
8 minute read
ASK A BOARD MEMBER
In this issue, we’ve asked board members from the Northeast Dairy Foods Association and Northeast Dairy Suppliers Association to tackle a question that many in the dairy industry are dealing with right now. We hope to make this a regular column addressing “hot topics” in the industry.
Advertisement
THE QUESTION: How do you see supply chain issues impacting the way you do business (either speaking broadly regarding the industry or more specifically regarding your sector of business)? What can be done to overcome these challenges in the short term?
“We’re seeing more open positions for logistics and supply chain managers, as I think employers have been forced to take a hard look at the critical nature of this part of their business. Those looking to hire logistics or supply chain managers really want to step it up and make sure to bring on someone with a specific set of skills in this area that will help their businesses run as smoothly as possible. The critical nature of supply chain management really came to the forefront during the pandemic when, for the first time in many years, people couldn’t immediately get some of the products or services they needed. We’re still feeling the effects of that, not only due to lack of product but lack of all the people who help get things to where they need to be. Everyone from CEOs to consumers are taking a closer look at how, when and where things come from as a direct result of experiencing shortages and delays. Mistakes in the supply chain can cause major cash flow problems to companies, and, in the case of the dairy industry, waste of perishable products. Some of this is still out of our control as the country continues to recover, but, from what I’ve seen, employers are taking a harder look at this aspect of their business and trying to find the most qualified people that they can for the good of their companies and their customers.” —Ryan Osterhout, chief operating officer and managing partner, KCO Resources Management, LLC, and NDSA treasurer/board member.
“Cheese was so popular during the pandemic, and cheese buyers want to continue to sell just as much again. We’re hoping that we see consumers continue to buy at that level, but it’s hard to read the demand right now. Retailers are really struggling with visibility to see what consumers are going to do for Q3, Q4 and into next year. But that’s a big question now that consumers are dealing with inflation, and, in the industry, we’re seeing challenges with high diesel costs, as well as packaging and manufacturing costs that are starting to creep up. On the international side of our business, we’re seeing challenges with shipping, delays
with exports, a shortage of containers for our powders, rolling appointments with our warehouse space and trucking challenges. One of the reasons it’s so difficult to predict what consumers are going to do in the future is that no one is quite sure what the labor pool is going to look like. That’s going to impact everyone. Some of our retailers are having problems keeping up at their own warehouses because of labor shortages and trucking issues, yet they are still holding us to the same expectations. On a positive note, I think the best part of these unprecedented times has come out of our people who, despite being tired after working so hard this past year, have stayed truly focused on their responsibility in helping to feed people during difficult times. We all felt like we were doing something for the good of others. We’ll see what the rest of this year and into next brings. Given the level of growth we saw during the height of the pandemic, we are trying to be reasonable with our expectations.” —Tom Herbick, plant manager, AgriMark Cooperative, and NDFA board member
“Our particular business, gable top ESL filling machines, has not really been affected by any supply chain issues, as our demand is fairly low compared to other manufacturers. However, others in the food and dairy industries are facing major shortages of stainless steel. Unfortunately, stainless steel has been rationed from the major suppliers, and they have had to pass on surcharges to customers. In many cases, lead times for their equipment have been extended well into late 2021 and 2022. There are no other major suppliers of stainless steel, so equipment manufactures continue to negotiate with suppliers for supplies until the issues with the stainless steel plants are resolved.” —Paul Knoerl, machines sales specialist, Evergreen Packaging Equipment, and NDSA board member
“Price inflation and inability to obtain raw materials affect the fluidity of a business in the present, but one consideration is the future and unseen risks. Valuation of exposures and insurance limits should be a priority. Building material costs are up. If you suffer property loss, you may be underinsured, which can void replacement cost coverage if there is a coinsurance clause. Additionally, your stock may be underinsured due to increased commodity pricing. Business interruption coverage is a segment of the property policy, and it covers financial loss to a company in a qualified event. A business interruption loss is complex and can be challenging to quantify. The increased cost of raw materials, building materials and labor shortages should be a consideration when re-evaluating the business interruption limit since those factors will increase cost and restoration period. Review contingency plans, contracts and purchase orders. Focus on the supply chain interruption exposure and have secondary suppliers. Consider near shore and domestic suppliers. Modify current contracts in case there are material changes in the way the orders are fulfilled. Use this event as an opportunity to consider what you would do if all of your computer network was locked up in a cyber attack. What if a specialty piece of equipment breaks down? How long will it take to replace and get running again? Do you have the right key spare parts in case of
an issue with equipment? Contingency plans should cover all potential issues that could come along.” —Lisa Bolduc, account executive, commercial lines, Brown & Brown Empire State, and NDSA board member
“We are seeing a huge problem in delivery that has only become worse this past year. Drivers are hard to come by, which affects raw milk pickup, hiring freight companies and finding drivers on our own. It just seems like there is way more tractor business needed, yet not enough people to drive the trucks. I think we, as a nation, should do things to encourage more people to want to become drivers, such as national advertising describing the great wages that can be made. Maybe even a “got milk?” style campaign would work. I think this will eventually help turn the tide.” —Aaron Jonas, director of business development, Mountainside Farms, Worcester Creameries, Inc., and an NDFA board member
“Supply chain issues are complicating the delivery of goods to almost every market in the U.S., including electronics, appliances, building materials, and food products, which includes food processing equipment. These delays are the result of an increase in consumer purchasing, spurred on by reductions in COVID-related restrictions and federal stimulus spending. As a result, imports have risen by almost 30% from previous years. This increase, coupled with a reduced workforce to transport goods once on shore, is leading to drastic increases in overseas transit times. The entire supply chain has been overwhelmed, with some ships anchored outside of ports for seven or more days waiting to be unloaded. Container shortages, longer delivery times and manpower shortages, in concert with the lack of availability of domestic delivery transportation, are leading to a quadrupling of shipping costs. With shipping issues predominantly out of the hands of manufacturers, one solution is to increase component inventory, but this cannot happen overnight. Further complicating matters is increased demand for processing equipment in 2021. This
The dairy industry faces enough challenges, insurance coverage shouldn’t be one of them. ASA can help make sure you’re covered correctly at a price that fits your budget.
• Property & Equipment • Environmental liability • Group health plans • Dental coverage • Vision insurance • Life insurance • Workers’ comp • Risk analysis • Loss control • And much more...
Give us a call today to learn how Agri-Services Agency can help protect your operation.
uptick in demand makes increasing inventories and reducing lead times an even slower process. With limited communication and information coming from freight forwarders, manufacturers may not know what has actually been shipped until late in the production timeline. This results in numerous production schedule changes and revised delivery dates to customers. This lack of stability causes extra work, increased stress on already tight internal scheduling systems and delays throughout the value stream, frustrating both manufacturers and customers. Longer delivery times for components leads to extended lead times for equipment manufacturing. Rest assured that equipment manufacturers are placing a priority on and putting a great deal of work into limiting the effects of this situation within the industry. Unfortunately, given current supply chain disruptions, some inconveniences and frustration are likely to be incurred.” —Melissa Fryer, sanitary heat exchange business development manager, Alfa- Laval, and NDSA vice president/ board member

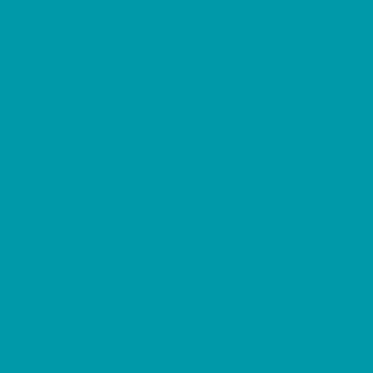
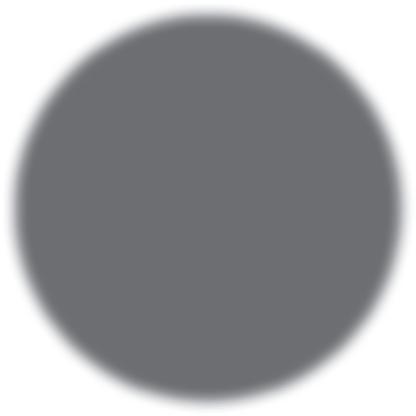
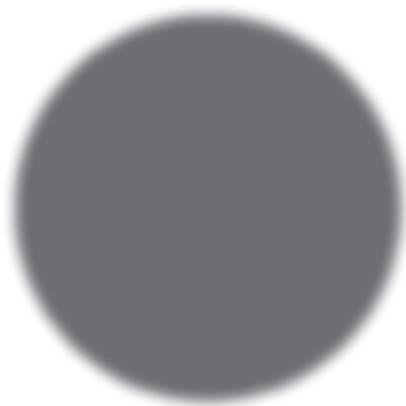
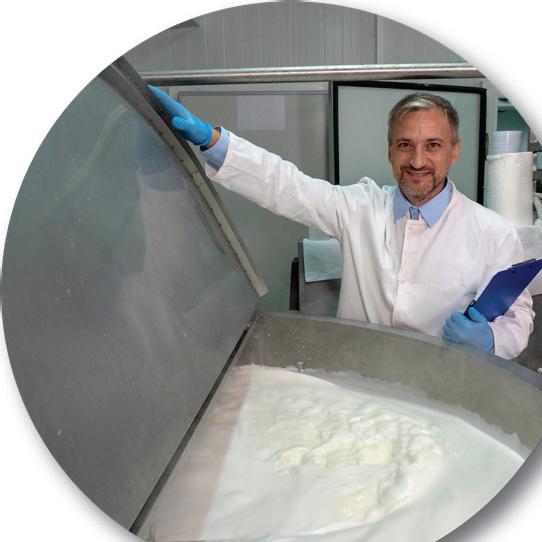
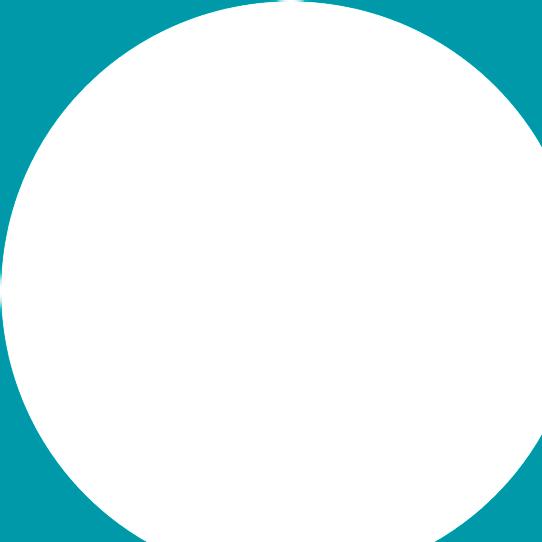
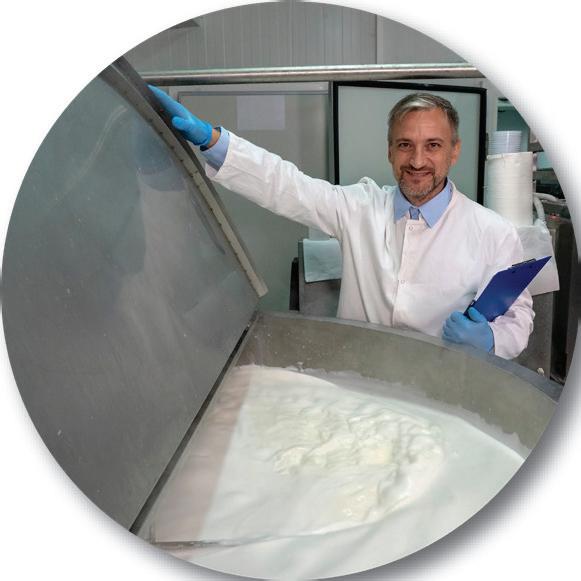
Phone: 877-466-9089
agri-servicesagency.com
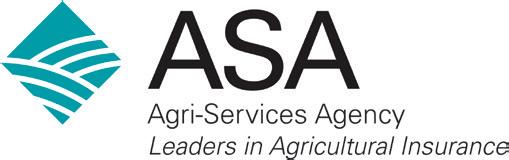