
6 minute read
INSPECTION, CODING & MARKING
Automation and digitalisation offers significant advantages
COVID-19 is creating major challenges for industrial companies. Food Manufacturing Africa looks at how digitalised and highly automated production can react to current and future challenges with the required degree of flexibility.
AS PART OF Siemens’ Digital Enterprise Virtual Summit, respresentatives from numerous companies from the discrete and process industries discussed strategies and technologies for future success under these new conditions.
The focus was on topics such as the horizontal and vertical integration of the value chain with simulation and optimisation from product creation through to servicing and from field level to the cloud. Other topics included online and remote solutions as well as edge and cloud computing, additive manufacturing, industrial 5G and artificial intelligence.
The Digital Enterprise Virtual Summit had around 12 000 registrations from customers and partners with 6 300 live attendees on the to preview and adjust labels digitally. It is also improved by a large intuitive touchscreen, which helps operators work more quickly.
With downtime, rework and recalls eating into profits, manufacturers must minimise these elements. The 2200 Series Print & Apply (P&A) labelling system for cases and pallets can save up to six days of downtime per year.
Traditionally, labels have been created and stored away from the production line. Untrained or distracted operators can make mistakes by picking the wrong product label and/or inputting the wrong data from the remote location (e.g. in an office or separate line PC). With no label preview function at printer level, mistakes can only be spotted after printing has started, resulting in day. The summit is now also available to be viewed on-demand at http://www.siemens. com/digital-enterprise-summit.
“Digital and automation solutions proved its worth during this crisis. Companies already invested in digitalisation were better equipped to handle new requirements, such as scaling back or ramping up production. These technologies will ensure that companies can react particularly effectively to crises and changing market requirements because they can adjust their products quickly and flexibly," explains Klaus Helmrich, member of the board of Siemens AG and CEO Digital Industries. “This flexibility is also the next step toward autonomous production processes.”
Siemens is integrating future technologies production stops and rework.
The Production Interface minimises scope for such mistakes and accelerates changeovers. It also makes case and pallet labelling less resource-intensive to manage, freeing up operators to do other, higher priority activities.
The improved storage capacity means labels are effectively stored en masse at printer level with limited image editing capabilities, protecting layout and data integrity, while increasing speed. Enhanced connectivity also makes it easier for label formats and data to be retrieved, on demand, from a remote location directly to the printer via the CoLOS information management system. Incorrect label selection by operators can also be eliminated by enabling keyboardfree label selection and variable data such as artificial intelligence, edge computing and cloud technologies, additive manufacturing or industrial 5G into its digital enterprise portfolio and helping industrial companies to work under these new conditions and to meet the requirements of today and tomorrow. Klaus Helmrich concludes, “No company can meet the current challenges on their own. It's all the more important that industrial companies act in ecosystems. Stakeholders - developers, users, partners and integrators - can bring their strengths and thus increase the value of these ecosystems. •
Production interface minimises case and pallet labelling downtime
Markem-Imaje’s 2200 Production Interface reduces the risk of rework and recalls by minimising the scope for operator error.
DOWNTIME IS REDUCED by the ability
Siemens – www.siemens.co.za updating through a connection to a handheld barcode reader - linked to a production manifest. The Production Interface’s large touchscreen shows exactly how variable content will appear on the eventually printed label. If needed, operators can easily make six types of minor adjustments, such as label position and print contrast, digitally via the interface. In other labellers such setting changes can be so difficult to access that operators commonly resort to manually moving the printer product sensor which can result in equipment damage and personal injury. Available in 261mm or 396mm touchscreens, colour-coded printer statuses are more visible at a distance so problems can be spotted and addressed without delay. •
Markem Imaje – www.markem-image.com
Potato processing line feels the Veryx difference Key Technology has teamed up with Bem Brasil, the largest potato processor in Brazil, to add a new state-of-the-art potato strip processing line to its facility.
THIS MULTIMILLION-DOLLAR purchase includes six Veryx digital sorters, an ADR Exos automatic defect removal system, three Sliver Sizer Removers and 57 Iso-Flo vibratory conveyors on a line designed to process 30 metric tonnes of frozen French fries per hour. Bem chose to partner with Key to maximise food safety and consistently meet final product quality specifications while improving operating efficiencies and increasing yield. “We selected Key for two primary reasons – their leadership in our industry and our trust in the company and their solutions,” Walter Takano, foreign trade manager at Bem Brasil points out. “Our confidence is based, in part, on years of experience with their Iso-Flo shakers on our other lines. To learn more about their Veryx sorters and ADR systems, we visited Key and then travelled to see the equipment operating at major potato processing facilities in North America and Europe. Overall, Key's expertise and the reliability of their technology impressed us." Key will equip Bem’s Veryx sorters with its full suite of sorter intelligence tools as well as top- and bottom-mounted sensors to achieve full-surface inspection. The sorters immediately before packaging will also feature Key's patented Pixel Fusion technology to find and remove even the most difficult-to-detect FM and defects immediately before packaging. Images of FM will be time-stamped and archived for retrieval utilising Key’s FMAlert feature. Veryx combines all camera views into one all-surface analysed object, which enables the sorters’ patented Sort-to-Grade (STG) software to automatically maintain final product specifications for both defect and/or length profile without operator intervention to increase yields and eliminate mechanical length grading. The sorters’ Information Analytics software exports real-time individual object data, allowing Bem to collect, analyse and share big data across the enterprise to reveal patterns, trends and associations, which can help optimise processes. “Bem is a prominent potato processor in Brazil, committed to becoming a global leader by investing in state-of-the-art technology as they grow. We are honoured that they have decided to partner with us,” said Bret Larreau, director of InterCon Sales - Latin America and Asia Pacific at Key Technology. “Before they selected their suppliers, they took a close look at what other world-class French fry facilities are doing. The real-world examples of yield increases, food safety practices and process optimisation achieved using tools such as our STG, FMAlert and Information Analytics, plus the reliability and consistency of our VERYX platform made a compelling impression that led to securing this business. Takano concluded, “For us, the single most important thing is taking good care of our consumers. Working with Key, we’ll ensure we produce the ideal final product quality. At the same time, we expect to increase yield and reduce operating costs.” • Key Technology – www.key.net
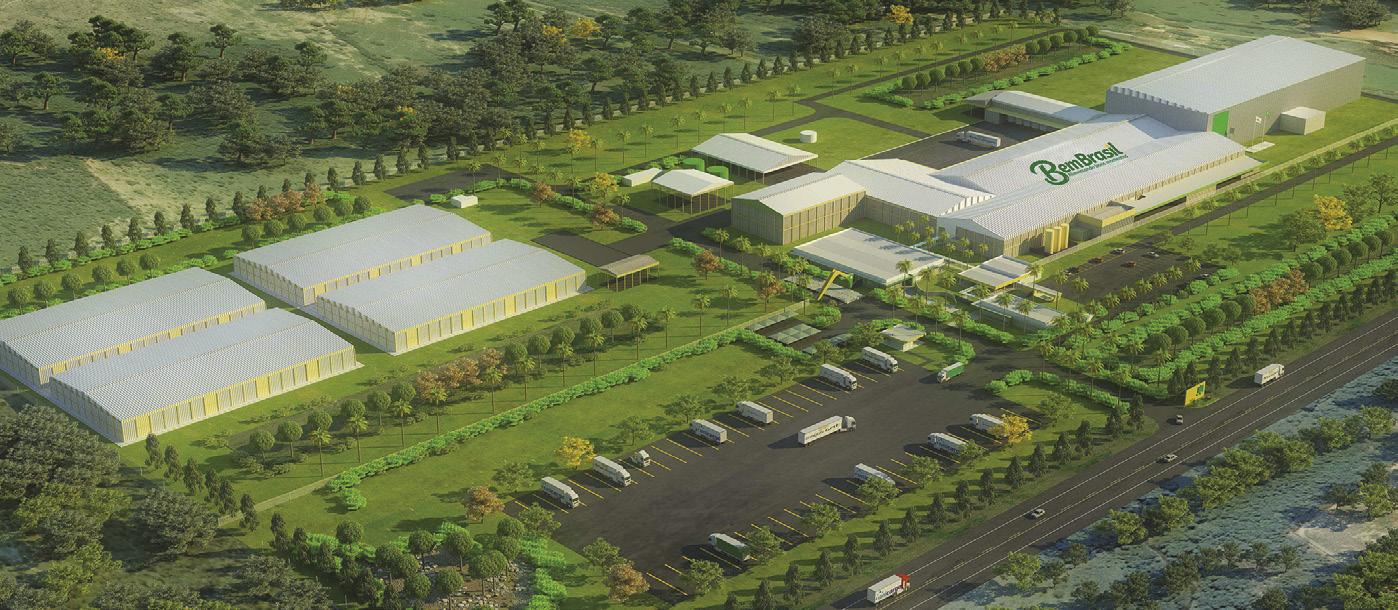
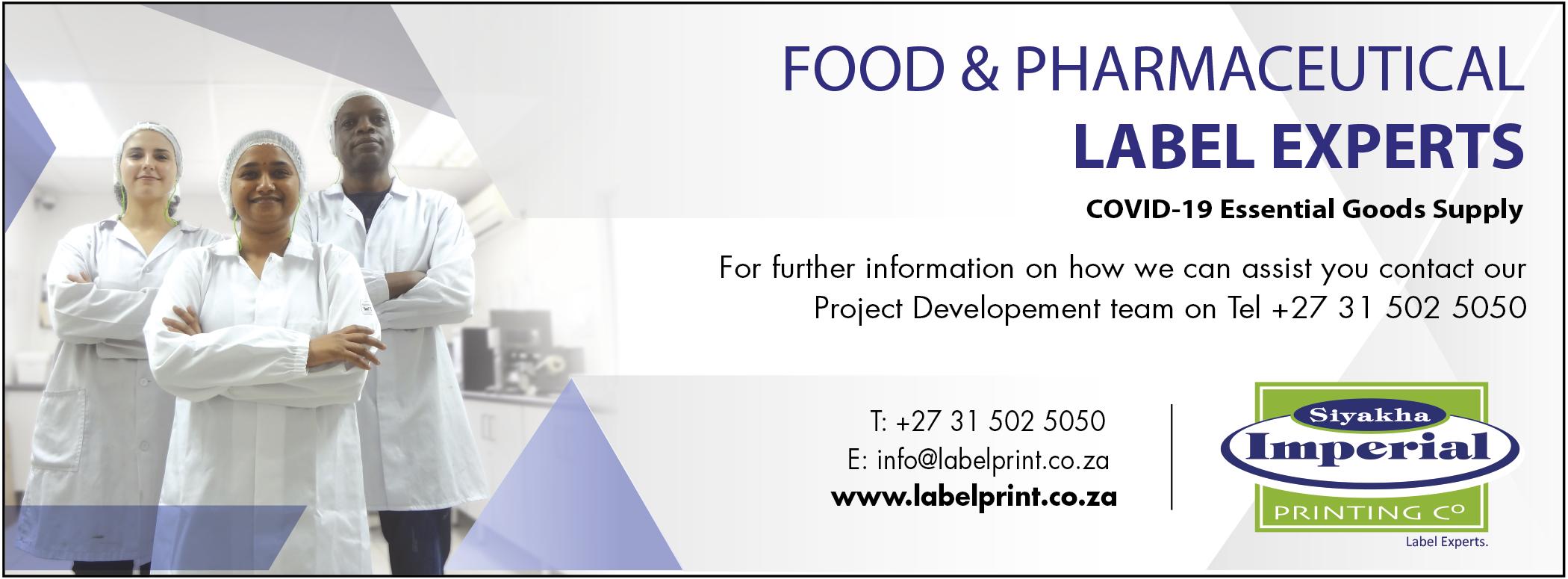