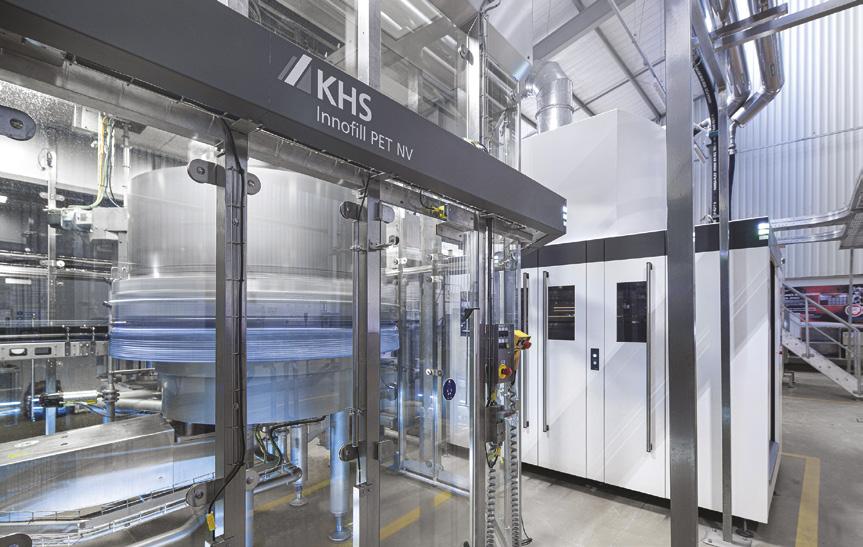
19 minute read
BEVERAGE PROCESSING TECHNOLOGY
Ugandan bottler climbs high with new PET line
Uganda’s Rwenzori water brand has a 65% market share in Africa
With the help of KHS technology, the sale of packaged water in Uganda is climbing to new heights. Denise Schneider-Walimohamed of KHS East Africa talks to Food Manufacturing Africa about how new technology can impact operations.
AT JUST OVER 5 000m above sea level, Margherita Peak in the Rwenzori Mountains in northwestern Uganda is Africa’s third-highest summit.
For many mountaineers, the massif is considered an attractive alternative to Kilimanjaro. Despite its location on the equator, surrounding peaks are still glaciated.
WATER AS GROWTH PRODUCT
One of Uganda’s best and largest mineral water brands, Rwenzori, depicts the mountain range on its logo. The product is bottled nearly 300km from Margherita Peak in Namanve in the greater Kampala region.
When the Rwenzori Bottling Company began operations in 1993, it faced the challenge that bottled water was still a relatively new and unknown product for many people. This has changed: the sale of bottled water has skyrocketed throughout Uganda, especially in urban centres. Annual growth rates clock in at a steady 10% - precipitated by a growing awareness that the product is safer to drink than tap water, better in quality and a brand with a long tradition.
EXPLORING POTENTIAL
In 2014, the Rwenzori Bottling Company was acquired by Coca-Cola Beverages Africa (CCBA), which operates in South and East Africa. Part of the new strategy is to locally integrate well-known mineral water brands into their group to develop them further. Targeted marketing measures can effectively exploit growth potential – in addition to Uganda, this is already happening in Kenya, Ghana and Ethiopia.
Rwenzori has plans for further growth of its water brand, which has gained an approximate 65% share of the Ugandan market, but it remains a challenge. There’s no space available for a new production line at the main plant where three smaller bottling lines are in operation. Instead, operations are to be expanded on the site belonging to CCBA subsidiary Century Bottling Company, just a few hundred meters away. The group is investing a total of $10m – about two-thirds of Uganda’s planned budget for 2018.
COMPELLING TECHNOLOGY
KHS was awarded the contract for the new PET line. In addition to an Innoket Neo labeller, the package includes an InnoPET BloFill stretch blow moulder/filler block with a capacity of up to 25 000, 500ml bottles per hour.
“This is the second water bottling line that CCBA will be receiving from us within a very short space of time,” enthuses Denise Schneider-Walimohamed, managing director of KHS East Africa. “Last year we installed an almost identical line at Voltic in Ghana. Until now, many customers in the region have associated KHS with higher-capacity machines outputting up to 80 000 bottles per hour. With these two projects, we’ve been able to prove that KHS offers excellent water bottling systems in the low-capacity range.”
All capacity levels are now in demand in Africa and most water bottling systems are sold in the KHS Middle East/Africa Market Zone managed by executive vice president Markus Auinger.
The company was particularly impressed by the Innofill PET NV water filler – the first machine designed for still water acquired by Coca-Cola Beverages Africa in Uganda. The German systems supplier has chalked up points with other projects KHS has also implemented for CCBA in Uganda, including a PET line for carbonated Coca-Cola soft drinks installed in Mbarara in 2015. “Our experience with KHS has been very good. We know that we can rely on short delivery times, fast installation and commissioning and the expert support and flexibility of the KHS team,” explains Edward Ojede, project manager at CCBA in Uganda.
EXPERTISE IN BOTTLES
Particularly noteworthy is the support provided by the KHS experts in the company’s Bottles & Shapes programme who contribute their expertise in the development and optimisation of bottles.
The consultancy service produces PET bottles which have been optimised in terms of ecology and economy and boast 100% line suitability and compliance with the customer’s design concepts.
Although the line was officially commissioned in May 2019 by the president of Uganda, represented by the minister of trade, industry and cooperatives, production has been running since the beginning of that year – and very smoothly at that. The performance figures of the new system have even exceeded CCBA’s high expectations. “We’re achieving a line efficiency of 98%,” says Conrad van Niekerk, managing director of CCBA Uganda, happily. “Rwenzori’s water bottling line operates around the clock, seven days a week. The performance figures of this line and those from Mbarara are the best in the entire group.”
Even though the expanded capacity is already reaching its limits, the key factor in CCBA’s output is the availability of water, which is a limited and therefore precious resource in Uganda.
In addition to efficiency, the subject of sustainability is important not only for beverage producers in Uganda but for the rest of Africa as well.
CCBA can score here, too: under the motto of ‘a world without waste’, CCBA wants to help ensure that by 2030, 100% of all PET bottles sold are collected and recycled. Plastic Recycling Industries, a recycling initiative owned by CCBA and founded specifically for this purpose, buys collected PET bottles from consumers and then reintroduces them to the recovered materials cycle. If many more companies follow this example and are thus able to stem climate change, the glaciers of the Rwenzori Mountains will retain their beauty for a long time to come. •
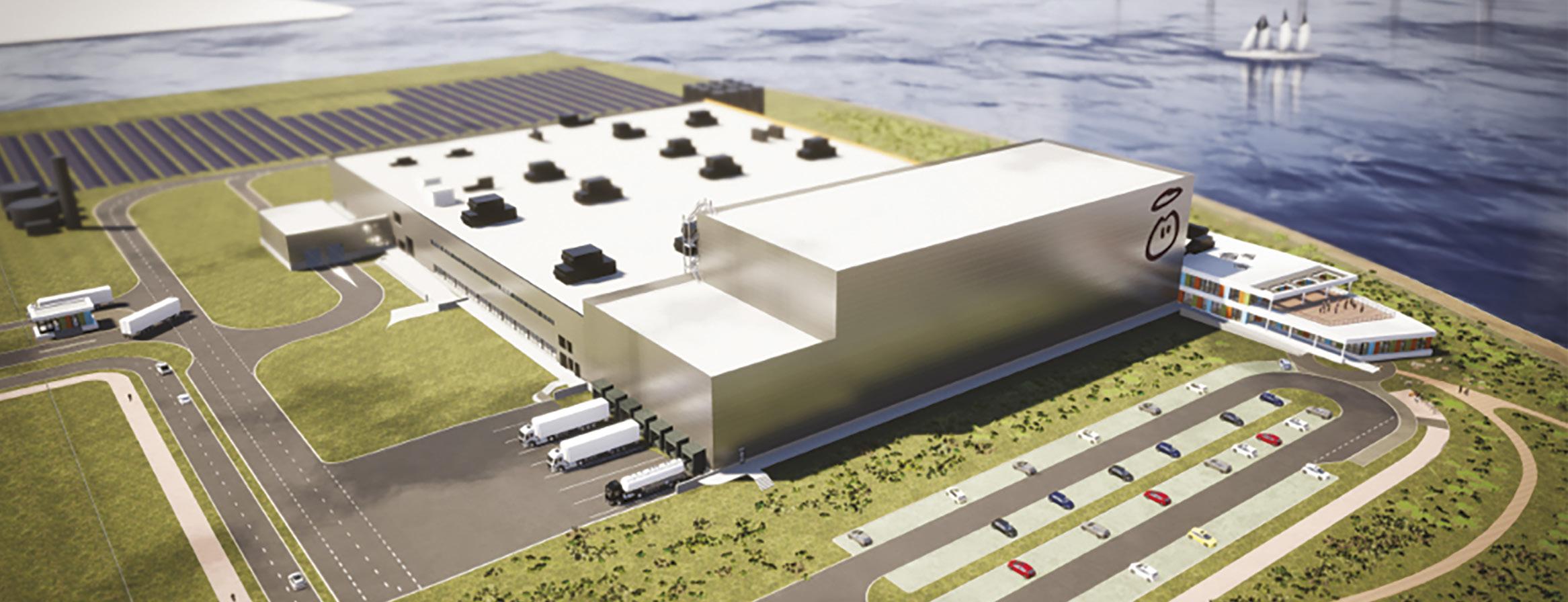
Innocent’s new CO2-neutral bottling plant in the Port of Rotterdam in Holland is equipped with four complete Krones PET bottling lines and the corresponding IT landscape
CO 2 -neutral bottling plant makes waves
Following years of contract-bottling, the smoothie and juice producer innocent has decided to build its own bottling plant.
KRONES WON THE order for four complete PET bottling lines and the corresponding IT landscape. The paramount consideration for “the blender”, as innocent has christened its greenfield project, was sustainability: the aim is to build an entirely CO2-neutral factory.
“We’re also keen to reduce water consumption to a minimum, since we want to treat and re-use as much of it as possible,” explains Sam Woollett, engineering and facilities lead. Each of the four identical PET lines handles up to 32 000 containers an hour. The new plant has been tasked with filling about 400 million bottles of chilled drinks a year. In all, innocent has invested approximately $250 million in this project.
FOUR COMPLETE PET BOTTLING LINES FROM KRONES
The Contipure AseptBloc DA blow-moulder/ filler block consists of a Contiform 3 Pro stretch blow-moulding machine and a Modulfill Asept aseptic filler. For the Contipure D preform sterilisation module, innocent opted for a particularly sustainable version. This ensures a reduced total cost of ownership (TCO), thanks to lower consumption of hydrogen peroxide, steam and energy, plus shorter preparation times.
After being filled, all containers are fitted with a tamper-evident seal, and depending on the format involved, dressed in a wrap
256 colours Individually selectable:
Measurement in progress Sensor switching Process malfunction
R2 870.00
VEGAPOINT 21 G½"
www.vega.com/vegapoint We bring colour into view!

Compact capacitive level switches with 360° custom-colour status display
around or pressure-sensitive label. The modularised Topmodul labeller is block-synchronised directly with the Variopac Pro FS packer.
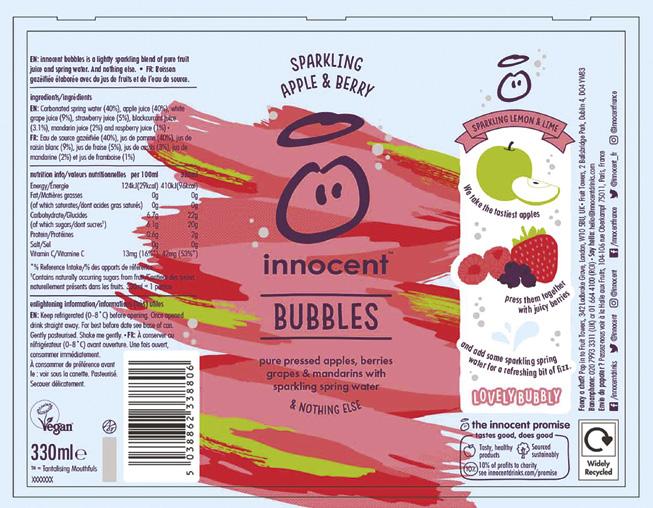
SYSKRON IS DIGITALISING ALL THE FACTORY’S PROCESSES
As the group’s digitalisation specialist, the Krones subsidiary Syskron has developed a turnkey MES concept for innocent that integrates through appropriate interfaces also integrates the ERP system, the process control and warehouse management systems in the new plant. This concept includes various solutions from the SitePilot IT family brand, not least the production planning system, the Line Management order and administration system, plus Line Diagnostics for production data acquisition and analysis. From the category of Share2Act services, innocent will in future be using Connect: this enables all information, such as shift schedules, to be made available to all staff in digital form.
Chief blender Andy Joynson explains, “Innocent is aiming to build the earth’s favourite little healthy drinks factory, the blender. It’s location in the Port of Rotterdam is no accident: We will minimise the distance between the place where the fruits arrive from overseas and the actual production facility. This enables us to reduce the company’s CO2 footprint by about 10%. We are delighted that we will be able to bottle our healthy drinks in our own plant, but more pleased that we will ensure that the production operation and the buildings comply with our sustainable standards.” •
DID YOU KNOW?
Every day, millions of glass bottles, cans and PET containers run through a Krones line. As a supplier for complete systems, Krones designs and implements complete lines for beverages and food, which cover each individual production process step – starting from product and container production, filling and packaging all the way up to material flow and container recycling.
South African Food Review , 132 x 200 mm, MetaPure, CC-en53-AZ036 07/20
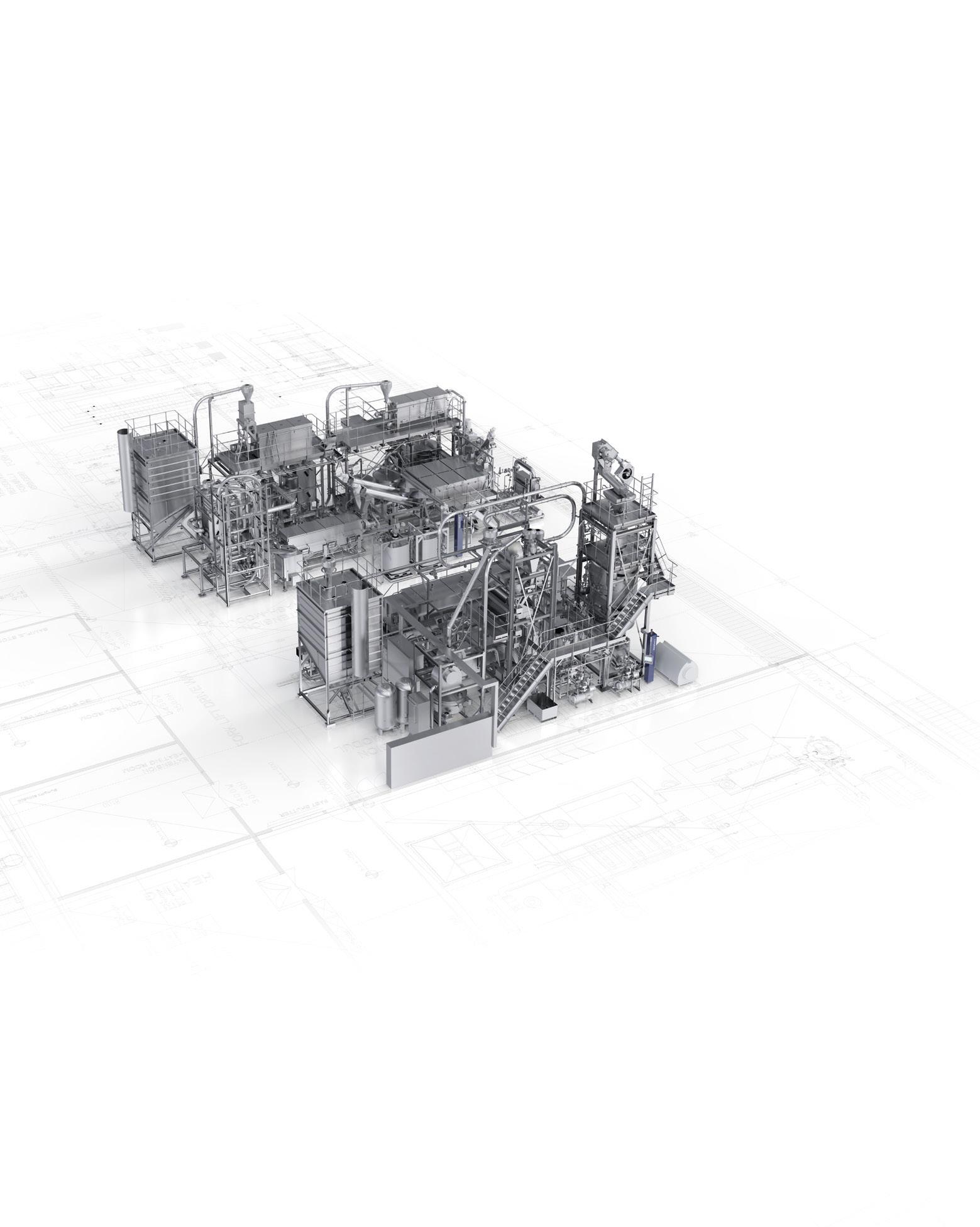
1, 2, 3: Sidel’s EvoFill HS Still guarantees a faster performance than some traditional units
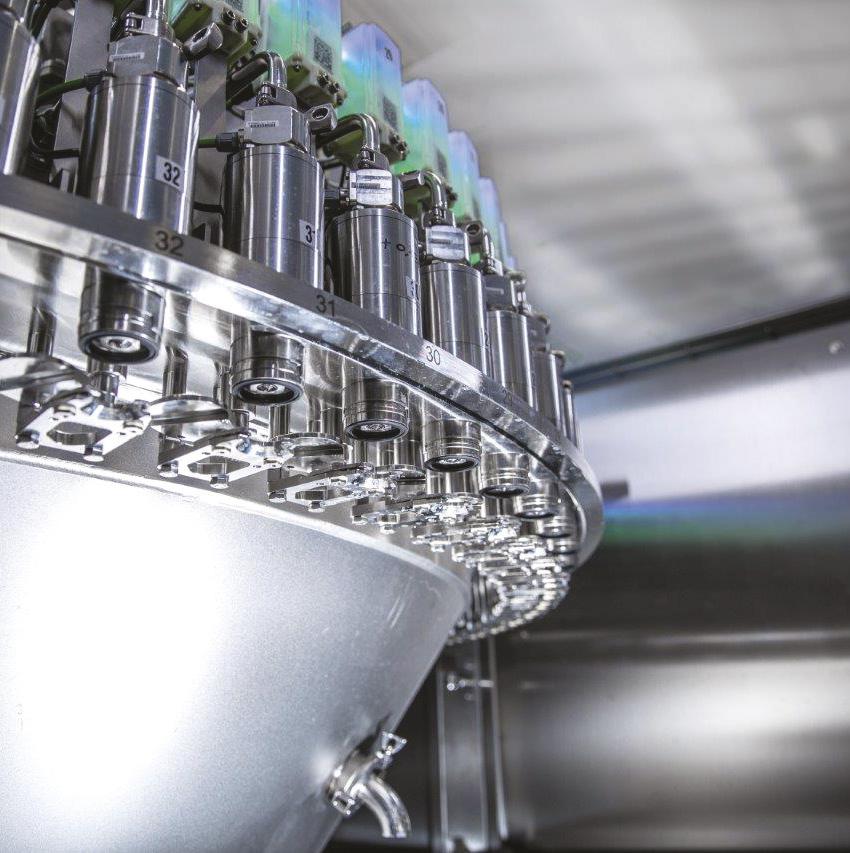
1

Super Combi Compact allows more performance using less space
Two years ago, Sidel introduced the Super Combi for compact line solutions. This year sees a bolder, next-generation solution Super Combi Compact that, as indicated in its name, is even more condensed.
With a 30% footprint reduction compared to the previous model, the solution features efficiency enhancement with new filling technology embedded in the Sidel EvoFILL HS Still. The technology guarantees a 30% faster performance.
Customers globally are seeking possibilities to optimise resources and space required for production. Sidel has developed a ready-made solution to fit any production site footprint. Line integration and planning are important drivers at the centre of Sidel’s technological advancement. Super Combi Compact is an innovative product designed and engineered to deliver low total costs of ownership (TCO) and production costs per square foot.
GROWING DEMAND FOR PACKAGED WATER
The water category is seeing an unprecedented growth fuelled by a worldwide increase in demand. “Rising health consciousness paired with the trend of better-for-you drinks, the packaged water category has remained at the forefront of consumer purchasing decisions since 2018,” explains Stefano Baini, product manager filling and Super Combi at Sidel. This is just one of the reasons why the company has invested in the development of a compact line solution for still water production. This green trajectory throughout the water category was globally influenced by a large hike in tourism along with extremely warm weather not only in warm climate countries but in parts of Western Europe too.
The overall higher level of efficiency of the solution is achieved by providing maximum uptime and consistent production output at medium to high speed. Maximum productivity of the line is reached
2
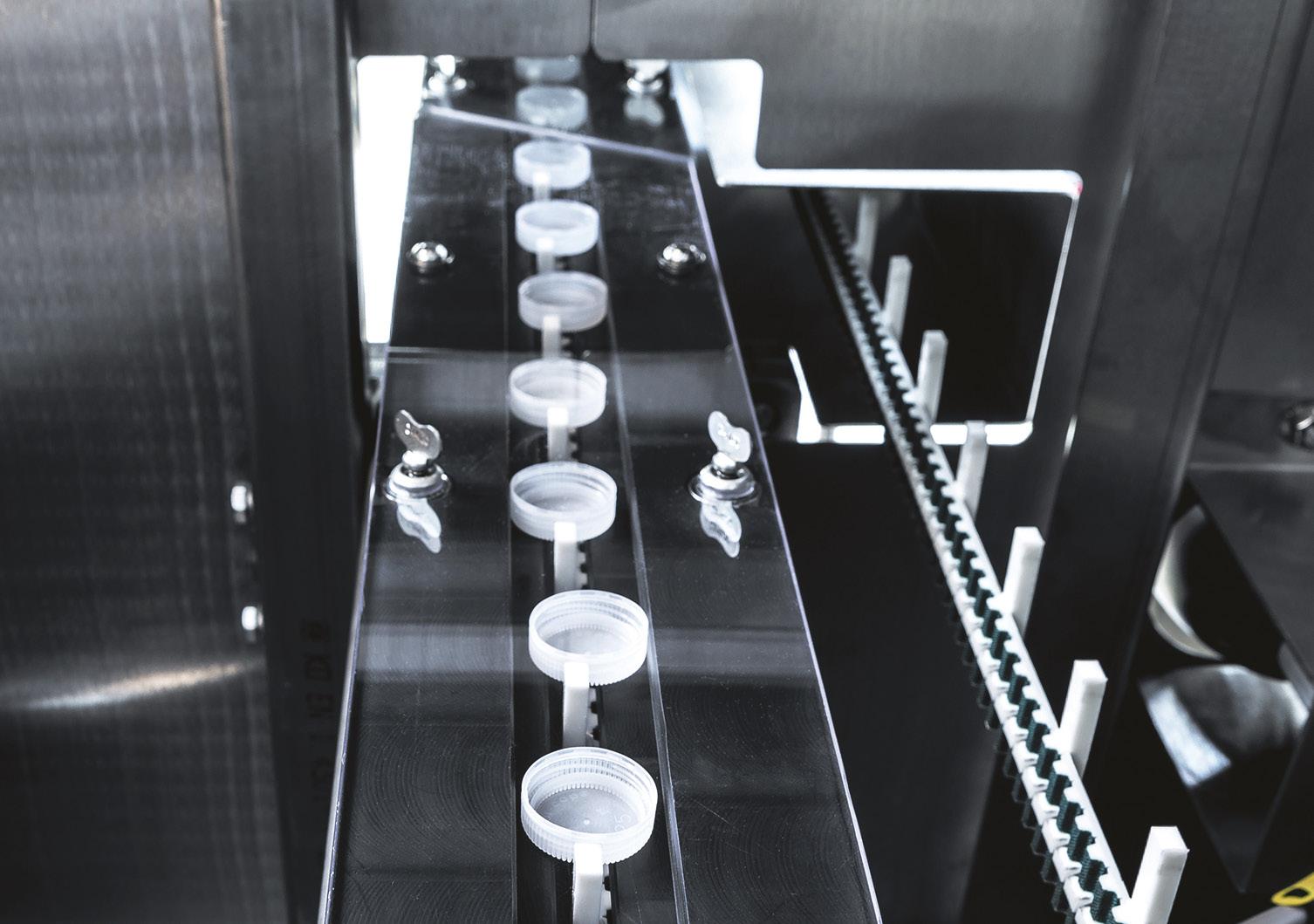
particularly due to improvements at the blowing, filling and labelling stages. To highlight some of the most important improvements, the blower can produce up to 2 700bph per mould. A robotic arm solution for automatic mould changeover is available to drastically reduce changeover time and improve safety conditions by not requiring any human intervention.
ENHANCED PERFORMANCE AND PRODUCTIVITY
Similarly, to its predecessor, Super Combi Compact is integrating five process steps – preform feeder, blower, labeller, filler/ capper and cap feeder into an all-in-one, smart system. What describes the new solution the best is the continuous toplevel performance it provides up to 54 000 bottles per hour (bph) in a reduced space. Ergonomic design and the latest technologies supports easy access, operation and maintenance while ensuring high end-product quality.
Labelling is assured by a single-aggregate labelling system, ensuring reliable production and fast and easy label-reel auto splicing. Super Combi Compact’s labeller technology features faster changeovers and easy replacement of parts and an automatic label vacuum extractor for maximised uptime. The labeller can accommodate different labels and technologies (roll-fed and PSL).
SIDEL EVOFILL HS STILL FILLING TECHNOLOGY
The new filler with proportional filling valves, controlled by electro-magnetic actuators, guarantees a 30% faster filling with total control and accuracy when it comes to dosing liquid into its designated container. The improved and completely dynamic filling technology allows for highest precision in modulating the beverage flow, as the plunger inside the filling valve can individually be moved to an infinite number of positions, resulting in maximum freedom in terms of different beverage types to be filled, and different optimum filling speeds and levels. Furthermore, the new hygienic valve design with no beverage membrane assures beverage quality with no flavour carry-over.
EvoFILL HS Still is a simplified solution characterised by fewer components and functions, resulting in fewer maintenance costs, and a highly reduced filler footprint with less filling valves. Additionally, filler features and onboard beverage tanks further contribute to minimising the required floor space. It could also be equipped with an Integrated Cleaning System (ICS), cutting down on water and chemical consumption for internal cleaning and rendering the need for an external cleaning-in-Place system and additional tanks unnecessary.
With savings of up to 30% floor space, a boost in production efficiency of 30%, and the delivery of maximum speeds of up to 54 000bph, the new Super Combi Compact is a perfect fit for producers of PET bottled water. Baini concludes, “Its new, compact design and innovative filling technology makes it an ideal solution for maximising production and increasing line efficiency at the best TCO per square foot – allowing producers to make the most of their existing space or new greenfield projects." •
Sidel - www.sidel.com/supercombicompact
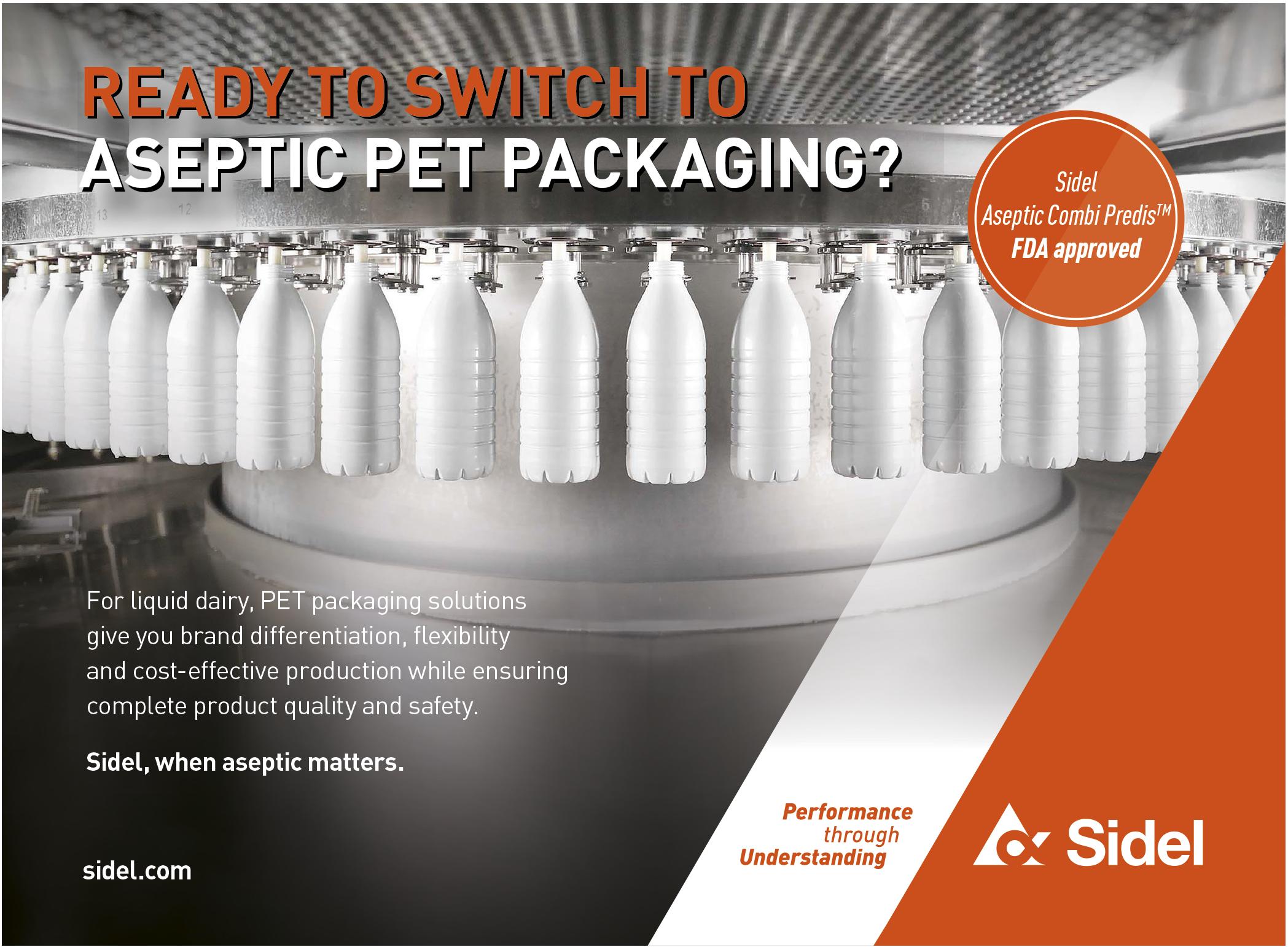
Cobot and flexible production - future-proofing SMEs
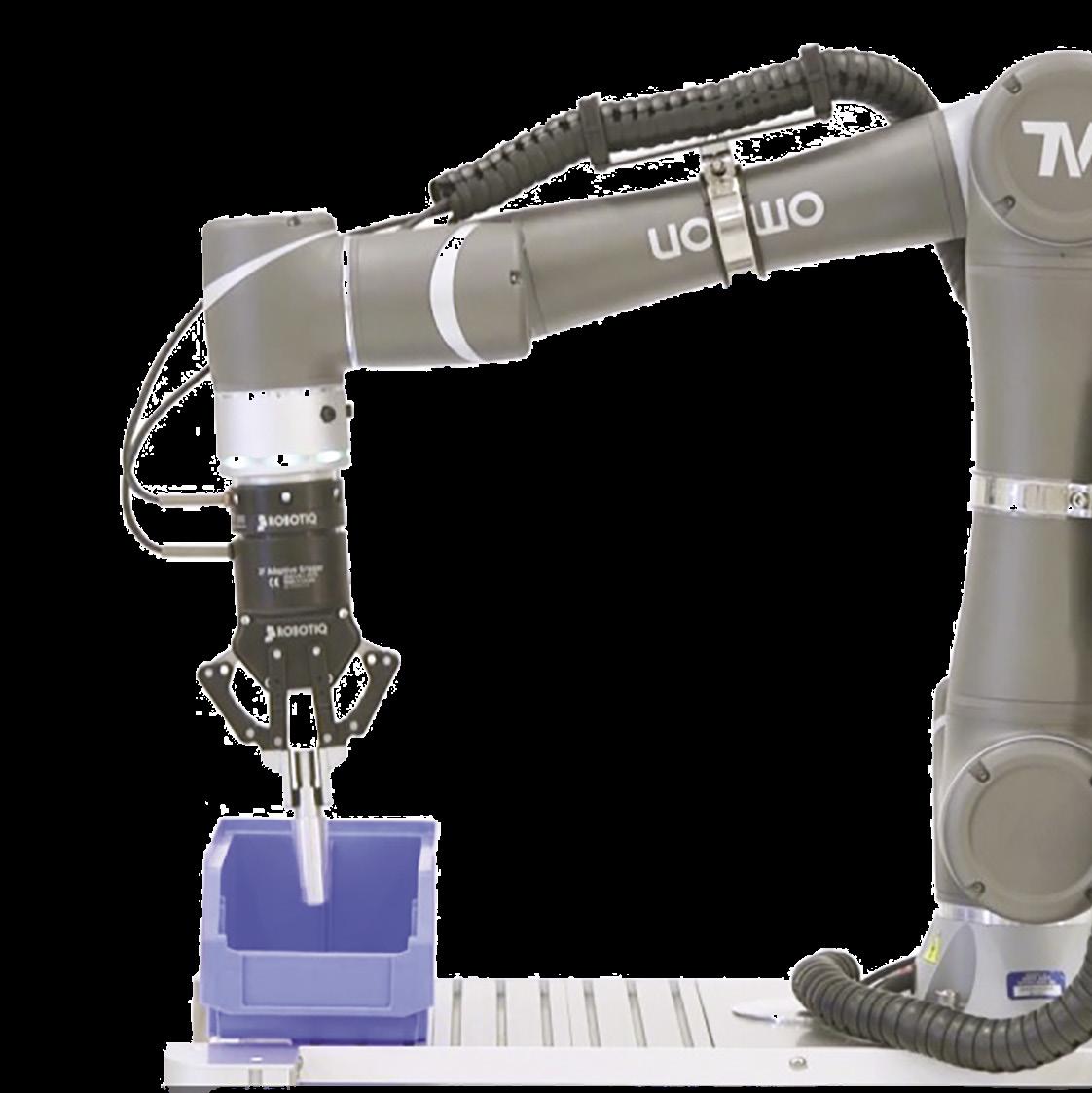
Many countries the EMEA region are likely to experience serious labour shortages over the coming decade, especially in relation to technical specialists. At the same time, product lifecycles are becoming shorter.
ABOUT INNOVATIVE-AUTOMATION
As a leader in industrial automation, Omron has extensive lines of control components and equipment, ranging from vision sensors and other input devices to various controllers and output devices such as servomotors, as well as a range of safety devices and industrial robots.
By combining these devices via software, the company has developed a variety of unique and highly effective automation solutions for manufacturers globally. Based on its reservoir of advanced technologies and comprehensive range of devices, it can set forth a strategic concept called innovative-Automation consisting of three innovations or "i's": integrated (control evolution), intelligent (development of intelligence by ICT) and interactive (new harmonisation between people and machines). Omron is now committed to bringing innovation to manufacturing sites by materialising this concept.
DESPITE THIS, SMALL and mediumsized enterprises (SMEs) might be reluctant to invest in additional automation due to the cost factor. Collaborative robots (cobots) are easy to set up and offer a quick and cost-effective solution, for example the Omron TM series of collaborative robots. They can increase the flexibility, quality and speed of production and enable companies to respond rapidly to changing market conditions.
The question is however, how will robots future- proof these enterprises?
Robots are not new to the industrial world and were first used in industrial manufacturing in the 1960s and since then, their number has increased inexorably. Some 500 000 to 600 000 new robot systems are now becoming operational throughout the world each year, although the increase is particularly noticeable in the Asian market, as reported in ‘World Robotics 2019’ by the International Federation of Robotics (IFR) and Fraunhofer IPA.
If small and medium-sized production companies in the EMEA region want to keep up with constant economic growth internationally, they need to invest more in automation for cost reasons alone. Due to technical skills shortages, greater automation is needed to counteract this decline.
COBOTS PROVIDE GREATER FLEXIBILITY
Classical industrial robotics might not be the solution in all applications. Traditional production lines are designed for manufacturing large numbers of products. In today’s world, product lifecycles are getting shorter for example, in the 1970s, the average product lifecycle of a vehicle was eight years. Today, car models often get their first modifications or facelifts after just two to three years. Production and automation must adapt to the shorter lifecycles of products, and cobots can help with this.
Cobots were first introduced in 2008 and represent a relatively new category of industrial robots. In contrast to traditional robots, which must be shielded from the human workspace by a security fence, cobots were developed to work safely with people. Users also need less time and money to program an application with these “helper robots.”
In addition, cobots can easily be moved from one location to another to work on different tasks, whereas conventional industrial robots have to stay in one location and can normally only be used for a specific task within the robot cell. Cobots therefore
provide greater flexibility to the user.
The diverse tasks they can handle vary from simple pick-and-place applications for parts handling, sorting, and palletising, right through to machine assembly, order picking, packaging, and testing. They can help to apply adhesive and sealants, assemble or disassemble parts, measure, test, check and take over screwing operations.
The result is seen in significant benefits for the employees, who no longer have to carry out monotonous, physically demanding or even dangerous work, but will receive support with precision work and can concentrate on their core abilities.
COBOTS ARE USER-FRIENDLY AND VERSATILE
Omron’s TM series of cobots illustrate how versatile and straightforward cobots are in today’s world. The different versions are suitable for practically any environment, such as the automotive, semiconductor, food, packaging, and cosmetics sectors. Due to the flowchart-based programming, an intuitive HMI user interface and simple, hand-guided teaching functions, almost no previous knowledge of programming is required. Just like with a PowerPoint presentation, the user can assemble complete function blocks
and fill the predefined attributes with the desired parameters. The cobots have options that include an integrated camera, vision and a lighting system which enable them to precisely handle and trace items.
Many core functions (such as pattern, barcode and colour recognition) enable detection, inspection, measurement and sorting applications to be implemented easily and, if necessary, adapted to other requirements. With the help of Omron’s Landmark positioning recognition facility, the cobot knows where it is and can be aligned with another machine, for example,

without much effort or recalibration. It can even move autonomously and work wherever it’s needed, because cobots can be combined with Omron’s LD series of mobile robots.
FROM NEEDS ANALYSIS TO SUPPORT
Additional components (such as extra axes, grippers, force sensors, communication devices or screwdrivers) can be easily used by the cobots via plug-and-play system. Omron has set up a partner network that offers a range of suitable components. The company’s automation experts also provide
Cobots were first introduced in 2008 and represent a relatively new category of industrial robots
support with any queries about the use of cobots. This starts with the analysis of the production task and the environment; the selection of the appropriate cobots and grippers or additional components; and also includes risk analysis and assessment, commissioning, training and technical support. All of this makes it easier for SMEs to gain a foothold in the flexible manufacturing industry of the future. •
Omron - www.industrial.omron.co.za
Superior image sensing speed and precision FH Series

• High-precision object detection • Ultra-high-speed searching • Flexible functionalities to provide high compatibility Flexible functionalities to provide high compatibility with manufacturing machines
Would you like to know more? +27 (0)11 579 2600 info_sa@omron.com industrial.omron.co.za
New measurement system
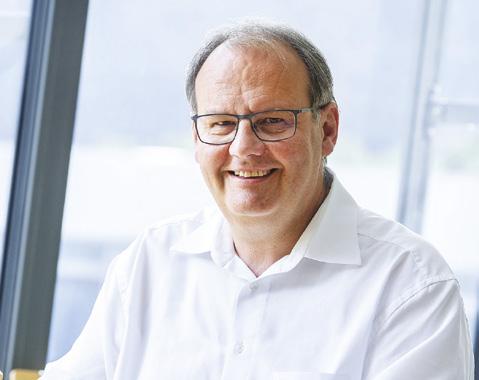


for perfectly sealed MAP packaging
“Optical sensors mounted LeakCheck is GEA’s new in-line measurement system capable of the on the thermoformer contactless checking of seal and package integrity on all forms of project light onto the modified atmosphere packs (MAP). This guarantees the protective function of the seal and assures consumers about the quality of the products and food packaging. sensor spot, gauging the wavelength of the light emitted by the dye to accurately determine the oxygen content”
CONSUMERS WANT FRESH, hygienically packaged food, while retailers want long-lasting products that look attractive. Positioned at the start of the supply chain, food manufacturers must provide solutions that meet all hygiene and quality standards. Meeting these demands while boosting productivity calls for end-toend process monitoring automation.
First in line was GEA’s tried-and-trusted OxyCheck quality control system. This contactless, non-invasive oxygen content measuring system has been verifying every MAP since 2017. Based on that system, the GEA LeakCheck now uses an in-line process on the GEA thermoformer to test the seal and package integrity on each package.
The test procedure comprises three steps. Firstly, the residual oxygen content in each package is measured with a fluorescent sensor GEA LeakCheck sensors measure the oxygen content of the MAP packs spot printed on the inside of the top film. Optical sensors mounted on the thermoformer project light onto the sensor spot, gauging the wavelength of the light emitted by the dye to accurately determine the oxygen content.

GEA LeackCheck Volker Sassmannshausen
This step alone significantly reduces the risk of defective packaging with excessively high residual oxygen levels. Next, packages are subjected to overpressure and under pressure in a stress unit before a second contactless measurement is taken. If the new result differs from the first, the package seal is broken. Using the GEA CombiPick, for instance, the leaky package is automatically detected and accurately removed on exiting the packaging machine. This method ensures that even the smallest leaks are detected.
To boost food processing productivity, the industry is increasingly focusing on automation. The aim is to achieve a consistent or even enhanced product quality.
Thanks to GEA LeakCheck, the two key factors for ensuring food safety – residual oxygen content and seal integrity – can now be continuously recorded and monitored on an end-to-end basis. Process errors are rapidly detected and the delivery of faulty packaging is virtually zero.
In summary, Volker Sassmannshausen, senior product manager, thermoforming packaging systems at GEA, emphasises, “With the GEA LeakCheck, all units leaving the packaging machine are tested non-invasively. Since the measuring techniques are non-invasive, neither the packaging material nor the contents are wasted. Besides efficiency and sustainability, the upshot is that practically no defective packaging reaches the market.” •
GEA – www.gea.com