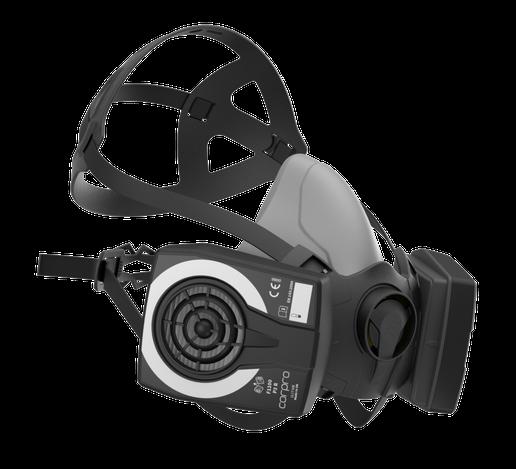
7 minute read
performance is key
DESIGNED FOR COMFORT, INCREDIBLE EASE-OF-BREATHING
BrEATHE EASilY, WiTHOUT COMprOMiSiNG prOTECTiON.
½ Functionality is essential. The
Half Mask features a dual mode harness; users can doff their mask without removing other ppE. The body of the HM 1400, has a built in a harness locking system, so users can retain the fit of their
Half Mask from wear to wear. ½ The breathing resistance of wearers’ equipment can affect their performance and comfort.
The masks are designed with a low burden airflow system, twin inhale valves and low pressure drop filters, to a create a system with ultra-low breathing resistance.
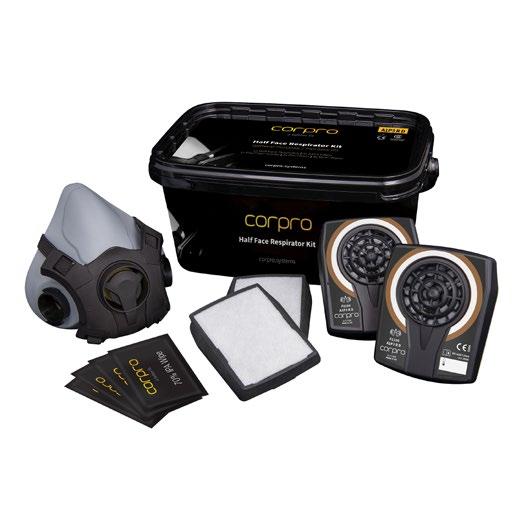
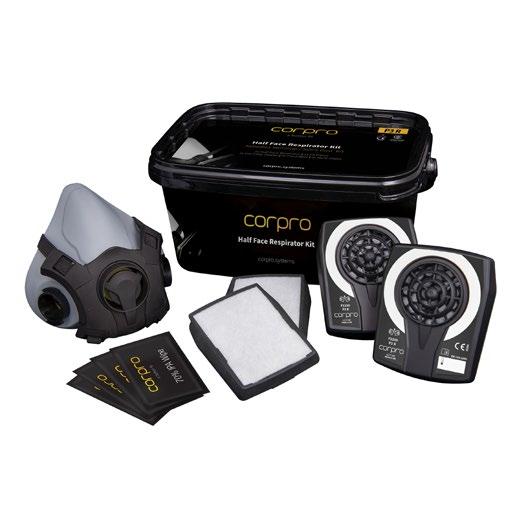
R1400AS Asbestos Removal / Silica Dust Kit
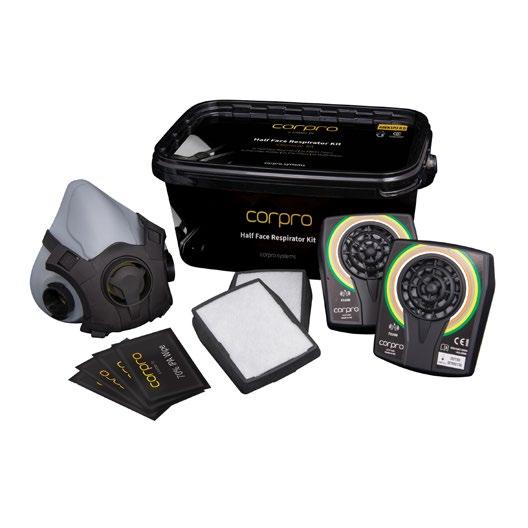
½ Half face mask (r1400) ½ 1 pair of p3 filters ½ 1 pair of pre-filter holders ½ 1 pack of 10 pre-filers ½ 4x multi-wipes
R1400CH Chemical Kit
½ Half face mask (r1400) ½ 1 pair of p3 filters ½ 1 pair of pre-filter holders ½ 1 pack of 10 pre-filers ½ 4x multi-wipes
R1400GP General Purpose / Painters Kit
½ Half face mask (r1400) ½ 1 pair of p3 filters ½ 1 pair of pre-filter holders ½ 1 pack of 10 pre-filers ½ 4x multi-wipes
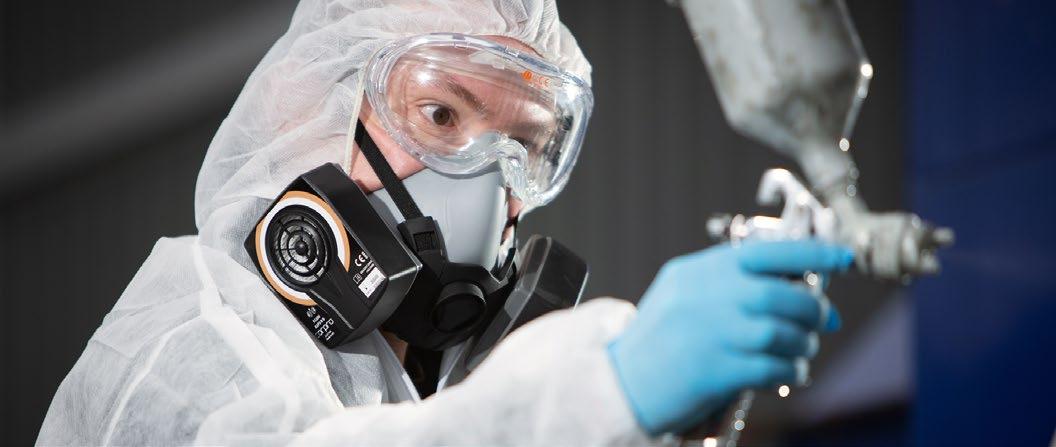
To view the whole range of the r1400 products, contact 1300 361 099 or visit safetyspecialists.com.au.
AWARD CHANGES RELATING TO CASUAL EMPLOYEES
THE FAir WOrK COMMiSSiON HAS COMplETED THE TASK OF iNSErTiNG CASUAl TErMS CONSiSTENT WiTH THE NATiONAl EMplOYMENT STANDArDS iNTO 151 MODErN AWArDS, iNClUDiNG THE ElECTriCAl, ElECTrONiC AND COMMUNiCATiONS CONTrACTiNG AWArD 2020 AND THE ClErKS priVATE SECTOr AWArD 2020.
pursuant to Section 66B of the Fair Work Act, employers (other than ‘small business employers’) must make an offer in writing to casual employees to convert to permanent part-time or full-time work if: ½ the employee has been employed for 12 months and ½ during the last six months has worked a regular pattern of hours on an ongoing basis.
There are exceptions based on reasonable grounds contained in Section 66C, but the employer is then obliged to give written notice to the employee as to why the offer is not being made and the reasons for it. Such notice must be given within 21 days after the end of the 12-month period.
Employers are reminded that casual employees must be given a copy of the Casual Employment information Statement (CEiS) as soon as practicable after the casual employee starts employment.
Employers are also reminded that under the Electrical, Electronic and Communications Contracting Award, they are required to apply the compounding approach when calculating the pay of their casual employees who work overtime. This means that the casual loading rate of 25% will apply to their ordinary hourly rate before the application of the relevant penalty rate. Therefore, the employer is required to pay time and a half, double time and double time and a half on the rate that is inclusive of the casual loading.
The Fair Work Commission has now clarified the overtime rate for casual shift workers effective from the first full pay period on or after 23 November 2021.
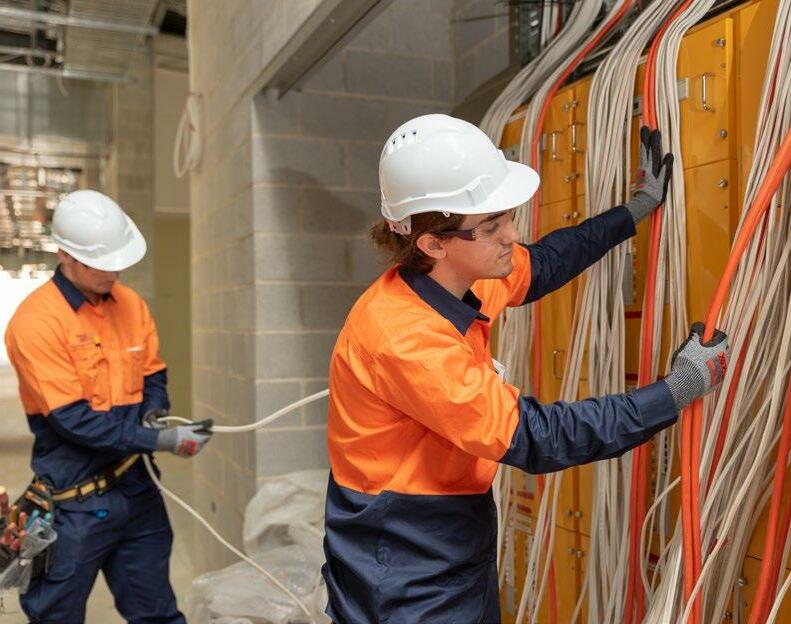
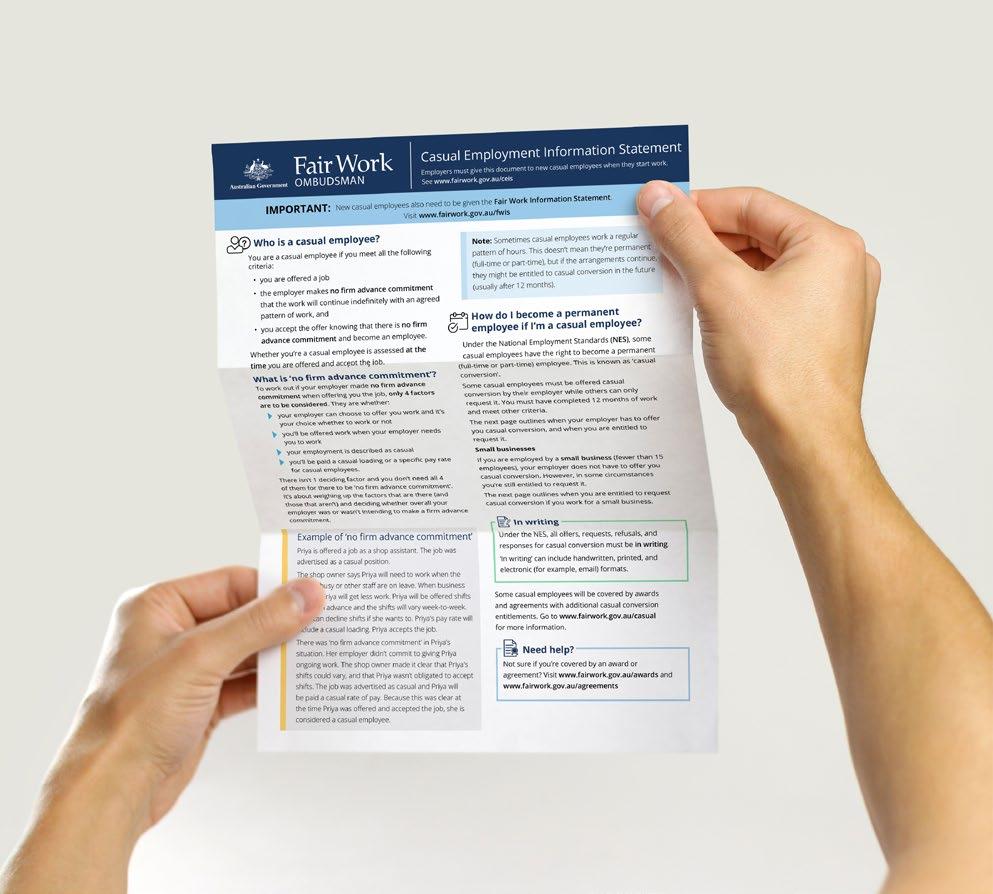
Disclaimer: This summary is a guide only and is not legal advice. For more information, call the legal services offered by your NECA branch.
CONTACT NECA FOR EXPERT LEGAL ADVICE AND REPRESENTATION
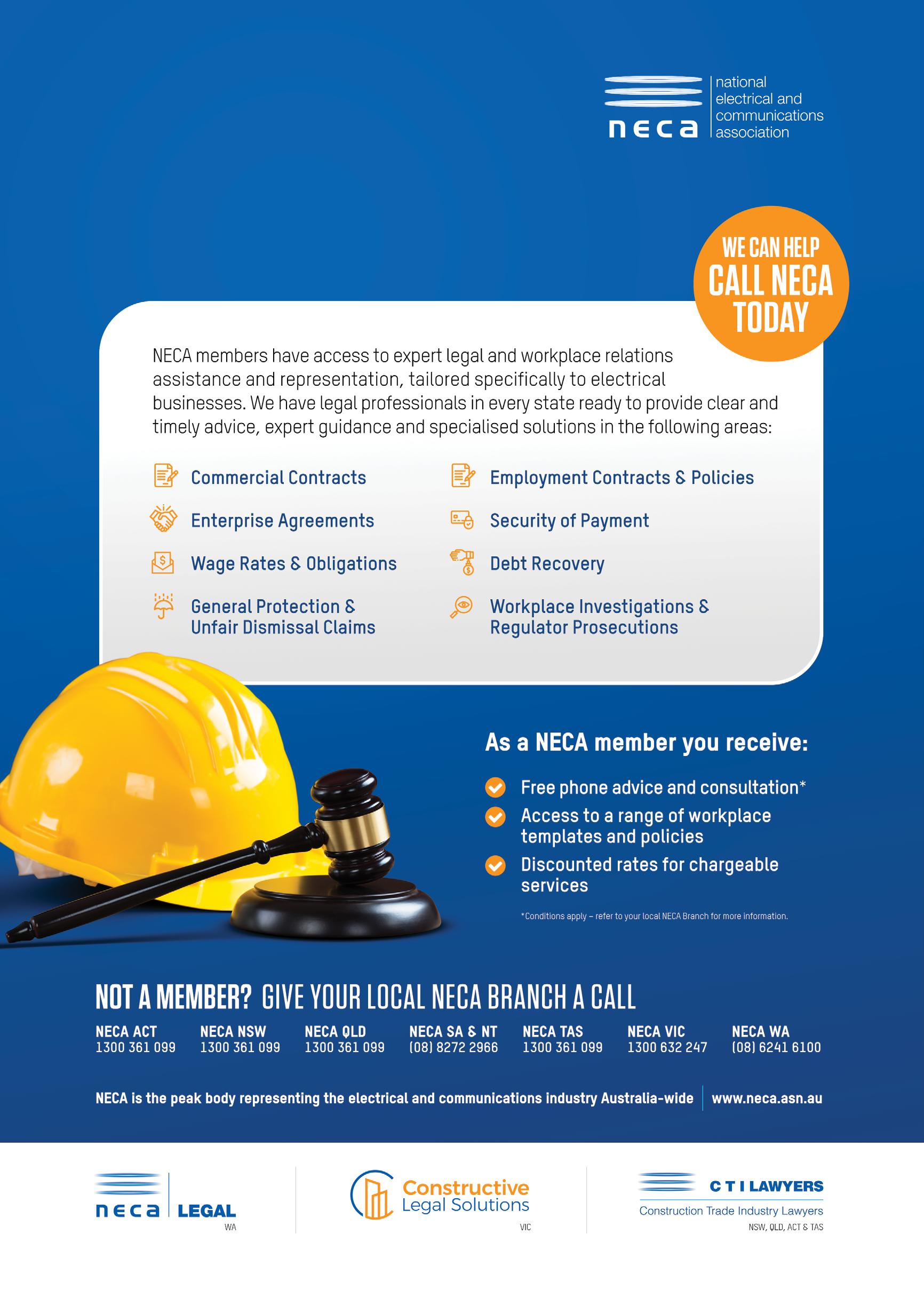
SUBCONTRACTING
A BUSINESS NECESSITY
Subcontracting work scopes, or entering joint ventures to execute projects, are common industry practices. Companies (referred to as the prime contractor) undertake these arrangements for a variety of reasons, the most common being:
½ To share the risk. ½ The subcontractor/joint venture partner may provide specialty services, expertise, or resources that the prime contractor may not have. ½ The prime contractor can undertake larger projects than they can handle on their own, earn a profit on the parts of the project handled by subcontractors and can grow their overall revenues. ½ The prime contractor can offer expanded and specialised services to their own clients. ½ Additional physical resources can be engaged with no long-term commitment.
Despite these obvious benefits, if there is a disconnect between the prime contractor and the subcontractor/joint venture partner with regards to workplace health and safety (WHS) expectations and requirements, the project most likely can expect cost and schedule overruns and a disharmonious relationship over the project duration. it is also important to note that the prime contractor has ultimate responsibility for the WHS performance of their subcontractors and joint venture partners.
Selection and alignment
From a WHS perspective, the two key elements for project success are subcontractor/joint venture partner selection and alignment.
Evaluation of a subcontractor/joint venture partner’s WHS qualifications and performance is a vital component of the selection process.
Their WHS program and procedures should be aligned with, and at least as stringent as, the prime contractor’s WHS Management System. This alignment will indicate the subcontractor’s ability to comply with the standards and requirements of the prime contractor, or in the case of a joint venture, the teaming agreement. Where a subcontractor/joint venture partner’s WHS system exceeds your standards, a clear alignment is still needed for a disconnect to be avoided. it should be clear that there is only one WHS system on site and all personnel, irrespective of their employer shall use that system. This is critical to success.
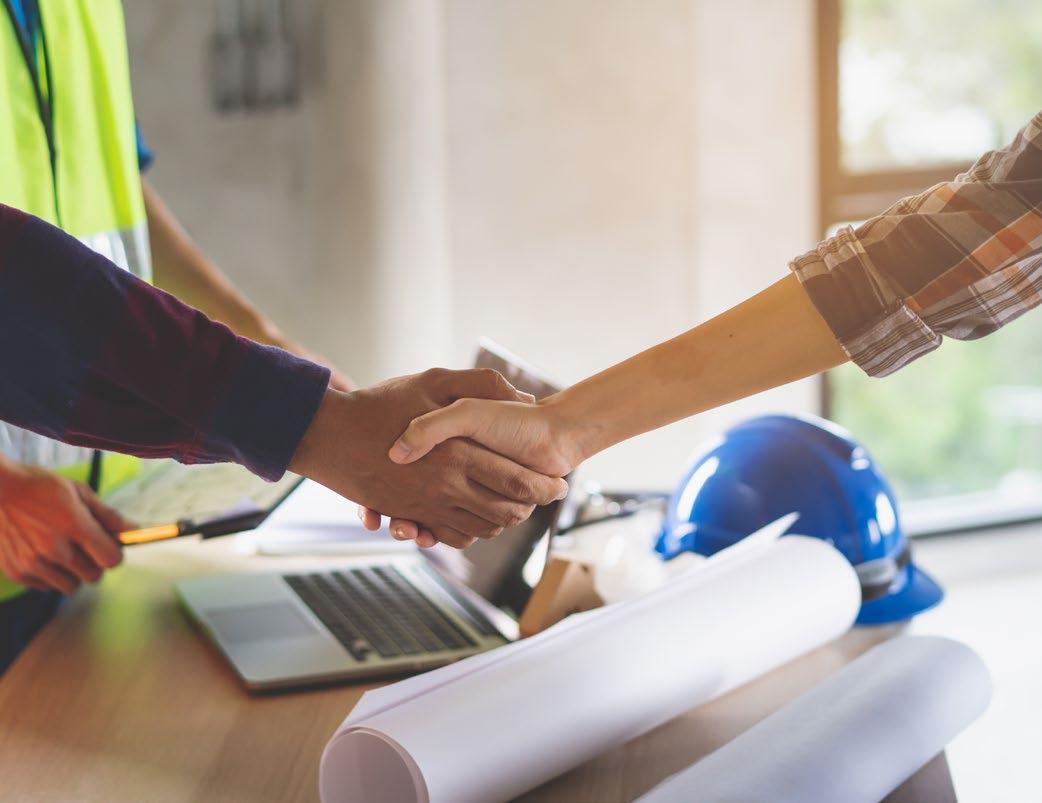
WHS performance evaluation
WHS performance evaluation is simply a statistical evaluation to benchmark the subcontractor/joint venture partner’s performance against the prime contractor’s performance. These evaluations are typically conducted using the previous three years’ data and may include elements such as: ½ Number of fatalities experienced. ½ lost time injury frequency rates. ½ recordable case frequency rates. ½ WHS regulator prohibition Notices. ½ Workers compensation claims experience rates or similar.
When using injury statistics as an evaluation element, it is important to consider not only how many incidents were experienced, but what corrective/preventative actions were taken to prevent a reoccurrence.
Expectations and requirements
potential subcontractors and partners need to understand exactly what the prime contractor’s expectations and requirements are, to enable them to correctly prepare their pricing, resource and execution schedules. Tender, expressions of interest and contract documentation must clearly define those requirements. A pre-bid meeting is beneficial to further facilitate understanding of the project conditions and WHS requirements. Gaining
this understanding before contract award will minimise the potential for change orders and contract variations after project commencement.
prior to the actual commencement of the work, a Kick-Off Meeting should be conducted to ensure that all the contract requirements are in place and to reinforce the prime contractor’s WHS expectations. Typical agenda items, depending on project scope could include: ½ Outline the job, including the construction sequence (purpose, layout, duration, and manpower). ½ review the expected site hazards. ½ Clarify the one WHS system on the site. ½ review the induction of new employees. ½ review accident/incident reporting requirements. ½ review project WHS plans and procedures and stress that they will be enforced on site. ½ Stress housekeeping is a high priority and will be enforced. ½ review first-aid/occupational health issues. ½ review relevant statutory
WHS requirements.
Relationships
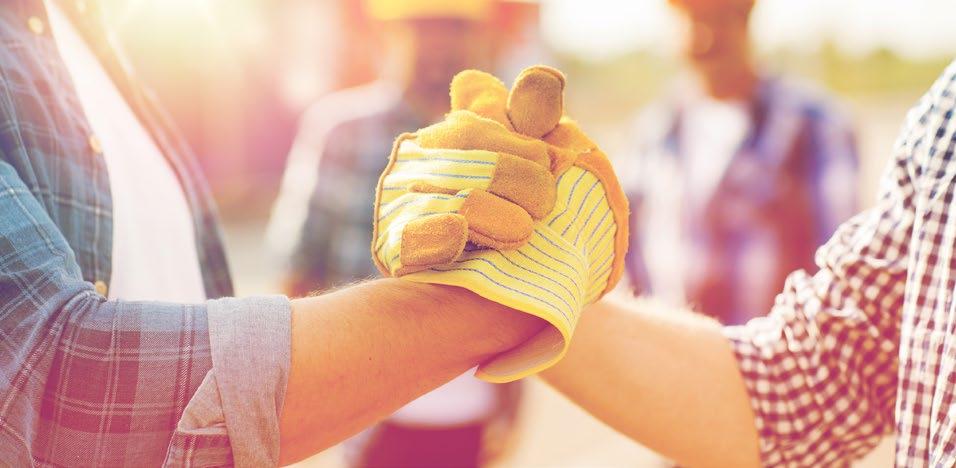
With proper selection of subcontractors and joint venture partners, companies can increase their ability to execute more diverse work scopes, leading to overall growth in their business. However, success goes further than just having robust selection and alignment processes in place. The relationship between the subcontractor/joint venture partner and the prime contractor is also an important factor for success, especially regarding the subcontractor. Treating the subcontractor as a true business partner can go a long way in accomplishing a healthy working relationship.
Brendan Craker
Safety Manager, ECA WA
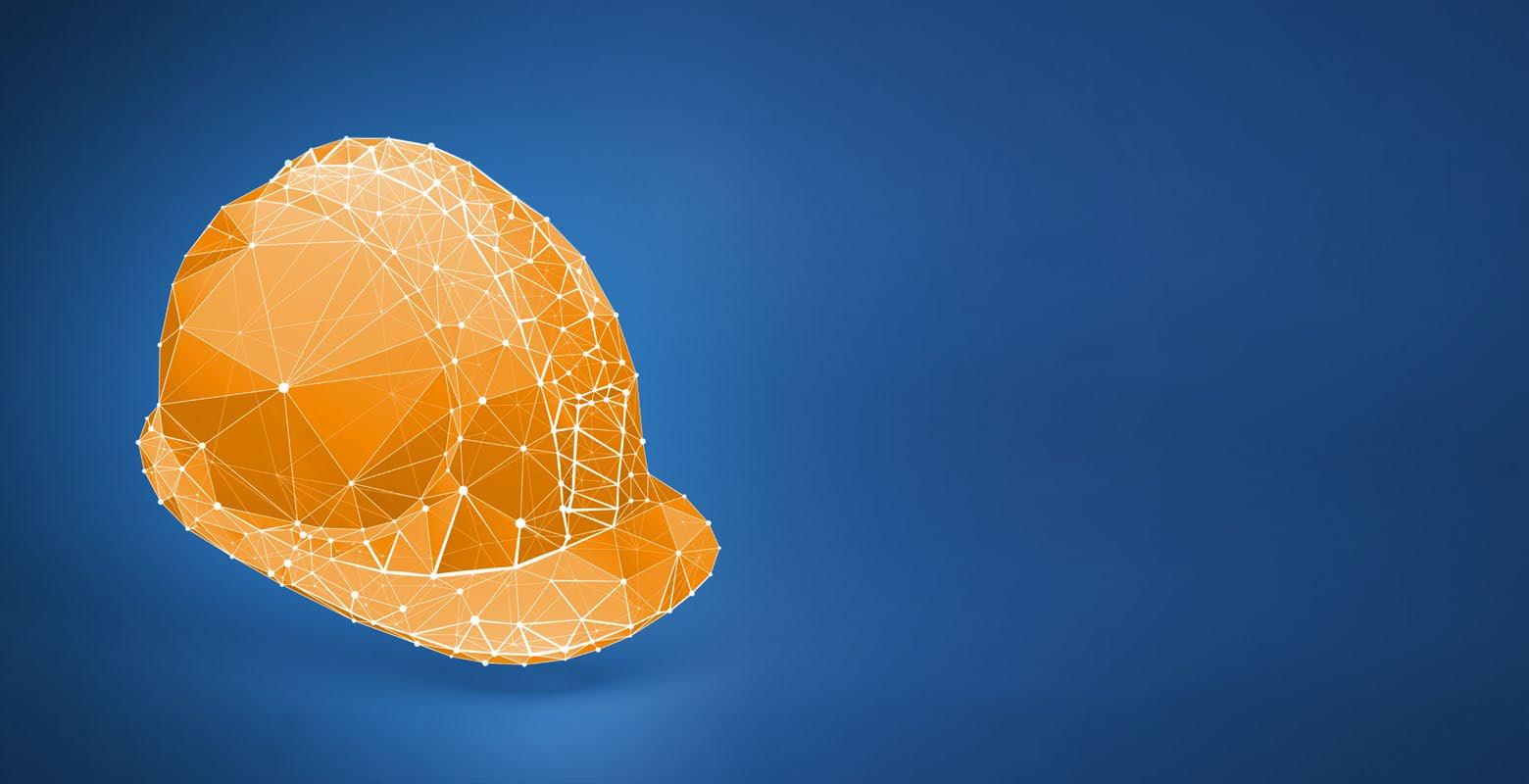
GET WHS EXPERT ADVICE
Safety in our industry is of the utmost importance. That’s why we offer a wide range of safety services for our members. let us help you stay on top of your workplace health and safety requirements.
If you have a WH&S question, get in touch with NECA in your state.
NECA ACT/QLD/NSW/TAS ............................................ 1300 361 099 NECA SA/NT ............................................................................ (08) 8272 2966 NECA VIC ........................................................................................... 1300 632 247 NECA WA ...................................................................................... (08) 6241 6100