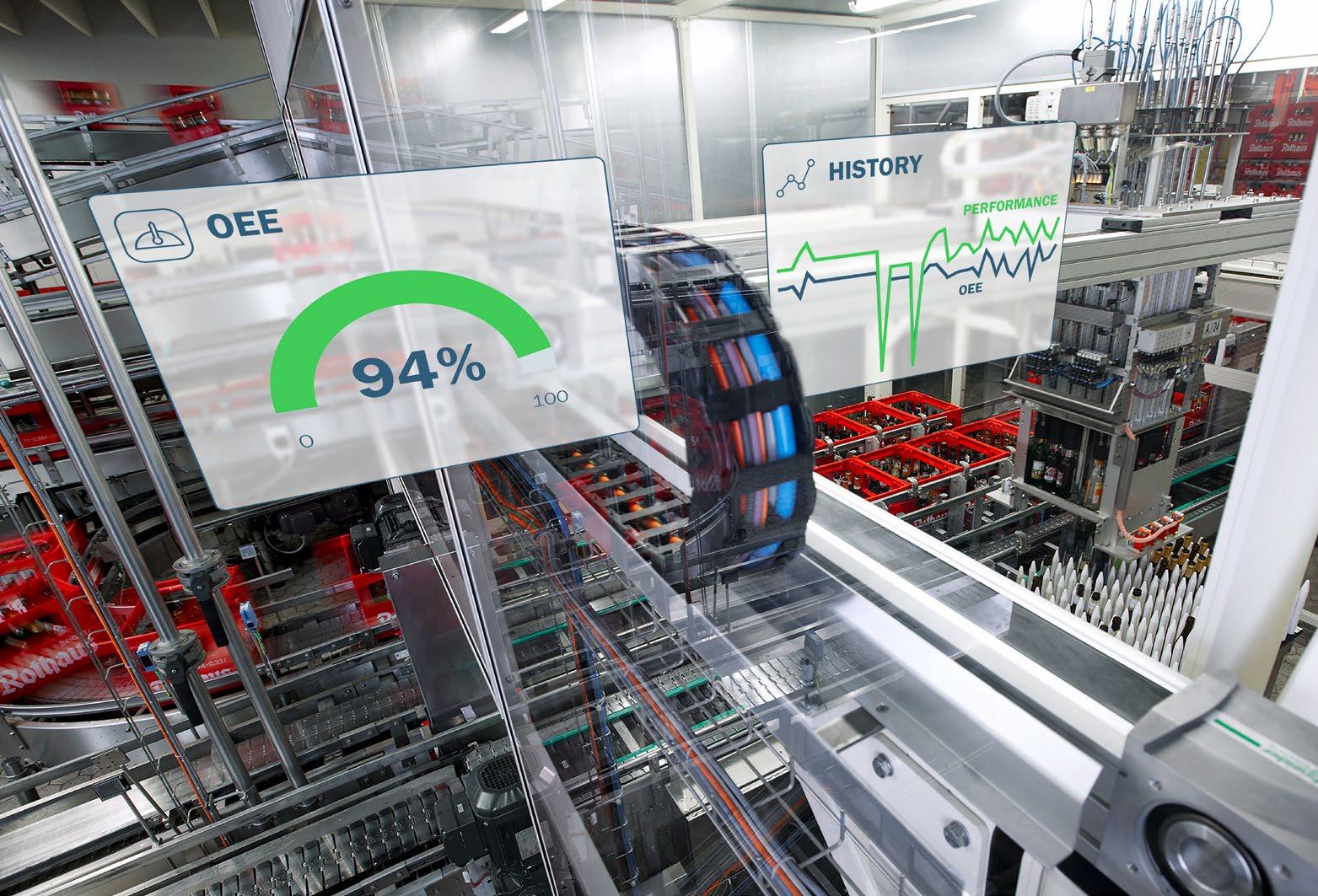
4 minute read
Leveraging Industry 4.0 for Digital Transformation
LEVERAGING INDUSTRY 4.0
FOR DIGITAL TRANSFORMATION
InDuSTRY 4.0, InDuSTRIAL InTeRneT OF THInGS (IIOT), SMART MAnuFACTuRInG, DIGITAL PLAnT, COnneCTeD InDuSTRY – nO MATTeR WHAT YOu CALL THIS neXT WAVe OF InDuSTRIAL ReVOLuTIOn, IT IS QuICKLY GAInInG IMPORTAnCe. THeReFORe, IT IS IMPORTAnT TO unDeRSTAnD WHAT IS InVOLVeD AnD WHAT BeneFITS ARe eXPeCTeD.
Industry 4.0, the next evolution in industrial processes, promises to deliver true integration of Information Technology (IT) and Operational Technology (OT), enabling dramatic improvements in efficiency while reducing costs. Where Industry 3.0 was all about automation, connecting devices, and determining what we could learn about the operations of business-critical equipment, Industry 4.0 is about applying advanced computer models to make more informed operational decisions. It’s less about understanding the behaviours and characteristics of individual machines and motors, and more about understanding interdependencies — cause and effect — of the entire complex production line, plant operation, and the plant itself. Getting there, however, will require industrial businesses to rethink and improve their existing infrastructure. IIoT is making way for more flexible models of accessing process and machine data. Generating and collecting data is an important aspect of IIoT, but this alone does not enable the full benefit of IIoT. There are other components to consider:
1. Smart connected devices that are IIoT ready, deliver an “advanced sensing system” that generates information with the first level of data analysis
completed by the device itself. Smart connected devices that are IIoT ready means embedding internet technologies like WIFI and web services natively into those devices.
For example, motor starters play a crucial role in driving critical infrastructure assets such as conveyor belts, pumps, compressors, agitators, fans and others. But despite their key operational role, traditional motor management approaches often fail to optimise performance. If a motor failure occurs, it can cause costly plant stoppages, damage to equipment and be a risk to people and the environment. In order to prevent such a failure happening, it is important that you have access to information about what the motor is doing and preventative measures that can be taken when a potential fault is detected. Motor starters are essential in providing information on motor use, and other devices like sensors and relays provide information on the device lifecycle. embedded digital services also become critical to support process optimisation. For example, the new series of Altivar Process drives or TeSys Island Digital load management system (smart DOL) with built in web technology standards, ethernet connectivity, intelligence and asset management or energy management features deliver additional contextual information, including real-time events, alarms, drifts, and historical data.
2. An edge gateway to aggregate data, display information and connect to
the cloud for advanced analytics. edge computing at the equipment level can provide more intuitive interfaces for monitoring and controlling operations, using the latest communication and automation technologies to detect and manage process issues across networks. This can include web-based access to operating parameters and interfaces with other systems. An edge gateway will aggregate data collected from various sources and deliver real-time business information to the right people at the right time. This is the key interface between the internet world and the process (the things). Devices such as Harmony HMIs act as an edge gateway ensuring a high level of performance and connectivity to address the critical needs of the IIoT platform.
3. Applications and services to further
analyse data and put it into context to help reach business goals. Analytics and services layers are increasingly cloud-based and merge and correlate data to assess current equipment status and potential problems. Digital applications and services are critical to end users, achieving the business performance gains promised by IIoT. Such applications and services include installation optimisation, energy management, asset management and protection and conditionbased monitoring among others. For example, with intelligent motor management solutions in place, maintenance teams no longer need to be close to asset components to troubleshoot. Abnormal situations can be addressed before they become critical and cause a production stop through pre-alarming that is based on pre-set behavioural parameters. The data gathered is combined and analysed with dedicated software solutions, such as ecoStruxure Asset Advisor, so that the future performance of the customer’s assets can be predicted. The total cost of ownership can be optimised with advanced analytics to identify potential failure modes via actionable web dashboards, timeline reports, and recommendations with operational support for people on site.
What approach can contractors take?
Familiarise yourself with the technologies available today and upskill your workforce.
Having control application and system integration capabilities in-house can be beneficial.
electrical contractors can now offer these monitoring/management services to facility owners as part of a post-construction services agreement, creating a new, recurring revenue stream. Look for opportunities to install smart devices so that the facility is future ready. For example, retrofitting with smart circuit breakers and smart motor starters instead of traditional methods will save energy, reduce environmental impact, reduce downtime and simplify installation and diagnosis.
Irene Kaur
Operational Offer Manager — Motor Control & Universal Enclosures Irendeep.Kaur@se.com
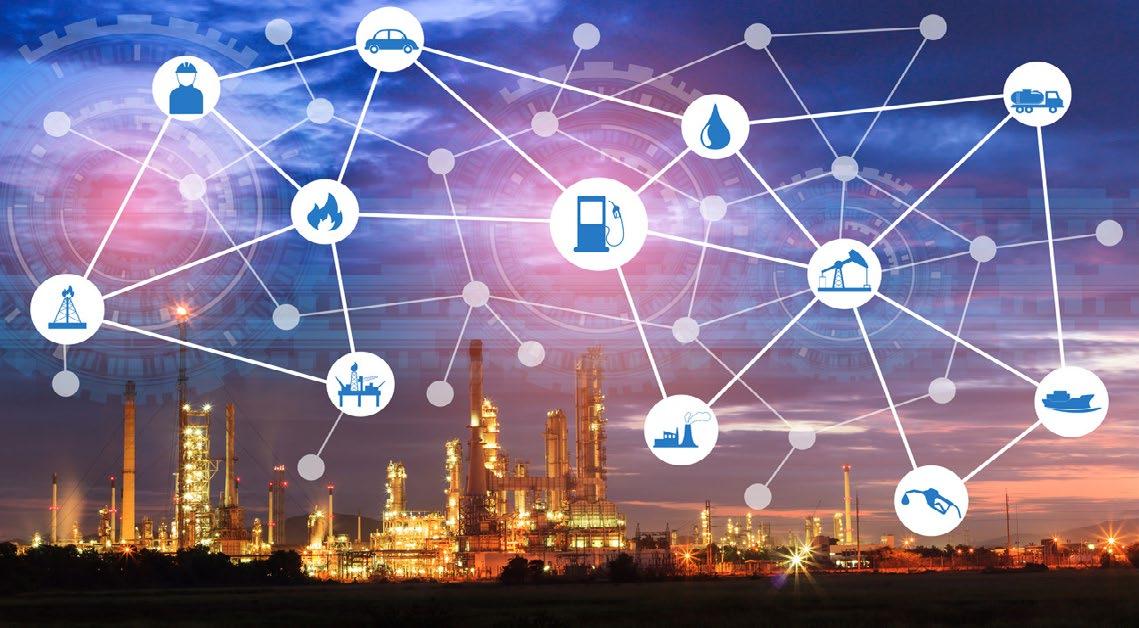