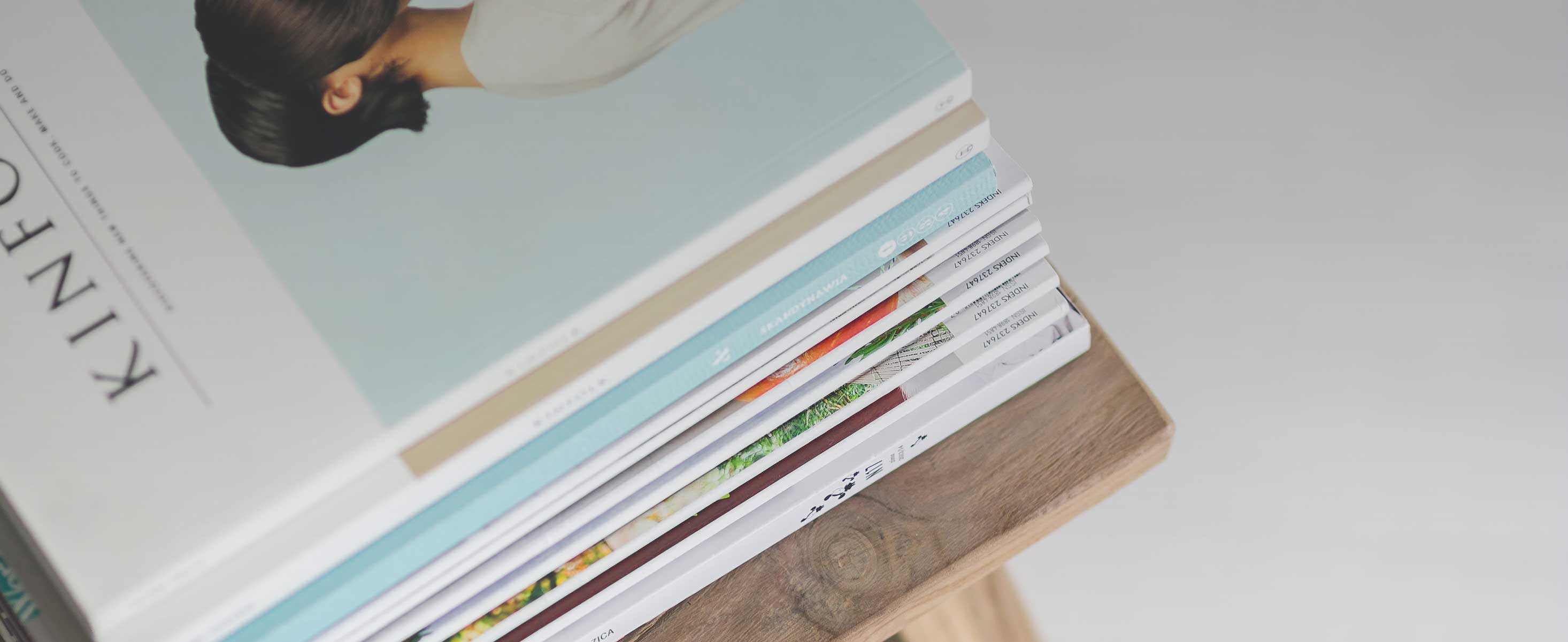
2 minute read
When clients opt for speed
In late 2018, Krones set a benchmark in stretch blow-moulding technology for PET bottles with the introduction of its Contiform 3 Speed. The technology boasts an hourly output so far unique in the sector: 2 750 containers per cavity. Less than two years later, the 100th Contiform 3 Speed has been sold.
The Krones Contiform 3 Speed
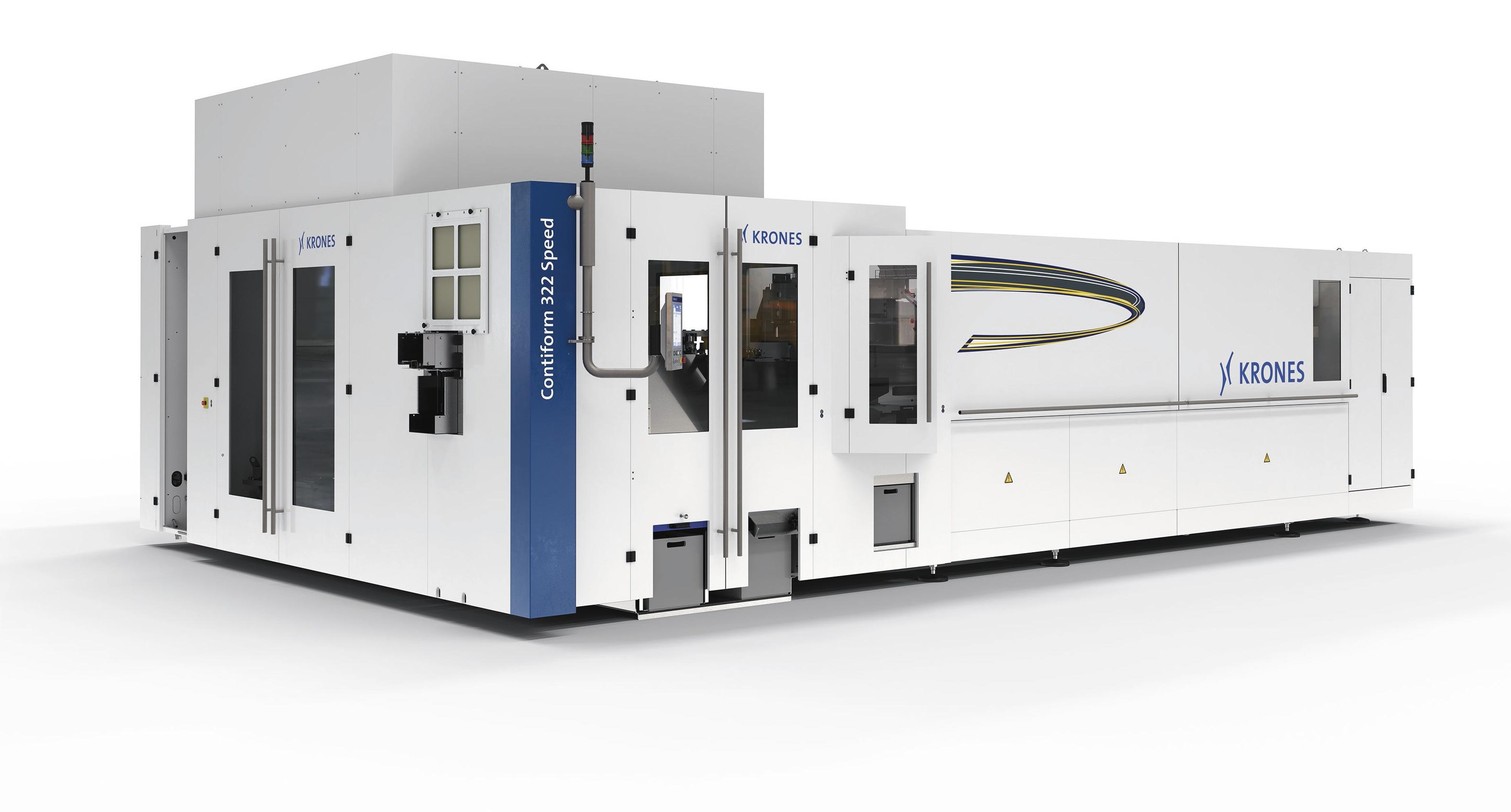
Since October 2020, this milestone machine from Krones has been up and running at the main facility of Odenwald Quelle, a producer of soft drinks headquartered in Heppenheim, Germany.
For Andreas Schmidt, managing partner at Odenwald Quelle, the decision to opt for the stretch blow-moulder from the House of Krones came quickly and easily. “The Contiform 3 Speed boasts several attractive benefits. It is compactly dimensioned and produces more containers while consumption levels are lower. It also effortlessly handles preforms made of rPET. This advantage was of crucial importance to us because we’ve since 2020 been selling only plastic bottles made of 100%recyclate,” he explains.
NO PRESSURE PAD MEANS HIGHER OUTPUT AND EFFICIENCY
Whereas in the case of conventional stretch blow-moulders, a pressure pad in the mould carrier additionally keeps the two halves of the mould together during the stretch blow-moulding process, the Contiform 3 Speed has been designed in such a way that the two halves are kept together purely by means of the revamped mould carrier locking mechanism. The omission of the pressure pad means that the moulds can produce bottles with a volume whereas in the case of conventional stretch blow-moulders, a pressure pad in the mould carrier additionally keeps the two halves of the mould together
during the stretch blow-moulding process, the Contiform 3 Speed has been designed in such a way that the two halves are kept together purely by means of the revamped mould carrier locking mechanism.
The omission of the pressure pad means that the moulds can produce bottles with a volume of up to 2L – and this in a blowmodule size so far used in the small-cavity machines, which is on average 22% smaller than the comparable blow module of the Contiform 3 Pro.
Dliminating the pressure pad provides advantages not only in terms of line layout but also in regard to media and energy consumption: it makes for savings of up to 15% of highly compressed air in comparison to all other stretch blow-moulders currently available on the market. •
Krones – www.krones.com