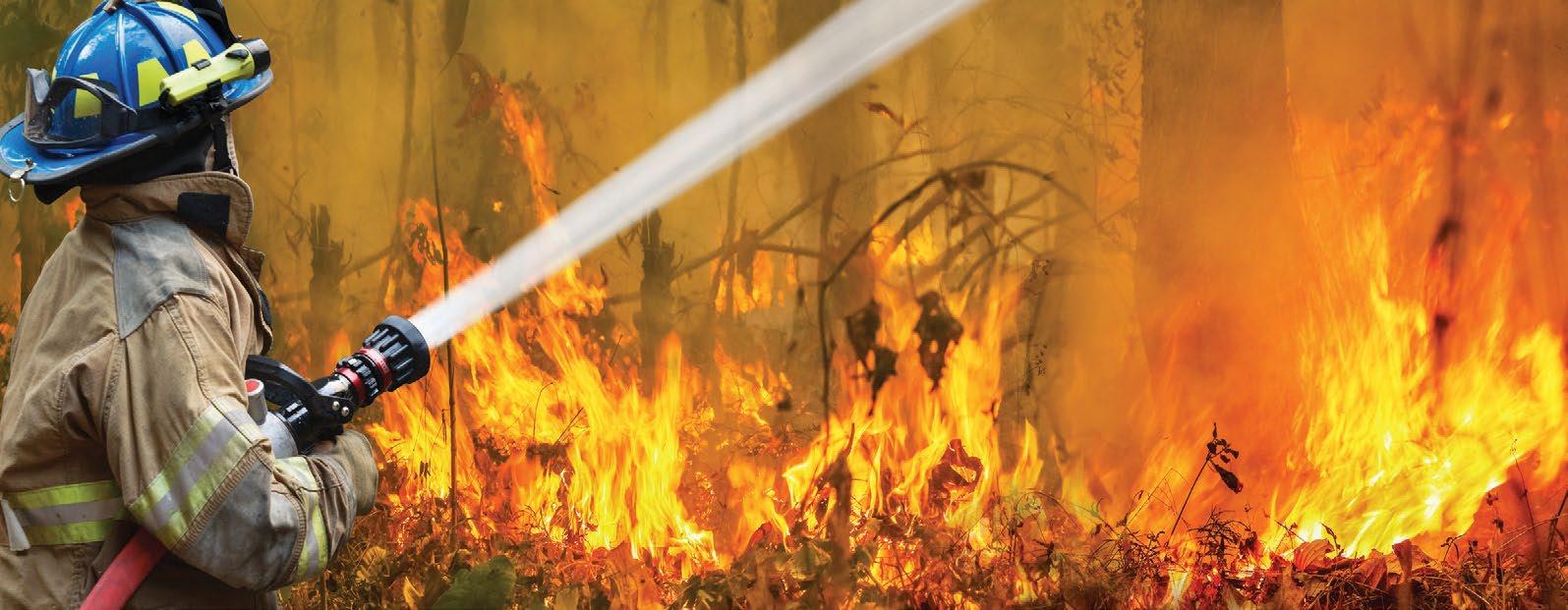
The key takeaway
It is critical that your workers fully understand the health and safety requirements of any work they are undertaking. Communicating, and importantly verifying, that your workers have been issued, read, and understood your safety documents can be achieved through several methods. We encourage you to review your options and decide what will work best for your business.
Owen Leslie Owen Leslie
WHS Manager, NECA Group WHS Manager, NECA Group owen.leslie@neca.asn.au 1300 361 099 owen.leslie@neca.asn.au